Boost Your Drywall Bids – Request a Precision Estimate!
- Accurancy
- Efficiency
- Transparency
- Customization
- Time Saving
- Professionalism
- Cost Control
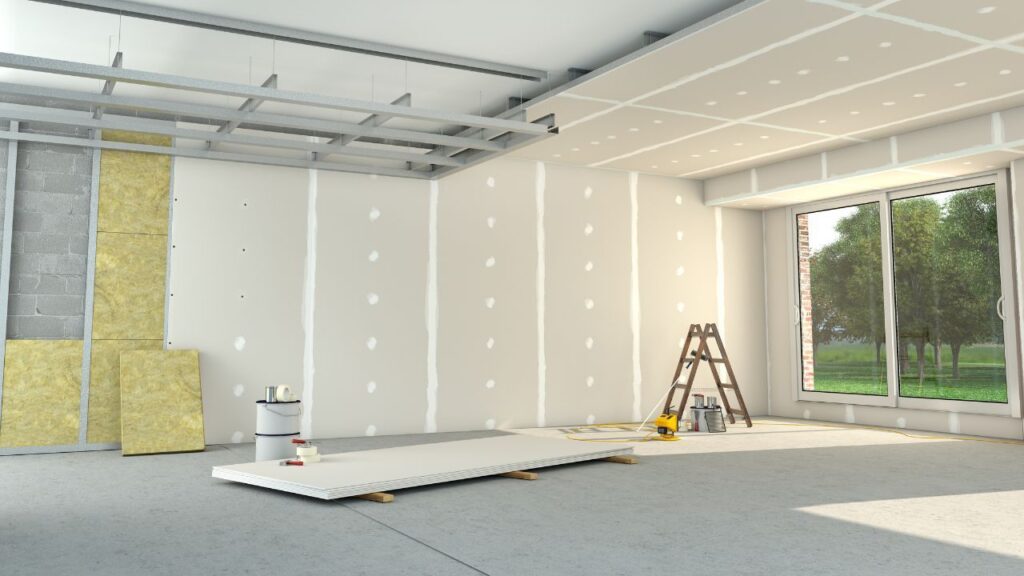
Erecting a high-rise stands as a remarkable achievement, showcasing our ambition and inventive spirit. Yet, amid the imposing steel and concrete, a pivotal element often escapes attention: the humble drywall. This underrated protagonist plays a defining role in crafting interiors, molding spaces, and impacting acoustics. As we navigate the intricacies of a high-rise endeavor, precise estimation of drywall costs takes center stage.
Embarking on projects at ground level enjoys the luxury of seamless material delivery and worker mobility. However, high-rises demand an entirely different choreography. Scaling the heights introduces a logistical ballet, with materials hoisted on cables and workers suspended like modern-day trapeze artists. This aerial waltz inevitably adds to the cost, with an estimated $0.60 to $1.80 per square foot premium compared to your street-level counterparts. Every sheet of drywall that takes an elevator ride, every tool that needs a pulley, adds to the price tag, reminding us that convenience, in this vertical world.
At the core of any high-rise project is concrete, and the larger the building, the more substantial the concrete volume required. As the structure ascends, envision the process akin to assembling Lego blocks – the more blocks stacked, the higher the cost. Yet, it’s not merely about size; ambitious architectural designs with intricate curves and daring cantilevers demand specialized formwork. Similar to sculpting with clay, intricate shapes necessitate advanced molds, adding a layer of cost intricacy.
Forget cookie-cutter layouts; high-rises crave the drama of soaring ceilings, the elegance of curved walls, and the intrigue of intricate floor plans. But with each flourish, complexity creeps in, demanding specialist skills and extended labor hours. Imagine the contortions it takes to hang drywall on a vaulted ceiling or navigate the labyrinthine curves of a modern open-plan living space. Such feats require the artistry of experienced professionals, and their expertise comes at a cost, bumping up the price by $2.40 to $6 per square foot or even more. So, while your high-rise may boast architectural pizzazz, remember, every corner you add adds another corner to your budget.
In the hushed world of high-rise living, peace and quiet are paramount. But ensuring such tranquility demands robust soundproofing measures, and these come at a price. Soundproof panels, thicker than their standard counterparts, can add an extra $1.20 to $3.60 per square foot to your drywall bill. Similarly, fire safety takes center stage, necessitating fire-resistant drywall options that can push the cost up by $0.30 to $1.20 per square foot. While these regulations may seem like financial hurdles, remember, they’re investments in the well-being and safety of your future residents, investments that contribute to the intrinsic value of your high-rise haven.
In the world of high-rise drywall, waste is not an option. With material deliveries requiring meticulous planning and sky-high logistics, minimizing discarded sheets becomes a crucial cost-saving strategy. This often necessitates prefabricated panels or custom sizing, adding $0.12 to $0.60 per square foot to the equation. But think of it as an investment in efficiency, a strategic dance with every inch of space, ensuring that every sheet of drywall reaches its intended destination, contributing to a perfectly finished interior without a penny wasted.
While squaring the footage might seem like a straightforward first step, in the intricate world of high-rise drywall, it’s just the opening act. Remember, those soaring ceilings, curved walls, and intricate layouts don’t simply vanish when converted to a number. They’re silent cost assassins, lurking in the shadows of your calculations. To truly conquer the estimate, a 24-60% complexity tax might be necessary. Imagine a swirling staircase wall – it demands more cuts, more angles, more acrobatics on the scaffolding. Each such flourish adds its own invisible digit to the price tag, reminding us that simplicity, in this domain, is a budget’s best friend.
Drywall may be the star of the show, but the supporting cast – fire-resistant panels, soundproof barriers, specialty screws – play crucial roles in a high-rise production. Each material upgrade comes with its own price tag, like a costuming fee for the actors in your interior design drama. Factor in local material availability and research their specific costs before adding them to your base estimate. Remember, fire safety regulations and noise-cancelling, so choose your materials wisely, considering both performance and the financial performance of your project.
Picture skilled artisans suspended from the heavens, their trowels dancing across vast swathes of ceiling, their saws whispering through intricate curves. These are the drywall ninjas of the high-rise world, and their expertise doesn’t come cheap. Complex designs and lofty heights necessitate additional crew members, specialized skills, and extended labor hours. Consult with experienced contractors to estimate the man-hours involved in your project, keeping in mind the $2.40 to $6 per square foot premium that high-rise labor often commands. Remember, their expertise ensures a flawless finish, but be prepared to pay for the privilege of their aerial artistry.
Don’t be fooled – drywall costs aren’t a universal constant. Location plays a starring role in this financial equation. Material availability, labor rates, and local regulations can all influence the final price tag. Research the drywall landscape in your specific city, understanding the unique factors that drive costs in your neck of the woods. Adjust your estimate accordingly, remembering that a material readily available in one urban jungle might be a rare and expensive beast in another.
By accounting for these hidden actors in the high-rise drywall drama, you can transform your estimate from a rough sketch to a detailed masterpiece. Remember, complexity demands a nuanced approach, materials play a supporting role with financial weight, skilled labor deserves its due, and local variations add their own spice to the cost equation. With careful consideration and these tips as your guide, you can conquer the budgetary heights and watch your high-rise drywall dreams take shape, one perfectly hung sheetrock at a time.
Embarking on the construction of a high-rise is a testament to human ambition and innovation. As steel and concrete ascend towards the sky, defying gravity and shaping city skylines, it’s the often-underappreciated layer of drywall that transforms these towering structures into habitable havens. Functioning as the unseen magician behind the scenes, drywall shapes rooms, whispers promises of comfort, and plays a pivotal role in both aesthetics and functionality. However, in this intricate dance of construction, a single misstep can lead to significant financial consequences.
Estimating drywall costs in a high-rise project goes beyond the simplicity of multiplying square footage by a fixed price. It requires a comprehensive understanding of the unique factors that can cause costs to escalate, much like an elevator ascending to the penthouse. From overcoming logistical challenges that seem to defy gravity to adhering to strict regulations ensuring the safety and comfort of future residents, every facet of a high-rise environment demands a nuanced approach to cost estimation.
Without accurate foresight, even the most meticulously planned project risks encountering budgetary setbacks that could shatter financial aspirations akin to a rogue pane of glass plummeting from a great height. Therefore, before embarking on the high-rise drywall journey, let’s delve into the intricate factors influencing the price tag and equip ourselves with the knowledge needed to conquer the financial summit—one perfectly hung sheetrock at a time.
While estimating costs is a vital component of overseeing a prosperous high-rise drywall project, it’s not the only consideration. Selecting the right contractor, one well-versed in high-rise construction and aligned with your vision, is paramount. Seamless communication and collaboration throughout the project, from intricate planning to on-site adjustments, play a pivotal role in ensuring top-notch finishes are achieved within the specified budget.
Scaling the heights of a high-rise project may present numerous challenges, but accurate drywall cost estimation doesn’t need to be one of them. By comprehending the distinctive factors influencing high-rise construction, leveraging available tools, and seeking expert guidance, you can conquer the financial summit and materialize your vision—each perfectly hung sheetrock contributing to the realization of your project.
Accurate cost estimation is vital to ensure that the budget aligns with the financial resources available. High-rise projects, with their unique challenges, demand a nuanced approach to drywall cost estimation to prevent budgetary setbacks and financial risks.
The intricacies of high-rise designs, such as soaring ceilings and curved walls, necessitate specialized skills and extended labor hours. This complexity adds to the overall drywall costs, emphasizing the importance of considering design intricacies during the estimation process.
Regulations, particularly those related to safety, soundproofing, and fire resistance, significantly influence drywall costs in high-rise constructions. Meeting these standards often requires specific materials and construction techniques, contributing to the overall project expenses.
Drywall costs are not universal, as they are influenced by local factors such as material availability, labor rates, and regulations. Understanding the unique variables in a specific location is essential for accurate cost estimation, ensuring that the project budget aligns with local market conditions.
In high-rise construction, waste management is crucial for cost-saving. Strategies such as using prefabricated panels, custom sizing, and meticulous planning for material deliveries help minimize discarded sheets. This efficient use of resources contributes to a well-managed budget and a perfectly finished interior.
Here I am going to share some steps to get your high-rise building drywall cost estimate report.
You can send us your plan on info@estimatorflorida.com
Before starting your project, we send you a quote for your service. That quote will have detailed information about your project. Here you will get information about the size, difficulty, complexity and bid date when determining pricing.
Our team will takeoff and estimate your project. When we deliver you’ll receive a PDF and an Excel file of your estimate. We can also offer construction lead generation services for the jobs you’d like to pursue further.
561-530-2845
info@estimatorflorida.com
Address
5245 Wiles Rd Apt 3-102 St. Pete Beach, FL 33073 United States
561-530-2845
info@estimatorflorida.com
Address
5245 Wiles Rd Apt 3-102 St. Pete Beach, FL 33073 United States
All copyright © Reserved | Designed By V Marketing Media | Disclaimer