Bid Strong, Bid Smart – Try Our Hospital Construction Cost Estimating Service!
- Accurancy
- Efficiency
- Transparency
- Customization
- Time Saving
- Professionalism
- Cost Control
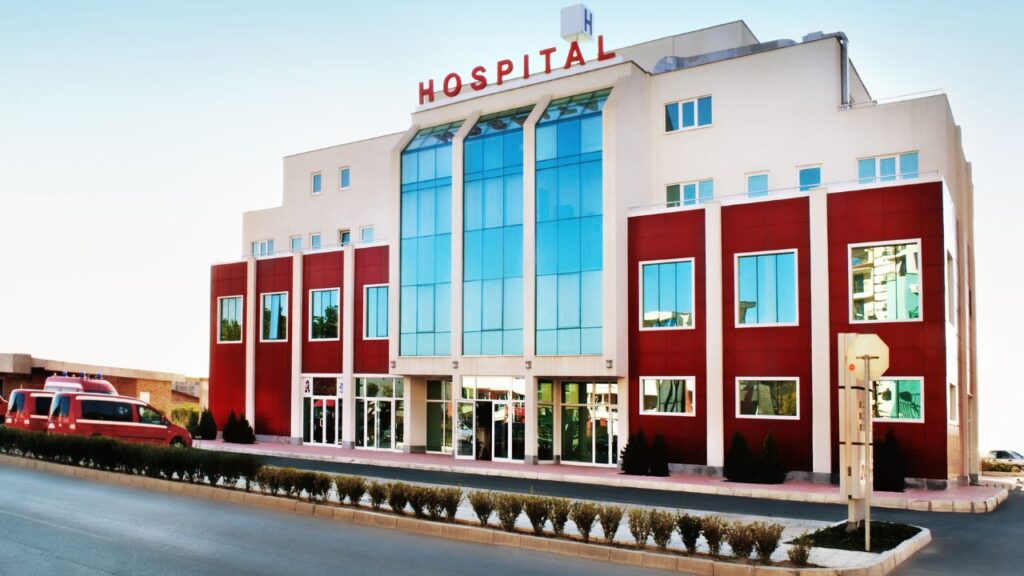
The construction of a hospital building involves various intricate processes, and one fundamental aspect is the installation of concrete walls. Concrete walls serve as the backbone of the structure, providing stability, durability, and a secure environment for patients, medical staff, and visitors. This article delves into the multifaceted factors that influence the cost of constructing concrete walls in hospital buildings, highlighting the importance of meticulous planning and considerations in achieving a balance between functionality, aesthetics, and budget constraints.
Concrete walls in hospital buildings play a pivotal role in ensuring the structural integrity and safety of the facility. Beyond their foundational purpose, these walls contribute significantly to creating a conducive healing environment. They serve as sound barriers, maintaining privacy for patients, and act as a canvas for various finishes and designs that can enhance the overall aesthetic appeal of the hospital. The selection of materials, construction methods, and finishes for concrete walls becomes a critical decision that impacts not only the building’s performance but also its visual and therapeutic aspects.
Fully Insured License
Hire Contractor For Hospital Construction
Make Informed Design Decisions Showcase Your Design Ideas
Get RenderingChoosing the right concrete material for hospital walls is a critical decision that significantly influences construction costs. Hospitals commonly have various options, including traditional concrete blocks, precast concrete panels, and insulated concrete forms (ICFs). While traditional blocks are often considered cost-effective, precast panels and ICFs offer distinct advantages such as rapid installation and improved insulation. The decision is guided by the specific requirements of the hospital project, considering factors like thermal efficiency and structural demands. For instance, hospitals may prioritize ICFs for their enhanced insulation properties, which could lead to potential long-term energy savings despite their higher initial cost. Striking a balance between cost considerations and long-term benefits is essential in ensuring that the chosen concrete material aligns with both immediate budget constraints and the overarching goals of the hospital construction project.
The architectural design of hospital buildings goes beyond mere functionality, often incorporating unique features and finishes to create a visually appealing and therapeutic environment. However, these design elements can contribute to increased construction costs. Intricate designs, decorative elements, and specialized finishes, while enhancing the aesthetics of hospital walls, may require additional resources and craftsmanship. Achieving a harmonious balance between the desire for visually appealing walls and budget constraints necessitates collaboration between architects and project stakeholders. Early engagement in the design phase allows for the exploration of cost-effective design solutions that maintain the intended aesthetic while ensuring financial feasibility. This collaboration ensures that the final design not only meets the creative aspirations of the stakeholders but also aligns with the overall budgetary parameters of the hospital construction project.
The thickness and height of concrete walls are crucial factors directly impacting construction costs. Hospital buildings often have specific requirements for wall thickness based on structural considerations and local building codes. Efficient design planning that optimizes wall thickness while meeting safety standards is essential to control costs without compromising structural integrity. Careful consideration of the structural demands of the hospital ensures that the walls provide the necessary support and stability while avoiding unnecessary material usage.
This optimization not only contributes to cost-effectiveness but also aligns with sustainability goals by minimizing material waste. Strategic planning during the design phase, involving architects, engineers, and construction teams, is paramount in achieving the delicate balance between meeting safety standards and controlling construction costs.
The conditions of the construction site and its accessibility significantly influence concrete wall construction costs. Hospitals are often situated in challenging terrains or densely populated urban areas, leading to potential complications. Factors such as limited access, challenging topography, or the need for special equipment can contribute to increased labor costs and logistical complexities. Identifying and addressing potential challenges early in the planning stages allows for strategic planning to mitigate additional costs associated with site-specific conditions. For instance, implementing efficient transportation strategies for materials and equipment can minimize logistical challenges and associated costs. Proactive site assessment and planning ensure that the construction process is optimized for the specific conditions of the hospital site, ultimately contributing to cost-effectiveness and timely project completion.
Hospitals demand advanced technological infrastructure and utilities integrated directly into their walls, including electrical wiring, plumbing, and medical gas lines. While these integrations are essential for the hospital’s functionality, they add complexity to the construction process and impact costs. Thoughtful planning and coordination between construction teams and technology specialists are paramount to optimize the integration of utilities without incurring undue financial burden. Integrating technology into the walls during the construction phase requires precise coordination to ensure that the infrastructure meets the hospital’s current and future needs. Early collaboration between construction teams and technology specialists allows for efficient planning, minimizing potential rework and additional costs during the construction process. The seamless integration of utilities is a critical aspect of hospital construction, emphasizing the need for meticulous planning and coordination to optimize costs.
Hospital construction must adhere to stringent regulatory standards and codes, ranging from seismic codes to fire safety regulations and energy efficiency requirements. Compliance with these standards may necessitate additional construction measures, impacting costs significantly. Proactive engagement with regulatory authorities during the planning phase helps anticipate and address compliance-related costs effectively. For example, hospitals may need to invest in specialized construction techniques or materials to meet seismic codes, ensuring the safety and resilience of the building in the event of an earthquake. While these compliance-related costs may seem additional, they are non-negotiable for ensuring the safety, functionality, and regulatory adherence of hospital buildings. Proactive engagement with regulatory authorities and early planning for compliance-related costs are essential steps in avoiding delays and cost overruns during the construction process.
Concrete wall construction costs for hospital buildings can vary widely based on the factors mentioned above. On average, the cost per square foot can range from $80 to $150 or more, encompassing materials, labor, finishes, and any additional features or utilities integrated into the walls. The intricacies of hospital construction often place it on the higher end of this spectrum due to specialized requirements and the critical nature of healthcare facility infrastructure.
Thorough project planning stands as the cornerstone of successful hospital construction, particularly when it comes to the intricate task of erecting concrete walls. This planning phase involves a meticulous examination of the hospital’s functional requirements and aesthetic aspirations. Clear and open communication channels between project stakeholders, architects, and construction teams are imperative during this phase. This ensures a shared vision and facilitates efficient decision-making throughout the construction process. By aligning everyone involved with the project’s goals and constraints, detailed project planning serves as a roadmap for the subsequent stages, helping to preemptively address challenges and streamline the construction of concrete walls.
The implementation of value engineering practices is a strategic approach to ensure cost-effectiveness without compromising quality at any stage of the hospital construction project. This systematic process involves a comprehensive evaluation of cost implications during design and construction. Value engineering identifies opportunities to achieve cost savings through creative problem-solving and the exploration of alternative materials or construction methods. In the context of concrete walls, this may involve assessing different concrete formulations, construction techniques, or sourcing options.
By fostering innovation and cost-conscious decision-making, value engineering plays a pivotal role in optimizing construction costs while maintaining the integrity of the hospital building.
Early engagement with experienced architects and design professionals is critical for achieving a harmonious balance between design ambitions and cost considerations. Hospital construction projects demand a unique blend of functionality and aesthetic appeal, especially concerning concrete walls. The expertise of design professionals is invaluable in ensuring that the chosen designs align with both functional requirements and aesthetic goals within the defined budget. Collaborative decision-making during the design phase allows for the exploration of various design possibilities, taking into account construction costs, material choices, and overall project feasibility. This proactive collaboration sets the stage for a well-informed and cost-effective construction process.
Exploring sustainable and efficient construction materials is a forward-thinking strategy that contributes to long-term cost-effectiveness. While innovative materials with enhanced insulation properties, recycled content, or reduced environmental impact may have higher upfront costs, they offer potential savings in operational and energy costs over the lifespan of the hospital building. This is particularly relevant in the context of concrete walls, where choosing materials with high thermal efficiency can lead to reduced heating and cooling expenses. Material efficiency and sustainability considerations not only align with modern construction practices but also position the hospital as an environmentally conscious and resource-efficient institution, further enhancing its long-term value.
The construction phase requires continuous monitoring to ensure that the project stays on track, both in terms of progress and budget adherence. Regular monitoring of construction progress and costs allows for the timely identification of potential deviations from the budget. Proactive adaptation to changing circumstances or unforeseen challenges is crucial for minimizing cost overruns. This adaptability ensures that the construction process remains agile and responsive to evolving conditions. In the realm of concrete walls, unforeseen issues related to site conditions, material availability, or regulatory changes may arise. Continuous monitoring enables project managers and stakeholders to address these challenges promptly, mitigating their impact on costs and maintaining the overall project timeline.
The construction of concrete walls in hospital buildings involves a complex interplay of factors that influence costs. From material selection to compliance with regulatory standards, each decision contributes to the overall expenses. The importance of concrete walls in hospitals goes beyond structural support, encompassing privacy, aesthetics, and the integration of advanced technologies. Cost estimation for these walls can range from $80 to $150 or more per square foot, reflecting the specialized nature of healthcare facility infrastructure.
To optimize costs, meticulous project planning, value engineering, collaboration with design professionals, and the exploration of sustainable materials are crucial strategies. Continuous monitoring and adaptation during the construction phase help address challenges promptly, ensuring that the project stays on track. Balancing functionality, aesthetics, and budget constraints is essential for the successful completion of hospital construction projects with durable, visually appealing, and cost-effective concrete walls.
The cost of concrete walls is influenced by various factors such as material selection, architectural design, wall thickness, site conditions, integration of technology, regulatory compliance, and more. Each decision in these areas can impact the overall expenses.
Material choices, including traditional concrete blocks, precast panels, or insulated concrete forms, play a crucial role in determining construction costs. Factors such as thermal efficiency, structural demands, and long-term benefits guide the selection, balancing immediate budget constraints with overarching project goals.
Hospitals require advanced technological infrastructure and utilities integrated into their walls, adding complexity and impacting costs. Thoughtful planning and coordination between construction teams and technology specialists are essential to optimize the integration of utilities without incurring undue financial burden.
Challenging terrains, limited access, or special equipment needs can contribute to increased labor costs and logistical complexities. Identifying and addressing potential challenges early in the planning stages allow for strategic planning to mitigate additional costs associated with site-specific conditions.
Hospital construction must adhere to stringent regulatory standards and codes, including seismic codes, fire safety regulations, and energy efficiency requirements. Compliance with these standards may necessitate additional construction measures, impacting costs significantly.
Value engineering practices involve evaluating cost implications during design and construction to identify opportunities for cost savings without compromising quality. This systematic process fosters creative problem-solving and exploration of alternative materials or construction methods, playing a pivotal role in optimizing construction costs while maintaining integrity.
Here I am going to share some steps to get your hospital building concrete wall cost estimate report.
You can send us your plan on info@estimatorflorida.com
Before starting your project, we send you a quote for your service. That quote will have detailed information about your project. Here you will get information about the size, difficulty, complexity and bid date when determining pricing.
Our team will takeoff and estimate your project. When we deliver you’ll receive a PDF and an Excel file of your estimate. We can also offer construction lead generation services for the jobs you’d like to pursue further.
561-530-2845
info@estimatorflorida.com
Address
5245 Wiles Rd Apt 3-102 St. Pete Beach, FL 33073 United States
561-530-2845
info@estimatorflorida.com
Address
5245 Wiles Rd Apt 3-102 St. Pete Beach, FL 33073 United States
All copyright © Reserved | Designed By V Marketing Media | Disclaimer