Bid Strong, Bid Smart – Try Our Concrete Cost Estimating Service!
- Accurancy
- Efficiency
- Transparency
- Customization
- Time Saving
- Professionalism
- Cost Control
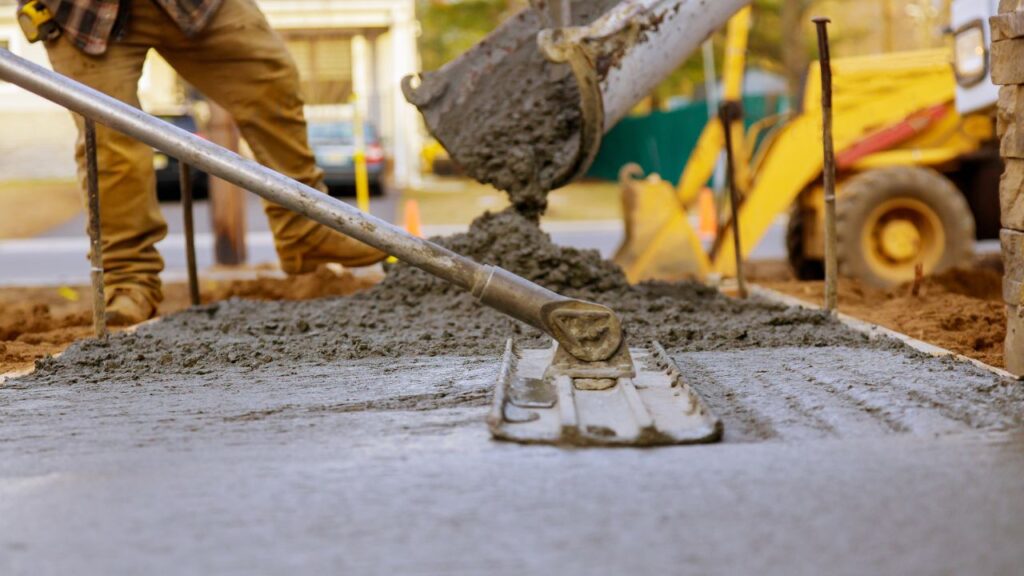
Soaring above the cityscape, high-rise structures stand as feats of contemporary engineering. Despite their elegant exteriors and glistening glass surfaces, a fundamental element lies beneath – concrete. This omnipresent substance constitutes the core of these architectural marvels, influencing their robustness, steadiness, and visual appeal.
Yet, calculating the expense of concrete in a high-rise venture is far from straightforward. A multitude of variables converges, turning it into a intricate equation that requires meticulous attention.
But fret not, bold developer, as this all-encompassing guide is here to provide you with the insights needed to navigate the intricate realm of concrete costs!
In the realm of high-rise construction, concrete stands as the backbone of towering structures, shaping their strength, stability, and aesthetic appeal. However, estimating the cost of concrete in such ambitious projects involves navigating a complex landscape influenced by various factors. Let’s unravel the intricacies of this concrete cost equation.
Fully Insured License
Concrete Construction Contractor
Make Informed Design Decisions Showcase Your Design Ideas
Get RenderingAt the core of any high-rise project is concrete, and the larger the building, the more substantial the concrete volume required. As the structure ascends, envision the process akin to assembling Lego blocks – the more blocks stacked, the higher the cost. Yet, it’s not merely about size; ambitious architectural designs with intricate curves and daring cantilevers demand specialized formwork. Similar to sculpting with clay, intricate shapes necessitate advanced molds, adding a layer of cost intricacy.
Concrete is a versatile material, capable of adapting to various challenges through different mixes. Each mix, with its unique blend of ingredients, comes at a cost. Whether it’s ensuring fire resistance or watertightness, the complexity of the mix, like a gourmet dish with premium ingredients, influences the overall expense.
Pouring liquid concrete requires temporary support – the formwork. Complex shapes demand intricate formwork, resembling the custom-carved molds for an elaborate sandcastle. As the building height increases, shoring becomes essential, adding another layer to the cost. The taller the structure, the more elaborate the shoring system, contributing to the overall concrete expenditure.
Concrete transformation involves skilled crews and specialized machinery. Expertise comes at a cost, reflected in the wages of skilled labor. Additionally, powerful tools like mixers, pumps, and cranes play vital roles, each with its own operational expenses. Project location and complexity further shape labor and equipment costs, influencing the overall expenditure.
Concrete transportation involves hauling tons of material over varying distances, impacting costs. Precision placement, whether through pumps or advanced techniques like slipforming, adds another layer of expense. The logistics of reaching the designated spot contribute significantly to the overall cost.
External factors, such as material availability and local competition, play pivotal roles. Limited resources in certain regions might inflate costs, while competitive markets offer negotiation opportunities. Understanding the local market landscape is key to navigating the intricate world of concrete costs in high-rise construction.
Armed with an understanding of concrete cost influencers, let’s delve into practical methods for estimation:
Drawing from historical data or industry benchmarks, this method assigns a cost per unit volume (cubic yard) of concrete. It takes into account the intricacies of the building, considering factors such as complexity and location.
In this meticulous approach, all concrete elements (walls, slabs, columns) are quantified from construction drawings. Volumes are multiplied by individual material and labor costs, providing a comprehensive and detailed estimation.
Specialized construction estimating software proves invaluable in the estimation process. These tools often integrate unit cost databases, consider project-specific variables, and generate detailed breakdowns of costs. Embracing technology streamlines the estimation journey, offering precision and efficiency in budget planning.
It’s essential to note that these figures are general estimates and not actual cost. Unforeseen challenges, fluctuations in material prices, or weather-related delays can impact the final concrete cost. Therefore, maintaining a contingency buffer in your budget is crucial for effective financial planning and project management.
In the realm of high-rise construction, managing costs is a delicate dance, but it should never compromise the quality of your concrete foundation. Building a skyscraper isn’t a passing trend; it’s the creation of a lasting monument. So, how can you navigate the balance between budget constraints and the need for durability? Dive into a toolbox of optimization strategies to transform the concrete cost labyrinth into a path leading to financial and structural success.
Challenge the conventional “pour-and-pray” method by exploring alternative materials and construction techniques that offer comparable performance at a more budget-friendly cost. Consider the advantages of precast concrete elements, arriving on-site ready for assembly, saving both time and labor costs. Picture building with large-scale Lego blocks – each precast piece seamlessly fits into place, minimizing mess and maximizing efficiency. By creatively substituting traditional methods with innovative alternatives, you can significantly reduce your concrete budget without compromising structural integrity.
While complex designs may appeal to your architectural ambitions, remember that complexity often translates to increased costs. Embrace the elegance of standardization by opting for standardized concrete shapes and sizes instead of bespoke curves. Think of it as choosing readily available Lego bricks over crafting your own – resulting in a robust structure without the expense and intricacy of custom molds and specialized craftsmanship. By prioritizing repetition, you minimize formwork complexity, decrease material waste, and bring relief to your concrete budget.
Don’t delay involving your concrete contractor until the mixer starts churning. Engage them during the design phase for a treasure trove of cost-effective optimization. Your contractor can propose modifications to the concrete mix design, recommend alternative formwork solutions, and suggest efficient placement techniques, all tailored to your specific project. Consider it a pre-construction handshake that can save millions down the line – a mutually beneficial strategy for both your budget and the structural health of the building.
Concrete doesn’t have to be a burden on the environment or your budget. Explore incorporating recycled concrete aggregates or low-carbon concrete mixes into your high-rise project. These eco-friendly options not only reduce your project’s environmental impact but can also unlock tax credits and incentives. Envision constructing your skyscraper with a conscience, offsetting costs while contributing to a greener future. Sustainability isn’t just a buzzword; it’s a savvy optimization strategy that enhances your bottom line and leaves a positive impact on the planet.
By embracing these optimization strategies, you can illuminate the path through the concrete cost labyrinth, guiding your high-rise project toward financial stability and structural magnificence. Remember, concrete is the heart and soul of your architectural dream; choose it wisely, optimize its costs strategically, and witness your masterpiece soaring to new heights with both financial and environmental responsibility.
Fully Insured License
Concrete Construction Contractor
Make Informed Design Decisions Showcase Your Design Ideas
Get RenderingEstimating concrete costs for high-rise projects involves factors like building size, mix design, labor, and local conditions. Practical methods and software tools aid accurate estimations, with cost breakdowns provided.
Concrete costs vary, and the article emphasizes the need for contingency buffers. Optimization strategies like value engineering, standardization, early collaboration, and sustainability offer financial efficiency without compromising quality.
This guide equips developers to manage concrete costs effectively, ensuring high-rise projects stand as enduring monuments of both financial prudence and environmental responsibility.
Estimating concrete costs for high-rise buildings is complex due to various factors such as building size, mix design, formwork intricacies, labor, transportation, and local market conditions. These variables interact, making it a nuanced and intricate calculation.
Building size directly influences the volume of concrete required. As the structure ascends, more concrete is needed, resembling the process of stacking Lego blocks. Additionally, ambitious designs with intricate shapes demand specialized formwork, adding complexity and cost.
Concrete mix design involves tailoring the material for specific challenges. Different mixes come at varying costs, akin to a gourmet dish with premium ingredients. Factors like fire resistance or watertightness influence the complexity of the mix, contributing to overall expenses.
Formwork provides temporary support for liquid concrete, and its complexity increases with intricate building designs. As structures grow taller, shoring becomes essential to support the weight of concrete above. Both formwork and shoring contribute significantly to overall concrete expenditure.
Skilled labor and specialized machinery, including mixers, pumps, and cranes, are crucial for transforming concrete. Skilled crews come at a cost reflected in wages, and equipment operational expenses contribute to the overall budget. Project location and complexity further shape these costs.
Optimization strategies include value engineering, exploring alternative materials and construction methods, embracing standardization, involving the concrete contractor early in the design phase, and incorporating sustainable practices. These approaches enhance financial efficiency while maintaining the quality of the concrete foundation.
Here I am going to share some steps to get your high-rise building cost estimate report.
You can send us your plan on info@estimatorflorida.com
Before starting your project, we send you a quote for your service. That quote will have detailed information about your project. Here you will get information about the size, difficulty, complexity and bid date when determining pricing.
Our team will takeoff and estimate your project. When we deliver you’ll receive a PDF and an Excel file of your estimate. We can also offer construction lead generation services for the jobs you’d like to pursue further.
561-530-2845
info@estimatorflorida.com
Address
5245 Wiles Rd Apt 3-102 St. Pete Beach, FL 33073 United States
561-530-2845
info@estimatorflorida.com
Address
5245 Wiles Rd Apt 3-102 St. Pete Beach, FL 33073 United States
All copyright © Reserved | Designed By V Marketing Media | Disclaimer