Estimating Expenses for a 40,000 sq ft
Industrial Complex in Palm Beach
Building a 40,000 sq ft industrial complex in Palm Beach involves considerable planning and financial investment. The costs are influenced by various factors, including land acquisition, construction, furnishing, installation of mechanical systems, and compliance with regulatory requirements. This guide provides a detailed breakdown of the expenses associated with developing an industrial complex in this location, helping investors make informed decisions and accurately budget for their projects. Palm Beach, known for its strategic location and business-friendly environment, offers a promising setting for industrial development, provided the costs are carefully managed.
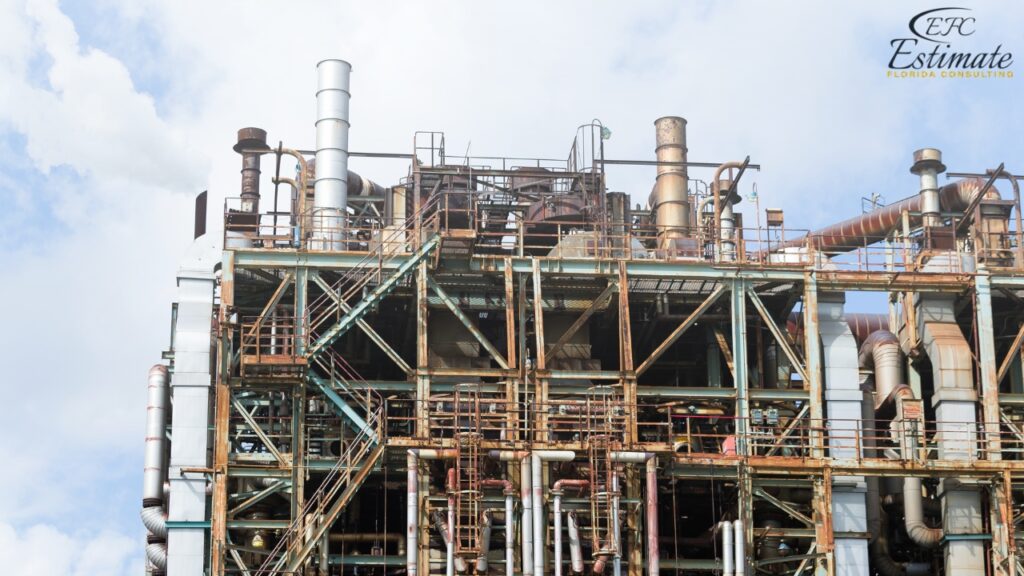
With its proximity to major transportation hubs and a robust local economy, investing in an industrial complex here can yield significant returns if planned and executed properly.
Factors Influencing Industrial Complex Costs
Land Acquisition
The cost of land in Palm Beach can be significant, given its prime location and high demand for industrial spaces. The proximity to major transportation hubs, accessibility, and the land’s development potential are crucial factors that influence the price. Securing land in a strategic location can enhance the industrial complex’s operational efficiency and market appeal. Additionally, the availability of infrastructure such as roads, utilities, and connectivity to other industrial areas can also impact the overall cost and attractiveness of the site. Proper due diligence and land valuation are essential to ensure the land acquired offers long-term benefits and aligns with the overall business strategy.
Location Type | Estimated Cost (per acre) |
Inland | $960,000 – $1,440,000 |
Near Highway | $1,440,000 – $2,400,000 |
Prime Industrial Area | $2,400,000 – $3,840,000 |
Construction Costs
Construction costs for an industrial complex include expenses for materials, labor, permits, and site preparation. These costs can vary widely depending on the quality of materials, design complexity, and local labor rates. High-quality construction ensures the durability and functionality of the complex, which is critical for industrial operations. Utilizing advanced construction techniques and sustainable building materials can also add value and reduce long-term maintenance costs. Furthermore, the choice of construction partners and contractors plays a significant role in adhering to budgets and timelines, ensuring that the project stays on track from inception to completion.
Construction Type | Estimated Cost (per sq ft) |
Basic | $144 – $216 |
Mid-Range | $216 – $360 |
High-End | $360 – $504 |
Mechanical, Electrical, and Plumbing (MEP) Systems
MEP systems are essential for the functionality and operational efficiency of the industrial complex. This includes HVAC systems, plumbing, electrical wiring, and other necessary mechanical systems. Investing in energy-efficient systems can reduce long-term operational costs and enhance the complex’s sustainability. Advanced MEP systems can also improve workplace safety and productivity by providing a comfortable and well-ventilated environment. Integration of smart technology in MEP systems allows for better control and monitoring, leading to optimized energy usage and reduced operational expenses.
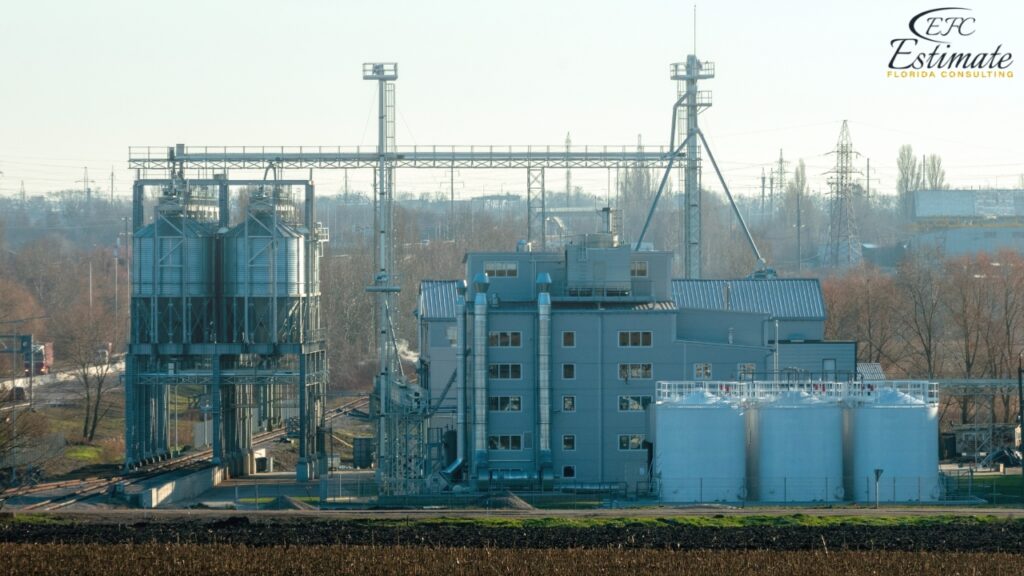
Regular maintenance and updates to these systems ensure compliance with safety standards and prolong their lifespan.
System Quality | Estimated Cost (per sq ft) |
Basic | $28.80 – $57.60 |
Mid-Range | $57.60 – $86.40 |
High-End | $86.40 – $115.20 |
Interior Finishing and Furnishing
The interior finishing and furnishing costs cover office spaces, work areas, restrooms, and common areas. High-quality finishes and functional furnishings contribute to the productivity and comfort of employees, enhancing the overall efficiency of the industrial complex. Choosing durable and easy-to-maintain materials for floors, walls, and fixtures can reduce long-term maintenance costs. Additionally, ergonomic furniture and well-designed workspaces can improve employee satisfaction and productivity, making the complex a more attractive place to work. Customizing the interiors to meet the specific needs of the operations, including specialized storage or assembly areas, can further enhance functionality.
Furnishing Quality | Estimated Cost (per sq ft) |
Basic | $24 – $48 |
Mid-Range | $48 – $72 |
Luxury | $72 – $120 |
Get 5 New Leads Next 7Days With Our System
- Multi-Family Building
- Hotel Building
- Hospital Building
- Warehouse Building
- High-Rise Building
- Shopping Complex
Permits and Fees
Obtaining the necessary permits and paying associated fees is a crucial part of the construction process. These costs ensure compliance with local building codes, safety regulations, and environmental standards. Properly managed permits and inspections help avoid legal issues and ensure that the complex meets all regulatory requirements. Engaging with local authorities and understanding the permitting process can help in anticipating any potential delays or additional requirements. Working with experienced legal and compliance consultants can streamline this process and ensure that all necessary documentation is in place, preventing costly disruptions and fines.
Permit Type | Estimated Cost |
Building Permit | $36,000 – $72,000 |
Environmental Permit | $24,000 – $48,000 |
Zoning and Land Use Permits | $18,000 – $36,000 |
Detailed Cost Breakdown
Here’s a detailed cost breakdown for constructing a 40,000 sq ft industrial complex in Palm Beach, considering various factors:
Cost Component | Estimated Cost |
Land Acquisition | $3,840,000 – $15,360,000 |
Construction | $5,760,000 – $20,160,000 |
MEP Systems | $1,152,000 – $4,608,000 |
Interior Finishing | $960,000 – $4,800,000 |
Permits and Fees | $78,000 – $156,000 |
Total | $11,790,000 – $45,084,000 |
Examples of Total Construction Costs for Different Scenarios
Basic Industrial Complex Build-Out
- Low-end: $11,790,000
- High-end: $21,444,000 This includes basic construction, MEP systems, and interior finishes. It is suitable for standard industrial operations with a focus on functionality and cost efficiency. Basic build-outs are ideal for businesses prioritizing operational space over aesthetic or additional features, ensuring essential needs are met within budget constraints. Despite the lower costs, quality should not be compromised as this can lead to higher maintenance costs and operational inefficiencies in the future.
Mid-Range Industrial Complex Build-Out
- Low-end: $21,444,000
- High-end: $33,516,000 This includes mid-range construction, MEP systems, and interior finishes. It is suitable for more advanced industrial operations that require a balance between cost and quality. Mid-range build-outs offer improved aesthetics, better quality materials, and more efficient systems, making them suitable for businesses that require both functionality and a professional appearance. These complexes can attract higher-end clients and tenants, providing a better return on investment.
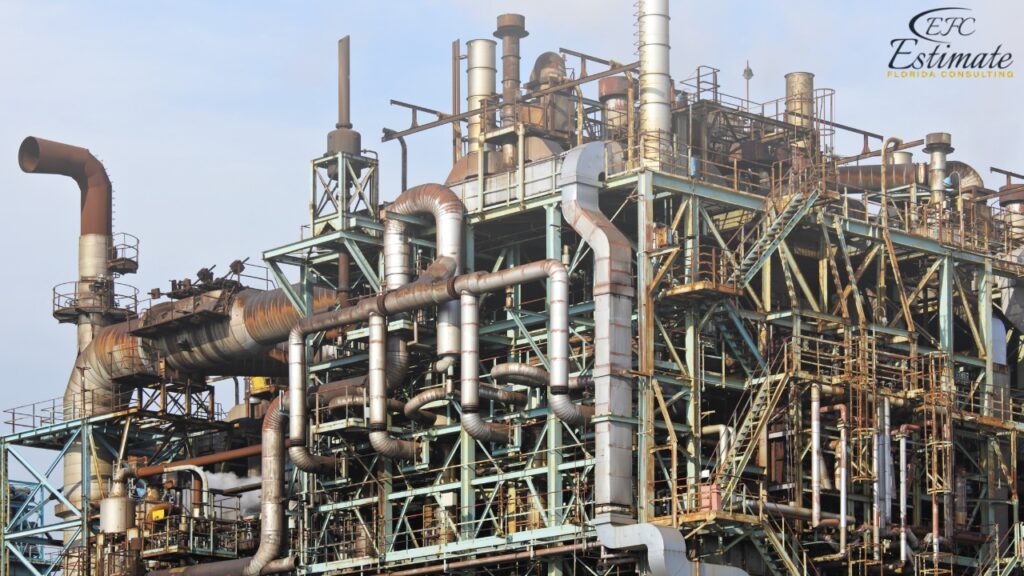
High-End Industrial Complex Build-Out:
- Low-end: $33,516,000
- High-end: $45,084,000 This includes high-end construction, luxury interior finishes, and top-of-the-line MEP systems. It is suitable for high-tech industrial operations requiring advanced systems and high-quality finishes. High-end build-outs are designed for businesses that prioritize advanced technology, superior environmental controls, and a high standard of employee comfort and productivity. These complexes are likely to attract high-profile tenants and provide long-term value due to their durability and state-of-the-art features.
Additional Considerations
Maintenance and Operational Costs
Ongoing maintenance and operational costs are crucial for the complex’s success. Regular maintenance ensures the longevity of the complex’s infrastructure and equipment. Operational costs include utilities, staff salaries, security, and supplies. Proper budgeting for these ongoing expenses ensures smooth operations and helps in planning for long-term sustainability. Establishing a comprehensive maintenance schedule and investing in preventive measures can significantly reduce the risk of costly breakdowns and service interruptions. Additionally, investing in advanced security systems and robust IT infrastructure can protect the complex from physical and cyber threats.
Maintenance Type | Estimated Annual Cost (per sq ft) |
Basic Maintenance | $2.40 – $4.80 |
Mid-Range Maintenance | $4.80 – $7.20 |
High-End Maintenance | $7.20 – $9.60 |
Energy Efficiency and Sustainability
Investing in energy-efficient systems can reduce operational costs and have a lower environmental impact. Energy-efficient HVAC, lighting, and machinery can lead to significant savings on utility bills and contribute to a sustainable business model. Additionally, energy-efficient systems may qualify for tax incentives or rebates, further offsetting the initial costs. Implementing green building practices and renewable energy sources, such as solar panels, can further enhance sustainability and reduce the carbon footprint of the industrial complex. Sustainable practices not only benefit the environment but also improve the complex’s marketability and appeal to eco-conscious clients and investors.
Efficiency Level | Estimated Savings (per year) |
Basic | $24,000 – $48,000 |
Intermediate | $48,000 – $96,000 |
Advanced | $96,000 – $144,000 |
Download Template For Industrial Complex Project Breakdown
- Materials list updated to the zip code
- Fast delivery
- Data base of general contractors and sub-contractors
- Local estimators
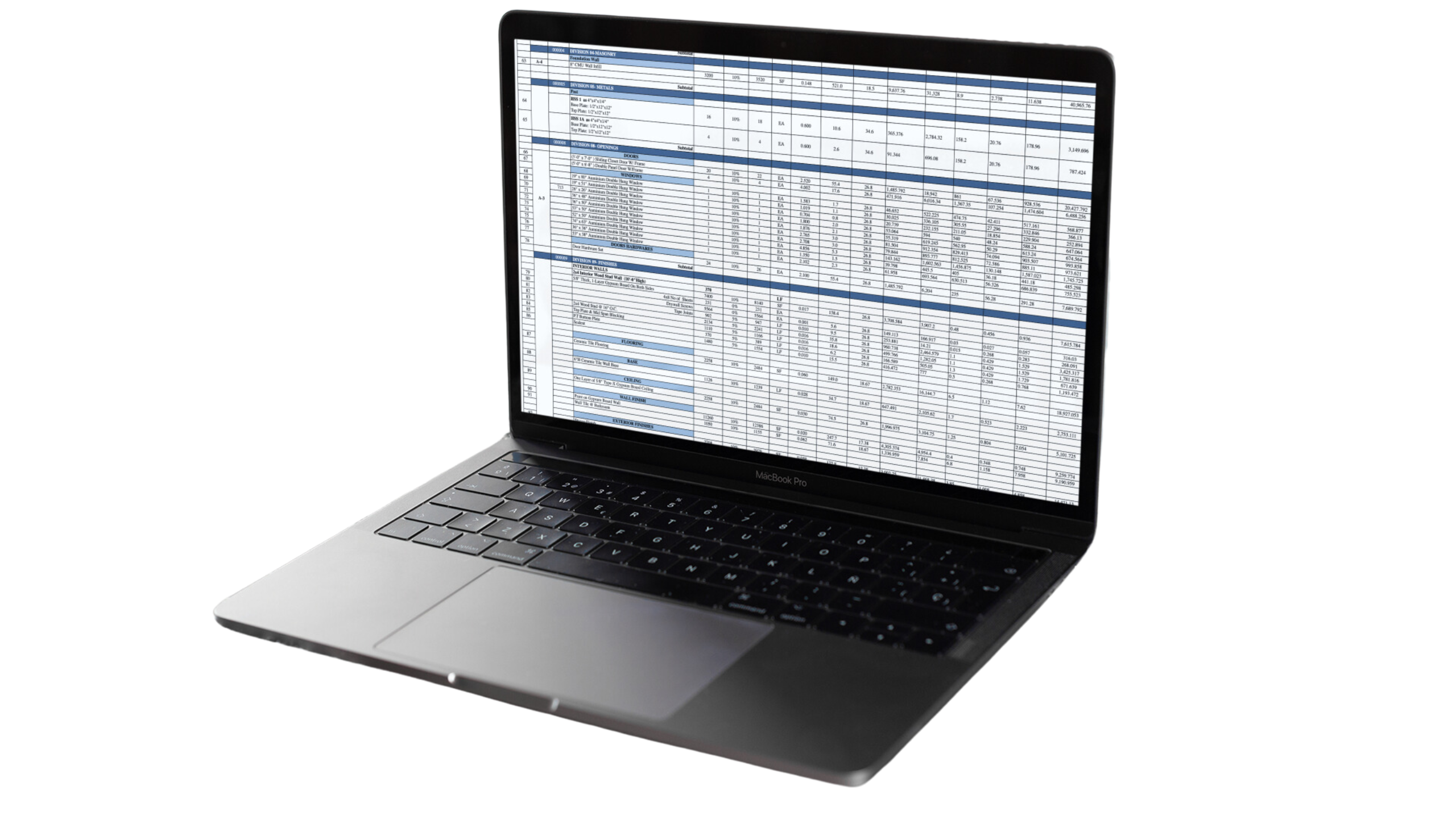
Conclusion
Estimating the costs of building a 40,000 sq ft industrial complex in Palm Beach involves considering various factors, including land acquisition, construction quality, MEP systems, interior finishing, and regulatory fees. By understanding these costs and planning accordingly, investors can develop a realistic budget and strategy for their industrial complex project. Whether opting for a basic, mid-range, or high-end build-out, careful consideration of all cost factors and potential savings from energy-efficient systems is crucial for achieving a successful and sustainable investment. Detailed financial planning, professional consultations, and a clear understanding of the market dynamics in Palm Beach are essential for making informed decisions and ensuring the long-term success of the industrial complex. Maintaining flexibility and staying abreast of industry trends can further enhance the complex’s ability to thrive in a competitive environment.
FAQs
The primary factors include land acquisition, construction costs, mechanical, electrical, and plumbing (MEP) systems, interior finishing and furnishing, and permits and fees. These costs can vary widely based on the quality of materials, design complexity, and specific location within Palm Beach.
The cost of land in Palm Beach varies based on its proximity to transportation hubs and industrial areas:
- Inland: $960,000 – $1,440,000 per acre
- Near Highway: $1,440,000 – $2,400,000 per acre
- Prime Industrial Area: $2,400,000 – $3,840,000 per acre
Construction costs depend on the quality and complexity of the build:
- Basic: $144 – $216 per sq ft
- Mid-Range: $216 – $360 per sq ft
- High-End: $360 – $504 per sq ft
The cost for MEP systems (HVAC, plumbing, electrical) varies by system quality:
- Basic: $28.80 – $57.60 per sq ft
- Mid-Range: $57.60 – $86.40 per sq ft
- High-End: $86.40 – $115.20 per sq ft
Interior costs depend on the quality of finishes and furnishings:
- Basic: $24 – $48 per sq ft
- Mid-Range: $48 – $72 per sq ft
- Luxury: $72 – $120 per sq ft
Permits and fees ensure compliance with regulations and vary by type:
- Building Permit: $36,000 – $72,000
- Environmental Permit: $24,000 – $48,000
- Zoning and Land Use Permits: $18,000 – $36,000
Google Reviews
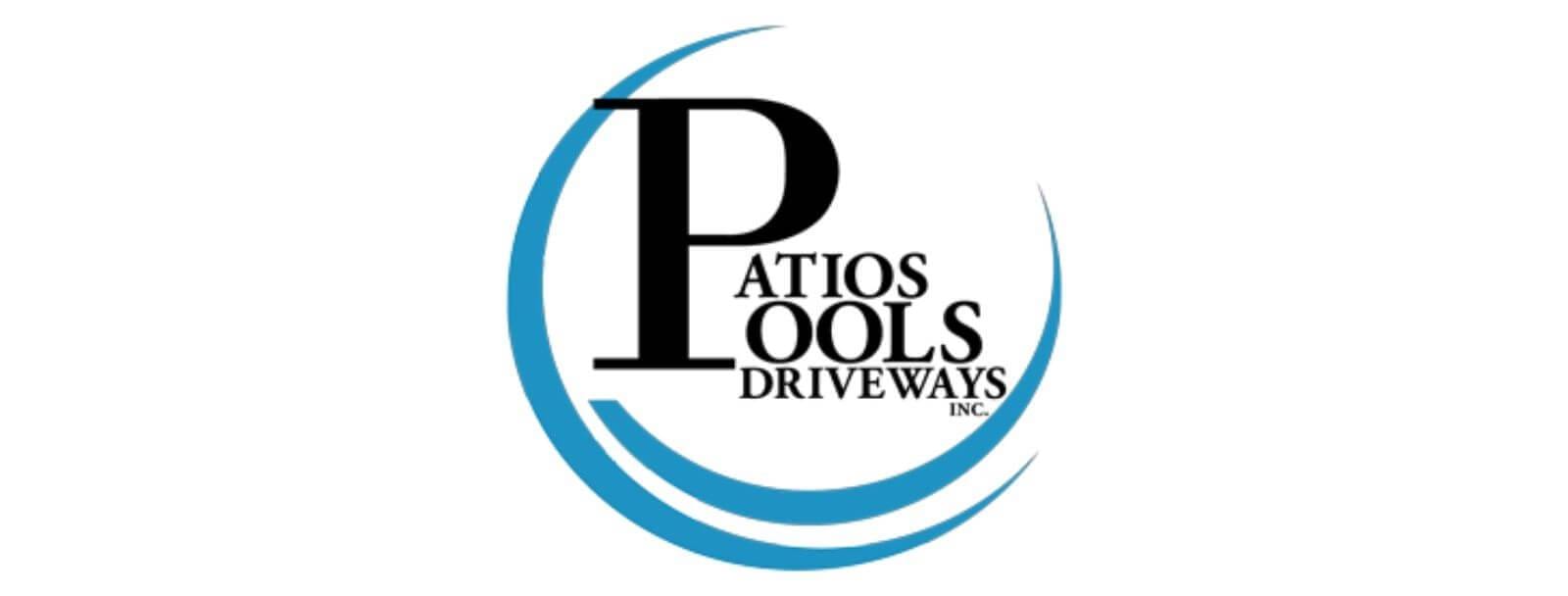
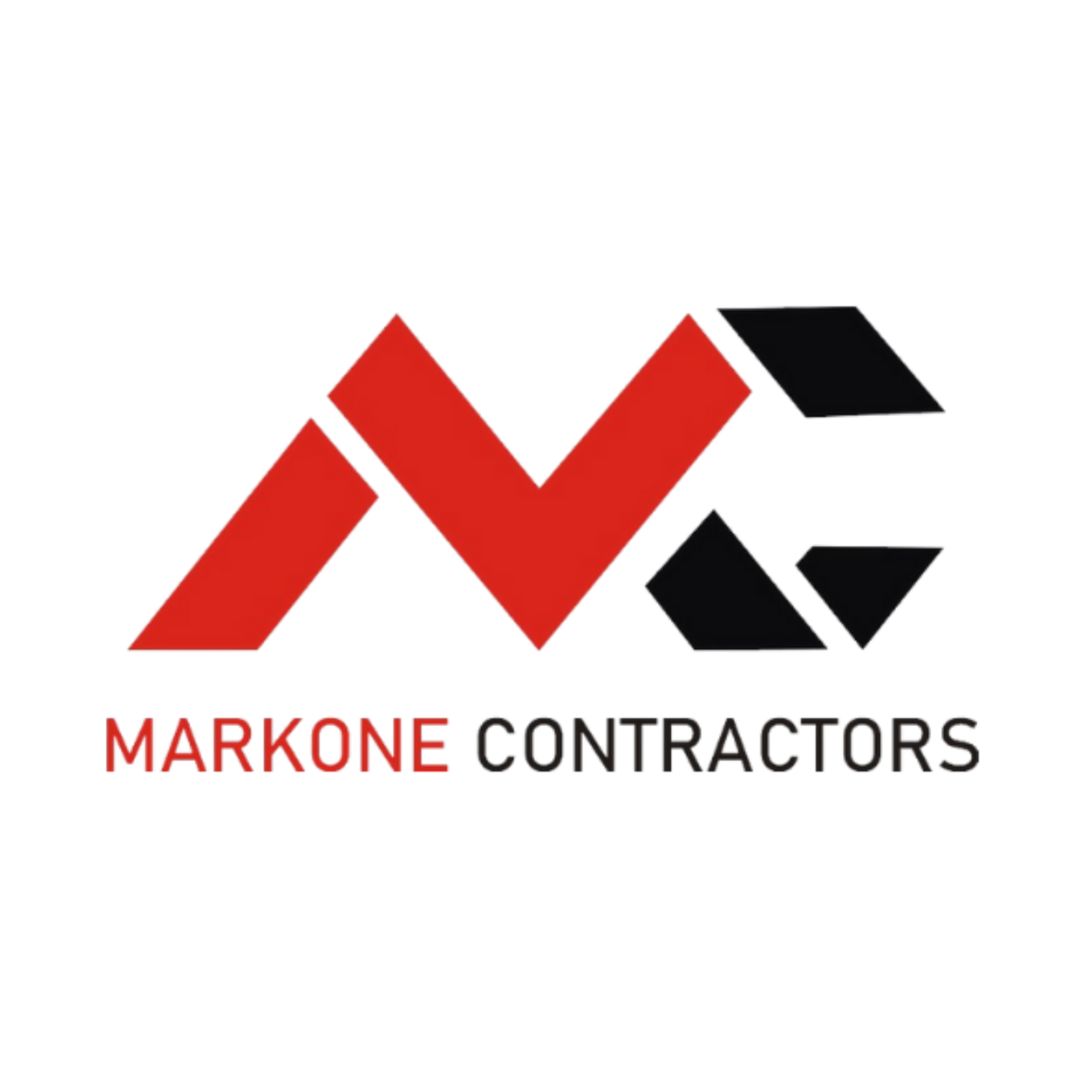

Process To Get A 40,000 sq ft Industrial Complex in Palm Beach Estimate Report
Here I am going to share some steps to get a 40,000 sq ft industrial complex in palm beach estimate report.
-
You need to send your plan to us.
You can send us your plan on info@estimatorflorida.com
-
You receive a quote for your project.
Before starting your project, we send you a quote for your service. That quote will have detailed information about your project. Here you will get information about the size, difficulty, complexity and bid date when determining pricing.
-
Get Estimate Report
Our team will takeoff and estimate your project. When we deliver you’ll receive a PDF and an Excel file of your estimate. We can also offer construction lead generation services for the jobs you’d like to pursue further.