How Much Does Precast Concrete Cost?
Precast concrete typically costs between $102,700 and $255,900, averaging $300 to $750 per cubic yard. This price includes materials, manufacturing, transportation, and installation. Costs can vary based on the project’s size, design complexity, local labor rates, and additional features such as finishes or reinforcements. Precast concrete is often used for structural components like walls, beams, and slabs due to its durability and efficiency. Investing in quality precast concrete ensures a long-lasting, low-maintenance solution that can save time and labor costs during construction. Proper planning and budgeting are essential for getting the best results with precast concrete.
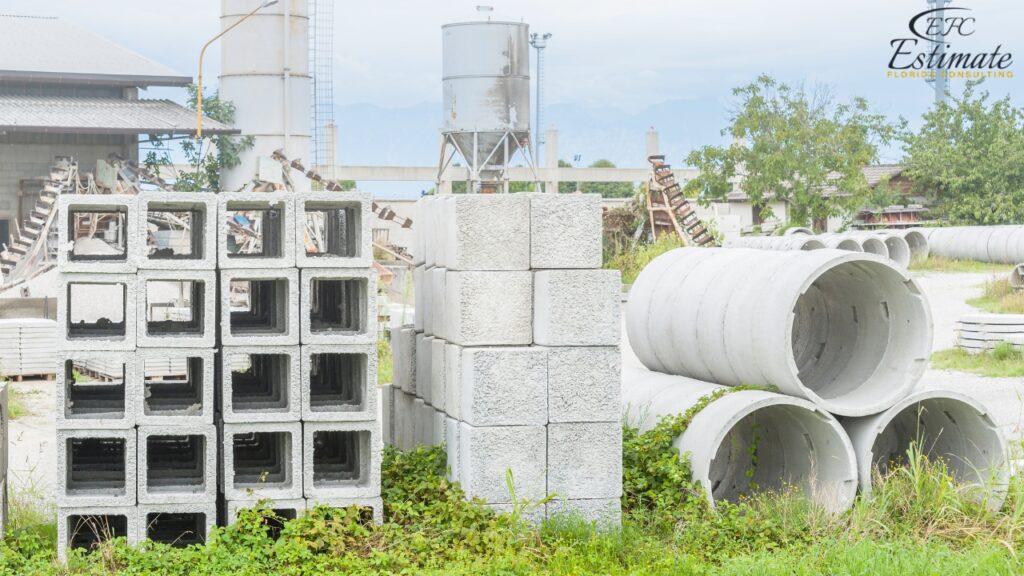
Factors Influencing the Cost of Precast Concrete
Type of Project
The type of project significantly impacts the cost of precast concrete. Different projects have varying requirements in terms of design, size, and complexity, all of which influence the overall cost. Common projects using precast concrete include building facades, structural components, retaining walls, and decorative elements. Each project type may have specific design considerations, which can affect the amount of material needed, the complexity of the mold, and the level of detail required. The end use of the precast concrete also determines the necessary strength and durability, further impacting costs.
Cost Breakdown by Project Type
Project Type | Estimated Cost per Sq Ft | Total Cost (for 1,000 Sq Ft) |
Building Facades | $25 – $50 | $25,000 – $50,000 |
Structural Components | $20 – $40 | $20,000 – $40,000 |
Retaining Walls | $15 – $35 | $15,000 – $35,000 |
Decorative Elements | $30 – $60 | $30,000 – $60,000 |
Materials
The materials used in precast concrete production can significantly influence the cost. High-quality materials ensure durability and longevity but may come at a higher price. The mix design, including the type of cement, aggregates, and admixtures, can also affect the cost. Using specialized additives to enhance the performance of the concrete can add to the expense but may provide benefits such as improved resistance to weathering, reduced maintenance needs, and extended lifespan. Choosing the right materials involves balancing initial costs with long-term benefits.
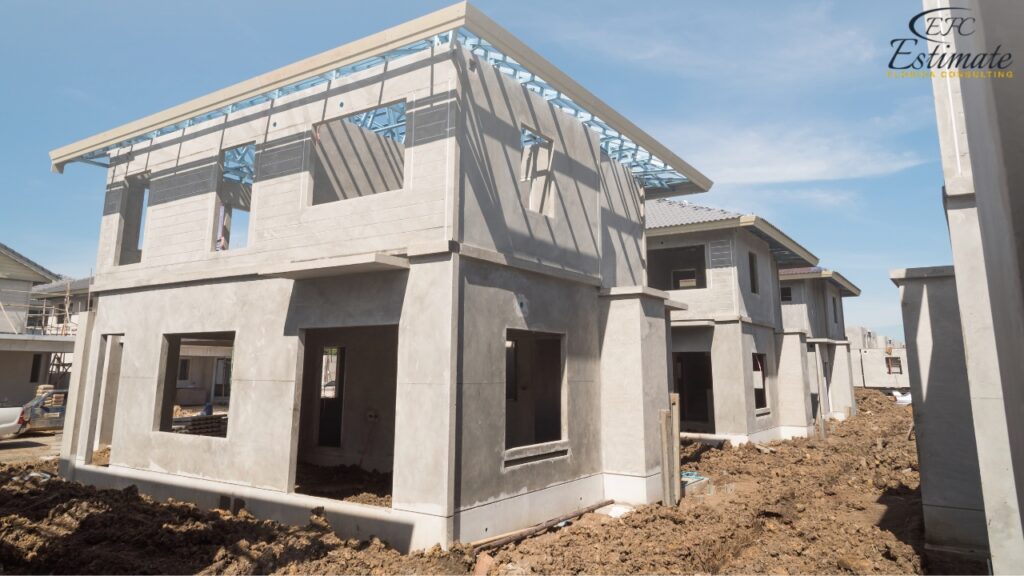
Cost Breakdown by Material Type
Material Type | Estimated Cost per Cubic Yard | Total Cost (for 100 Cubic Yards) |
Standard Concrete | $100 – $150 | $10,000 – $15,000 |
High-Strength Concrete | $150 – $200 | $15,000 – $20,000 |
Lightweight Concrete | $120 – $170 | $12,000 – $17,000 |
Labor Costs
Labor costs are a significant component of the overall expense when using precast concrete. These costs can vary based on the complexity of the project, local labor rates, and the experience of the workers. Skilled labor is essential to ensure proper casting, curing, and installation of the precast concrete elements. The quality of workmanship directly affects the durability and performance of the precast concrete, making it crucial to hire experienced professionals. Labor costs also encompass project management, supervision, and quality control, all of which contribute to the successful completion of the project.
Cost Breakdown by Labor
Labor Task | Estimated Cost per Hour | Total Hours Required | Total Cost |
Casting and Molding | $50 – $100 | 100 – 150 | $5,000 – $15,000 |
Curing and Finishing | $40 – $80 | 80 – 120 | $3,200 – $9,600 |
Installation | $60 – $120 | 100 – 150 | $6,000 – $18,000 |
Manufacturing Process
The manufacturing process of precast concrete involves several stages, including casting, curing, and finishing. The complexity and duration of each stage can affect the overall cost. High-precision molds and advanced curing techniques can increase the cost but improve the quality and durability of the final product. Additionally, the manufacturing process may require specialized equipment and facilities to ensure optimal conditions for producing high-quality precast elements. Investing in advanced manufacturing processes can lead to better performance and aesthetics, justifying the higher initial costs.
Cost Breakdown by Manufacturing Process
Process Stage | Estimated Cost per Unit | Total Units (for 1,000 Units) | Total Cost |
Casting | $10 – $20 | 1,000 | $10,000 – $20,000 |
Curing | $5 – $10 | 1,000 | $5,000 – $10,000 |
Finishing | $7 – $15 | 1,000 | $7,000 – $15,000 |
Transportation and Handling
Transportation and handling of precast concrete elements are crucial factors that contribute to the overall cost. These elements are typically heavy and require specialized equipment for loading, unloading, and installation. The distance between the manufacturing facility and the construction site also impacts transportation costs. Proper handling during transportation is essential to prevent damage, which can lead to additional costs for repairs or replacements. Planning efficient logistics can help minimize these expenses and ensure timely delivery of the precast elements.
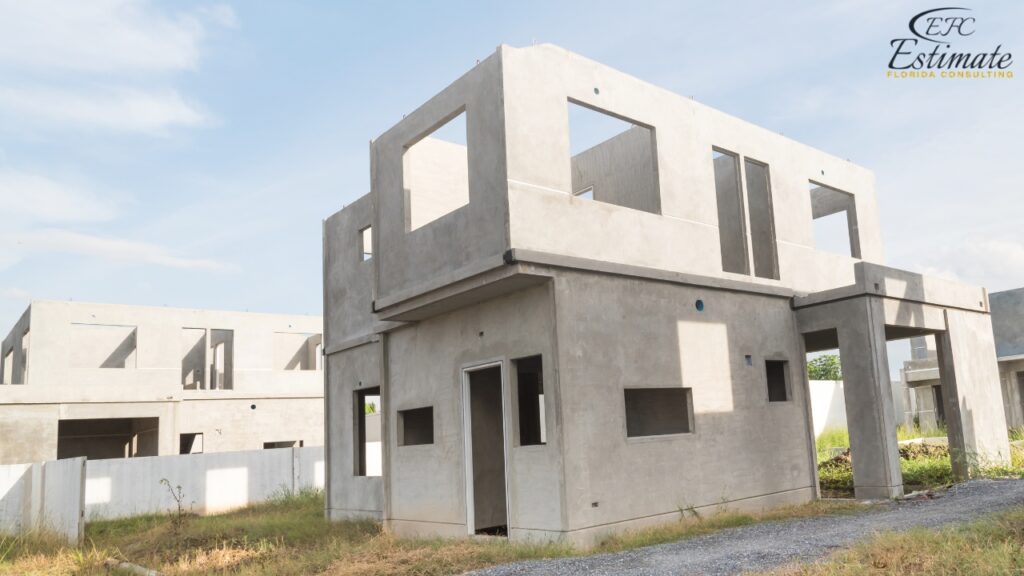
Cost Breakdown by Transportation and Handling
Transportation Distance | Estimated Cost per Mile | Total Cost (for 100 Miles) |
Short Distance (0-50 miles) | $5 – $10 | $500 – $1,000 |
Medium Distance (50-100 miles) | $10 – $20 | $1,000 – $2,000 |
Long Distance (100+ miles) | $20 – $40 | $2,000 – $4,000 |
Site Preparation
Proper site preparation is essential for the successful installation of precast concrete elements. This can include clearing the site, leveling the ground, and setting up necessary infrastructure. The cost of site preparation can vary based on the condition of the site and the amount of work required. Ensuring that the site is well-prepared can prevent delays and additional costs associated with unanticipated obstacles. Effective site preparation also involves coordination with other construction activities to ensure a smooth installation process.
Get 5 New Leads Next 7Days With Our System
- Multi-Family Building
- Hotel Building
- Hospital Building
- Warehouse Building
- High-Rise Building
- Shopping Complex
Cost Breakdown by Site Preparation
Preparation Task | Estimated Cost per Sq Ft | Total Cost (for 1,000 Sq Ft) |
Clearing and Leveling | $2 – $5 | $2,000 – $5,000 |
Infrastructure Setup | $3 – $7 | $3,000 – $7,000 |
Foundation Work | $5 – $10 | $5,000 – $10,000 |
Permits and Regulations
Obtaining the necessary permits and complying with local building regulations are essential for legal and safe construction using precast concrete. Permit costs can vary based on location and the scope of the project. Ensuring compliance with regulations helps avoid fines and ensures that the project meets all safety standards. Navigating the permitting process can be complex, requiring coordination with local authorities and adherence to various codes and standards. Proper planning and documentation can streamline this process and reduce potential delays.
Cost Breakdown by Permits and Regulations
Permit and Compliance Task | Estimated Cost | Total Cost |
Building Permits | $500 – $1,000 | $500 – $1,000 |
Inspection Fees | $200 – $500 | $200 – $500 |
Regulatory Compliance | $300 – $800 | $300 – $800 |
Additional Components
Additional components such as reinforcement, connections, and finishes can add to the overall cost of using precast concrete. These components are essential for the structural integrity and aesthetic appeal of the final product. Reinforcement materials, such as steel bars, provide the necessary strength to withstand loads, while connections ensure that the precast elements are securely joined. Finishes can enhance the visual appeal and durability of the concrete, adding to the overall value of the project.

Cost Breakdown by Additional Components
Component | Estimated Cost per Unit | Total Cost (for 1,000 Units) |
Reinforcement | $10 – $20 | $10,000 – $20,000 |
Connections | $5 – $10 | $5,000 – $10,000 |
Finishes | $15 – $30 | $15,000 – $30,000 |
Additional Considerations
Seasonal Timing
The time of year can impact the cost and ease of using precast concrete. Scheduling the project during mild weather conditions can prevent delays and reduce complications related to extreme temperatures. This can also affect the availability of labor and materials, potentially leading to cost savings. Planning the project around favorable weather conditions can help ensure timely completion and reduce the risk of weather-related interruptions. Additionally, certain times of the year may see lower demand for construction services, leading to potential discounts on labor and materials.
Quality Assurance
Ensuring high-quality production and installation of precast concrete elements is essential for the longevity and performance of the structure. Implementing rigorous quality control measures during manufacturing and installation can prevent defects and ensure compliance with standards. Regular inspections and testing throughout the production process can identify and address issues early, reducing the risk of costly repairs or replacements later. Investing in quality assurance measures can enhance the durability and safety of the project, providing long-term benefits.
Environmental Impact
Choosing environmentally friendly materials and practices in precast concrete production can reduce the environmental impact of the construction project. This includes using recycled materials, optimizing the mix design for reduced carbon footprint, and implementing waste management practices. Incorporating sustainable practices can also enhance the project’s appeal to environmentally conscious stakeholders and potentially qualify for green building certifications. Reducing environmental impact not only benefits the planet but can also improve the project’s marketability and value.
Financing Options
Financing the use of precast concrete in a construction project may involve exploring different financing options such as construction loans, grants, or partnerships. Understanding the terms and conditions of these options can help property owners secure the necessary funds. Different financing options may offer varying interest rates and repayment terms, so it’s important to compare your choices carefully to find the most suitable solution for your financial situation. Working with financial advisors can help identify the best financing strategies and optimize funding for the project.
Cost Breakdown by Financing Options
Financing Option | Estimated Interest Rate Range | Total Interest Cost (for $100,000 loan) |
Construction Loan | 4% – 8% | $4,000 – $8,000 |
Government Grant | Variable | Dependent on grant terms |
Public-Private Partnership | Variable | Dependent on agreement |
Choosing the Right Precast Concrete Supplier
Selecting a reliable and experienced precast concrete supplier is crucial for the success of the project. A reputable supplier can ensure high-quality materials, timely delivery, and compliance with specifications. Homeowners and developers should research potential suppliers, check references, and review past projects to make an informed decision.
Evaluating Supplier Quotes
When evaluating quotes from precast concrete suppliers, it’s essential to compare the scope of work, materials used, and warranties offered. The lowest quote isn’t always the best option, as it may exclude critical components or use inferior materials. Reviewing the details of each quote helps ensure you’re getting the best value for your investment. Thoroughly vetting suppliers can prevent issues and ensure the project stays within budget and on schedule. By obtaining multiple quotes, stakeholders can compare prices and services, ensuring they choose the best supplier for their needs.
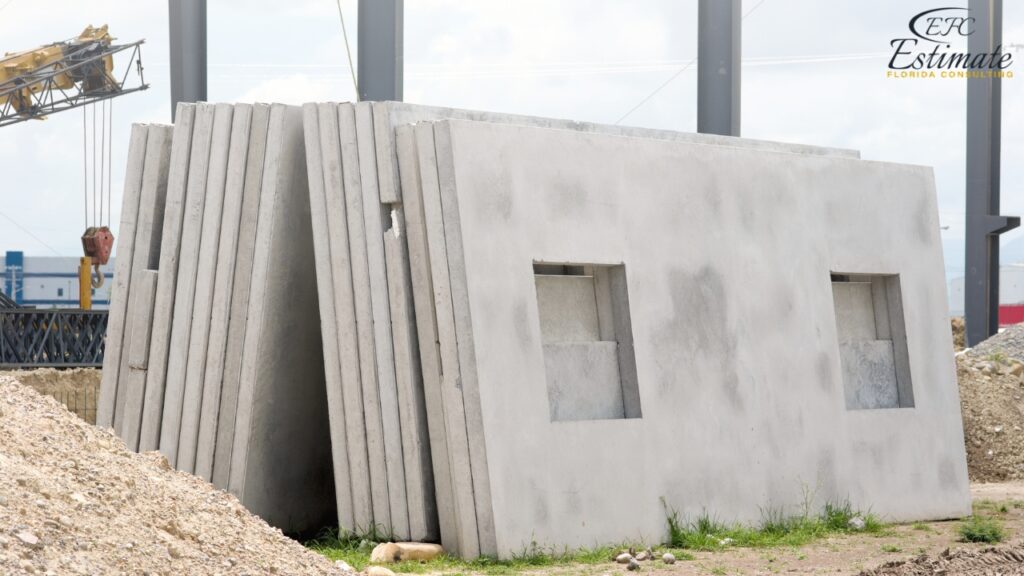
Checking Certifications and Compliance
Ensure that the supplier holds the necessary certifications and complies with industry standards. Proper certification indicates that the supplier adheres to best practices in manufacturing and quality control, while compliance with regulations ensures that the materials meet safety and performance standards. Verifying these credentials can give you peace of mind and protect you from potential issues. Ensuring the supplier is properly certified and compliant can also provide financial protection in case of defects or non-compliance.
Supplier's Track Record
Investigate the supplier’s track record to understand their reliability and reputation in the industry. Look for reviews, testimonials, and case studies from previous clients to gauge their performance. A supplier with a strong track record of successful projects and satisfied clients is more likely to deliver high-quality results. Evaluating the supplier’s past performance can help you make an informed decision and avoid potential problems.
Delivery and Installation Services
Some precast concrete suppliers offer delivery and installation services, which can simplify the project management process. Coordinating with a single supplier for both materials and installation can ensure better communication and streamline logistics. This approach can also reduce the risk of delays and miscommunication, leading to a smoother and more efficient project. Considering suppliers who provide comprehensive services can enhance the overall project experience.
Download Template For Concrete Project Breakdown
- Materials list updated to the zip code
- Fast delivery
- Data base of general contractors and sub-contractors
- Local estimators
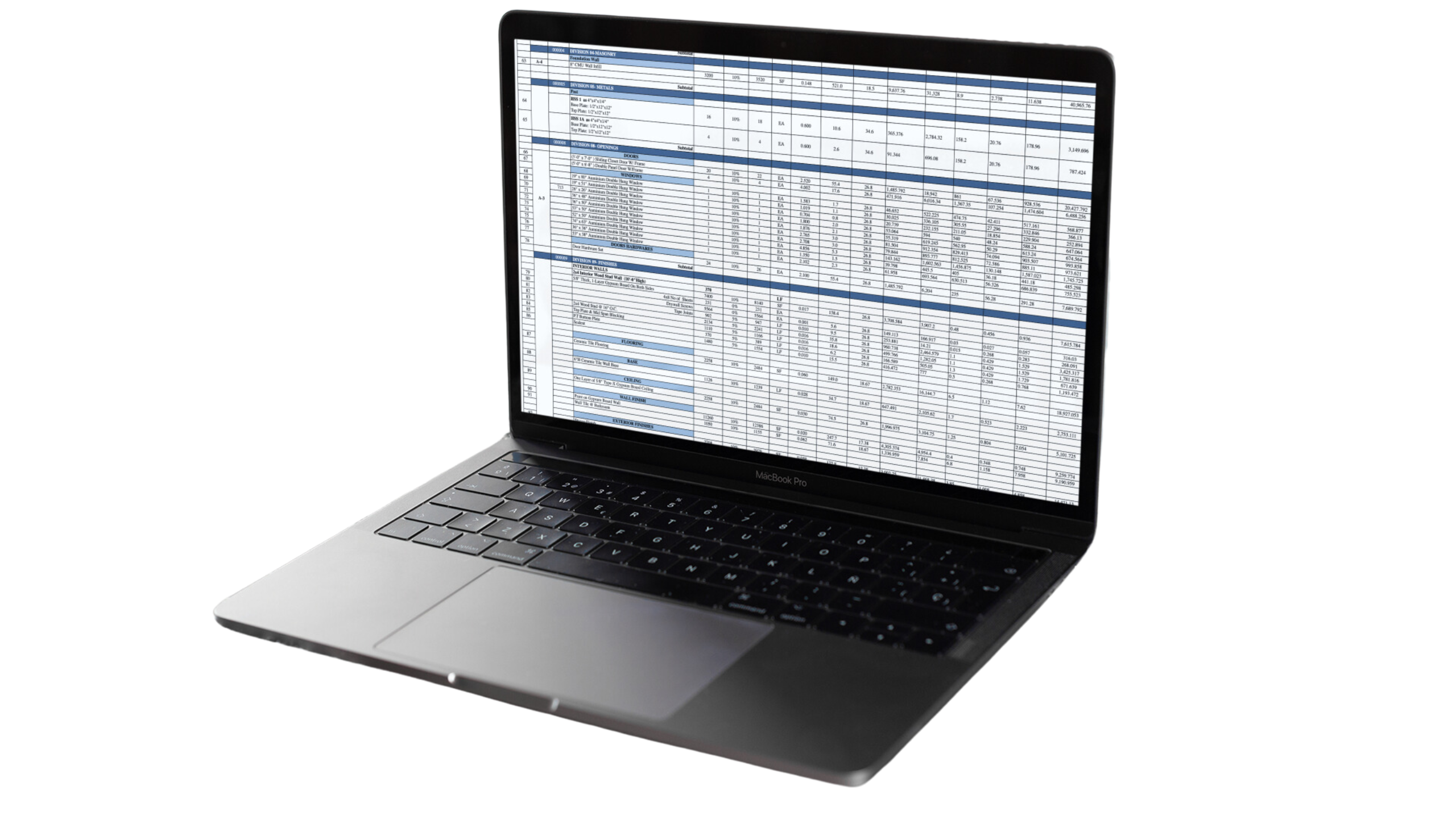
Conclusion
Precast concrete offers numerous advantages for construction projects, including durability, versatility, and efficiency. However, the cost of precast concrete can vary based on factors such as the type of project, materials, labor, manufacturing process, transportation, site preparation, permits, and additional components. By understanding and planning for these costs, property owners and developers can create a realistic budget and ensure the successful completion of their projects. Proper budgeting for all aspects of the project helps avoid financial surprises and ensures the precast concrete elements are installed to high standards. With careful planning and attention to detail, stakeholders can achieve a functional and reliable structure that meets their needs and stands the test of time. Working with experienced professionals and considering all relevant factors can help ensure a smooth and cost-effective construction process using precast concrete.
FAQs
Precast concrete typically costs between $102,700 and $255,900, averaging $300 to $750 per cubic yard. This price includes materials, manufacturing, transportation, and installation.
Key factors include the type of project, materials used, labor costs, manufacturing process, transportation, site preparation, permits, and additional components such as reinforcement and finishes.
Different projects have varying requirements in terms of design, size, and complexity, impacting the overall cost. Common projects include building facades, structural components, retaining walls, and decorative elements.
- Building Facades: $25 – $50 per sq ft
- Structural Components: $20 – $40 per sq ft
- Retaining Walls: $15 – $35 per sq ft
- Decorative Elements: $30 – $60 per sq ft
The materials used can significantly influence the cost. Common types include standard concrete, high-strength concrete, and lightweight concrete.
- Standard Concrete: $100 – $150 per cubic yard
- High-Strength Concrete: $150 – $200 per cubic yard
- Lightweight Concrete: $120 – $170 per cubic yard
Labor costs vary based on the complexity of the project, local labor rates, and the experience of the workers. Labor tasks include casting, curing, and installation.
- Casting and Molding: $50 – $100 per hour
- Curing and Finishing: $40 – $80 per hour
- Installation: $60 – $120 per hour
The manufacturing process involves casting, curing, and finishing. Advanced techniques and high-precision molds can increase costs but improve quality and durability.
- Casting: $10 – $20 per unit
- Curing: $5 – $10 per unit
- Finishing: $7 – $15 per unit
Transportation costs depend on the distance between the manufacturing facility and the construction site, as well as the weight of the precast elements.
- Short Distance (0-50 miles): $5 – $10 per mile
- Medium Distance (50-100 miles): $10 – $20 per mile
- Long Distance (100+ miles): $20 – $40 per mile
Google Reviews
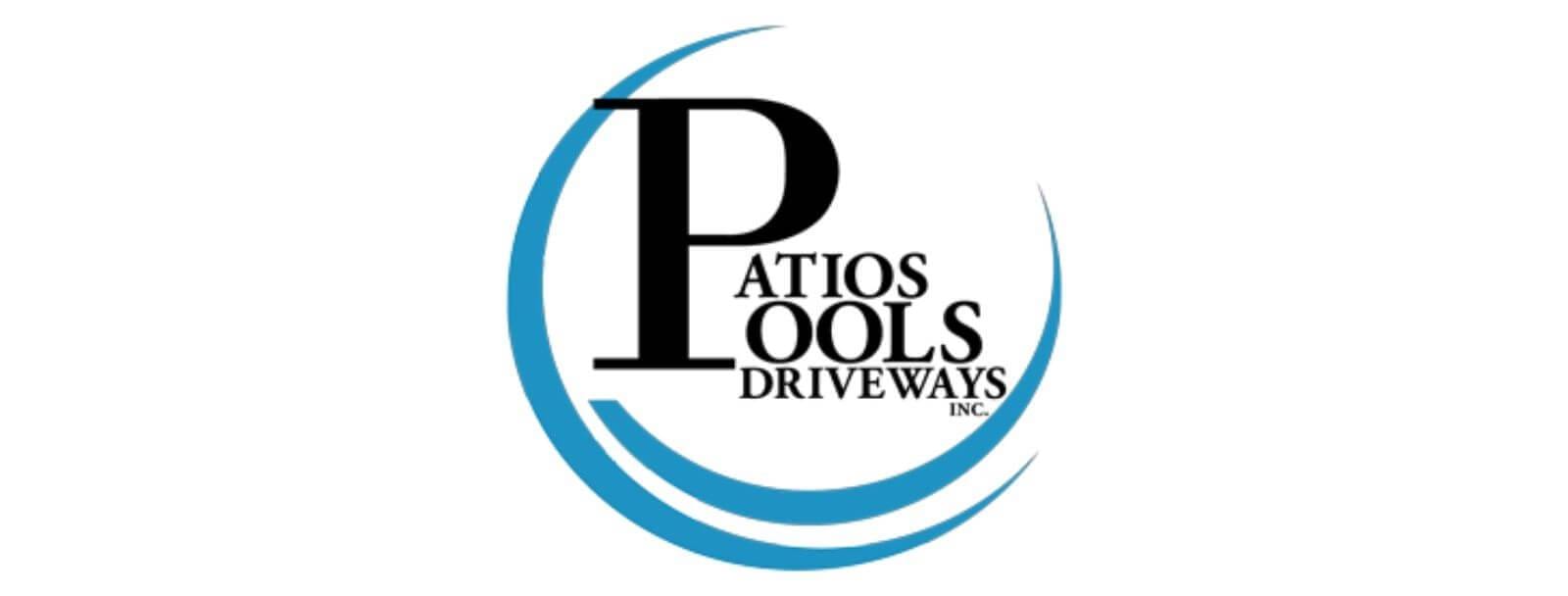
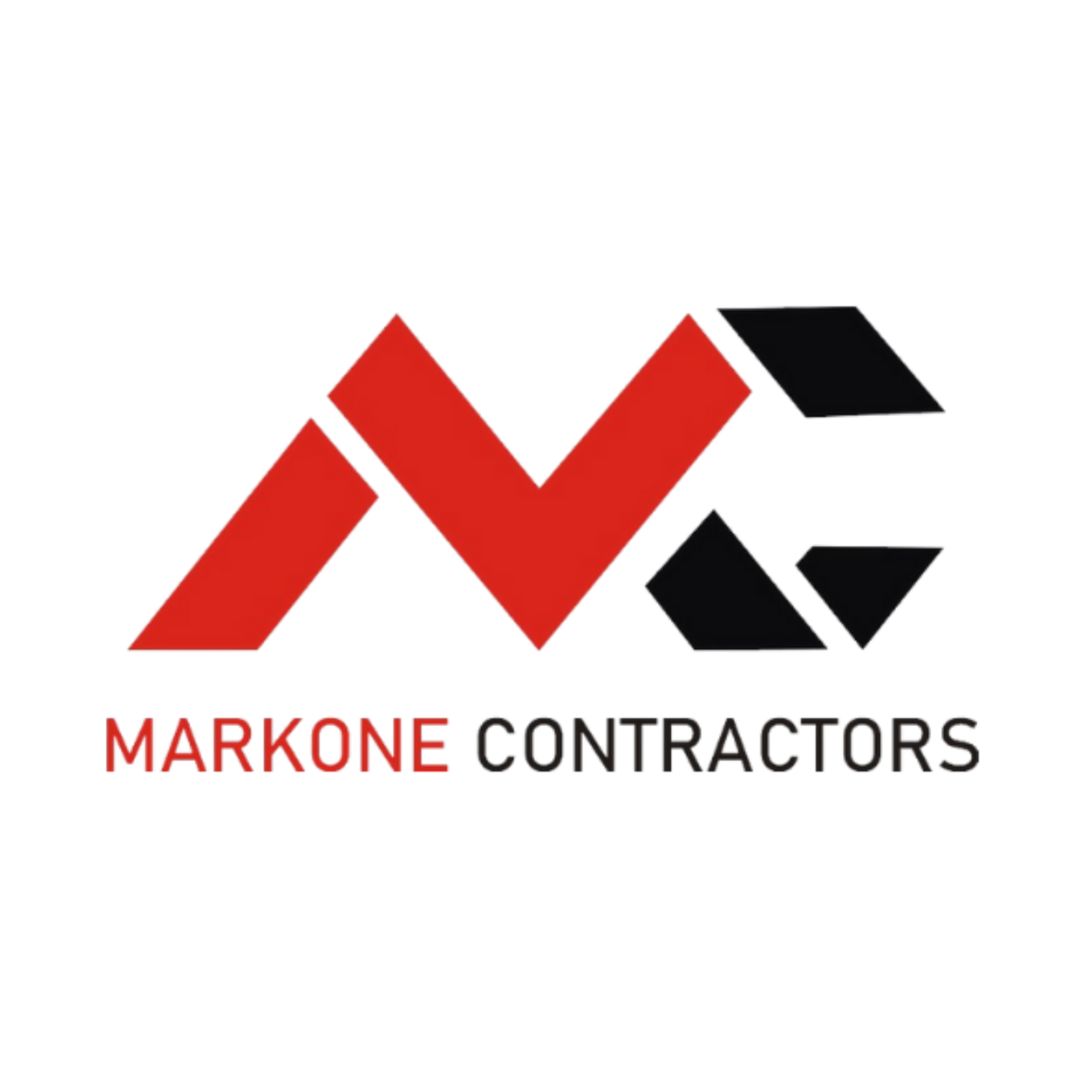

Process To Get Precast Concrete Cost Estimate Report
Here I am going to share some steps to get precast concrete cost estimate report.
-
You need to send your plan to us.
You can send us your plan on info@estimatorflorida.com
-
You receive a quote for your project.
Before starting your project, we send you a quote for your service. That quote will have detailed information about your project. Here you will get information about the size, difficulty, complexity and bid date when determining pricing.
-
Get Estimate Report
Our team will takeoff and estimate your project. When we deliver you’ll receive a PDF and an Excel file of your estimate. We can also offer construction lead generation services for the jobs you’d like to pursue further.