How Much Does It Cost to Pour a Concrete Slab?
Pouring a concrete slab is a common project for homeowners and builders, whether for a new patio, driveway, foundation, or other purposes. Understanding the costs involved in pouring a concrete slab can help you plan and budget effectively. In this blog, we will explore the various factors that contribute to the cost of pouring a concrete slab, providing detailed breakdowns and cost estimates to help you understand the financial commitment required for such a project. With the right information, you can ensure a successful and cost-effective concrete project, enhancing the value and functionality of your property.
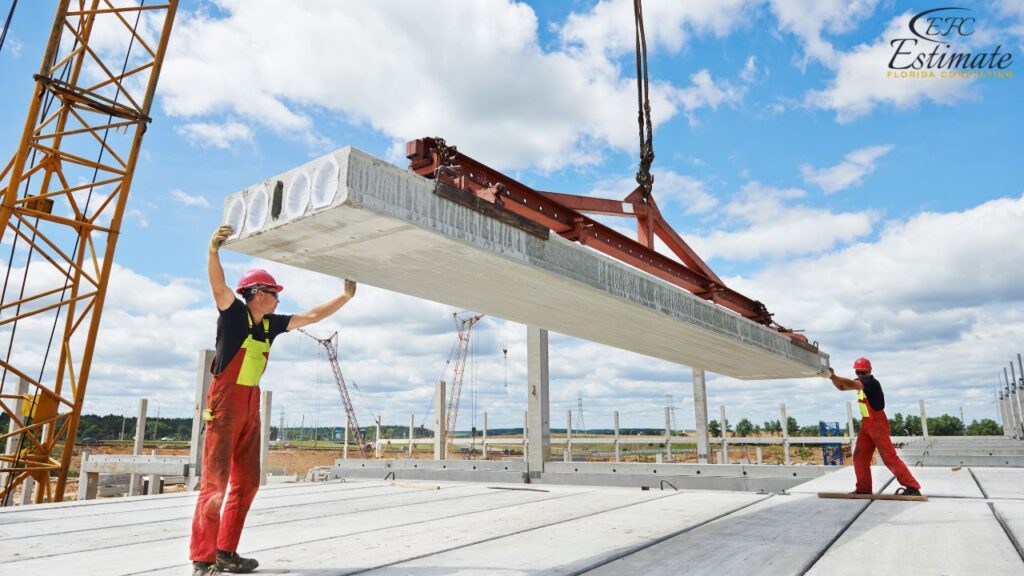
Proper planning and understanding of all potential costs can help avoid unexpected expenses and delays, making the entire process smoother and more efficient.
Benefits of a Concrete Slab
Concrete slabs offer several benefits that make them a popular choice for various construction projects:
- Durability: Concrete is a strong and durable material that can withstand heavy loads and harsh weather conditions, making it ideal for foundations, driveways, and patios. The longevity of concrete means that once installed, it can last for decades with minimal maintenance, providing long-term value. Its resistance to wear and tear makes it a reliable choice for high-traffic areas and heavy-duty applications.
- Versatility: Concrete slabs can be used for a wide range of applications, including floors, foundations, patios, driveways, and more. They can be customized with various finishes and designs to suit different needs and aesthetics. This versatility makes concrete a preferred choice for both residential and commercial projects. The ability to stain, stamp, or paint concrete allows for creative and attractive designs that can complement the overall look of your property.
- Low Maintenance: Once poured and cured, concrete slabs require minimal maintenance, providing long-term value and cost savings. Regular sealing and occasional cleaning can keep the surface in good condition. Compared to other materials, concrete does not need frequent repairs or replacements, reducing ongoing maintenance costs. Simple maintenance tasks, such as sealing and cleaning, can keep the concrete looking new and extend its lifespan.
- Energy Efficiency: Concrete slabs can help improve energy efficiency by providing thermal mass, which helps regulate indoor temperatures. This can lead to lower energy costs and increased comfort in buildings with concrete slab foundations. The thermal mass of concrete absorbs heat during the day and releases it at night, creating a more stable indoor environment. This property can be particularly beneficial in climates with significant temperature fluctuations, reducing the need for heating and cooling.
Average Cost Breakdown
The cost of pouring a concrete slab can vary widely based on several factors, including the size and thickness of the slab, the type of concrete used, and local labor rates. On average, the cost to pour a concrete slab can range from $7,800 to $25,480 or more. Here’s a general cost breakdown:
Component | Estimated Cost (in dollars) |
Materials | $2,340 – $10,140 |
Labor | $5,460 – $15,340 |
Total Cost | $7,800 – $25,480 |
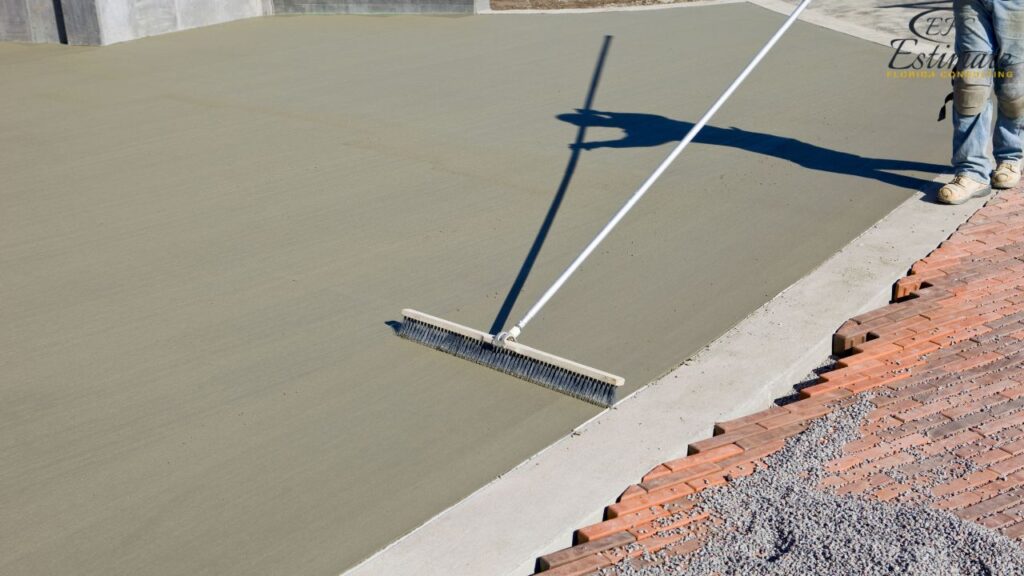
Factors Affecting the Cost of Pouring a Concrete Slab
Several factors can influence the cost of pouring a concrete slab, including:
Size and Thickness of the Slab
The size and thickness of the slab are primary factors in determining the cost. Larger and thicker slabs require more materials and labor, increasing the overall expense. For example, a small slab of 500 square feet with a standard thickness of 4 inches may cost between $7,800 and $15,640, while a larger slab of 1,000 square feet could cost between $15,640 and $25,480. Accurately measuring the area and determining the required thickness is essential for obtaining precise cost estimates. Larger projects also tend to incur higher labor costs due to the increased time and effort required. Moreover, thicker slabs are often necessary for areas that will bear heavy loads, such as driveways or garage floors, which adds to the overall cost.
Type of Concrete
The type of concrete used can also impact the cost. Standard concrete is typically less expensive, while specialty concretes, such as high-strength, reinforced, or decorative concrete, can increase the cost. The choice of concrete should be based on the specific requirements of the project. High-strength and reinforced concrete are ideal for heavy load-bearing applications, while decorative concrete can add aesthetic value to patios and driveways. Specialty concretes may also require specific installation techniques, adding to the labor costs. Additionally, the use of colored or stamped concrete can enhance the visual appeal but also increase the overall project cost.
Site Preparation
Site preparation involves clearing the area, leveling the ground, and installing forms to hold the concrete. The complexity of site preparation can vary based on the condition of the site and any obstacles that need to be removed. Site preparation can add $1,300 to $5,200 to the overall cost. Proper site preparation ensures that the slab is level and stable, which is crucial for the durability and performance of the concrete. This step may also involve soil testing and compaction to ensure a solid foundation. In some cases, additional excavation or grading may be required to create a suitable base for the concrete slab, further increasing costs.
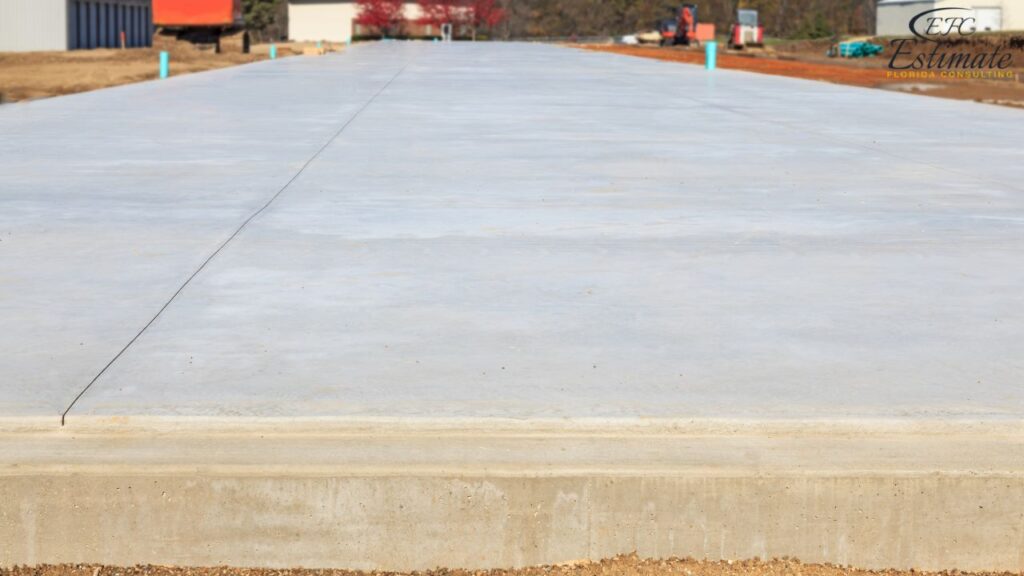
Reinforcement
Reinforcement, such as steel rebar or wire mesh, is often used to strengthen the concrete slab and prevent cracking. The cost of reinforcement can vary depending on the type and amount used. Reinforcement can add $780 to $2,600 to the total cost. Reinforcing the concrete slab is especially important for areas that will bear heavy loads, such as driveways and foundations. Proper reinforcement helps distribute the weight and stresses, reducing the likelihood of cracks and structural failures. The choice of reinforcement material and design should be based on the specific load requirements and environmental conditions of the project.
Cost Breakdown by Component
Materials
The cost of materials includes the concrete itself, reinforcement, and other necessary supplies. High-quality materials can increase the cost but provide better durability and longevity. Using high-quality concrete and reinforcement ensures that the slab can withstand heavy loads and adverse conditions. Materials also include additional items such as formwork, curing compounds, and finishing tools. Investing in high-quality materials can prevent future issues and repairs, ultimately saving money in the long run.
Cost Breakdown for Materials:
Cost Component | Estimated Cost (in dollars) |
Concrete (8-30 cubic yards) | $1,950 – $7,800 |
Reinforcement | $780 – $2,600 |
Additional Supplies | $390 – $1,040 |
Total Cost | $2,340 – $10,140 |
Download Template For Concrete Slab Project Breakdown
- Materials list updated to the zip code
- Fast delivery
- Data base of general contractors and sub-contractors
- Local estimators
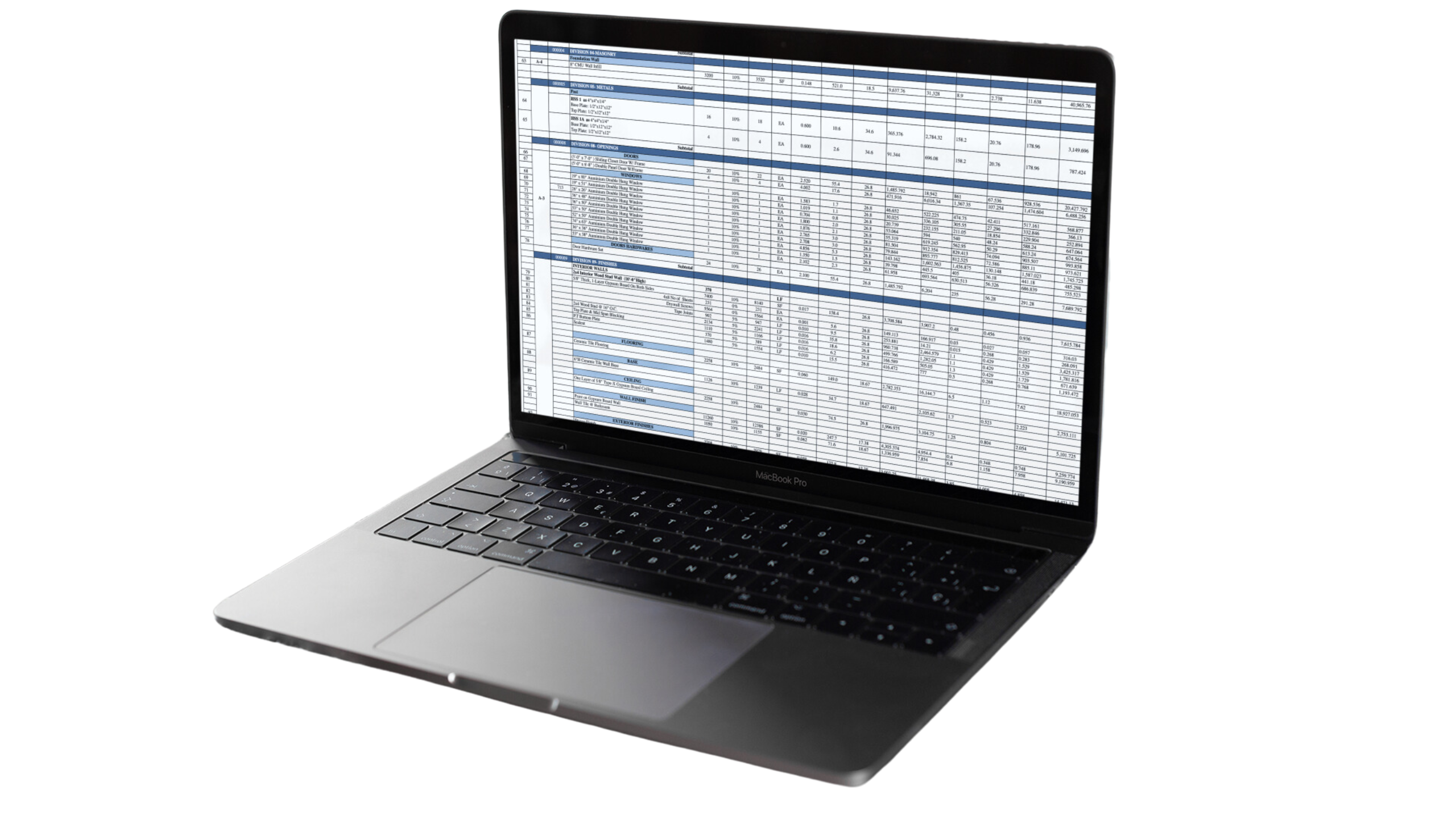
Labor
Labor costs include the time and expertise required to prepare the site, pour the concrete, and finish the surface. The total labor cost can vary based on the complexity of the project and the rates charged by local contractors. Skilled labor is essential for achieving a high-quality result, and the use of proper tools and techniques ensures the durability and appearance of the concrete slab. Labor costs also include post-pouring tasks such as curing, sealing, and potential repair work. Hiring experienced professionals can ensure that the job is done correctly, reducing the risk of costly mistakes and future repairs.
Cost Breakdown for Labor:
Cost Component | Estimated Cost (in dollars) |
Site Preparation | $1,300 – $5,200 |
Concrete Pouring | $2,600 – $7,800 |
Finishing and Curing | $1,560 – $3,120 |
Total Cost | $5,460 – $15,340 |
Additional Costs to Consider
In addition to the basic materials and labor costs, several other expenses can influence the total cost of pouring a concrete slab:
Permits and Inspections
Depending on local regulations, you may need permits and inspections for pouring a concrete slab. These fees can vary widely, typically ranging from $260 to $1,040. Ensuring compliance with local building codes and regulations is essential for avoiding legal issues and ensuring the safety and integrity of the concrete slab. Obtaining the necessary permits and passing inspections can provide peace of mind that the project is done correctly and legally. Permits and inspections help ensure that the project meets all safety and quality standards. It’s important to check with local authorities to understand the specific requirements and fees for your area.
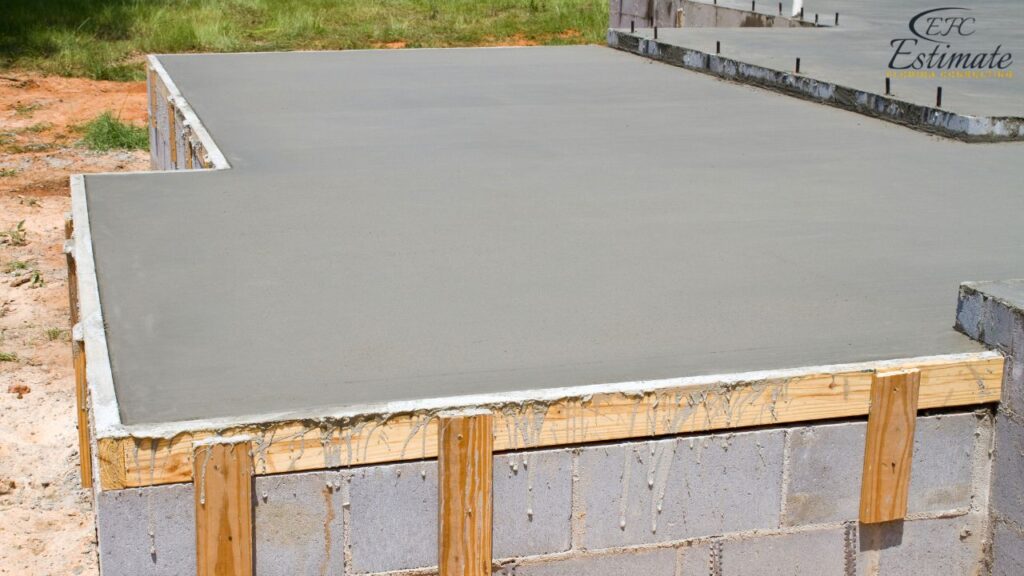
Drainage Solutions
Proper drainage is essential to prevent water from pooling on the slab surface, which can lead to damage and reduced lifespan. Installing drainage solutions such as French drains, culverts, or catch basins can add $520 to $2,080 to the overall cost. Effective drainage solutions help maintain the integrity of the slab by directing water away from the surface, reducing the risk of cracks and other damage. Drainage solutions are especially important in areas prone to heavy rainfall or poor soil drainage. Proper drainage design and installation can prevent future water damage and extend the lifespan of the concrete slab.
Sealing and Waterproofing
Sealing and waterproofing the concrete slab can help protect it from moisture, stains, and other environmental factors. The cost of sealing typically ranges from $0.50 to $1.50 per square foot, adding $520 to $1,560 to the overall cost for a standard slab. Regular sealing can help maintain the appearance and durability of the slab, reducing long-term maintenance costs. Sealing also helps protect the concrete from chemical spills, oil stains, and other contaminants that can degrade the surface over time. Waterproofing can be particularly important in areas where moisture penetration is a concern, such as basements or outdoor patios.
Example Cost Calculation
Let’s consider an example of pouring a 1,000 square foot concrete slab:
Component | Estimated Cost (in dollars) |
Materials | $2,340 – $10,140 |
Labor | $5,460 – $15,340 |
Permits and Inspections | $260 – $1,040 |
Drainage Solutions | $520 – $2,080 |
Sealing and Waterproofing | $520 – $1,560 |
Total Cost | $9,100 – $30,160 |
Get 5 New Leads Next 7Days With Our System
- Multi-Family Building
- Hotel Building
- Hospital Building
- Warehouse Building
- High-Rise Building
- Shopping Complex
Conclusion
Pouring a concrete slab is a significant investment that requires careful planning and consideration of various factors. The cost can vary widely depending on the size and thickness of the slab, the type of concrete used, the complexity of the site preparation, and local labor rates. By understanding these factors and budgeting for additional expenses such as permits, drainage solutions, and sealing, homeowners can make informed decisions and ensure the successful completion of their concrete project. Investing in high-quality materials and professional services can provide a durable, long-lasting, and visually appealing concrete slab, enhancing the overall value and functionality of the property. Proper planning and maintenance can prevent costly repairs and ensure that the concrete slab remains in excellent condition for years to come. Regular inspections and timely maintenance can further extend the lifespan and performance of the concrete slab, providing continued value and functionality.
Frequently Asked Questions (FAQs)
The time required to pour and cure a concrete slab can vary depending on the size and complexity of the project. On average, it can take 1 to 2 days to pour the slab, with additional time needed for curing, which typically takes 7 to 28 days. The curing process is essential to ensure the concrete reaches its full strength and durability.
While it is possible to pour a concrete slab yourself, it is not recommended unless you have experience with similar projects. Hiring a professional ensures the job is done correctly and safely, providing better and longer-lasting results. DIY projects can often lead to mistakes and issues that require costly repairs.
The thickness of a concrete slab depends on its intended use. For residential patios and driveways, a thickness of 4 inches is typically sufficient. For heavier loads, such as garage floors or commercial applications, a thickness of 6 inches or more may be required. Thicker slabs provide additional strength and durability for heavy-duty applications.
The type of concrete used for a slab depends on its intended use and the specific requirements of the project. Standard concrete is suitable for most residential applications, while high-strength or reinforced concrete may be necessary for heavier loads or commercial projects. Decorative concrete can be used for aesthetic purposes in patios and driveways.
Maintaining a concrete slab involves regular cleaning, sealing, and inspections for cracks or damage. Promptly addressing any issues can prevent further damage and extend the lifespan of the slab. Regular maintenance helps keep the concrete in good condition and ensures it remains durable and visually appealing.
Google Reviews
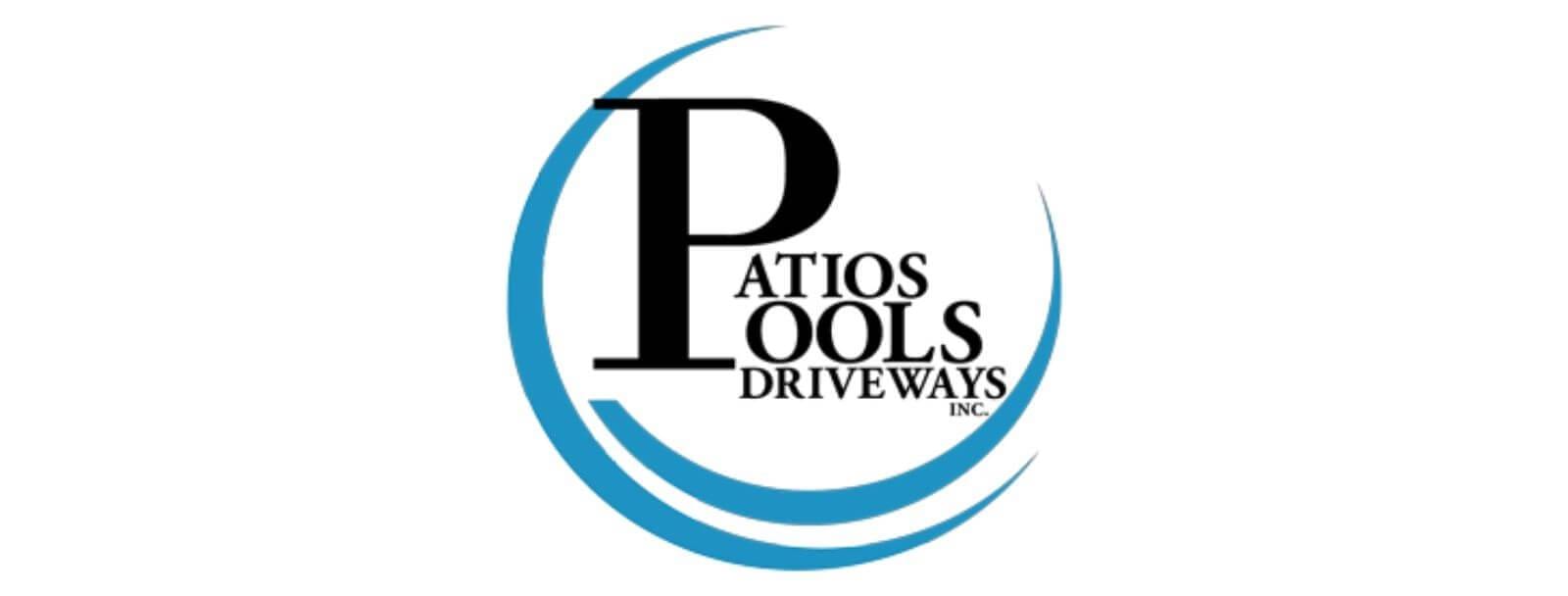
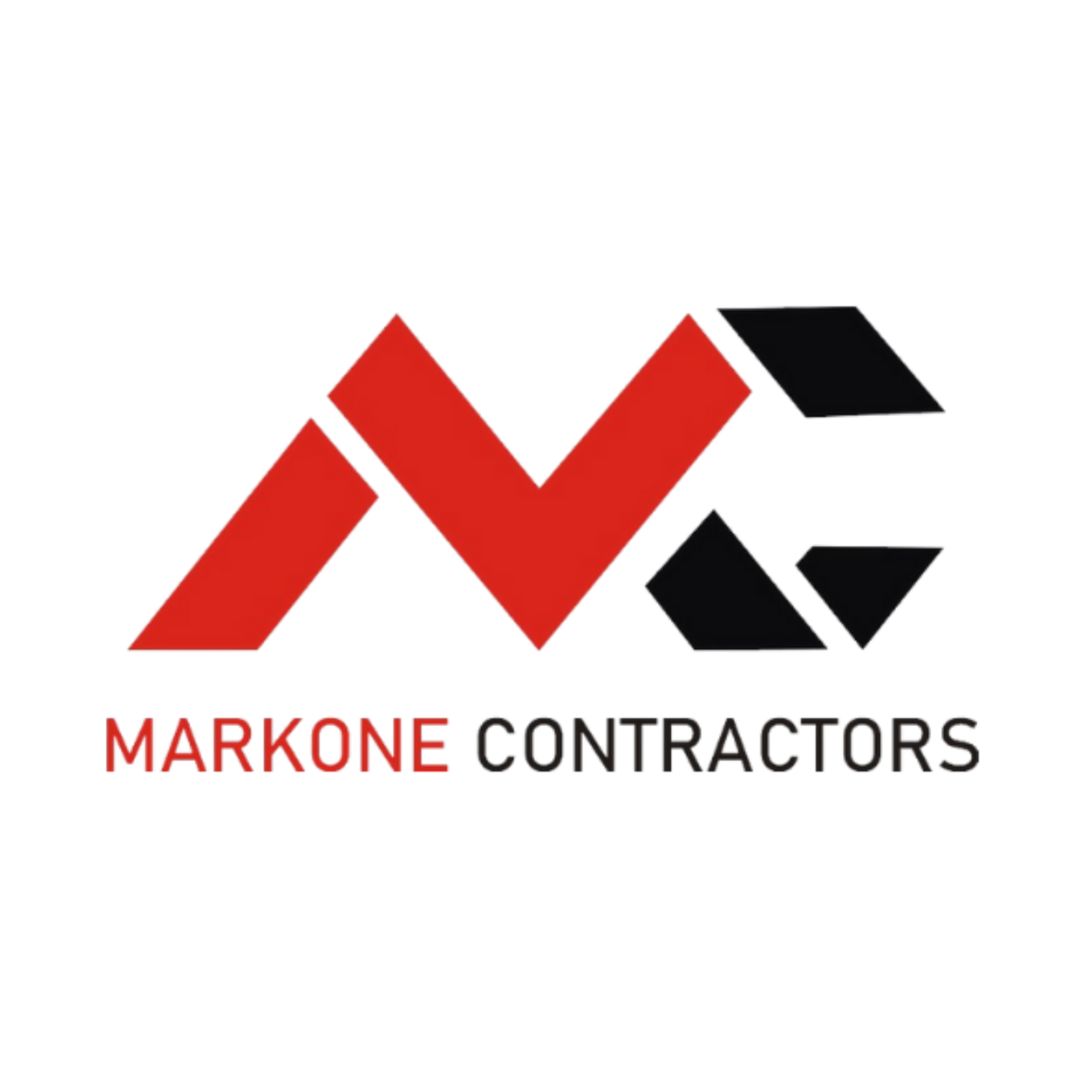

Process To Get Concrete Slab Cost Estimate Report
Here I am going to share some steps to get your concrete slab cost estimate report.
-
You need to send your plan to us.
You can send us your plan on info@estimatorflorida.com
-
You receive a quote for your project.
Before starting your project, we send you a quote for your service. That quote will have detailed information about your project. Here you will get information about the size, difficulty, complexity and bid date when determining pricing.
-
Get Estimate Report
Our team will takeoff and estimate your project. When we deliver you’ll receive a PDF and an Excel file of your estimate. We can also offer construction lead generation services for the jobs you’d like to pursue further.