- Homepage
- How Much Does a Concrete Column Cost?
How Much Does a Concrete Column Cost?
Leading provider of concrete column services.
Concrete columns are essential structural elements used in various types of construction projects, from residential buildings to large commercial structures. They provide the necessary support to bear loads and distribute weight evenly across the building. Understanding the cost of concrete columns is crucial for budgeting and planning any construction project. This article will break down the different factors influencing the cost of concrete columns, providing a detailed guide to help you estimate your expenses accurately. By considering factors like size, materials, labor, formwork, and additional costs, you can make informed decisions to optimize your budget and ensure the structural integrity of your project.
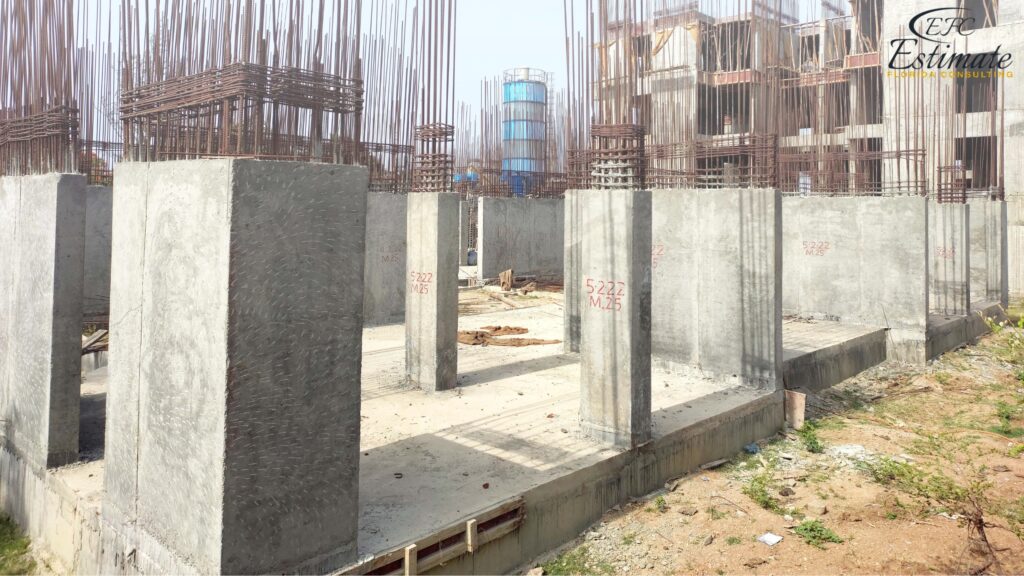
Factors Influencing the Cost of Concrete Columns
Size and Dimensions
The size and dimensions of the concrete columns significantly impact the overall cost. Larger and taller columns require more materials and labor, increasing the cost. The diameter and height of the column are critical factors; for example, a column with a larger diameter will need more concrete and reinforcement. Additionally, the complexity of the column design, such as tapered or decorative columns, can further increase costs due to additional labor and specialized materials. For instance, decorative columns may require custom molds and finishing techniques, adding to both material and labor expenses.
Column Size (Diameter x Height) | Estimated Cost |
12 inches x 10 feet | $243 – $729 |
18 inches x 15 feet | $608 – $1,822 |
24 inches x 20 feet | $1,458 – $3,645 |
90% More Chances to Concrete Bids with Our Estimate
Material Costs
The primary materials required for concrete columns are cement, aggregates (sand and gravel), water, and steel reinforcement. The quality and grade of these materials can affect the overall cost.
- Cement: $162 – $243 per ton. The type of cement used (e.g., Portland cement) and its grade can impact the cost. High-grade cement ensures better strength and durability, which is essential for structural integrity. Additionally, the choice of cement can influence the setting time and workability of the concrete mix, impacting the efficiency of the construction process.
- Aggregates: $14 – $68 per ton. The cost varies depending on the quality and type of aggregate used. Aggregates provide volume and stability to the concrete mix, and choosing high-quality aggregates can enhance the column’s strength and durability. The size and type of aggregates also affect the workability and finish of the concrete.
- Steel Reinforcement: $1.01 – $2.03 per pound. Steel bars (rebar) are essential for reinforcing the concrete columns, providing tensile strength and stability. The amount and type of steel reinforcement depend on the load-bearing requirements and the structural design. High-strength steel may be necessary for columns in earthquake-prone areas or high-load applications.
Material Component | Estimated Cost |
Cement (per ton) | $162 – $243 |
Aggregates (per ton) | $14 – $68 |
Steel Reinforcement (per pound) | $1.01 – $2.03 |
Labor Costs
Labor costs vary depending on the complexity of the project, the location, and the experience of the workers. On average, labor costs for constructing concrete columns can range from $68 to $203 per hour. The total labor cost will depend on the number of columns, their size, and the project’s overall complexity. Skilled labor is crucial for ensuring the structural integrity and quality of the concrete columns, as improper construction can lead to significant safety risks and additional costs for repairs. Labor costs also encompass the time spent on site preparation, formwork assembly, concrete pouring, and finishing, each requiring specific expertise and precision.
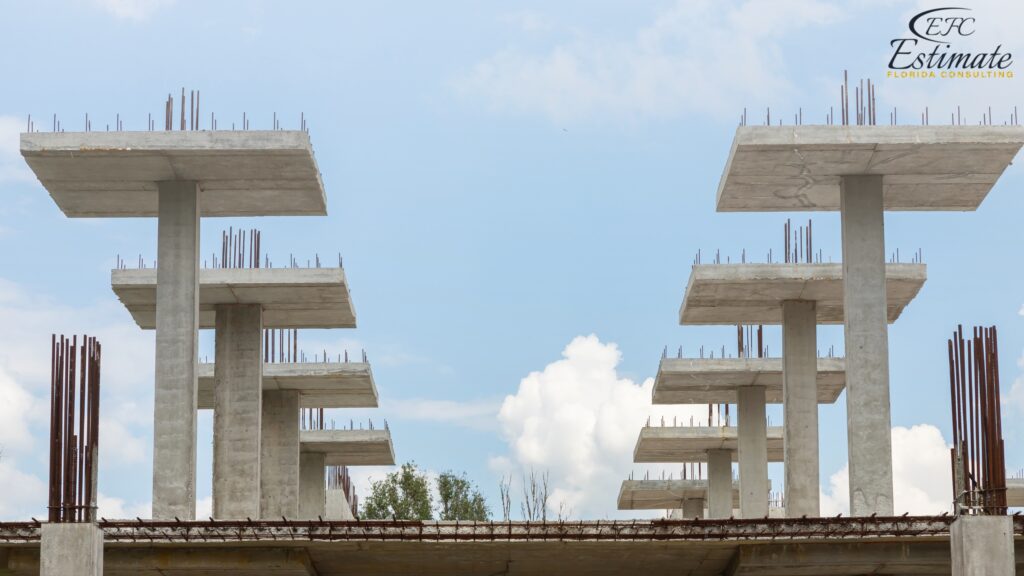
Labor Component | Estimated Cost |
Per Hour | $68 – $203 |
Total Labor Cost | $675 – $4,050 |
Formwork
Formwork is the temporary structure used to hold the concrete in place until it sets and gains enough strength. The cost of formwork can vary depending on the type of material used (wood, steel, or plastic) and the complexity of the design.
- Wood Formwork: $1.35 – $4.05 per square foot. Typically used for smaller projects and is easy to construct and dismantle. Wood formwork is versatile and can be easily adjusted to fit various column shapes and sizes. However, it may not be as durable as other types and might require frequent replacement.
- Steel Formwork: $2.70 – $6.75 per square foot. More durable and suitable for larger projects but more expensive. Steel formwork offers high precision and can be reused multiple times, making it cost-effective for large-scale projects. Its durability also ensures a smoother finish on the concrete surface.
- Plastic Formwork: $2.03 – $5.40 per square foot. Lightweight and reusable but can be costly for large projects. Plastic formwork is resistant to weather and chemicals, making it suitable for specialized construction needs. Its lightweight nature makes it easy to handle and assemble, reducing labor costs and time.
Formwork Type | Estimated Cost (per square foot) |
Wood | $1.35 – $4.05 |
Steel | $2.70 – $6.75 |
Plastic | $2.03 – $5.40 |
We Provide 3D Rendering Services!
For Building Construction and Other Projects
Turnaround time is 1-2 days.
Win More Projects With Us
Transportation and Miscellaneous Costs
Transportation costs for delivering materials to the construction site can also impact the overall cost. Additionally, miscellaneous expenses such as permits, inspections, and equipment rental should be considered. Proper planning and logistics can help minimize these costs by ensuring timely delivery and efficient use of materials and equipment. Coordinating deliveries to avoid delays and optimize labor scheduling is essential for keeping transportation costs manageable.
Miscellaneous Costs | Estimated Cost |
Transportation | $135 – $675 |
Permits and Inspections | $68 – $405 |
Equipment Rental | $135 – $675 per day |
Detailed Cost Breakdown for a Standard Concrete Column
Here’s a detailed cost breakdown for constructing a standard concrete column:
Cost Component | Estimated Cost |
Cement (1 ton) | $162 – $243 |
Aggregates (2 tons) | $28 – $137 |
Steel Reinforcement (200 lbs) | $202 – $405 |
Formwork (100 sq ft) | $135 – $405 |
Labor (20 hours) | $1,350 – $4,050 |
Transportation | $135 – $675 |
Permits and Inspections | $68 – $405 |
Equipment Rental (2 days) | $270 – $1,350 |
Total | $2,350 – $7,670 |
Examples of Total Costs for Different Scenarios
To provide a clearer picture, here are some examples of total costs for different scenarios:
Small Concrete Column (12 inches x 10 feet)
- Low-end: $2,350
- High-end: $3,375.
This includes essential components like materials, labor, and basic formwork without additional features. Suitable for small residential projects or minor structural supports. These columns typically support less weight and have simpler designs, which helps keep costs lower.
Medium Concrete Column (18 inches x 15 feet)
- Low-end: $4,860
- High-end: $7,290.
This scenario includes standard materials and some additional features like higher-quality steel reinforcement and more complex formwork. Ideal for medium-sized residential or commercial buildings. These columns need to support more weight and may require additional features like decorative elements or custom shapes.
Large Concrete Column (24 inches x 20 feet)
- Low-end: $6,750
- High-end: $7,670.
This includes high-end materials, advanced features like steel formwork, and high labor costs for complex projects. Suitable for large commercial or industrial structures requiring significant load-bearing capacity. These columns often involve more intricate designs and higher safety requirements, leading to increased costs.
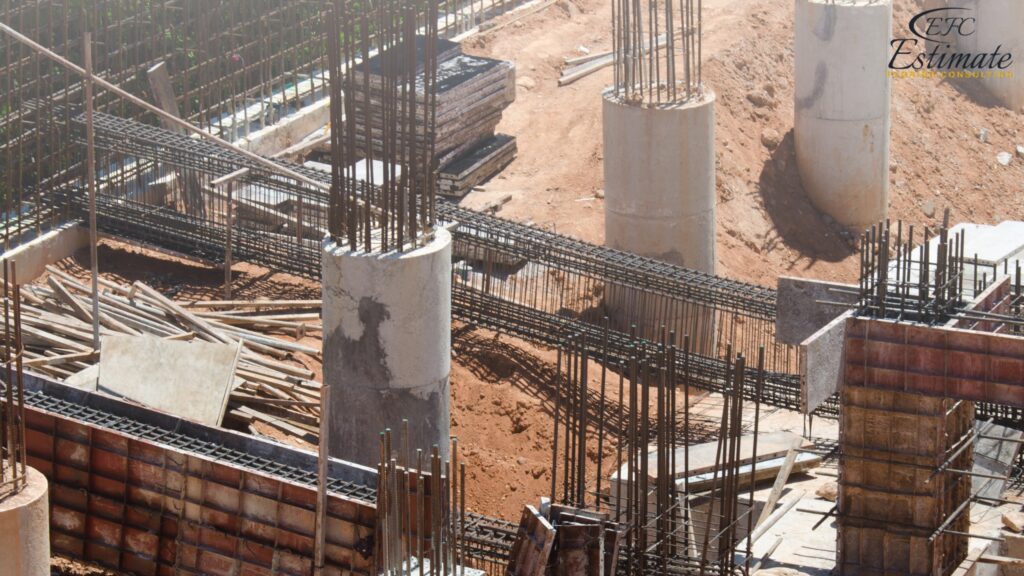
Cost Considerations by Region for Concrete Columns
The cost of building concrete columns can vary significantly depending on your location due to differences in labor costs, materials, and local economic conditions. Here’s a brief overview of regional cost variations:
- Northeast: Generally higher costs due to labor and material expenses. Expect to pay 10-20% more than the national average. The higher cost of living in this region often translates to increased construction costs. Additionally, the need for more robust structures to withstand harsh winter conditions can increase costs.
- Midwest: More affordable, with costs typically 5-15% lower than the national average. The lower cost of living and availability of materials can help keep prices more reasonable in this region. However, the shorter construction season due to harsh winters may impact project timelines and costs.
- South: Moderate costs, often close to the national average. The warm climate and steady housing market contribute to stable pricing for construction services. Lower labor costs in some Southern states can also help reduce overall expenses.
- West: Higher costs, similar to the Northeast, with variations depending on the urban or rural setting. Coastal areas and major cities tend to have higher labor and material costs, while rural areas may be more affordable. The need for specialized materials and construction techniques in earthquake-prone areas can also increase costs.
Understanding regional cost differences can help you budget more accurately and make informed decisions about hiring local contractors. It’s also helpful to ask for local references and view previous work to ensure you’re getting the best quality for your investment.
Advantages of Using Concrete Columns
Strength and Durability
Concrete columns are known for their strength and durability, making them an ideal choice for supporting heavy loads in buildings and other structures. They can withstand harsh weather conditions and have a long lifespan, reducing the need for frequent repairs and replacements. The inherent fire resistance of concrete also adds to its durability, providing an extra layer of safety in the event of a fire. This makes concrete columns a reliable choice for long-term structural integrity.
Fire Resistance
Concrete columns are highly fire-resistant, providing an additional layer of safety in the event of a fire. This makes them a preferred choice for buildings where fire safety is a critical concern, such as high-rise buildings and commercial structures. The fire resistance of concrete columns helps to contain fires and prevent them from spreading, offering valuable time for evacuation and firefighting efforts. This property significantly enhances the overall safety of the building and its occupants.
Versatility
Concrete columns can be molded into various shapes and sizes, allowing for design flexibility in construction projects. They can be customized to meet specific architectural requirements and are suitable for both residential and commercial applications. This versatility makes them a popular choice for a wide range of projects, from simple residential homes to complex commercial buildings. The ability to create custom designs with concrete columns allows architects and builders to achieve unique aesthetic and functional goals.
Disadvantages of Using Concrete Columns
Initial Cost
The upfront cost of constructing concrete columns can be high, especially when using high-quality materials and advanced construction techniques. It’s important to weigh these costs against the long-term benefits and durability of concrete columns. Budgeting carefully and obtaining multiple quotes can help manage these expenses and avoid unexpected financial strain. Considering the long-term benefits, including durability and low maintenance, can help justify the initial investment.
Labor-Intensive Construction
Constructing concrete columns is a labor-intensive process that requires skilled workers and specialized equipment. This can increase the overall cost and time required for construction. Proper planning and budgeting are essential to manage these factors effectively. Ensuring that the construction team has the necessary expertise and equipment can help maintain the quality and efficiency of the project. Labor-intensive processes may also require additional safety measures and compliance with local building regulations, adding to the complexity and cost.
Get 5 New Projects in the Next 7 Days With Our System
Conclusion
Concrete columns are essential structural elements that provide strength and stability to buildings and other structures. By understanding the various costs involved, including materials, labor, formwork, and additional expenses, you can budget effectively and ensure a successful construction project. Whether you’re planning a small residential build or a large commercial structure, careful planning and consideration of regional cost differences will help you achieve the best results for your investment. Engaging with experienced contractors and considering regional cost variations will help you achieve the best results for your project.
Frequently Asked Question
The construction timeline for a concrete column can vary depending on the size and complexity of the project. On average, it takes 1-2 days to complete a small column, while larger columns can take up to a week or more. The timeline can be influenced by factors such as weather conditions, availability of materials, and the efficiency of the construction team.
High-strength concrete is typically used for columns to ensure they can bear the required loads. The specific type of concrete may vary based on the project’s requirements and local building codes. Using the appropriate type of concrete ensures the structural integrity and longevity of the columns.
While it’s possible to build a concrete column yourself, it’s a complex process that requires specialized skills and equipment. Hiring professional contractors ensures the job is done correctly and safely. DIY construction may lead to errors and safety risks, making professional expertise crucial.
A well-constructed concrete column can last for several decades, often exceeding 50 years with proper maintenance. The lifespan depends on factors such as the quality of materials used, construction techniques, and environmental conditions. Regular inspections and maintenance can help extend the lifespan of concrete columns.
Comprehensive Trade-Specific Estimates
At Estimate Florida Consulting, we offer detailed cost estimates across all major trades, ensuring no part of your project is overlooked. From the foundation to the finishing touches, our trade-specific estimates provide you with a complete and accurate breakdown of costs for any type of construction project.
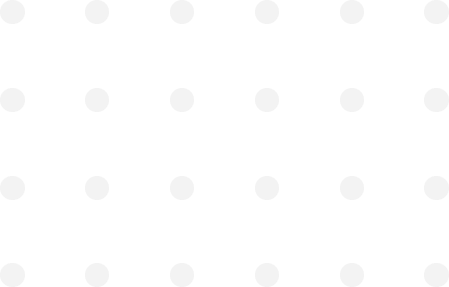
Testimonials
What Our Clients Say
We take pride in delivering accurate, timely, and reliable estimates that help contractors and builders win more projects. Our clients consistently praise our attention to detail, fast turnaround times, and the positive impact our estimates have on their businesses.
Estimate Florida Consulting has helped us win more bids with their fast and accurate estimates. We trust them for every project!
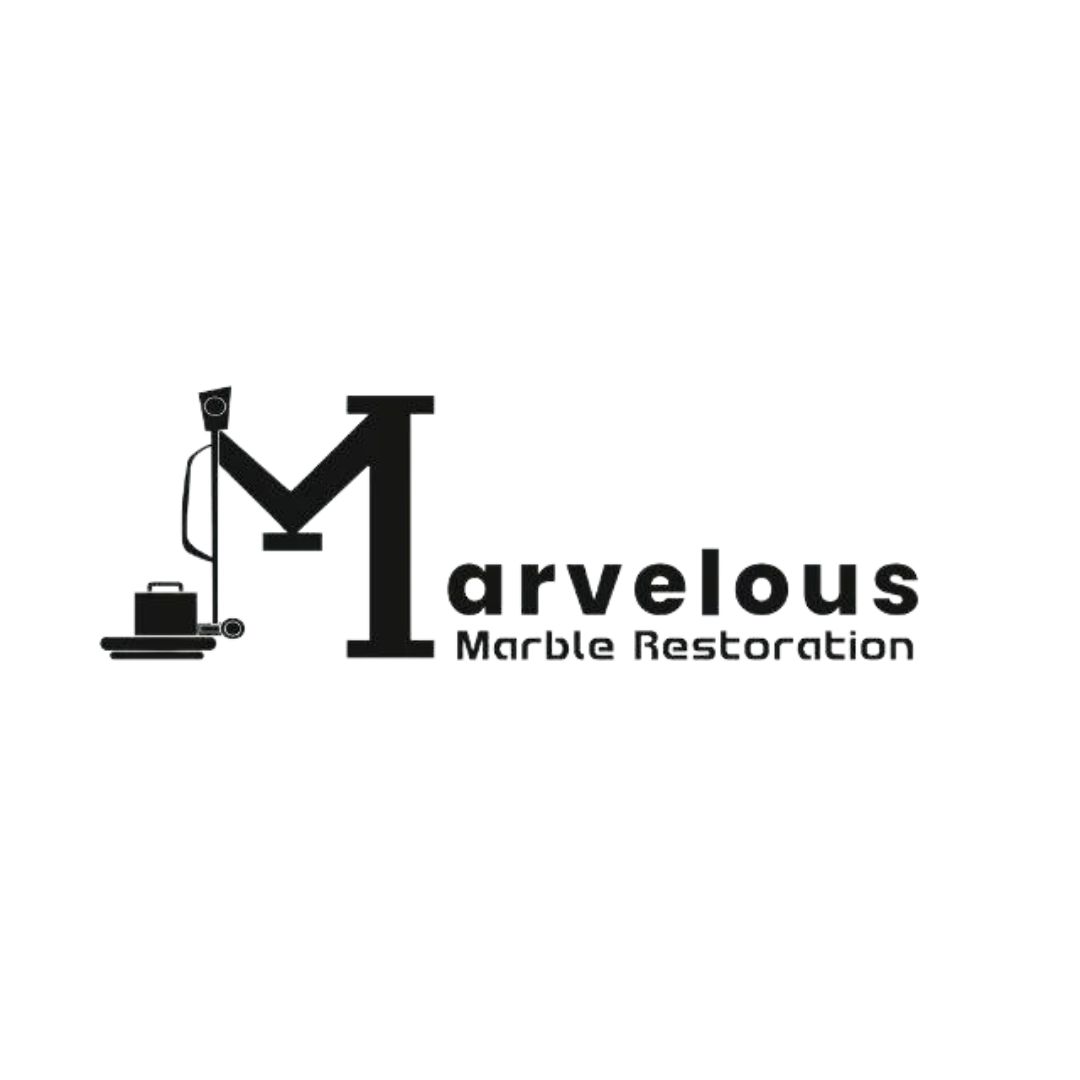
Steps to Follow
Our Simple Process to Get Your Estimate
01
Upload Plans
Submit your project plans, blueprints, or relevant documents through our online form or via email.
02
Receive Quotation
We’ll review your project details and send you a quote based on your scope and requirements.
03
Confirmation
Confirm the details and finalize any adjustments to ensure the estimate meets your project needs.
04
Get Estimate
Receive your detailed, trade-specific estimate within 1-2 business days, ready for your project execution.
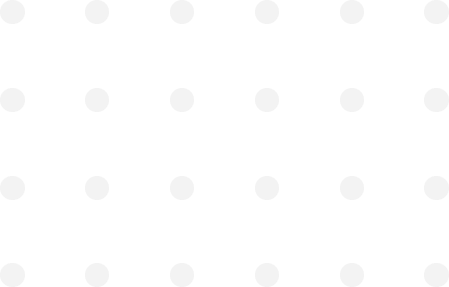