How Much Does It Cost to Insulate a 20'x20' Garage?
Insulating a 20’x20′ garage typically costs between $1,120 and $4,312, averaging $2.80 to $10.78 per square foot. This price includes materials like fiberglass batts ($0.50 to $1.50 per sq ft), spray foam ($1.00 to $4.50 per sq ft), or rigid foam boards ($1.50 to $3.00 per sq ft), and professional installation. Costs can vary based on the insulation type, local labor rates, and any additional work such as sealing gaps or installing vapor barriers. Proper insulation improves energy efficiency, reduces noise, and enhances the garage’s overall comfort. Always obtain multiple quotes and choose high-quality materials for the best results.
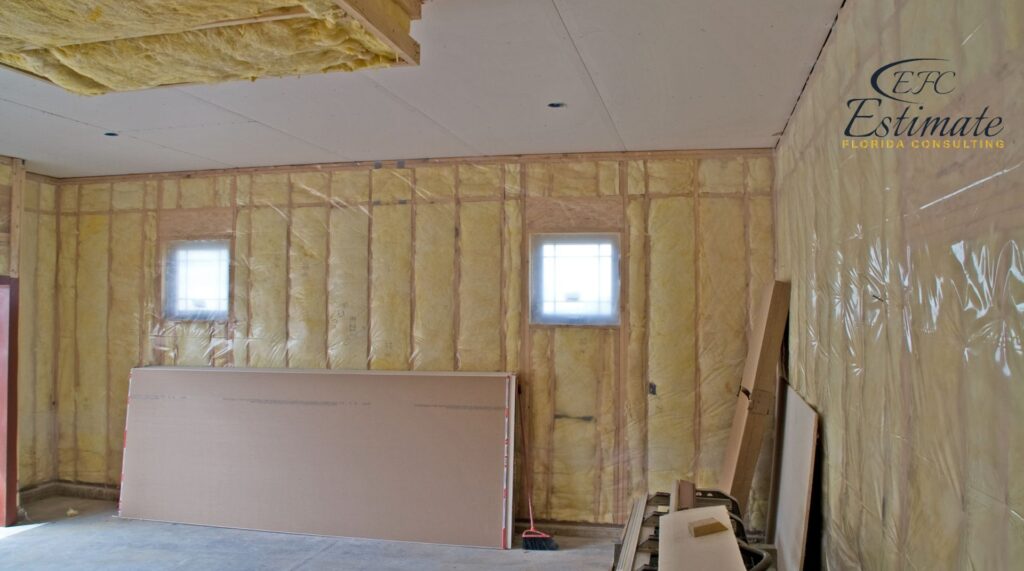
Cost Breakdown for Insulating a 20'x20' Garage
Materials
The cost of materials is a significant portion of the total cost for insulating a garage. Here is an estimate of typical material costs for a 20’x20′ garage (400 square feet):
Insulation Type | Cost per Sq Ft (in dollars) | Total Cost for 400 Sq Ft (in dollars) |
Fiberglass Batts | $0.70 – $1.40 | $280 – $560 |
Spray Foam | $2.10 – $4.20 | $840 – $1,680 |
Rigid Foam Boards | $1.40 – $2.80 | $560 – $1,120 |
Cellulose | $1.12 – $2.10 | $448 – $840 |
Labor
Labor costs for installing insulation can vary based on the type of insulation and the complexity of the job. Here’s an estimate of labor costs:
Insulation Type | Labor Cost per Sq Ft (in dollars) | Total Labor Cost for 400 Sq Ft (in dollars) |
Fiberglass Batts | $0.70 – $1.40 | $280 – $560 |
Spray Foam | $1.40 – $2.80 | $560 – $1,120 |
Rigid Foam Boards | $1.05 – $2.10 | $420 – $840 |
Cellulose | $1.05 – $2.10 | $420 – $840 |
Additional Costs
Additional costs can include vapor barriers, drywall, and finishing materials, as well as any necessary repairs or improvements to the garage structure. Here’s an estimate of additional costs:
Additional Component | Cost (in dollars) | Total Cost (in dollars) |
Vapor Barrier | $0.21 – $0.42 per sq ft | $84 – $168 |
Drywall | $0.56 – $0.91 per sq ft | $224 – $364 |
Finishing Materials | $0.28 – $0.70 per sq ft | $112 – $280 |
Repairs/Improvements | Varies | $140 – $700 |
Get 5 New Leads Next 7Days With Our System
- Multi-Family Building
- Hotel Building
- Hospital Building
- Warehouse Building
- High-Rise Building
- Shopping Complex
Detailed Cost Breakdown by Insulation Type
Fiberglass Batts
Fiberglass batts are one of the most cost-effective insulation options. They are easy to install and provide good thermal insulation. Here’s a detailed cost breakdown for fiberglass batts:
Component | Estimated Cost (in dollars) |
Material Cost | $280 – $560 |
Labor Cost | $280 – $560 |
Vapor Barrier | $84 – $168 |
Drywall | $224 – $364 |
Finishing Materials | $112 – $280 |
Fiberglass batts are versatile and widely used for their affordability and ease of installation. They come in various sizes and can be fitted between studs and joists, providing effective insulation for walls and ceilings. However, their performance can be compromised if not installed correctly, as gaps and compression can reduce their insulating properties. Despite these potential issues, fiberglass batts remain a popular choice for many homeowners due to their cost-effectiveness and ease of handling. When installed properly, they can provide a significant improvement in thermal comfort and energy efficiency.
Spray Foam
Spray foam insulation offers excellent thermal insulation and air sealing but is more expensive. Here’s a detailed cost breakdown for spray foam:
Component | Estimated Cost (in dollars) |
Material Cost | $840 – $1,680 |
Labor Cost | $560 – $1,120 |
Vapor Barrier | Not typically required |
Drywall | $224 – $364 |
Finishing Materials | $112 – $280 |
Spray foam insulation expands upon application, filling gaps and cracks, and creating an airtight seal. It provides superior thermal performance and moisture resistance, making it an excellent choice for energy efficiency. However, it requires professional installation and is more expensive than other options, making it suitable for projects where maximum insulation performance is desired. The long-term benefits of spray foam, including improved energy savings and enhanced structural integrity, can justify the higher upfront costs. Additionally, spray foam’s ability to prevent air leakage can significantly improve indoor air quality and comfort.
Rigid Foam Boards
Rigid foam boards provide a high R-value per inch and are effective for both thermal insulation and moisture control. Here’s a detailed cost breakdown for rigid foam boards:
Component | Estimated Cost (in dollars) |
Material Cost | $560 – $1,120 |
Labor Cost | $420 – $840 |
Vapor Barrier | $84 – $168 |
Drywall | $224 – $364 |
Finishing Materials | $112 – $280 |
Rigid foam boards are durable and resistant to moisture, making them suitable for walls, floors, and ceilings. They are available in various thicknesses and can be cut to fit specific spaces, providing versatile insulation solutions. While they offer high insulating properties, their installation can be labor-intensive, especially in irregular spaces. Rigid foam boards are ideal for applications where space is limited but high insulation value is required, such as in basement walls or exterior sheathing. Their high compressive strength also makes them suitable for use in load-bearing applications, adding to their versatility and functionality.
Cellulose
Cellulose insulation is made from recycled materials and offers good thermal properties. Here’s a detailed cost breakdown for cellulose:
Component | Estimated Cost (in dollars) |
Material Cost | $448 – $840 |
Labor Cost | $420 – $840 |
Vapor Barrier | $84 – $168 |
Drywall | $224 – $364 |
Finishing Materials | $112 – $280 |
Cellulose insulation is typically blown into walls and attics, providing a dense, energy-efficient barrier. It is treated with fire retardants and offers good soundproofing properties. However, installation requires specialized equipment and skills, making professional installation necessary for optimal performance. Despite the higher installation complexity, cellulose is an eco-friendly option that provides excellent thermal and acoustic insulation. Its use of recycled materials also makes it a sustainable choice, appealing to environmentally conscious homeowners. Proper installation of cellulose insulation can result in significant energy savings and enhanced comfort.
Factors Influencing the Cost of Insulating a Garage
Type of Insulation
The type of insulation chosen will significantly impact the overall cost. Common types of insulation include fiberglass batts, spray foam, rigid foam boards, and cellulose. Each type has its own advantages and cost implications:
- Fiberglass Batts: Cost-effective and easy to install, but may not provide the highest R-value. They are typically used in walls, ceilings, and floors, and are available in pre-cut sizes, making installation straightforward. However, fiberglass batts can leave gaps and voids if not installed correctly, reducing their effectiveness. Additionally, they may lose some insulating properties if they become compressed or damp, which can lead to reduced energy efficiency and potential issues with mold or mildew. Despite these potential drawbacks, fiberglass batts remain a popular choice for many homeowners due to their affordability and ease of installation.
- Spray Foam: Offers excellent insulation and air sealing but is more expensive. Spray foam expands upon application, filling gaps and cracks, providing a superior barrier against air infiltration. It is available in open-cell and closed-cell varieties, with closed-cell offering a higher R-value and better moisture resistance. Spray foam also adds structural strength to walls, making it a versatile choice for both insulation and reinforcement. The initial higher cost of spray foam can be offset by its long-term benefits in energy savings and improved structural integrity. Furthermore, spray foam’s ability to prevent air leakage can enhance indoor air quality by reducing the infiltration of outdoor pollutants and allergens.
- Rigid Foam Boards: Provide high R-value per inch but can be costlier and harder to install in some areas. Rigid foam boards are often used in foundation walls and under slabs due to their moisture-resistant properties. They come in various thicknesses and can be cut to fit specific spaces, making them versatile but potentially labor-intensive to install. They are also effective in providing a continuous insulation layer that reduces thermal bridging. Rigid foam boards can be used in combination with other insulation types to achieve optimal performance and cost efficiency. Additionally, their high compressive strength makes them suitable for use in load-bearing applications, adding to their versatility.
- Cellulose: Made from recycled materials and offers good insulation properties, but can be more challenging to install. Cellulose is typically blown into walls and attics, providing a dense, energy-efficient barrier. It is also treated with fire retardants, making it a safer option for residential use. However, installation requires specialized equipment and skills, and it can settle over time, reducing its effectiveness if not properly installed. Despite these challenges, cellulose is an eco-friendly option that provides excellent thermal and sound insulation. Its use of recycled materials also makes it a sustainable choice, appealing to environmentally conscious homeowners.
Insulation Thickness and R-Value
The thickness of the insulation and its R-value, which measures its resistance to heat flow, will also affect the cost. Higher R-values provide better insulation but typically come at a higher cost. The recommended R-value for garage insulation depends on your climate zone and whether the garage is attached or detached. For instance, a detached garage in a mild climate may require lower R-value insulation compared to an attached garage in a colder region. The desired use of the garage also plays a role; if the garage will be used as a living space, higher R-values are essential for comfort and energy efficiency. Insulation thickness can also impact the installation process and the amount of space taken up by the insulation within the walls or ceiling. Thicker insulation can provide better energy savings but may require modifications to the existing structure to accommodate the added thickness. Additionally, thicker insulation may affect the available interior space, which is an important consideration if the garage is used for parking or storage.
Garage Walls, Ceiling, and Floor
Insulating the walls, ceiling, and floor of the garage will influence the total cost. While walls and ceilings are typically insulated, insulating the floor can provide additional benefits, especially if the garage is being converted into a living space. Each area may require different types of insulation and installation methods. For example, insulating the walls and ceiling can prevent heat loss and improve overall energy efficiency, while insulating the floor can reduce cold drafts and make the space more comfortable for activities such as working out or hobbies. Additionally, garages with living spaces above them will benefit significantly from proper ceiling insulation to reduce noise and heat transfer. Insulating all parts of the garage ensures a comprehensive approach to energy efficiency and comfort, reducing temperature fluctuations and improving indoor air quality. Properly insulated walls, ceiling, and floor can also help prevent moisture intrusion and damage, extending the lifespan of the garage and its contents. Moreover, insulation can contribute to the structural integrity of the garage by providing additional support and protection against environmental factors.
Existing Structure and Preparation
The current condition of the garage will affect the cost. If the garage is unfinished with exposed studs, insulation will be easier and less expensive to install. However, if the garage is finished or requires significant preparation work, such as removing old insulation or addressing moisture issues, the costs will increase. Preparing the space may involve tasks like repairing cracks, sealing gaps, and ensuring the structure is free of pests and mold. Proper preparation is crucial for achieving optimal insulation performance and longevity, preventing issues such as moisture buildup and insulation degradation. Any structural repairs needed to support the insulation must also be factored into the overall cost, as they ensure the insulation can be installed correctly and effectively. Addressing any underlying issues before installing insulation can prevent future problems and additional costs, ensuring a durable and efficient insulation system. Additionally, thorough preparation can enhance the effectiveness of the insulation by eliminating potential sources of heat loss or air infiltration.
Labor and Installation
Labor costs for installing insulation can vary based on the complexity of the job, local labor rates, and the type of insulation being installed. DIY installation can save on labor costs but may not be suitable for all types of insulation or for individuals without the necessary skills and tools. Professional installation ensures that the insulation is correctly applied, maximizing its effectiveness and longevity. Labor costs also include tasks such as cutting and fitting the insulation, sealing gaps, and potentially installing additional components like vapor barriers and drywall. Choosing a reputable contractor with experience in insulation can ensure a high-quality installation and adherence to building codes. Additionally, professional installers can identify and address potential issues that might be overlooked in a DIY project, ensuring the insulation performs as expected and provides the desired energy efficiency benefits. The expertise of professional installers can also contribute to a quicker and more efficient installation process, reducing disruptions and ensuring the project stays on schedule. Furthermore, professionals can provide valuable advice on selecting the most suitable insulation materials and methods for your specific needs and conditions.
Additional Costs
Additional costs can include vapor barriers, drywall, and finishing materials, as well as any necessary repairs or improvements to the garage structure. Proper insulation may also require sealing gaps and cracks to ensure maximum efficiency. These additional elements can significantly impact the overall cost of the project but are essential for achieving the best results. Vapor barriers, for example, prevent moisture from penetrating the insulation, while drywall provides a finished look and additional protection. Finishing materials can enhance the aesthetic appeal and functionality of the garage, making it more suitable for various uses. Additional costs might also include upgrading electrical systems to handle the new insulation or installing ventilation systems to maintain air quality, especially if the garage will be used as a living or working space. Ensuring all components are properly installed and integrated can prevent future issues and enhance the overall performance and durability of the insulation system. Investing in these additional elements can also contribute to a healthier and more comfortable indoor environment by preventing issues such as mold growth, moisture damage, and poor air quality.
Benefits of Insulating a Garage
Improved Energy Efficiency
Insulating your garage can significantly reduce energy loss, helping to maintain a consistent temperature inside the space. This is particularly beneficial if your garage is attached to your home, as it can help reduce overall heating and cooling costs. Improved energy efficiency not only lowers your utility bills but also reduces your carbon footprint, contributing to environmental sustainability. By minimizing energy loss, insulation helps create a more comfortable living environment while reducing the strain on your HVAC system.
Enhanced Comfort
Proper insulation keeps the garage warmer in the winter and cooler in the summer, making it a more comfortable space for various activities. Whether you’re using the garage for storage, a workshop, or a recreational area, insulation can help create a more pleasant environment. This is especially important if you spend a significant amount of time in the garage or use it for activities that require a stable temperature. Insulation can also help reduce noise from outside, creating a quieter and more peaceful space.
Increased Property Value
A well-insulated garage can add value to your property by improving its energy efficiency and usability. Potential buyers are often attracted to homes with energy-efficient features, and a well-insulated garage can be a selling point. Additionally, the improved comfort and functionality of the insulated space can enhance the overall appeal of your home. Investing in insulation can provide a good return on investment by increasing the marketability and desirability of your property.
Versatility of Use
Insulating your garage opens up possibilities for using the space for more than just parking cars. With proper insulation, the garage can be converted into a workshop, home gym, office, or even a guest room. The versatility of an insulated garage adds to the overall functionality and value of your home. Whether you’re looking to create additional living space or a specialized area for hobbies and activities, insulation provides the foundation for transforming your garage into a versatile and useful part of your home.
Benefits of Insulating a Garage
DIY Installation
If you have the skills and tools, consider installing the insulation yourself. DIY installation can save on labor costs, especially for materials like fiberglass batts and rigid foam boards. However, ensure you understand the installation process and safety precautions before starting. Proper installation is crucial for achieving the desired insulating properties and preventing issues such as moisture buildup and mold growth. While DIY installation can reduce costs, it requires careful planning and attention to detail to ensure the insulation is effective and safe.
Choose Cost-Effective Materials
Opt for cost-effective insulation materials that meet your needs without compromising quality. For example, fiberglass batts offer good insulation properties at a lower cost compared to spray foam. Consider the specific requirements of your garage and the climate in your area to choose the most suitable and cost-effective insulation material. Balancing cost and performance can help you achieve optimal energy efficiency and comfort within your budget. Additionally, exploring different suppliers and comparing prices can help you find the best deals on materials.
Buy in Bulk
Buying insulation materials in bulk can reduce costs. Many suppliers offer discounts for large purchases, which can be beneficial if you are insulating multiple areas of your home. Additionally, buying in bulk ensures you have enough material to complete the project without delays, allowing you to take advantage of bulk pricing and reduce overall expenses. Planning your project to maximize bulk purchase discounts can lead to significant cost savings. Ensuring that you have a detailed plan and accurate measurements before purchasing materials can also help avoid waste and additional expenses.
Compare Quotes
Get multiple quotes from insulation contractors to find the best price for your project. Comparing quotes based on the scope of work, materials included, and the experience of the contractors can help you find the most cost-effective option. Ensure that the quotes are detailed and include all necessary components, such as labor, materials, and additional costs, to make an informed decision. Evaluating the reputation and reviews of contractors can also provide insights into their reliability and quality of work. By obtaining multiple quotes, you can negotiate better terms and potentially lower the overall cost of the project.
Plan Efficiently
Plan your insulation project efficiently to minimize delays and reduce overall costs. Ensure that all necessary modifications and preparations are considered before starting the installation to avoid unexpected expenses. Proper planning includes assessing the condition of the garage, addressing any structural issues, and coordinating with contractors for a smooth and timely installation process. Efficient planning helps prevent costly delays and ensures the project stays within budget. Additionally, thorough planning can help identify potential challenges and opportunities for cost savings, leading to a more successful and cost-effective project.
Download Template For Insulation Project Breakdown
- Materials list updated to the zip code
- Fast delivery
- Data base of general contractors and sub-contractors
- Local estimators
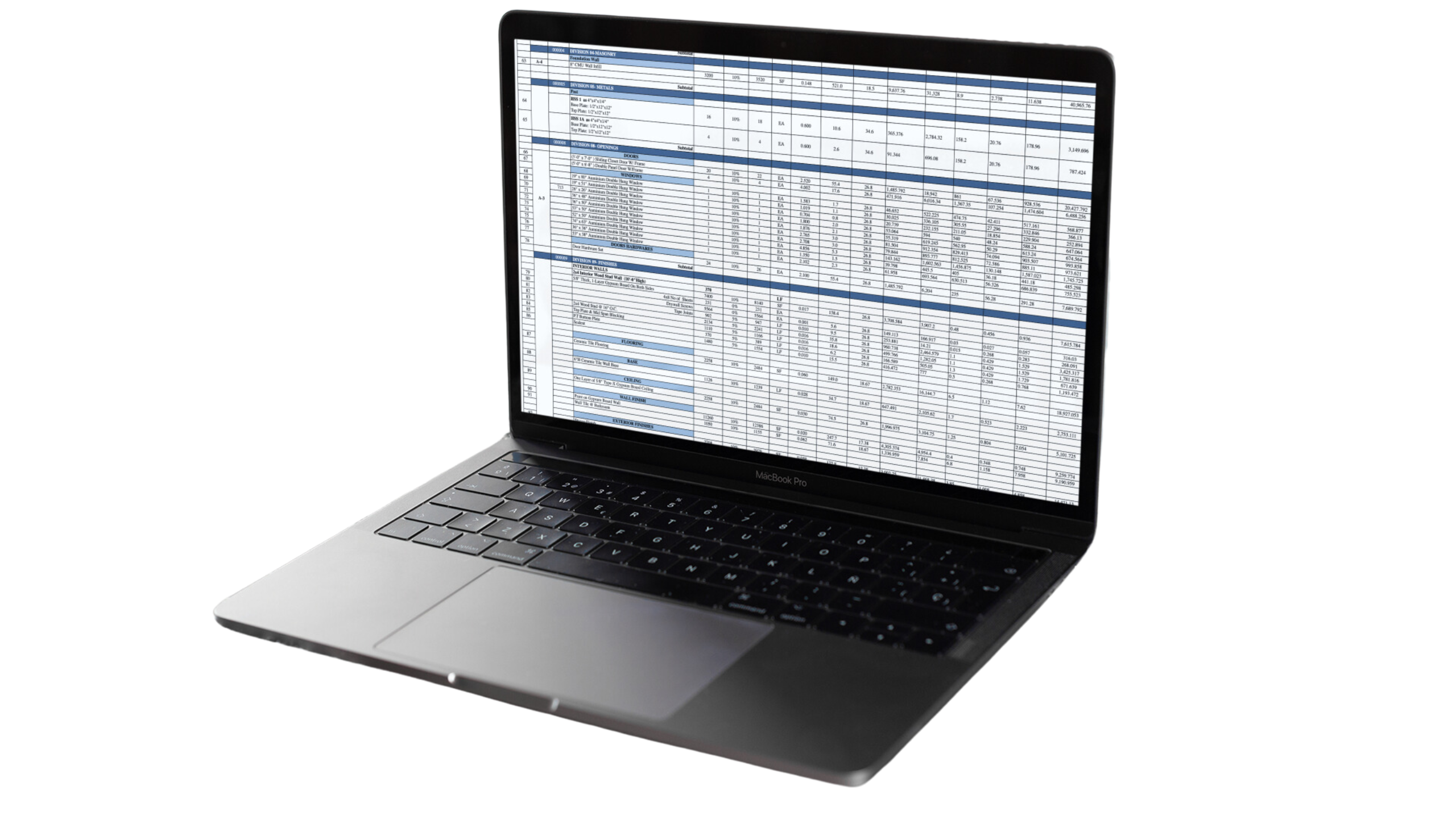
Conclusion
Insulating a 20’x20′ garage typically costs between $1,120 and $4,312, averaging $2.80 to $10.78 per square foot. The price includes materials such as fiberglass batts, spray foam, or rigid foam boards, and professional installation. Costs can vary based on insulation type, local labor rates, and additional work such as sealing gaps or installing vapor barriers. Proper insulation enhances energy efficiency, reduces noise, and improves overall comfort. For the best results, always obtain multiple quotes and choose high-quality materials. Effective planning and selecting cost-effective options can further optimize your investment in garage insulation.
FAQs
The typical cost range for insulating a 20’x20′ garage is between $1,120 and $4,312. This averages to about $2.80 to $10.78 per square foot.
Common types of insulation materials for a garage include fiberglass batts, spray foam, rigid foam boards, and cellulose.
Fiberglass batts insulation costs between $0.70 and $1.40 per square foot, totaling $280 to $560 for a 20’x20′ garage.
Spray foam insulation costs between $2.10 and $4.20 per square foot, totaling $840 to $1,680 for a 20’x20′ garage.
Rigid foam boards cost between $1.40 and $2.80 per square foot, totaling $560 to $1,120 for a 20’x20′ garage.
Cellulose insulation costs between $1.12 and $2.10 per square foot, totaling $448 to $840 for a 20’x20′ garage.
Labor costs vary based on the type of insulation and complexity of the job. For a 20’x20′ garage, labor costs range from $280 to $1,120, depending on the insulation type.
Yes, additional costs can include vapor barriers, drywall, finishing materials, and any necessary repairs or improvements to the garage structure.
Vapor barriers cost between $0.21 and $0.42 per square foot, totaling $84 to $168 for a 20’x20′ garage.
Google Reviews
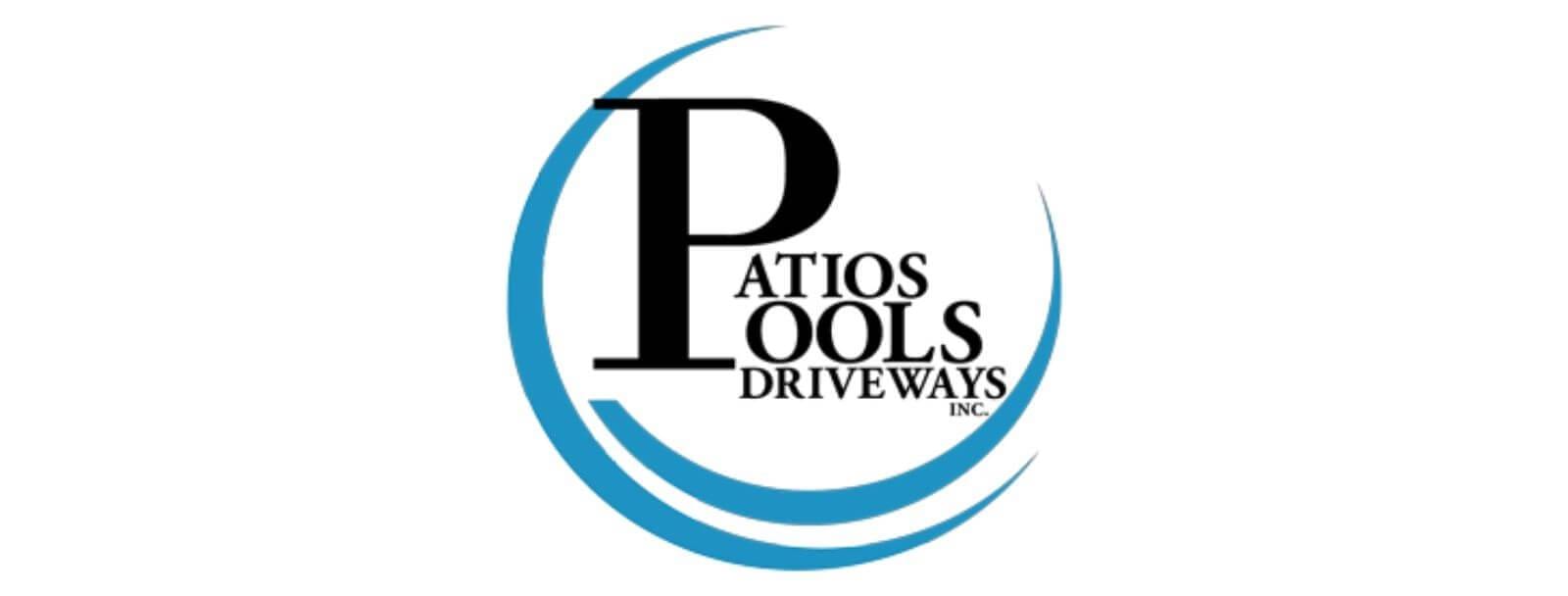
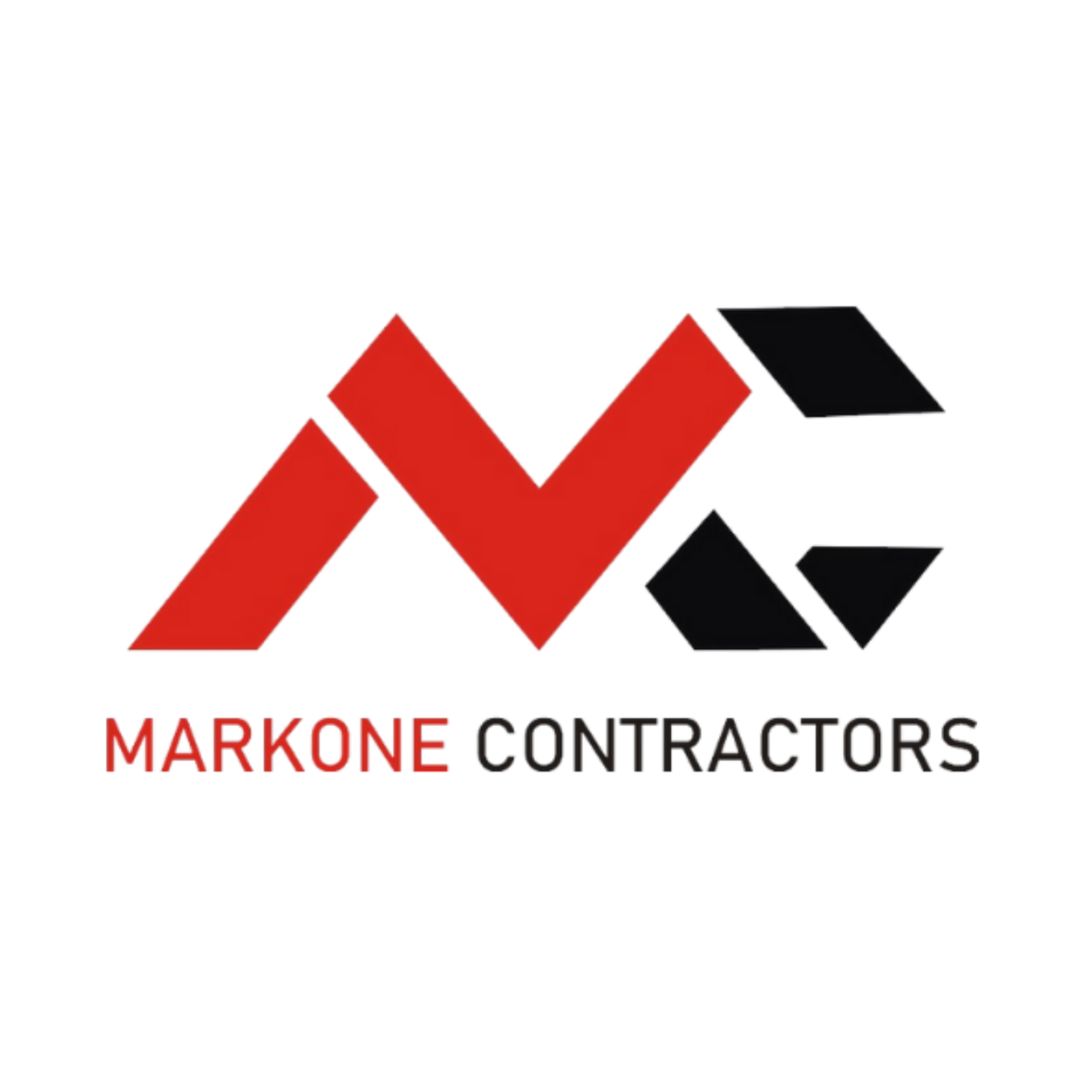

Process To Get Warehouse Fire Sprinkler System Cost Estimate Report
Here I am going to share some steps to get warehouse fire sprinkler system cost estimate report.
-
You need to send your plan to us.
You can send us your plan on info@estimatorflorida.com
-
You receive a quote for your project.
Before starting your project, we send you a quote for your service. That quote will have detailed information about your project. Here you will get information about the size, difficulty, complexity and bid date when determining pricing.
-
Get Estimate Report
Our team will takeoff and estimate your project. When we deliver you’ll receive a PDF and an Excel file of your estimate. We can also offer construction lead generation services for the jobs you’d like to pursue further.