Boost Your Warehouse Construction Bids – Request a Precision Estimate!
- Accurancy
- Efficiency
- Transparency
- Customization
- Time Saving
- Professionalism
- Cost Control
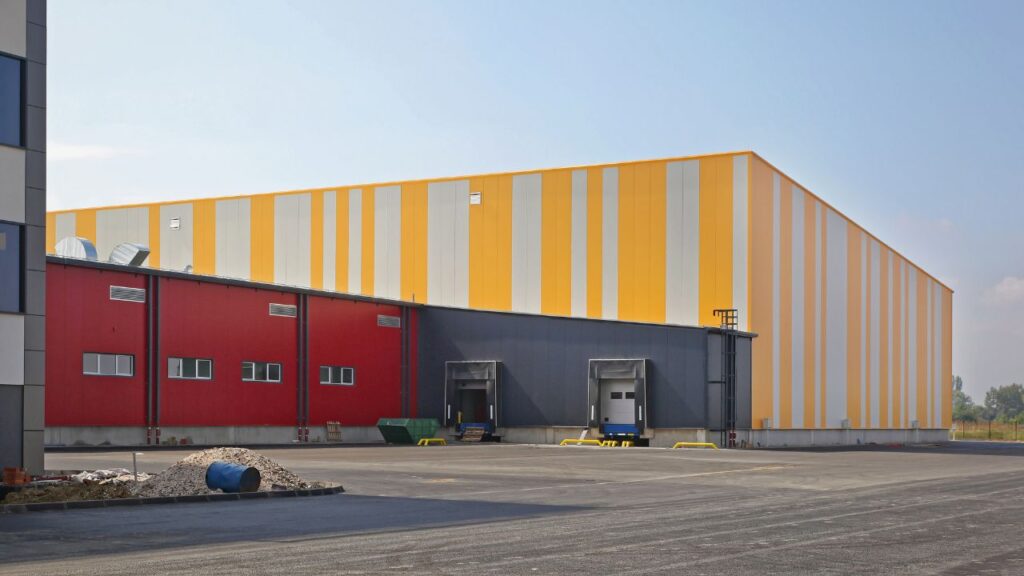
The cost of building a 25,000 sq ft warehouse can vary significantly, influenced by location, material choices, and labor expenses. On average, the price ranges from $30 to $60 per square foot, leading to a total cost of about $750,000 to $1.5 million for the entire project. At Estimate Florida Consulting, we provide detailed cost assessments for warehouse construction projects, tailored to your specific needs and budget. Our expertise ensures accurate estimations, taking into account factors like material optimization and labor efficiency.
We aim to guide you through every step of your project, offering insights and support for an efficient and cost-effective build, ensuring that your warehouse project aligns with both your financial and functional goals.
Make Informed Design Decisions Showcase Your Design Ideas
Get RenderingAt Estimate Florida Consulting, we offer specialized expertise in planning and estimating for these diverse types of 20-floor buildings. Our services ensure that each project, regardless of its specific use, is approached with a deep understanding of its unique requirements, emphasizing cost-efficiency, compliance, and quality.
The cost of constructing a warehouse is influenced by various factors such as location, size, materials, labor costs, permitting requirements, and adherence to building codes and zoning regulations.
The location of a warehouse plays a crucial role in determining the overall expenses involved in construction. For instance, selecting a site in an urban area with higher land costs may drive up the total project costs. Accessibility to transportation networks and proximity to suppliers or customers can impact construction expenses.
Factors like the availability of skilled labor and resources can influence material and labor costs. Obtaining permits and working with contractors proficient in warehouse construction are vital steps that can affect the project timeline and budget. When selecting land for warehouse construction, considerations such as zoning regulations, infrastructure, and utilities availability must be taken into account to streamline the building process and avoid unforeseen costs.”
The location of a warehouse plays a vital role in determining construction costs, influenced by market rates, economic factors, and accessibility to transportation networks.
When selecting a site for warehouse construction, choosing a strategic location can significantly impact the overall expenses involved. For instance, urban areas often have higher land and labor costs compared to rural locations. Market rates for building materials and construction services can vary depending on regional economic conditions. By carefully evaluating these factors and opting for a well-connected site that offers logistical advantages, businesses can optimize their construction budget and ensure cost-effective warehouse development.
The size and design of a warehouse significantly affect construction expenses, with considerations for square footage, materials, roofing, flooring, HVAC systems, electrical installations, and plumbing requirements.
These factors not only impact the initial construction costs but also play a crucial role in the long-term operational expenses. For instance, a larger warehouse will require more materials for construction and maintenance, leading to higher costs in the long run. The type of flooring chosen can affect maintenance costs and durability over time. Properly designed HVAC, electrical, and plumbing systems are essential for efficient warehouse operations, ensuring the safety of goods and personnel. Therefore, careful planning and investment in the size and design elements are imperative for managing overall costs effectively.
Materials and labor costs are key components of warehouse construction expenses, encompassing framing materials, insulation, doors, windows, and other essential elements required for the building’s structure.
Selection of materials plays a vital role, with steel, concrete, and wood being commonly used due to their durability and cost-effectiveness.
Labor considerations involve skilled workers for tasks like framing techniques, ensuring the structural integrity of the warehouse. Proper insulation is crucial to regulate temperature and reduce energy costs.
When it comes to doors and windows, factors such as security, energy efficiency, and durability are carefully assessed to meet the specific needs of the warehouse space.
Incorporating additional features such as lighting, security systems, fire safety measures, loading docks, office spaces, and maintenance considerations can impact the overall cost of warehouse construction.
Lighting plays a crucial role in ensuring a well-lit and productive work environment within the warehouse.
Security systems are essential for safeguarding valuable inventory and assets.
Fire safety measures are vital to protect against potential hazards and comply with safety regulations.
Installing loading docks efficiently facilitates the smooth flow of goods in and out of the warehouse.
Adequate office spaces are necessary for administrative tasks and employee workstations.
Considering maintenance requirements upfront helps in long-term cost management and operational efficiency.
Estimating the cost of constructing a 25,000 sq ft warehouse involves analyzing the total expenses and creating a detailed breakdown of construction costs for accurate budgeting.
Labor expenses vary depending on the complexity of the project and the region’s prevailing wages. Other essential components to factor in include professional fees, insurance, utilities connection fees, and any specialized installations.
By breaking down the costs into these categories, project managers can gain better control over the budget and ensure a successful construction process.
Determining the cost per square foot is a critical factor in estimating the overall expenses of building a warehouse, reflecting the pricing structure based on the total square footage.
This metric is a fundamental component in determining the budget for warehouse construction projects. By calculating the cost per square foot, stakeholders can gain insights into how much they should allocate for the construction process. For instance, if a warehouse has a total square footage of 50,000 and the estimated cost per square foot is $100, the overall cost can be projected at $5,000,000. This calculation helps in making informed decisions regarding material choices, design aspects, and overall budget planning.
Creating a comprehensive breakdown of total construction costs involves analyzing expenses, budget allocations, contingency plans, tax considerations, insurance coverage, and financing options for the project.
Understanding how the expenses are categorized within a warehouse construction project is crucial. These costs typically include materials, labor, equipment rental, permits, and professional fees. Budget planning involves setting realistic financial boundaries for each aspect of the construction process to avoid overspending.
In terms of contingency strategies, it’s essential to set aside a portion of the budget for unexpected costs or changes in the project scope. Tax implications must also be carefully calculated to ensure compliance with local laws and regulations, potentially affecting the overall cost.
Exploring different insurance requirements for the project can provide protection against unforeseen events that could impact the construction timeline or budget. Selecting the appropriate financing mechanisms, such as loans, grants, or partnerships, can play a significant role in ensuring cost-effective construction while maintaining financial stability throughout the project.
Exploring strategies to reduce warehouse construction costs involves optimizing budget allocations, selecting cost-effective locations, simplifying design choices, considering alternative materials, and negotiating effectively with contractors.
Selecting a cost-effective location for a warehouse involves evaluating land costs, site preparation expenses, utility connection fees, and potential tax implications to ensure optimal budget utilization.
When determining the ideal warehouse location, it is crucial to consider the prevailing land prices in the area. Land costs can vary significantly depending on the region, proximity to transportation hubs, and local market dynamics.
Analyzing the site preparation requirements is essential to avoid unexpected expenses during construction. Understanding the utility connection fees and availability of services such as electricity, water, and internet is also key in the decision-making process. Assessing the tax considerations associated with different locations can help in maximizing cost savings over the long term.
Simplifying the design of a warehouse can lead to cost savings by reducing material expenses, focusing on essential finishes, optimizing interior and exterior layouts, and streamlining construction processes.
When opting for a straightforward warehouse layout, you not only save on construction costs but also benefit from improved construction efficiency. By minimizing material usage and prioritizing finishes, you can achieve a clean, functional space that meets your needs without unnecessary complexities.
This approach not only enhances the overall aesthetics of the building but also makes maintenance and future modifications easier. A simple warehouse design allows for quicker construction timelines, reducing labor costs and potential project delays.
Exploring alternative materials in warehouse construction can promote sustainability, enhance energy efficiency, and potentially reduce long-term operational costs by leveraging eco-friendly and resource-efficient building components.
Utilizing materials such as reclaimed wood, recycled steel, and renewable resources like bamboo or cork can significantly lower the environmental impact of warehouse construction. These eco-friendly options not only contribute to reducing carbon emissions but also help in conserving natural resources.
The use of such materials can lead to improved indoor air quality, creating a healthier work environment for warehouse staff. By incorporating sustainable materials, warehouses can align with modern construction trends that prioritize environmental stewardship and long-term cost savings.
Engaging in effective negotiations with contractors can lead to cost control measures, value engineering opportunities, and optimized pricing structures that align with budget constraints for warehouse construction projects.
Negotiating with contractors requires careful evaluation of project needs, clear communication of expectations, and establishing mutually beneficial agreements.
Implementing value engineering practices involves exploring alternative materials, methods, and designs that can reduce costs without compromising quality.
To optimize pricing agreements, contractors can be incentivized to propose innovative solutions and cost-saving techniques.
By prioritizing open dialogue, fostering collaborative relationships, and conducting thorough research on market rates, project owners can ensure successful negotiations that balance affordability with construction standards.
Site selection for warehouse construction involves evaluating soil conditions, drainage issues, and environmental considerations. Factors like contaminated soil or protected habitats may require remediation or special permits, adding complexity to the process. Proximity to transportation hubs and zoning regulations must be carefully assessed to ensure compliance and operational efficiency.
Navigating zoning regulations and obtaining necessary permits can be complex and time-consuming. Regulations governing land use, building height, setback requirements, and environmental impact assessments can vary significantly between jurisdictions, requiring coordination with multiple government agencies. Delays in the permitting process can impact project timelines and incur additional costs.
Designing a warehouse layout that maximizes storage capacity, material flow, and operational efficiency requires collaboration between architects, engineers, and logistics experts. Advanced technologies like 3D modeling and simulation software can aid in visualizing and refining design concepts before construction begins. Balancing competing priorities such as space utilization, accessibility, and safety is essential.
Selecting the right construction materials and methods is crucial for ensuring the durability, functionality, and sustainability of the warehouse. Factors such as environmental impact, long-term maintenance costs, and energy efficiency must be considered when choosing materials. Sustainable building practices, including the use of recycled materials and energy-efficient design strategies, are increasingly important considerations.
Managing the budget and timeline for warehouse construction requires accurate cost estimation, expense tracking, and proactive risk management. Contingency plans should be in place to address unforeseen circumstances or changes in project scope that may affect the budget or timeline. Developing a realistic construction schedule involves careful coordination of activities and resources to ensure timely completion of the project. Delays in obtaining permits, adverse weather conditions, or shortages of skilled labor can impact the construction schedule.
The construction of a 25,000 sq ft warehouse is a complex endeavor with costs influenced by location, materials, and labor, averaging between $750,000 and $1.5 million. At Estimate Florida Consulting, we specialize in providing detailed and customized cost assessments, ensuring each project aligns with specific needs and budgets. Our focus extends from selecting optimal materials to enhancing labor efficiency, guiding clients through every project phase with expertise. Our goal is to ensure each warehouse construction venture is not only cost-effective but also meets the functional requirements of our clients, combining financial practicality with operational excellence for successful project completion.
From small to large projects, residential to commercial, we’re here to help you win. Fast results guaranteed.
The average cost to build a 25000 sq ft warehouse can vary greatly depending on factors such as location, materials used, and labor costs. However, on average, it can cost anywhere from $750,000 to $1.5 million.
The main factors that affect the cost of building a 25000 sq ft warehouse include the type of materials used, the complexity of the design, the location, and any additional amenities or features included.
This ultimately depends on your specific needs and budget. Generally, buying a pre-built warehouse may be more cost-effective, but building a custom warehouse allows for more control over design and can save money in the long run.
In addition to construction costs, there may be additional expenses to consider such as building permits, site preparation, utility connections, and interior finishing costs.
Some ways to potentially reduce the cost of building a 25000 sq ft warehouse include choosing more cost-effective materials, simplifying the design, and being open to alternative locations or building methods.
While it is not required, it is highly recommended to hire a professional contractor or construction company with experience in building warehouses. They can help ensure the project stays within budget and is completed efficiently and safely.
Here I am going to share some steps to get your it cost to build a 25000 sq ft warehouse estimate report.
You can send us your plan on info@estimatorflorida.com
Before starting your project, we send you a quote for your service. That quote will have detailed information about your project. Here you will get information about the size, difficulty, complexity and bid date when determining pricing.
Our team will takeoff and estimate your project. When we deliver you’ll receive a PDF and an Excel file of your estimate. We can also offer construction lead generation services for the jobs you’d like to pursue further.
561-530-2845
info@estimatorflorida.com
Address
5245 Wiles Rd Apt 3-102 St. Pete Beach, FL 33073 United States
561-530-2845
info@estimatorflorida.com
Address
5245 Wiles Rd Apt 3-102 St. Pete Beach, FL 33073 United States
All copyright © Reserved | Designed By V Marketing Media | Disclaimer