How Much Do Glass Walls Cost?
Glass walls typically cost between $9,750 and $28,600, translating to $65 to $190 per square foot for a 150 sq ft area. The total cost includes high-quality glass panels, framing, installation labor, and necessary hardware. Lower-end costs cover standard glass and basic designs, while higher-end costs involve premium glass, custom designs, and specialized installation techniques. Factors influencing the cost per square foot include glass type, design complexity, framing materials, and local labor rates. Proper planning and budgeting for unforeseen expenses are essential to ensure the project stays within the estimated cost range.
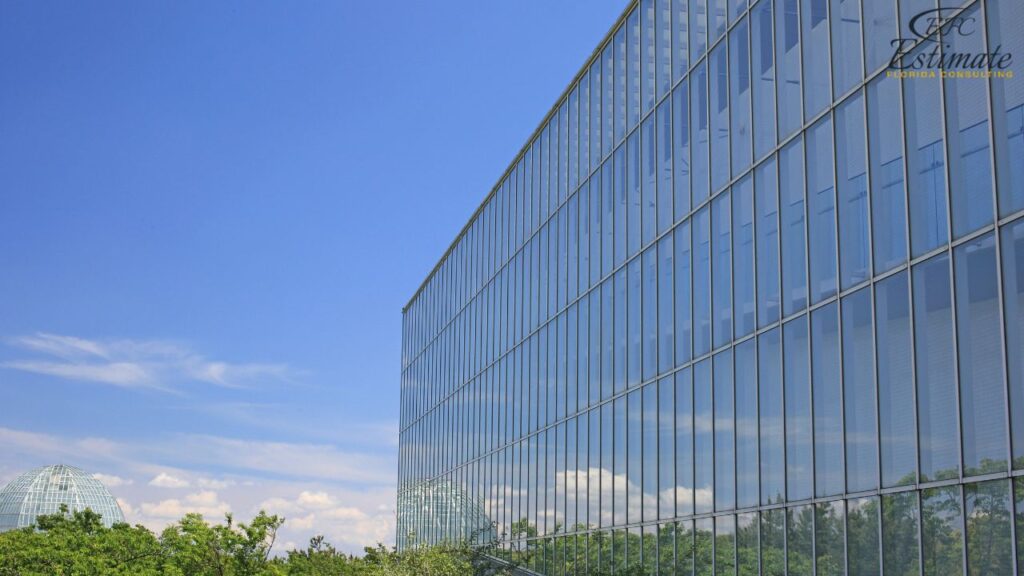
Cost Breakdown for Glass Walls
Materials
The cost of materials for glass walls can vary widely depending on the type and quality of glass used. Here’s a detailed breakdown of typical material costs:
Material | Estimated Cost per Sq Ft (in dollars) | Total Cost for 100 Sq Ft (in dollars) |
Standard Clear Glass | $32.50 – $65 | $3,250 – $6,500 |
Low-E Glass | $39 – $78 | $3,900 – $7,800 |
Tempered Glass | $45.50 – $91 | $4,550 – $9,100 |
Laminated Glass | $52 – $104 | $5,200 – $10,400 |
Insulated Glass Units (IGUs) | $65 – $130 | $6,500 – $13,000 |
Standard Clear Glass
Standard clear glass is the most basic and affordable option. It offers transparency and an unobstructed view but provides minimal insulation and soundproofing. This type of glass is suitable for interior partitions where insulation is not a priority. While it is cost-effective, it may not be ideal for exterior walls due to its lower energy efficiency. The clear view provided by standard glass is perfect for creating a sense of openness and continuity between spaces.
Low-E Glass
Low-emissivity (Low-E) glass has a special coating that reflects infrared light, keeping heat inside during the winter and outside during the summer. This type of glass is more energy-efficient and can help reduce heating and cooling costs. It is ideal for exterior walls and windows, where maintaining a stable indoor temperature is important. The coating also reduces the amount of UV light entering the space, protecting furniture and interiors from fading. The initial investment in Low-E glass can be offset by long-term energy savings.
Tempered Glass
Tempered glass is heat-treated to be stronger and more resistant to breakage than standard glass. When it does break, it shatters into small, blunt pieces rather than sharp shards, making it safer for use in high-traffic areas and places where safety is a concern. It is commonly used for doors, shower enclosures, and other areas where impact resistance is important. The enhanced safety and durability make tempered glass a preferred choice for many applications. The cost is higher than standard glass, but the added benefits justify the expense.
Laminated Glass
Laminated glass consists of two or more layers of glass with an interlayer of polyvinyl butyral (PVB). This type of glass offers enhanced safety, sound insulation, and UV protection. It is commonly used in exterior applications and in areas where sound reduction is important. In the event of breakage, the interlayer holds the glass fragments together, preventing them from scattering. Laminated glass also provides better security against break-ins and vandalism. Its acoustic properties make it suitable for environments where noise reduction is a priority, such as offices and urban residences.
Insulated Glass Units (IGUs)
Insulated glass units consist of two or more panes of glass separated by a spacer and sealed to create an insulating air space. IGUs provide excellent thermal insulation and soundproofing, making them ideal for exterior walls and windows in climates with extreme temperatures. The air space between the panes can be filled with inert gases like argon or krypton to further enhance insulation. IGUs help reduce energy consumption by maintaining indoor temperatures and minimizing heat transfer. They are an excellent choice for homes and buildings aiming for high energy efficiency standards. The upfront cost is higher, but the long-term energy savings and improved comfort make them a worthwhile investment.
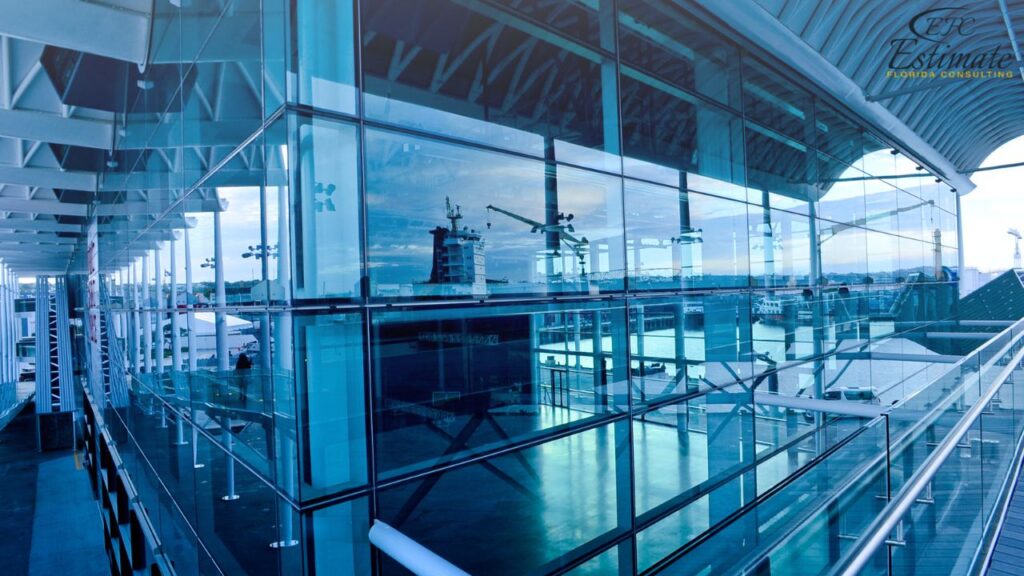
Labor Costs
Labor costs are a significant part of the overall expense of installing glass walls. Here’s an estimate of labor costs:
Labor Task | Estimated Cost per Sq Ft (in dollars) | Total Cost for 100 Sq Ft (in dollars) |
Site Preparation | $6.50 – $13 | $650 – $1,300 |
Installation | $19.50 – $39 | $1,950 – $3,900 |
Finishing and Sealing | $6.50 – $13 | $650 – $1,300 |
Site Preparation
Site preparation involves measuring, cutting openings, and ensuring the site is ready for installation. This step is crucial to ensure a smooth installation process and proper fit for the glass panels. It may also include clearing debris, making structural adjustments, and preparing any necessary support structures. Proper site preparation can prevent issues during installation and ensure the glass walls are securely and accurately placed.
Installation
The installation of glass walls requires skilled labor to handle and fit the glass panels correctly. Proper installation is critical to ensure the safety, stability, and performance of the glass walls. The process may include fitting frames, securing the glass, and ensuring alignment and balance. Specialized equipment and techniques are often required to handle and install large or custom-shaped glass panels. Professional installation ensures that the glass walls meet all safety standards and function as intended.
Finishing and Sealing
Finishing and sealing involve applying caulk or sealant to ensure airtight and watertight connections. This step is essential for both the aesthetic finish and the functional performance of the glass walls, preventing leaks and drafts. Proper sealing also helps maintain the energy efficiency of the building by reducing heat transfer and air infiltration.
The quality of the finishing work can impact the overall appearance and durability of the glass walls.
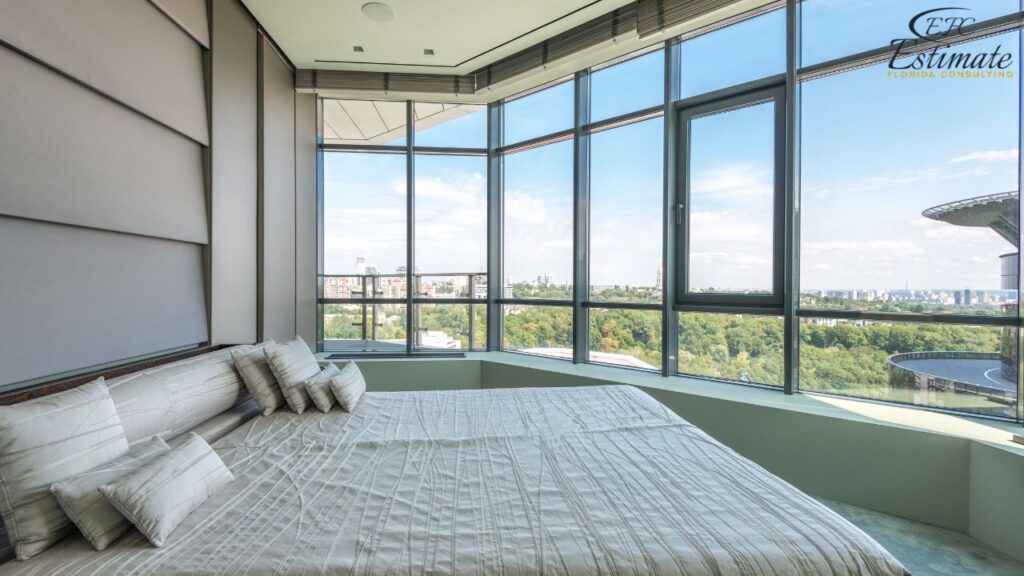
Additional Costs
Additional costs can include permits, inspections, and any custom features or finishes. Here’s an estimate of these costs:
Additional Component | Estimated Cost (in dollars) |
Permits and Inspections | $650 – $1,300 |
Custom Finishes (tints, frosts, patterns) | $650 – $2,600 |
Structural Modifications | $1,300 – $3,900 |
Miscellaneous Expenses | $650 – $1,300 |
Permits and Inspections
Obtaining the necessary permits and passing inspections are crucial steps in the installation process. These ensure that your glass walls comply with local building codes and regulations. Permit fees and inspection costs can vary depending on the location and scope of the project. Ensuring compliance with local regulations can prevent legal issues and ensure the safety and durability of the installation.
Custom Finishes
Custom finishes, such as tinted, frosted, or patterned glass, can add to the aesthetic appeal of the glass walls but also increase the cost. These finishes can provide privacy, reduce glare, or add a decorative element to the design. The additional processing and materials required for custom finishes contribute to the higher price. Custom finishes can also enhance the functionality of the glass walls, such as by providing additional UV protection or reducing solar heat gain.
Structural Modifications
Depending on the existing structure, modifications may be necessary to support the weight and installation of glass walls. This can include reinforcing walls, adding support beams, or modifying the layout. Structural modifications ensure that the building can safely accommodate the new glass walls and maintain their integrity over time. These modifications can also involve additional engineering and design work to ensure the structural integrity and compliance with building codes.
Miscellaneous Expenses
Miscellaneous expenses can include unexpected costs that arise during the project, such as additional materials, equipment rentals, or unforeseen repairs. Having a contingency budget for these expenses helps ensure the project stays on track and can handle any surprises without significant delays or cost overruns. Properly managing these costs can prevent disruptions and ensure the smooth completion of the project.
90% More Chances to Win Projects With Our Estimate!
- Multi-Family Building
- Hotel Building
- Hospital Building
- Warehouse Building
- School & University Building
- High-Rise Building
- Shopping Complex
- Data Center Building
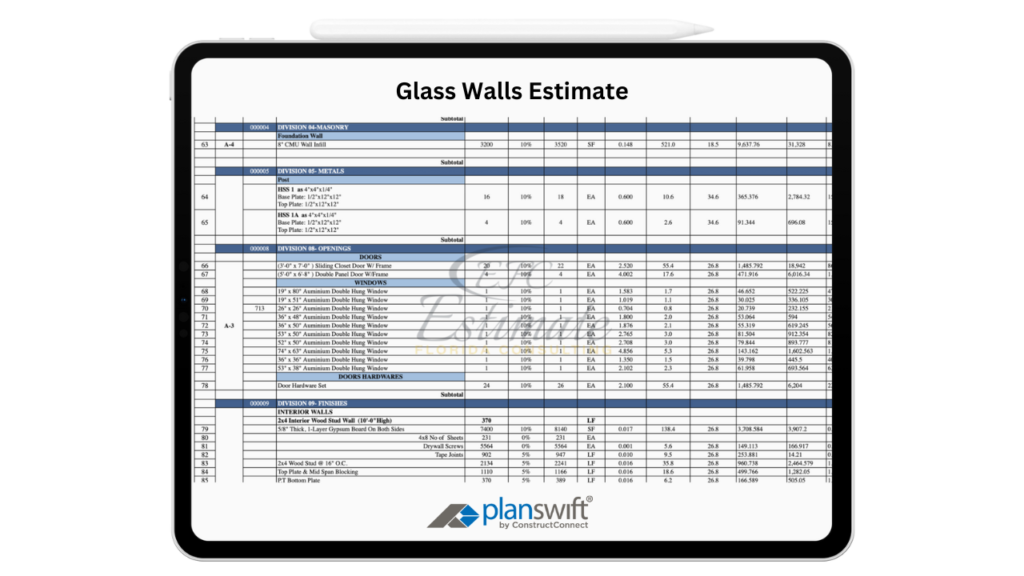
Factors Influencing the Cost of Glass Walls
Type of Glass
The type of glass chosen can significantly impact the cost. Standard clear glass is the most affordable, while specialized glass types, such as Low-E, tempered, or laminated glass, can be more expensive due to their enhanced features and performance. The choice of glass should consider the specific requirements of the project, such as energy efficiency, safety, and aesthetic preferences.
Size and Thickness
Larger and thicker glass panels will cost more due to the increased material required and the additional complexity of handling and installing heavier panels. Custom-sized panels can also add to the cost. The thickness of the glass can impact its strength and insulation properties, influencing both the initial cost and long-term performance. Thicker glass provides better insulation and soundproofing but is more expensive and requires stronger structural support.
Complexity of Installation
The complexity of the installation can affect labor costs. Projects that require structural modifications, custom shapes, or intricate designs will take more time and expertise, leading to higher labor expenses. Complex installations may also require specialized equipment and techniques, adding to the overall cost. The more intricate the design and installation process, the higher the labor costs will be due to the additional time and expertise required.
Customization and Finishes
Adding custom finishes, such as tints, frosts, or patterns, can increase the overall cost but provide added benefits like privacy, reduced glare, and aesthetic appeal. These finishes require additional processing and materials, contributing to the higher price. The level of customization and the quality of the finishes will significantly impact the final cost, as well as the overall look and functionality of the glass walls.
Detailed Cost Comparison
Material Quality
The quality of materials used for glass walls can affect both the initial cost and the long-term performance. Higher-quality glass types, such as laminated or insulated glass, offer better durability, insulation, and safety features but come with a higher price tag.
Material Quality | Estimated Cost per Sq Ft (in dollars) | Total Cost for 100 Sq Ft (in dollars) |
Standard Clear Glass | $32.50 | $3,250 |
Low-E Glass | $39 | $3,900 |
Tempered Glass | $45.50 | $4,550 |
Laminated Glass | $52 | $5,200 |
Insulated Glass Units (IGUs) | $65 | $6,500 |
Labor Complexity
The complexity of the construction job can influence labor costs. More complex installations, such as those involving structural modifications or custom designs, will require more time and expertise.
Labor Complexity | Estimated Cost per Sq Ft (in dollars) | Total Cost for 100 Sq Ft (in dollars) |
Basic | $32.50 | $3,250 |
Intermediate | $45.50 | $4,550 |
Complex | $65 | $6,500 |
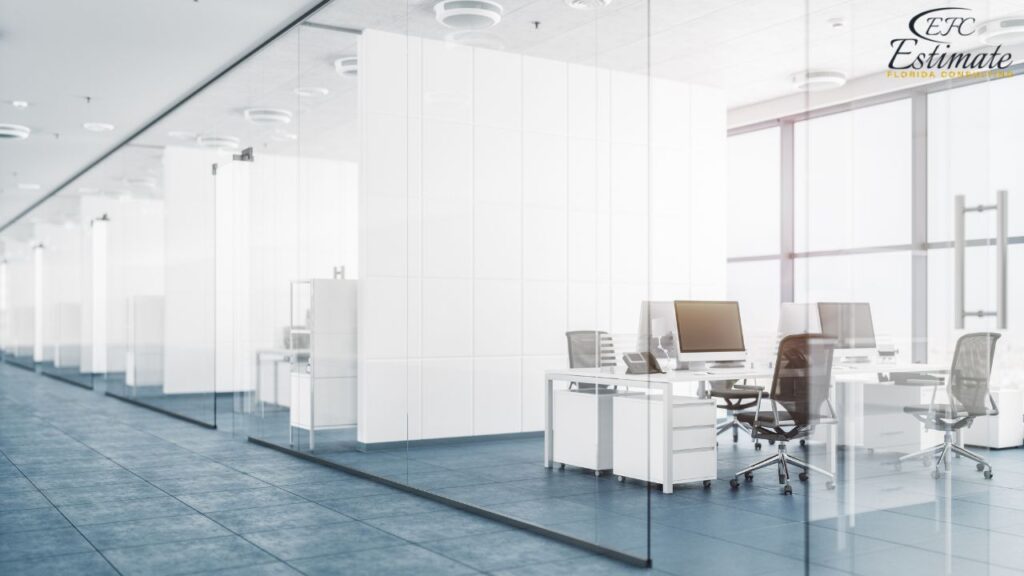
Custom Features
Adding custom features to the glass walls, such as advanced tinting, integrated blinds, or smart glass technology, can increase the overall cost but provide enhanced functionality and convenience.
Feature | Estimated Cost (in dollars) |
Advanced Tinting | $650 – $1,300 |
Integrated Blinds | $1,300 – $2,600 |
Smart Glass Technology | $2,600 – $5,200 |
Benefits of Glass Walls
Aesthetics
Glass walls offer a contemporary, elegant look that can enhance the aesthetic appeal of any space. They create a seamless transition between indoor and outdoor areas and can make interiors feel more spacious and airy. The clean lines and transparent nature of glass walls contribute to a minimalist design aesthetic that is highly sought after in modern architecture. Additionally, glass walls can be customized with various finishes, tints, and textures to match the design vision of any project, adding a unique touch to the overall look. The reflective quality of glass can also amplify natural light, creating a bright and inviting atmosphere.
Natural Light
One of the primary benefits of glass walls is the increased natural light they bring into a space. Natural light can improve mood, increase productivity, and reduce the need for artificial lighting, thereby lowering energy costs. The use of glass walls allows for unobstructed views and maximizes the penetration of daylight, creating a bright and welcoming environment. In commercial settings, the increased natural light can enhance the work environment, contributing to employee satisfaction and well-being. The health benefits of natural light, such as improved sleep patterns and increased vitamin D levels, also make glass walls an attractive option for residential spaces.
Versatility
Glass walls are highly versatile and can be used in a variety of settings, from residential homes to offices and commercial buildings. They can be designed as fixed panels, sliding doors, or partitions, offering flexibility in both function and aesthetics. This versatility allows glass walls to be tailored to meet specific design and functional requirements, whether it’s creating private spaces within an open-plan office or integrating indoor and outdoor living areas. The ability to customize the configuration and style of glass walls ensures they can fit seamlessly into any architectural design. Additionally, glass walls can be combined with other materials, such as wood or metal, to create a unique and cohesive look.
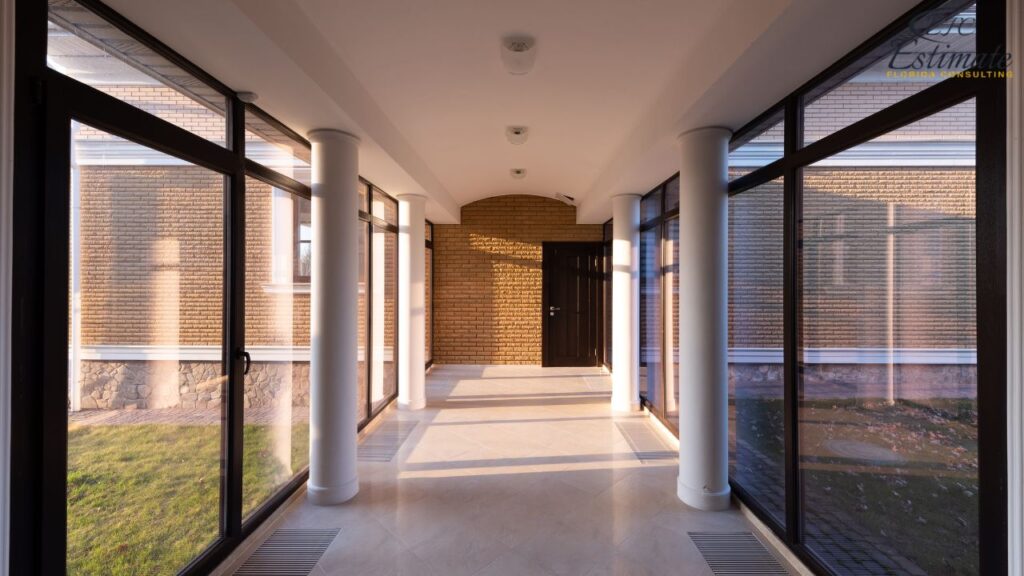
Cost-Saving Tips
Plan Ahead
Planning the construction project early can help identify potential issues and reduce costs. Consider future needs and include features that can accommodate growth and changes in operations. Early planning allows for more efficient project management and resource allocation. Engaging with professionals early in the planning process can ensure all aspects are considered, leading to a more streamlined and cost-effective project. Comprehensive planning can also identify opportunities for cost-saving measures and efficiency improvements. Early engagement with suppliers and contractors can secure better pricing and availability.
Get Multiple Quotes
Obtain multiple quotes from contractors to compare prices and services. This can help you find the best deal and ensure that you’re getting quality work at a competitive price. Additionally, checking references and reviewing past projects can provide insights into the contractor’s reliability and workmanship. Competitive bidding can encourage better pricing and service offerings, enhancing overall project value. Building strong relationships with contractors can also lead to better terms and potential discounts. Negotiating with contractors based on multiple quotes can also result in cost savings.
Use Standard Designs
Opt for standard designs and materials instead of custom or high-end options. Standard designs are often more affordable and readily available, helping to reduce overall costs. Using pre-engineered building designs can also streamline the construction process and reduce costs. Standardized designs can simplify permitting and regulatory compliance, reducing the time and cost associated with approval processes. Additionally, standard designs often benefit from established supply chains and proven construction methods, further enhancing efficiency and cost savings. Choosing standard design options can also speed up the construction timeline.
Download Template For Glass Wall Project Breakdown
- Materials list updated to the zip code
- Fast delivery
- Data base of general contractors and sub-contractors
- Local estimators
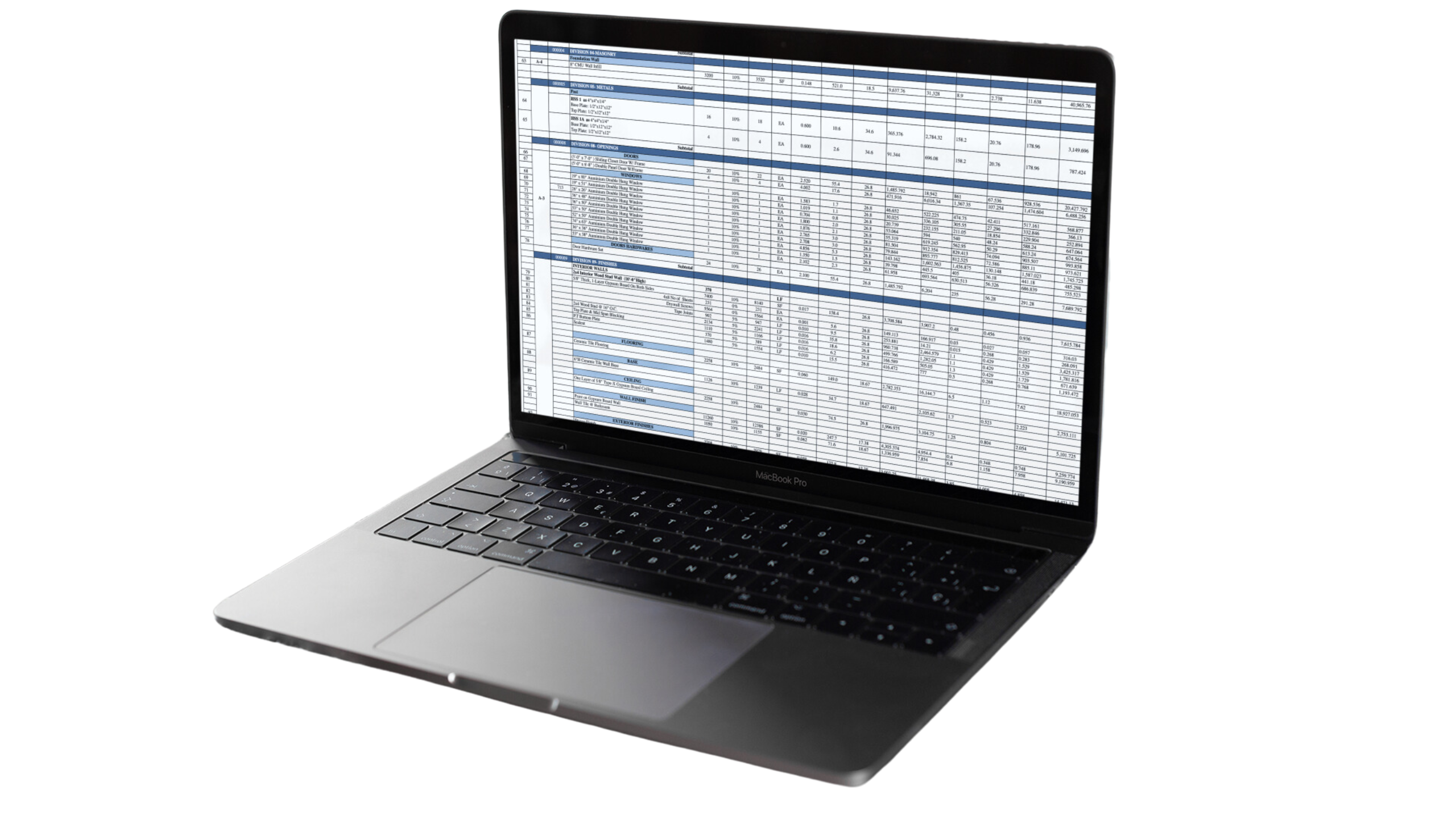
Perform Some Tasks In-House
If you have the expertise and resources, consider performing some tasks in-house, such as site preparation or interior finishing. This can save on labor costs and provide more control over the project. However, it’s important to ensure that all work meets safety and quality standards. Leveraging in-house capabilities can also enhance project flexibility and responsiveness, allowing for efficient management of resources and timelines. Performing tasks in-house can also build internal skills and knowledge, benefiting future projects and maintenance needs. Careful planning and coordination can ensure that in-house tasks are completed efficiently and effectively.
Plan for Contingencies
Include a contingency budget of 10-20% to cover unexpected expenses. This ensures that you are prepared for any unforeseen issues that may arise during the project. Planning for contingencies can provide peace of mind and financial flexibility, allowing you to address any surprises without derailing your budget. A well-planned contingency budget can enhance project resilience and ensure successful completion despite unforeseen challenges. Being prepared for unexpected costs demonstrates thorough planning and risk management, which can instill confidence in stakeholders and financial backers. Contingency planning also allows for quicker response to unexpected issues, minimizing project delays.
Conclusion
Building a modern glass house is a significant investment that requires careful planning and budgeting. By understanding the various costs involved and the factors that influence these costs, you can make informed decisions and ensure the success of your building project. Investing in high-quality materials, working with experienced professionals, and planning for contingencies can ensure a successful and cost-effective construction process. Properly managing the project not only ensures compliance with safety standards but also maximizes the long-term benefits of the investment. Taking a proactive approach to project management and budgeting can lead to a successful outcome, providing a functional, efficient, and valuable asset that supports your specific needs and goals for years to come. By considering all aspects of the construction process and leveraging best practices in project planning and execution, you can achieve a high-quality building that meets your expectations and delivers significant return on investment. Comprehensive planning and execution will help you navigate challenges, optimize resources, and achieve a building that enhances your operational efficiency and meets all regulatory and safety requirements. With the right approach, you can create a glass house that serves your needs and provides long-term value, ensuring that your investment pays off in the years ahead.
FAQs
Glass walls typically cost between $9,750 and $28,600, translating to $65 to $190 per square foot for a 150 sq ft area. The total cost includes high-quality glass panels, framing, installation labor, and necessary hardware.
Several factors influence the cost, including the type of glass, design complexity, framing materials, local labor rates, and any additional custom features or finishes.
- Standard Clear Glass: $32.50 – $65 per sq ft
- Low-E Glass: $39 – $78 per sq ft
- Tempered Glass: $45.50 – $91 per sq ft
- Laminated Glass: $52 – $104 per sq ft
- Insulated Glass Units (IGUs): $65 – $130 per sq ft
- Standard Clear Glass: Offers basic transparency with minimal insulation and soundproofing.
- Low-E Glass: Energy-efficient, reflects infrared light, reduces UV light, and helps lower heating and cooling costs.
- Tempered Glass: Stronger and safer, shatters into blunt pieces, ideal for high-traffic areas.
- Laminated Glass: Enhanced safety, sound insulation, and UV protection; holds fragments together when broken.
- Insulated Glass Units (IGUs): Excellent thermal insulation and soundproofing, ideal for extreme climates.
Labor costs include:
- Site Preparation: $6.50 – $13 per sq ft
- Installation: $19.50 – $39 per sq ft
- Finishing and Sealing: $6.50 – $13 per sq ft
Additional costs can include permits and inspections ($650 – $1,300), custom finishes ($650 – $2,600), structural modifications ($1,300 – $3,900), and miscellaneous expenses ($650 – $1,300).
- Type of Glass: Different types of glass have varying costs.
- Size and Thickness: Larger and thicker glass panels cost more.
- Complexity of Installation: Custom shapes and designs increase labor costs.
- Customization and Finishes: Custom tints, frosts, or patterns add to the cost.
- Plan Ahead: Early planning can identify potential issues and reduce costs.
- Get Multiple Quotes: Comparing quotes from contractors helps find the best deal.
- Use Standard Designs: Opt for standard designs and materials to reduce costs.
- Perform Some Tasks In-House: If feasible, performing some tasks in-house can save on labor costs.
- Plan for Contingencies: Include a contingency budget of 10-20% to cover unexpected expenses.
Proper planning and budgeting are essential to ensure the project stays within the estimated cost range, preventing unforeseen expenses and delays.
Building a modern glass house requires careful planning and budgeting. Understanding the various costs and factors influencing these costs allows for informed decision-making, ensuring a successful and cost-effective construction process. Investing in high-quality materials, experienced professionals, and planning for contingencies can maximize the long-term benefits of the investment.
Google Reviews
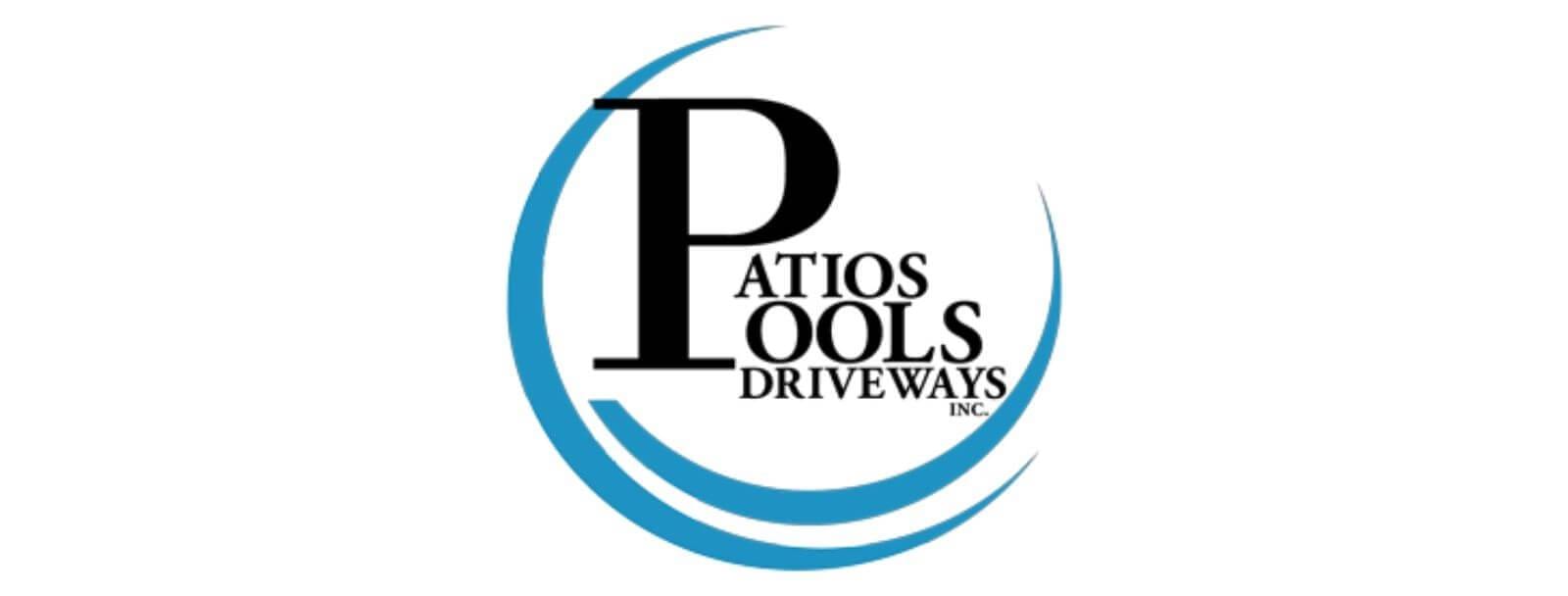
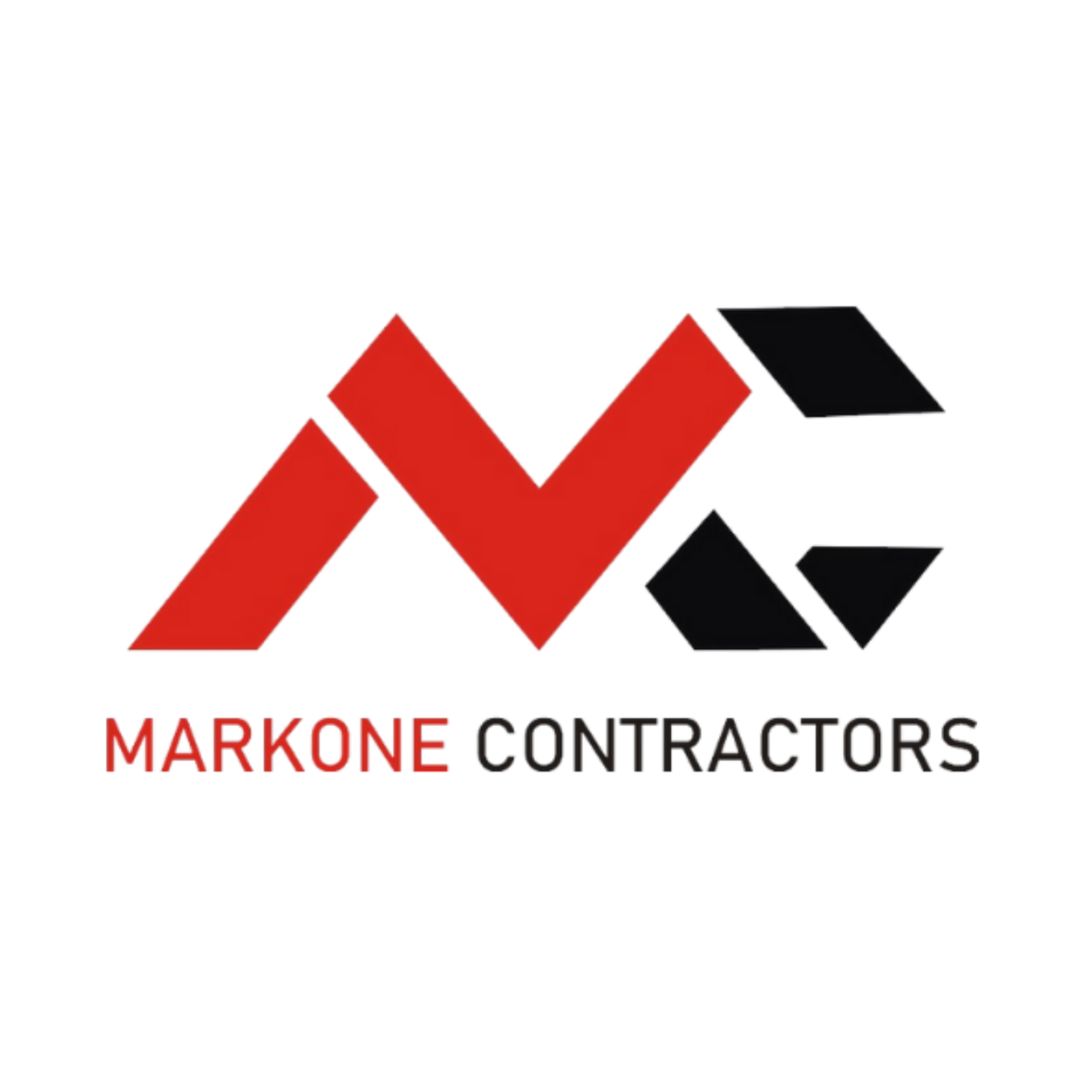

Process To Get Steel Building Cost Estimate Report
Here I am going to share some steps to get steel building cost estimate report.
-
You need to send your plan to us.
You can send us your plan on info@estimatorflorida.com
-
You receive a quote for your project.
Before starting your project, we send you a quote for your service. That quote will have detailed information about your project. Here you will get information about the size, difficulty, complexity and bid date when determining pricing.
-
Get Estimate Report
Our team will takeoff and estimate your project. When we deliver you’ll receive a PDF and an Excel file of your estimate. We can also offer construction lead generation services for the jobs you’d like to pursue further.