How Much Does an Elevator Cost for
a 10-Story Building?
An elevator for a 10-story building typically costs between $185,472 and $370,944, averaging $250 to $500 per square foot. This includes the elevator unit ($120,000 to $200,000), installation ($65,472 to $170,944), permits ($2,000 to $5,000), and necessary building modifications. Costs vary based on the type of elevator (hydraulic, traction, or machine-room-less), customization options, and the building’s structural requirements. Additional expenses may arise from structural changes ($20,000 to $50,000), electrical work ($5,000 to $10,000), and finishes ($5,000 to $15,000). To ensure a successful installation, obtain multiple quotes, choose a reliable installer, and plan for long-term maintenance. Proper installation enhances accessibility and property value.
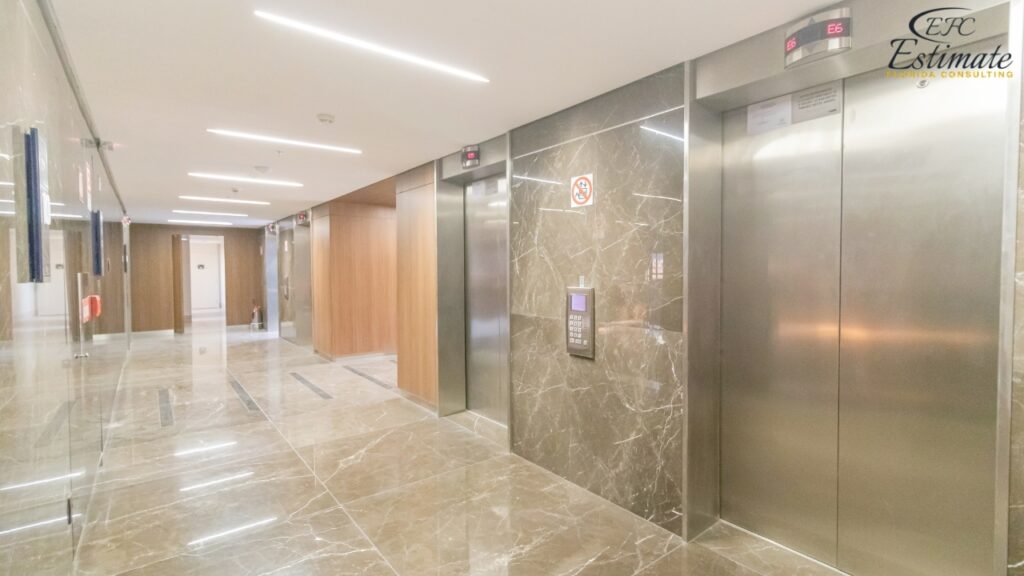
Cost Breakdown for a 10-Story Building Elevator
Equipment Costs
The cost of the elevator equipment itself varies based on the type and features. Here is a rough estimate of equipment costs for a 10-story building:
Type of Elevator | Estimated Cost |
Hydraulic | $100,800 – $201,600 |
Traction | $67,200 – $134,400 |
Machine Room-Less (MRL) | $60,480 – $120,960 |
Hydraulic elevators are the most expensive due to their complex systems and the requirement for a machine room. Traction elevators are more energy-efficient and faster, making them suitable for taller buildings. Machine Room-Less elevators are a space-efficient and modern option that balances cost and functionality. Each type of elevator has its advantages and is suited to different building requirements, influencing the overall project cost and expected performance. Considering the specific needs and constraints of the building can help determine the most cost-effective and suitable elevator type. Additionally, investing in higher-quality equipment can ensure better performance and longevity, potentially reducing long-term maintenance and operational costs.
Roofing Videos
Commercial Roofing
Metal Roof Installation
Roof Installation
Installation Costs
Installation costs can vary widely depending on the complexity of the project. Here’s an estimate of installation costs for a 10-story building:
Installation Component | Estimated Cost |
Basic Installation | $40,320 – $80,640 |
Structural Modifications | $20,160 – $40,320 |
Electrical Work | $10,080 – $20,160 |
Basic installation includes setting up the elevator, integrating it into your building, and ensuring it meets all safety standards. Structural modifications might include reinforcing floors or modifying walls to accommodate the elevator. Electrical work involves wiring and connections, essential for powering the elevator and ensuring it operates safely and efficiently. The complexity and scope of these tasks can vary significantly based on the building’s existing infrastructure and design, impacting overall costs. Proper planning and coordination with other construction activities can help streamline the installation process and reduce potential disruptions. Engaging experienced professionals for the installation can ensure compliance with all safety standards and regulations, minimizing the risk of future issues and ensuring a smooth, efficient installation process.
Additional Costs
Additional costs can include permits, inspection fees, and maintenance plans. Here’s an estimate of additional costs for a 10-story building:
Additional Component | Estimated Cost |
Permits and Inspections | $2,016 – $4,032 |
Maintenance Plan (annually) | $4,032 – $8,064 |
Contingency Budget | $8,064 – $16,128 |
Permits and inspections are necessary to ensure the installation complies with local building codes and safety regulations. A maintenance plan is crucial for the ongoing safety and reliability of the elevator, covering regular inspections and any necessary repairs. A contingency budget accounts for unexpected expenses that might arise during installation. Properly accounting for these additional costs can help prevent budget overruns and ensure a smooth and compliant installation process. Additionally, these costs ensure that the elevator meets all legal and safety requirements, protecting both the building owner and its occupants. Planning for these additional costs from the outset can help avoid financial surprises and ensure that the project stays within budget.
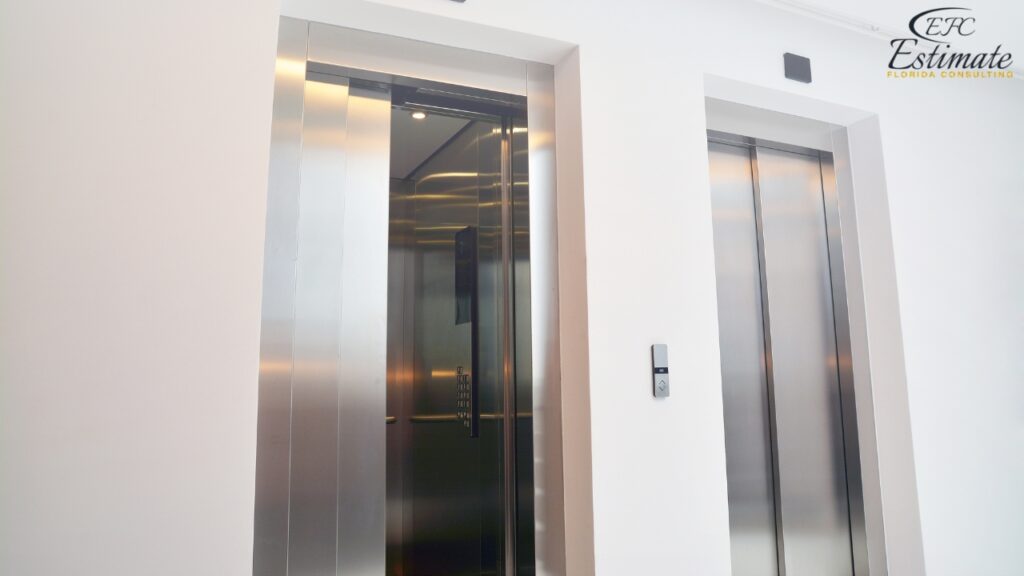
Detailed Cost Breakdown by Components
Hydraulic Elevators
Hydraulic elevators are known for their smooth ride and reliability. They require a machine room, which adds to the cost.
Component | Estimated Cost |
Elevator Car | $53,760 – $80,640 |
Hydraulic Pump System | $32,256 – $53,760 |
Machine Room Equipment | $21,504 – $33,600 |
Controls and Fixtures | $13,440 – $26,880 |
Hydraulic elevators provide a comfortable and efficient means of moving between floors, particularly in buildings where smooth operation and reliability are priorities. The need for a machine room and additional hydraulic components adds to the overall cost, but these elevators are highly regarded for their durability and performance. They are especially suitable for buildings with moderate traffic where their smooth and quiet operation can be fully appreciated. The long-term reliability and ease of maintenance of hydraulic elevators make them a cost-effective choice despite their higher initial cost. Additionally, hydraulic elevators can be easier to service and repair, which can contribute to lower maintenance costs over their lifespan.
Traction Elevators
Traction elevators use a counterweight system and don’t require a machine room, making them a more space-efficient option.
Component | Estimated Cost |
Elevator Car | $43,008 – $67,200 |
Traction Equipment | $26,880 – $43,008 |
Controls and Fixtures | $13,440 – $26,880 |
Traction elevators are known for their quiet operation and energy efficiency. These elevators use a counterweight system, eliminating the need for a machine room and making them a space-saving option. Their efficiency and performance make them a popular choice for commercial installations, particularly in buildings where space is at a premium. Traction elevators are ideal for high-rise buildings where speed and energy efficiency are critical, providing a reliable and swift means of transportation across multiple floors. Although they have a higher initial cost, their long-term operational savings and efficiency can make them a cost-effective choice over time. The advanced technology used in traction elevators can also provide smoother rides and improved performance, enhancing user satisfaction. Furthermore, traction elevators typically have a longer lifespan compared to hydraulic elevators, which can further justify their higher upfront costs.
Machine Room-Less (MRL) Elevators
Machine Room-Less elevators are ideal for buildings with limited space and are typically easier to retrofit into existing structures.
Component | Estimated Cost |
Elevator Car | $40,320 – $67,200 |
Drive System | $20,160 – $33,600 |
Controls and Fixtures | $18,144 – $26,880 |
MRL elevators are compact and can be installed with minimal structural changes. They are perfect for buildings where space is a concern. These elevators provide an economical and efficient solution for enhancing accessibility without the need for extensive construction work. MRL elevators are increasingly popular due to their space-saving design and lower energy consumption, making them a sustainable and cost-effective option for modern buildings. Their integration into the existing structure without requiring a separate machine room translates to lower construction costs and faster installation times, offering significant advantages for both new constructions and retrofits. Additionally, MRL elevators often come with advanced features that improve safety, efficiency, and user experience, making them a modern and versatile choice for many building types. The compact design of MRL elevators can also allow for more flexible building layouts and increased rentable space, contributing to higher revenue potential.
Installation Costs
Installation costs can vary based on the complexity of the project and the specific requirements of your building. Here’s a detailed breakdown of installation costs:
Basic Installation
Basic installation includes setting up the elevator, integrating it into your building, and ensuring it meets all safety standards.
Task | Estimated Cost |
Setup and Integration | $32,256 – $53,760 |
Testing and Safety Checks | $8,064 – $13,440 |
Basic installation involves the fundamental tasks required to get the elevator operational. This includes the physical installation of the elevator, integration with the building’s existing systems, and comprehensive testing to ensure safety and functionality. Proper installation is crucial for the long-term performance and reliability of the elevator. Engaging qualified professionals for the installation ensures adherence to all safety protocols and industry standards, thereby minimizing the risk of future operational issues. The involvement of experienced installers also helps in addressing any unforeseen challenges promptly, ensuring the project stays on schedule and within budget.
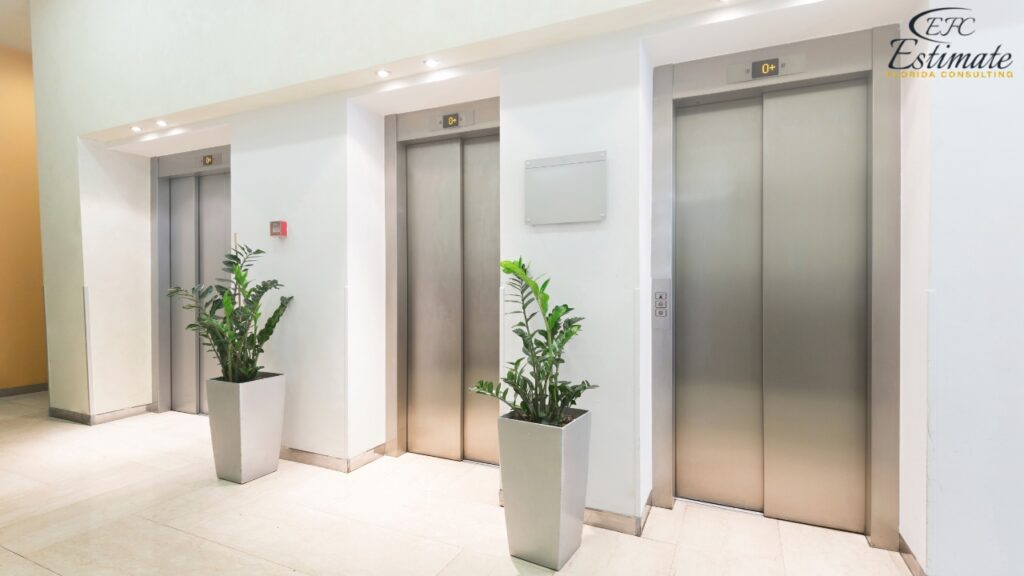
Proper planning and execution during the installation phase can also prevent costly repairs and modifications in the future. Additionally, thorough testing and safety checks can ensure the elevator operates smoothly and safely from the outset, reducing the risk of early operational issues.
Structural Modifications
Structural modifications might be necessary to accommodate the elevator, such as reinforcing floors or modifying walls.
Task | Estimated Cost |
Reinforcing Floors | $16,128 – $26,880 |
Modifying Walls | $16,128 – $26,880 |
Structural modifications ensure that the building can safely support the new elevator system. This can involve reinforcing floors to handle the additional weight or modifying walls to create the necessary space for the elevator shaft. These modifications are essential for the safety and stability of the installation. Addressing structural modifications early in the planning process can prevent delays and unexpected costs during installation, ensuring a seamless integration of the elevator into the building’s infrastructure. Proper structural modifications also enhance the overall durability and safety of the elevator system, providing peace of mind to building owners and occupants. Investing in high-quality materials and construction practices for structural modifications can further ensure the longevity and performance of the elevator. Additionally, early planning and coordination with structural engineers can help identify potential issues and address them proactively, reducing the risk of costly changes during the construction phase.
Electrical Work
Electrical work is essential for powering the elevator and ensuring it operates safely and efficiently.
Task | Estimated Cost |
Wiring and Connections | $6,720 – $13,440 |
Electrical Panel Upgrades | $3,360 – $6,720 |
Electrical work involves connecting the elevator to the building’s power supply and ensuring that all electrical components are installed correctly. This includes wiring, connections, and any necessary upgrades to the electrical panel. Proper electrical installation is critical for the safe operation of the elevator and compliance with building codes. Ensuring that the electrical system is robust and capable of handling the elevator’s power requirements is crucial for preventing operational disruptions and ensuring long-term reliability. Additionally, implementing energy-efficient electrical components can reduce operational costs and enhance the overall sustainability of the building. Engaging experienced electricians and ensuring all work meets industry standards and regulations can prevent future electrical issues and ensure safe, reliable operation. Proper electrical installation can also enhance the overall efficiency and performance of the elevator system, reducing energy consumption and operating costs over time.
Additional Costs
Additional costs include permits, inspection fees, and a maintenance plan to keep the elevator in good working condition.
Additional Component | Estimated Cost |
Permits and Inspections | $2,016 – $4,032 |
Maintenance Plan (annually) | $4,032 – $8,064 |
Contingency Budget | $8,064 – $16,128 |
Permits and inspections are necessary to ensure the elevator installation complies with local building codes and safety regulations. Regular maintenance is essential for the long-term reliability and safety of the elevator, covering routine inspections and necessary repairs. A contingency budget accounts for unexpected expenses that may arise during the installation process, such as additional structural modifications or unforeseen technical issues. Properly budgeting for these additional costs ensures that the project stays on track and avoids financial surprises, contributing to a smoother and more predictable installation process. These costs also ensure that the elevator remains compliant with regulatory standards, reducing the risk of legal issues and ensuring the safety of building occupants. Planning for these additional costs from the outset can help avoid financial surprises and ensure that the project stays within budget. Regular inspections and maintenance can also extend the lifespan of the elevator system and reduce the likelihood of unexpected breakdowns or costly repairs.
Get 5 New Leads Next 7Days With Our System
- Multi-Family Building
- Hotel Building
- Hospital Building
- Warehouse Building
- High-Rise Building
- Shopping Complex
Factors Influencing the Cost of an Elevator in a 10-Story Building
Type of Elevator
The type of elevator you choose will have a major impact on the cost. Several types are suitable for a 10-story building, each with its own features and installation requirements:
- Hydraulic Elevators: Common in low- to mid-rise buildings, these elevators require a machine room and are known for their smooth ride and reliability. However, they tend to be more expensive due to their complex installation. Hydraulic elevators use a fluid-driven piston to move the elevator car, providing a smooth and quiet operation, ideal for buildings where noise levels need to be minimized. These elevators are especially suitable for residential complexes and hotels where comfort and quiet operation are critical. The need for a machine room increases installation space requirements and costs but ensures excellent long-term reliability and ease of maintenance. Additionally, hydraulic elevators are typically easier to repair and maintain, which can lead to lower ongoing maintenance costs over the lifespan of the elevator. The hydraulic system’s simplicity also makes it less prone to mechanical failure, enhancing overall reliability.
- Traction Elevators: Using a counterweight system, these elevators are more energy-efficient and faster than hydraulic elevators, making them suitable for mid- to high-rise buildings. They are driven by electric motors and use steel ropes to lift the elevator car. Traction elevators are ideal for busy commercial buildings like office towers and shopping centers, where quick and frequent elevator use is essential. Although they have a higher initial cost, they offer savings over time due to lower energy consumption and operational costs. The faster speed and higher efficiency of traction elevators can also improve the overall user experience, reducing wait times and enhancing the building’s appeal to potential tenants and visitors. Additionally, traction elevators generally have a longer lifespan than hydraulic elevators, which can further justify their higher upfront costs.
- Machine Room-Less (MRL) Elevators: These elevators do not require a separate machine room, making them a space-efficient option. They are becoming increasingly popular in modern buildings due to their energy efficiency and smaller footprint. MRL elevators have the machinery located within the elevator shaft, which saves space and reduces construction costs. They are well-suited for buildings where maximizing usable space is crucial, such as urban office buildings and mixed-use developments. The absence of a machine room also simplifies building design and can lower overall project costs while providing similar benefits to traditional traction elevators. Furthermore, the reduced space requirements can allow for more flexible building layouts and increased rentable space, contributing to higher revenue potential. MRL elevators also tend to be quieter and more energy-efficient, which can contribute to lower operating costs over time.
Size and Capacity
The size and capacity of the elevator will also affect the cost. Larger elevators with higher weight capacities will generally cost more. For a 10-story building, a standard size typically supports 15-20 passengers or up to 3,500 pounds. The size and capacity not only impact the equipment cost but also the complexity of the installation and the amount of space required in the building. Larger elevators may also necessitate stronger structural support and more advanced safety systems, further increasing the cost. Choosing an appropriately sized elevator can enhance user convenience, reduce wait times during peak hours, and improve overall tenant satisfaction.
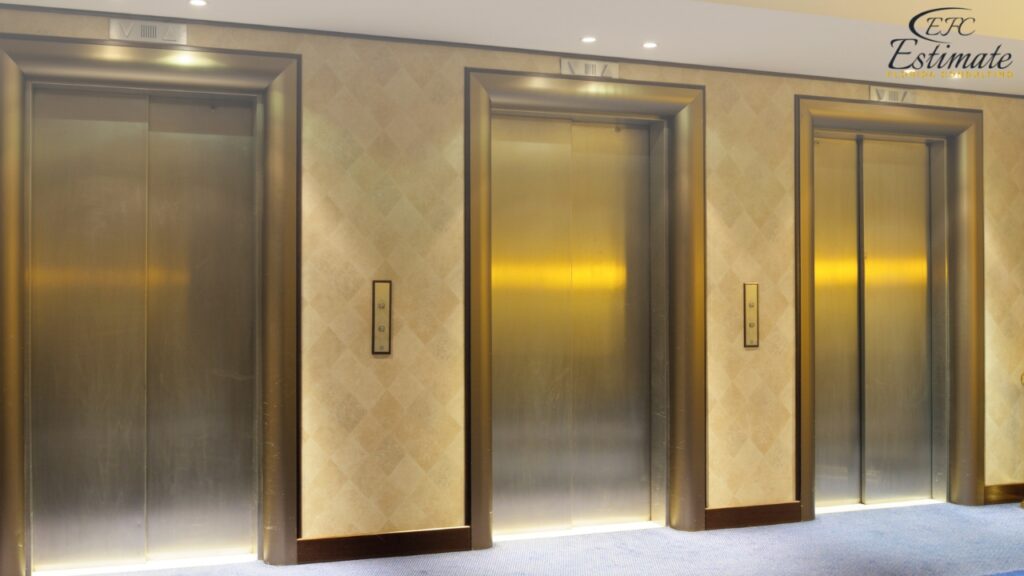
Additionally, larger elevators may be necessary for buildings with high traffic volumes or specific usage needs, such as hospitals or commercial centers, where efficient vertical transportation is critical. Ensuring the elevator is adequately sized for the building’s needs can prevent future operational issues and enhance the overall functionality of the space.
Customization and Features
Custom features such as high-end cabin finishes, advanced control systems, and additional safety features will add to the cost. Features like automatic doors, custom lighting, and high-end materials can significantly enhance the look and functionality of the elevator. Custom finishes like wood paneling, glass walls, and designer flooring can transform the elevator into a luxurious space. Advanced control systems can improve the efficiency and user experience, while additional safety features like emergency lowering systems and backup power supplies enhance reliability and safety. Investing in these features can provide long-term benefits, such as higher tenant satisfaction and potential increases in property value, making the initial cost worthwhile. Additionally, integrating smart technologies, such as touchless controls and energy-efficient lighting, can further enhance the elevator’s appeal and functionality, aligning with modern building standards and user expectations. Custom features can also be tailored to match the building’s aesthetic, creating a cohesive and attractive design that adds to the overall appeal of the property.
Installation Complexity
The complexity of the installation can significantly influence the cost. Factors such as structural modifications needed, the location of the elevator, and the difficulty of integrating it into the existing building layout will all play a role. Older structures or buildings with challenging layouts may require more extensive modifications. The installation process may also involve coordinating with other construction activities and ensuring compliance with local building codes and regulations, adding to the complexity and duration of the project. Thorough planning and site assessment can help mitigate unexpected challenges, ensuring a smoother installation process and potentially reducing overall costs. Additionally, engaging experienced contractors and engineers can minimize delays and ensure that the installation meets all safety and regulatory requirements, providing peace of mind and protecting the investment. Proper planning can also identify potential issues early, allowing for more efficient resolution and preventing costly delays or modifications later in the project.
Maintenance and Operating Costs
Ongoing maintenance and operating costs are important considerations. Regular maintenance ensures the elevator operates safely and efficiently. Maintenance plans can help manage these expenses by providing regular service and addressing issues before they become significant problems. Understanding these recurring costs is crucial for long-term budgeting and ensuring the elevator remains a reliable part of the building. Investing in high-quality maintenance services can extend the lifespan of the elevator and prevent costly repairs, ensuring it remains in optimal condition and operates smoothly for years to come. Additionally, energy-efficient models can reduce long-term operating costs by lowering electricity consumption, providing savings over the elevator’s lifetime. Proper maintenance also ensures compliance with safety regulations, reducing the risk of fines or legal issues. Moreover, well-maintained elevators can improve tenant satisfaction by minimizing downtime and ensuring a safe, reliable means of vertical transportation. Regular maintenance can also help identify and address minor issues before they escalate, reducing the likelihood of major repairs and extending the overall lifespan of the elevator system.
Download Template For Elevator Project Breakdown
- Materials list updated to the zip code
- Fast delivery
- Data base of general contractors and sub-contractors
- Local estimators
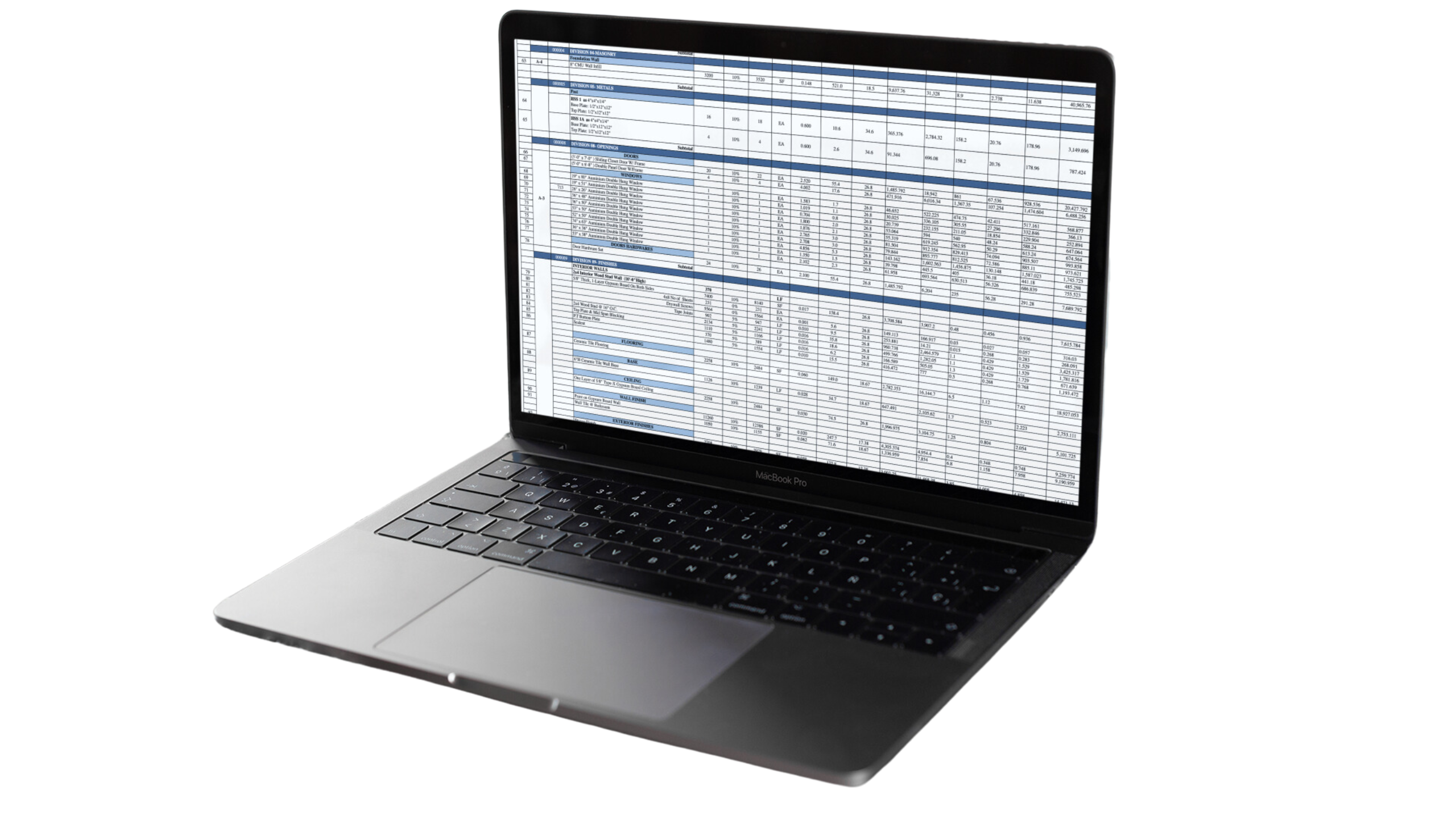
Conclusion
Installing an elevator in a 10-story building is a significant investment that requires careful planning and budgeting. By understanding the various costs involved and considering the factors that influence these costs, you can make informed decisions to ensure the success of your project. Investing in high-quality equipment, professional installation, and regular maintenance ensures a durable, reliable, and safe elevator that enhances the accessibility and value of your building. A well-installed elevator not only improves the functionality of the building but also adds to its overall appeal and market value. Moreover, thoughtful investment in quality components and installation practices can lead to lower maintenance costs and longer service life, providing better value over time. Properly managed, the installation and maintenance of an elevator can significantly enhance the user experience and operational efficiency of your 10-story building. Furthermore, a well-maintained elevator can contribute to higher tenant satisfaction and retention rates, making it a valuable asset for any multi-story building. Regular maintenance and upgrades can also ensure that the elevator system remains up-to-date with the latest safety standards and technological advancements, further enhancing its reliability and performance.
FAQs
The cost to install an elevator in a 10-story building typically ranges from $185,472 to $370,944, averaging $250 to $500 per square foot. This includes the elevator unit, installation, permits, and necessary building modifications.
Different types of elevators have varying costs based on their design and functionality. Hydraulic elevators are generally more expensive due to their complex systems, while machine room-less (MRL) elevators are typically more space-efficient and cost-effective.
Larger elevators with higher weight capacities cost more due to the additional materials and more powerful systems required to support the increased load. For a 10-story building, a standard size typically supports 15-20 passengers or up to 3,500 pounds.
Custom features such as high-end cabin finishes, advanced control systems, and additional safety features can increase the cost but provide enhanced aesthetics and functionality.
Regular maintenance and operating costs include annual maintenance plans ($4,032 – $8,064) and electricity. Proper maintenance ensures the elevator operates safely and efficiently, reducing the likelihood of costly repairs.
Google Reviews
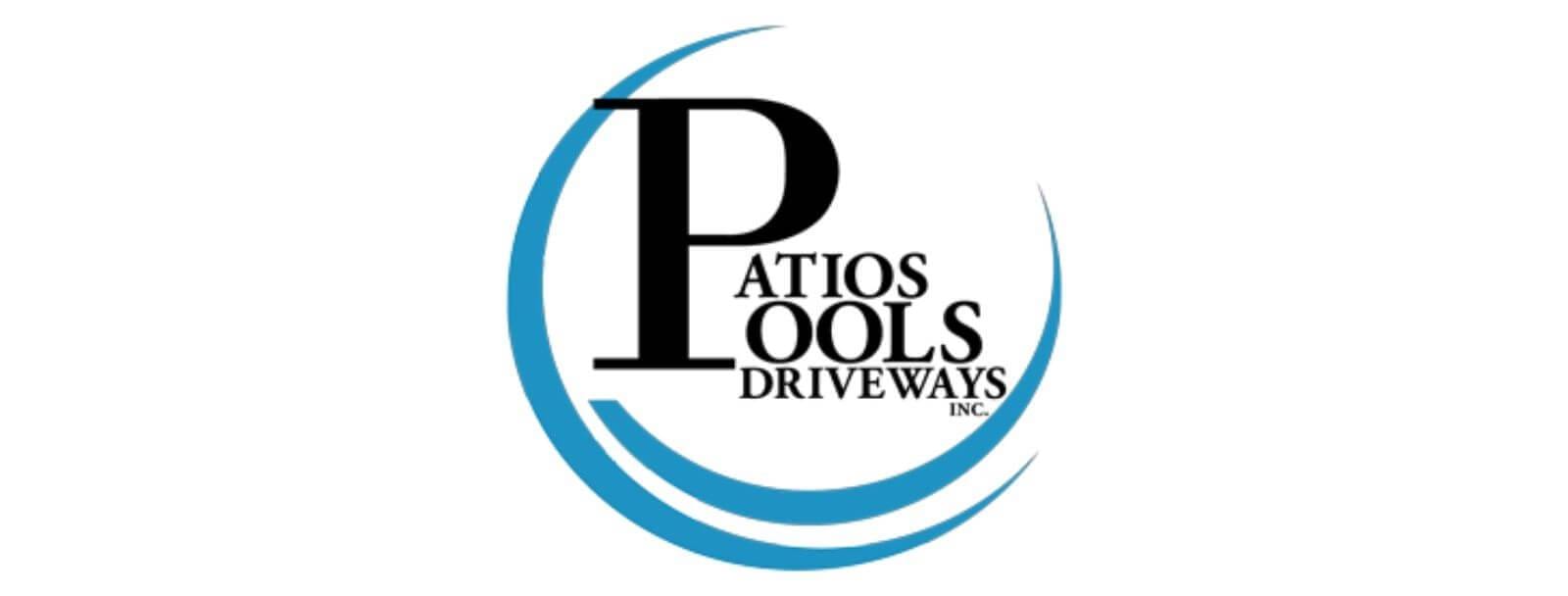
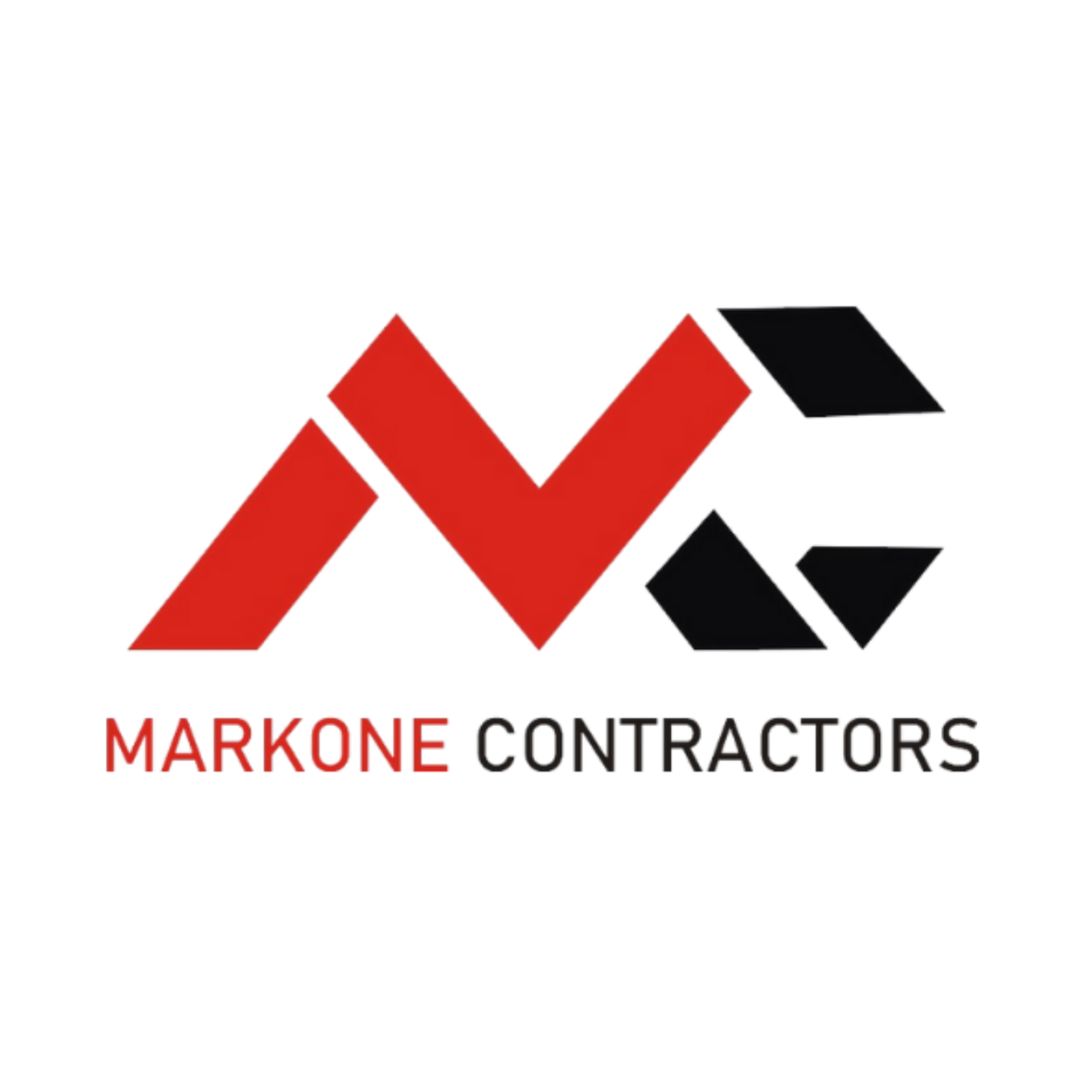

Process To Get an Elevator Cost for a 10-Story Building Estimate Report
Here I am going to share some steps to get an elevator cost for a 10-story building estimate report.
-
You need to send your plan to us.
You can send us your plan on info@estimatorflorida.com
-
You receive a quote for your project.
Before starting your project, we send you a quote for your service. That quote will have detailed information about your project. Here you will get information about the size, difficulty, complexity and bid date when determining pricing.
-
Get Estimate Report
Our team will takeoff and estimate your project. When we deliver you’ll receive a PDF and an Excel file of your estimate. We can also offer construction lead generation services for the jobs you’d like to pursue further.