How Much Does Cement Cost Per Square Foot?
On average, the cost of cement ranges from $4.20 to $16.80 per square foot. This price range includes the cost of the cement itself as well as basic installation fees. However, the total cost can vary depending on the specifics of the project, including the type of cement used and the complexity of the installation. Basic cement, which is commonly used for sidewalks and driveways, tends to be on the lower end of the price spectrum, while high-strength and decorative cement, used for more specialized applications, can significantly increase the overall cost. For instance, basic cement might be suitable for a simple driveway, whereas decorative cement could be chosen for an elegant patio area, enhancing both durability and aesthetic appeal.
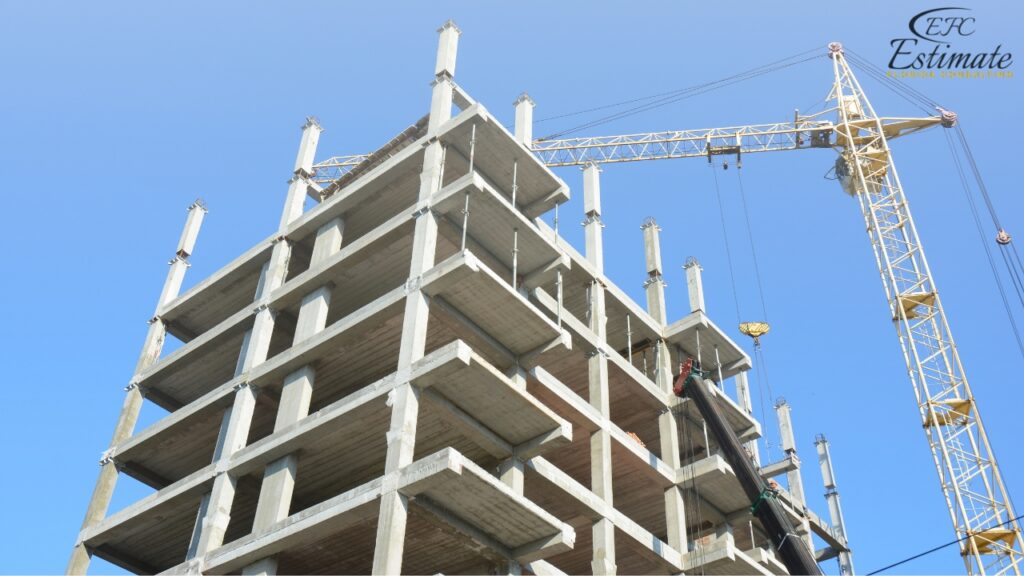
Furthermore, the costs may also be influenced by seasonal variations and market demand, making it essential to plan purchases during off-peak times if possible.
Type of Cement | Estimated Cost Per Square Foot |
Basic Cement | $4.20 – $7.00 |
High-Strength Cement | $7.00 – $11.20 |
Decorative Cement | $11.20 – $16.80 |
Factors Influencing Cement Costs
Type of Cement
The type of cement used in a project can significantly impact the overall cost. Basic cement is the most affordable option, while high-strength and decorative cement varieties are more expensive due to their enhanced properties and aesthetics. High-strength cement, for example, is often used in structural applications where durability is critical, whereas decorative cement is chosen for its visual appeal in spaces like patios or interior floors. The choice of cement type should align with the project’s requirements and desired outcomes to ensure cost-effectiveness and functionality. Additionally, some types of cement may offer specific advantages such as improved resistance to environmental factors or better load-bearing capabilities, which can justify their higher costs.
Location and Region
Geographical location plays a crucial role in the cost of cement. Prices can vary based on regional demand, availability of raw materials, and transportation costs. Urban areas might have higher prices compared to rural regions due to higher operational costs. In addition, regions with limited access to raw materials or those that rely heavily on imported cement might see higher prices. Understanding the regional pricing dynamics can help in better budget planning and potentially finding cost-saving opportunities by sourcing materials from nearby suppliers. Being aware of local market conditions can also help you time your purchases strategically, taking advantage of seasonal price fluctuations and promotions offered by suppliers.
Quantity and Scale of Project
Larger projects typically benefit from bulk pricing, which can reduce the cost per square foot. Smaller projects may incur higher costs due to the lack of volume discounts and additional charges for small deliveries. For instance, a large commercial project might secure better pricing per square foot compared to a small residential project. Contractors often offer discounts for bulk orders, making it economically viable to purchase more significant quantities at once if the project scope allows it. Planning the project scale carefully can lead to substantial savings, especially when negotiating with suppliers for bulk purchases. Additionally, coordinating with other projects or combining orders with neighboring sites can further enhance bulk purchasing advantages.
Installation and Labor
The cost of labor and installation can vary widely depending on the complexity of the project, local labor rates, and the contractor’s experience. Simple installations will be less expensive, whereas projects requiring specialized skills or decorative finishes will increase the overall cost. Labor costs also include site preparation, mixing, pouring, and finishing the cement, each of which can add to the overall expense. Ensuring that the chosen contractor has a proven track record can help avoid hidden costs and ensure quality workmanship. Investing in skilled labor can enhance the project’s overall quality and longevity, providing better value for your investment. Furthermore, experienced contractors can offer insights into efficient installation techniques and suggest materials that might offer better performance at a lower cost.
Breakdown of Cement Costs
Material Costs
The material cost of cement itself is a primary component of the total cost per square foot. Basic cement costs between $4.20 and $7.00 per square foot, high-strength cement ranges from $7.00 to $11.20, and decorative cement can cost between $11.20 and $16.80 per square foot. These prices reflect the raw materials needed for the project. Investing in quality materials can enhance the longevity and durability of the cement work, making it a crucial consideration for both budget and performance. High-quality materials can reduce the need for repairs and maintenance over time, offering long-term savings.
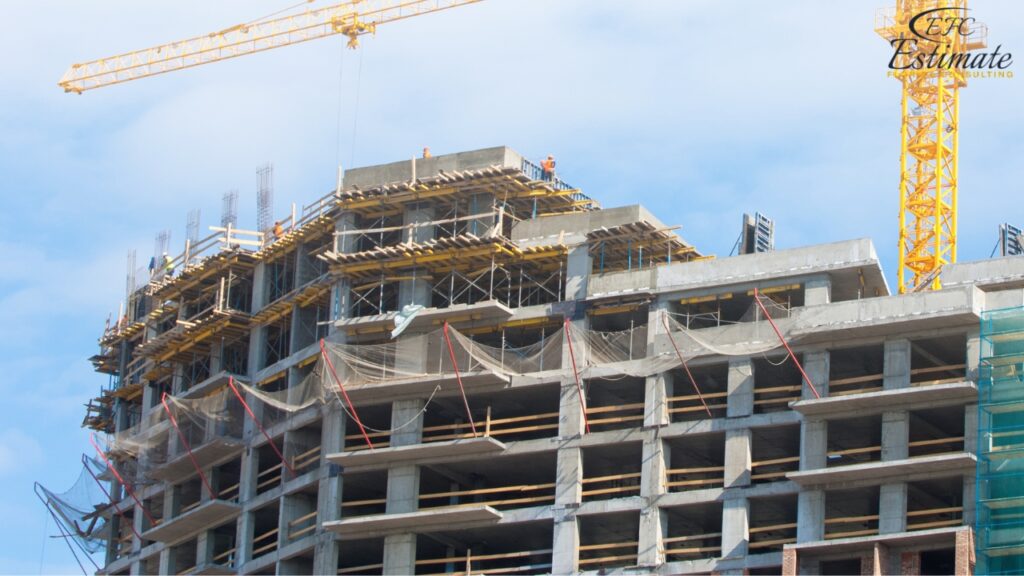
Additionally, opting for environmentally-friendly cement options can contribute to sustainable building practices, potentially qualifying for green building incentives.
Labor Costs
Labor costs for cement installation typically range from $2.80 to $8.40 per square foot. This includes site preparation, mixing, pouring, and finishing the cement. Complex designs or decorative finishes can increase labor costs. Hiring skilled labor ensures the job is done efficiently and correctly, which can save money in the long run by avoiding costly mistakes. Experienced contractors can also provide valuable insights into optimizing the installation process and selecting the best materials for the project. Quality workmanship can enhance the aesthetic appeal and structural integrity of the finished product. Moreover, considering labor costs in different seasons can help in planning, as some contractors might offer off-season discounts to secure work during slower periods.
Labor Cost Component | Estimated Cost Per Square Foot |
Basic Installation | $2.80 – $5.60 |
Complex Installation | $5.60 – $8.40 |
Additional Costs
Additional costs can include the preparation of the site, reinforcement materials (such as rebar or mesh), and any necessary permits or inspections. These additional costs can add $1.40 to $4.20 per square foot to the total project cost. Proper site preparation and reinforcement are essential for ensuring the longevity and durability of the cement installation. Neglecting these aspects can lead to structural issues and higher maintenance costs in the future. Including these costs in the budget helps ensure a comprehensive understanding of the total project expenses. Moreover, acquiring all necessary permits and adhering to local building codes can prevent legal issues and potential fines, ensuring smooth project progression.
Additional Cost Component | Estimated Cost Per Square Foot |
Site Preparation | $1.40 – $2.80 |
Reinforcement Materials | $0.70 – $2.10 |
Permits and Inspections | $0.70 – $1.40 |
90% More Chances to Win Projects With Our Estimate!
- Multi-Family Building
- Hotel Building
- Hospital Building
- Warehouse Building
- School & University Building
- High-Rise Building
- Shopping Complex
- Data Center Building
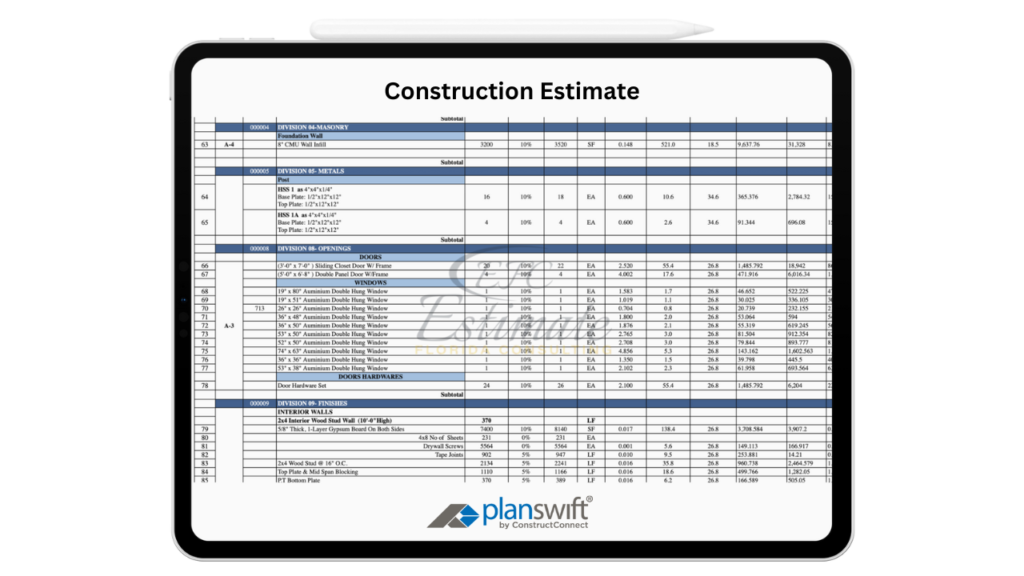
Cost Comparison by Cement Type
Basic Cement
Basic cement is suitable for standard construction projects and is the most cost-effective option. It offers good durability and strength for general use. Choosing basic cement can help keep the project within budget while still achieving satisfactory performance for everyday applications like sidewalks and driveways. However, it may lack the aesthetic appeal or specialized properties required for certain projects. Basic cement is often the go-to choice for budget-conscious projects that prioritize function over form. Understanding its limitations can help manage expectations and plan for potential upgrades in the future.
- Estimated Cost Per Square Foot: $4.20 – $7.00
- Ideal For: Sidewalks, driveways, and general construction.
High-Strength Cement
High-strength cement is designed for projects requiring greater durability and load-bearing capacity. It is often used in structural applications. The additional cost of high-strength cement is justified by its enhanced properties, making it ideal for critical structural elements that demand higher performance. This type of cement is essential for projects that experience heavy use or extreme conditions. Investing in high-strength cement can lead to longer-lasting structures, reducing the need for frequent repairs and replacements. Additionally, its superior performance under stress makes it suitable for industrial and commercial applications where reliability is paramount.
- Estimated Cost Per Square Foot: $7.00 – $11.20
- Ideal For: Foundations, heavy-use areas, and structural components.
Decorative Cement
Decorative cement includes options like stamped, stained, or polished finishes. It provides aesthetic appeal in addition to functional strength. Although decorative cement is more expensive, it offers unique design opportunities that can significantly enhance the visual appeal and value of a property. This type of cement is often used in residential and commercial spaces where appearance is as important as function. Incorporating decorative cement can transform ordinary spaces into visually striking environments, adding a touch of elegance and sophistication. The investment in decorative cement can also increase property value, making it a worthwhile consideration for upscale projects.
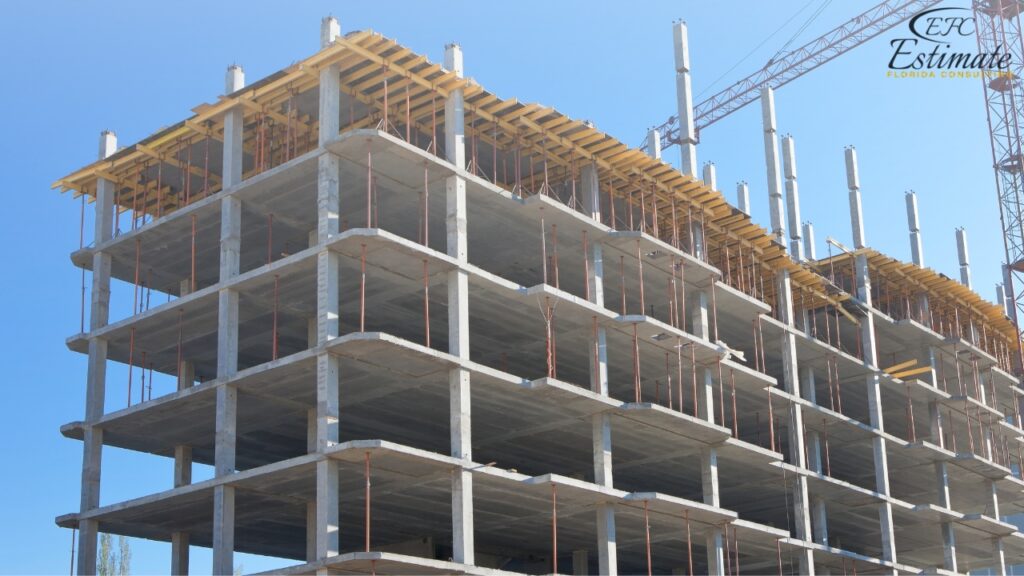
- Estimated Cost Per Square Foot: $11.20 – $16.80
- Ideal For: Patios, interior floors, and architectural features.
Average Cost to Replace Flooring by Location
Cement costs can vary depending on your geographical location. Urban areas with higher living costs might have higher cement prices compared to rural areas. Additionally, regions with easy access to raw materials might see lower prices compared to areas where materials need to be imported. Evaluating local market conditions can provide insights into potential cost variations and help in making informed decisions regarding material sourcing. Being aware of these variations can aid in planning and budgeting more accurately. Additionally, understanding the local market trends and seasonal fluctuations can help in timing purchases to take advantage of lower prices and promotions.
Floor Replacement Cost by Material
The type of material you are replacing with cement will also affect the overall cost. For example, replacing a wooden floor with cement might be less expensive than replacing a tile floor due to differences in removal and preparation costs. Each material has its unique set of challenges and costs associated with its removal and replacement. Properly assessing the existing flooring condition and the required preparation work can help in estimating the total replacement cost. Factoring in these considerations ensures a comprehensive budget that covers all aspects of the project. Moreover, understanding the specific requirements and challenges associated with different flooring materials can help in selecting the most cost-effective and efficient replacement options.
Download Template For Construction Project Breakdown
- Materials list updated to the zip code
- Fast delivery
- Data base of general contractors and sub-contractors
- Local estimators
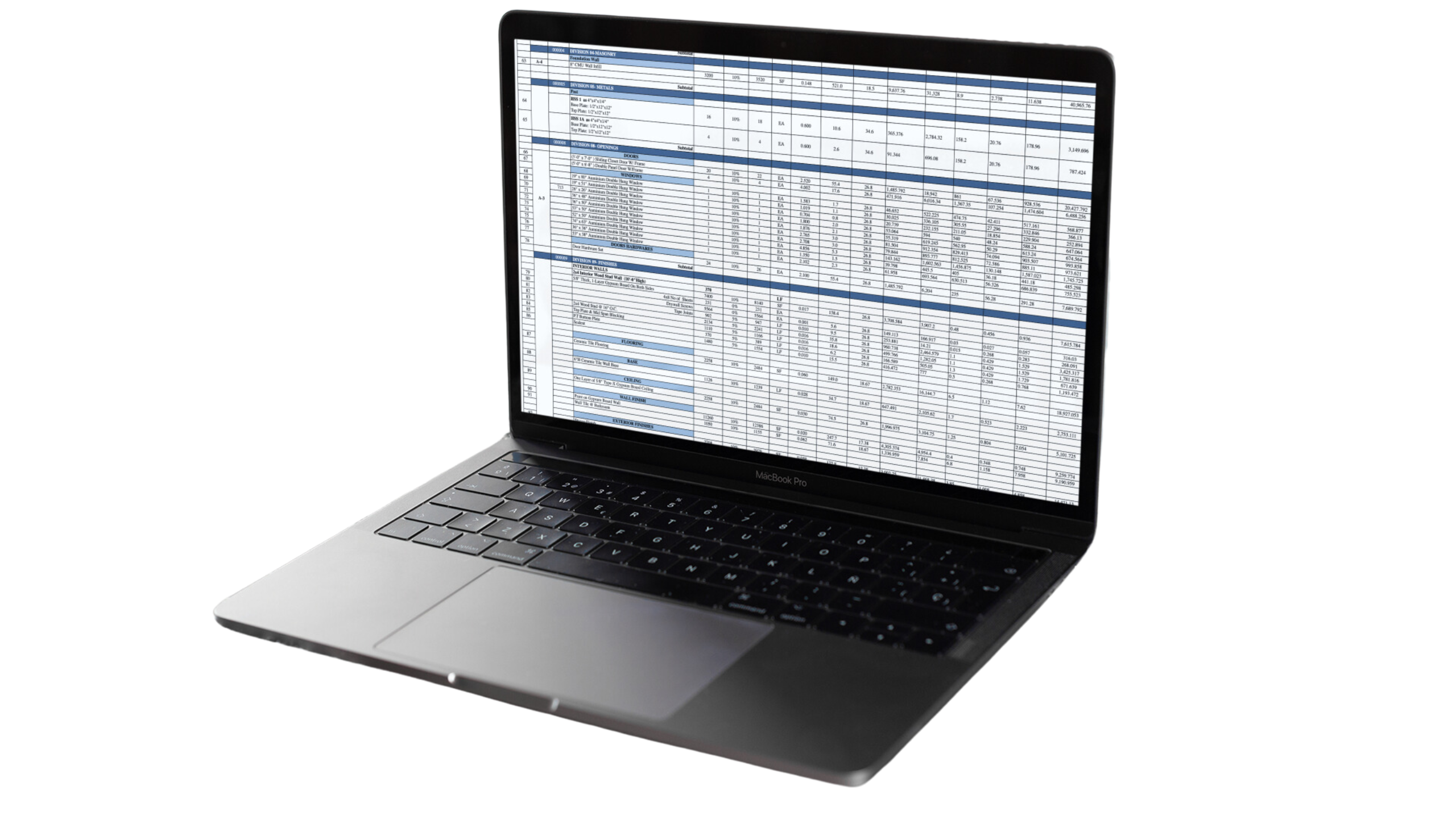
Conclusion
The cost of cement per square foot is influenced by various factors, including the type of cement, project location, and additional costs for installation and materials. On average, you can expect to pay between $4.20 and $16.80 per square foot for cement, depending on these factors. By understanding these cost components and planning your project accordingly, you can ensure a more accurate budget and a successful outcome. Investing in the right type of cement and skilled labor can enhance the durability and aesthetics of the project, providing long-term value and satisfaction. Proper planning and budgeting can lead to significant cost savings and a smoother construction process.
FAQs
On average, the cost of cement ranges from $4.20 to $16.80 per square foot. This price includes the cost of the cement itself and basic installation fees. The total cost can vary based on the type of cement used and the complexity of the installation.
The costs vary based on the type of cement:
- Basic Cement: $4.20 – $7.00
- High-Strength Cement: $7.00 – $11.20
- Decorative Cement: $11.20 – $16.80
Several factors can affect cement costs:
- Type of Cement: Basic, high-strength, and decorative cements have different price points.
- Location and Region: Prices vary due to regional demand, raw material availability, and transportation costs.
- Quantity and Scale of Project: Larger projects can benefit from bulk pricing, reducing the cost per square foot.
- Installation and Labor: Costs vary depending on project complexity, local labor rates, and contractor experience.
The type of cement significantly impacts the cost:
- Basic Cement is affordable and suitable for general use like sidewalks and driveways.
- High-Strength Cement is more expensive due to its durability, used in structural applications.
- Decorative Cement costs the most, offering enhanced aesthetics for patios and interior floors.
Geographical location influences cement costs due to:
- Regional demand and availability of raw materials.
- Transportation costs.
- Urban areas typically have higher prices due to operational costs, while rural areas may have lower prices.
Larger projects can secure better bulk pricing, reducing the cost per square foot. Smaller projects might incur higher costs due to the lack of volume discounts and additional charges for small deliveries.
Google Reviews
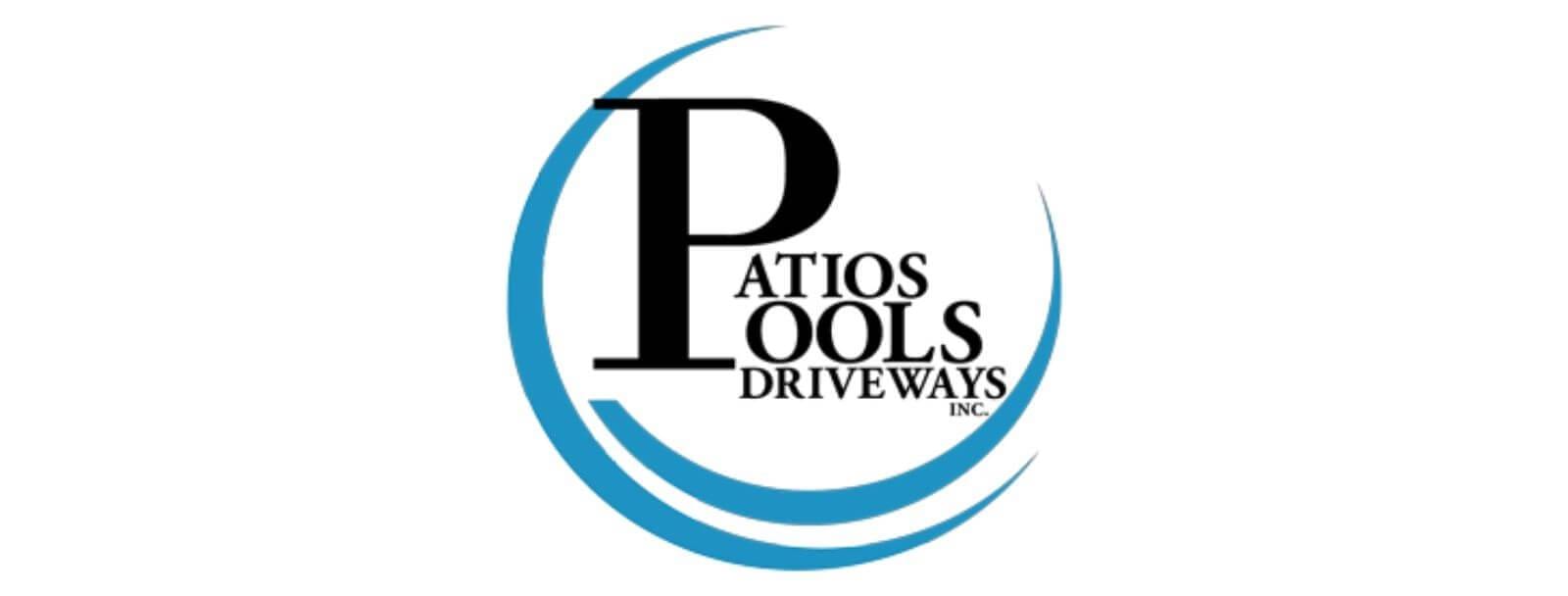
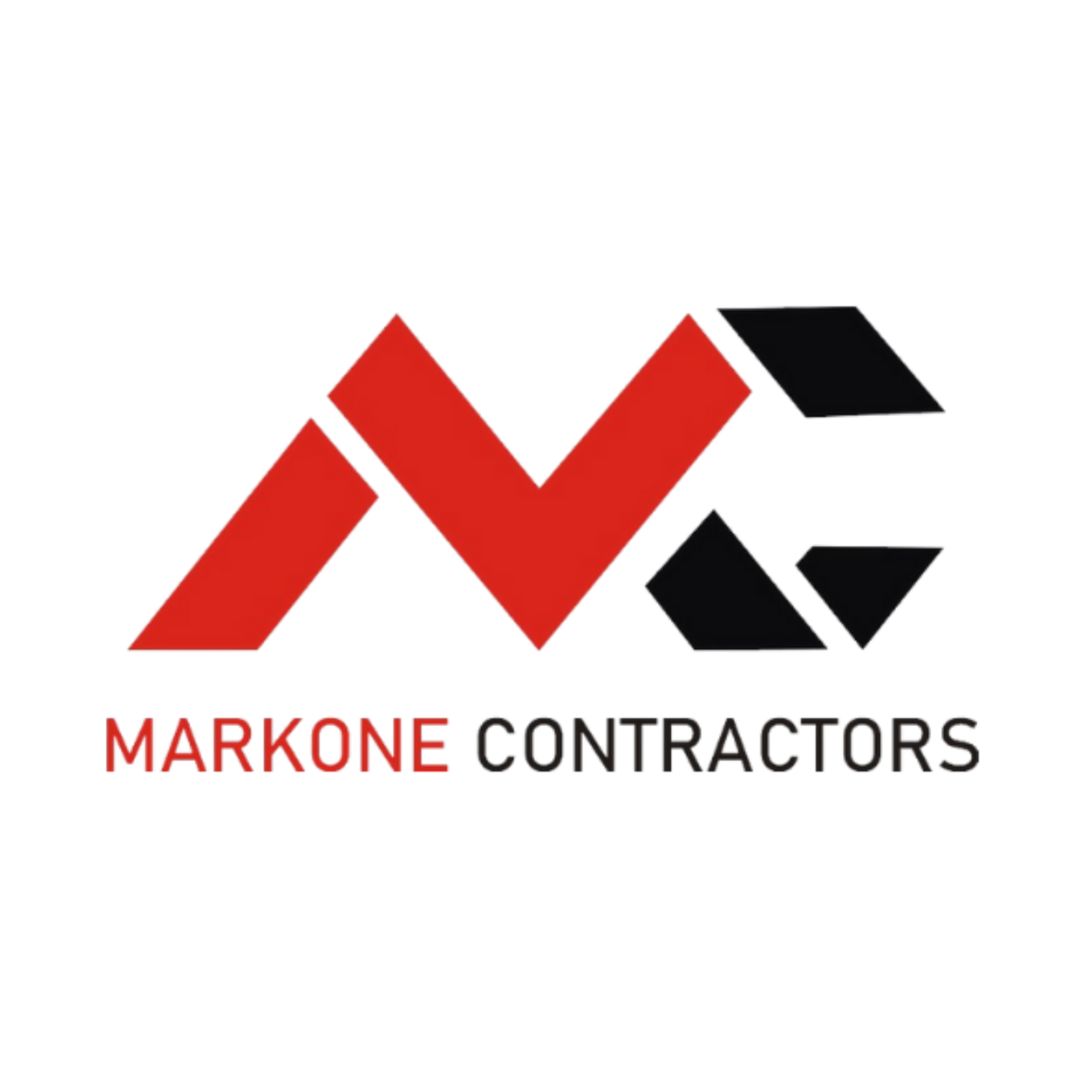

Process To Get Cement Cost Per Square Foot Estimate Report
Here I am going to share some steps to get cement cost per square foot estimate report.
-
You need to send your plan to us.
You can send us your plan on info@estimatorflorida.com
-
You receive a quote for your project.
Before starting your project, we send you a quote for your service. That quote will have detailed information about your project. Here you will get information about the size, difficulty, complexity and bid date when determining pricing.
-
Get Estimate Report
Our team will takeoff and estimate your project. When we deliver you’ll receive a PDF and an Excel file of your estimate. We can also offer construction lead generation services for the jobs you’d like to pursue further.