How Much is Concrete Per Yard Right Now?
Concrete is a fundamental building material used in various construction projects, from foundations and driveways to sidewalks and more. If you’re planning a construction project, one of the first questions that might cross your mind is, “How much is concrete per yard right now?” In this article, we’ll delve into the factors that influence concrete pricing and help you understand the current costs associated with this versatile material.
Understanding Concrete Pricing Factors
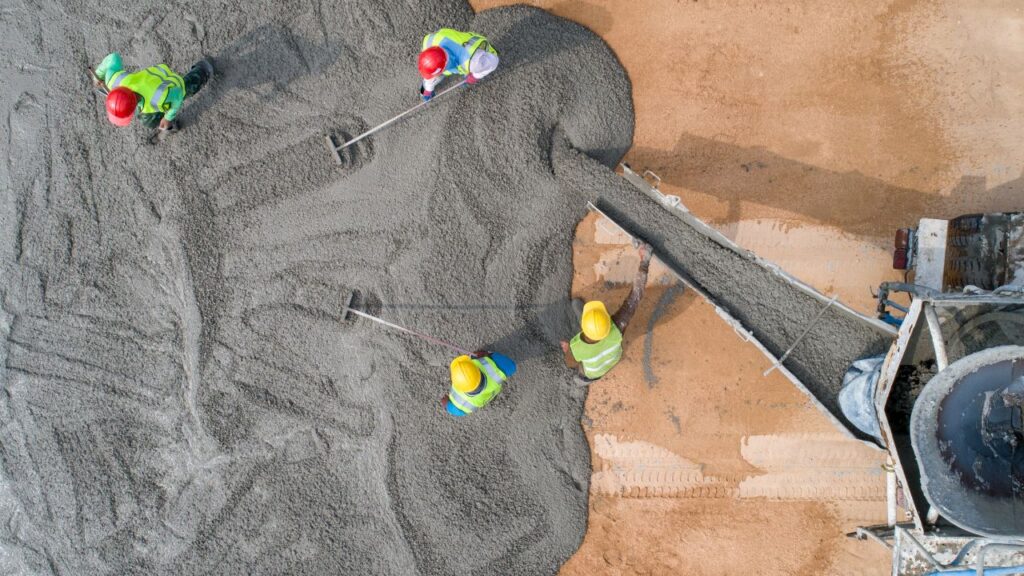
The price of concrete can vary widely based on several factors, including your location, the type of concrete you need, and market fluctuations. To determine how much you’ll pay for concrete, it’s crucial to consider these variables carefully.
Are You Looking For?
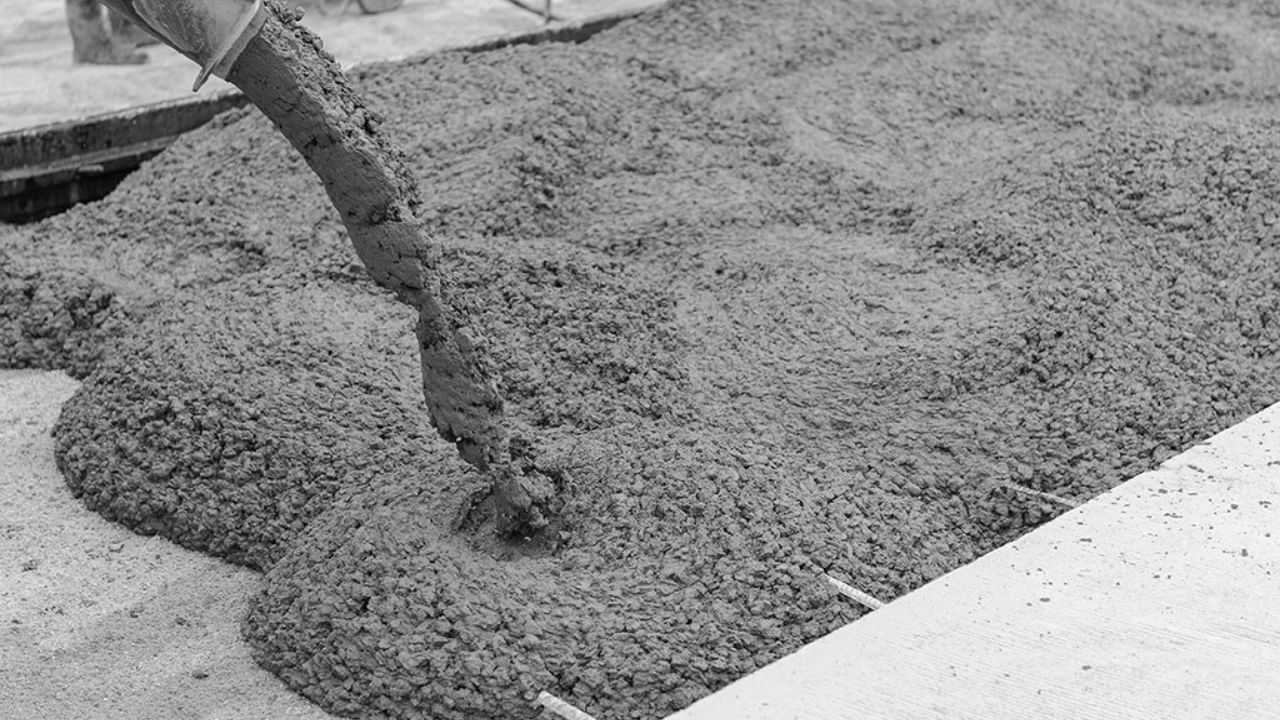
Fully Insured License
Concrete Construction Contractor
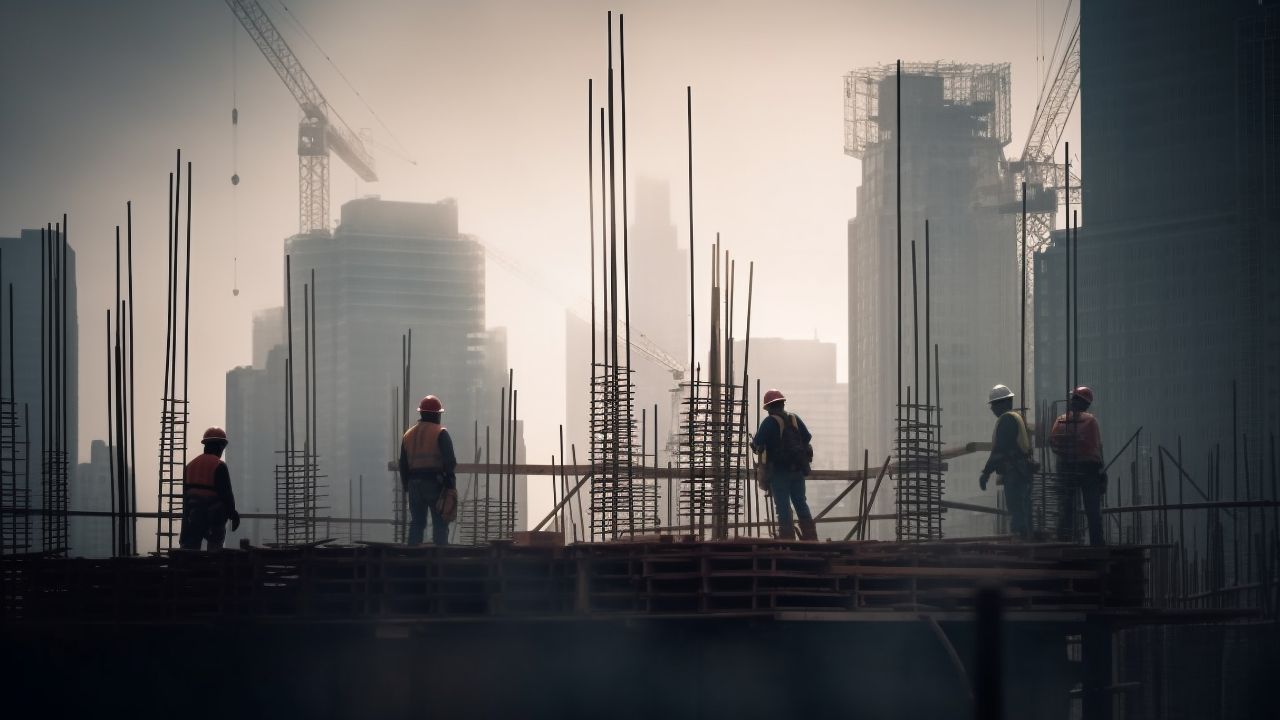
Make Informed Design Decisions Showcase Your Design Ideas
Get RenderingAverage Cost of Concrete Per Yard
On average, the cost of concrete per cubic yard ranges from $120 to $185. Please note that this cost does not include labor charges. It’s essential to understand that the price may vary from one region to another. Local market conditions and supply and demand can significantly impact the price you pay for concrete.
Factors Affecting Concrete Prices
Several factors contribute to the fluctuations in concrete prices. These factors include:
Location
Prices can differ based on your geographical location and proximity to concrete suppliers. In metropolitan areas, concrete may be pricier due to higher demand and increased operating costs. In rural areas, prices might be lower due to lower overhead expenses.
Concrete Mix
The type of concrete mix you require can significantly impact pricing. Standard concrete mixes are generally more affordable, while specialty mixes designed for specific applications might be more expensive. The price range for concrete mix can vary from $75 to $150 per cubic yard, with specialty mixes at the higher end of the range.
Order Volume
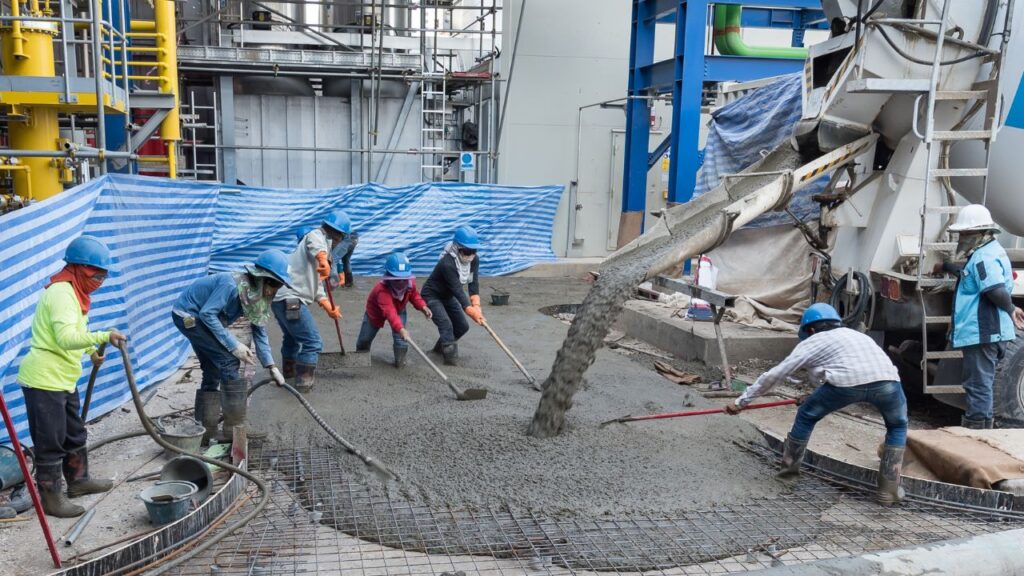
Ordering in larger quantities can often result in a lower cost per yard. For larger projects, it’s advisable to buy in bulk to save on costs. Bulk purchases may offer savings of around $10 to $20 per cubic yard, which can add up significantly for extensive projects.
Delivery Distance
If the concrete supplier needs to travel a considerable distance to deliver the concrete, it may impact the price due to transportation expenses. Choosing a local supplier can help reduce this cost. Delivery fees can range from $60 to $200 or more, depending on the distance, and can represent a notable portion of your overall expenses.
Market Conditions
Like any other commodity, concrete prices can be influenced by market dynamics and economic conditions. Prices may rise during times of high demand, such as during the construction season. Market-driven price fluctuations can lead to variations of $10 to $30 per cubic yard or more, and these fluctuations can happen rather quickly.
Calculating the Cost of Concrete for Your Project
To estimate the cost of concrete for your project, you need to determine the volume of concrete you require. This is typically measured in cubic yards. You can use online calculators or seek assistance from a concrete supplier to determine the exact amount you’ll need. Remember that overordering can lead to unnecessary expenses, so accurate calculations are crucial to avoid waste and additional costs.
Additional Costs Involved
In addition to the cost of concrete per yard, you should consider other expenses that may be part of your project, such as:
- Labor costs for pouring and finishing the concrete, which can range from $10 to $25 per square foot. Highly specialized finishes may cost even more. For example, for a 500 square foot project, labor costs can add $5,000 to $12,500 to your overall expenses.
- Rental fees for equipment like concrete mixers or pumps, especially if you’re taking the DIY approach. Equipment rental can vary from $150 to $500 per day or more, depending on the equipment type and duration of use. Renting equipment can be a significant cost, particularly for smaller projects where the cost of equipment rental might be proportionally higher.
- Any necessary permits and inspections, which can vary based on your location and project requirements. Permit costs can range from $100 to $1,000 or more, depending on the complexity of your project and local regulations, while inspection fees may be around $200 to $500. Failing to account for permits and inspections in your budget can lead to unforeseen costs and project delays.
Hire a Commercial Concrete Contractor
We provide commercial concrete estimating services for small and big construction projects. We analyze the costs of commercial concrete works like sidewalks, driveways, office buildings, hospitals, restaurants, government office, curbs, basement, etc.
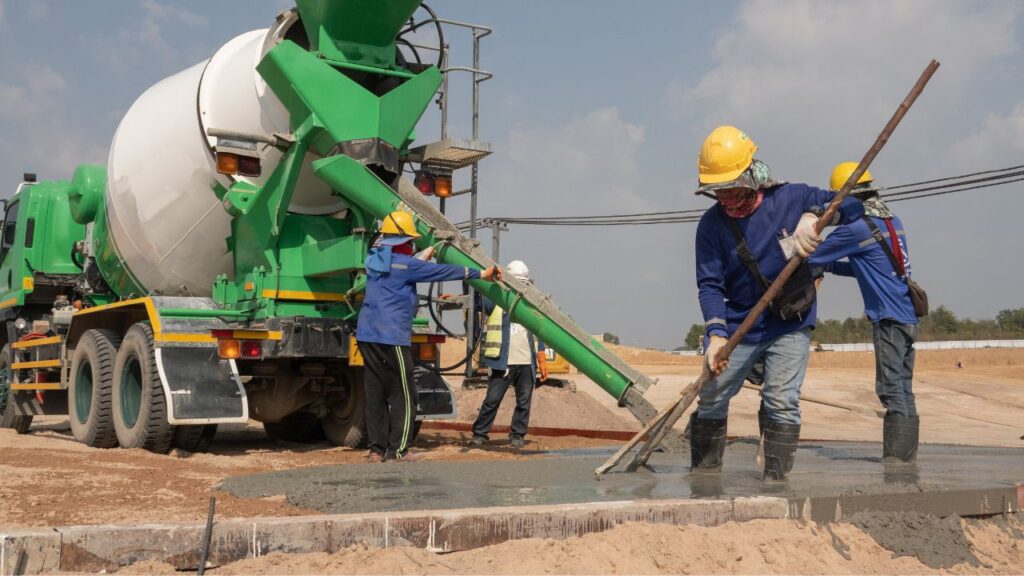
Ways to Save on Concrete Costs
If you’re working with a tight budget, there are strategies to help you save on concrete costs:
- Opt for a standard concrete mix rather than specialty mixes unless your project requires a specific blend. Standard mixes are more readily available and affordable, helping you avoid higher material costs.
- Combine multiple small projects into a single large pour to reduce costs and minimize labor charges. A larger single pour can be more cost-effective in terms of labor, and you can also benefit from bulk purchasing of concrete, further lowering material costs.
- Plan your project during a time of the year when concrete demand is lower. Fall and winter are typically less busy seasons for contractors, potentially resulting in cost savings. Contractors are often more willing to negotiate lower prices during these times, and concrete suppliers may offer discounts to encourage business during their offseason.
Best Time to Purchase Concrete
Concrete prices can fluctuate throughout the year. It’s often more cost-effective to purchase concrete during the off-season when demand is lower. Spring and summer are typically the peak periods for concrete projects, and prices may be higher due to increased demand. Planning your project during the off-peak season can save you money. Additionally, planning your project well in advance and ordering concrete early can help you secure more favorable prices.
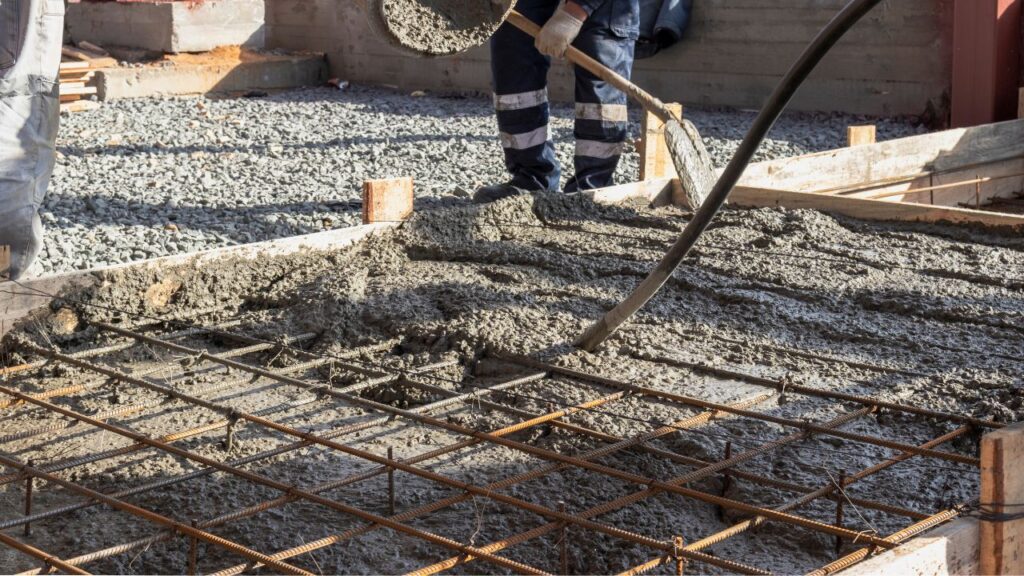
Quality vs. Cost: Making the Right Choice
While it’s essential to consider cost when planning a project, it’s equally crucial to prioritize quality. Investing in high-quality concrete can lead to a more durable and long-lasting end product, potentially saving you money in the long run. Lower-quality concrete may result in quicker wear and tear, leading to costly repairs and replacements. It’s important to balance your budget constraints with the long-term value of a quality project to make the right choice for your specific needs.
Hiring a Professional vs. DIY
Deciding whether to hire a professional contractor or take the DIY approach depends on your skills and the scale of your project. Professionals bring expertise and efficiency to the table, ensuring that the concrete is mixed and poured correctly. However, if you have experience and are confident in your abilities, a DIY project can be more cost-effective. Keep in mind that larger, more complex projects may be best left to the professionals, as they have the knowledge and equipment needed to handle significant undertakings. Smaller projects, on the other hand, can often be successfully tackled by homeowners who are experienced in concrete work.
Conclusion
The cost of concrete per yard is influenced by various factors, including location, concrete mix, market conditions, and project scale. To get an accurate estimate, consult with local suppliers and consider the specific needs of your project. By making informed decisions, exploring cost-saving options, and balancing cost and quality, you can effectively manage your project and stay within budget, ensuring that your construction project is both cost-efficient and successful.
FAQs
To calculate the volume in cubic yards, multiply the length, width, and depth of the area you want to pour concrete into. Online calculators can assist you in this process.
Yes, besides the cost of concrete, you should budget for labor, equipment rental, permits, and inspections. These costs can vary depending on the size and complexity of your project.
Purchasing concrete during the off-season, typically in fall or winter, can often result in cost savings. During peak construction seasons, prices may be higher due to increased demand.
It’s essential to strike a balance between cost and quality. While cost is crucial, investing in high-quality concrete can lead to a more durable and long-lasting end product, potentially saving you money in the long run.
The decision depends on your skills and the project’s scale. Smaller, simpler projects may be suitable for a DIY approach, while larger or more complex projects may benefit from the expertise of a professional concrete contractor.
Process To Get Concrete Per Yard Cost Estimate Report
Here I am going to share some steps to get a concrete per yard cost estimate report.
-
You need to send your plan to us.
You can send us your plan on info@estimatorflorida.com
-
You receive a quote for your project.
Before starting your project, we send you a quote for your service. That quote will have detailed information about your project. Here you will get information about the size, difficulty, complexity and bid date when determining pricing.
-
Get Estimate Report
We do concrete per yard cost estimating and prepare a detailed report for your project. At last you finalize the report and finish the project.
Google Reviews
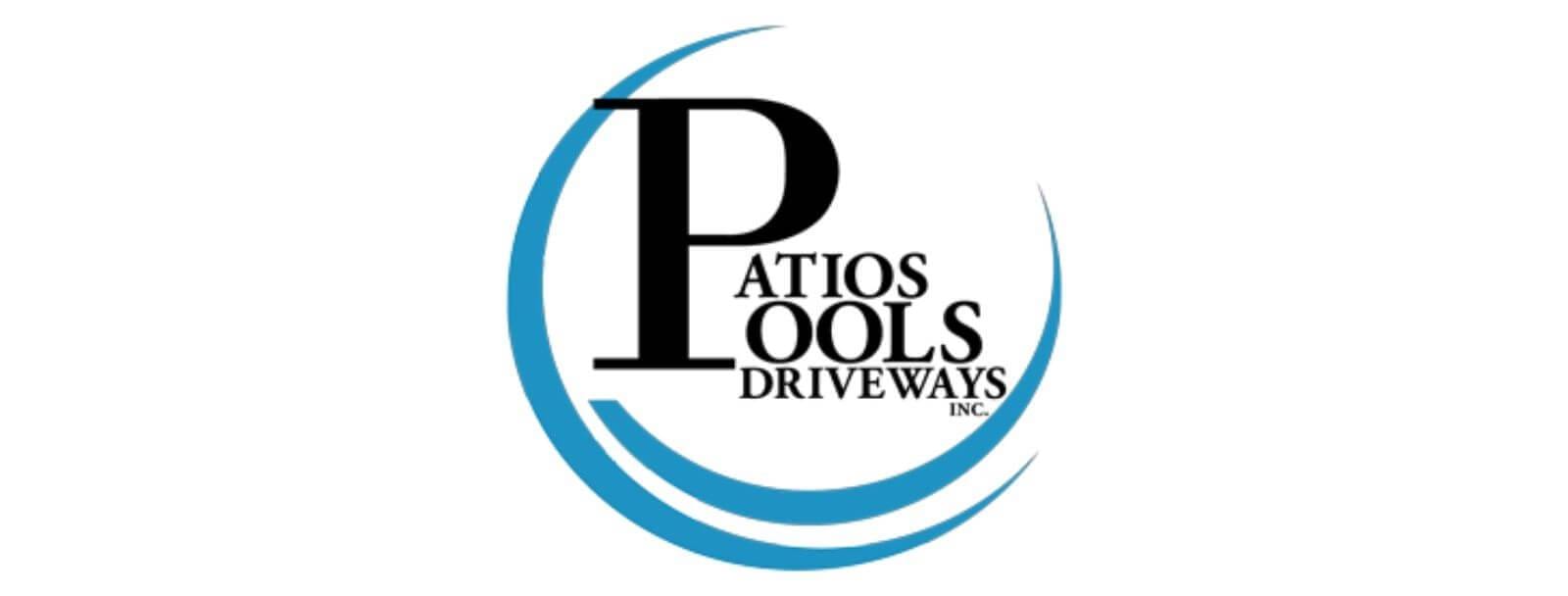
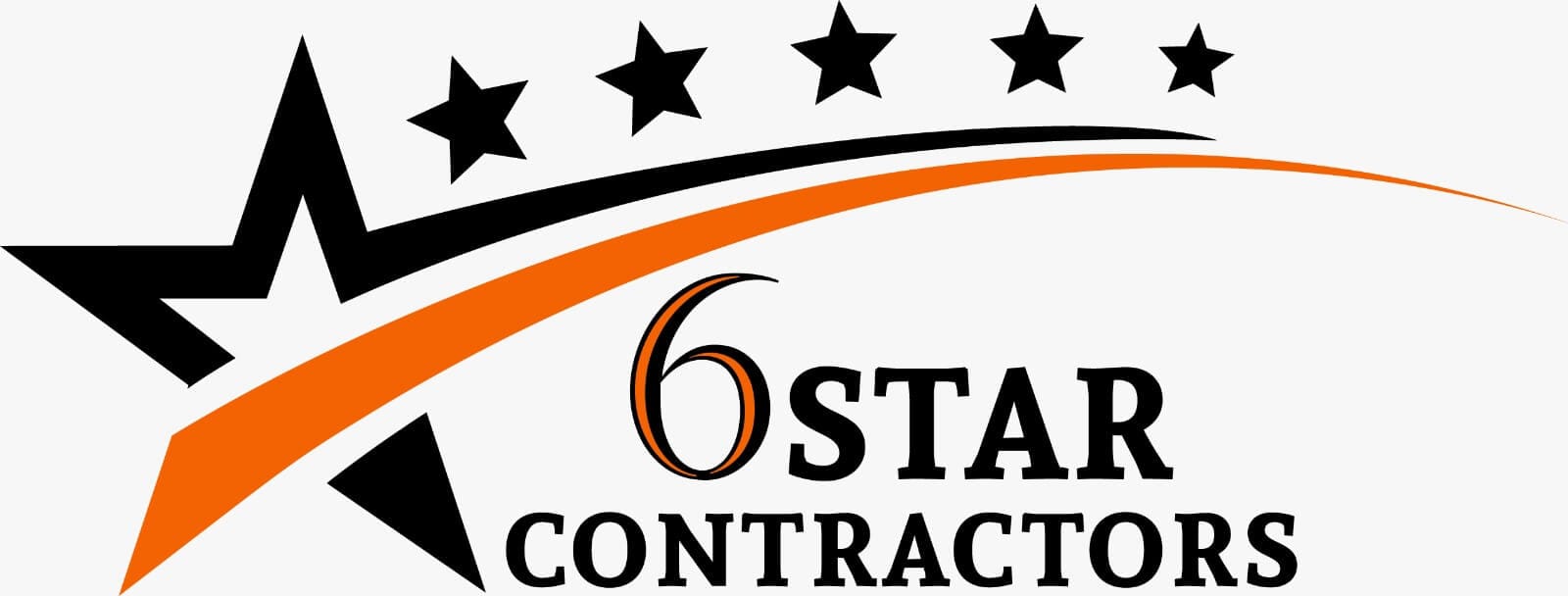
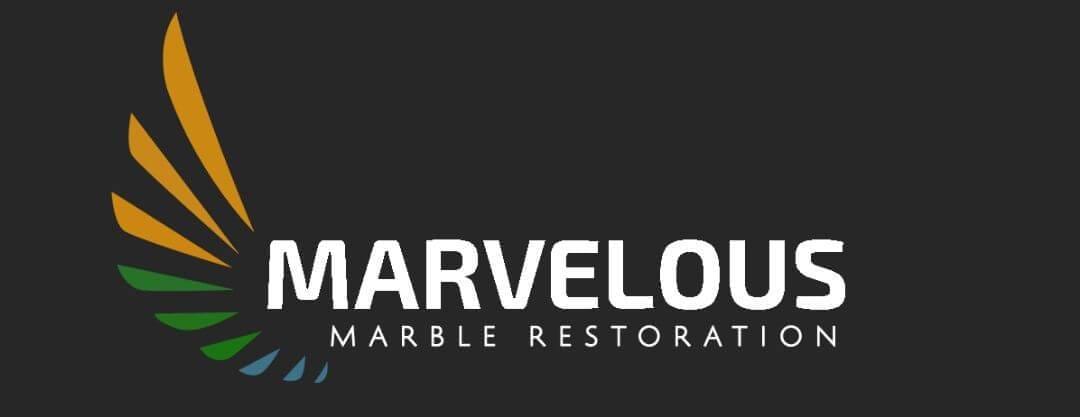