HDPE pipes are widely used across various industries due to their strength, flexibility, and resistance to environmental factors such as chemicals and UV radiation. From municipal water supply lines to industrial piping systems, HDPE pipes are integral in many infrastructure projects. However, the costs associated with HDPE pipe installation can vary significantly based on factors like pipe size, installation method, and location.
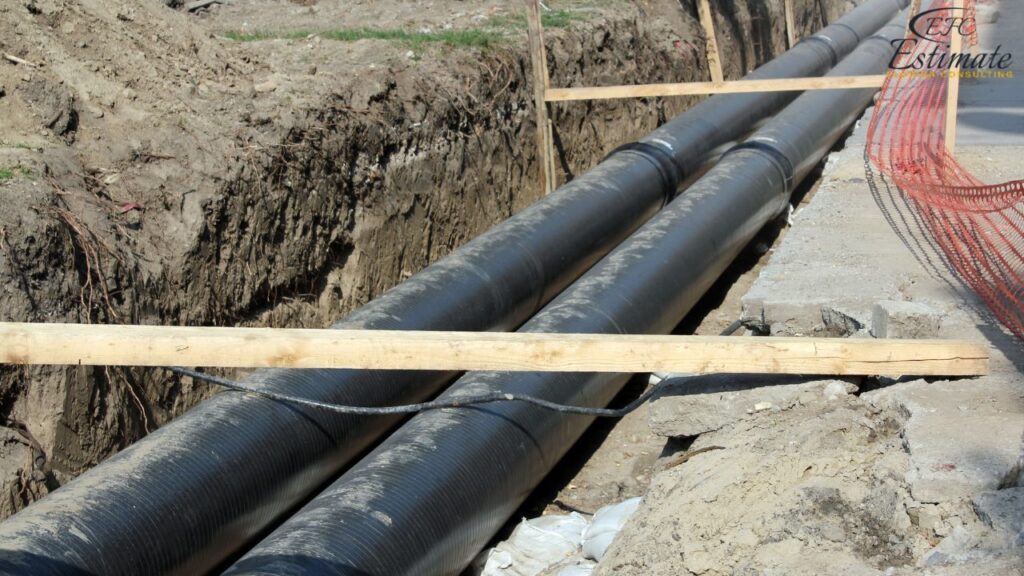