Boost Your Dock Bids – Request a Precision Estimate!
- Accurancy
- Efficiency
- Transparency
- Customization
- Time Saving
- Professionalism
- Cost Control
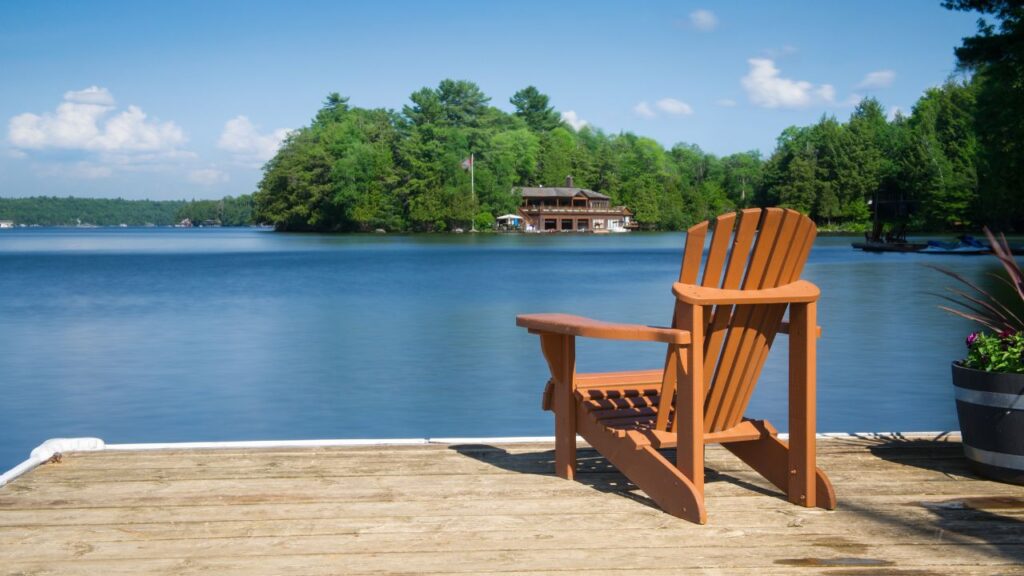
Envisioning the idyllic embrace of waterfront living often involves the cherished dream of a private dock, gracefully extending into the calm waters, promising a stable haven for boats, fishing escapades, and moments of tranquil relaxation. Yet, the very essence of stability and durability in this aquatic haven is intricately tied to a critical element – the pilings. For those contemplating the installation of dock pilings, a profound understanding of the associated costs becomes imperative, serving as the compass for making judicious and well-informed decisions. Within the confines of this article, we embark on a comprehensive exploration of the myriad factors that shape the cost dynamics of installing dock pilings, offering valuable insights to illuminate your path through this pivotal facet of dock construction.
Wooden pilings have long been a staple in dock construction, combining tradition with affordability. Options such as pressure-treated pine or cedar offer a charming aesthetic while being generally budget-friendly. However, it’s essential to acknowledge that wood is prone to decay over time due to exposure to water and the elements. While it remains a popular choice, understanding the maintenance demands and potential lifespan limitations is crucial when opting for the traditional warmth of wood in your dock pilings.
For those seeking a harmonious blend of low-maintenance upkeep and extended lifespan, composite materials emerge as the gold standard. Although pricier than wood, composite pilings offer a durable alternative that resists decay, pests, and the harsh effects of weather. Choosing composite materials ensures a longer-lasting solution without compromising on aesthetic appeal, making it a wise investment for those prioritizing longevity and ease of maintenance.
For those seeking a harmonious blend of low-maintenance upkeep and extended lifespan, composite materials emerge as the gold standard. Although pricier than wood, composite pilings offer a durable alternative that resists decay, pests, and the harsh effects of weather. Choosing composite materials ensures a longer-lasting solution without compromising on aesthetic appeal, making it a wise investment for those prioritizing longevity and ease of maintenance.
When durability is non-negotiable, steel pilings stand out as a robust choice for dock construction. Exceptionally durable and resistant to pests, steel pilings provide unparalleled strength and longevity. However, this durability comes at a higher price, and careful installation is imperative to prevent corrosion, which can compromise their integrity over time. While the initial investment is higher, the long-term benefits of steel pilings make them a strategic choice for those prioritizing structural resilience.
Concrete pilings are synonymous with permanence, often used in the construction of robust and enduring structures. Highly durable and capable of withstanding various environmental challenges, concrete pilings provide a stable foundation for docks, particularly in permanent installations. However, it’s crucial to note that the benefits of concrete come with a cost, both in terms of the material itself and the labor-intensive installation process. Understanding the balance between durability and cost is key when opting for the steadfast foundation that concrete pilings offer.
The dimensions of pilings play a pivotal role in determining the stability and resilience of a dock structure. As a fundamental principle, longer and thicker pilings contribute to greater stability in the face of various environmental factors, including waves, currents, and the overall weight-bearing capacity of the dock. However, this enhanced stability comes with an associated increase in cost. Striking the right balance between achieving the necessary stability and managing costs effectively is a nuanced decision that involves considering the specific conditions of the water body, the intended use of the dock, and the budget constraints of the overall construction project.
Careful evaluation of these factors ensures that the size and length of pilings selected align precisely with the structural requirements while optimizing cost efficiency.
Jetting, as a piling installation method, employs the force of high-pressure water to drive pilings into the ground. This technique is particularly well-suited for soft soils, where the natural resistance is relatively lower. The process involves the use of specialized equipment that directs a focused stream of water with significant force, effectively displacing the soil and creating space for the piling. The advantage of jetting lies in its precision, allowing for a controlled and gradual insertion of pilings, minimizing potential soil disturbance. While ideal for certain soil conditions, the suitability of jetting should be carefully assessed based on the specific characteristics of the installation site to ensure optimal stability and long-term performance.
Hammering stands as a traditional yet robust method for installing pilings, relying on the mechanical force generated by a pile driver. This heavy-duty equipment exerts controlled impact force, driving the piling into the ground and creating a stable foundation. While hammering is a well-established and widely used technique, it may result in more significant soil disturbance compared to jetting. The suitability of hammering is often preferred for various soil types, and its effectiveness lies in its ability to handle dense or compacted soils. Careful consideration of the soil conditions and environmental impact is crucial when opting for hammering as the chosen piling installation method.
Drilling emerges as a method of piling installation that involves creating a hole in the ground before inserting the piling. This technique is particularly employed in hard or rocky soils, where the direct driving of pilings may be challenging or less effective. Drilling provides a precise and controlled approach, allowing for accurate placement of pilings in conditions where other methods might face obstacles. While drilling offers advantages in challenging terrains, it tends to be more labor-intensive and may require specialized equipment. The decision to use drilling as the preferred method should factor in the specific geological characteristics of the site, ensuring that it aligns with the overall stability and performance goals of the dock structure.
The geographical context and soil conditions of the chosen location play a pivotal role in determining the feasibility and cost of installing dock pilings. Difficult terrain, such as areas with uneven topography or geographical features, can pose challenges that impact both labor and equipment requirements. In regions with challenging soil types, such as expansive clay or rocky substrates, the complexity of the installation process may increase. Factors like excavation difficulties and the need for specialized equipment to navigate tough soils contribute to elevated costs. Therefore, a thorough site assessment, considering the intricacies of the terrain and soil composition, is essential to anticipate and mitigate potential challenges, ensuring a robust and cost-effective piling installation.
The process of installing dock pilings is not only influenced by the physical characteristics of the location but also by the regulatory framework governing construction activities. Obtaining the necessary permits and undergoing inspections are integral steps in the piling installation process, and the requirements for these approvals can vary significantly by location. Regulatory compliance ensures that the construction adheres to safety standards, environmental regulations, and zoning ordinances. However, navigating the permit acquisition process and accommodating inspections can add to the overall project expense.
It’s crucial for individuals undertaking piling installations to familiarize themselves with the specific regulatory landscape of their location, accounting for potential costs associated with permits and inspections in the overall budget planning.
Receive highly accurate estimates tailored to your zip code, giving you the edge to secure more projects. Upload your plans and start winning!
In the quest for a stable waterfront retreat, the installation of dock pilings emerges as a pivotal chapter in the construction narrative. This exploration has illuminated the diverse factors shaping the costs of this crucial aspect, providing a comprehensive guide for informed decision-making.
From the selection of piling materials, balancing tradition, durability, and cost considerations, to the intricacies of size, length, and installation methods, each element has been dissected to empower your choices. Geography, soil conditions, and regulatory aspects have been highlighted as critical considerations in steering through this aquatic journey.
Several factors impact the cost, including the chosen piling material, size, and length of pilings, installation method, location, soil conditions, and regulatory requirements.
Wood, composite, steel, and concrete are common materials. Each has unique characteristics, costs, and considerations, influencing choices based on factors like aesthetics, durability, and budget.
Longer and thicker pilings provide greater stability but come with higher costs. The right balance depends on factors like water conditions, dock use, and budget constraints.
etting, hammering, and drilling are common methods. Jetting is suitable for soft soils, hammering is traditional and robust, and drilling is used in hard or rocky soils, each with its advantages and considerations.
Difficult terrain or challenging soil types may increase labor and equipment costs. Site assessments help anticipate challenges and ensure a cost-effective piling installation.
Permit requirements vary by location. Obtaining necessary permits and undergoing inspections are crucial steps, contributing to the overall project expense.
DIY installation is an option for those with skills and equipment. However, it’s essential to ensure safety, adherence to regulations, and a thorough understanding of the installation process.
Yes, tips include choosing wood pilings for affordability, considering off-season installation for potential discounts, obtaining multiple quotes for price comparison, and prioritizing essential features to manage costs.
Here I am going to share some steps to get your Cost to Install Dock Pilings Estimating report.
You can send us your plan on info@estimatorflorida.com
Before starting your project, we send you a quote for your service. That quote will have detailed information about your project. Here you will get information about the size, difficulty, complexity and bid date when determining pricing.
Our team will takeoff and estimate your project. When we deliver you’ll receive a PDF and an Excel file of your estimate. We can also offer construction lead generation services for the jobs you’d like to pursue further.
561-530-2845
info@estimatorflorida.com
Address
5245 Wiles Rd Apt 3-102 St. Pete Beach, FL 33073 United States
561-530-2845
info@estimatorflorida.com
Address
5245 Wiles Rd Apt 3-102 St. Pete Beach, FL 33073 United States
All copyright © Reserved | Designed By V Marketing Media | Disclaimer