How Much Does It Cost To Replace Pilings?
Replacing pilings can incur significant costs, influenced by several key factors. Material expenses are a primary consideration, varying widely depending on the type chosen—wood ranging from $13 to $52 per linear foot, steel from $39 to $78, concrete from $26 to $65, and composite from $52 to $104. Labor costs also play a crucial role, typically ranging from $52 to $130 per hour, depending on the complexity of the installation and local labor market conditions. Additional costs such as permits, equipment rental, and site preparation further contribute to the total expense.
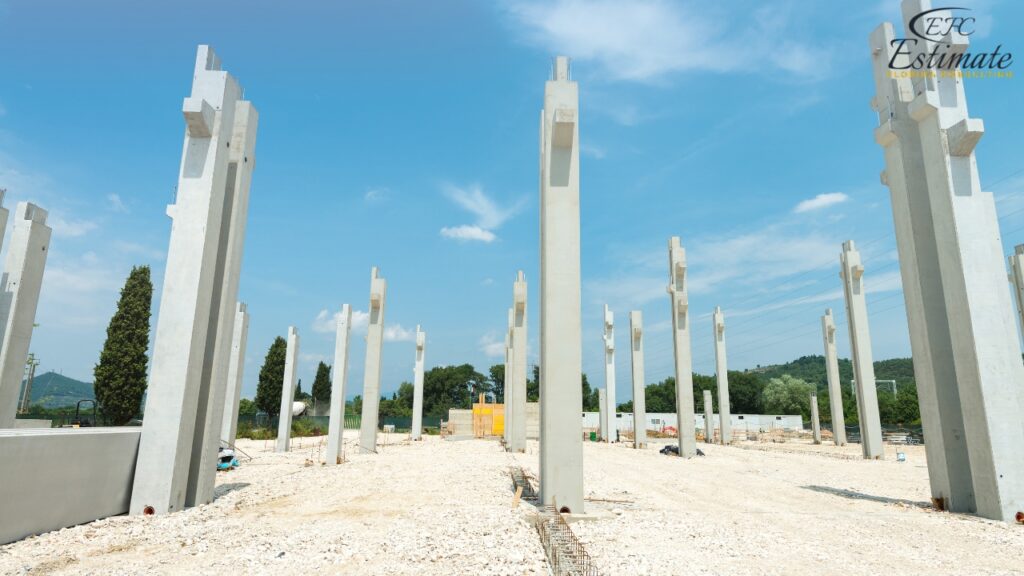
Factors Affecting Piling Replacement Costs
Several factors influence the cost of replacing pilings, and understanding these can help in budgeting and planning your project effectively:
Material Costs
Different materials come with different price tags. For example, wood is generally cheaper than steel or concrete, but it may not last as long, potentially leading to higher long-term costs. Material quality and local availability can also affect prices, with higher-grade materials costing more but offering better performance and longevity. Factors such as supply chain disruptions and market demand can also impact material costs. On average, material costs for pilings can range from $13 to $104 per linear foot, depending on the type.
Labor Costs
Labor costs vary depending on the complexity of the job and the local labor market. Skilled labor is essential for proper installation, which can impact overall costs. Complex projects requiring specialized techniques or equipment can drive up labor costs significantly. Additionally, labor costs can vary based on geographic location and the availability of skilled workers. Typically, labor costs for piling installation range from $52 to $130 per hour, with total labor expenses for a project varying widely based on its size and complexity.
Geographic Location
Costs can vary significantly based on the location due to differences in labor costs, availability of materials, and local regulations. Coastal areas may have higher costs due to increased demand for specialized materials. Additionally, remote or difficult-to-access locations can incur extra transportation and logistical expenses. Local building codes and regulations can also affect the overall cost. For example, projects in urban areas might incur additional costs due to limited access and higher labor rates, adding approximately 10-20% to the overall project cost.
Depth and Diameter of Pilings
Deeper and wider pilings require more material and labor, increasing the overall cost. The soil conditions also play a role, as more challenging conditions may require more robust solutions. Pilings for taller or heavier structures generally need to be deeper and stronger, adding to the cost. Soil tests and engineering assessments are often required to determine the appropriate specifications for the pilings. The cost increases proportionally with the depth and diameter, with deeper pilings potentially costing 50-100% more than standard ones.
Accessibility of the Site
Sites that are difficult to access can increase costs due to the need for specialized equipment and additional labor. Urban locations or areas with limited space can present additional challenges. Obstacles such as existing buildings, landscaping, or water bodies can complicate the installation process. In some cases, temporary infrastructure, such as access roads or staging areas, may need to be constructed. These additional requirements can add 10-30% to the overall project cost.
Permits and Regulations
Obtaining the necessary permits and adhering to local regulations can add to the cost. Different regions have varying requirements, and failing to comply can lead to fines and project delays. It’s important to account for the time and cost of obtaining permits and ensuring all regulatory requirements are met. The permitting process can involve multiple inspections and approvals, adding to the project timeline. Permit fees and regulatory compliance can add $650 to $6,500 or more, depending on the complexity and location of the project.
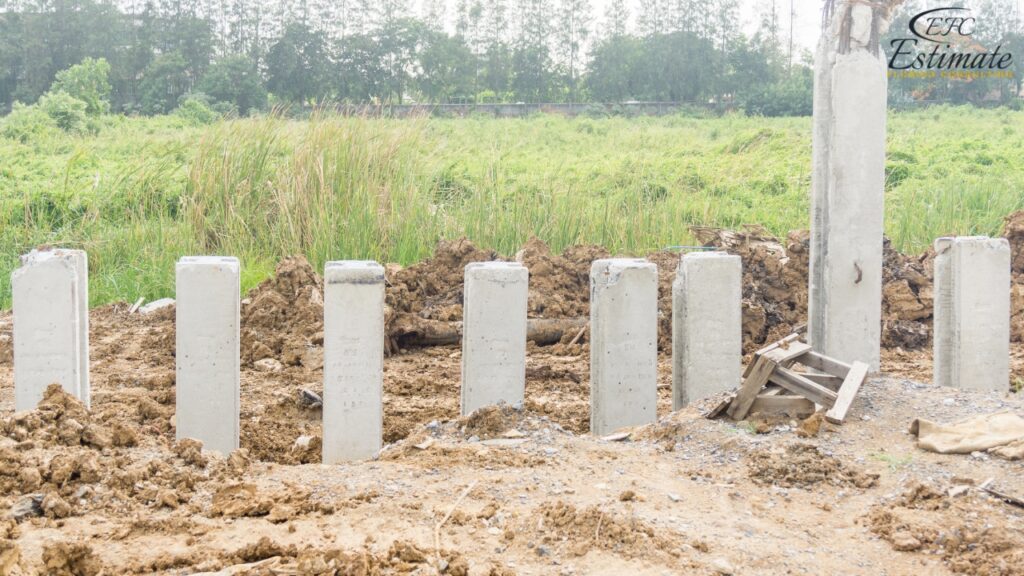
Types of Pilings and Their Costs
Understanding the costs associated with different types of pilings can help in making an informed decision:
Piling Type | Cost Per Linear Foot | Lifespan | Suitable For |
Wood | $13 – $52 | 15 – 30 years | Light-duty applications |
Steel | $39 – $78 | 50 – 100 years | Heavy structures, industrial use |
Concrete | $26 – $65 | 50 – 100 years | Residential and commercial projects |
Composite | $52 – $104 | 50 – 100+ years | Harsh environmental conditions |
Wood Pilings
Wood pilings are the most cost-effective option, typically ranging from $13 to $52 per linear foot. However, they have a shorter lifespan compared to other materials and may require more frequent replacement. They are best suited for light-duty applications and areas with low to moderate moisture exposure. The initial low cost can be appealing, but potential maintenance and replacement costs should be considered.
Steel Pilings
Steel pilings are durable and strong, costing between $39 and $78 per linear foot. They are suitable for heavy structures but can be prone to corrosion, necessitating protective coatings or treatments. Steel pilings are commonly used in industrial, commercial, and marine applications due to their load-bearing capacity and flexibility in design. The initial higher cost is offset by their strength and long lifespan, provided they are properly maintained.
Concrete Pilings
Concrete pilings are robust and long-lasting, with costs ranging from $26 to $65 per linear foot. They are ideal for both residential and commercial projects, offering a good balance between cost and durability. Pre-cast and pre-stressed concrete pilings are commonly used for their consistent quality and ease of installation. Concrete pilings are resistant to environmental factors, making them a durable choice for various applications.
Composite Pilings
Composite pilings, made from a mix of materials, offer durability and resistance to environmental factors. They cost between $52 and $104 per linear foot and are often used in areas with harsh environmental conditions. Their resistance to rot, corrosion, and marine organisms makes them ideal for waterfront and marine structures. While they are more expensive, their longevity and low maintenance needs can make them cost-effective over time.
Cost Breakdown
A detailed cost breakdown helps in understanding where the money goes during piling replacement:
Get 5 New Leads Next 7Days With Our System
- Multi-Family Building
- Hotel Building
- Hospital Building
- Warehouse Building
- High-Rise Building
- Shopping Complex
Material Costs Breakdown
Material costs include the price of the pilings themselves as well as any additional materials needed for installation, such as connectors and protective coatings. The quality and type of material directly affect the cost, with higher-quality materials offering better performance but at a higher price. For example, treated wood or galvanized steel may cost more upfront but provide greater longevity and protection. Material costs for different types of pilings can range from $13 to $104 per linear foot.
Material Type | Cost Range per Linear Foot | Notes |
Wood | $13 – $52 | Shorter lifespan, light-duty |
Steel | $39 – $78 | Durable but prone to corrosion |
Concrete | $26 – $65 | Robust, long-lasting |
Composite | $52 – $104 | Resistant to environmental factors |
Labor Costs Breakdown
Labor costs cover the wages of the workers and any additional expenses related to the replacement process, such as equipment rental and site preparation. Skilled labor for specialized tasks, such as driving deep pilings or working in difficult conditions, can significantly increase labor costs. Labor costs can also vary based on the complexity of the project and the time required for completion. On average, labor costs range from $52 to $130 per hour, with total labor expenses depending on the project’s size and complexity.
Labor Type | Cost Range per Hour | Notes |
General Labor | $52 – $78 | Basic installation and preparation tasks |
Skilled Labor | $91 – $130 | Specialized tasks and equipment operation |
Project Management | $104 – $130 | Oversight and coordination |
Additional Costs
These can include permits, equipment rental, site preparation, and unexpected expenses such as dealing with unforeseen site conditions. Additional costs may also arise from delays, weather-related interruptions, and the need for specialized equipment or techniques. Contingency budgets are essential to cover these potential extra costs and prevent budget overruns.
Additional Cost Type | Cost Range | Notes |
Permits | $650 – $6,500+ | Varies by location and complexity |
Equipment Rental | $1,000 – $5,000+ | Depending on the type and duration of equipment needed |
Site Preparation | $500 – $3,000+ | Includes clearing, grading, and access improvements |
Unexpected Expenses | $1,000 – $10,000+ | Contingency for unforeseen site conditions |
Steps to Replace Pilings
The piling replacement process involves several steps to ensure a successful outcome:
Inspection and Assessment
The first step is a thorough inspection to assess the condition of the existing pilings and determine the extent of the work needed. This may involve soil testing and structural analysis to identify the best type of piling and the required depth and diameter. Professional inspections can provide a detailed assessment and recommendations for the most suitable replacement approach. Costs for inspections and assessments typically range from $500 to $2,000.
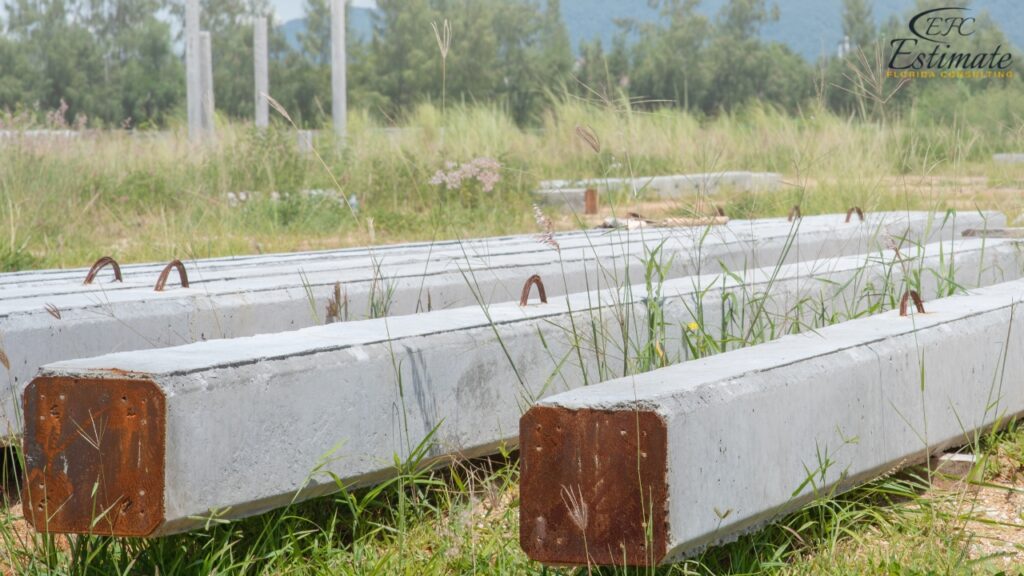
Planning and Permits
Next, you’ll need to plan the project and obtain the necessary permits from local authorities. This step ensures compliance with local regulations and helps avoid legal issues. Detailed planning also includes scheduling, budgeting, and selecting the appropriate materials and contractors. Coordination with local authorities is crucial to ensure all permits and approvals are secured in a timely manner. Permit costs can range from $650 to $6,500, depending on the project’s complexity and location.
Hiring Contractors
It’s essential to hire experienced contractors to ensure the work is done correctly and safely. Look for contractors with specific experience in piling replacement and good references. Contract negotiations should cover the scope of work, timelines, costs, and contingency plans. Choosing a reputable contractor can provide peace of mind and ensure high-quality work. Contractor costs can vary widely, but overall project management and labor can range from $10,000 to $50,000 or more, depending on the project’s scale.
Replacement Process
The actual replacement involves removing the old pilings and installing the new ones. This process can take several days to weeks, depending on the project’s complexity and site conditions. It includes mobilizing equipment, preparing the site, driving new pilings, and securing them properly. The cost for the replacement process itself can range from $20,000 to $100,000 or more, depending on the number and type of pilings, as well as site-specific challenges.
DIY vs Professional Replacement
Choosing between DIY and professional replacement involves weighing the pros and cons:
Pros and Cons of DIY
DIY replacement can save money but requires significant skill and knowledge. Mistakes can be costly and dangerous, and DIY projects may not meet local code requirements. It’s suitable for smaller, simpler projects where the owner has the necessary skills and equipment. DIY costs can be reduced by avoiding labor fees, but there are still significant expenses for materials and equipment.
DIY Cost Elements | Cost Range | Notes |
Material Costs | $13 – $104 per linear foot | Based on material type and quality |
Equipment Rental | $1,000 – $5,000+ | Depending on the type and duration of equipment |
Permit Fees | $650 – $6,500+ | Varies by location and complexity |
Pros and Cons of Hiring Professionals
Hiring professionals ensures the job is done correctly but comes at a higher cost. Professional contractors bring expertise, proper equipment, and adherence to safety standards. For complex or large-scale projects, professional replacement is often the best choice to ensure quality and compliance.
Professional Cost Elements | Cost Range | Notes |
Labor Costs | $52 – $130 per hour | Based on skill level and project complexity |
Contractor Fees | $10,000 – $50,000+ | Overall project management and specialized services |
Permit Fees | $650 – $6,500+ | Varies by location and complexity |
Cost-Saving Tips
Implementing cost-saving strategies can help manage expenses:
Choosing the Right Material
Selecting the appropriate material for your specific needs can save money in the long run. Consider factors such as durability, environmental conditions, and maintenance requirements. Opting for slightly more expensive but longer-lasting materials can reduce future replacement costs.
Scheduling During Off-Peak Seasons
Contractors may offer discounts during slower seasons when demand for their services is lower. Plan your project during these times to save on labor costs. Off-peak scheduling can also mean quicker project completion due to better contractor availability.
Negotiating with Contractors
Don’t be afraid to negotiate prices and seek multiple quotes. Getting at least three quotes can give you a good idea of the fair market price and help you find the best deal. Negotiation can also include discussing payment terms and potential discounts for larger projects.
Regular Maintenance to Extend Piling Life
Regular inspections and maintenance can prevent the need for early replacement. Addressing minor issues promptly can extend the life of your pilings and reduce long-term costs. Maintenance practices include treating wood pilings against rot and pests, applying protective coatings to steel, and monitoring for signs of wear.
Financing Options for Piling Replacement
There are several ways to finance piling replacement, each with its own benefits and drawbacks:
Personal Savings
Using personal savings is the most straightforward way to finance the project. It avoids interest payments and keeps you debt-free. However, it may not be feasible for larger projects requiring significant funds.
Loans and Mortgages
Home improvement loans or second mortgages can provide the necessary funds. Be sure to compare interest rates and terms to find the best option. Financing through loans allows spreading the cost over time but incurs interest expenses.
Government Grants and Subsidies
Check for any available government programs that offer financial assistance for such projects. These programs can significantly reduce your out-of-pocket expenses. Eligibility criteria and application processes vary, so research local, state, and federal options.
Potential Risks and Challenges
Replacing pilings involves potential risks and challenges that can impact the overall cost and timeline:
Unforeseen Damages
Unexpected damage during replacement can increase costs. Having a contingency budget can help manage these surprises.
Weather Conditions
Bad weather can delay the project and add to the expenses. Plan for potential weather-related delays and have a flexible timeline.
Delays and Overruns
Projects can take longer than expected, leading to higher labor costs. Clear communication with your contractor and a detailed project plan can help mitigate these risks.
Download Template For Pilings Project Breakdown
- Materials list updated to the zip code
- Fast delivery
- Data base of general contractors and sub-contractors
- Local estimators
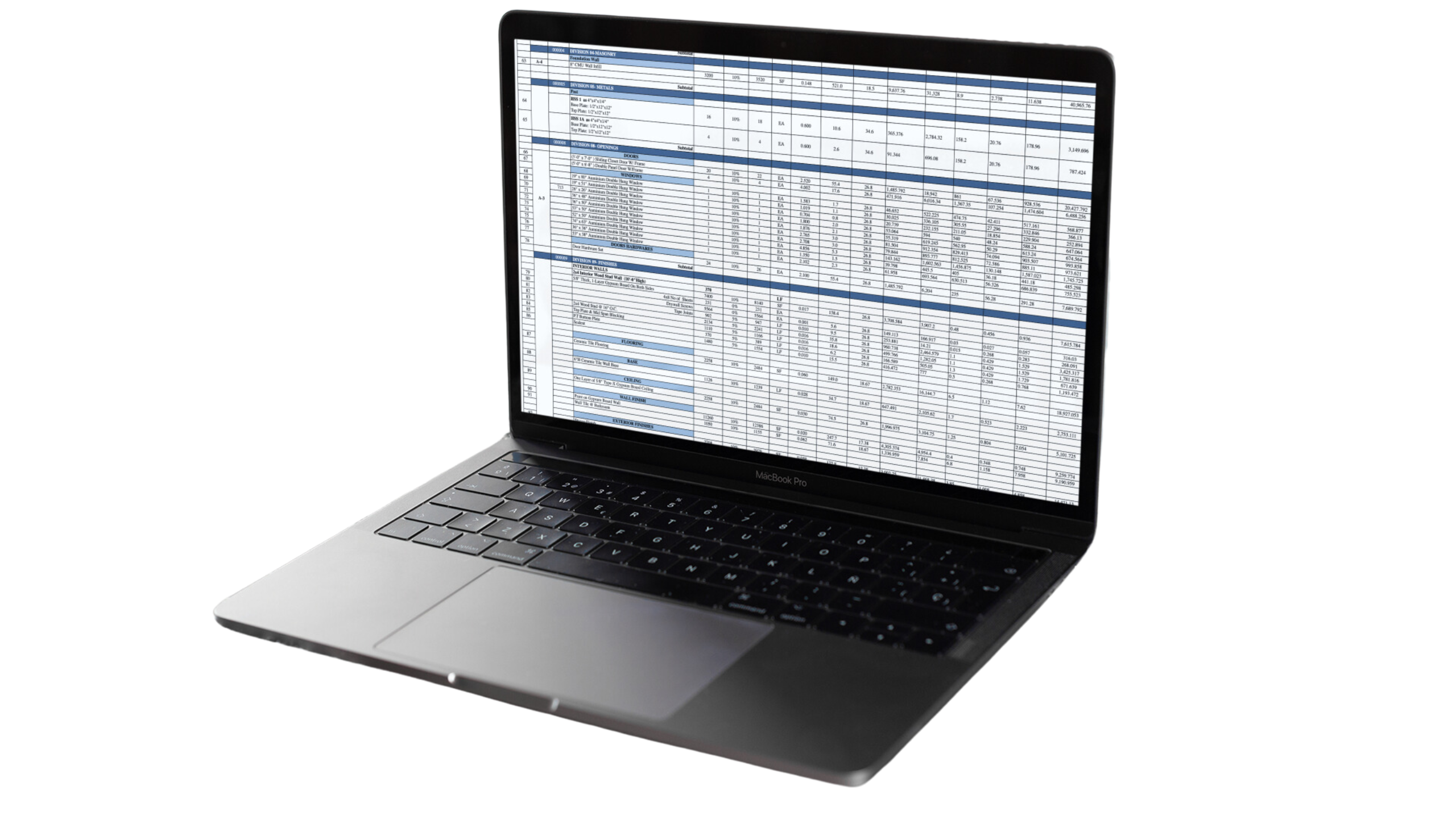
Importance of Regular Inspection and Maintenance
Preventing Future Costs
Regular inspections can catch issues early, preventing costly repairs. Scheduled maintenance can address wear and tear before it becomes a major problem.
Ensuring Structural Safety
Maintaining your pilings ensures the safety and stability of your structure. A proactive approach to maintenance can protect your investment and prevent accidents.
Environmental Considerations
Eco-friendly Materials
Using sustainable materials can reduce the environmental impact of your project. Look for materials that are recyclable or have a lower carbon footprint.
Sustainable Practices
Adopting eco-friendly practices during replacement can help preserve the environment. Consider methods that minimize waste and energy consumption.
Conclusion
Replacing pilings is a significant investment, but it’s crucial for maintaining the integrity and safety of your structure. By understanding the costs involved and taking steps to manage them, you can ensure a successful project without breaking the bank. Regular maintenance and inspections are key to extending the life of your pilings and avoiding future expenses. Proper planning, choosing the right materials, and hiring experienced professionals will contribute to a successful and cost-effective piling replacement project.
FAQs
The cost to replace pilings varies widely based on factors such as material, labor, geographic location, depth, diameter, site accessibility, and permits. Material costs range from $13 to $104 per linear foot, while labor costs range from $52 to $130 per hour. Total project costs can range from $20,000 to $100,000 or more.
Several factors influence the cost of replacing pilings:
- Material Costs: Wood, steel, concrete, and composite pilings each have different price ranges and lifespans.
- Labor Costs: Vary based on job complexity and local labor market rates.
- Geographic Location: Costs differ due to local labor costs, material availability, and regulations.
- Depth and Diameter of Pilings: Deeper and wider pilings require more materials and labor.
- Accessibility of the Site: Difficult-to-access sites increase costs.
- Permits and Regulations: Obtaining necessary permits can add to the cost.
Material Type | Cost Range per Linear Foot | Notes |
Wood | $13 – $52 | Shorter lifespan, light-duty |
Steel | $39 – $78 | Durable but prone to corrosion |
Concrete | $26 – $65 | Robust, long-lasting |
Composite | $52 – $104 | Resistant to environmental factors |
Labor Type | Cost Range per Hour | Notes |
General Labor | $52 – $78 | Basic installation and preparation tasks |
Skilled Labor | $91 – $130 | Specialized tasks and equipment operation |
Project Management | $104 – $130 | Oversight and coordination |
Additional Cost Type | Cost Range | Notes |
Permits | $650 – $6,500+ | Varies by location and complexity |
Equipment Rental | $1,000 – $5,000+ | Depending on the type and duration of equipment needed |
Site Preparation | $500 – $3,000+ | Includes clearing, grading, and access improvements |
Unexpected Expenses | $1,000 – $10,000+ | Contingency for unforeseen site conditions |
- Inspection and Assessment: Costs $500 – $2,000 for soil testing and structural analysis.
- Planning and Permits: Permit costs range from $650 to $6,500, depending on project complexity.
- Hiring Contractors: Contractor costs can range from $10,000 to $50,000+.
- Replacement Process: Total cost can range from $20,000 to $100,000 or more.
Google Reviews
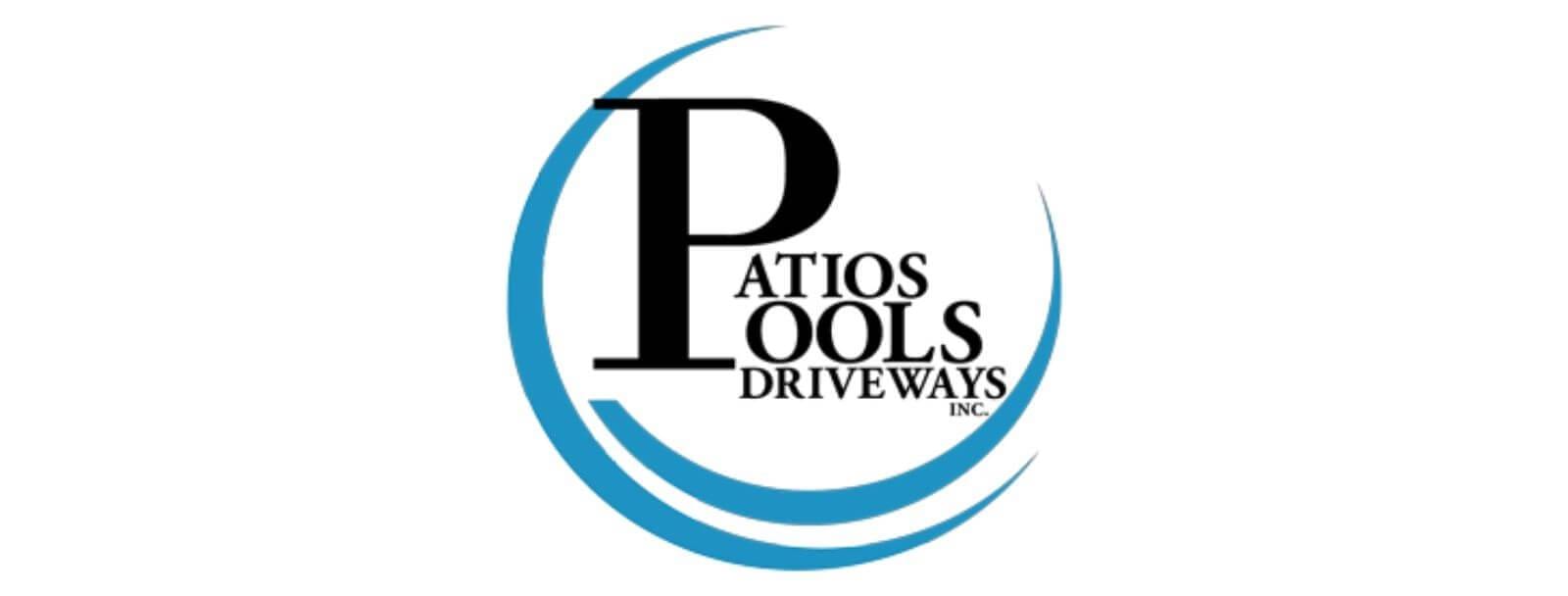
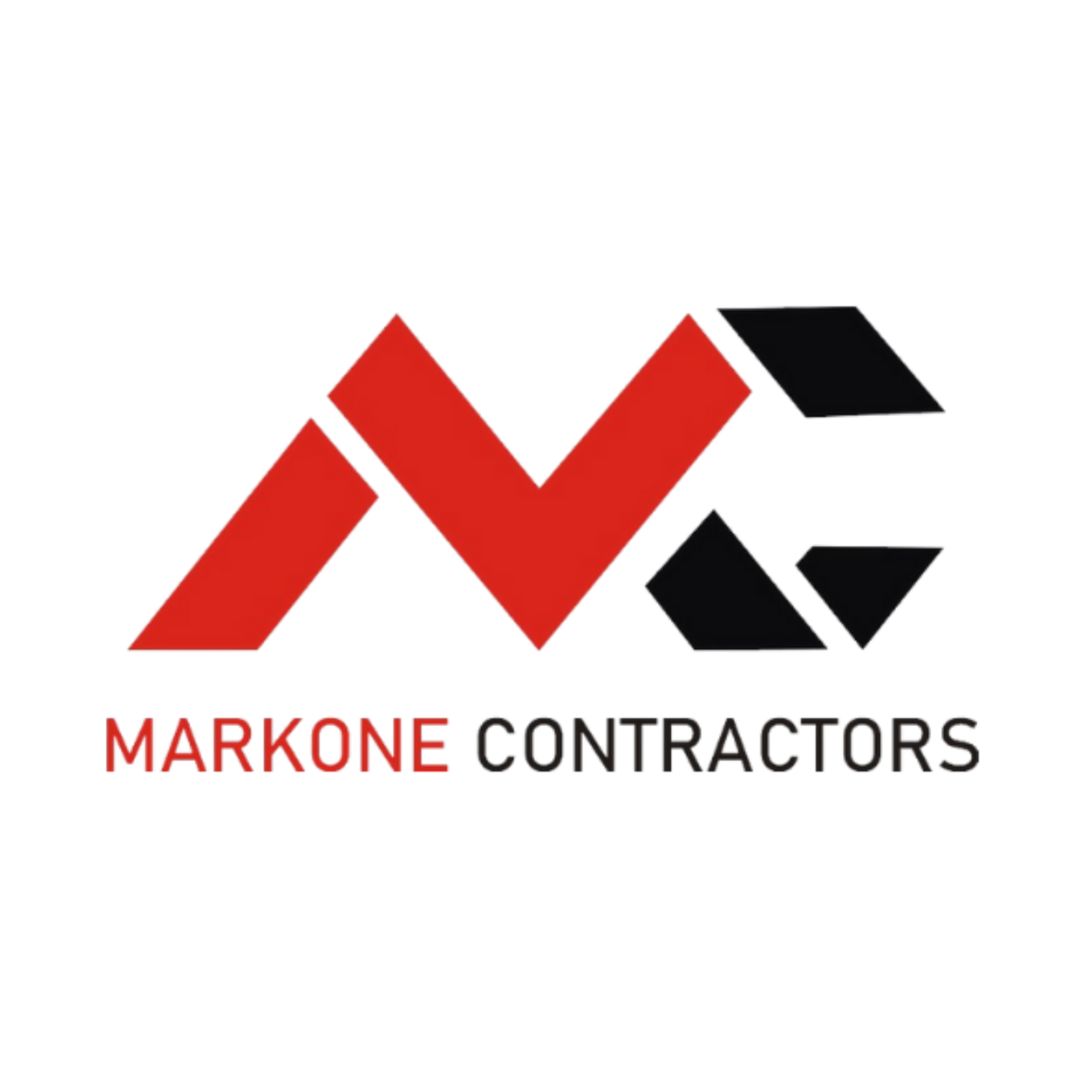

Process To Get Replace Pilings Estimate Report
Here I am going to share some steps to get replace pilings estimate report.
-
You need to send your plan to us.
You can send us your plan on info@estimatorflorida.com
-
You receive a quote for your project.
Before starting your project, we send you a quote for your service. That quote will have detailed information about your project. Here you will get information about the size, difficulty, complexity and bid date when determining pricing.
-
Get Estimate Report
Our team will takeoff and estimate your project. When we deliver you’ll receive a PDF and an Excel file of your estimate. We can also offer construction lead generation services for the jobs you’d like to pursue further.