- Homepage
- Blogs
Cost-Saving Solutions for Construction Managers
Leading provider of construction estimating.
Cost management is one of the most critical aspects of construction project management. Construction managers often face the challenge of balancing quality, timelines, and budgets, making cost-saving solutions invaluable. In this guide, we’ll explore strategies to reduce expenses, improve efficiency, and deliver value without compromising on quality. Whether managing large-scale developments or smaller projects, these solutions can be tailored to meet specific needs and maximize profitability.
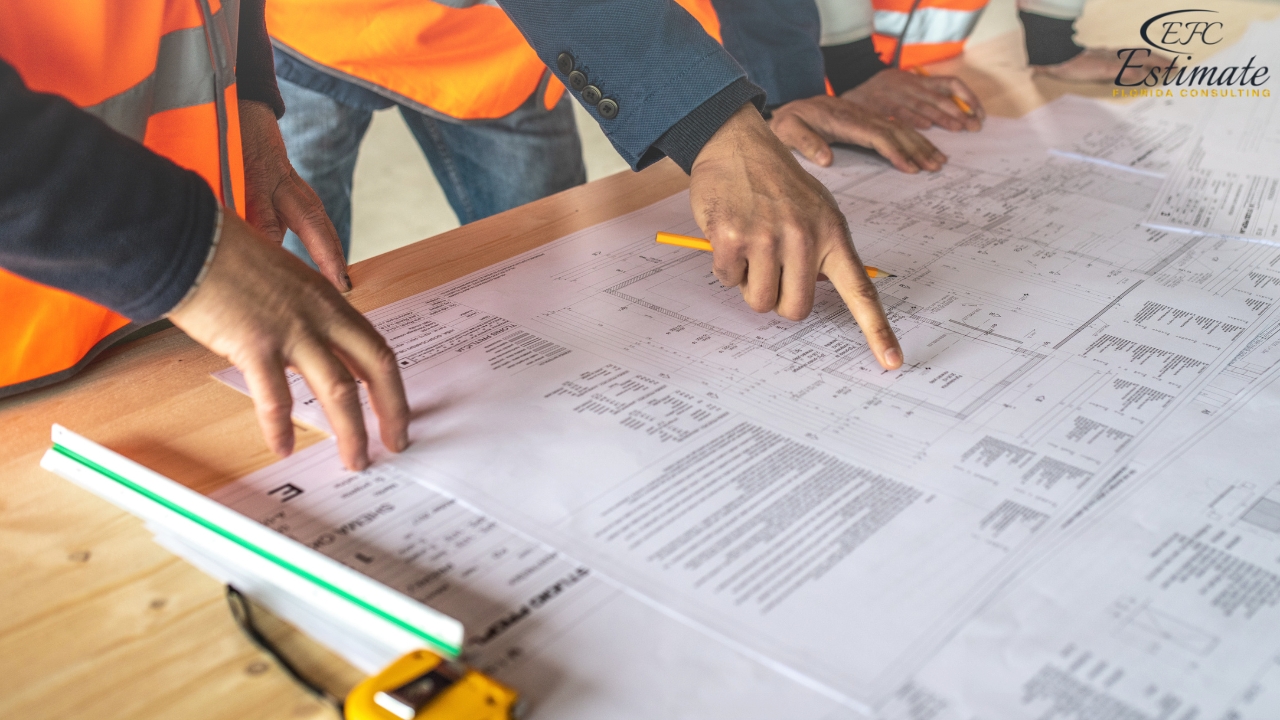
Cost Drivers in Construction
To effectively manage and control costs, construction managers must first understand the primary cost drivers that influence the overall budget. These key factors include:
Labor Costs
Labor costs represent one of the largest expenditures in any construction project. These costs encompass wages for the workforce, overtime pay, and subcontractor fees. Labor rates vary depending on the project’s complexity, location, and the skill level required. Overtime costs can significantly impact the budget if work schedules are delayed, while hiring specialized subcontractors for specific tasks, like electrical or plumbing work, may also add additional expenses.
Material Costs
Material costs are highly variable and can fluctuate significantly based on market conditions, availability, and the quality of materials chosen. Prices for essential building materials, such as steel, concrete, lumber, and glass, can change unexpectedly due to supply chain disruptions, demand spikes, or seasonal factors. Additionally, material wastage during construction can lead to further cost increases, making efficient inventory management and accurate ordering essential for staying within budget.
Equipment Costs
Construction projects often require heavy machinery and specialized equipment, which can be costly to acquire and maintain. Equipment costs include initial purchase or rental fees, maintenance, and operational expenses like fuel and insurance. Renting equipment can be more cost-effective for short-term projects, but long-term projects may justify the purchase of equipment. Regular maintenance is critical to avoid costly downtime, and mismanagement of equipment usage can result in increased operational costs.
Permits and Regulatory Fees
Permits and regulatory fees are essential to ensure compliance with local building codes and regulations. These costs can vary widely depending on the location and scope of the project. Compliance with zoning laws, environmental regulations, and safety standards often requires paying for various permits, inspections, and licensing fees. Failure to account for these costs or delays in securing necessary permits can lead to penalties or project stoppages, which can escalate the overall cost of construction.
Project Delays
Unexpected project delays can disrupt schedules, cause labor inefficiencies, and increase material costs. Delays may arise from weather conditions, supply chain issues, labor strikes, or unforeseen site conditions. These disruptions can lead to increased labor costs due to extended timelines, as well as additional material costs if prices rise during the project. Managing risks and establishing clear contingency plans is essential to minimize the financial impact of delays and keep the project on track.
Pre-Construction Planning for Cost Efficiency
Thorough Budgeting
Creating a detailed and realistic budget is one of the most important steps in pre-construction planning. A well-structured budget should not only cover the known costs but also include contingencies for unexpected issues or risks that may arise during construction. By forecasting potential challenges and including buffers for unforeseen expenses, you can better manage the overall financial health of the project. This proactive approach helps avoid financial surprises and ensures the project stays on track financially.
Value Engineering
Value engineering involves exploring alternative construction methods, materials, and design solutions to achieve the same desired outcomes at a lower cost. This process typically includes evaluating options such as switching to more affordable materials, altering construction techniques, or adjusting the project’s design to be more cost-effective. By focusing on value without compromising the project’s overall quality or functionality, value engineering helps optimize the use of resources and reduce unnecessary expenses, ultimately leading to a more cost-efficient project.
Site Assessments
Comprehensive site assessments are crucial in identifying potential issues that could increase costs down the line. By thoroughly evaluating the site before beginning construction, you can uncover challenges such as poor soil conditions, drainage issues, or difficult access to the construction area. These factors can all lead to increased costs if not addressed early in the planning phase. Conducting detailed surveys, soil tests, and environmental assessments helps mitigate potential surprises and ensures that the project can proceed smoothly with minimal disruptions.
Accurate Scheduling
A well-thought-out construction schedule is essential for minimizing delays and associated costs. By setting realistic timelines and ensuring that all necessary materials and labor are available on time, you can avoid costly delays that may arise from supply chain issues, weather interruptions, or labor shortages. Effective scheduling also helps coordinate different phases of the project, ensuring that all activities run efficiently and resources are utilized optimally. Timely project completion reduces overall costs and helps keep the project on track, preventing budget overruns due to extended labor hours or additional overhead expenses.
Effective Procurement Strategies
Bulk Purchasing
One of the most effective ways to reduce procurement costs is through bulk purchasing. By buying construction materials in large quantities, construction managers can take advantage of volume discounts offered by suppliers. Purchasing in bulk also ensures a steady supply of materials, reducing the risk of delays caused by shortages. However, it’s important to balance bulk purchasing with storage capabilities, as buying large quantities may lead to excess inventory costs if not managed correctly.
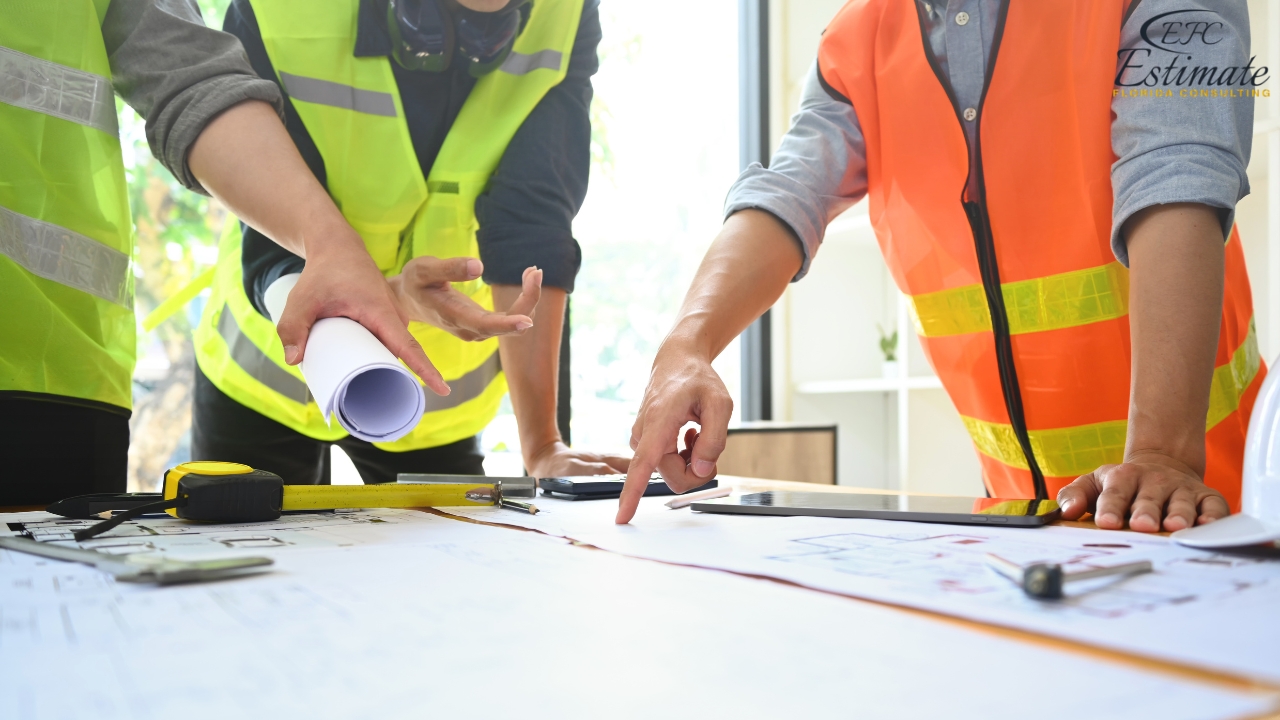
Vendor Relationships
Building strong, long-term relationships with reliable suppliers can also contribute to cost savings. By working closely with trusted vendors, construction managers can often secure better pricing, more favorable payment terms, and priority service. A good vendor relationship can also lead to exclusive offers, early access to new products, or quicker delivery times, which can be crucial in time-sensitive projects. Cultivating open lines of communication and offering loyalty can help strengthen these relationships and maximize procurement efficiency.
Local Sourcing
Local sourcing is another strategy that can help reduce costs. By purchasing materials from local suppliers, construction managers can minimize transportation expenses, which can add up quickly, especially for large or heavy materials. Additionally, local sourcing supports regional economies and can lead to quicker delivery times, further reducing the risk of delays. In some cases, locally sourced materials may also have a lower carbon footprint, aligning with sustainability goals while cutting costs.
Competitive Bidding
Finally, competitive bidding is a proven procurement strategy that ensures the best pricing for materials and services. By soliciting bids from multiple vendors or contractors, construction managers can compare costs and select the most cost-effective option without compromising quality. This approach fosters transparency and encourages vendors to offer their best prices to win the contract. To further enhance the competitive bidding process, construction managers should clearly define project requirements, scope, and timelines to avoid any misunderstandings or hidden costs later on.
Leveraging Technology to Reduce Costs
Building Information Modeling (BIM)
Building Information Modeling (BIM) is a game-changer in construction project management. BIM uses detailed 3D models to visualize the entire building before construction begins, allowing project teams to identify and resolve potential design conflicts early in the process. This proactive approach prevents costly mistakes during construction and minimizes rework, ensuring that the project stays on schedule and within budget. BIM also improves collaboration among architects, engineers, and contractors, making it easier to coordinate efforts and avoid costly delays or misunderstandings. By integrating all aspects of the design into a single digital platform, BIM reduces waste and resource usage, leading to overall cost savings.
Project Management Software
Project management software like Procore and Buildertrend has revolutionized how construction projects are tracked and managed. These tools enable real-time updates on project status, allowing managers to monitor budgets, schedules, and resource allocation more effectively. By centralizing all project data in one platform, these software solutions help eliminate inefficiencies, reduce errors, and improve communication between team members, contractors, and subcontractors. This enhances decision-making and enables construction teams to respond swiftly to any issues, minimizing costly delays and overruns. Project management software also provides valuable analytics and reporting features, helping to forecast potential cost overruns and implement corrective actions in advance.
Drones
Drones are becoming an increasingly common tool in construction projects for tasks such as site surveys, progress monitoring, and inspections. By using drones to capture aerial footage and high-resolution images of construction sites, managers can gain real-time insights into the progress of a project. Drones significantly reduce the need for manual labor for tasks like site inspections, providing accurate data without the safety risks or labor costs associated with traditional surveying methods. They can also monitor large or difficult-to-reach areas more efficiently, speeding up inspections and reducing downtime. Drones improve both the quality of data collected and the speed at which it’s gathered, ultimately reducing overall project costs.
Automation
Automation in construction is becoming more widespread, with automated equipment handling tasks such as concrete pouring, material handling, and even bricklaying. The use of automated machines significantly boosts productivity by performing repetitive and time-consuming tasks with precision and speed. For example, automated concrete pourers and robotic material handlers reduce the labor required, while also minimizing the potential for human error. This leads to a more consistent output, reduced labor costs, and faster project completion times. Additionally, automation reduces the need for manual supervision, freeing up workers for more complex tasks. By integrating automation into daily construction operations, projects can be completed more efficiently, with less waste and lower overall labor costs.
Improving Labor Productivity
Training Programs
Investing in ongoing training programs for workers is one of the most effective ways to boost productivity. Skilled workers are more efficient and make fewer mistakes, leading to fewer delays and rework. By providing continuous education on the latest construction techniques, safety protocols, and equipment handling, you can help workers enhance their capabilities and reduce errors, which ultimately contributes to faster project completion times and lower labor costs.
Efficient Crew Scheduling
Optimizing crew sizes and scheduling can greatly improve labor productivity. Avoiding overstaffing ensures that you don’t waste resources on unnecessary labor, while preventing understaffing ensures that the crew can complete tasks within the required timeline. Properly matching crew members with their skill sets and balancing workloads based on project demands will keep the workforce engaged and productive, reducing idle time and increasing efficiency.
Incentive Programs
Implementing performance-based incentive programs can significantly motivate workers to perform at their best. Offering financial or other tangible rewards for meeting or exceeding productivity targets can encourage employees to work harder and stay focused. Incentive programs can help workers feel more valued and invested in the project’s success, leading to better results and higher-quality work with fewer delays.
On-Site Supervision
Active on-site supervision is essential for maintaining productivity and addressing inefficiencies in real-time. Supervisors should be proactive in monitoring the progress of the project, ensuring that workers have the necessary resources, and identifying any potential bottlenecks. By actively managing the workforce and providing immediate feedback or corrective actions, supervisors can keep the project on track and ensure that tasks are completed as efficiently as possible.
Win More Projects With Us
Optimizing Material Usage
Accurate Material Estimation
One of the most important steps in minimizing material waste is ensuring accurate material estimation. Using advanced software tools or working with professional estimators can help calculate material quantities with high precision. This allows for better planning and prevents over-purchasing, which can lead to excess materials and wasted resources. Proper estimation ensures that only the necessary amount of materials is ordered, reducing the likelihood of surplus and cutting down on unnecessary costs.
Recycling and Reuse
Another way to optimize material usage is by repurposing leftover materials. For example, concrete, wood, or metal that remains from one part of the project can often be reused in other areas of the build, such as for structural components, landscaping, or even temporary supports. Recycling materials not only saves money but also reduces the environmental impact of a project by lowering the need for new resources. Many construction sites are increasingly incorporating sustainable practices like material recycling to support green building certifications and to cut costs.
Just-In-Time Delivery
Implementing a Just-In-Time (JIT) delivery strategy is a crucial aspect of material optimization. By scheduling material deliveries to coincide with specific project timelines, contractors can avoid the cost of storing excess materials on-site. This practice reduces the potential for damage, theft, or spoilage while minimizing the need for storage space, which can be costly. JIT delivery ensures that materials arrive as they are needed, helping to streamline workflow and prevent project delays due to supply chain disruptions.
Sustainable Construction Practices
Energy-Efficient Designs
Incorporating energy-efficient systems and designs can significantly lower long-term utility costs. Features like solar panels, high-performance windows, and insulated walls help minimize energy consumption by improving heat retention and reducing the need for heating and cooling systems. These energy-saving features not only lower electricity bills but also contribute to the building’s overall sustainability. Over time, the initial investment in these energy-efficient designs is offset by the reduction in energy consumption, providing both environmental and financial benefits.
Green Materials
The use of sustainable and eco-friendly materials is another effective way to reduce the environmental footprint of a construction project while saving on costs. Materials like bamboo, reclaimed wood, and recycled steel are renewable, durable, and often less expensive than traditional building materials. Additionally, they can contribute to earning points toward certifications such as LEED (Leadership in Energy and Environmental Design), which can boost a project’s marketability. By choosing green materials, builders can not only reduce the environmental impact but also cut down on the cost of raw materials and labor, as these materials are often easier to source and work with.
LEED Certification
Striving for LEED certification (Leadership in Energy and Environmental Design) is a great way to showcase a building’s sustainability while also unlocking financial incentives. Achieving LEED certification demonstrates a commitment to environmental responsibility, which can attract eco-conscious clients and investors. Furthermore, LEED-certified buildings often qualify for tax incentives, grants, and rebates, reducing overall construction costs. The certification process encourages the use of energy-efficient systems, water-saving technologies, and eco-friendly materials, all of which can contribute to substantial cost savings in the long term. This can help differentiate a project in a competitive market and increase its resale value.
Energy Efficiency in Construction
- Smart HVAC Systems: Installing advanced, energy-efficient HVAC systems is one of the most effective ways to reduce energy consumption. These systems can adjust to the building’s needs by optimizing temperature control based on occupancy and time of day, helping to reduce unnecessary heating and cooling costs. Smart thermostats and zoning systems allow for greater control, which can cut down on energy usage and lower utility bills.
- LED Lighting: Utilizing LED lighting throughout the building can significantly lower electricity consumption. LED lights consume less power and have a much longer lifespan compared to traditional incandescent bulbs, reducing both energy costs and the need for frequent replacements.
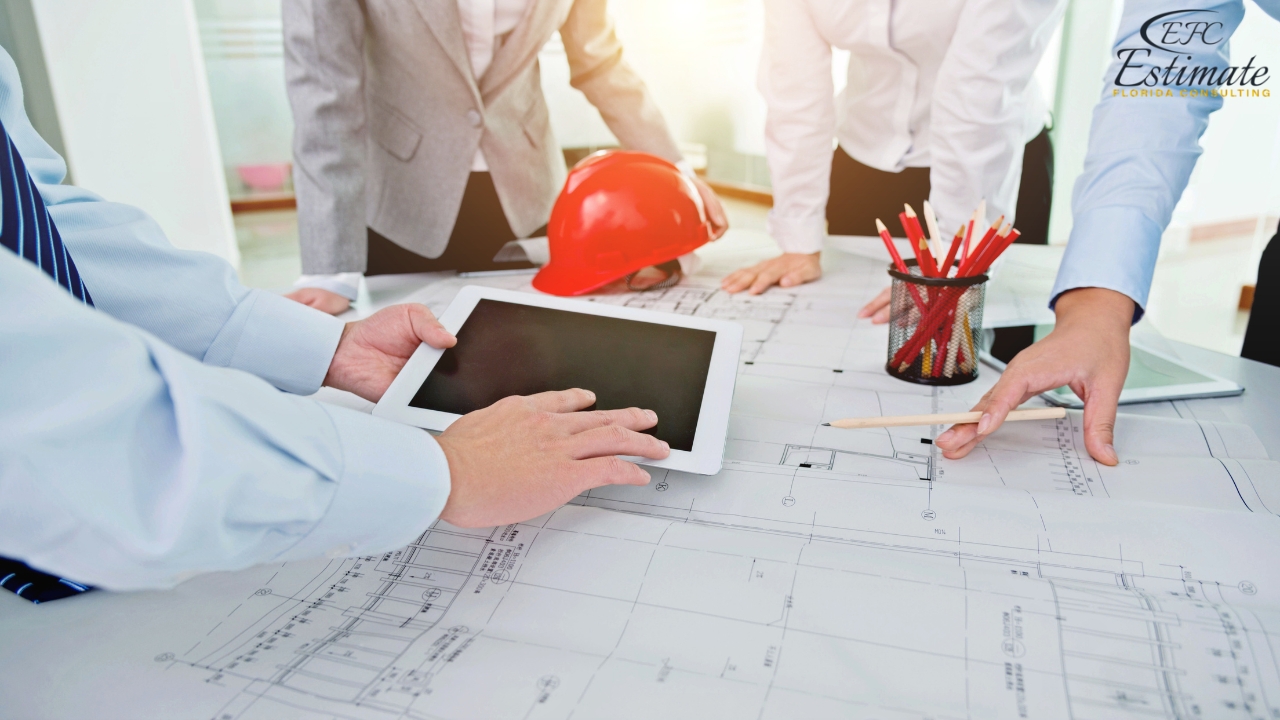
These lights are also available in a variety of designs and applications, making them a versatile and efficient option for both commercial and residential spaces.
- Insulation Upgrades: Proper insulation plays a crucial role in maintaining a comfortable indoor environment while minimizing energy waste. Investing in high-quality insulation, such as spray foam or rigid foam boards, helps to reduce the loss of heat in the winter and keep cool air inside during the summer. This reduces the strain on heating and cooling systems, leading to lower energy bills and a more consistent indoor temperature.
Reducing Construction Waste
Detailed Waste Management Plans
Creating a detailed waste management plan is essential for identifying how materials will be handled, reused, or recycled throughout the construction process. This plan should include clear guidelines on sorting waste, recycling materials, and reducing the amount of waste generated. By organizing waste from the start, contractors can ensure that recyclable materials like metal, wood, and cardboard are separated from non-recyclables, thereby reducing landfill contributions and cutting disposal costs. Additionally, such plans can identify opportunities to repurpose materials within the project, reducing the need for new purchases and further lowering costs.
Prefabrication
Utilizing prefabricated components is a highly effective way to reduce waste on construction sites. Prefabrication involves manufacturing building components, such as walls, floors, and roof sections, in a controlled factory setting before transporting them to the site for assembly. This approach ensures that materials are used more efficiently, reducing on-site waste caused by cutting and trimming. Since prefabricated components are made to precise measurements, the overall waste generated during construction is minimized. Additionally, the time spent on-site is reduced, leading to faster project completion and cost savings.
On-Site Recycling Stations
Setting up dedicated recycling stations on-site can help streamline the waste management process and ensure that materials like wood, metal, concrete, and plastic are properly sorted and recycled. Having designated bins for different materials makes it easier for workers to dispose of waste correctly, reducing contamination and ensuring higher rates of recycling. By separating materials on-site, contractors can reduce disposal costs and may even generate revenue by selling recyclable materials to salvage yards or recycling centers. Implementing such practices also improves sustainability efforts and can contribute to earning green building certifications.
Get Acquainted with Estimation
Maximize Profits: Budgeting Hacks for Big Construction Projects
Estimating Construction Costs in Bad Weather: What You Need to Know?
Cost-Saving Solutions for Specific Construction Phases
Foundation and Excavation
Cost savings during the foundation and excavation phases can be achieved by implementing efficient excavation techniques and optimizing foundation designs. By adopting value-engineered solutions, such as using reinforced concrete or slab foundations in appropriate conditions, contractors can reduce material and labor costs while still maintaining structural integrity. Additionally, employing modern excavation machinery that speeds up the digging process can minimize labor costs and reduce the overall duration of the project.
Framing and Structural Work
In framing and structural work, one of the key strategies for cost reduction is to optimize the use of materials. By accurately calculating the precise lumber and materials required, contractors can avoid overordering and unnecessary waste. Additionally, utilizing prefabricated structural components—such as walls, roofs, and trusses—can help reduce labor costs and improve building speed. These pre-made elements are typically more affordable and quicker to install compared to traditional methods.
Electrical and Plumbing
Electrical and plumbing systems offer significant opportunities for cost-saving without compromising on quality. Opting for energy-efficient electrical systems can reduce both initial installation costs and long-term utility expenses. For plumbing, choosing cost-effective fixtures such as low-flow toilets or water-saving faucets can help keep costs down while meeting environmental standards. Additionally, using modern piping and wiring technologies that are easier and faster to install can reduce labor costs and overall project time.
Finishing Work
In the finishing phase, careful selection of materials can provide cost-effective solutions while maintaining aesthetics. Pre-fabricated cabinetry, for instance, offers both quality and affordability compared to custom-built options. Similarly, engineered wood flooring provides a durable, attractive finish at a fraction of the cost of traditional hardwood. By selecting these cost-efficient options, contractors can achieve a polished look without exceeding the project budget.
Negotiating Better Contracts
Negotiating favorable contracts with suppliers, subcontractors, and clients is a powerful tool for reducing construction costs while maintaining quality and efficiency. Strategic contract negotiations can lead to long-term financial savings.
- Bulk Discounts: One of the most effective ways to reduce material costs is by negotiating bulk discounts with suppliers. By committing to larger orders or establishing a regular supply relationship, you can secure lower prices, which can be passed on as savings for the entire project.
- Flexible Payment Terms: Aligning payment terms with the project’s cash flow can greatly improve liquidity. Negotiating extended payment terms with suppliers or subcontractors can provide more flexibility, ensuring that funds are available when needed without straining finances.
- Long-Term Agreements: Building long-term relationships with reliable vendors can lead to better pricing and priority service. By entering into extended contracts with preferred suppliers or subcontractors, you may benefit from reduced rates, priority delivery, and access to better materials, all contributing to cost efficiency over time.
Using Prefabrication and Modular Construction
Prefabrication and modular construction are becoming increasingly popular due to their ability to lower overall project costs. These methods streamline the construction process, reduce labor demands, and offer numerous benefits for both residential and commercial projects.
- Faster Timelines: Prefabricated components can be manufactured in a controlled environment off-site and then quickly assembled on-site. This reduces the time required for construction, allowing for faster project completion and enabling the use of resources on multiple projects simultaneously.
- Reduced Waste: By producing components in a factory setting, prefabrication minimizes material waste. The controlled environment allows for precise measurements and material use, significantly reducing scrap and the need for excess materials on-site, which lowers material costs.
- Cost Predictability: Modular construction often offers fixed prices for prefabricated units, providing more accurate cost estimates. With fewer variables and faster build times, project budgets become more predictable, reducing the risk of unexpected costs during the construction phase.
Streamlining Project Management Processes
Effective project management is critical to ensuring that construction projects are completed on time and within budget. Streamlining project management processes can help prevent delays, minimize waste, and improve overall project efficiency.
- Integrated Software Solutions: Using project management software that integrates budgeting, scheduling, and resource allocation in real-time can greatly enhance efficiency. These tools allow project managers to track progress, adjust schedules, and ensure that budgets are adhered to, helping avoid costly overruns and delays.
- Clear Communication Channels: Establishing clear and efficient communication between all stakeholders—including contractors, subcontractors, clients, and suppliers—ensures that issues are resolved quickly and decisions are made efficiently. Good communication helps prevent misunderstandings that could lead to costly errors or delays.
- Regular Progress Reviews: Regularly reviewing the progress of the project ensures that any potential issues are identified early and addressed before they become larger problems. By holding consistent progress meetings and reviewing the timeline, budget, and scope of work, project managers can keep everything on track and avoid unforeseen costs.
Download Template For Construction Project Breakdown
- Materials list updated to the zip code
- Fast delivery
- Data base of general contractors and sub-contractors
- Local estimators
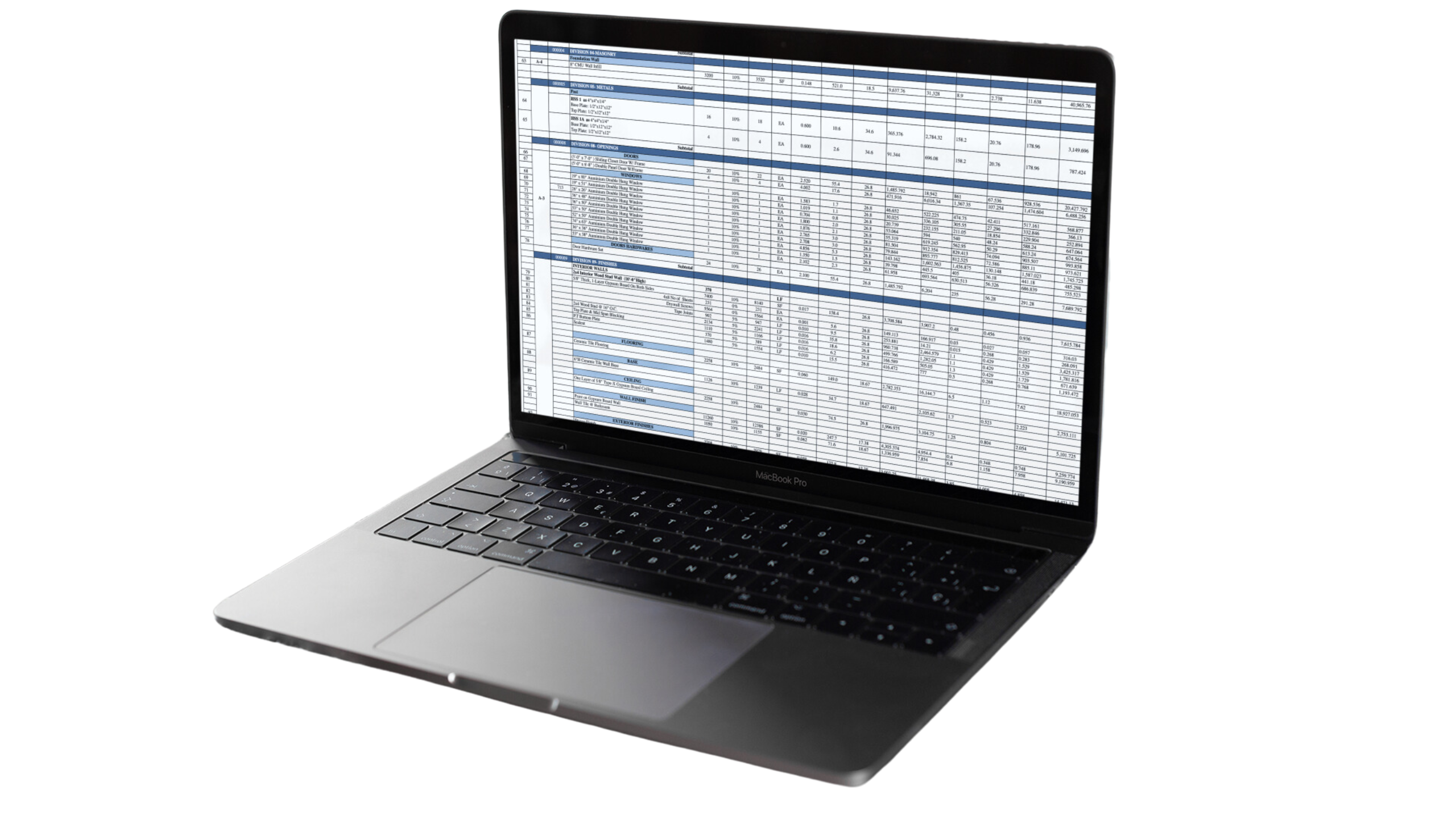
conclusion
Cost-saving strategies are integral to successful construction project management, helping to balance quality, timelines, and budgets. By addressing primary cost drivers, optimizing material usage, leveraging advanced technologies, and adopting sustainable practices, construction managers can achieve efficiency and profitability. Approaches like value engineering, accurate scheduling, and prefabrication not only minimize waste but also streamline operations. Additionally, fostering strong vendor relationships and negotiating favorable contracts can further reduce expenses. By integrating these solutions, construction managers can confidently deliver high-quality projects while maintaining financial stability and competitive advantage in an ever-evolving industry.
Question Answer
Frequently Asked Question
Cost management is essential in construction projects to ensure the budget aligns with project goals without compromising quality. Effective cost management helps in balancing expenses, optimizing resources, and avoiding financial overruns, which can jeopardize the project's success.
The main cost drivers in construction include:
- Labor Costs: Wages, overtime, and subcontractor fees.
- Material Costs: Prices of raw materials and potential wastage.
- Equipment Costs: Purchase, rental, and maintenance expenses.
- Permits and Fees: Regulatory compliance costs.
- Project Delays: Extended timelines leading to increased labor and material costs.
Labor costs can be minimized by:
- Scheduling crews efficiently.
- Investing in training programs to enhance worker productivity.
- Implementing incentive programs to boost performance.
- Using automated tools and machinery to reduce manual labor.
To reduce material costs:
- Bulk Purchasing: Take advantage of volume discounts.
- Local Sourcing: Cut transportation expenses by buying locally.
- Accurate Estimation: Prevent over-ordering and material wastage.
- Recycling and Reuse: Repurpose materials from other projects.
Technology reduces costs by:
- BIM (Building Information Modeling): Resolves design conflicts and minimizes rework.
- Project Management Software: Tracks budgets and schedules effectively.
- Drones: Speeds up inspections and reduces manual labor needs.
- Automation: Boosts efficiency and reduces errors in repetitive tasks.
Value engineering involves evaluating alternative methods, materials, and designs to achieve the same results at a lower cost. For example, switching to cost-effective materials or optimizing designs for efficiency can significantly reduce expenses without sacrificing quality.
Prefabrication saves costs by:
- Reducing waste with precise measurements.
- Speeding up on-site assembly, leading to shorter project timelines.
- Offering predictable pricing for prefabricated components, reducing budget variability.
To minimize delays:
- Develop an accurate project schedule.
- Secure permits and materials in advance.
- Use advanced tools like project management software for tracking progress.
- Establish contingency plans for weather or supply chain disruptions.
- Site Preparation Costs: $6,000–$60,000, depending on size and conditions.
- Material Costs: Make up 40–60% of total costs, with specialized materials costing more.
- Labor Costs: Depend on trade complexity, timelines, and market demand.
- Overhead and Indirect Costs: Include permits, insurance, and administration, typically 10–20% of the budget.
- Contingency Costs: Set aside funds for unexpected challenges, typically 6–18% of the total budget.
Sustainable construction saves costs by:
- Using energy-efficient systems like LED lighting and smart HVACs, reducing utility bills.
- Selecting green materials, which are often cheaper and easier to source.
- Recycling waste materials to lower disposal and new material costs.
Comprehensive Trade-Specific Estimates
At Estimate Florida Consulting, we offer detailed cost estimates across all major trades, ensuring no part of your project is overlooked. From the foundation to the finishing touches, our trade-specific estimates provide you with a complete and accurate breakdown of costs for any type of construction project.
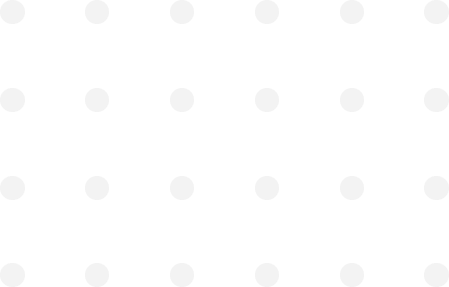
Testimonials
What Our Clients Say
We take pride in delivering accurate, timely, and reliable estimates that help contractors and builders win more projects. Our clients consistently praise our attention to detail, fast turnaround times, and the positive impact our estimates have on their businesses.
Estimate Florida Consulting has helped us win more bids with their fast and accurate estimates. We trust them for every project!
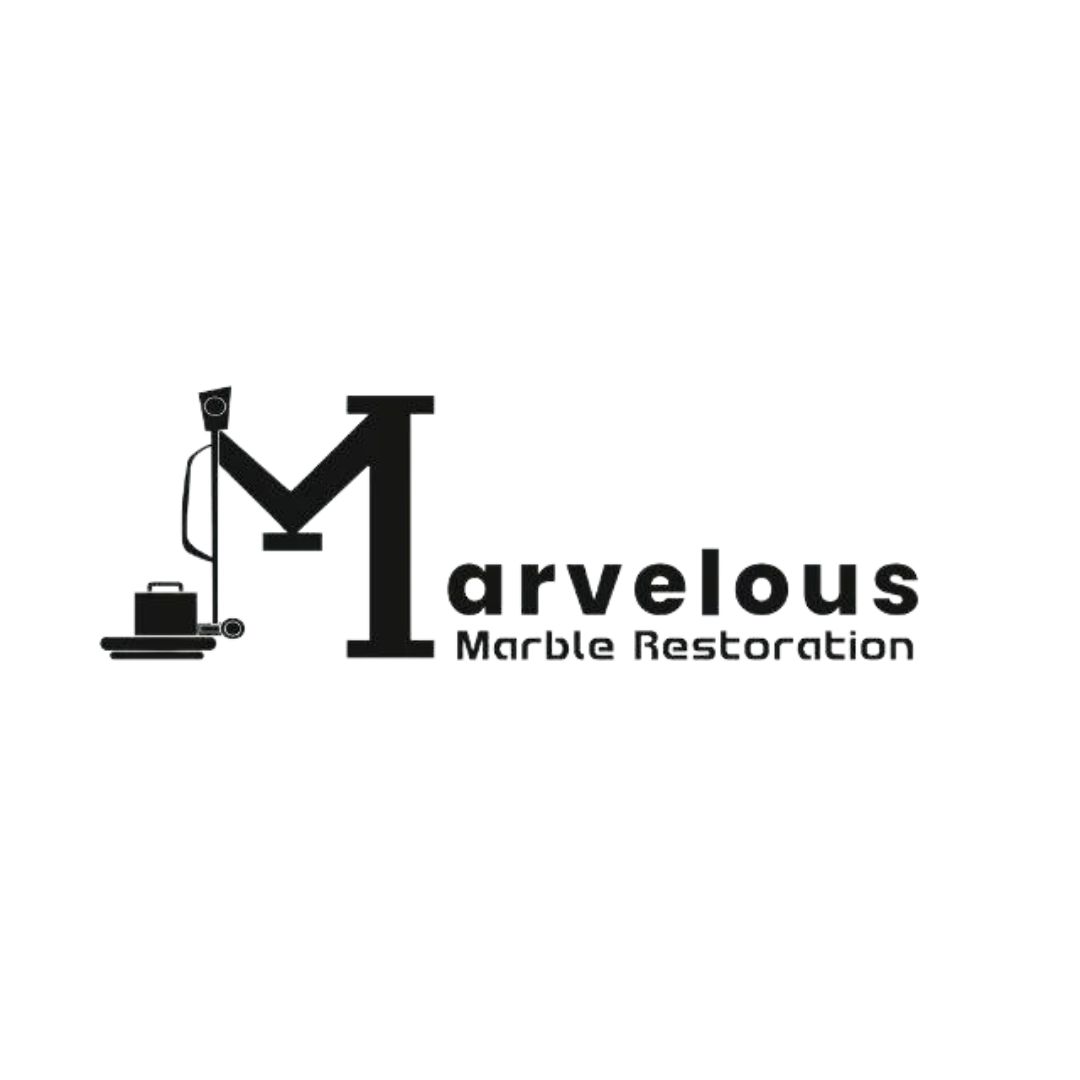
Steps to Follow
Our Simple Process to Get Your Estimate
01
Upload Plans
Submit your project plans, blueprints, or relevant documents through our online form or via email.
02
Receive Quotation
We’ll review your project details and send you a quote based on your scope and requirements.
03
Confirmation
Confirm the details and finalize any adjustments to ensure the estimate meets your project needs.
04
Get Estimate
Receive your detailed, trade-specific estimate within 1-2 business days, ready for your project execution.
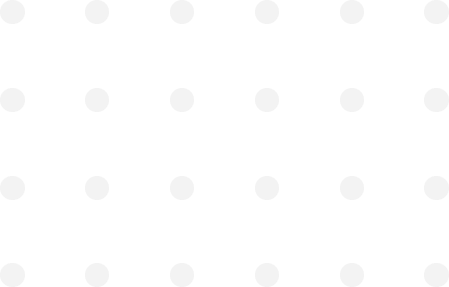