How Much Material Is Required for a 1,500 Sq Ft House?
Building or renovating a 1,500 sq ft house requires careful planning and a clear understanding of the materials needed.
Accurately estimating the amount of materials required ensures that the project stays on budget and on schedule. This guide provides a detailed overview of the materials needed for various parts of the house, helping you plan effectively and avoid unnecessary delays or costs. From the foundation to the finishing touches, each component plays a crucial role in the overall success of the project.
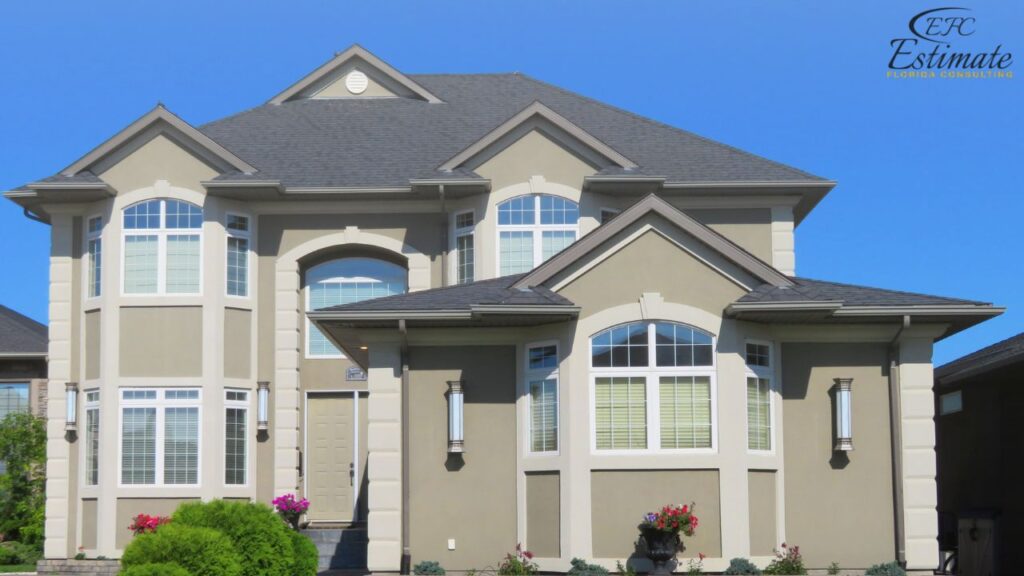
By understanding these needs, you can make informed decisions and ensure that every aspect of your home construction or renovation is well-managed, leading to a smoother and more efficient construction process. Proper planning and precise material estimation can also prevent wastage and save costs in the long run.
Foundation Materials
The foundation is one of the most critical parts of a house, providing structural support. The materials needed for the foundation will depend on the type (slab, crawl space, or basement) and the local building codes. A strong foundation not only supports the weight of the house but also ensures its stability and longevity. It is essential to choose the right materials and ensure they are installed correctly to prevent future issues such as settling or cracking. Proper foundation materials and installation techniques can significantly impact the durability and lifespan of your home, making it crucial to invest in high-quality materials and skilled labor.
Cost Details for Foundation
The cost of foundation materials can vary significantly based on the type and quality of materials used. Here’s a breakdown of the average costs for the foundation materials:
Component | Estimated Quantity | Estimated Cost (in dollars) |
Concrete | 25 – 30 cubic yards | $4,550 – $5,460 |
Rebar | 1 ton | $2,730 – $3,640 |
Gravel | 5 – 10 cubic yards | $455 – $910 |
Formwork (plywood, braces) | Depends on foundation design | $910 – $1,820 |
Concrete
Concrete is the primary material used for the foundation. For a 1,500 sq ft house, the amount of concrete needed will vary based on the foundation type and design. Concrete provides the necessary strength and durability to support the house and withstand environmental factors such as moisture and temperature changes. A well-poured concrete foundation will help prevent issues like water infiltration and soil erosion, contributing to the house’s overall stability and safety.
Concrete is typically mixed on-site or delivered pre-mixed, and it is poured into forms to create the foundation slab, footings, or walls. The inclusion of rebar reinforces the concrete, enhancing its tensile strength and preventing cracks. Gravel is used as a base layer to provide drainage and prevent water from accumulating under the foundation, ensuring long-term stability. The combination of these materials helps create a robust and durable foundation that can withstand various environmental stresses.
Formwork and Reinforcement
Formwork and reinforcement are essential for shaping and strengthening the concrete foundation. Proper formwork ensures that the concrete sets in the desired shape and dimensions, while reinforcement materials like rebar provide additional structural support. This process is critical for ensuring the foundation’s ability to bear loads and resist external pressures.
Formwork is typically made from plywood and supported by braces to hold the concrete in place until it cures. The reinforcement bars (rebar) are placed within the formwork before pouring the concrete to enhance the foundation’s strength.
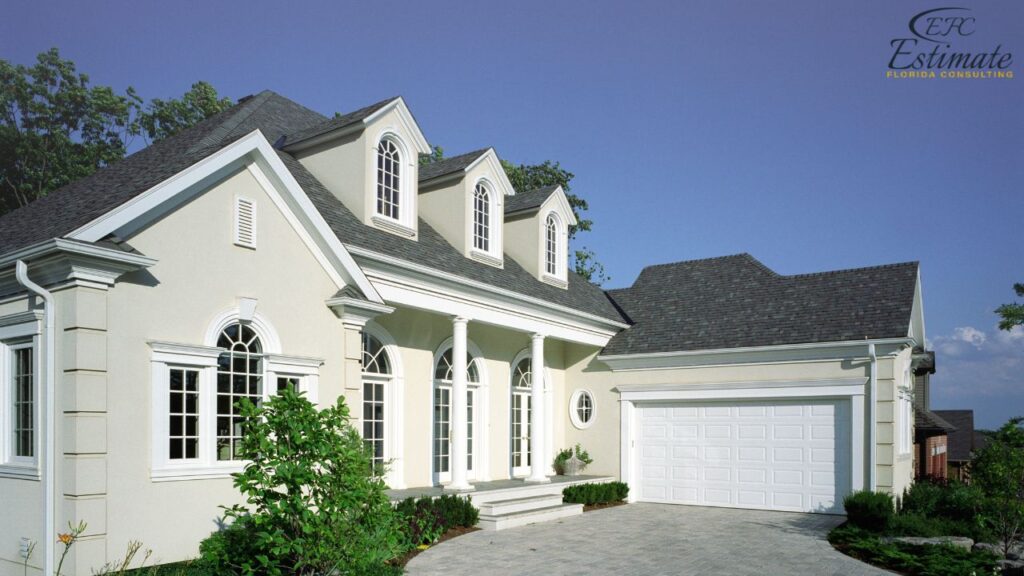
This combination of formwork and reinforcement ensures a durable and stable foundation that can support the entire structure of the house, contributing to the overall longevity and resilience of the building. Investing in high-quality formwork and reinforcement materials is essential for building a foundation that will last for decades without significant issues.
Framing Materials
Framing forms the skeleton of the house, providing structure and support for the walls, roof, and floors. The framing process involves creating the framework for each level of the house, including walls, floors, and ceilings. This stage is crucial for defining the house’s layout and ensuring its structural integrity. Proper framing is essential for ensuring the stability and safety of the entire structure, as it provides the necessary support for all other building components.
Cost Details for Framing
Framing costs depend on the size and complexity of the house design. Here’s a breakdown of the average costs for framing materials:
Component | Estimated Quantity | Estimated Cost (in dollars) |
2×4 Lumber | 12,000 – 15,000 linear feet | $13,104 – $16,380 |
2×6 Lumber | 2,500 – 3,000 linear feet | $4,550 – $5,460 |
Plywood/OSB Sheets | 150 – 200 sheets | $5,460 – $7,280 |
Nails (various sizes) | 50 – 60 pounds | $280 – $360 |
Fasteners | Varies based on design | $180 – $360 |
Lumber
Lumber is the primary material used in framing. The amount required depends on the house design and the number of floors. High-quality lumber ensures that the frame is sturdy and can support the weight of the roof and any additional floors. Using treated or high-grade lumber can also help prevent issues such as warping, rot, and pest infestation, contributing to the long-term stability of the house.
2×4 lumber is commonly used for constructing walls, while 2×6 lumber is used for exterior walls that require additional insulation and strength.
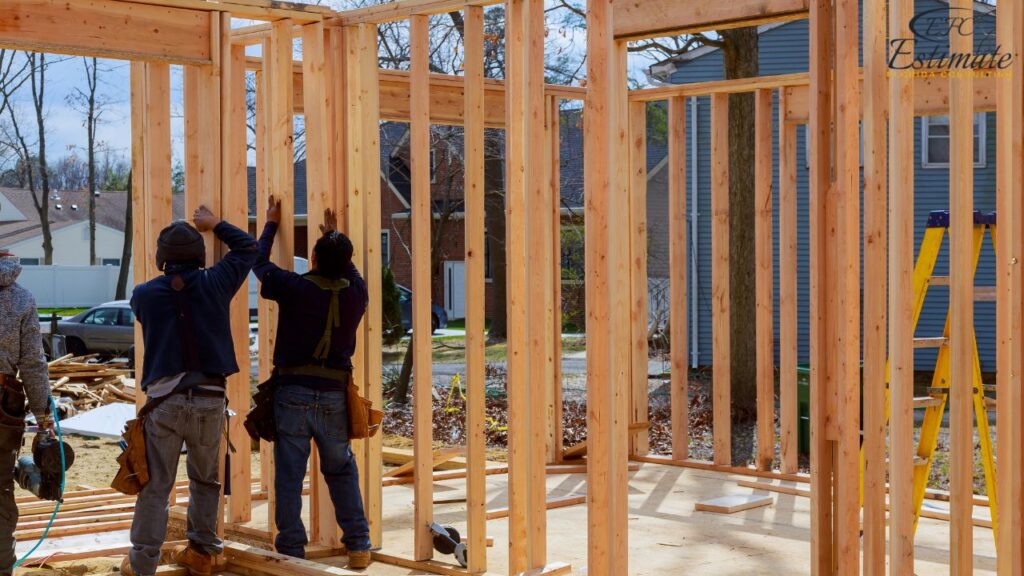
Plywood or oriented strand board (OSB) sheets are used for sheathing the walls, floors, and roof, providing a solid surface to attach siding, roofing, and interior finishes. The choice of lumber and sheathing materials significantly impacts the house’s overall strength and energy efficiency.
Nails and Fasteners
Nails and fasteners are used to join the framing components. Proper fastening is essential for maintaining the structural integrity of the frame and ensuring that all components are securely connected. The quality and type of fasteners used can affect the durability and stability of the frame.
The type and size of nails and fasteners will vary depending on the specific requirements of the framing. Common sizes include 16d nails for framing walls and 8d nails for attaching sheathing. Using the correct fasteners ensures that the frame remains stable and can withstand environmental stresses such as wind and seismic activity. High-quality nails and fasteners also help prevent issues like loosening over time, which can compromise the structure’s integrity.
Roofing Materials
The roof protects the house from weather elements and adds to its aesthetic appeal. Choosing the right roofing materials is essential for ensuring the roof’s durability, energy efficiency, and overall appearance. The type of roofing material will also impact the cost and maintenance requirements of the roof. A well-installed roof can significantly enhance the home’s curb appeal and overall value, making it an important investment.
Cost Details for Roofing
Roofing costs can vary widely depending on the materials chosen and the complexity of the roof design. Here’s a breakdown of the average costs for roofing materials:
Component | Estimated Quantity | Estimated Cost (in dollars) |
Asphalt Shingles | 45 – 50 bundles | $2,730 – $3,640 |
Underlayment | 15 – 18 rolls | $819 – $1,092 |
Flashing | 100 – 200 linear feet | $364 – $728 |
Ridge Caps | 3 – 4 bundles | $546 – $728 |
Roof Vents | 6 – 10 units | $546 – $910 |
Shingles
The amount of shingles needed depends on the roof design and pitch. Shingles provide the primary layer of protection against the elements, and their quality and installation directly affect the roof’s longevity. Asphalt shingles are known for their durability, affordability, and ease of installation, making them a popular choice for residential roofing.
Asphalt shingles are a popular choice due to their affordability, durability, and ease of installation. Underlayment is installed beneath the shingles to provide an additional layer of protection against moisture and wind. Proper installation of both shingles and underlayment is crucial for preventing leaks and extending the roof’s lifespan. High-quality shingles can also improve the home’s energy efficiency by reflecting more sunlight and reducing heat absorption.
Additional Roofing Materials
Additional materials include flashing, ridge caps, and ventilation. These components are essential for ensuring the roof’s overall performance and preventing issues such as leaks and poor ventilation. Properly installed flashing helps seal joints and transitions in the roof, such as around chimneys, vents, and skylights, preventing water infiltration.
Flashing is used to seal joints and transitions in the roof, such as around chimneys, vents, and skylights. Ridge caps are installed along the roof’s peak to provide a finished look and enhance ventilation. Roof vents help to regulate attic temperature and moisture levels, preventing issues such as mold growth and ice dams. Proper ventilation is crucial for maintaining the roof’s integrity and ensuring a comfortable living environment. Adequate ventilation also helps extend the life of the roof by preventing heat and moisture buildup.
Fill Out & Get A Contractor
Exterior Siding
Exterior siding protects the house and enhances its appearance. The type and amount of siding depend on the chosen material (vinyl, wood, brick, etc.). Siding not only adds to the aesthetic appeal of the house but also provides an additional layer of insulation and protection against the elements. High-quality siding materials can significantly improve the home’s energy efficiency and curb appeal, making it a worthwhile investment.
Cost Details for Siding
Siding costs vary based on the material chosen and the complexity of the installation. Here’s a breakdown of the average costs for siding materials:
Component | Estimated Quantity | Estimated Cost (in dollars) |
Vinyl Siding Panels | 1,500 – 1,800 sq ft | $5,460 – $8,190 |
Insulation Board | 1,500 – 1,800 sq ft | $2,730 – $3,640 |
Bricks | 10,000 – 12,000 bricks | $12,740 – $18,200 |
Mortar | 2,500 – 3,000 pounds | $910 – $1,456 |
Vinyl Siding
Vinyl siding is a popular choice due to its durability and low maintenance. It is available in a variety of colors and styles, allowing homeowners to customize the exterior look of their home. Vinyl siding is also resistant to pests and weather damage, making it a long-lasting and cost-effective option.
Vinyl siding panels are installed over insulation boards, which improve the house’s energy efficiency and provide a smooth surface for attaching the siding. Proper installation of vinyl siding includes securing the panels tightly and ensuring they are level to prevent warping and buckling. Investing in high-quality vinyl siding can enhance the home’s appearance and provide lasting protection against the elements.
Brick Siding
Brick siding offers a classic look and requires more materials and labor compared to other siding options. It provides excellent durability and insulation but is also more expensive and time-consuming to install. Brick siding can significantly enhance the home’s aesthetic appeal and resale value.
Brick siding involves laying individual bricks in a pattern, secured with mortar. This process requires skilled labor and attention to detail to ensure a uniform and aesthetically pleasing appearance. The additional weight of brick siding also necessitates a strong foundation and support structure. Properly installed brick siding can last for decades, providing a durable and attractive exterior that requires minimal maintenance.
Windows and Doors
Windows and doors are essential for ventilation, light, and security. They also contribute significantly to the home’s energy efficiency and aesthetic appeal. Choosing the right windows and doors involves considering factors such as insulation, durability, and style. High-quality windows and doors can enhance the home’s comfort, safety, and overall value.
Cost Details for Windows and Doors
The cost of windows and doors can vary widely based on the materials, sizes, and styles chosen. Here’s a breakdown of the average costs for windows and doors:
Component | Estimated Quantity | Estimated Cost (in dollars) |
Windows | 15 – 20 units | $6,300 – $14,000 |
Exterior Doors | 2 – 3 units | $2,100 – $4,200 |
Interior Doors | 10 – 15 units | $2,100 – $6,300 |
Windows
Windows should be energy-efficient, with double or triple glazing to reduce heat loss and improve insulation. Energy-efficient windows help maintain a consistent indoor temperature, reducing heating and cooling costs. They also reduce noise from outside, enhancing the home’s comfort.
Properly installed windows also prevent drafts and water infiltration, which can cause damage to the interior of the home. Additionally, windows contribute to the home’s aesthetic appeal, providing natural light and views while complementing the overall design.
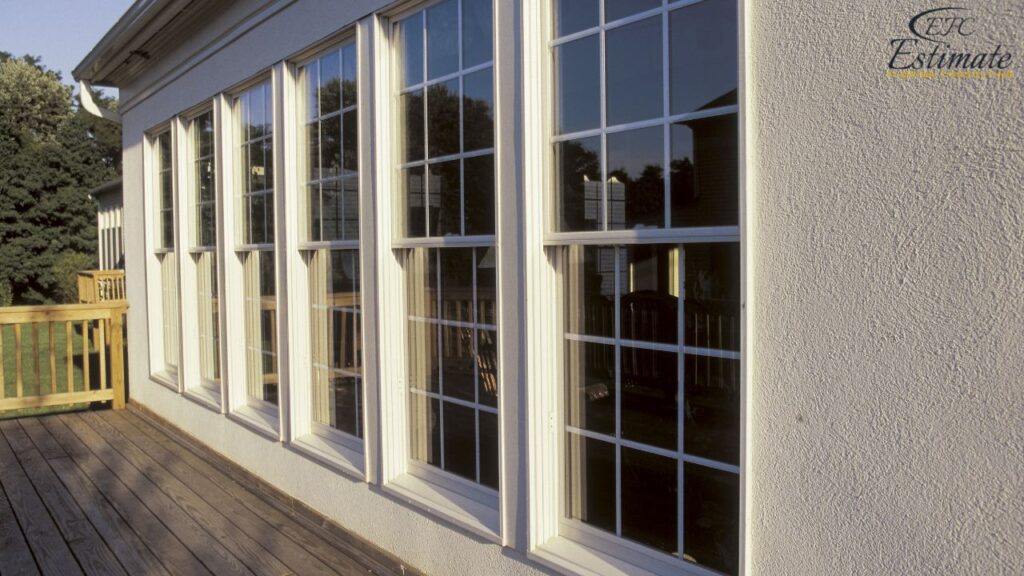
Investing in high-quality windows can improve the home’s energy efficiency and enhance its market value.
Exterior and Interior Doors
Exterior doors need to be sturdy and secure, with proper weatherstripping to prevent drafts. High-quality exterior doors enhance the home’s security and energy efficiency, providing a barrier against the elements and potential intruders.
Interior doors can be lighter but should still provide privacy and sound insulation. Choosing doors that match the home’s interior design can enhance the overall aesthetic appeal. Properly installed doors also contribute to the functionality and comfort of the living spaces, making them an essential component of the home’s design.
Insulation
Insulation is crucial for maintaining the house’s energy efficiency. Proper insulation reduces heating and cooling costs by preventing heat loss in the winter and keeping the house cool in the summer. Effective insulation also improves indoor comfort and helps maintain a consistent temperature throughout the home.
Cost Details for Insulation
The cost of insulation depends on the type of insulation used and the area being insulated. Here’s a breakdown of the average costs for insulation:
Component | Estimated Quantity | Estimated Cost (in dollars) |
Wall Insulation | 1,500 – 1,800 sq ft | $3,510 – $5,400 |
Attic Insulation | 1,500 – 2,000 sq ft | $3,510 – $6,120 |
Floor Insulation | 1,500 sq ft | $2,340 |
Types of Insulation
Different types of insulation, such as fiberglass, foam, or cellulose, can be used depending on the specific requirements and budget. Each type of insulation offers different benefits in terms of thermal performance, installation ease, and cost.
Installing insulation correctly is essential for maximizing its effectiveness and ensuring the home remains comfortable year-round. Proper insulation also helps reduce noise transmission, enhancing the overall comfort and privacy of the living spaces.
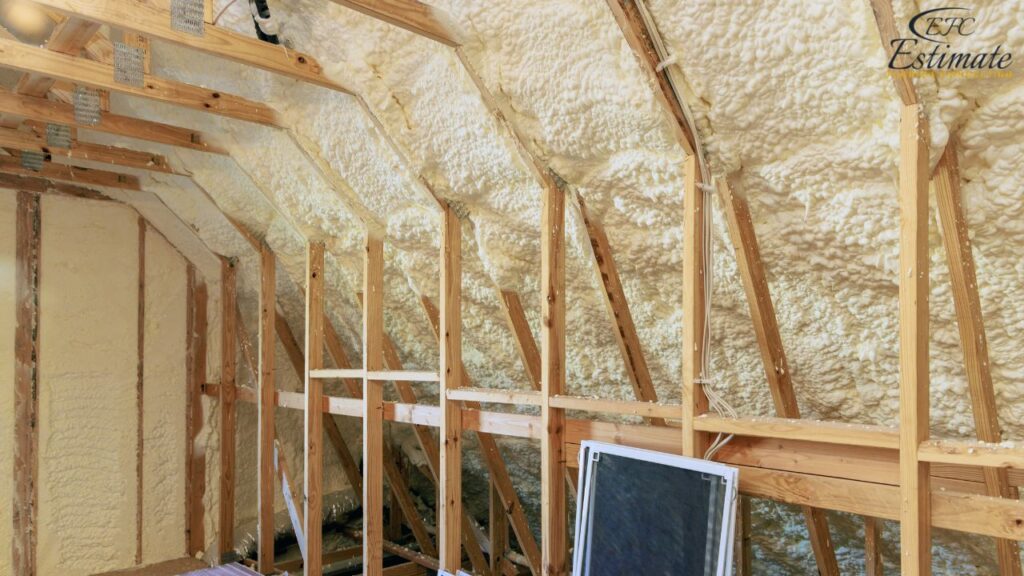
Investing in high-quality insulation materials and professional installation can lead to significant energy savings and improved indoor air quality.
Cost Details for Insulation
The cost of insulation depends on the type of insulation used and the area being insulated. Here’s a breakdown of the average costs for insulation:
Component | Estimated Quantity | Estimated Cost (in dollars) |
Wall Insulation | 1,500 – 1,800 sq ft | $3,510 – $5,400 |
Attic Insulation | 1,500 – 2,000 sq ft | $3,510 – $6,120 |
Floor Insulation | 1,500 sq ft | $2,340 |
Drywall
Drywall is used for constructing interior walls and ceilings. It provides a smooth surface for painting or wallpapering and helps with soundproofing and insulation. Drywall is a versatile material that can be used to create various architectural features and designs, adding to the home’s aesthetic appeal.
Cost Details for Drywall
The cost of drywall installation includes the materials, labor, and finishing. Here’s a breakdown of the average costs for drywall:
Component | Estimated Quantity | Estimated Cost (in dollars) |
Drywall Sheets | 150 – 180 sheets (4×8 ft) | $2,940 – $3,920 |
Joint Compound | 500 – 700 pounds | $700 – $980 |
Drywall Tape | 15 – 20 rolls | $84 – $112 |
Installation Process
Drywall installation involves attaching the sheets to the framing, taping the joints, and applying joint compound to create a smooth, seamless surface. Proper installation is essential for creating a durable and aesthetically pleasing interior finish. High-quality drywall installation can also enhance the home’s fire resistance and improve its overall safety.
Sanding and finishing the drywall ensures a smooth surface ready for painting or other finishes. This process requires skill and attention to detail to achieve a flawless result. Investing in professional drywall installation can lead to a higher-quality finish and reduce the need for future repairs.
Installation Process
Drywall installation involves attaching the sheets to the framing, taping the joints, and applying joint compound to create a smooth, seamless surface. Proper installation is essential for creating a durable and aesthetically pleasing interior finish. High-quality drywall installation can also enhance the home’s fire resistance and improve its overall safety.
Sanding and finishing the drywall ensures a smooth surface ready for painting or other finishes. This process requires skill and attention to detail to achieve a flawless result. Investing in professional drywall installation can lead to a higher-quality finish and reduce the need for future repairs.
Download Template For House Project Breakdown
- Materials list updated to the zip code
- Fast delivery
- Data base of general contractors and sub-contractors
- Local estimators
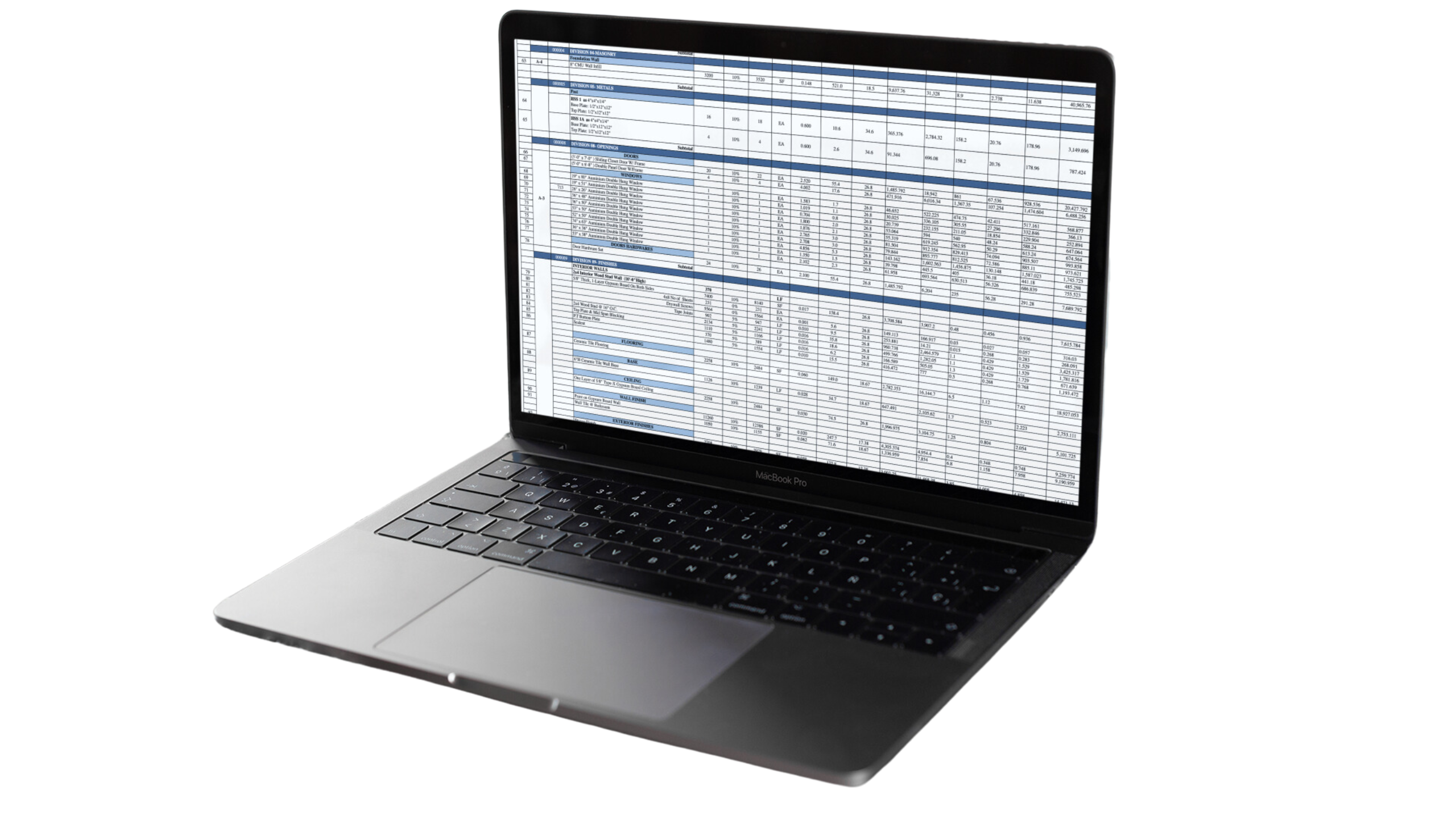
Flooring Materials
Flooring materials depend on the type chosen (hardwood, tile, carpet, etc.). Each type of flooring offers different benefits in terms of durability, maintenance, and appearance. Choosing the right flooring material can enhance the home’s aesthetic appeal and functionality, making it an important aspect of interior design.
Cost Details for Flooring
The cost of flooring materials varies widely based on the type and quality of the flooring chosen. Here’s a breakdown of the average costs for different types of flooring:
Flooring Type | Estimated Cost per Sq Ft (in dollars) | Total Cost for 1,500 Sq Ft (in dollars) |
Hardwood | $14.56 – $31.92 | $21,840 – $47,880 |
Tile | $18.20 – $45.50 | $27,300 – $68,250 |
Carpet | $5.20 – $12.48 | $7,800 – $18,720 |
Vinyl | $6.76 – $15.34 | $10,140 – $23,010 |
Laminate | $7.80 – $17.16 | $11,700 – $25,740 |
Hardwood Flooring
Hardwood flooring is durable and adds value to the home. It requires regular maintenance but offers a timeless and elegant look. Hardwood floors can be refinished multiple times, extending their lifespan and maintaining their appearance.
Component | Estimated Quantity | Estimated Cost (in dollars) |
Hardwood Planks | 1,500 sq ft | $21,840 – $47,880 |
Underlayment | 1,500 sq ft | $2,100 – $3,150 |
Tile Flooring
Tile is often used in kitchens and bathrooms for its durability and ease of cleaning. It comes in various styles and finishes, allowing for a high degree of customization. Tile flooring is also water-resistant, making it ideal for areas prone to moisture.
Component | Estimated Quantity | Estimated Cost (in dollars) |
Tiles | 1,500 sq ft | $27,300 – $68,250 |
Grout | 200 – 300 pounds | $392 – $588 |
Mortar | 500 – 700 pounds | $980 – $1,372 |
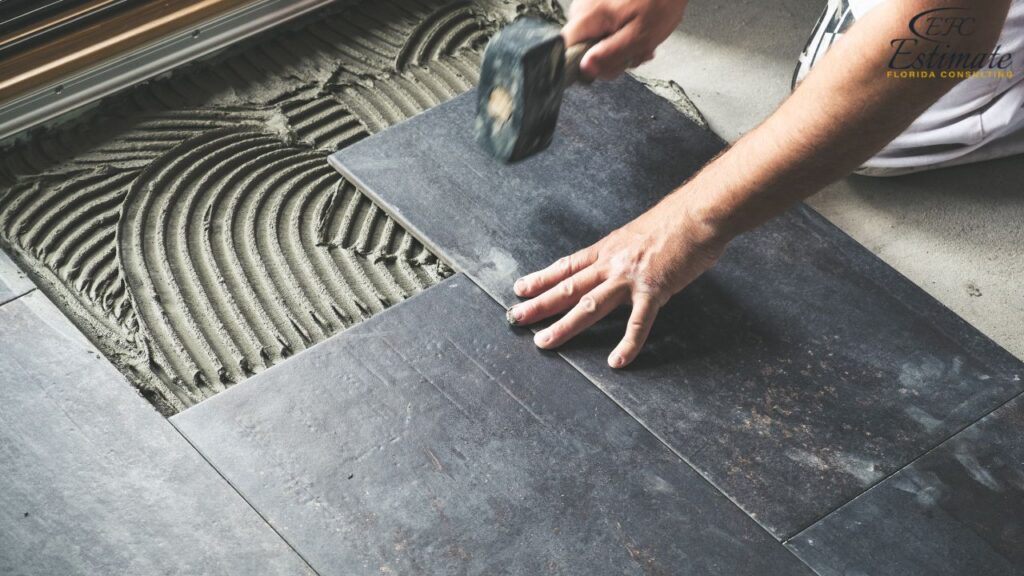
Carpet Flooring
Carpet provides comfort and warmth, making it ideal for bedrooms and living areas. It comes in a variety of colors and textures, allowing homeowners to match their decor. Carpet also provides sound insulation, creating a quieter living environment.
Component | Estimated Quantity | Estimated Cost (in dollars) |
Carpet | 1,500 sq ft | $7,800 – $18,720 |
Padding | 1,500 sq ft | $1,050 – $1,680 |
Vinyl Flooring
Vinyl flooring is versatile, water-resistant, and available in various styles, including planks and tiles. Its affordability and durability make it a popular choice for many homeowners. Vinyl flooring is also easy to install and maintain, making it a practical option for busy households.
Component | Estimated Quantity | Estimated Cost (in dollars) |
Vinyl | 1,500 sq ft | $10,140 – $23,010 |
Underlayment | 1,500 sq ft | $1,050 – $1,680 |
Laminate Flooring
Laminate flooring mimics the appearance of hardwood or stone at a lower cost. It is easy to install and maintain, making it a practical choice for many homeowners. Laminate flooring is also resistant to scratches and stains, making it ideal for households with pets and children.
Component | Estimated Quantity | Estimated Cost (in dollars) |
Laminate | 1,500 sq ft | $11,700 – $25,740 |
Underlayment | 1,500 sq ft | $1,050 – $1,680 |
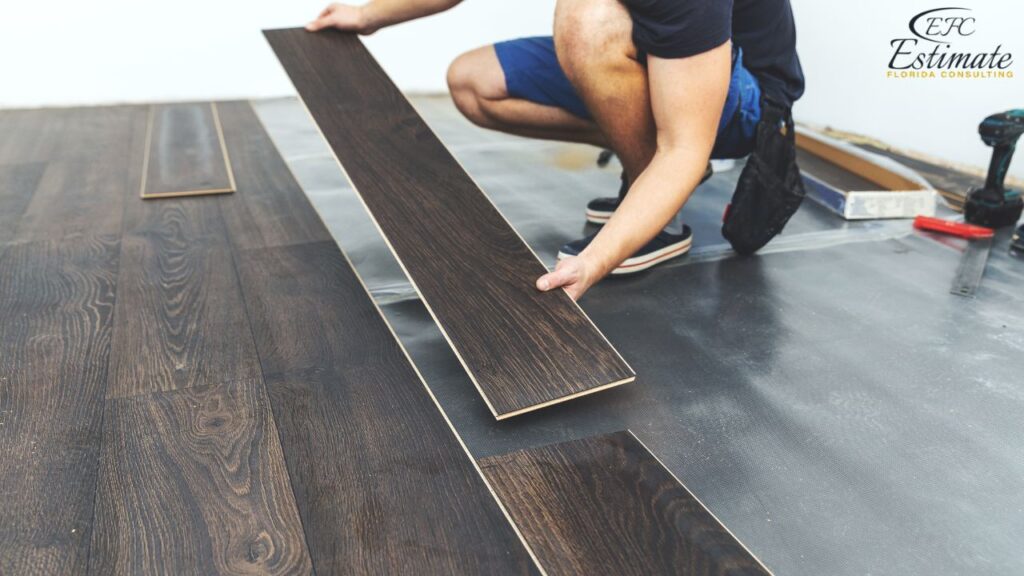
Plumbing Materials
Plumbing includes pipes, fixtures, and fittings. Proper plumbing installation ensures the functionality and safety of the water supply and waste systems. High-quality plumbing materials and professional installation are essential for preventing leaks, clogs, and other issues that can lead to costly repairs.
Cost Details for Plumbing
The cost of plumbing materials depends on the type of pipes and fixtures used. Here’s a breakdown of the average costs for plumbing materials:
Component | Estimated Quantity | Estimated Cost (in dollars) |
PVC Pipes | 500 – 600 feet | $2,548 – $3,276 |
Copper Pipes | 200 – 300 feet | $1,456 – $2,184 |
Fixtures (sinks, toilets) | 8 – 10 units | $7,644 – $11,466 |
Fittings | Varies | $910 – $1,820 |
Types of Plumbing Materials
PVC pipes are commonly used for their affordability and ease of installation. Copper pipes are preferred for their durability and resistance to corrosion. Fixtures such as sinks and toilets vary in price depending on the design and quality.
Proper installation of plumbing systems is essential for ensuring reliable water supply and waste disposal. High-quality fittings and connections help prevent leaks and ensure the system’s longevity. Investing in durable plumbing materials and professional installation can save money on future repairs and maintenance.
Electrical Materials
Electrical systems include wiring, outlets, switches, and the main panel. Proper electrical installation is crucial for safety and functionality. High-quality electrical materials and skilled installation can prevent issues such as short circuits, electrical fires, and power outages.
Cost Details for Electrical
The cost of electrical materials depends on the complexity of the electrical system. Here’s a breakdown of the average costs for electrical materials:
Component | Estimated Quantity | Estimated Cost (in dollars) |
Wiring | 2,000 – 2,500 feet | $3,920 – $4,900 |
Outlets | 50 – 60 units | $1,274 – $2,184 |
Switches | 25 – 30 units | $546 – $764 |
Main Electrical Panel | 1 unit | $1,456 – $2,184 |
Installation Process
Wiring includes running cables throughout the house to connect outlets, switches, and fixtures. The main electrical panel distributes electricity to different circuits. Proper installation ensures safety and compliance with building codes.
Investing in high-quality wiring and electrical components reduces the risk of electrical failures and enhances the system’s efficiency. Professional electricians ensure that all connections are secure and that the system is properly grounded, providing a reliable and safe electrical system for the home.
Painting Materials
Painting materials include primer, paint, and tools. Proper painting techniques enhance the home’s aesthetic appeal and protect surfaces. High-quality paint and professional application can improve the durability and appearance of walls and other surfaces.
Cost Details for Painting
The cost of painting materials depends on the type and quality of paint used. Here’s a breakdown of the average costs for painting materials:
Component | Estimated Quantity | Estimated Cost (in dollars) |
Primer | 15 – 20 gallons | $420 – $560 |
Paint | 30 – 40 gallons | $1,260 – $1,680 |
Brushes and Rollers | Varies | $140 – $280 |
Get 5 New Leads Next 7Days With Our System
- Multi-Family Building
- Hotel Building
- Hospital Building
- Warehouse Building
- High-Rise Building
- Shopping Complex
Painting Process
The painting process includes applying primer to prepare the surface and improve paint adhesion. Multiple coats of paint ensure even coverage and durability. Proper preparation and application are essential for achieving a smooth, long-lasting finish.
Investing in high-quality paint and tools can enhance the appearance and longevity of the painted surfaces. Professional painters ensure that surfaces are properly prepared, and that paint is applied evenly, resulting in a high-quality finish that enhances the home’s aesthetic appeal.
Conclusion
Accurately estimating the materials required for a 1,500 sq ft house is crucial for staying within budget and ensuring timely completion. This guide provides an overview of the essential materials needed for various parts of the house, helping you plan effectively. Each project is unique, and consulting with professionals can help refine these estimates to better suit your specific needs and design preferences. Proper planning and accurate estimation can lead to a successful and stress-free building or renovation project, ensuring that your home is built to last and meets all your expectations. Investing in high-quality materials and skilled labor can enhance the durability, efficiency, and overall value of your home.
FAQs
Accurate material estimation ensures that your project stays on budget and on schedule. It helps avoid unnecessary delays and additional costs, ensuring that every aspect of your home construction or renovation is well-managed. Proper planning and precise material estimation can also prevent wastage and save costs in the long run. By understanding the material needs for each component of the house, you can make informed decisions and ensure a smoother, more efficient construction process.
The foundation materials depend on the type of foundation (slab, crawl space, or basement) and local building codes. Typically, materials include concrete, rebar, gravel, and formwork. The estimated quantities are 25-30 cubic yards of concrete, 1 ton of rebar, 5-10 cubic yards of gravel, and formwork materials. The cost for these materials can range from $8,645 to $11,830, with high-quality materials and skilled labor ensuring a stable and durable foundation.
For a 1,500 sq ft house, approximately 25-30 cubic yards of concrete are required. Concrete provides the necessary strength and durability to support the house and withstand environmental factors. It is crucial to ensure the concrete is mixed and poured correctly to prevent future issues such as settling or cracking.
Formwork shapes the concrete as it sets, and reinforcement materials like rebar provide additional structural support. Proper formwork and reinforcement are essential for the foundation’s ability to bear loads and resist external pressures. These components ensure the foundation’s stability and longevity, contributing to the overall durability of the house.
Framing materials include 2×4 and 2×6 lumber, plywood or OSB sheets, nails, and fasteners. Approximately 12,000-15,000 linear feet of 2×4 lumber, 2,500-3,000 linear feet of 2×6 lumber, 150-200 sheets of plywood/OSB, 50-60 pounds of nails, and various fasteners are needed. The estimated cost for these materials ranges from $24,054 to $29,838.
Lumber forms the skeleton of the house, providing structure and support for the walls, roof, and floors. High-quality lumber ensures the frame is sturdy and can support additional floors and the roof. Treated or high-grade lumber helps prevent issues like warping, rot, and pest infestation, contributing to the house’s long-term stability.
Essential roofing materials include asphalt shingles, underlayment, flashing, ridge caps, and roof vents. The estimated quantities are 45-50 bundles of shingles, 15-18 rolls of underlayment, 100-200 linear feet of flashing, 3-4 bundles of ridge caps, and 6-10 roof vents. The cost for these materials ranges from $5,005 to $7,198.
Shingles provide the primary layer of protection against weather elements, while underlayment adds an extra layer of moisture and wind protection. Proper installation of both components is crucial for preventing leaks and extending the roof’s lifespan. High-quality shingles can also improve the home’s energy efficiency.
Key materials for exterior siding include vinyl siding panels, insulation boards, bricks, and mortar. Approximately 1,500-1,800 sq ft of vinyl siding, 1,500-1,800 sq ft of insulation board, 10,000-12,000 bricks, and 2,500-3,000 pounds of mortar are needed. The cost for these materials ranges from $22,895 to $32,540.
Vinyl siding is durable, low maintenance, and available in various colors and styles. It is resistant to pests and weather damage, making it a long-lasting and cost-effective option. Proper installation over insulation boards improves the house’s energy efficiency and provides a smooth surface for attaching the siding.
Essential materials for windows and doors include energy-efficient windows, exterior doors, and interior doors. Approximately 15-20 windows, 2-3 exterior doors, and 10-15 interior doors are needed. The cost for these materials ranges from $10,500 to $24,500.
High-quality windows and doors enhance energy efficiency, security, and aesthetic appeal. Energy-efficient windows reduce heat loss and noise, while sturdy exterior doors provide security and prevent drafts. Properly installed windows and doors contribute to the home’s overall comfort and value.
Insulation materials include wall insulation, attic insulation, and floor insulation. Approximately 1,500-1,800 sq ft of wall insulation, 1,500-2,000 sq ft of attic insulation, and 1,500 sq ft of floor insulation are needed. The cost for these materials ranges from $9,360 to $13,860.
Insulation reduces heating and cooling costs by preventing heat loss in the winter and keeping the house cool in the summer. It also improves indoor comfort and maintains a consistent temperature throughout the home. Proper insulation helps reduce noise transmission and enhances overall energy efficiency.
Drywall materials include drywall sheets, joint compound, and drywall tape. Approximately 150-180 sheets of drywall, 500-700 pounds of joint compound, and 15-20 rolls of drywall tape are needed. The cost for these materials ranges from $3,724 to $5,012.
Google Reviews
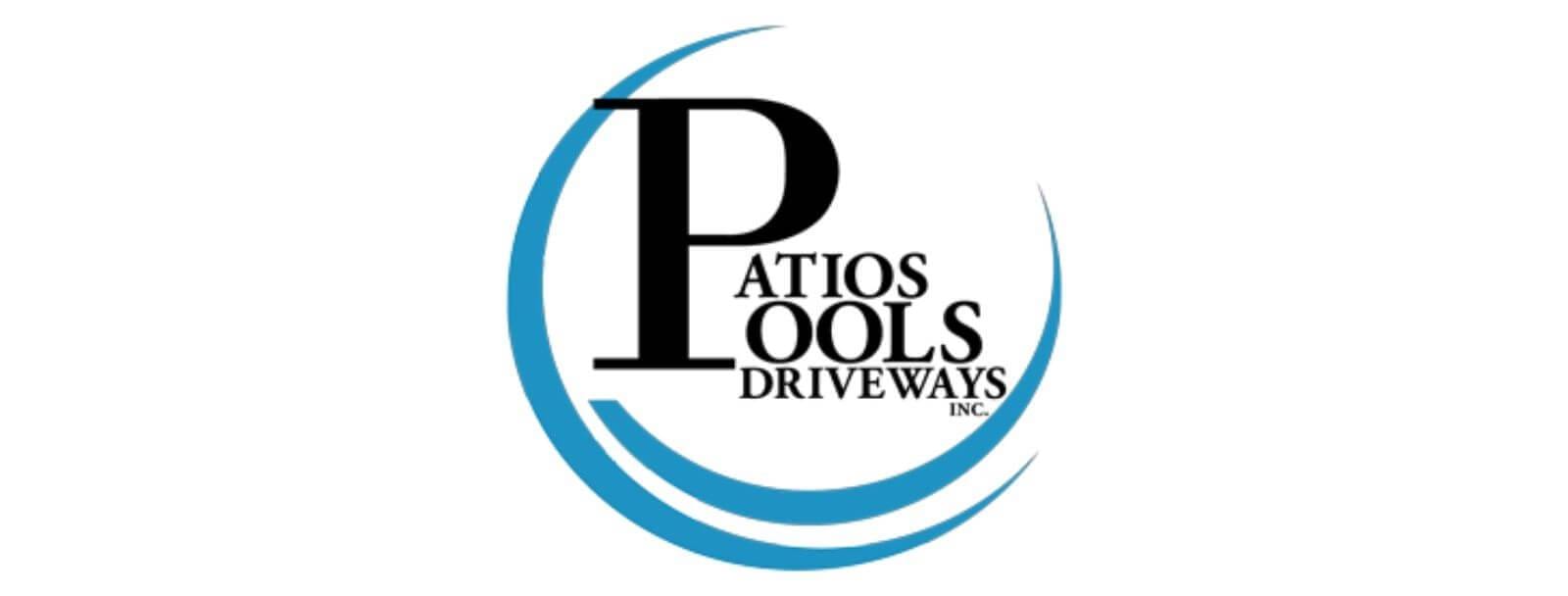
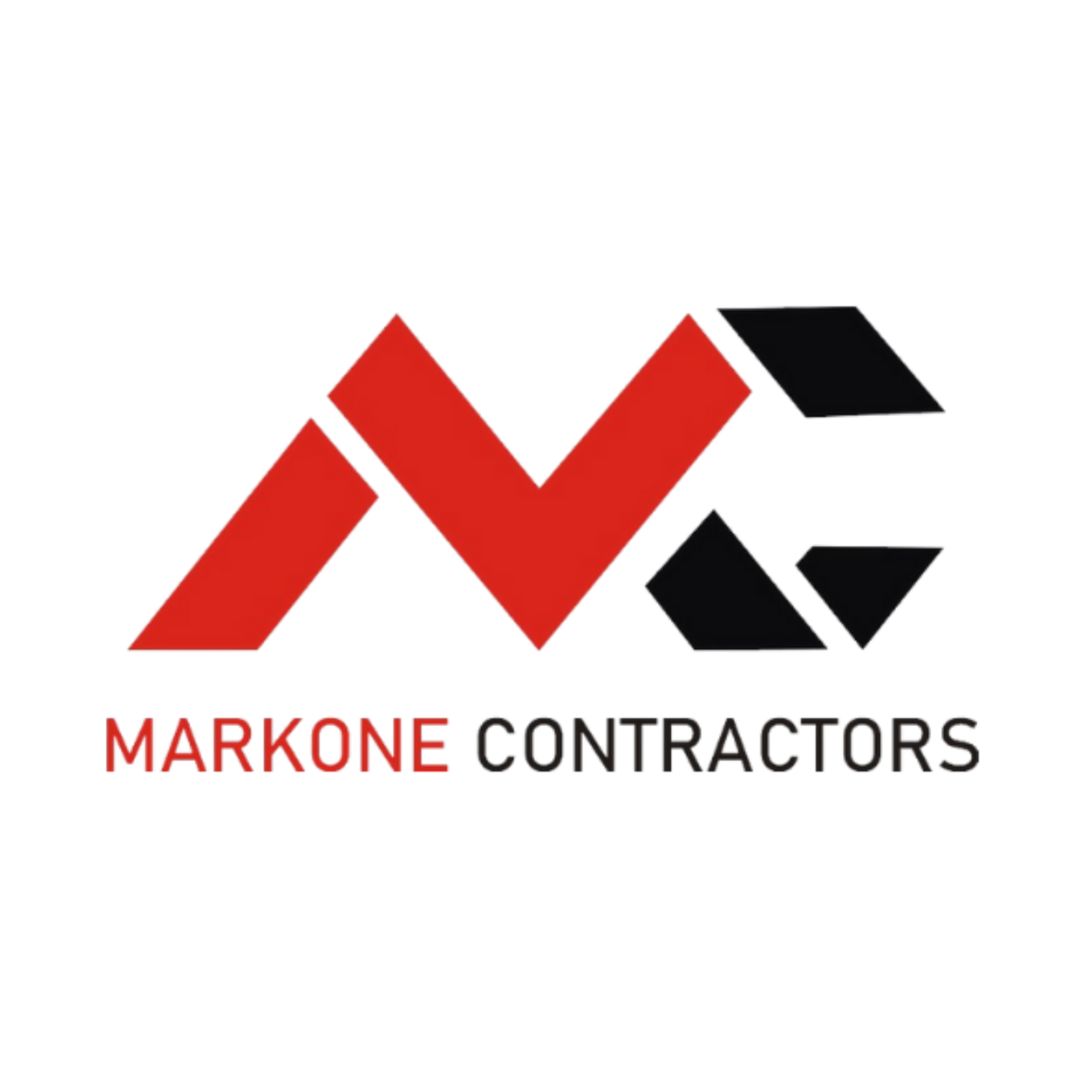

Process To Get House Material Cost Estimate Report
Here I am going to share some steps to get a house material cost estimate report.
-
You need to send your plan to us.
You can send us your plan on info@estimatorflorida.com
-
You receive a quote for your project.
Before starting your project, we send you a quote for your service. That quote will have detailed information about your project. Here you will get information about the size, difficulty, complexity and bid date when determining pricing.
-
Get Estimate Report
Our team will takeoff and estimate your project. When we deliver you’ll receive a PDF and an Excel file of your estimate. We can also offer construction lead generation services for the jobs you’d like to pursue further.