How Much Does Metal Siding Cost?
Metal siding is a popular choice for both residential and commercial buildings due to its durability, low maintenance, and modern aesthetic appeal. The cost of metal siding varies widely based on the type of metal, quality of material, project size, and labor costs. On average, the cost ranges from $3.90 to $15.60 per square foot. Aluminum is generally the most affordable option, costing between $3.90 and $7.80 per square foot, while steel ranges from $5.20 to $10.40 per square foot. Copper, the most expensive, ranges from $10.40 to $15.60 per square foot, and zinc falls between $7.80 and $13.00 per square foot.
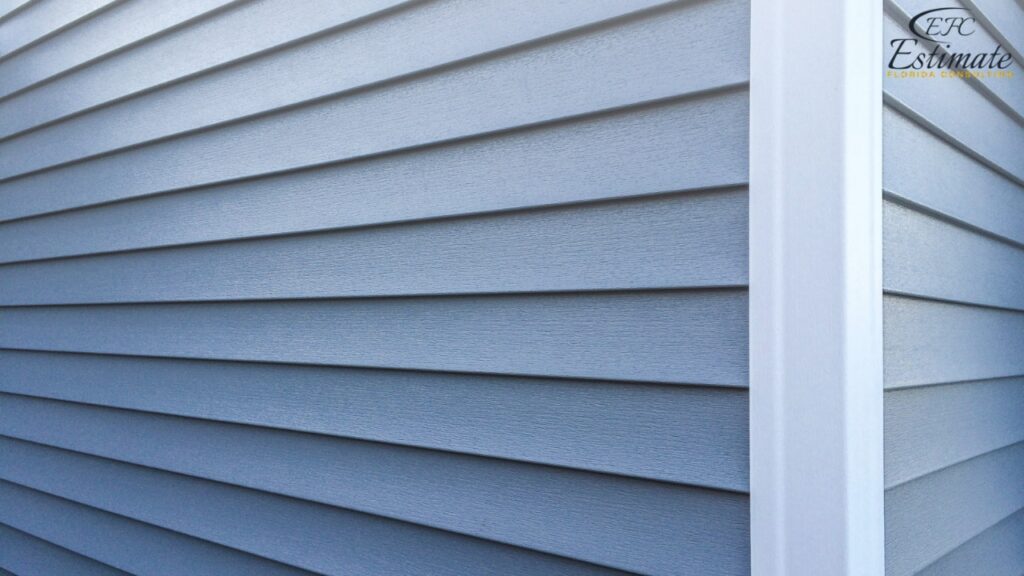
Average Cost of Metal Siding
The cost of metal siding can vary widely based on several factors, including the type of metal, the quality of the material, the size of the project, and labor costs. On average, the cost of metal siding ranges from $3.90 to $15.60 per square foot. Understanding these costs is crucial for effective budgeting and planning. Here’s a more detailed cost breakdown to help you get a better sense of what to expect:
Cost Breakdown by Type of Metal
Type of Metal | Cost per Square Foot |
Aluminum | $3.90 – $7.80 |
Steel | $5.20 – $10.40 |
Copper | $10.40 – $15.60 |
Zinc | $7.80 – $13.00 |
Aluminum is generally the most affordable option and is widely used due to its resistance to rust and corrosion. Steel is more durable and offers better protection against impacts but can be more expensive. Copper, while the most costly, provides a unique and attractive appearance and excellent longevity. Zinc is valued for its durability and low maintenance but comes at a mid-to-high price range. Each type of metal offers distinct benefits and aesthetic options, making it important to choose the one that best fits your needs and budget.
Cost Breakdown by Project Size
Project Size | Small (1,000 sq ft) | Medium (2,000 sq ft) | Large (3,000 sq ft) |
Type of Metal | Total Cost | Total Cost | Total Cost |
Aluminum | $3,900 – $7,800 | $7,800 – $15,600 | $11,700 – $23,400 |
Steel | $5,200 – $10,400 | $10,400 – $20,800 | $15,600 – $31,200 |
Copper | $10,400 – $15,600 | $20,800 – $31,200 | $31,200 – $46,800 |
Zinc | $7,800 – $13,000 | $15,600 – $26,000 | $23,400 – $39,000 |
This breakdown illustrates how costs scale with the size of the project. Smaller projects might be more manageable in terms of budget, but larger projects can benefit from bulk purchasing discounts and more efficient use of labor. Additionally, larger projects might require more complex planning and coordination, especially if they involve multiple stories or intricate architectural details.
Design and Architecture
Materials
Materials make up a significant portion of the cost for metal siding. The type and quality of the metal will determine the price. Here’s a breakdown of material costs:
Component | Cost per Square Foot |
Basic Aluminum Siding | $3.90 – $5.20 |
Premium Aluminum Siding | $5.20 – $7.80 |
Galvanized Steel Siding | $5.20 – $7.80 |
Premium Steel Siding | $7.80 – $10.40 |
Standard Copper Siding | $10.40 – $13.00 |
Premium Copper Siding | $13.00 – $15.60 |
Basic Zinc Siding | $7.80 – $10.40 |
Premium Zinc Siding | $10.40 – $13.00 |
Choosing the right material involves balancing cost with the desired appearance and durability. For instance, while basic aluminum siding is cost-effective and rust-resistant, premium options offer enhanced aesthetic appeal and longer lifespan. Similarly, premium steel and copper siding provide superior strength and beauty but come at a higher price point.
Labor
Labor costs can vary depending on the complexity of the project and the location. Professional installation is crucial for ensuring the siding is properly installed. Here’s an estimated labor cost breakdown:
Labor Task | Cost per Square Foot |
Installation | $1.95 – $3.90 |
Removal of Old Siding | $1.30 – $2.60 |
Insulation Installation | $0.65 – $1.30 |
Repairs to Underlying Structure | $1.95 – $3.25 |
Professional labor ensures that the siding is installed correctly, preventing potential issues such as leaks or improper alignment. Labor costs may also be influenced by the contractor’s experience and reputation, as well as the accessibility of the building site. Complex installations, such as those involving intricate designs or multi-story buildings, can increase labor costs significantly.
Additional Costs
There are often additional costs associated with metal siding projects, including permits, insulation, and site preparation. These costs can add up and should be included in the overall budget.
Additional Costs | Cost per Square Foot |
Permits | $0.10 – $0.30 |
Site Preparation | $0.50 – $1.00 |
Insulation | $1.00 – $1.50 |
Disposal of Old Siding | $0.20 – $0.50 |
Permits are necessary to ensure the project complies with local building codes and regulations. Site preparation may include leveling the ground, removing vegetation, or installing foundational support. Insulation adds to the overall cost but can improve energy efficiency and comfort. Disposal of old siding must be handled properly to avoid environmental issues and additional fees.
Factors Affecting the Cost of Metal Siding
Type of Metal
The type of metal you choose significantly impacts the cost. Aluminum is generally the most affordable option, while copper is on the higher end due to its durability and aesthetic appeal. Steel and zinc fall somewhere in between, offering a good balance of cost and performance. Each metal type has its advantages and considerations: aluminum is lightweight and rust-resistant, steel is strong and impact-resistant, copper develops a beautiful patina over time, and zinc is self-healing and long-lasting. These characteristics can influence not only the initial installation cost but also long-term maintenance and repair expenses.
Quality of Material
Higher quality metal siding materials tend to be more expensive but offer better durability, resistance to weather, and overall longevity. Investing in high-quality materials can reduce maintenance costs and extend the lifespan of your siding. For example, premium-grade aluminum may include additional coatings for enhanced weather resistance, while high-quality steel might be treated to resist corrosion and dents more effectively. High-quality materials often come with longer warranties and better performance, making them a worthwhile investment for long-term projects.
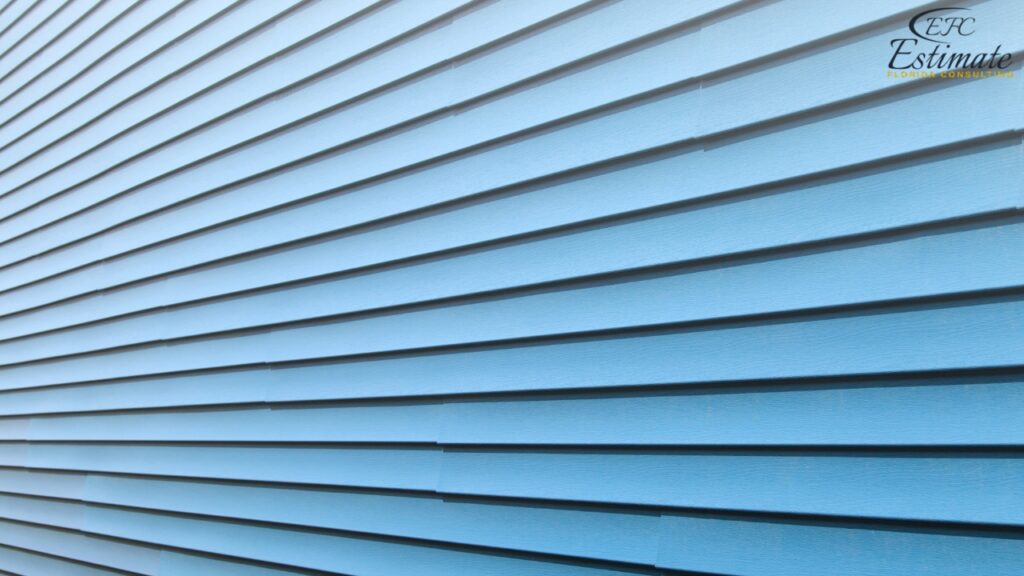
Size of the Project
The size of your project directly affects the total cost. Larger projects will naturally require more materials and labor, increasing the overall expense. It’s important to measure the area accurately to get an accurate estimate. Larger projects might also require more complex logistics and coordination, especially if scaffolding or specialized equipment is needed for high or expansive walls. Additionally, larger projects can sometimes benefit from economies of scale, where bulk purchasing and efficient labor deployment reduce the per-unit cost.
Labor Costs
Labor costs can vary based on your location and the complexity of the installation. Professional installation ensures that the siding is installed correctly and can significantly impact the total cost. On average, labor costs for installing metal siding range from $1.95 to $5.20 per square foot. Labor costs may also be influenced by factors such as the contractor’s experience, the difficulty of the job (e.g., working around windows and doors), and the condition of the existing structure. High-quality labor not only ensures a better installation but can also reduce future repair and maintenance costs by preventing initial installation errors.
Additional Costs
Additional costs can include insulation, removal of old siding, and any necessary repairs to the underlying structure. These costs can add up, so it’s important to factor them into your overall budget. For example, adding a layer of insulation beneath the metal siding can improve energy efficiency but will increase the project’s cost. Similarly, removing old siding can be labor-intensive and generate disposal fees. Ensuring that the underlying structure is sound before installation is crucial, as any damage or weakness can affect the longevity and performance of the new siding.
Get 5 New Leads Next 7Days With Our System
- Multi-Family Building
- Hotel Building
- Hospital Building
- Warehouse Building
- High-Rise Building
- Shopping Complex
Tips for Managing Your Metal Siding Project
Get Multiple Quotes
It’s a good idea to get multiple quotes from different contractors to compare prices and services. This can help you find the best deal and ensure that you’re not overpaying for the installation. When comparing quotes, ensure that each contractor provides a detailed breakdown of materials, labor, and any additional costs to make an informed decision. Checking references and reading reviews can also provide insights into the quality of their work and customer satisfaction. By comparing multiple quotes, you can identify the most cost-effective and reliable option for your project.
Choose the Right Material
Consider the climate and environmental conditions in your area when choosing the type of metal siding. For example, aluminum is resistant to rust and is a good choice for coastal areas, while steel offers better protection against impacts. Copper and zinc can be great options in areas with varying weather conditions due to their durability and low maintenance requirements. Additionally, consider the aesthetic appeal and how the siding will complement the overall design of your property. The right material will not only look good but also perform well under the specific environmental conditions of your location.
Plan for Additional Costs
Make sure to budget for additional costs such as insulation, removal of old siding, and potential repairs. Having a contingency budget can help you manage unexpected expenses without disrupting your project. It’s often recommended to set aside an additional 10-20% of the total project cost for unforeseen issues. This buffer can cover any surprise expenses that may arise during installation, such as discovering underlying structural issues that need attention. Proper planning and budgeting can prevent financial strain and ensure a smooth project execution.
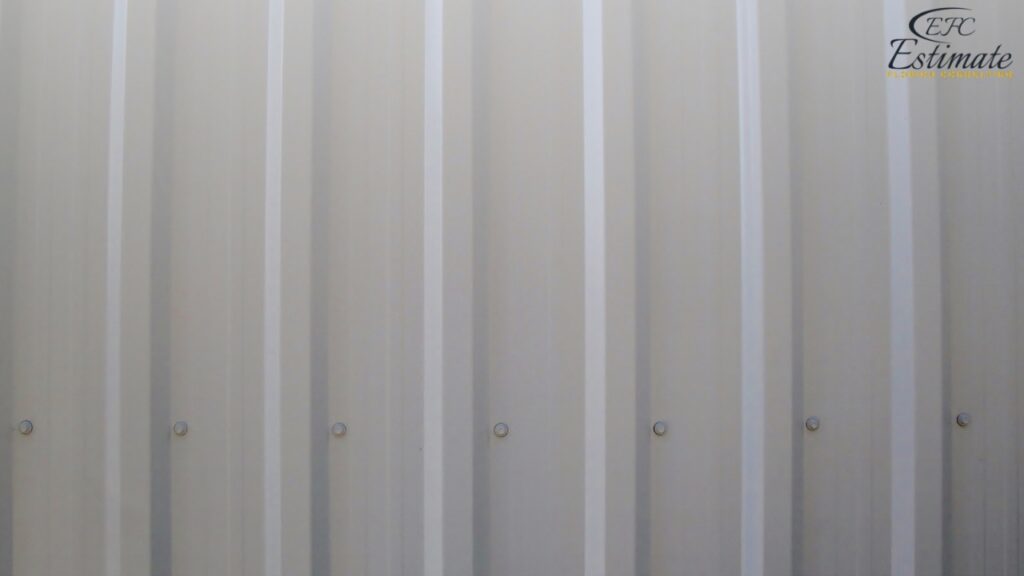
Invest in Quality
While it may be tempting to choose the cheapest option, investing in high-quality materials can save you money in the long run by reducing maintenance costs and extending the lifespan of your siding. High-quality siding is also more likely to maintain its appearance and performance over time, enhancing your property’s curb appeal and value. Premium materials often come with better warranties, offering additional peace of mind. Investing in quality can provide long-term benefits, such as improved durability, better weather resistance, and lower overall maintenance costs.
Regular Maintenance
To keep your metal siding looking its best and to extend its lifespan, perform regular maintenance such as cleaning and inspecting for damage. Address any issues promptly to prevent more significant problems down the line. Regular maintenance can include washing the siding with a gentle detergent to remove dirt and debris, checking for signs of rust or corrosion, and ensuring that all fasteners and seals remain secure. Scheduling annual inspections can help catch potential issues early and maintain the integrity of your siding. Proper maintenance not only extends the lifespan of your siding but also keeps your property looking its best.
Download Template For Siding Project Breakdown
- Materials list updated to the zip code
- Fast delivery
- Data base of general contractors and sub-contractors
- Local estimators
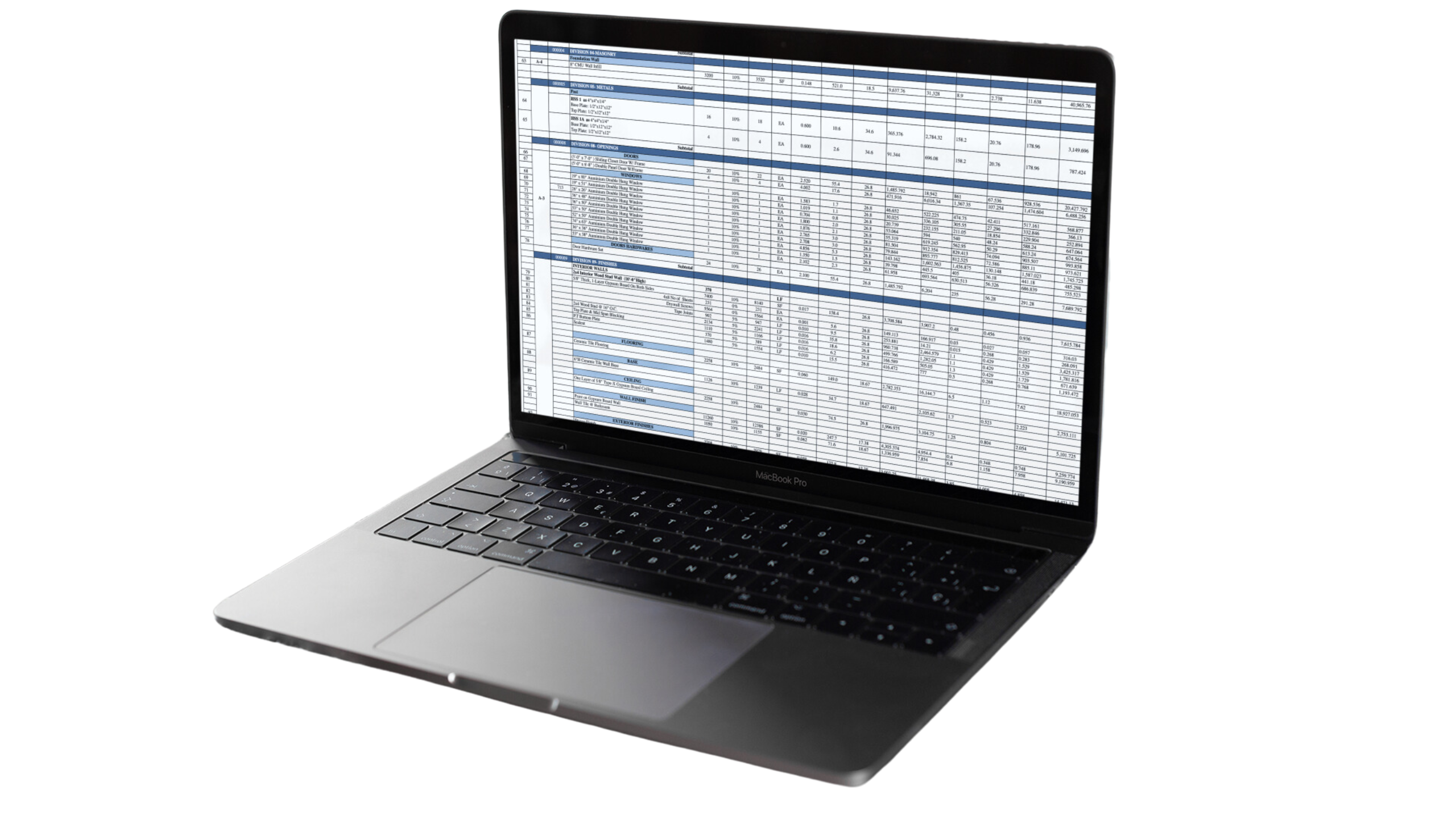
Conclusion
Estimate Florida Consulting is your premier partner for comprehensive construction takeoff services in Cape Coral, FL. We specialize in delivering detailed and accurate takeoff services for a wide range of commercial buildings, including hotels, hospitals, apartment complexes, shopping malls, warehouses, schools, and colleges. Our expert team ensures precise budgeting, efficient resource allocation, and superior project outcomes for your construction needs. By choosing Estimate Florida Consulting, you benefit from our extensive experience, advanced technology, and customized solutions, all designed to support the successful completion of your projects. Contact us today to learn more about how our construction takeoff services can help you achieve your goals efficiently and cost-effectively.
FAQs
The average cost of metal siding ranges from $3.90 to $15.60 per square foot, depending on the type of metal, quality of materials, and project size.
Several factors influence the cost of metal siding, including the type of metal, quality of material, project size, labor costs, and additional expenses such as insulation and site preparation.
The type of metal significantly impacts the cost. Aluminum is the most affordable option, ranging from $3.90 to $7.80 per square foot. Steel costs between $5.20 and $10.40 per square foot. Copper is the most expensive, costing $10.40 to $15.60 per square foot, while zinc ranges from $7.80 to $13.00 per square foot.
Costs vary based on project size:
- Small (1,000 sq ft): $3,900 – $15,600
- Medium (2,000 sq ft): $7,800 – $31,200
- Large (3,000 sq ft): $11,700 – $46,800
Material costs depend on the type and quality of metal:
- Basic Aluminum: $3.90 – $5.20 per sq ft
- Premium Aluminum: $5.20 – $7.80 per sq ft
- Galvanized Steel: $5.20 – $7.80 per sq ft
- Premium Steel: $7.80 – $10.40 per sq ft
- Standard Copper: $10.40 – $13.00 per sq ft
- Premium Copper: $13.00 – $15.60 per sq ft
- Basic Zinc: $7.80 – $10.40 per sq ft
- Premium Zinc: $10.40 – $13.00 per sq ft
Labor costs for installing metal siding range from $1.95 to $3.90 per square foot. Additional tasks such as removing old siding, installing insulation, and repairing the underlying structure can add to these costs.
Additional costs include permits ($0.10 – $0.30 per sq ft), site preparation ($0.50 – $1.00 per sq ft), insulation ($1.00 – $1.50 per sq ft), and disposal of old siding ($0.20 – $0.50 per sq ft).
To manage costs effectively, get multiple quotes from contractors, choose the right material based on your needs and climate, plan for additional costs, invest in high-quality materials, and perform regular maintenance.
Choosing the right material ensures your siding will perform well under local environmental conditions and enhance the aesthetic appeal of your property. Each type of metal has its unique benefits, such as aluminum’s rust resistance and copper’s longevity.
Regular maintenance, including cleaning and inspections, can extend the lifespan of your metal siding. Addressing any damage promptly prevents more significant problems and maintains the appearance and functionality of the siding.
Google Reviews
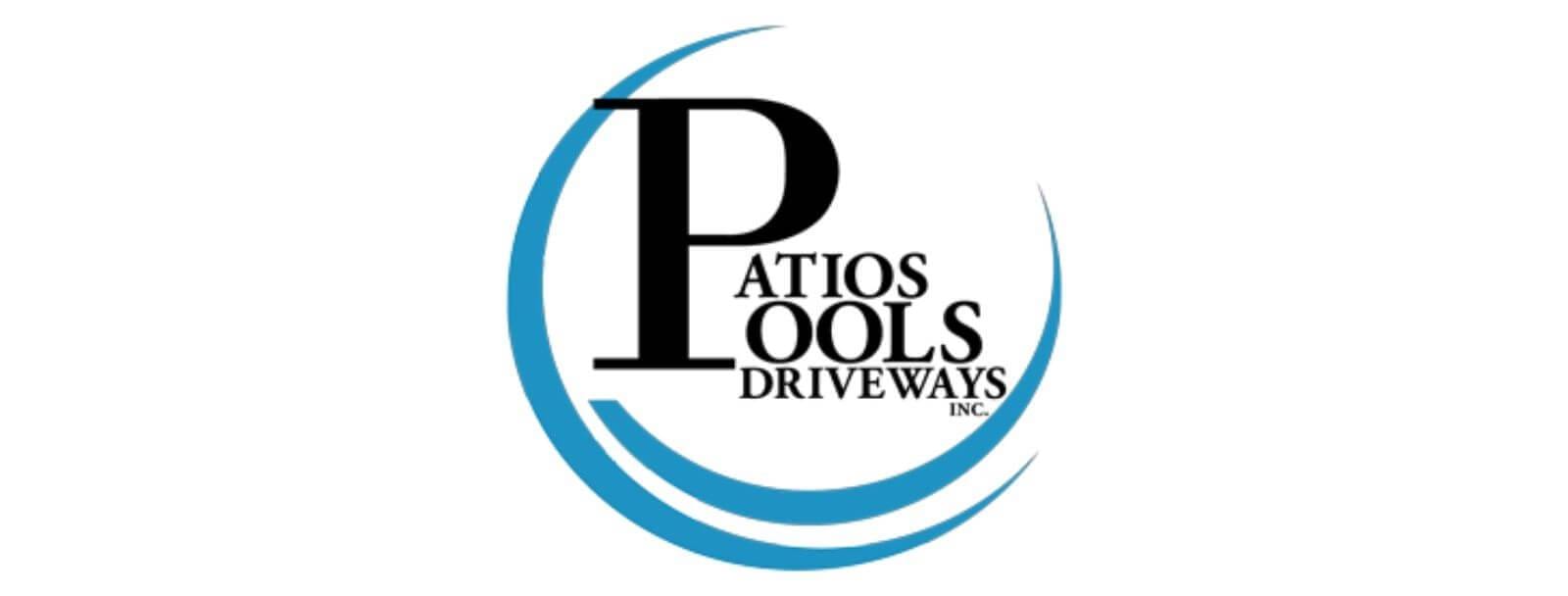
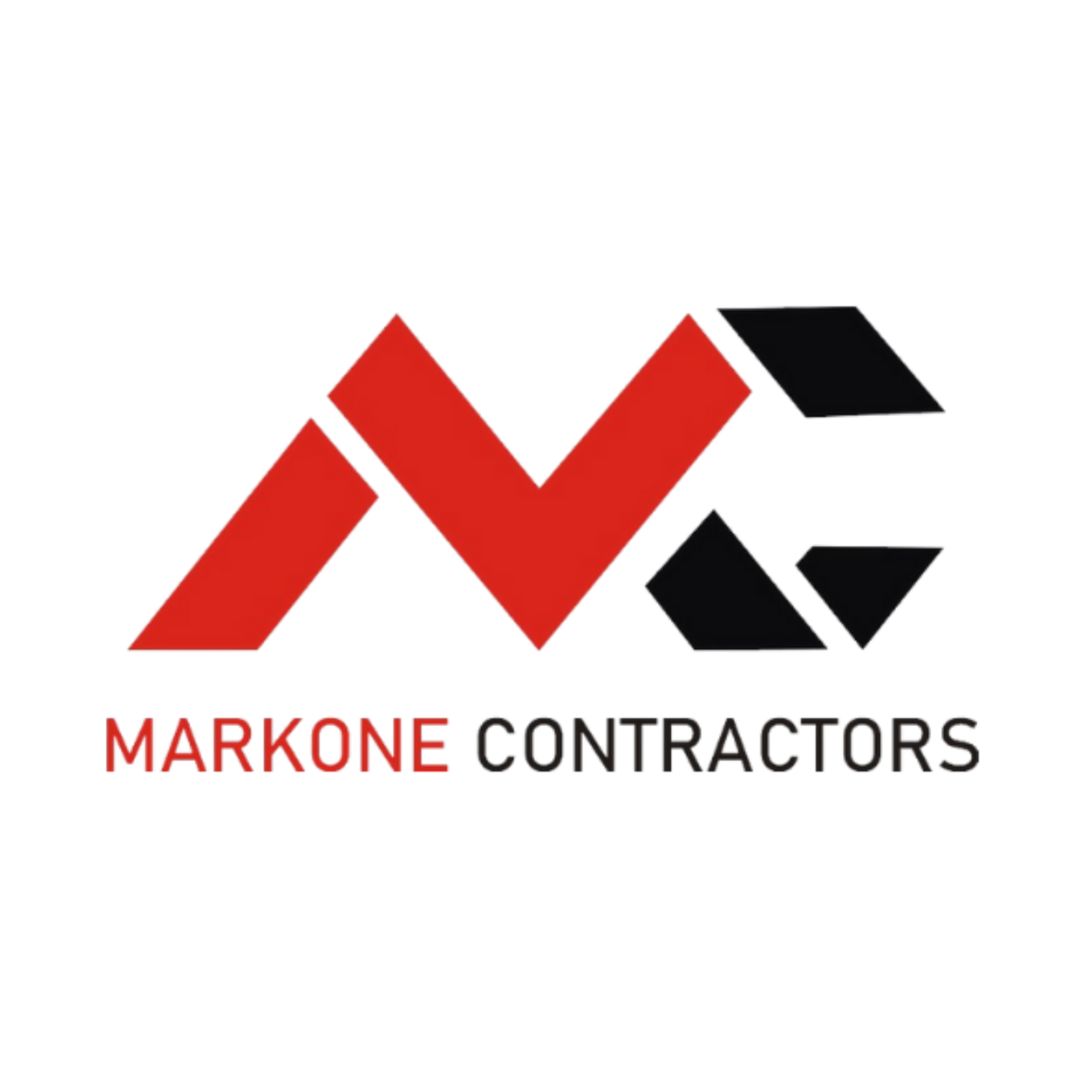

Process To Get Metal Siding Cost Estimate Report
Here I am going to share some steps to get metal siding cost estimate report.
-
You need to send your plan to us.
You can send us your plan on info@estimatorflorida.com
-
You receive a quote for your project.
Before starting your project, we send you a quote for your service. That quote will have detailed information about your project. Here you will get information about the size, difficulty, complexity and bid date when determining pricing.
-
Get Estimate Report
Our team will takeoff and estimate your project. When we deliver you’ll receive a PDF and an Excel file of your estimate. We can also offer construction lead generation services for the jobs you’d like to pursue further.