How Much Does It Cost to Drive Pilings for a Dock?
Driving pilings for a dock typically costs between $37,500 and $198,000, or about $75 to $200 per square foot. This estimate includes materials, labor, equipment, and necessary permits. Costs can vary based on the length and diameter of the pilings, water depth, soil conditions, and local labor rates. Using high-end materials like steel or concrete pilings can increase the total cost. Additional expenses might include site preparation, environmental assessments, and specialized equipment for challenging conditions. Investing in quality pilings ensures your dock’s stability, durability, and safety. Proper planning and budgeting are essential for a successful dock construction project.
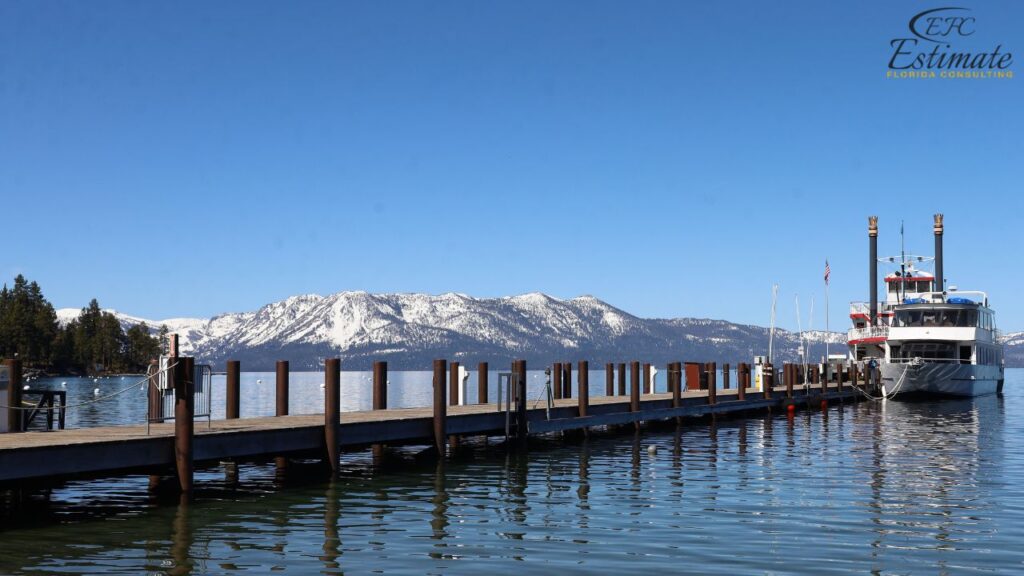
Factors Influencing the Cost of Driving Pilings
Type of Pilings
The type of pilings used can significantly impact the overall cost. Common types include wood, steel, and concrete pilings, each with its own set of advantages and price points. Wood pilings are often the least expensive option and are popular for their aesthetic appeal and ease of installation. However, they may require more maintenance over time due to susceptibility to rot and marine borers. Steel pilings offer greater strength and durability, making them suitable for harsher environments, but they come at a higher cost and require protective coatings to prevent corrosion. Concrete pilings are known for their longevity and resistance to environmental factors, but they are the most expensive option and require specialized equipment for installation. Choosing the right type of piling depends on the specific needs of the project, including the expected load, environmental conditions, and budget constraints.
Cost Breakdown by Piling Type
Piling Type | Estimated Cost per Linear Foot | Total Cost (for 30 Pilings, 20 ft each) |
Wood Pilings | $20 – $40 | $12,000 – $24,000 |
Steel Pilings | $40 – $60 | $24,000 – $36,000 |
Concrete Pilings | $50 – $80 | $30,000 – $48,000 |
Depth and Length of Pilings
The depth and length of the pilings required can also affect the cost. Deeper and longer pilings provide more stability but are more expensive to install due to the additional materials and labor needed. The required depth depends on the soil composition and load-bearing capacity, with softer or unstable soils necessitating longer pilings to reach a solid foundation. In some cases, pilings may need to be driven as deep as 50 feet or more, significantly increasing the overall cost. Additionally, the water depth and tidal variations must be considered to ensure the pilings are adequately anchored. Properly assessing these factors during the planning phase can help determine the optimal length and depth for the pilings, balancing cost and stability.
Cost Breakdown by Depth
Depth (in feet) | Estimated Cost per Linear Foot | Total Cost (for 30 Pilings) |
10 – 20 feet | $20 – $40 | $6,000 – $24,000 |
20 – 30 feet | $40 – $60 | $24,000 – $36,000 |
30 – 40 feet | $60 – $80 | $36,000 – $48,000 |
Site Conditions
The conditions of the site, including soil type, water depth, and accessibility, can impact the cost of driving pilings. Challenging conditions may require specialized equipment and techniques, increasing the overall expense. For example, rocky or dense soil may necessitate the use of heavy-duty pile drivers and longer installation times, while soft, sandy soil may be easier to work with but require deeper pilings for stability. Additionally, the presence of underwater obstacles, such as debris or previous construction remnants, can complicate the installation process and increase costs.
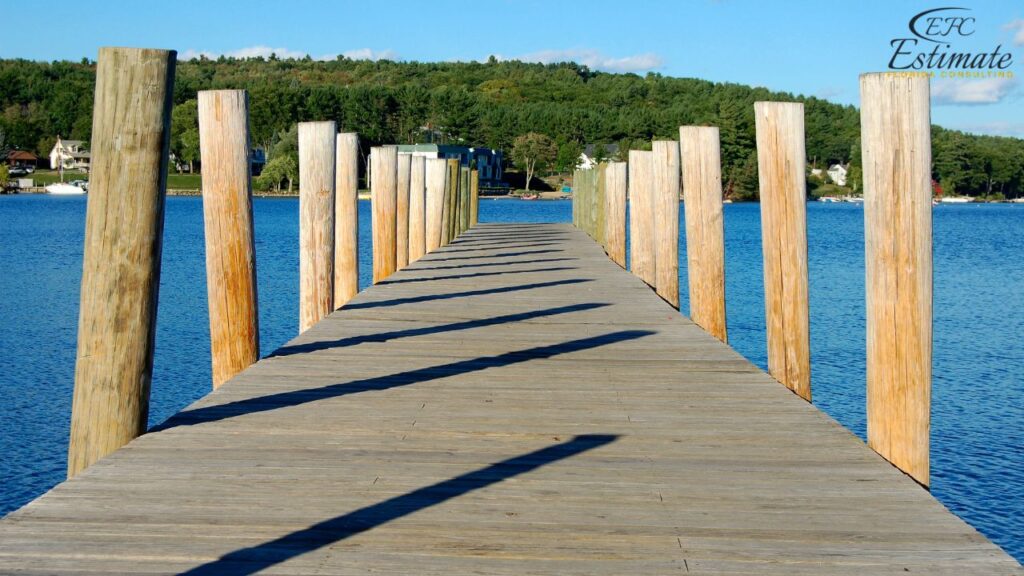
Proper site assessment and preparation are crucial to identify potential challenges and plan accordingly. Accessibility to the site is another important factor; remote or difficult-to-reach locations may require additional transportation and logistical arrangements, further adding to the cost.
Cost Breakdown by Site Conditions
Site Condition | Estimated Additional Cost | Total Cost (for 30 Pilings) |
Easy (sandy soil, shallow water) | $0 – $10,000 | $0 – $10,000 |
Moderate (mixed soil, moderate depth) | $10,000 – $20,000 | $10,000 – $20,000 |
Difficult (rocky soil, deep water) | $20,000 – $30,000 | $20,000 – $30,000 |
Labor Costs
Labor costs are a significant component of the overall expense. These costs can vary based on the complexity of the project, local labor rates, and the experience of the workers. Skilled labor is essential to ensure proper installation and compliance with local building codes and regulations. Experienced workers can efficiently handle the equipment and techniques required for driving pilings, minimizing the risk of errors and ensuring a stable foundation. Labor costs also include the time needed for site preparation, actual driving of the pilings, and any finishing work required to complete the installation.
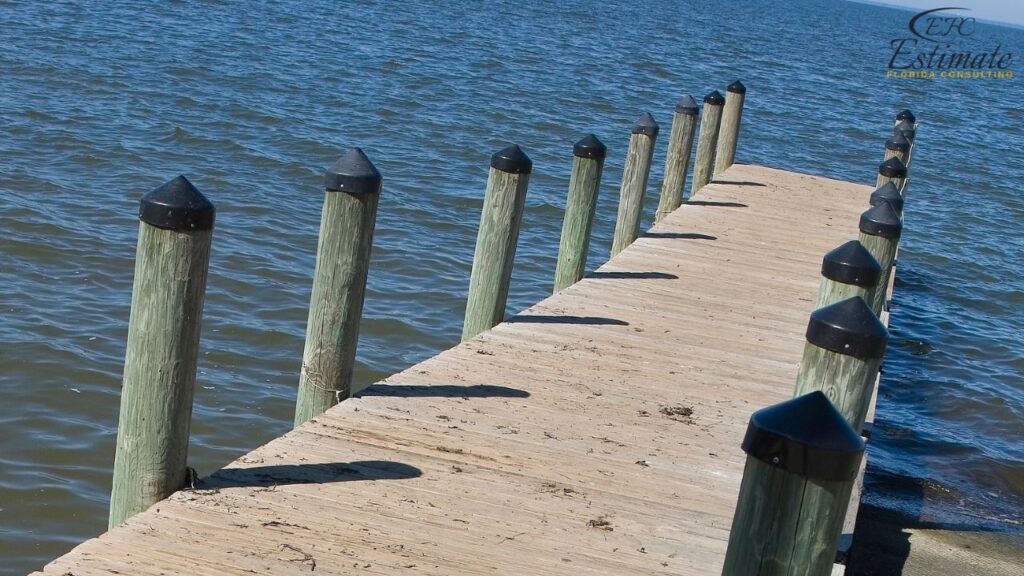
In regions with higher labor rates, such as urban or coastal areas, these costs can be substantial. Hiring a reputable contractor with a proven track record can provide assurance of quality workmanship and adherence to safety standards.
Cost Breakdown by Labor
Labor Task | Estimated Cost per Hour | Total Hours Required | Total Cost |
Site Preparation | $50 – $100 | 50 – 100 | $2,500 – $10,000 |
Piling Installation | $60 – $120 | 100 – 150 | $6,000 – $18,000 |
Finishing and Inspection | $50 – $100 | 20 – 40 | $1,000 – $4,000 |
Download Template For Dock Piling Project Breakdown
- Materials list updated to the zip code
- Fast delivery
- Data base of general contractors and sub-contractors
- Local estimators
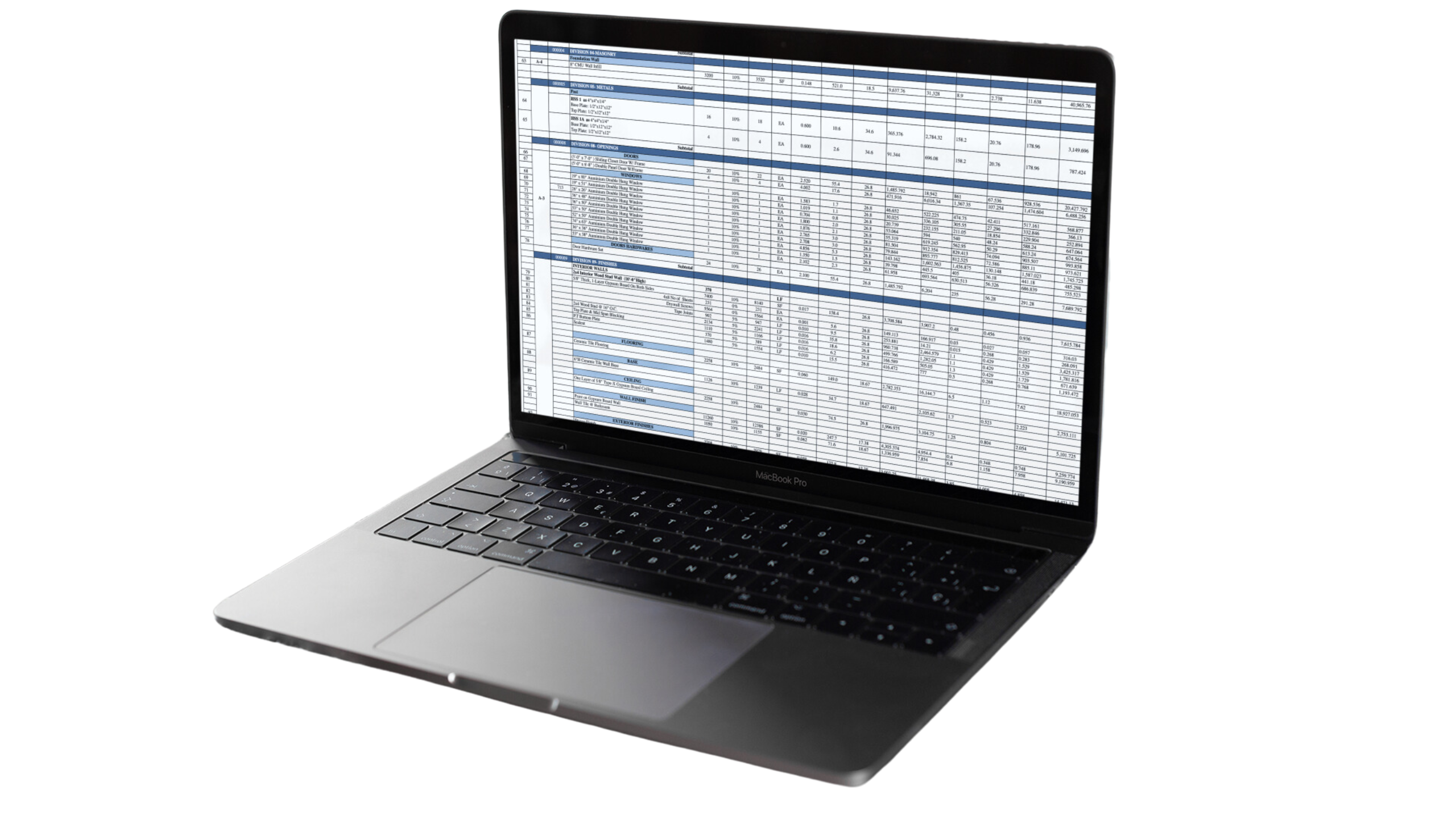
Equipment Rental
The cost of renting specialized equipment needed for driving pilings, such as pile drivers and cranes, can also add to the overall expense. This equipment is essential for handling the heavy materials and driving them deep into the ground or seabed. The duration of the rental period will depend on the size and complexity of the project, with longer projects requiring extended rental times and higher costs. Equipment rental costs can also include transportation to and from the site, setup, and operator fees. Using advanced equipment can improve efficiency and reduce the overall time required for the installation, but it comes with a higher rental cost. Balancing the need for specialized equipment with budget constraints is a key consideration for property owners.
Cost Breakdown by Equipment Rental
Equipment | Estimated Rental Cost per Day | Total Days Required | Total Cost |
Pile Driver | $500 – $1,000 | 10 – 20 | $5,000 – $20,000 |
Crane | $1,000 – $2,000 | 5 – 10 | $5,000 – $20,000 |
Additional Considerations
Seasonal Timing
The time of year can impact the cost and ease of driving pilings for a dock. Scheduling the project during mild weather conditions can prevent delays and reduce complications related to extreme temperatures or adverse weather conditions. This can also affect the availability of labor and equipment, potentially leading to cost savings. Planning the project around favorable weather conditions can help ensure timely completion and reduce the risk of weather-related interruptions, which can delay the project and increase costs. Seasonal timing also affects the demand for construction services, with off-peak seasons potentially offering more competitive pricing.
Permits and Regulations
Obtaining the necessary permits and complying with local regulations are essential for legal and safe construction. Permit costs can vary based on location and the scope of the project. Ensuring compliance with regulations helps avoid fines and ensures that the project meets all safety standards. Working with local authorities to obtain the necessary permits and inspections ensures that the pilings are installed according to code and legal requirements, providing peace of mind and legal protection. Understanding local zoning laws and environmental regulations can also help avoid delays and additional costs.
Cost Breakdown for Permits and Regulations
Permit and Compliance Task | Estimated Cost | Total Cost |
Building Permits | $500 – $2,000 | $500 – $2,000 |
Environmental Compliance | $1,000 – $3,000 | $1,000 – $3,000 |
Inspection Fees | $500 – $1,500 | $500 – $1,500 |
Quality Assurance
Ensuring high-quality construction is essential for the longevity and performance of the dock. Implementing rigorous quality control measures during the installation of pilings can prevent defects and ensure compliance with standards. Regular inspections and testing throughout the process can identify and address issues early, reducing the risk of costly repairs or replacements later. Property owners should work closely with their contractors to ensure all quality standards are met, ensuring the final product meets their expectations and provides long-term value. Quality assurance includes verifying that materials meet specifications, ensuring proper installation techniques, and conducting thorough final inspections before the dock is used.
Environmental Impact
Choosing environmentally friendly practices in piling installation can reduce the environmental impact of the project. This includes using sustainable materials, optimizing the design for reduced environmental footprint, and implementing waste management practices. Sustainable practices not only benefit the environment but can also enhance the property’s value and appeal to environmentally conscious buyers. Additionally, some environmentally friendly practices may qualify for incentives or rebates, further reducing the overall cost.
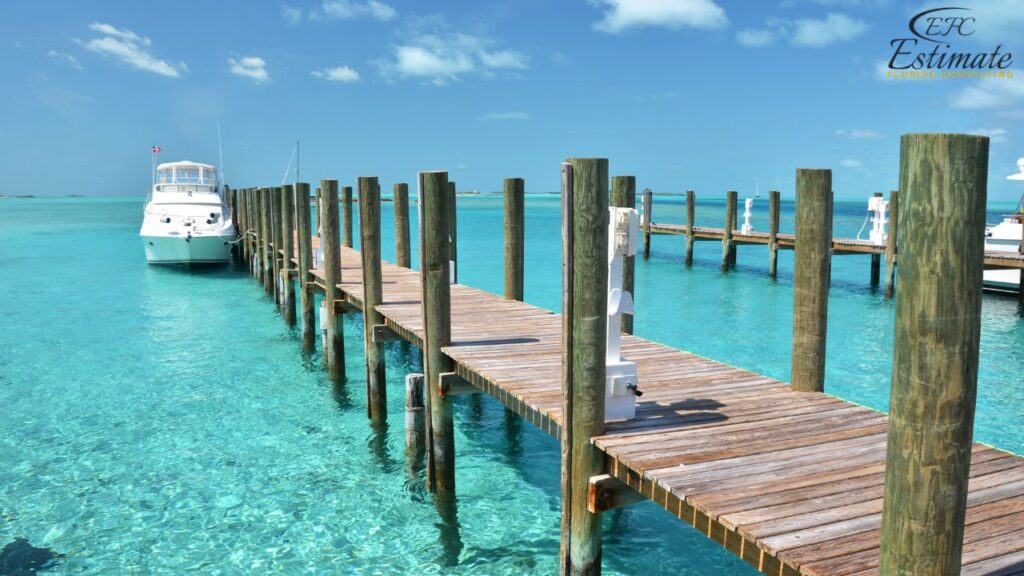
By prioritizing sustainability, property owners can contribute to environmental conservation while enhancing their properties. Green building certifications and adherence to environmental standards can also improve the dock’s marketability and long-term value.
Choosing the Right Contractor
Selecting a reliable and experienced contractor is crucial for the successful installation of pilings. Property owners should research potential contractors, check references, and review past projects to make an informed decision. Choosing the right contractor can prevent delays and ensure that the pilings meet the necessary standards for quality and durability. A good contractor will also provide accurate estimates, transparent pricing, and a clear timeline for the project. Ensuring that the contractor has experience with similar projects can increase the likelihood of a successful outcome.
Evaluating Contractor Quotes
When evaluating quotes from contractors, it’s essential to compare the scope of work, materials used, and warranties offered. The lowest quote isn’t always the best option, as it may exclude critical components or use inferior materials. Reviewing the details of each quote helps ensure you’re getting the best value for your investment. Thoroughly vetting contractors can prevent issues and ensure the project stays within budget and on schedule. By obtaining multiple quotes, property owners can compare prices and services, ensuring they choose the best contractor for their needs. Detailed quotes should outline all costs, including labor, materials, permits, and additional features.
Checking Certifications and Compliance
Ensure that the contractor holds the necessary certifications and complies with industry standards. Proper certification indicates that the contractor adheres to best practices in construction and quality control, while compliance with regulations ensures that the project meets safety and performance standards. Verifying these credentials can give you peace of mind and protect you from potential issues. Ensuring the contractor is properly certified and compliant can also provide financial protection in case of defects or non-compliance, reducing the risk of additional costs. Certifications to look for include licenses from local building authorities and memberships in professional organizations.
Contractor's Track Record
Investigate the contractor’s track record to understand their reliability and reputation in the industry. Look for reviews, testimonials, and case studies from previous clients to gauge their performance. A contractor with a strong track record of successful projects and satisfied clients is more likely to deliver high-quality results. Evaluating the contractor’s past performance can help you make an informed decision and avoid potential problems, ensuring the project is completed to a high standard. By choosing a contractor with a proven history of excellence, property owners can increase the likelihood of a successful and satisfactory outcome. Additionally, visiting completed projects can provide insights into the contractor’s workmanship and attention to detail.
Get 5 New Leads Next 7 Days With Our System
- Multi-Family House
- Single-Faimly House
- Modern House
- Duplex
- Ranch House
- Bungalow
Conclusion
Driving pilings for a dock is a critical step in ensuring the stability and durability of the structure. The cost of this process can vary significantly based on factors such as the type of pilings, depth required, site conditions, labor, and equipment rental. By understanding and planning for these costs, property owners can create a realistic budget and ensure the successful completion of their dock project. Proper budgeting for all aspects of the project helps avoid financial surprises and ensures the dock is built to high standards. With careful planning and attention to detail, property owners can achieve a functional and beautiful structure that enhances the value and enjoyment of their waterfront property. Working with experienced professionals and considering all relevant factors can help ensure a smooth and cost-effective construction process for driving pilings. By making informed decisions and choosing the right materials and services, property owners can enjoy the long-lasting benefits of a well-constructed dock, providing a safe and enjoyable space for various water activities.
FAQs
The average cost to drive pilings for a dock ranges between $37,500 and $198,000, or about $75 to $200 per square foot. This estimate includes materials, labor, equipment, and necessary permits.
Several factors influence the cost, including the type of pilings used, the depth and length of the pilings, site conditions, labor rates, and the need for specialized equipment.
The type of pilings (wood, steel, or concrete) significantly impacts the cost. Wood pilings are generally the least expensive but may require more maintenance. Steel and concrete pilings are more durable but come at a higher cost.
Certainly. Here’s a cost breakdown by piling type:
- Wood Pilings: $20 – $40 per linear foot, Total for 30 pilings (20 ft each): $12,000 – $24,000
- Steel Pilings: $40 – $60 per linear foot, Total for 30 pilings (20 ft each): $24,000 – $36,000
- Concrete Pilings: $50 – $80 per linear foot, Total for 30 pilings (20 ft each): $30,000 – $48,000
Deeper and longer pilings provide more stability but increase costs due to additional materials and labor. The required depth depends on soil composition and load-bearing capacity.
Here’s a breakdown by depth:
- 10 – 20 feet: $20 – $40 per linear foot, Total for 30 pilings: $6,000 – $24,000
- 20 – 30 feet: $40 – $60 per linear foot, Total for 30 pilings: $24,000 – $36,000
- 30 – 40 feet: $60 – $80 per linear foot, Total for 30 pilings: $36,000 – $48,000
Site conditions such as soil type, water depth, and accessibility impact the cost. Challenging conditions require specialized equipment and techniques, increasing expenses.
Google Reviews
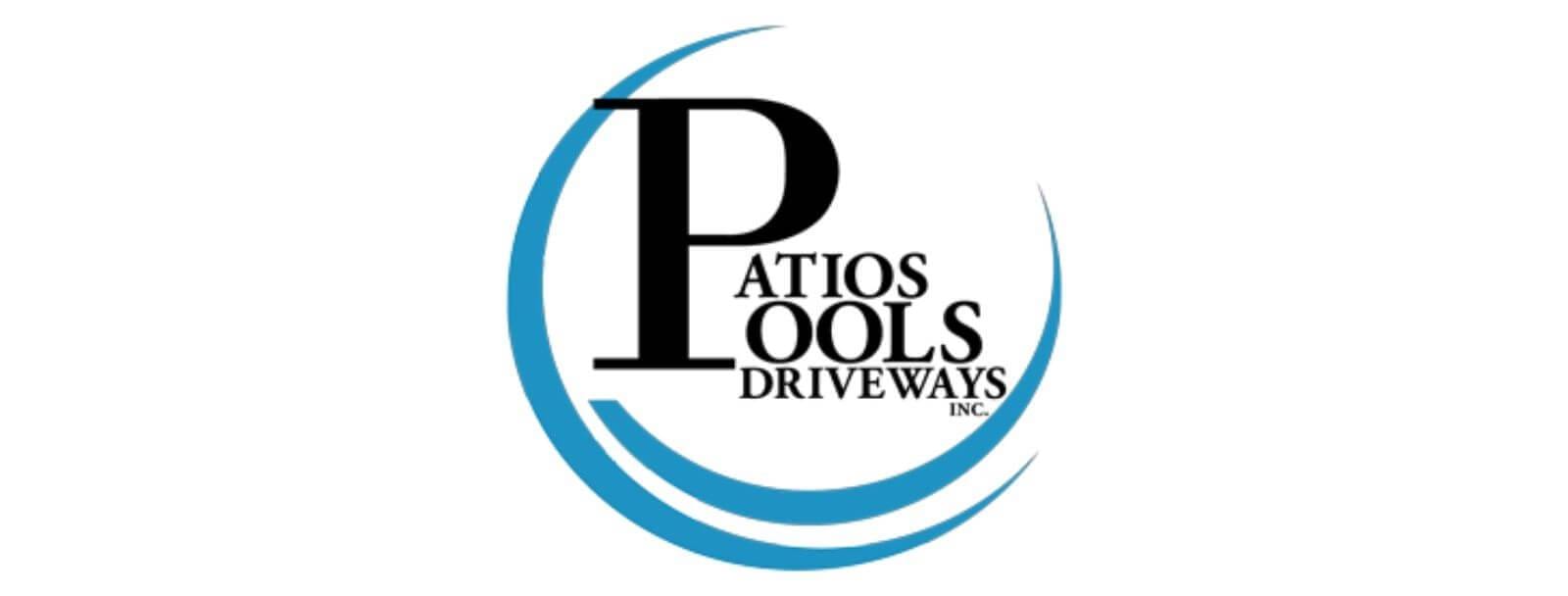
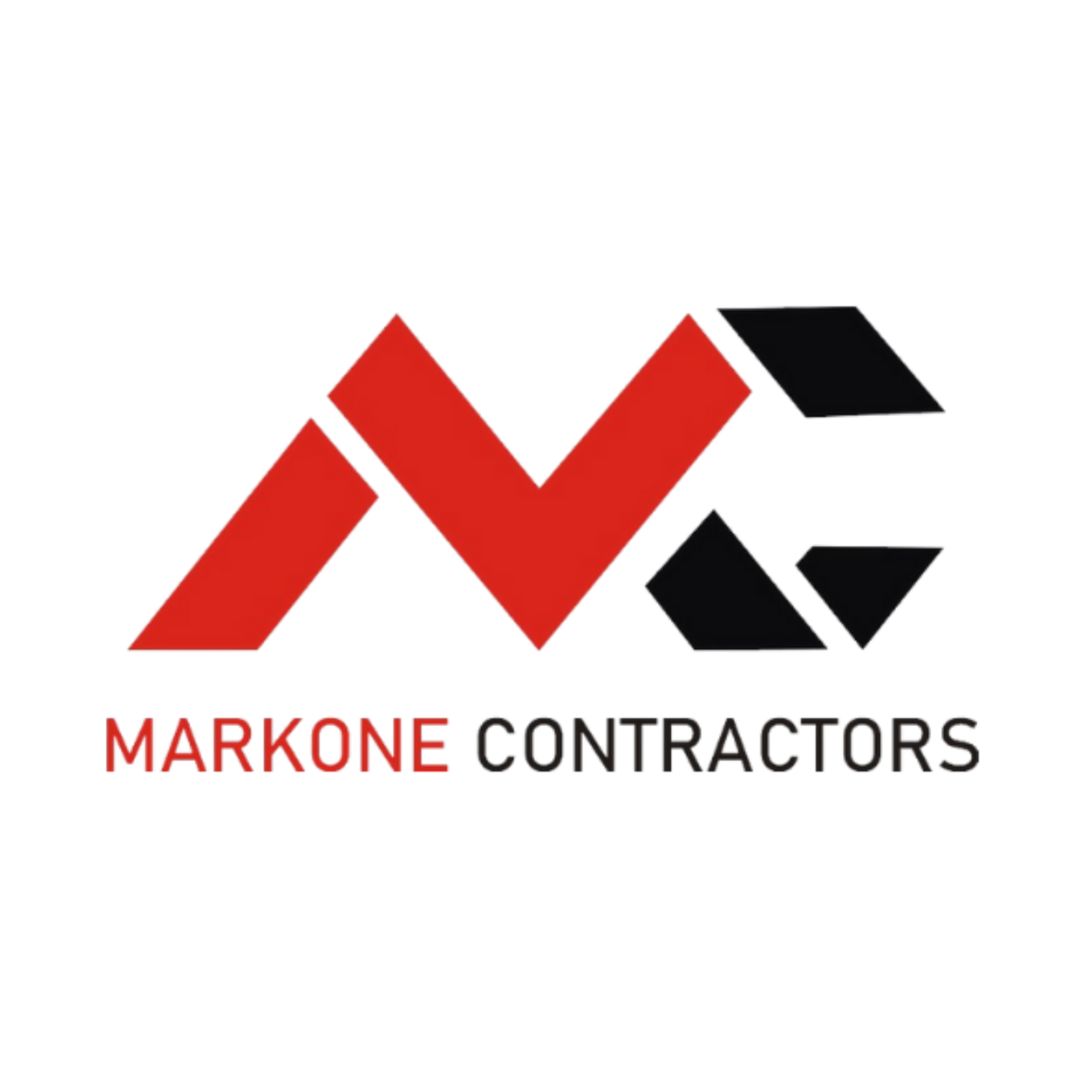

Process To Get Dock Piling Cost Estimate Report
Here I am going to share some steps to get dock piling cost estimate report.
-
You need to send your plan to us.
You can send us your plan on info@estimatorflorida.com
-
You receive a quote for your project.
Before starting your project, we send you a quote for your service. That quote will have detailed information about your project. Here you will get information about the size, difficulty, complexity and bid date when determining pricing.
-
Get Estimate Report
Our team will takeoff and estimate your project. When we deliver you’ll receive a PDF and an Excel file of your estimate. We can also offer construction lead generation services for the jobs you’d like to pursue further.