- Homepage
- How Much Does It Cost to Install Porcelain Slabs?
How Much Does It Cost to Install Porcelain Slabs?
Leading provider of porcelain tile installation services.
As a senior construction estimator with over two decades of experience in Florida’s premium construction market, I’ve witnessed the dramatic evolution of finishing materials across residential and commercial projects. Large-format porcelain slabs have emerged as the definitive luxury surface solution, transitioning from a niche specialty product to the gold standard for discerning clients seeking exceptional aesthetics and performance.
The question of porcelain slab installation costs requires detailed analysis that accounts for current market conditions, technical installation challenges, and the significant expertise required for successful implementation. What many developers and general contractors fail to recognize is the substantial difference between traditional tile installation and the specialized requirements of large-format porcelain slabs.
At Estimate Florida Consulting, we provide precision cost forecasting for premium porcelain slab installations that reflects current material availability, regional labor market conditions, and the technical specifications demanded by Florida’s unique climate challenges. For immediate consultation on your porcelain slab installation requirements, contact our specialized estimating team at (561)530-2845.
Premium Cost Analysis
When budgeting for porcelain slab installation in today’s Florida market, expect comprehensive costs ranging from $55 to $125+ per square foot, depending on multiple variables including material selection, format size, application type, and specific performance requirements. These figures represent complete installed costs including all necessary preparation, materials, and expert installation.
Material Quality | Installed Cost Range | Key Characteristics |
---|---|---|
Standard Porcelain Slabs | $55-75/sq ft | Basic large-format porcelain, limited designs |
Premium Porcelain Slabs | $75-95/sq ft | Enhanced aesthetics, superior durability |
Ultra-Premium Porcelain Slabs | $95-125+/sq ft | Exceptional designs, through-body veining, luxury finishes |
These comprehensive figures include proper substrate preparation, specialized setting materials, and expert installation techniques. For commercial applications requiring enhanced performance specifications, expect costs in the upper ranges of these categories due to additional technical requirements.
The material cost component typically ranges from $15 to $35 per square foot for the porcelain slabs themselves, with installation labor adding $40 to $90 per square foot due to the specialized expertise, equipment, and technical precision required.
Skilled Porcelain Slab Installation Expert for your Project?
Size Variations and Cost Implications
Porcelain slab format size dramatically impacts both material and installation costs, creating significant variations in overall project budgets:
Slab Format | Typical Dimensions | Installed Cost Range | Installation Complexity Factor |
---|---|---|---|
Standard Large Format | 5′ × 3′ (15 sq ft) | $55-85/sq ft | Base reference (1.0x) |
Oversized Format | 5′ × 10′ (50 sq ft) | $75-105/sq ft | 1.4-1.6x standard installation |
Maximum Format | 5′ × 12′ (60 sq ft) | $95-125+/sq ft | 1.7-2.0x standard installation |
While larger slabs create dramatic visual impact through minimized seams, they introduce substantial technical challenges in handling, transportation, substrate preparation, and installation precision. These factors directly impact labor costs, with larger formats requiring specialized teams commanding premium rates.
The complexity multipliers above reflect not just reduced installer productivity with larger formats, but the enhanced technical expertise and specialized equipment required for successful installation—factors that must be incorporated into accurate project budgeting.
Regional Cost Variations Across Florida
Installation costs for porcelain slabs vary significantly throughout Florida due to regional labor market conditions, code requirements, and availability of specialized installation teams:
Florida Region | Price Range (Installed) | Market Factors |
---|---|---|
Miami-Dade/Palm Beach | $65-135/sq ft | Stringent building codes, high-end market expectations |
Naples/Marco Island | $60-125/sq ft | Luxury residential focus, high standards |
Tampa Bay Area | $55-115/sq ft | Growing luxury market, emerging expertise |
Orlando/Central Florida | $50-105/sq ft | Hospitality expertise, competitive pricing |
Jacksonville/North Florida | $45-95/sq ft | Developing premium market, limited specialist availability |
Panhandle Region | $45-90/sq ft | Emerging luxury market, fewer specialists |
These regional variations reflect not just labor cost differences but varying levels of technical expertise availability. Coastal regions typically command 15-25% higher rates due to enhanced moisture protection requirements and stringent building codes related to water intrusion prevention.
Contact Estimate Florida Consulting at (561)530-2845 for a region-specific analysis tailored to your project location and requirements.
Technical Requirements
Substrate Preparation Standards for Porcelain Slabs
The thin profile (typically 6-12mm) and large dimensions of porcelain slabs create unique substrate preparation requirements that significantly impact installation costs. While national standards allow for minor surface variations in traditional tile installations, porcelain slabs demand exceptional preparation standards:
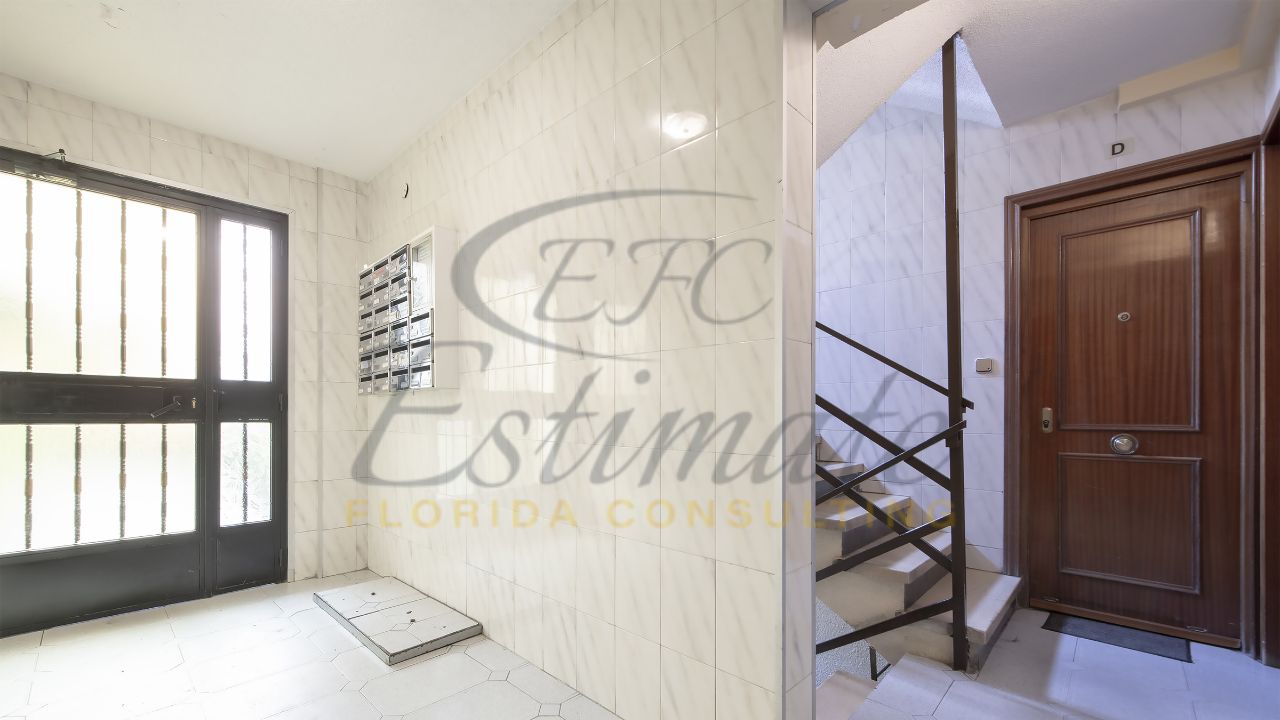
Application Type | Required Flatness | Additional Requirements | Cost Impact |
---|---|---|---|
Wall applications | 1/16″ in 10′ | Enhanced adhesion systems | +$8.50-14.75/sq ft |
Horizontal surfaces | 1/32″ in 10′ | Premium leveling systems | +$12.25-18.50/sq ft |
Wet area installations | 1/32″ in 10′ | Comprehensive waterproofing | +$15.75-22.50/sq ft |
Commercial applications | 1/32″ in 10′ | Enhanced load distribution | +$18.50-26.75/sq ft |
Florida-Specific Requirements:
- Enhanced moisture vapor emission control systems due to high ambient humidity
- Superior anti-fracture membrane applications to accommodate seasonal movement
- Comprehensive waterproofing systems beyond typical wet area applications
- Additional substrate reinforcement for elevated installations
- Enhanced adhesive performance requirements due to thermal expansion/contraction
These substrate requirements represent 30-40% of total installation costs but are absolutely essential for successful long-term performance in Florida’s demanding climate. Inadequate substrate preparation represents the primary cause of installation failures, making these investments critical to project success.
We Provide 3D Rendering Services!
For Commercial & Residential and Other Projects
Turnaround time is 1-2 days.
Win More Projects With Us
Specialized Equipment for Porcelain Slab Installation
Professional porcelain slab installation requires specialized equipment that directly impacts both quality outcomes and project costs:
Equipment Type | Purpose | Cost Impact | Required For |
---|---|---|---|
Vacuum lifting systems | Safe handling of large slabs | +$4.75-8.50/sq ft | All porcelain slab installations |
Specialized cutting systems | Precision cutting without breakage | +$3.50-7.25/sq ft | All applications with cutouts |
Transport frames | Safe movement and positioning | +$2.75-5.50/sq ft | All installations |
Advanced leveling systems | Perfect alignment and support | +$3.25-7.75/sq ft | All horizontal applications |
Specialized adhesive application tools | Consistent adhesive distribution | +$2.50-4.85/sq ft | All installations |
Equipment Impact Factors:
- Specialized equipment typically adds $12.50-22.50 per square foot to installation costs
- Proper equipment is essential for minimizing breakage and waste
- Advanced equipment significantly improves finished quality and reduces warranty claims
- Equipment availability often influences project scheduling in Florida’s busy market
- Technical equipment requirements vary by municipality, adding compliance costs
General contractors should verify equipment availability when evaluating bids, as inadequate tooling leads to compromised installations and substantial material waste. Professional installation teams investing in proper equipment command premium rates that deliver superior installation results.
Labor Expertise Requirements
The technical complexity of porcelain slab installation demands specialized labor teams with specific training and certifications:
Expertise Level | Hourly Rate Range | Applications | Qualifications |
---|---|---|---|
Porcelain Slab Specialists | $85-125/hour | All porcelain slab installations | Specialized certification |
Master Installers | $125-175/hour | Premium and oversized slabs | Advanced technical expertise |
Technical Supervisors | $150-225/hour | Project management, QC oversight | Master certification, extensive experience |
In today’s Florida market, expect minimum 3-5 person installation teams for porcelain slab projects, with productivity rates 50-70% lower than traditional tile installations. This reduction in productivity directly impacts labor costs, as installation teams require significantly more time per square foot for these technically demanding installations.
For high-end residential and commercial applications, specialized installation teams command premium rates but deliver superior finished quality, reduced warranty claims, and enhanced long-term performance—representing significant value despite higher initial costs.
Call (561)530-2845 to discuss labor requirements specific to your project scope and timeline.

Investment Examples
What's the Price of a 5,000 sq ft Restaurant Build-Out in Tampa with Premium Porcelain Slab Features?
For an upscale restaurant in Tampa utilizing premium porcelain slabs for feature walls, bar surfaces, and restrooms (approximately 800 sq ft of porcelain slabs), current cost projections would allocate:
Component | Total Cost | Per Square Foot | % of Project |
---|---|---|---|
Material | $48,000-64,000 | $60-80/sq ft | 3.2-4.2% |
Installation | $64,000-88,000 | $80-110/sq ft | 4.3-5.9% |
Total Porcelain Slab Package | $112,000-152,000 | $140-190/sq ft | 7.5-10.1% |
Key Considerations for Restaurant Applications:
- Enhanced durability specifications for high-traffic commercial use
- Specialized seam treatments for food service environments
- Custom fabrication for bar tops and service areas
- Commercial cleaning protocol compatibility requirements
- Extended performance warranties necessary for hospitality applications
This investment delivers exceptional long-term value through reduced maintenance costs, superior durability, and elevated guest experience—critical factors in competitive hospitality markets.
90% More Chances to Win Bids with Our Estimate
Estimating Expenses for a 40,000 sq ft Industrial Complex in Palm Beach
For an industrial complex with executive areas featuring premium porcelain slab wall cladding and countertops (approximately 1,200 sq ft of porcelain slabs):
Component | Total Cost | Per Square Foot | % of Project |
---|---|---|---|
Material | $72,000-96,000 | $60-80/sq ft | 1.3-1.7% |
Installation | $96,000-132,000 | $80-110/sq ft | 1.7-2.4% |
Total Porcelain Slab Package | $168,000-228,000 | $140-190/sq ft | 3.0-4.1% |
Industrial Application Requirements:
- Enhanced durability for executive areas
- Superior chemical resistance for laboratory surfaces
- Specialized seams for maintenance protocols
- Custom fabrication for reception and conference areas
- Superior cleanability for corporate environments
These premium finishes create significant value in client-facing areas, enhancing corporate identity while delivering exceptional lifecycle performance.
What's the Investment for a 100-Room Hotel in Destin?
For a luxury hotel with premium porcelain slabs in public spaces, bathroom feature walls, and vanities (approximately 3,500 sq ft):
Component | Total Cost | Per Square Foot | % of Project |
---|---|---|---|
Material | $210,000-280,000 | $60-80/sq ft | 1.4-1.9% |
Installation | $280,000-385,000 | $80-110/sq ft | 1.9-2.6% |
Total Porcelain Slab Package | $490,000-665,000 | $140-190/sq ft | 3.3-4.5% |
Hotel-Specific Considerations:
- Enhanced aesthetic continuity across multiple areas
- Superior moisture resistance for bathroom applications
- Specialized maintenance protocols for hospitality operations
- Brand standard compliance specifications
- Extended lifecycle performance expectations (10+ years)
Hotel installations demand specialized expertise for consistent quality across numerous rooms while maintaining absolute precision with project timelines—a significant factor in overall project success.
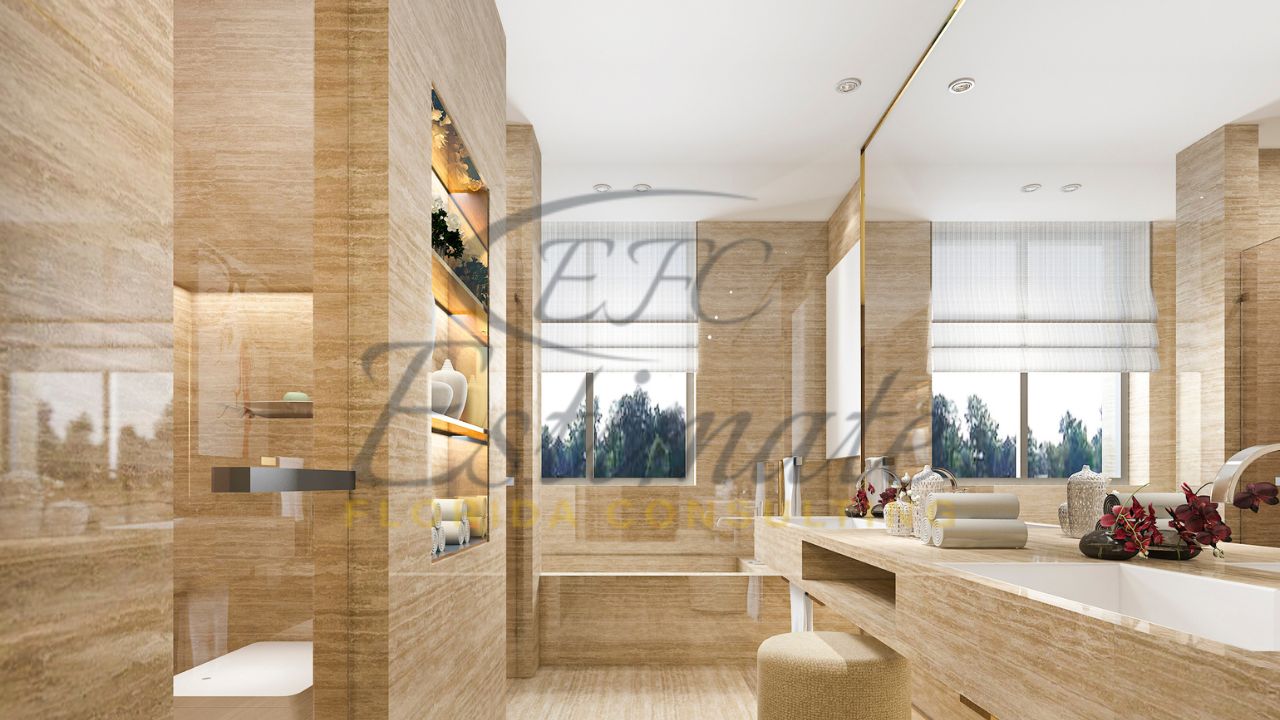
Estimating the Cost of a 20,000 sq ft Warehouse in Orlando
For a warehouse facility with executive offices featuring porcelain slab feature walls and conference areas (approximately 600 sq ft of porcelain slabs):
Component | Total Cost | Per Square Foot | % of Project |
---|---|---|---|
Material | $36,000-48,000 | $60-80/sq ft | 1.2-1.6% |
Installation | $48,000-66,000 | $80-110/sq ft | 1.6-2.2% |
Total Porcelain Slab Package | $84,000-114,000 | $140-190/sq ft | 2.8-3.8% |
Get 5 New Projects in the Next 7 Days With Our System
Warehouse Office Requirements:
- Enhanced aesthetic for client-facing areas
- Superior durability for transition zones
- Specialized designs for corporate branding integration
- Custom fabrication for executive areas
- Superior cleanability for professional environments
These premium finishes create significant value in client-facing areas, enhancing professional credibility while providing exceptional durability in mixed-use facilities.
Contact Estimate Florida Consulting at (561)530-2845 for comprehensive project assessment tailored to your specific requirements.
Question Answer
Frequently Asked Question
Material selection, slab dimensions, and installation complexity represent the most significant cost drivers in porcelain slab installations. Premium porcelain slabs with enhanced technical specifications range from $15-35/sq ft for materials alone, while installation labor rates vary from $40-90/sq ft depending on application type and technical complexity. Additionally, Florida's climate necessitates enhanced substrate preparation ($8.50-26.75/sq ft) not required in drier regions. These three factors—material quality, slab dimensions, and Florida-specific preparation requirements—typically account for 80-85% of cost variations between projects. For precise budgeting, comprehensive assessment addressing these specific factors provides more accurate forecasting than generalized square footage estimates.
Large-format porcelain slabs typically increase installation costs by 150-200% compared to traditional tile installations due to several technical factors. Porcelain slabs require significantly enhanced substrate preparation (adding $8.50-26.75/sq ft), specialized handling equipment, dramatically reduced installer productivity (50-70% lower than traditional tile), and advanced technical expertise commanding premium labor rates. While material costs might be only marginally higher for porcelain slabs, the technical installation complexity drives substantially higher overall installed costs. For typical Florida projects, expect minimum installed cost differentials of $30-60/sq ft when upgrading from traditional tile to porcelain slabs, with premium installations showing even greater variations.
The exceptional thinness (6-12mm) combined with large dimensions (up to 5'×12') creates several technical challenges that impact costs. First, transportation and handling require specialized equipment to prevent breakage. Second, substrate preparation must achieve near-perfect flatness (typically 1/32" in 10') to prevent stress points that can crack the material. Third, installation requires specialized adhesives with proper coverage and support during curing. Finally, edge treatments and seams demand precision fabrication techniques rarely found in traditional tile installation. These technical requirements typically add 40-60% to standard installation costs but are essential for preventing the catastrophic material failures that plague inadequately planned installations.
Vertical applications (wall cladding) typically represent the lower end of the installation cost spectrum ($55-95/sq ft installed) while horizontal applications (countertops, flooring) command premium rates ($75-125+/sq ft installed) due to additional technical requirements. Wet area installations such as showers and bathroom surfaces add approximately 15-25% to standard costs due to enhanced waterproofing requirements. Custom fabrication for specialized applications like feature walls with integrated lighting or countertops with waterfall edges can increase costs by 30-45% over standard installations. Finally, exterior applications in Florida's demanding climate require additional UV-resistant adhesives and enhanced expansion accommodation, typically adding 20-30% to comparable interior installations.
Several market trends are currently impacting porcelain slab installation costs across Florida. Supply chain disruptions have increased material lead times from 6-8 weeks to 12-20 weeks for premium European porcelain slabs, necessitating earlier procurement decisions and potential storage costs. Labor shortages in specialized installation trades have driven hourly rates up 18-25% since 2023, with certified porcelain slab installers commanding unprecedented premiums. Rising energy costs have increased transportation expenses for these heavy materials by approximately 15-20% year-over-year. Additionally, enhanced building code requirements in coastal regions have introduced new substrate preparation specifications adding $3.50-7.75/sq ft to standard installations. Navigating these market dynamics requires sophisticated cost forecasting to establish accurate project budgets.