How Much Do Precast Concrete Walls Cost?
The cost of precast concrete walls involves various factors. Precast concrete walls are made in a factory and transported to the construction site for installation, ensuring consistent quality and quicker construction. The cost of precast concrete walls typically ranges from $74.10 to $175.50 per square foot, including materials, manufacturing, transportation, installation, and additional features. Material costs range from $32.50 to $65 per square foot, manufacturing from $13 to $39, transportation from $2.60 to $6.50, and installation from $19.50 to $39. Additional features can add $6.50 to $26 per square foot.
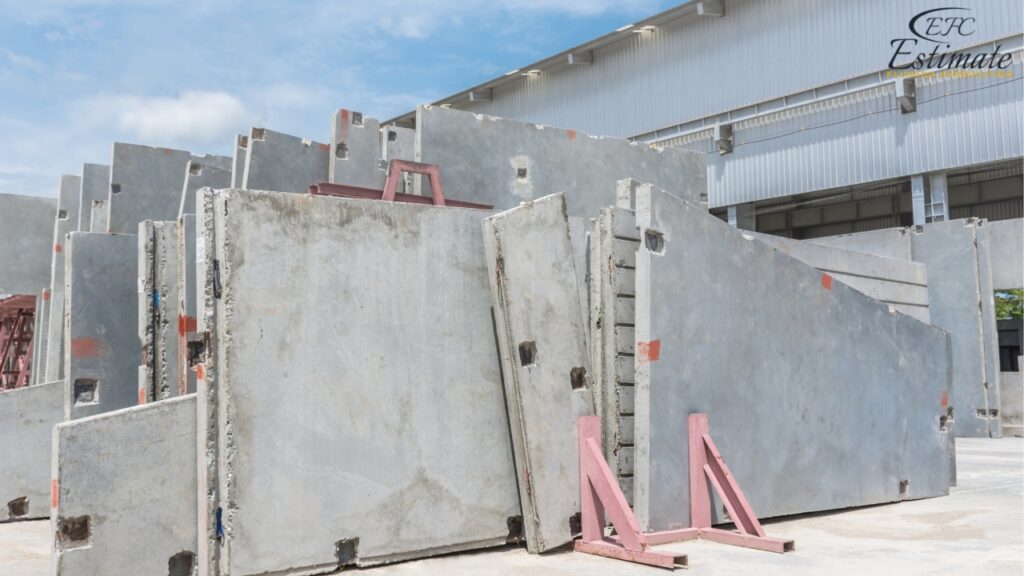
Precast concrete walls offer durability, speed of construction, and versatility, making them a cost-effective choice despite their higher initial cost.
Understanding Precast Concrete Walls
What Are Precast Concrete Walls?
Precast concrete walls are manufactured in a controlled factory environment and then transported to the construction site for installation. This method ensures consistent quality and reduces construction time on-site. Precast walls can be used for a variety of purposes, including exterior walls, interior partitions, and retaining walls. The controlled environment allows for precise casting and curing, leading to superior quality compared to traditional on-site methods. Precast concrete walls are known for their strength and durability, making them a reliable choice for various construction needs.
Types of Precast Concrete Walls
There are several types of precast concrete walls, each serving different purposes and having unique cost implications:
- Solid Precast Walls: These are solid concrete panels that provide excellent strength and sound insulation. They are ideal for load-bearing applications and offer high resistance to weather and environmental factors. Solid precast walls are often used in industrial buildings and high-rise structures due to their robustness.
- Sandwich Panels: These panels consist of two layers of concrete with insulation in between, offering superior thermal performance. They are commonly used in energy-efficient buildings and can help reduce heating and cooling costs. Sandwich panels provide a balance of strength, insulation, and aesthetic appeal, making them suitable for both residential and commercial projects.
- Hollow-core Panels: These panels have hollow spaces to reduce weight and cost while maintaining structural integrity. They are often used in flooring and roofing applications. Hollow-core panels are advantageous in multi-story buildings where reducing the load on the foundation is crucial.
- Retaining Walls: These are used to hold back soil and can be decorative or functional. Retaining walls are essential for landscaping and managing elevation changes on a property. They can be designed to blend seamlessly with the surrounding environment while providing necessary support.
Detailed Cost Breakdown
Here’s a general cost breakdown for a standard precast concrete wall project:
Cost Component | Cost per Square Foot |
Materials | $32.50 – $65 |
Manufacturing | $13 – $39 |
Transportation | $2.60 – $6.50 |
Installation | $19.50 – $39 |
Additional Features | $6.50 – $26 |
Total | $74.10 – $175.50 |
This table provides a comprehensive view of the various cost components involved in a precast concrete wall project. It helps in understanding how each element contributes to the total cost, enabling better budget planning and management.
Examples of Total Costs
To give you a clearer picture, here are some examples of total costs for different sizes of projects:
- Small Project (1,000 sq ft):
- Low-end: $74,100
- High-end: $175,500
- Medium Project (5,000 sq ft):
- Low-end: $370,500
- High-end: $877,500
- Large Project (10,000 sq ft):
- Low-end: $741,000
- High-end: $1,755,000
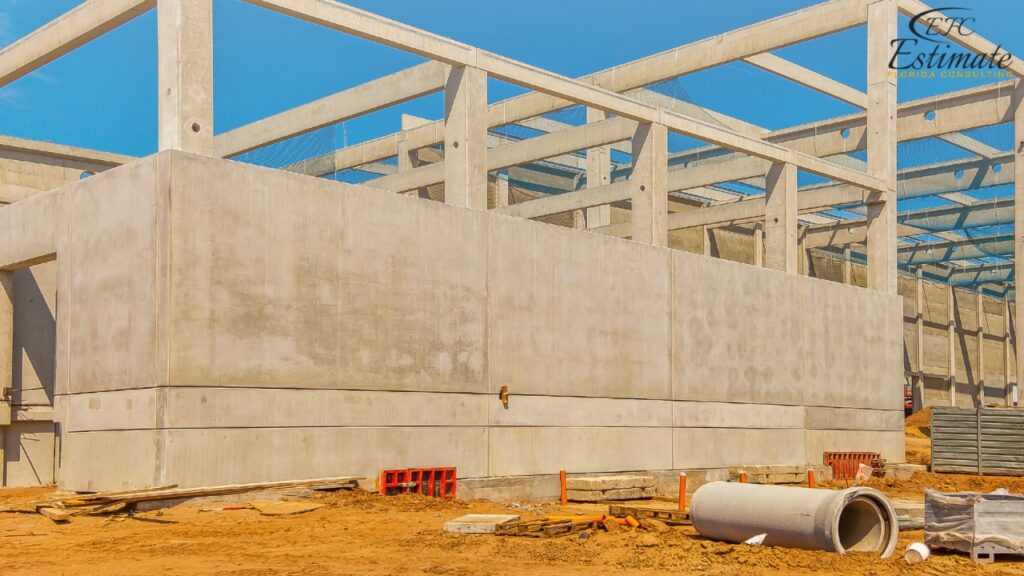
These estimates provide a baseline for budgeting your project. Actual costs may vary depending on specific project requirements and local market conditions. For instance, projects in urban areas might incur higher transportation and labor costs compared to rural areas.
Cost Comparison by Wall Type
The type of precast concrete wall you choose will significantly impact the overall cost. Here’s a comparison of different wall types:
Wall Type | Cost per Square Foot |
Solid Precast Walls | $65 – $130 |
Sandwich Panels | $78 – $156 |
Hollow-core Panels | $52 – $104 |
Retaining Walls | $91 – $182 |
This table highlights the variation in costs based on the specific type of precast wall used. Each type has its own set of benefits and applications, influencing the final price. Solid walls, for example, offer superior strength and sound insulation but are more expensive than hollow-core panels.
Additional Cost Considerations
In addition to the primary cost factors, there are several other considerations that can influence the total cost of precast concrete walls:
Site Preparation
Site preparation involves clearing the area, leveling the ground, and setting up the foundation for the walls. This can add $6.50 to $19.50 per square foot to the overall cost, depending on the site’s condition and the extent of preparation required.
Permits and Inspections
Obtaining necessary permits and scheduling inspections are essential parts of any construction project. Permit fees and inspection costs can vary widely by location but typically range from $650 to $3,900 for a precast concrete wall project.
Design and Engineering
Professional design and engineering services are often needed to ensure that the precast concrete walls meet all structural and safety requirements. These services can add $3.90 to $13 per square foot to the project cost.
Environmental Impact Fees
Some regions impose environmental impact fees or require specific environmental assessments for construction projects. These fees can add $1,300 to $6,500 to the overall cost, depending on local regulations and the project’s scope.
Get 5 New Leads Next 7Days With Our System
- Multi-Family Building
- Hotel Building
- Hospital Building
- Warehouse Building
- High-Rise Building
- Shopping Complex
Factors Influencing the Cost of Precast Concrete Walls
Material Costs
The cost of materials is a significant factor in the overall cost of precast concrete walls. High-quality concrete, reinforcing steel, and insulation (if used) can affect the price. Typically, the material costs for precast concrete walls range from $32.50 to $65 per square foot. The choice of materials and their quality directly impact the durability and performance of the walls. Using premium materials may increase the initial cost but can lead to long-term savings through reduced maintenance and repairs.
Manufacturing Costs
Manufacturing precast concrete walls involves several steps, including mixing the concrete, casting it into molds, curing, and finishing. The complexity and customization of the molds can impact the cost. On average, manufacturing costs range from $13 to $39 per square foot. Advanced manufacturing techniques and quality control measures in the factory setting ensure that each panel meets the required standards. The controlled environment allows for precise measurements and consistent mixing, leading to uniform panels that fit together seamlessly on-site.
Transportation Costs
Transporting precast concrete panels from the factory to the construction site can be expensive, especially for larger projects or sites that are far from the manufacturing facility. Transportation costs typically range from $2.60 to $6.50 per square foot, depending on the distance and logistics involved. Efficient transportation planning can help minimize costs and ensure timely delivery of the panels. Specialized trucks and handling equipment are often required to transport the large and heavy panels safely, adding to the overall cost.
Installation Costs
Installation costs can vary based on the complexity of the project, site conditions, and labor rates in your area. Generally, installation costs for precast concrete walls range from $19.50 to $39 per square foot. This includes preparing the site, erecting the panels, and securing them in place. Proper installation is crucial for the structural integrity and longevity of the walls. Skilled labor is required to ensure that the panels are correctly aligned and securely fastened, preventing issues such as shifting or settling.
Additional Features and Customization
Additional features such as embedded insulation, decorative finishes, or specialized structural elements can increase the overall cost. Customization can add anywhere from $6.50 to $26 per square foot, depending on the specifications. These features enhance the functionality and aesthetic appeal of the walls but also require additional time and resources to implement. Custom finishes and design elements can make the structure stand out and meet specific architectural requirements, but they need careful planning and execution.
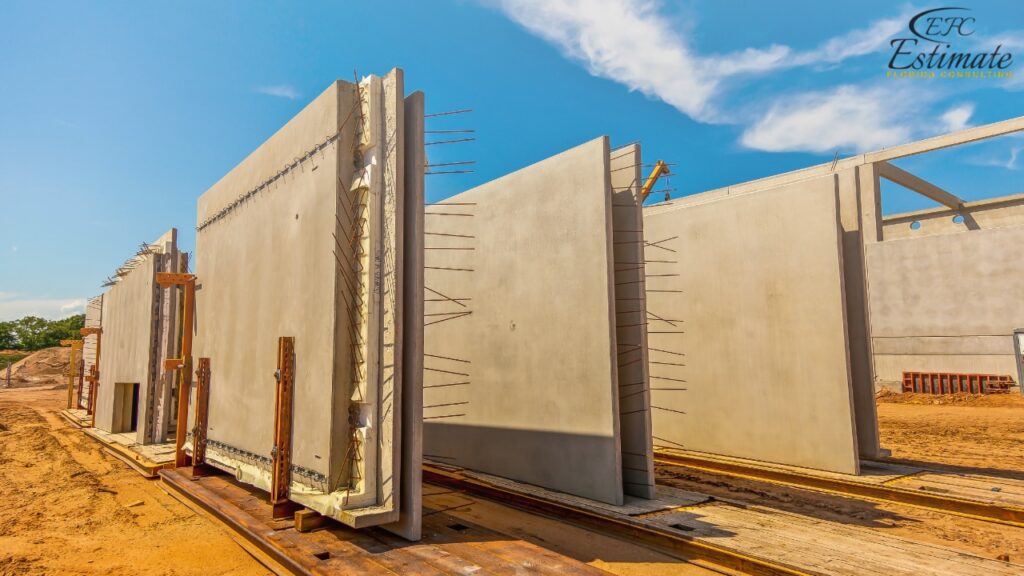
Advantages of Precast Concrete Walls
Durability
Precast concrete walls are highly durable and can withstand extreme weather conditions, fire, and pests. This durability translates to lower maintenance costs over the life of the building. The robust construction ensures that the walls remain intact and functional for decades. Unlike traditional building materials, precast concrete does not warp, rot, or decay, making it an excellent long-term investment.
Speed of Construction
Since precast concrete panels are manufactured off-site, they can be installed quickly once delivered to the construction site. This reduces overall construction time and can lead to significant cost savings. The accelerated construction timeline also minimizes disruptions to the surrounding area. Projects that utilize precast concrete can often be completed in a fraction of the time required for traditional construction methods, allowing for faster occupancy and revenue generation.
Quality Control
Manufacturing in a controlled environment ensures consistent quality and reduces the risk of defects. This quality control results in a superior finished product compared to traditional on-site concrete pouring. The factory setting allows for precise measurements and consistent mixing, leading to uniform panels that meet stringent quality standards. Regular inspections and testing during the manufacturing process further ensure that each panel is free from defects and ready for installation.
Versatility
Precast concrete walls can be customized to meet a wide range of design and structural requirements. They can be made in various shapes, sizes, and finishes to suit different architectural styles. This versatility makes them suitable for a variety of applications, from residential buildings to commercial complexes. Precast walls can also be designed to incorporate windows, doors, and other openings, providing flexibility in building design. The ability to create complex shapes and detailed finishes allows architects to achieve unique and aesthetically pleasing designs.
Disadvantages of Precast Concrete Walls
Initial Cost
The initial cost of precast concrete walls can be higher compared to some traditional building materials. However, the long-term savings in maintenance and energy efficiency often offset this initial expense. Investing in high-quality materials and construction techniques pays off over time through reduced repair and energy costs. It’s important to consider the total cost of ownership rather than just the initial investment when evaluating the cost-effectiveness of precast concrete walls.
Transportation and Handling
Transporting and handling large precast panels can be challenging and requires specialized equipment. This can add to the overall cost, particularly for projects located far from the manufacturing facility. Careful planning and coordination are essential to ensure that the panels are delivered and installed without damage. Additionally, the size and weight of the panels may necessitate the use of cranes and other heavy machinery, which can further increase costs.
Limited Modifications
Once manufactured, precast concrete panels are difficult to modify. Any changes to the design or dimensions need to be addressed during the planning and manufacturing stages. This limitation necessitates thorough planning and accurate measurements to avoid costly adjustments later. While the customization options are extensive during the design phase, any post-manufacturing changes can be costly and time-consuming, requiring new molds or additional materials.
Download Template For Design Project Breakdown
- Materials list updated to the zip code
- Fast delivery
- Data base of general contractors and sub-contractors
- Local estimators
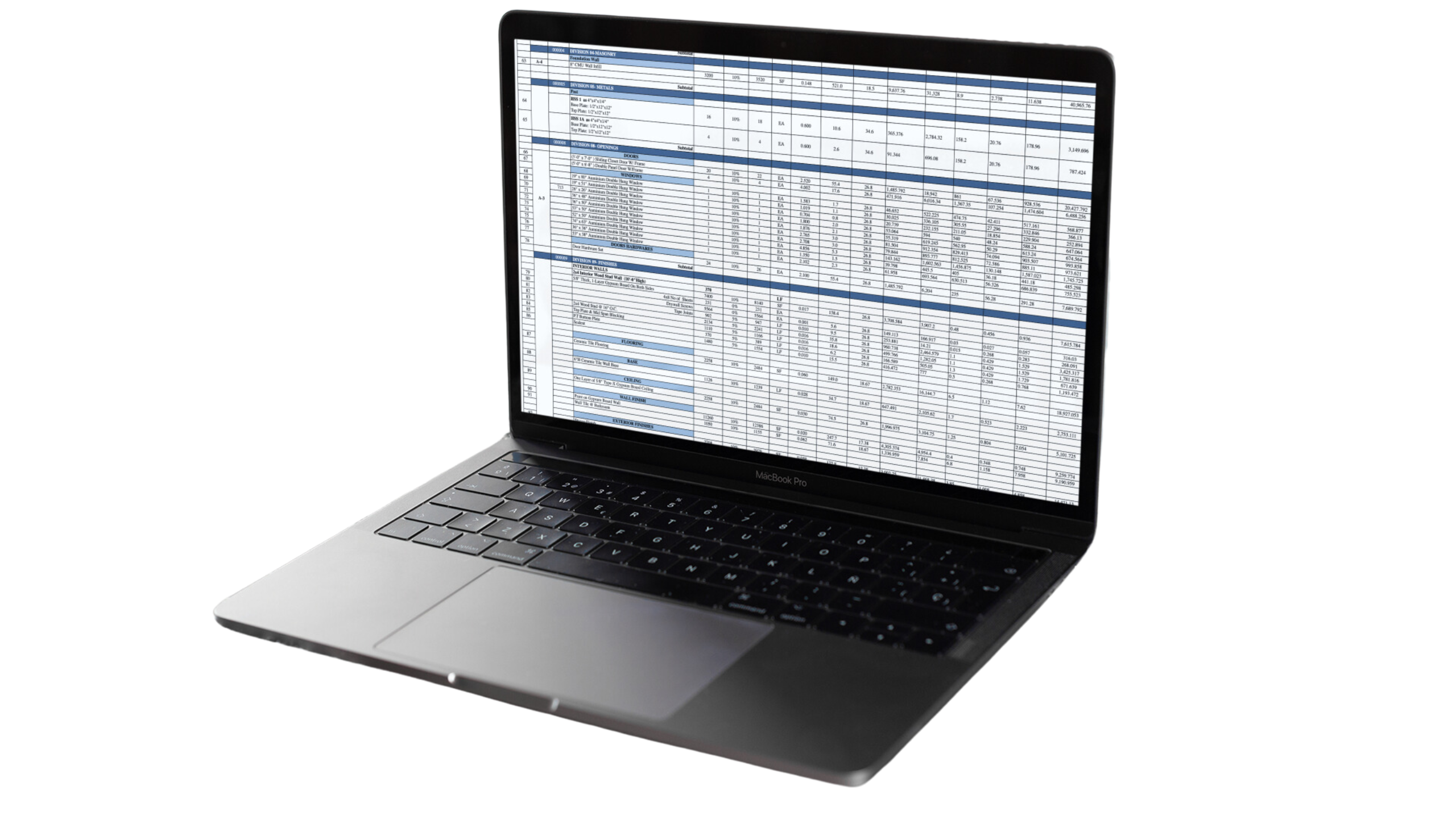
Conclusion
Precast concrete walls offer a durable, efficient, and versatile solution for many construction projects. While the initial costs can be higher, the long-term benefits often make them a cost-effective choice. By understanding the factors that influence the cost and planning accordingly, you can ensure that your project stays within budget while achieving the desired quality and performance. Thorough planning, selecting the right materials, and working with experienced professionals are key to a successful project. The investment in precast concrete walls can result in a structure that stands the test of time, with reduced maintenance and repair costs over its lifespan.
FAQs
Precast concrete walls can last for several decades, often 50 years or more, with minimal maintenance. Their durability makes them an excellent investment for long-term construction projects.
Yes, precast concrete walls are commonly used in residential construction for exterior walls, foundations, and retaining walls. They offer excellent thermal performance and sound insulation, making them ideal for homes.
Precast concrete walls can be environmentally friendly, especially when made with sustainable materials and manufacturing processes. They also offer energy efficiency benefits, contributing to lower heating and cooling costs.
Precast concrete walls are manufactured in a controlled environment, which ensures consistent quality and faster installation compared to traditional poured concrete walls. However, they may have higher initial costs. The controlled manufacturing process reduces the likelihood of defects and ensures a high-quality finish.
Yes, precast concrete walls can be customized in terms of shape, size, and finish to meet specific design and structural requirements. Customization options include decorative textures, colors, and integrated insulation for improved energy efficiency.
Google Reviews
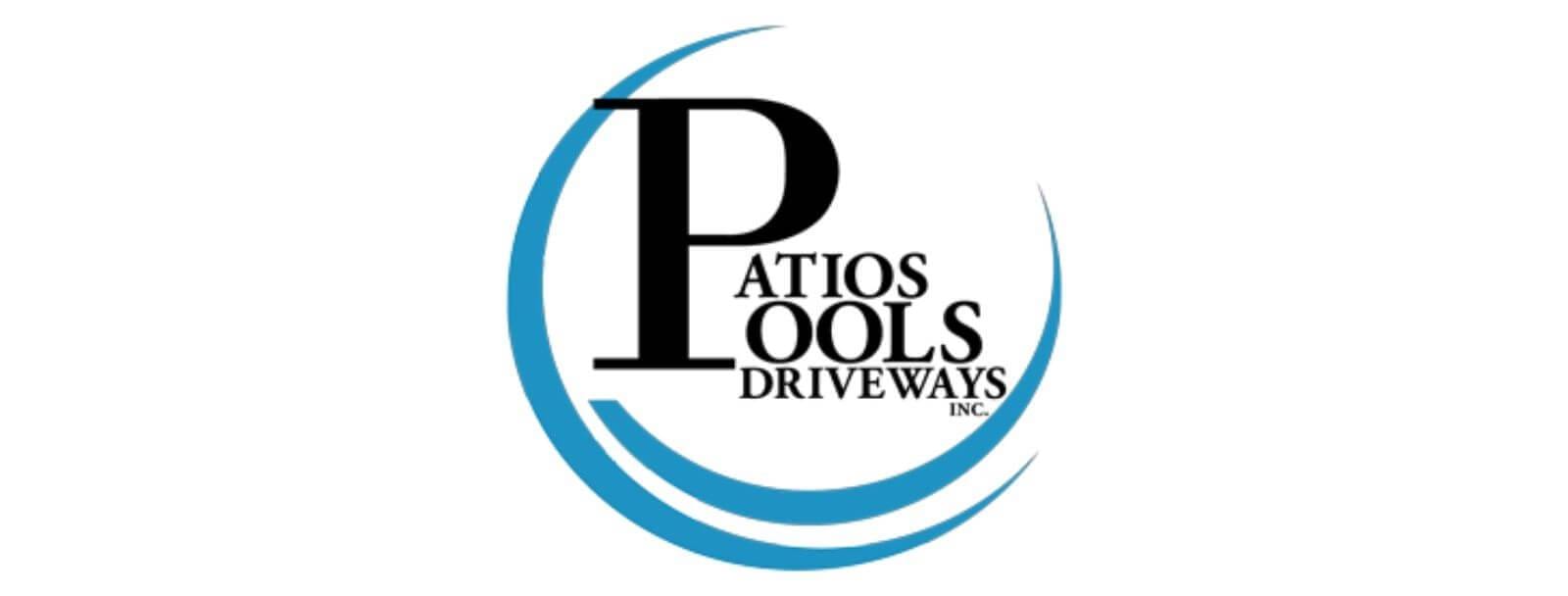
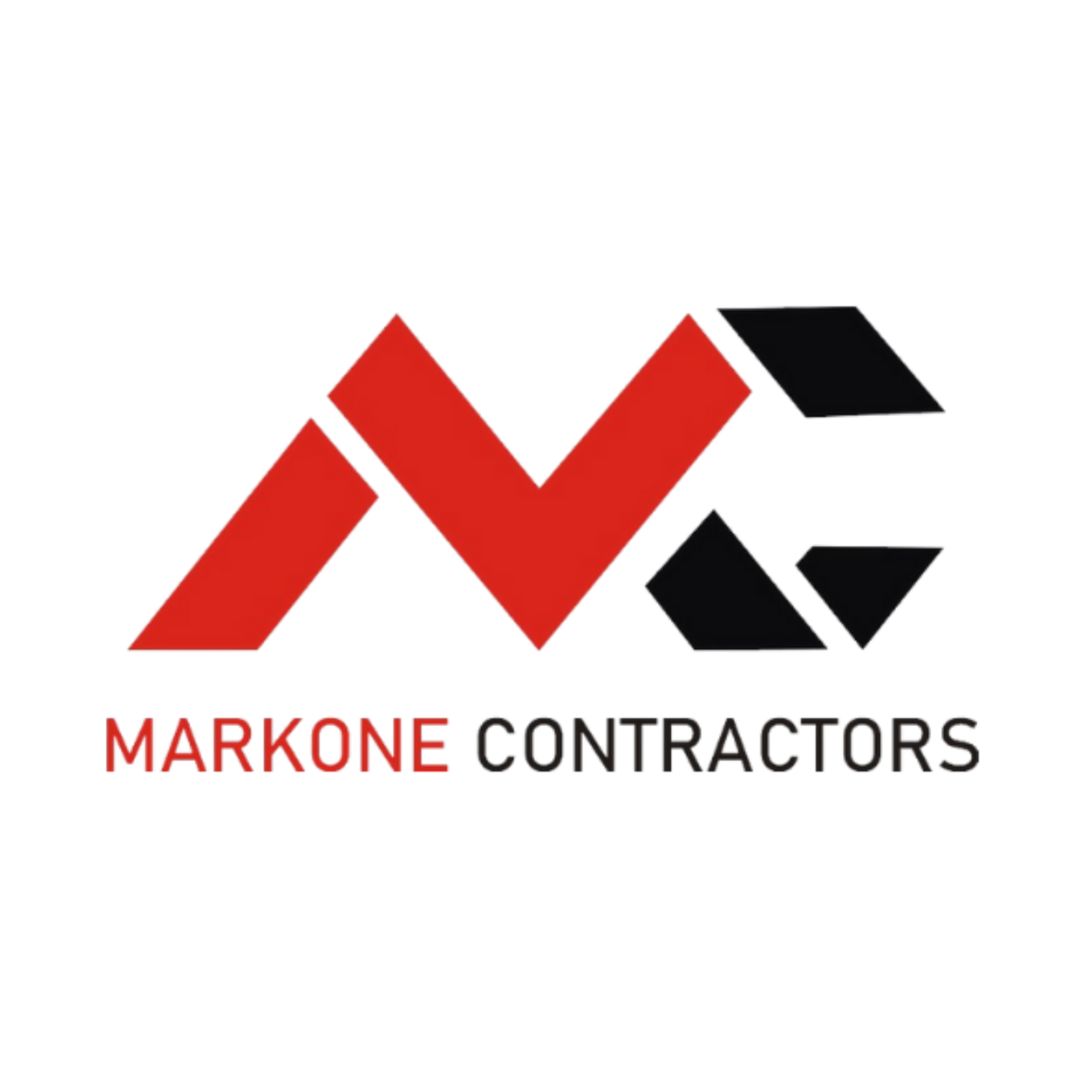

Process To Get Concrete Wall Estimate Report
Here I am going to share some steps to get concrete wall estimate report.
-
You need to send your plan to us.
You can send us your plan on info@estimatorflorida.com
-
You receive a quote for your project.
Before starting your project, we send you a quote for your service. That quote will have detailed information about your project. Here you will get information about the size, difficulty, complexity and bid date when determining pricing.
-
Get Estimate Report
Our team will takeoff and estimate your project. When we deliver you’ll receive a PDF and an Excel file of your estimate. We can also offer construction lead generation services for the jobs you’d like to pursue further.