How Much Cost to Build a 10,000 Sq Ft Commercial Building?
Building a 10,000 sq ft commercial building typically costs between $1,610,600 and $4,050,000, averaging $160 to $405 per square foot. This comprehensive estimate includes site preparation, construction, interior finishes, plumbing, electrical systems, HVAC, and necessary permits. Costs can vary based on the building’s design complexity, material quality, and local labor rates. Additional expenses may arise from custom features, advanced technology integrations, and compliance with local building codes. Investing in quality construction ensures durability, energy efficiency, and long-term value. Proper planning, obtaining multiple quotes, and careful budgeting are essential for a successful commercial building project.
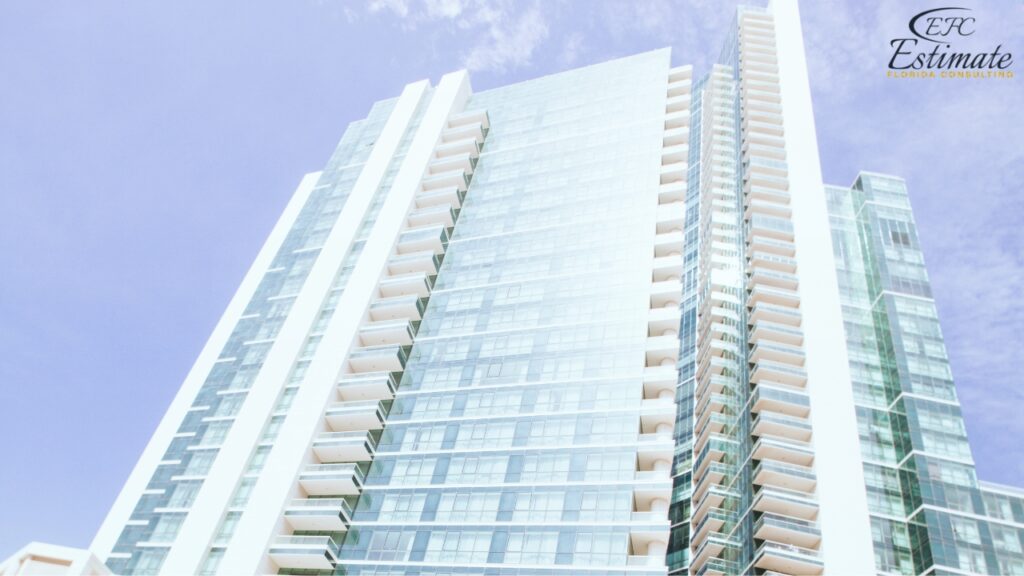
Cost Breakdown for Building a 10,000 Sq Ft Commercial Building
Pre-Construction Costs
Pre-construction costs include expenses related to planning, design, permits, and site preparation. These costs are essential for laying the groundwork for the project and ensuring compliance with local regulations. Proper pre-construction planning can help identify potential challenges and streamline the construction process.
Architectural and Engineering Fees
Architectural and engineering fees typically range from 5% to 15% of the total construction cost. For a 10,000 sq ft building, this can be significant, but these professionals are crucial for designing a functional and compliant structure. They help in creating detailed blueprints and ensuring that the design meets all regulatory requirements. Detailed architectural plans and engineering assessments are essential for obtaining permits and ensuring the building’s safety and functionality. These professionals also play a critical role in coordinating with other stakeholders, such as contractors and inspectors, to ensure the project progresses smoothly.
Permits and Inspections
Permits and inspections are necessary to ensure that the construction complies with local building codes and regulations. These costs can vary based on the location and the complexity of the project. Typically, they range from $6,000 to $24,000, depending on the specific requirements of the area. Obtaining permits and scheduling inspections in advance can help avoid delays and additional costs during construction. Proper documentation and adherence to regulations are crucial for avoiding legal issues and ensuring smooth project progression. Regular inspections throughout the construction phase ensure that any issues are identified and addressed promptly, maintaining the project’s compliance with safety and quality standards.
Site Preparation
Site preparation includes clearing the land, grading, and ensuring proper drainage. Depending on the site’s condition, this can range from $12,000 to $60,000. Proper site preparation is essential to prevent future issues such as flooding or foundation problems. It also includes any necessary demolition of existing structures, if applicable. Ensuring the site is ready for construction can help avoid delays and additional costs once the building phase begins. Proper site preparation also involves addressing any environmental concerns, such as soil contamination, which may require remediation before construction can proceed.
Pre-Construction Cost Component | Estimated Cost |
Architectural and Engineering | $60,000 – $180,000 |
Permits and Inspections | $6,000 – $24,000 |
Site Preparation | $12,000 – $60,000 |
Construction Costs
Construction costs encompass the main expenses related to building the structure, including materials, labor, and equipment. These are the core costs of the project and will constitute the majority of the budget. Properly managing construction costs is crucial for keeping the project on track and within budget.
Foundation
The foundation is a critical component of any building. For a commercial building, the foundation cost can range from $12 to $30 per square foot. For a 10,000 sq ft building, this would be approximately $120,000 to $300,000. The foundation must be strong enough to support the structure and any additional loads it may carry. A well-built foundation ensures the stability and longevity of the building. The type of soil and ground conditions at the site can also affect foundation costs, as some soils may require more extensive preparation and reinforcement.
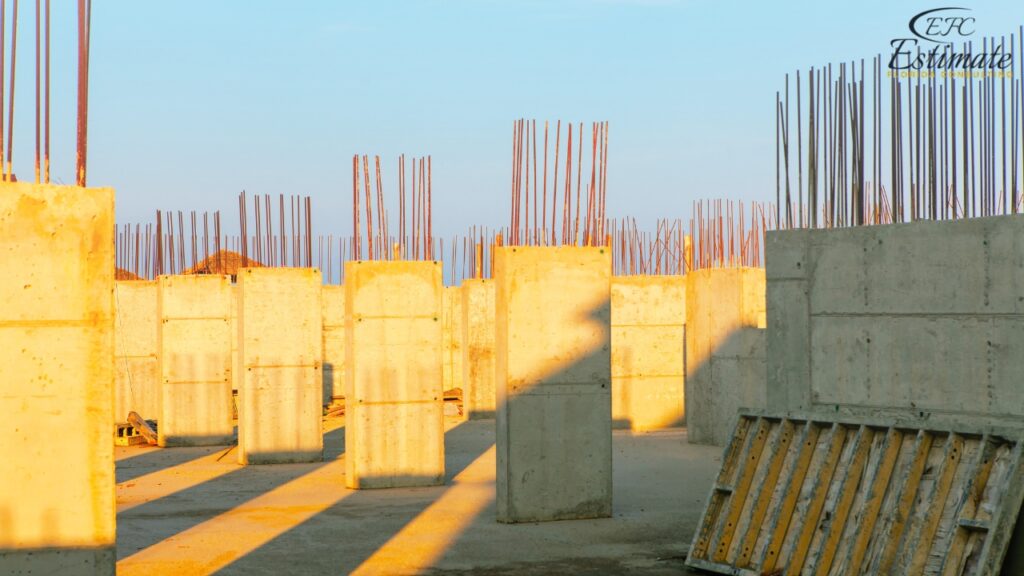
Structural Frame
The cost of the structural frame varies depending on the materials used. Steel frames are common for commercial buildings, and the cost can range from $18 to $36 per square foot, amounting to $180,000 to $360,000. The structural frame provides the skeleton of the building and must be designed to handle the stresses it will face. The choice of material for the structural frame affects both the construction timeline and the building’s overall strength. Steel frames offer durability and flexibility in design but may require specialized labor and equipment for installation.
Exterior Finishes
Exterior finishes, including walls, windows, and doors, can cost between $24 to $42 per square foot, totaling $240,000 to $420,000. These finishes contribute to the building’s aesthetic appeal and energy efficiency. High-quality finishes can also improve the building’s durability and reduce maintenance costs. The exterior appearance of the building can influence its marketability and appeal to potential tenants or customers. Selecting energy-efficient windows and insulated walls can help reduce long-term energy costs and improve the building’s environmental performance.
Roofing
Roofing costs can range from $12 to $24 per square foot, amounting to $120,000 to $240,000. The type of roofing material and the complexity of the roof design can significantly influence the cost. A well-constructed roof is essential for protecting the building from weather and environmental elements. Investing in a high-quality roofing system can reduce long-term maintenance costs and improve energy efficiency. Roof designs may also need to accommodate additional features such as solar panels or HVAC systems, which can impact overall costs.
Interior Finishes
Interior finishes, including flooring, ceilings, and walls, can cost between $24 to $48 per square foot, totaling $240,000 to $480,000. The choice of materials and the level of finish can vary based on the intended use of the building. High-quality interior finishes can enhance the functionality and appearance of the space. Customizing the interior design to meet specific business needs can improve the building’s usability and attractiveness. High-quality interior finishes can also contribute to a more comfortable and productive environment for occupants.
Mechanical, Electrical, and Plumbing (MEP)
MEP systems are vital for the operation of the building. These costs can range from $36 to $72 per square foot, amounting to $360,000 to $720,000. This includes HVAC systems, electrical wiring, and plumbing installations. Efficient MEP systems are crucial for ensuring the building’s comfort and functionality. Investing in modern, energy-efficient MEP systems can result in significant operational savings over time. Properly designed and installed MEP systems also ensure the safety and reliability of the building’s infrastructure.
Construction Cost Component | Estimated Cost per Sq Ft | Total Cost for 10,000 Sq Ft |
Foundation | $12 – $30 | $120,000 – $300,000 |
Structural Frame | $18 – $36 | $180,000 – $360,000 |
Exterior Finishes | $24 – $42 | $240,000 – $420,000 |
Roofing | $12 – $24 | $120,000 – $240,000 |
Interior Finishes | $24 – $48 | $240,000 – $480,000 |
Mechanical, Electrical, Plumbing (MEP) | $36 – $72 | $360,000 – $720,000 |
Post-Construction Costs
Post-construction costs include expenses related to finishing touches, landscaping, and final inspections. These costs are necessary to complete the project and ensure it meets all operational and aesthetic requirements. Proper post-construction planning can enhance the building’s functionality and curb appeal.
90% More Chances to Win Projects With Our Estimate!
- Multi-Family Building
- Hotel Building
- Hospital Building
- Warehouse Building
- School & University Building
- High-Rise Building
- Shopping Complex
- Data Center Building

Landscaping
Landscaping around the building can range from $6,000 to $36,000, depending on the extent and quality of the landscaping desired. Proper landscaping enhances the building’s exterior appeal and can provide environmental benefits such as improved air quality and reduced stormwater runoff. Well-designed landscaping can also create a welcoming environment for visitors and employees. Incorporating native plants and sustainable landscaping practices can reduce maintenance costs and support local ecosystems.
Final Inspections and Approvals
Final inspections and obtaining occupancy permits are necessary to ensure that the building meets all local codes and regulations. These costs can range from $3,600 to $12,000. Completing these steps is crucial for legally occupying and operating the building. Ensuring that all inspections and approvals are completed on time can prevent delays in the building’s opening. Proper documentation and compliance with local regulations are essential for avoiding legal issues and ensuring the building’s safety.
Furnishings and Equipment
Furnishings and equipment can vary widely based on the building’s intended use. For a typical commercial building, this can range from $60,000 to $240,000. This includes office furniture, fixtures, and any specialized equipment needed for business operations. High-quality furnishings and equipment can improve the functionality and comfort of the building. Selecting durable and ergonomic furnishings can enhance the productivity and well-being of occupants.
Post-Construction Cost Component | Estimated Cost |
Landscaping | $6,000 – $36,000 |
Final Inspections and Approvals | $3,600 – $12,000 |
Furnishings and Equipment | $60,000 – $240,000 |
Additional Costs
Additional costs may include unexpected expenses and contingency funds. It’s important to budget for these to avoid any financial surprises.
Contingency Fund
A contingency fund of about 10-20% of the total project cost is recommended to cover unexpected expenses. For a project of this scale, this could range from $140,000 to $600,000. This fund helps manage unforeseen costs such as design changes, delays, and additional materials. Having a contingency fund ensures that the project can continue smoothly even if unexpected issues arise.
Project Management
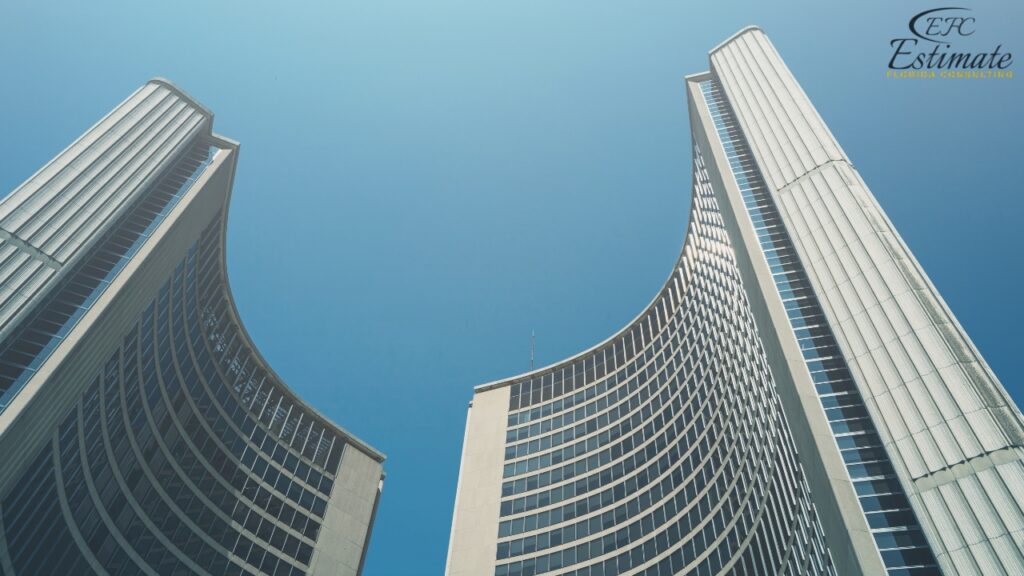
Hiring a project manager or construction management team can cost between 5% to 15% of the total construction cost. This ensures that the project stays on schedule and within budget. A skilled project manager can coordinate all aspects of the construction, ensuring efficient use of resources and timely completion. Effective project management can also help minimize risks and improve communication among stakeholders.
Additional Cost Component | Estimated Cost |
Contingency Fund | $140,000 – $600,000 |
Project Management | $63,000 – $378,000 |
Key Factors Influencing Construction Costs
Location
The location of the building site is a major factor that influences construction costs. Urban areas typically have higher costs due to the price of land, labor, and materials. Conversely, rural areas might offer lower costs but could face challenges such as limited access to skilled labor and materials. The location also affects the cost of permits, inspections, and adherence to local building codes. Additionally, the proximity to transportation and infrastructure can impact logistical costs, influencing the overall budget. Urban locations might also offer advantages such as higher foot traffic and better access to utilities, which can be crucial for certain types of commercial buildings. Proximity to suppliers and ease of access for construction vehicles can also impact costs.
Building Design
The design and complexity of the building significantly affect the overall cost. Modern, high-tech designs with unique architectural features tend to be more expensive due to the need for specialized materials and construction techniques. Simpler designs with standard materials are usually more cost-effective. The number of floors, layout, and structural elements also play a crucial role in determining the cost. Custom designs often require more detailed planning and can result in higher architectural and engineering fees. Incorporating sustainable or energy-efficient features can also increase upfront costs but may provide long-term savings through reduced operational expenses. Detailed design plans and thorough project management can help mitigate unexpected costs during the construction phase.
Materials Used
The choice of materials can greatly impact the cost. High-quality materials like steel, glass, and premium finishes will increase expenses, while more economical materials can help keep costs down. However, it is important to balance cost with durability and maintenance needs to ensure long-term value. Sustainable and energy-efficient materials may have higher upfront costs but can lead to savings in operational expenses over time. Additionally, fluctuations in material prices can affect the overall budget, so it’s crucial to plan for potential price changes. Choosing the right materials can also affect the building’s aesthetic appeal and functionality.
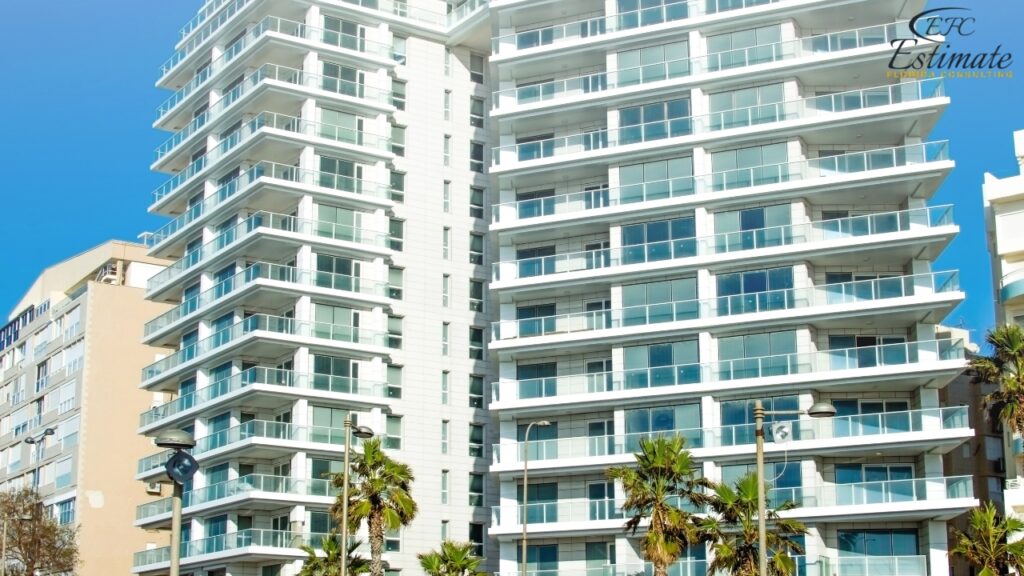
Investing in high-quality materials can improve the building’s longevity and reduce long-term maintenance costs.
Construction Type
The type of construction, whether it’s a steel frame, concrete, or wood frame, will also influence costs. Steel frames are commonly used for commercial buildings due to their strength and durability, but they can be more expensive than wood or concrete. The construction type impacts not only the material costs but also the labor and time required for the project. Each type has its own advantages and challenges, which must be considered when planning the construction. The choice of construction type can also influence the building’s structural integrity and resistance to natural disasters. Steel frames, for example, are highly durable and resistant to fire and pests but may require more skilled labor for installation.
Financing and Budgeting
Securing Financing
Securing financing for a commercial building project often involves obtaining a construction loan, which can cover a significant portion of the construction costs. Understanding the terms and conditions of the loan, including interest rates and repayment schedules, is crucial for effective financial planning. Business owners and developers may also explore other financing options such as commercial mortgages, investor funding, or government grants. Proper financial planning ensures that there are sufficient funds to cover all costs and avoid project delays due to cash flow issues. Additionally, having a solid financing plan can make the project more attractive to potential investors and partners.
Creating a Budget
Creating a detailed budget that includes all potential costs can help manage expenses effectively. This involves listing all material, labor, and additional costs, and allocating funds accordingly. Regularly reviewing and adjusting the budget can ensure that the project stays within financial limits. A well-planned budget can also help identify potential savings opportunities and prevent overspending. Documenting all expenses and comparing them against the budget can provide insights into where costs may be reduced. Additionally, keeping track of all receipts and invoices can help with future financial planning and tax deductions. Using budgeting software or hiring a financial consultant can improve accuracy and accountability.
Cost-Saving Tips
Choosing the Right Material
Opting for cost-effective piping materials like PEX or CPVC can significantly reduce the overall cost of the project. These materials are durable, easier to install, and more affordable compared to traditional copper pipes. By choosing the right materials, homeowners can achieve a balance between cost and quality, ensuring long-term reliability without overspending. It’s important to consider the specific needs of your home and consult with professionals to determine the best material for your situation. Additionally, sourcing materials locally can reduce transportation costs and support the local economy.
Efficient Planning
Planning the repiping project during off-peak times for contractors can potentially lower labor costs. Contractors may offer discounts during less busy periods, which can help reduce overall expenses. Additionally, efficient planning can help minimize disruptions to daily life, making the process smoother and more manageable. Proper scheduling and coordination with the contractor can also prevent delays and ensure that the project is completed on time. Implementing a phased approach to construction can also help manage costs and resources more effectively.
Obtaining Multiple Quotes
Getting multiple quotes from reputable plumbing contractors can help ensure competitive pricing. Comparing quotes allows you to choose the best value for your money and negotiate better terms. It also provides an opportunity to understand the scope of work and identify any potential hidden costs. Thoroughly reviewing each quote and asking questions can help clarify what is included and avoid unexpected expenses. Additionally, checking references and reviews can help ensure that you select a reliable and experienced contractor. Building strong relationships with contractors can also lead to better service and potential discounts on future projects.
DIY Minor Repairs
If you have the skills, consider handling minor repairs yourself to save on labor costs. Tasks such as patching small holes in drywall or painting can be done by homeowners, reducing the overall project cost. However, it’s important to only undertake tasks that you are confident in completing to avoid potential issues or additional costs from mistakes. Properly researching and preparing for DIY tasks can ensure successful completion and contribute to overall cost savings. Taking on small tasks can also provide a sense of accomplishment and reduce the overall project timeline.
Regular Maintenance
Regular maintenance of your plumbing system can help prevent major issues and extend the lifespan of your pipes. Scheduled inspections and minor repairs can prevent costly damage and ensure the long-term functionality of your plumbing system. Implementing a maintenance schedule can help identify potential problems early, allowing for timely repairs and avoiding more significant issues. Regularly checking for leaks, corrosion, and other signs of wear can help maintain the efficiency and reliability of your plumbing system. Proper maintenance can also improve the building’s energy efficiency and reduce operational costs over time.
Download Template For Commercial Building Project Breakdown
- Materials list updated to the zip code
- Fast delivery
- Data base of general contractors and sub-contractors
- Local estimators
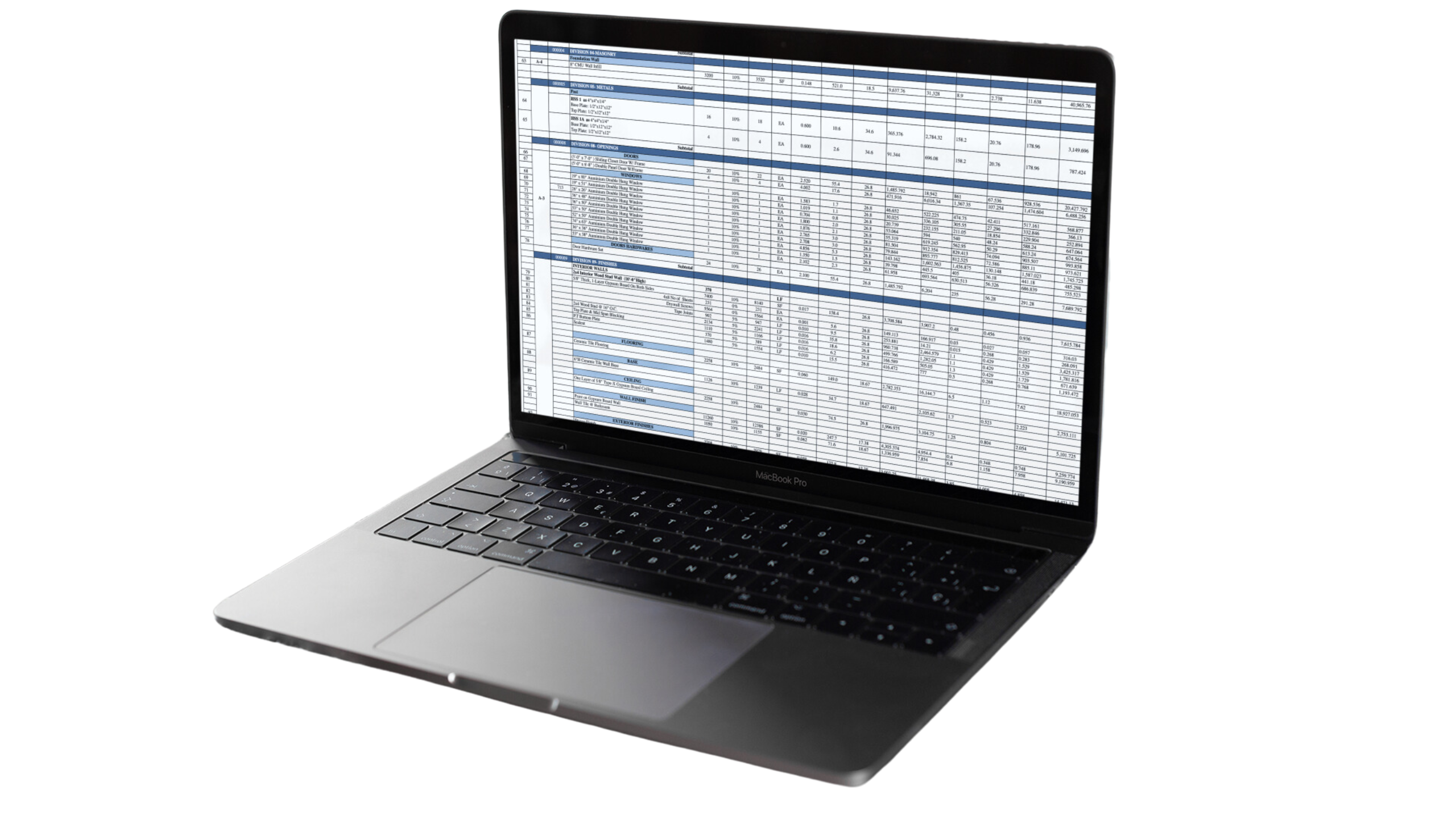
Conclusion
Repiping a house in Florida is a significant investment that requires careful planning and budgeting. By understanding the various cost components, including materials, labor, and additional expenses, homeowners can make informed decisions and ensure the success of their repiping project. Proper financial planning and cost management are crucial for completing the project on time and within budget, ultimately leading to a functional and efficient plumbing system. By focusing on efficient planning, choosing cost-effective materials, and obtaining multiple quotes, homeowners can achieve the best value for their investment in repiping. Additionally, considering cost-saving tips and setting aside a contingency fund can enhance the overall success and financial stability of the project. Implementing these strategies can lead to a smooth, cost-effective repiping project that enhances the home’s value and functionality. Moreover, a successful repiping project can provide peace of mind and improve the overall quality of life for homeowners by ensuring a reliable and efficient plumbing system.
FAQs
Building a 10,000 sq ft commercial building in Florida typically costs between $1,610,600 and $4,050,000, averaging $160 to $405 per square foot. This includes site preparation, construction, interior finishes, plumbing, electrical systems, HVAC, and necessary permits.
Factors include the building’s design complexity, material quality, local labor rates, site preparation, and additional features such as advanced technology integrations and custom finishes.
Pre-construction costs include architectural and engineering fees ($60,000 – $180,000), permits and inspections ($6,000 – $24,000), and site preparation ($12,000 – $60,000).
Architectural and engineering fees usually range from 5% to 15% of the total construction cost. For a 10,000 sq ft building, this can be between $60,000 and $180,000.
Permit and inspection costs can range from $6,000 to $24,000, depending on the location and complexity of the project.
Site preparation, including clearing the land, grading, and ensuring proper drainage, can range from $12,000 to $60,000.
Main construction costs include the foundation ($120,000 – $300,000), structural frame ($180,000 – $360,000), exterior finishes ($240,000 – $420,000), roofing ($120,000 – $240,000), interior finishes ($240,000 – $480,000), and mechanical, electrical, and plumbing (MEP) systems ($360,000 – $720,000).
Google Reviews
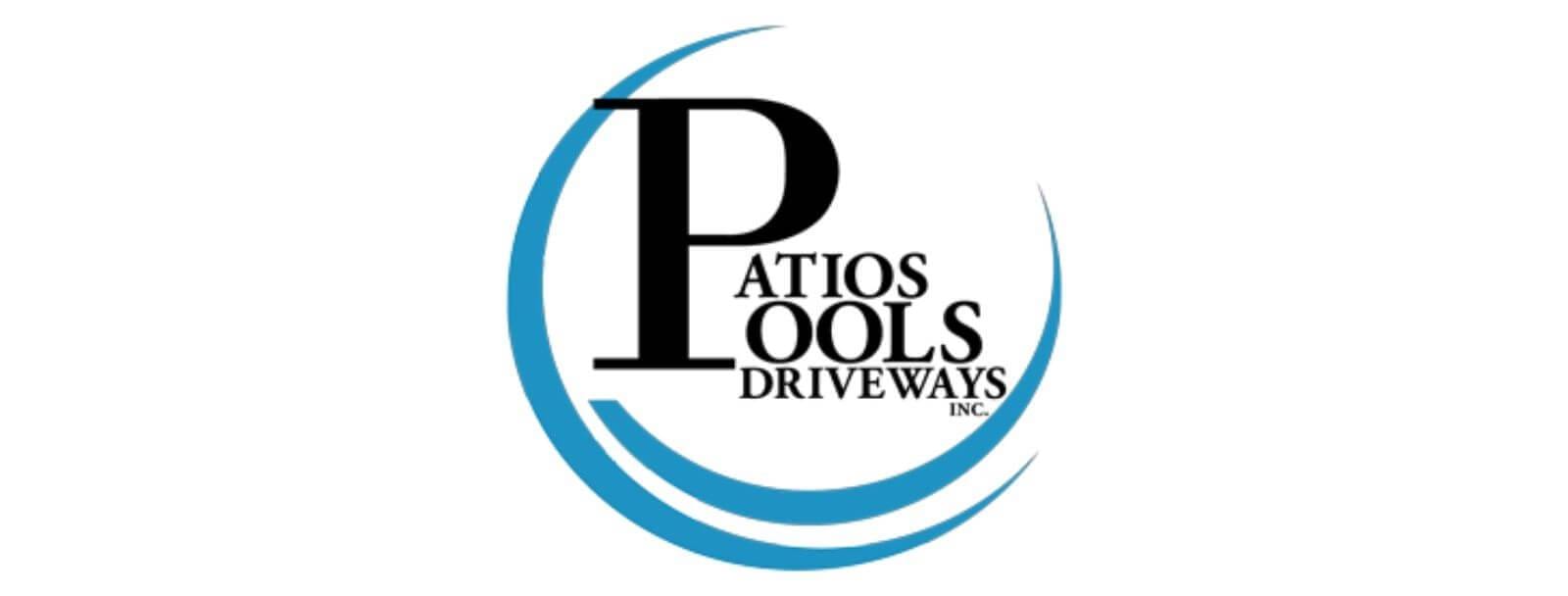
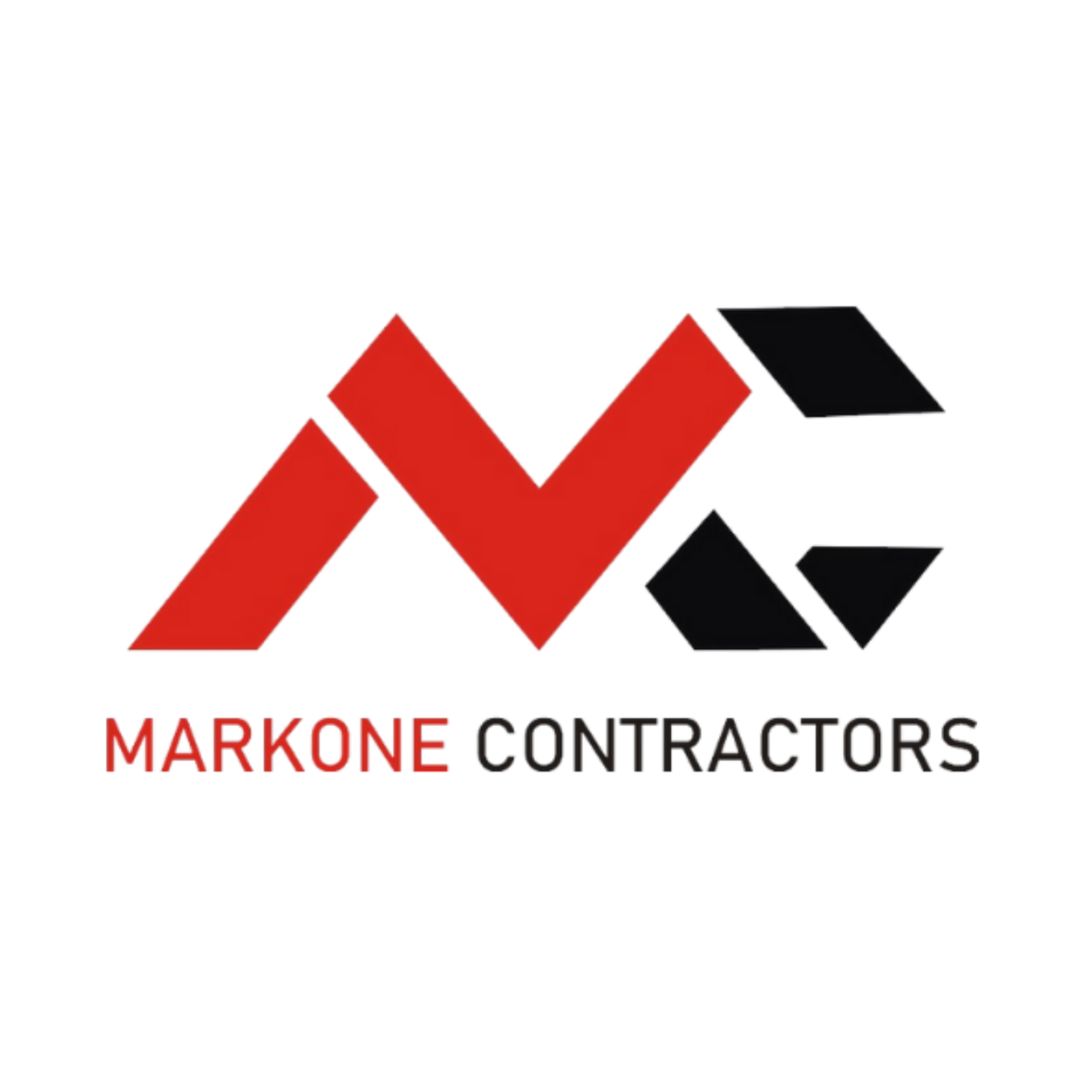

Process To Get Build a 10,000 Sq Ft Commercial Building Estimate Report
Here I am going to share some steps to get build a 10,000 sq ft commercial building estimate report.
-
You need to send your plan to us.
You can send us your plan on info@estimatorflorida.com
-
You receive a quote for your project.
Before starting your project, we send you a quote for your service. That quote will have detailed information about your project. Here you will get information about the size, difficulty, complexity and bid date when determining pricing.
-
Get Estimate Report
Our team will takeoff and estimate your project. When we deliver you’ll receive a PDF and an Excel file of your estimate. We can also offer construction lead generation services for the jobs you’d like to pursue further.