- Homepage
- How Much is a 10-Yard Truck of Concrete?
How Much is a 10-Yard Truck of Concrete?
Leading provider of concrete construction services.
A 10-yard truck of concrete typically costs between $1,560 and $2,600, averaging $156 to $260 per cubic yard. This estimate includes the price of the concrete mix and standard delivery fees. Costs can vary based on the type of concrete, such as standard, reinforced, or high-strength mixes, and additional services like pumping or small load fees. Factors such as distance from the supplier and local market rates also influence the total price. Proper planning and obtaining multiple quotes can help ensure you get the best value for your concrete delivery needs. Investing in quality concrete ensures durability and optimal performance for your project.
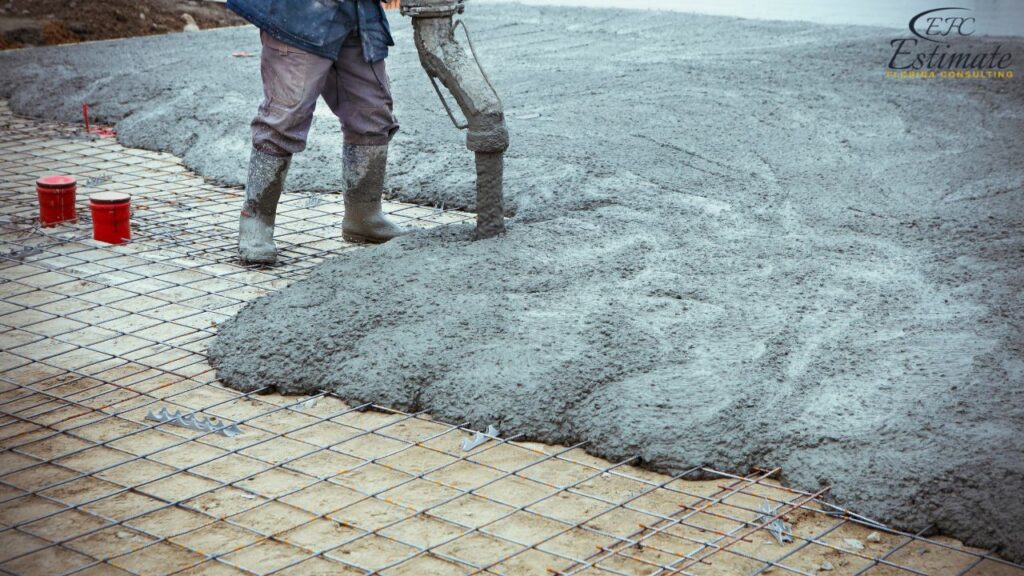
Key Factors Influencing Concrete Costs
The cost of repairing a crawl space can vary based on several key factors. Understanding these factors can help you estimate where your project might fall within the typical price range.
Quality and Type of Concrete
The quality and type of concrete required for a project can significantly influence the cost. Standard concrete mixes for general use are typically less expensive than specialized mixes designed for specific applications such as high-strength or fast-setting concrete. The inclusion of additives like fibers, colorants, and admixtures to improve performance can also increase the price. The choice of concrete type should align with the project’s specific requirements to ensure optimal performance and durability. Additionally, using the right type of concrete can reduce maintenance costs and extend the lifespan of the structure, providing long-term savings. Understanding the specific needs of your project can help you select the most appropriate and cost-effective concrete mix.
Cost Breakdown by Concrete Type
Different types of concrete serve various purposes, and their costs reflect their unique properties and intended uses. Standard concrete is ideal for most residential projects, while high-strength concrete is necessary for structures that must withstand heavy loads or adverse conditions. Specialty concretes, which include additives for enhanced performance or aesthetics, cater to specific needs such as rapid setting, increased durability, or decorative finishes. Selecting the right type of concrete not only affects the initial cost but also the longevity and maintenance costs of the project.
Type of Concrete | Cost per Cubic Yard | Cost for 10 Yards |
Standard Concrete | $120 – $144 | $1,200 – $1,440 |
High-Strength Concrete | $180 – $204 | $1,800 – $2,040 |
Specialty Concrete | $240+ | $2,400+ |
Delivery Fees
Delivery fees are a crucial component of the overall cost when ordering concrete. These fees can vary based on the distance from the concrete plant to the construction site, the accessibility of the site, and any specific delivery requirements such as multiple trips or timed deliveries. Understanding these fees is essential for accurate budget planning and avoiding unexpected expenses. Properly planning the delivery can also help ensure that the concrete arrives at the right time and is poured under optimal conditions, reducing the risk of delays and additional costs. Being aware of potential extra charges for difficult deliveries or long distances can help in negotiating better terms with the supplier.
Delivery Fee Breakdown
Delivery fees can fluctuate based on logistical considerations and the specific needs of the project. For instance, delivering to a remote or hard-to-access location might incur higher costs due to the increased time and effort required. Additionally, scheduling deliveries during peak traffic hours or requiring specialized equipment can further drive up the costs. It’s important to communicate clearly with the supplier about the delivery details to get an accurate estimate. Planning the delivery during off-peak hours or ensuring easy site access can help reduce these fees.
Delivery Distance | Delivery Fee | Total Delivery Cost for 10 Yards |
Local Deliveries | $72 – $120 | $72 – $120 |
Long-Distance Deliveries | $120 – $240 | $120 – $240 |
Local Market Conditions
Local market conditions, including the demand for concrete and the availability of materials, can affect prices. Regions with high construction activity might experience higher prices due to increased demand. Conversely, areas with lower demand might offer more competitive pricing. Being aware of these conditions can help in negotiating better deals and planning purchases accordingly. Seasonal fluctuations can also impact prices, with higher costs often seen during peak construction seasons. Monitoring these trends can help in timing purchases to take advantage of lower prices. Understanding the local market can also help in identifying reliable suppliers who offer competitive rates and quality service.
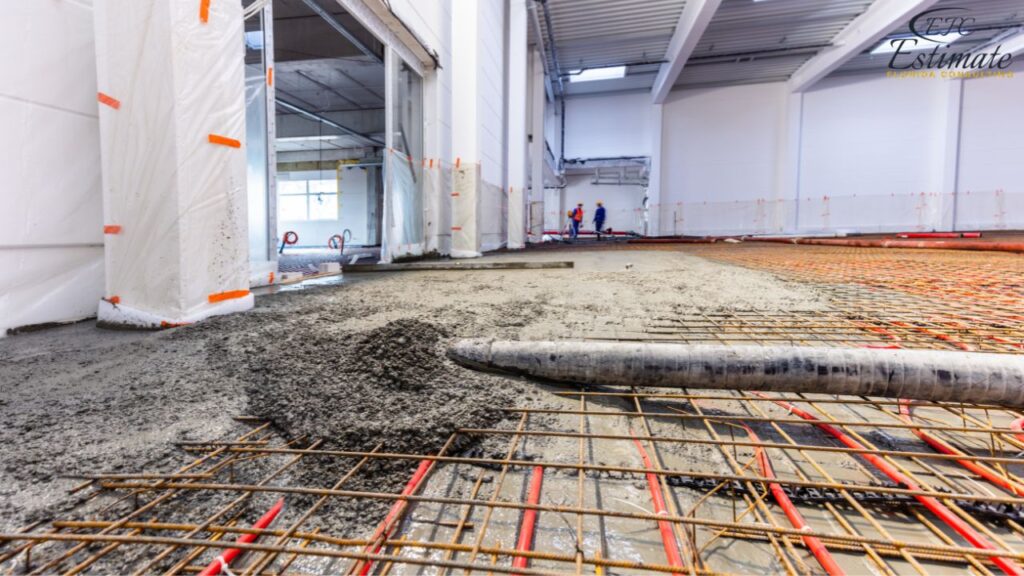
Impact of Market Conditions
Market conditions can significantly influence the cost of concrete. In booming construction areas, the high demand for materials can lead to price increases as suppliers adjust to market dynamics. Conversely, in areas with less construction activity, suppliers might offer discounts or promotional rates to attract business. Understanding these trends allows for strategic planning and potential cost savings. Knowing the right time to buy can result in significant savings and ensure the project stays within budget.
Market Condition | Price Adjustment | Adjusted Cost for 10 Yards |
High-Demand Areas | +12% – 24% | +$120 – $480 |
Low-Demand Areas | -6% – 18% | -$60 – $180 |
Additional Costs
Additional costs such as labor for pouring and finishing, equipment rental, and site preparation can also impact the overall expense of a concrete project. These costs need to be factored into the total budget to avoid any shortfalls. Properly accounting for these expenses ensures that the project is fully funded and can proceed without financial interruptions. Moreover, considering all potential costs upfront can help in securing adequate financing and managing cash flow throughout the project. Anticipating additional costs and planning accordingly can prevent budget overruns and project delays.
90% More Chances to Win Concrete Bids with Our Estimate
Breakdown of Additional Costs
These additional costs encompass various aspects of the construction process. Labor costs can vary based on the complexity of the job and local wage rates. Equipment rental, such as for concrete pumps or mixers, is necessary for efficient and timely project completion. Site preparation costs can include clearing, grading, and installing forms, which are essential for ensuring a stable and level base for the concrete pour. Properly planning for these costs can help avoid surprises and keep the project on track.
Cost Component | Estimated Cost per Unit | Total Cost for 10 Yards |
Labor (per hour) | $60 – $120 | $600 – $1,200 |
Equipment Rental | $240 – $600 | $240 – $600 |
Site Preparation | $1,200 – $2,400 | $1,200 – $2,400 |
Additives | $12 – $60 per yard | $120 – $600 |
Ordering the Right Amount of Concrete
It is crucial to order the correct amount of concrete for your project. Ordering too little can cause delays and additional delivery fees, while ordering too much can result in wasted material. Consulting with a concrete supplier or a construction professional can help determine the exact amount needed for your specific project. Accurate calculations and considerations for potential waste are essential for efficient project execution. Proper planning and measurement can save money and prevent project delays, ensuring that the construction proceeds smoothly and on schedule. Ensuring accurate calculations can also help in optimizing resources and reducing overall project costs.
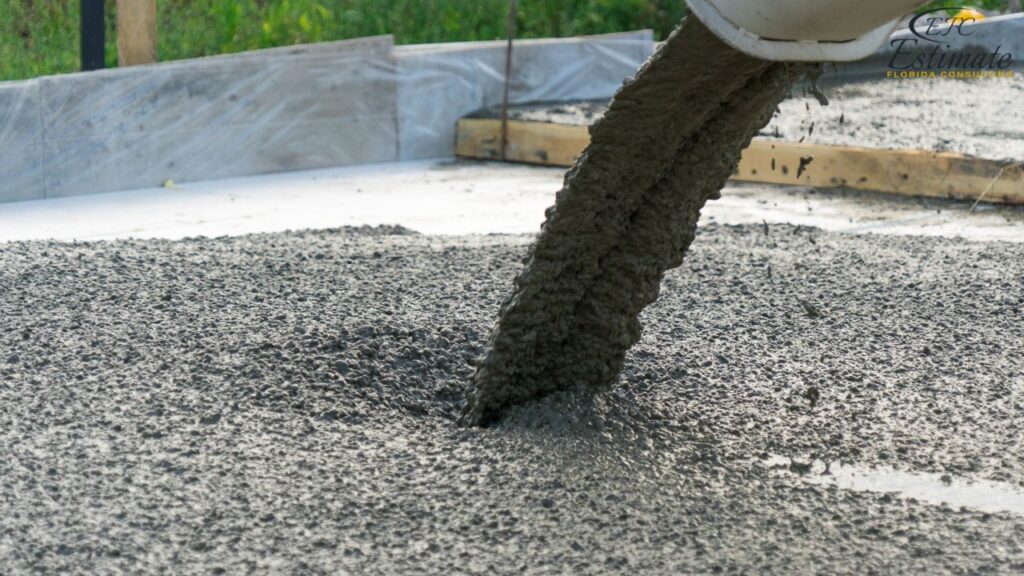
Calculating Concrete Volume
Calculating the volume of concrete needed involves measuring the length, width, and depth of the area to be filled. This is usually done in cubic yards. Accurate measurements ensure that the correct amount of concrete is ordered, preventing shortages or excess. Utilizing tools such as volume calculators or consulting with professionals can enhance accuracy and efficiency in determining the required amount of concrete. Proper calculation methods can prevent the risk of ordering too much or too little concrete, which can impact project timelines and costs.
Example Calculation
To illustrate the process of calculating concrete volume, consider a simple example where you need to pour a concrete slab for a driveway. The dimensions of the slab are essential in determining the total volume of concrete required. This example shows how accurate measurements can help in ordering the right amount of concrete, minimizing waste and ensuring cost-effectiveness.
Dimension | Measurement (feet) | Calculation |
Length | 30 | |
Width | 10 | |
Depth | 0.33 (4 inches) | |
Volume (cubic yards) | (30 x 10 x 0.33) / 27 = 3.67 |
Adjusting for Waste
It’s advisable to order slightly more concrete than calculated to account for waste, spillage, or variations in project specifications. Typically, adding an extra 5-10% to the calculated amount is recommended. This adjustment ensures that the project can continue smoothly without interruptions due to material shortages. Allowing for a margin of error in the calculations provides a buffer that accommodates unexpected changes or mishaps during the pour. Including this contingency in the order helps prevent project delays and additional costs associated with last-minute orders.
Calculated Volume | Waste Adjustment (10%) | Total Volume to Order |
3.67 cubic yards | 0.37 cubic yards | 4.04 cubic yards |
Site Preparation for Concrete Pouring
Proper site preparation is essential for a successful concrete pour. This includes leveling the ground, installing forms, and ensuring proper drainage. Failing to prepare the site adequately can lead to issues such as uneven surfaces, cracking, and poor durability. Thorough site preparation ensures a strong and durable finished product. Investing time and resources in this phase can prevent costly repairs and enhance the overall quality of the construction. Proper site preparation also contributes to the longevity and stability of the concrete structure.
We Provide 3D Rendering Services!
For Construction Building and Other Projects
Turnaround time is 1-2 days.
Win More Projects With Us
Leveling and Grading
Leveling and grading the site ensures a smooth and even surface for the concrete pour. This can involve removing debris, compacting soil, and creating a stable base. Proper leveling and grading are crucial for the structural integrity and longevity of the concrete surface. A well-prepared base supports the concrete and prevents settlement or shifting, which can cause cracks and damage over time. Ensuring the ground is properly leveled and graded can also improve the aesthetic appeal and functionality of the finished surface.
Leveling and Grading Costs
The costs associated with leveling and grading depend on the size and condition of the site. Removing debris might involve hauling away large amounts of soil or rocks, while soil compaction requires specialized equipment. Base preparation includes adding a layer of gravel or sand to provide a stable foundation for the concrete. Properly budgeting for these tasks ensures that the site is ready for the concrete pour, reducing the risk of issues during and after the project.
Task | Estimated Cost | Total Cost for 10 Yards |
Debris Removal | $240 – $600 | $240 – $600 |
Soil Compaction | $120 – $360 | $120 – $360 |
Base Preparation | $360 – $840 | $360 – $840 |
Installing Forms
Forms are used to contain the concrete and shape it as it cures. They must be securely installed and properly aligned to ensure accurate results. The quality and precision of form installation affect the final appearance and structural soundness of the concrete. Properly installed forms prevent the concrete from spreading beyond the desired boundaries and help achieve the intended shape and finish. Ensuring the forms are level and secure is essential for a successful pour.
Cost of Installing Forms
The cost of installing forms depends on the complexity and size of the project. Simple projects might only require basic wooden forms, while more complex designs might need metal or custom-built forms. Ensuring the forms are level and secure is essential for a successful pour. Properly installed forms help maintain the concrete’s shape during curing, resulting in a smoother and more durable surface.
Task | Estimated Cost | Total Cost for 10 Yards |
Form Installation | $1.20 – $2.40 per linear foot | $120 – $240 |
Ensuring Proper Drainage
Proper drainage is critical to prevent water accumulation, which can weaken the concrete and cause damage over time. This may involve installing drainage pipes or creating slopes to direct water away from the concrete. Good drainage systems extend the life of concrete surfaces by preventing water damage. Adequate drainage helps maintain the structural integrity of the concrete and prevents issues such as erosion, mold growth, and foundation problems. Proper drainage planning can also reduce the need for costly repairs and maintenance.
Drainage Installation Costs
The cost of installing drainage systems varies based on the complexity of the project and the specific requirements. Simple projects might only need basic drainage pipes, while more complex installations might require extensive trenching or the addition of sump pumps. Properly budgeting for drainage installation can help ensure that the concrete remains strong and durable over time.
Task | Estimated Cost | Total Cost for 10 Yards |
Drainage Pipes | $120 – $360 | $120 – $360 |
Slope Creation | $240 – $480 | $240 – $480 |
Timing and Weather Considerations
The timing of the concrete pour and weather conditions can also impact the success of the project. Pouring concrete in extreme temperatures, either hot or cold, can affect the curing process and the final strength of the concrete. Proper planning for weather conditions ensures the best possible outcome for the concrete pour. Monitoring weather forecasts and choosing the right time for the pour can prevent issues related to temperature extremes, ensuring the concrete cures properly. Choosing the optimal time for pouring concrete can prevent issues related to extreme temperatures and improve the overall quality of the finished product.
Ideal Pouring Conditions
The ideal temperature for pouring concrete is between 50°F and 60°F. Pouring in these conditions helps ensure that the concrete cures properly and achieves maximum strength. Choosing the optimal time for pouring concrete can prevent issues related to extreme temperatures and improve the overall quality of the finished product. Proper curing in the right conditions enhances the concrete’s strength, durability, and resistance to environmental factors. Ensuring the right curing conditions can also prevent defects and reduce long-term maintenance costs.
Precautions for Hot Weather
In hot weather, it’s important to keep the concrete cool and hydrated. This can involve using ice water in the mix, shading the area, and applying curing compounds to retain moisture. These precautions help prevent rapid drying and potential cracking of the concrete. Keeping the concrete at the right temperature during curing is essential for achieving optimal strength and durability. Ensuring proper hydration and temperature control can prevent defects and prolong the lifespan of the concrete.
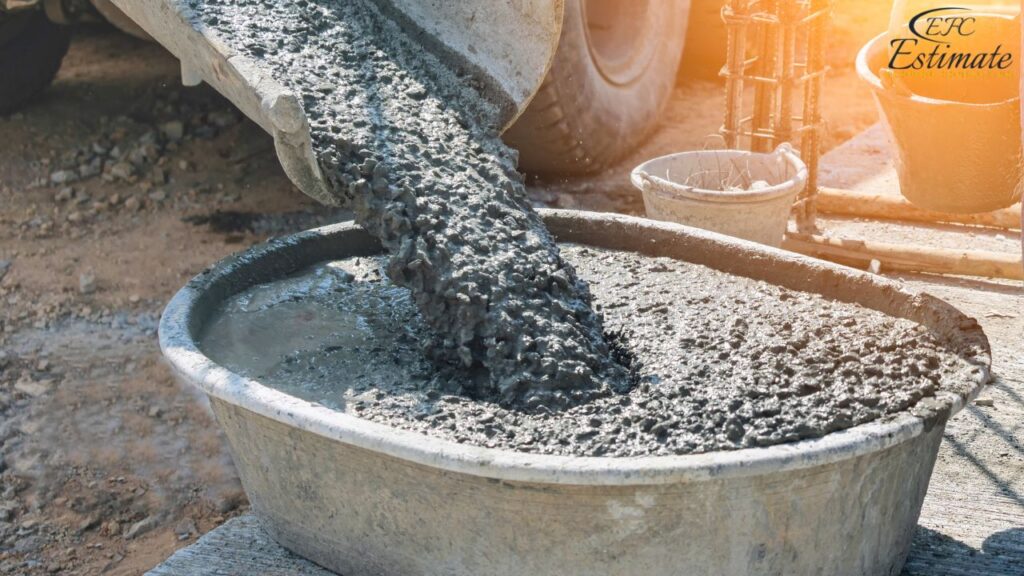
Hot Weather Considerations
Taking the necessary steps to manage the effects of hot weather on concrete can involve additional costs but is essential for ensuring the concrete cures properly. These measures help maintain the right moisture levels and prevent the concrete from drying too quickly. Properly managing hot weather conditions can prevent cracks, reduce maintenance needs, and improve the overall quality of the concrete.
Task | Estimated Cost | Total Cost for 10 Yards |
Ice Water | $60 – $120 | $60 – $120 |
Shading | $120 – $360 | $120 – $360 |
Curing Compounds | $120 – $240 | $120 – $240 |
Download Template For Concrete Construction Project Breakdown
- Materials list updated to the zip code
- Fast delivery
- Data base of general contractors and sub-contractors
- Local estimators
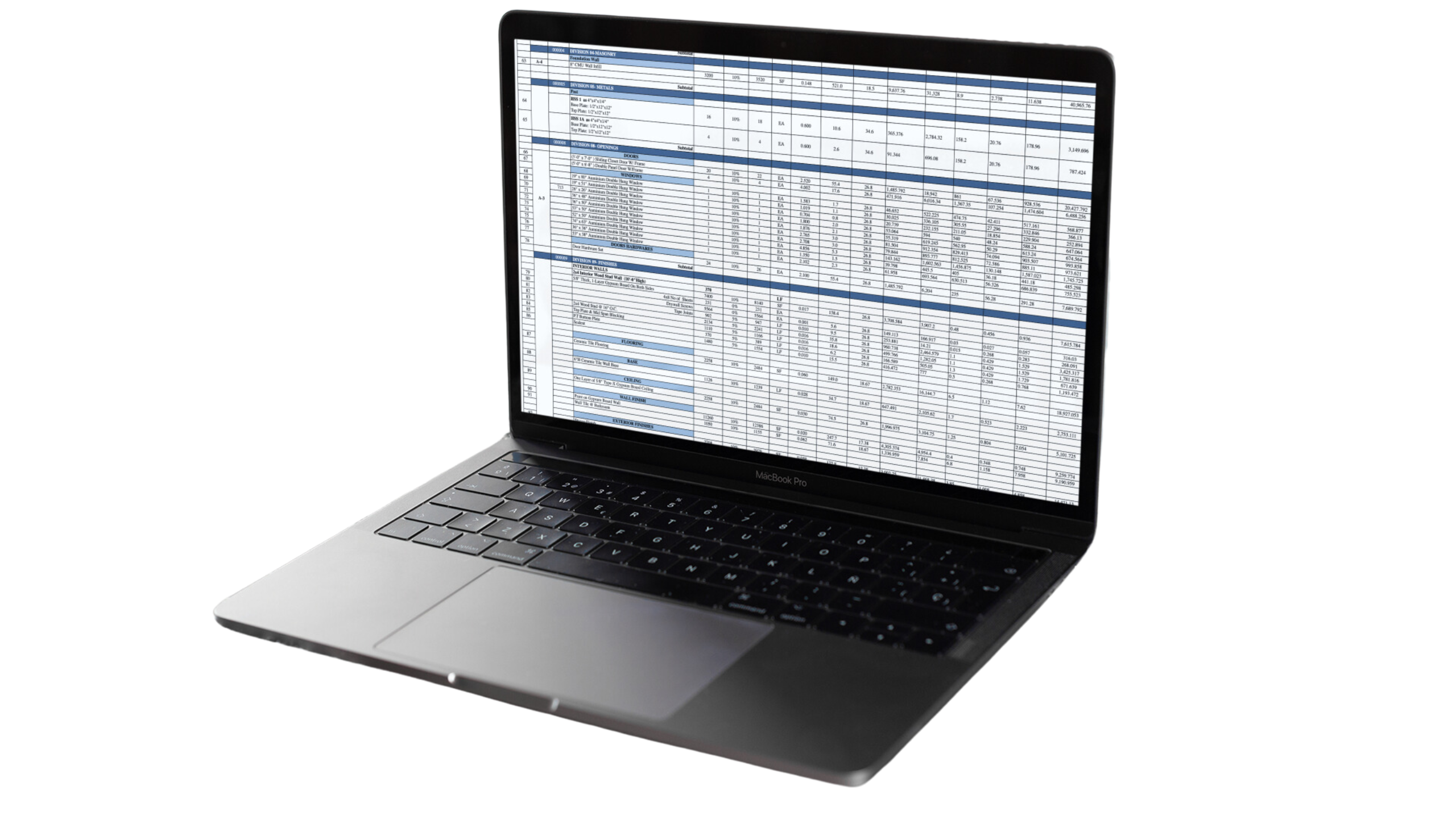
Precautions for Cold Weather
In cold weather, protecting the concrete from freezing is crucial. This can involve using heated water in the mix, insulating the forms, and covering the concrete with thermal blankets. These measures help maintain the necessary curing temperature and prevent damage from freezing. Properly managing the curing process in cold weather ensures that the concrete reaches its full strength and durability. Ensuring the right curing conditions in cold weather can prevent defects and prolong the lifespan of the concrete.
Cold Weather Considerations
Implementing these precautions can add to the overall cost of the project but is necessary to ensure the concrete cures properly and remains durable in the long term. Cold weather management helps prevent issues such as frost damage and ensures a strong, durable finished product. Proper planning and preparation for cold weather conditions can improve the quality and longevity of the concrete.
Task | Estimated Cost | Total Cost for 10 Yards |
Heated Water | $60 – $120 | $60 – $120 |
Form Insulation | $120 – $240 | $120 – $240 |
Thermal Blankets | $120 – $360 | $120 – $360 |
Choosing a Reputable Supplier
Choosing a reputable concrete supplier is essential for ensuring the quality of the concrete and the reliability of the delivery. Reading reviews, asking for recommendations, and checking the supplier’s credentials can help ensure a smooth and successful project. A good supplier can also provide valuable advice and support throughout the project. Ensuring the supplier meets high standards of quality and reliability reduces the risk of delays, errors, and subpar materials. Building a relationship with a reliable supplier can also lead to better prices and services for future projects.
Researching Suppliers
Research potential suppliers to find one with a good reputation for quality and reliability. Look for reviews and testimonials from previous customers. Engaging with a reputable supplier can ensure timely deliveries and high-quality materials. Building a relationship with a reliable supplier can also lead to better prices and services for future projects. Ensuring the supplier meets high standards of quality and reliability reduces the risk of delays, errors, and subpar materials.
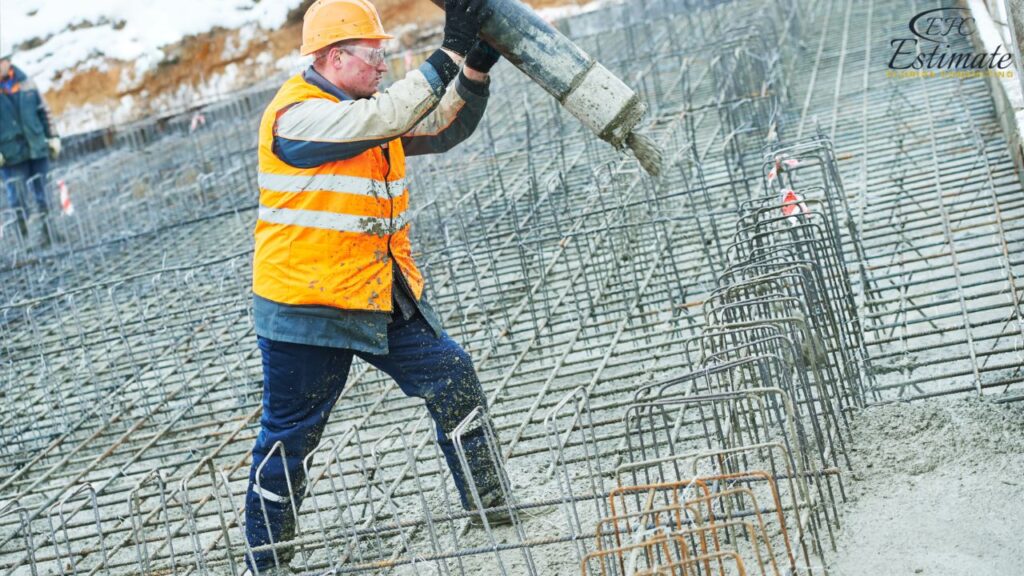
Supplier Research Checklist
Conducting thorough research on potential suppliers can help identify the best options for your project. This checklist outlines key steps to take during the research process. Proper research can help in identifying suppliers who offer the best combination of price, quality, and service.
Task | Steps to Take |
Read Reviews | Check online reviews and ratings |
Ask for Recommendations | Talk to contractors and other industry professionals |
Verify Credentials | Ensure the supplier is licensed and insured |
Comparing Quotes
Obtain quotes from multiple suppliers to compare prices and services. This helps ensure that you get the best value for your money. Comparing quotes allows you to understand the market rate and choose a supplier that offers the best combination of price and service. Detailed comparisons can highlight any discrepancies and help negotiate better terms. Properly comparing quotes can also reveal hidden costs and ensure transparency in the supplier’s pricing.
Get 5 New Projects in the Next 7 Days With Our System
Quote Comparison Table
Creating a comparison table helps in evaluating the quotes from different suppliers, making it easier to identify the most cost-effective option. Properly comparing quotes can also reveal hidden costs and ensure transparency in the supplier’s pricing. Ensuring the supplier meets high standards of quality and reliability reduces the risk of delays, errors, and subpar materials.
Supplier | Base Cost | Delivery Fee | Total Cost for 10 Yards |
Supplier A | $1,440 | $96 | $1,536 |
Supplier B | $1,320 | $120 | $1,440 |
Supplier C | $1,500 | $72 | $1,572 |
Verifying Credentials
Ensure that the supplier is properly licensed and insured. This protects you in case of any issues or damages during delivery. Verifying credentials also confirms the supplier’s legitimacy and reliability. Working with licensed and insured suppliers reduces the risk of liability and ensures compliance with industry standards. Ensuring that the supplier meets all regulatory requirements is crucial for the smooth execution of the project.
Credential Verification Checklist
Use this checklist to verify the credentials of potential suppliers, ensuring they meet all necessary requirements for your project.
Credential | Verification Method |
License | Check with local licensing authority |
Insurance | Request proof of insurance |
Certification | Look for industry certifications or memberships |
Conclusion
The cost of a 10-yard truck of concrete can vary widely based on several factors, including the quality and type of concrete, delivery fees, local market conditions, and additional costs such as labor and equipment rental. By understanding these factors and planning accordingly, contractors and homeowners can budget effectively and ensure the success of their construction projects. Proper planning, site preparation, and choosing a reputable supplier are key to achieving a high-quality finished product that meets the specific needs of the project. By considering all these aspects, you can ensure a smooth and cost-effective concrete project that delivers long-lasting results. Careful attention to detail and thorough planning can lead to a successful outcome and enhance the overall quality and durability of your construction project. Investing time in research and preparation pays off by reducing the risk of unexpected costs and ensuring a high standard of workmanship.
Frequently Asked Question
A 10-yard truck of concrete typically costs between $1,560 and $2,600, averaging $156 to $260 per cubic yard. This price includes the cost of the concrete mix and standard delivery fees.
Key factors include the type and quality of concrete, delivery distance, local market conditions, and additional costs such as labor for pouring, equipment rental, and site preparation.
The cost varies depending on the type of concrete. Standard concrete is usually the least expensive, while high-strength and specialty concrete mixes are more costly due to their specific properties and applications.
- Standard Concrete: $120 – $144 per cubic yard
- High-Strength Concrete: $180 – $204 per cubic yard
- Specialty Concrete: $240+ per cubic yard
Delivery fees can range from $72 to $240 depending on the distance from the concrete plant to the project site and any special delivery requirements. Local deliveries are generally less expensive than long-distance ones.
- Local Deliveries: $72 – $120
- Long-Distance Deliveries: $120 – $240
Prices can vary based on local demand and availability. High-demand areas may experience higher prices, while low-demand areas may offer more competitive pricing.
Accurately calculating the volume needed prevents over-ordering or under-ordering, both of which can lead to increased costs. Consulting with a supplier or construction professional can help determine the correct amount.
Measure the length, width, and depth of the area to be filled and multiply these dimensions to get the volume in cubic feet. Divide by 27 to convert to cubic yards. Adding 5-10% to account for waste is recommended.
Proper site preparation, including leveling, grading, and installing forms, ensures a stable and durable finished product. It also helps prevent issues such as uneven surfaces, cracking, and poor drainage.
Comprehensive Trade-Specific Estimates
At Estimate Florida Consulting, we offer detailed cost estimates across all major trades, ensuring no part of your project is overlooked. From the foundation to the finishing touches, our trade-specific estimates provide you with a complete and accurate breakdown of costs for any type of construction project.
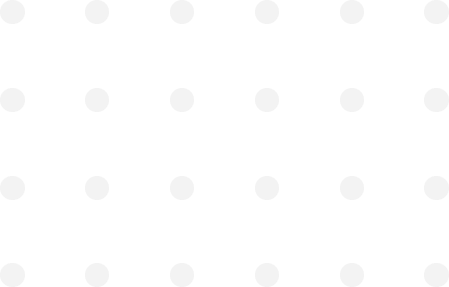
Testimonials
What Our Clients Say
We take pride in delivering accurate, timely, and reliable estimates that help contractors and builders win more projects. Our clients consistently praise our attention to detail, fast turnaround times, and the positive impact our estimates have on their businesses.
Estimate Florida Consulting has helped us win more bids with their fast and accurate estimates. We trust them for every project!
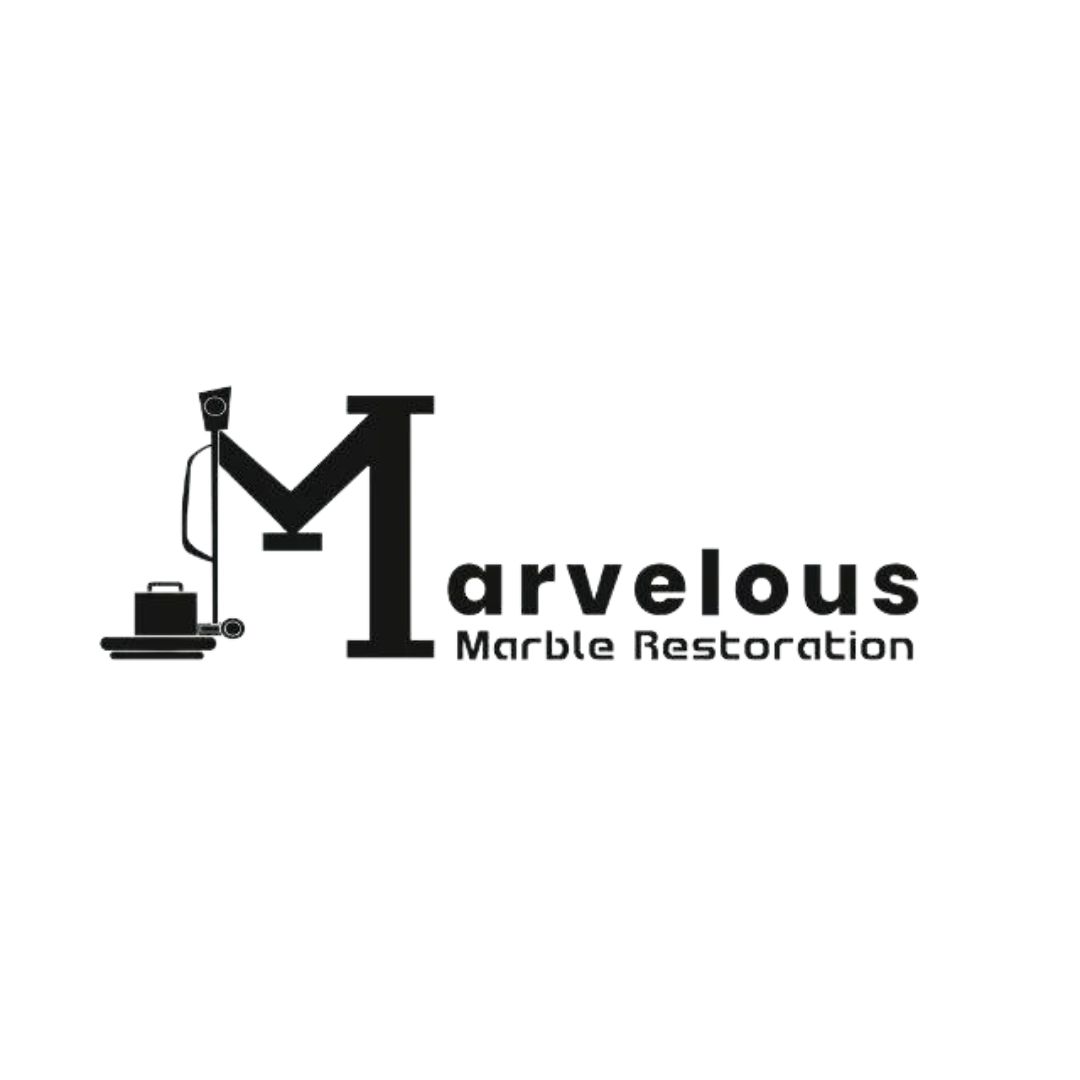
Steps to Follow
Our Simple Process to Get Your Estimate
01
Upload Plans
Submit your project plans, blueprints, or relevant documents through our online form or via email.
02
Receive Quotation
We’ll review your project details and send you a quote based on your scope and requirements.
03
Confirmation
Confirm the details and finalize any adjustments to ensure the estimate meets your project needs.
04
Get Estimate
Receive your detailed, trade-specific estimate within 1-2 business days, ready for your project execution.
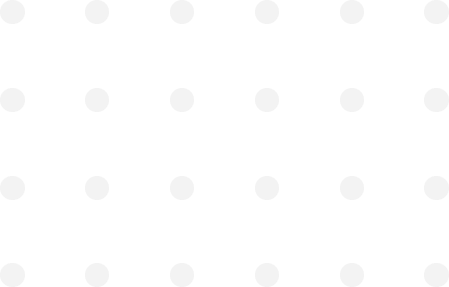