Cost Of Gravel Road
Building a gravel road is not only a practical solution but also a cost-effective one, especially for rural and suburban properties. Gravel roads provide a durable, low-maintenance surface for accessing private properties, driveways, or construction sites. However, understanding the associated costs and factors that influence the overall price is essential for successful project planning. In this guide, we will explore the detailed cost breakdown of building a gravel road, along with key considerations that will help you budget effectively and keep the project within your financial scope.
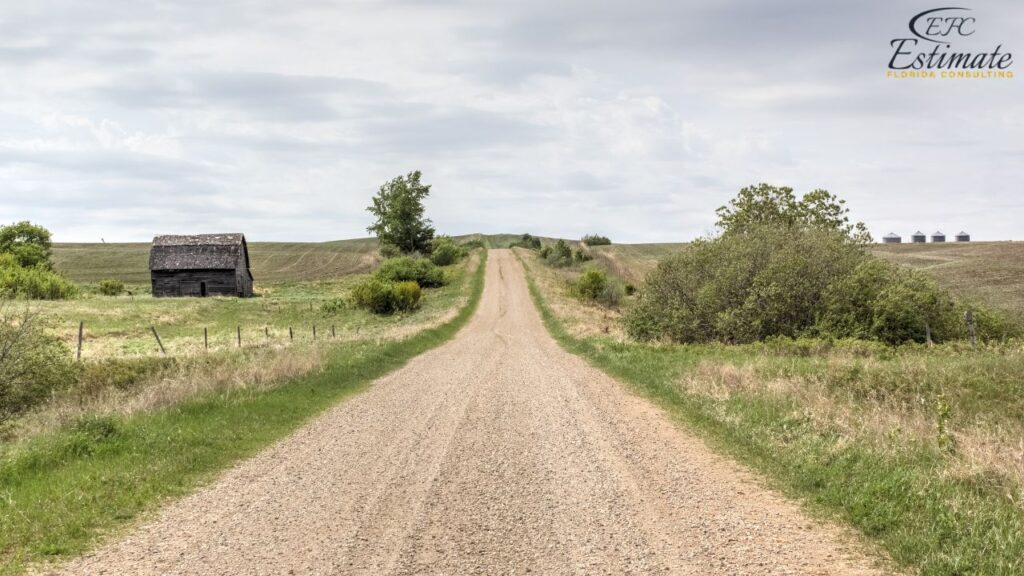
How Much Does It Cost to Build a Gravel Road?
When constructing a gravel road, the typical costs range between $4.80 and $14.40 per linear foot. These costs depend on various factors, including the length, width, and material type. If you’re constructing a longer gravel road, such as a private road leading to your property, the cost will increase proportionally. For a mile-long private road, expect to pay between $25,200 and $78,000, depending on your specific requirements. The cost variation also hinges on factors like the local availability of materials and the complexity of your terrain.
Below is a cost breakdown based on the road width:
Gravel Road Width | Cost per Linear Foot | Cost per Mile |
9 feet | $4.86 – $8.96 | $25,680 – $47,280 |
12 feet | $6.48 – $11.95 | $34,200 – $63,120 |
15 feet | $8.10 – $14.94 | $42,720 – $78,840 |
These figures provide an overall estimate for gravel road construction costs. Keep in mind that several additional factors, such as labor, grading, and permits, can influence the final total.
Factors That Influence Gravel Road Costs
Several factors contribute to the overall cost of constructing a gravel road. From the size of the road to the soil conditions and the type of materials used, these elements can significantly influence the budget. Being aware of these factors will help you make informed decisions and better manage your costs.
Width and Length of the Road:
The dimensions of the road are one of the most significant factors influencing the cost. A wider or longer road requires more materials and labor, which increases the overall price. For example, a 9-foot-wide road typically costs between $4.86 and $8.96 per linear foot, while a 15-foot-wide road may cost between $8.10 and $14.94 per linear foot. The total cost for a mile-long road increases accordingly with its width, which is why choosing the correct dimensions based on your usage is essential. A wider road may be necessary for larger vehicles, but for residential access, a narrower road might suffice and reduce costs.
Depth of the Gravel Layer:
Another critical factor that affects the cost of a gravel road is the depth of the gravel layer. Most gravel roads are constructed with a depth of 12 inches, which typically consists of several layers of different-sized stones and gravel. However, if the soil beneath the road is stable, such as clay or stone, you might be able to reduce the gravel layer to 3 or 4 inches. This reduction can save a significant amount of money, especially for longer roads, without compromising the road’s durability. Keep in mind, however, that reducing the depth may require more frequent maintenance, which could offset initial cost savings.
Material Availability and Quality:
The type and quality of gravel you use are also crucial to the project’s cost. Gravel typically costs between $10 and $50 per ton, depending on the grade, quality, and local availability. For a mile-long road, you could need between 1,500 to 2,500 tons of gravel, which translates to material costs ranging from $15,000 to $125,000. Using locally available gravel can significantly reduce transportation costs, making the project more affordable. However, high-quality gravel, while more expensive, can increase the road’s longevity and reduce future maintenance costs.
Detailed Breakdown of Gravel Road Construction Costs
A thorough understanding of the cost components that make up the total price of constructing a gravel road is essential for accurate budgeting. Below is a detailed breakdown of the various expenses involved in building a gravel road:
Grading and Site Preparation:
Before laying gravel, the site must be graded and prepared to ensure a smooth, stable surface. This process involves leveling the ground and removing any obstacles, such as rocks or vegetation, to create an even foundation for the gravel layers. The cost of grading depends on the length of the road and the condition of the site. For most projects, grading costs range from $500 to $2,500, but the price can increase if significant leveling or soil stabilization is required.
Proper grading is essential for the road’s longevity, as it helps prevent erosion and ensures that the gravel stays in place.
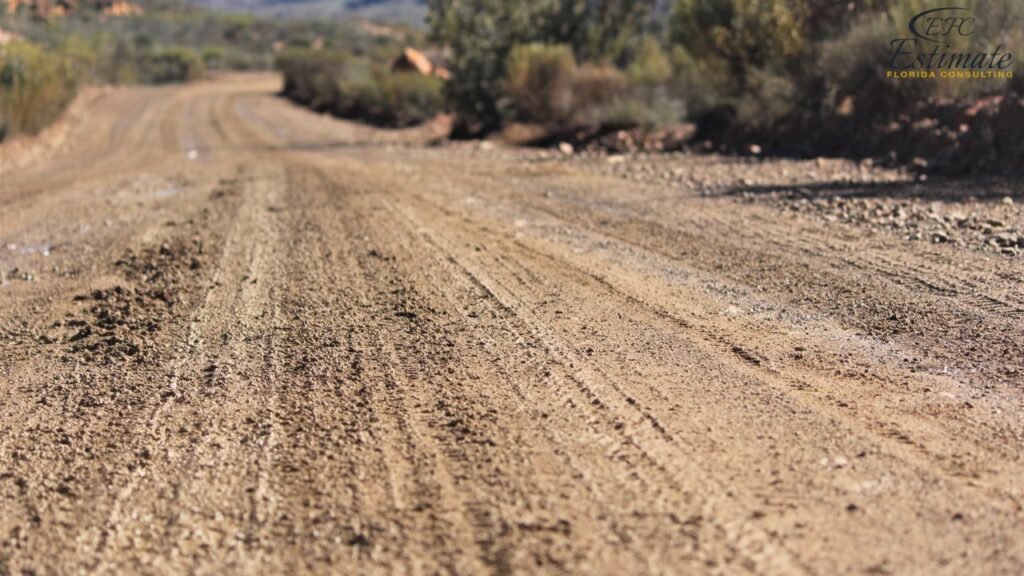
Gravel and Materials:
The gravel itself is a major expense, especially for longer roads. Most gravel road projects require 1 to 2 tons of gravel per 50 feet of road, meaning that for a mile-long road, you may need between 1,500 and 2,500 tons of gravel. The cost of gravel ranges between $10 and $50 per ton, depending on the quality and availability of materials. Using locally sourced gravel can reduce transportation costs, making the project more cost-effective. Additionally, higher-quality gravel may offer better durability, reducing the need for frequent maintenance and repairs.
Labor Costs:
Labor is another significant factor in the overall cost of building a gravel road. The cost of hiring skilled labor to complete the grading, material placement, and drainage installation can range from $2,000 to $15,000, depending on the complexity of the project and regional labor rates. Projects that require specialized equipment or involve challenging terrain may incur higher labor costs. It’s important to get multiple estimates from contractors to ensure you’re getting a fair price for the labor required for your road project.
Drainage Systems:
Proper drainage is essential for preventing erosion and water damage, which can reduce the lifespan of a gravel road. Installing drainage systems, such as culverts or ditches, ensures that water does not accumulate on the road, which can lead to potholes or washouts. The cost of installing drainage systems ranges from $1,000 to $10,000, depending on the length of the road and the complexity of the drainage solution. Investing in good drainage during the initial construction phase can save you from costly repairs down the road.
Permit Costs:
Depending on your location, building a gravel road may require permits, particularly if it connects to public roads or crosses environmentally sensitive areas. Permit fees typically start at $600, but they can vary depending on local regulations and the scope of the project. It’s essential to check with your local planning authorities before starting construction to avoid fines or delays. Securing the proper permits ensures that your road complies with local standards, making it safer and more durable in the long term.
90% More Chances to Win Projects With Our Estimate!
- Multi-Family Building
- Hotel Building
- Hospital Building
- Warehouse Building
- School & University Building
- High-Rise Building
- Shopping Complex
- Data Center Building
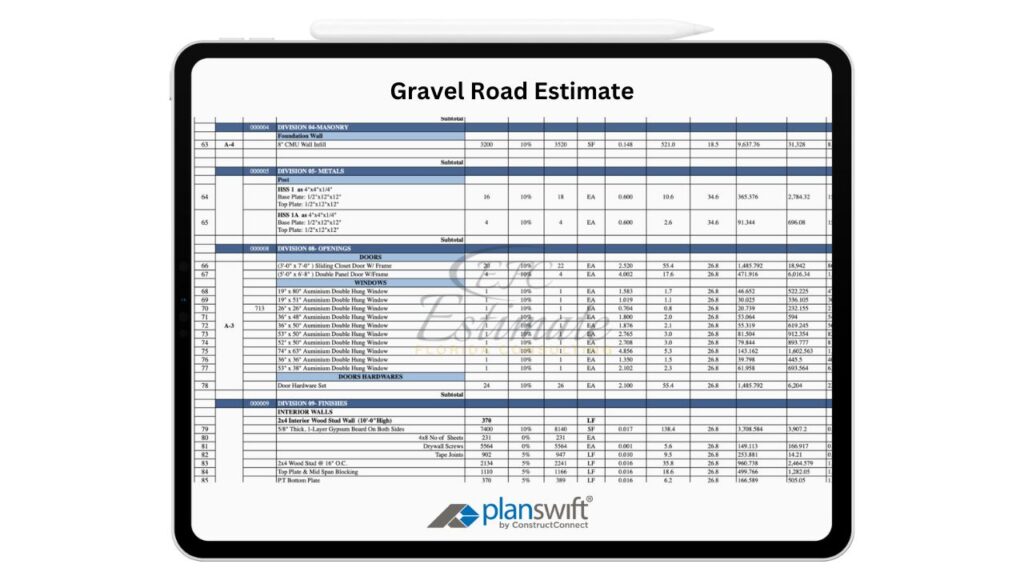
Ideal Width and Depth for a Gravel Road
Choosing the right width and depth for your gravel road is essential for ensuring that it meets your needs while staying within your budget. The width of a gravel road typically ranges from 9 to 15 feet, depending on the types of vehicles that will use it. A 12-foot-wide road is standard for most residential and private driveways, as it provides sufficient space for vehicles to pass without taking up excessive material costs. For commercial or agricultural purposes, wider roads may be necessary to accommodate larger vehicles, but this will also increase the cost.
When it comes to depth, a 12-inch depth is recommended for most gravel roads. This depth typically includes several layers, with larger stones at the bottom and finer gravel at the top. In areas with stable soil conditions, such as clay or rock, the depth can be reduced to 3 or 4 inches to save on material costs. However, reducing the depth may require more frequent maintenance, as a thinner gravel layer may not hold up as well under heavy traffic or inclement weather.
Additional Costs to Consider for Gravel Road Construction
In addition to the primary construction costs, there are several ongoing expenses that you should be aware of when building and maintaining a gravel road. These costs can affect the long-term affordability of the project, so it’s important to account for them in your budget.
Road Maintenance:
Gravel roads require regular maintenance to keep them in good condition. Over time, the surface can become uneven due to traffic, weather conditions, and natural wear. Maintenance tasks include grading the road to smooth out any bumps or ruts, adding fresh gravel, and repairing any potholes or washouts. Annual maintenance costs can range from $500 to $3,000, depending on the length and condition of the road. Regular maintenance is essential for preventing larger, more expensive repairs in the future.
Snow Removal Costs:
In areas that experience heavy snowfall, snow removal is a necessary expense for maintaining access to your property. Snow removal on gravel roads requires specialized equipment to avoid damaging the surface. Costs for snow removal can range from $100 to $500 per event, depending on the length of the road and the amount of snowfall. Budgeting for snow removal is important, especially in regions where frequent snow events are common.
Dust Control:
Gravel roads can generate a significant amount of dust, especially in dry climates or areas with frequent traffic. Dust control measures are necessary to minimize the dust and ensure the road remains functional and safe for users. Applying dust control treatments, such as calcium chloride or other dust suppressants, can help to reduce the dust and improve visibility for drivers. These treatments generally cost between $500 and $2,000 annually for a mile-long road, depending on the frequency of application and the level of dust control required. While dust control is an additional expense, it is essential for maintaining air quality and preventing excessive wear and tear on the road surface.
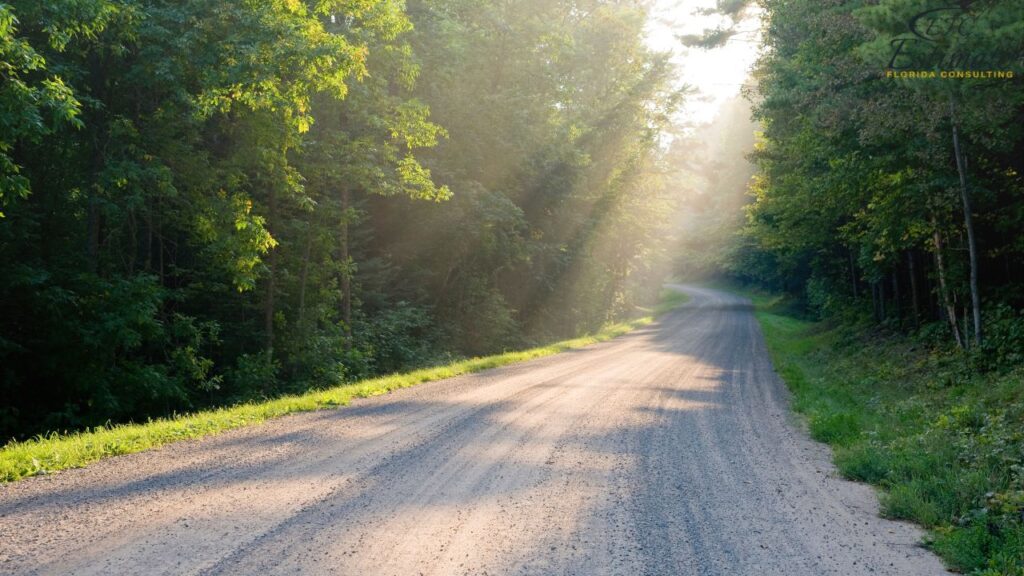
Tips to Reduce Costs When Building a Gravel Road
When constructing a gravel road, there are several strategies you can employ to help reduce the overall costs without sacrificing the quality of the project. Implementing these tips can lead to significant savings, especially for longer roads or more complex projects.
DIY Grading:
If you have access to the necessary equipment, such as a tractor or grader, performing the grading work yourself can save a considerable amount of money. Professional grading services typically cost between $500 and $2,500, depending on the length of the road and the complexity of the terrain. By doing the grading yourself, you can eliminate this expense, but it’s important to ensure that the grading is done correctly to avoid future issues with the road’s stability.
Source Local Materials:
One of the best ways to cut costs is by sourcing gravel from local suppliers. Transporting gravel over long distances can significantly increase the cost of materials due to shipping fees. By using locally available gravel, you can reduce transportation costs and ensure that the material is well-suited to the local environment. Additionally, locally sourced materials are often more affordable and readily available, making it easier to stay within your budget.
Plan for Proper Drainage:
Although installing drainage systems can add to the upfront cost of your project, it’s a wise investment that can save you money in the long term. Proper drainage prevents water from accumulating on the road, reducing the risk of erosion and washouts. By planning for adequate drainage during the initial construction phase, you can avoid expensive repairs down the road. Installing culverts or ditches may increase the project’s initial cost by $1,000 to $10,000, but it’s an investment that will pay off over time by prolonging the life of the road.
Get Acquainted with Road Construction
Permit Requirements and Legal Considerations for Gravel Roads
Before beginning construction on your gravel road, it’s crucial to check with local authorities regarding permit requirements and legal regulations. In many areas, building a road, especially if it connects to a public roadway or crosses environmentally sensitive areas, requires a permit. The cost of obtaining a permit typically starts at $600, but it may vary depending on the location, the size of the road, and the potential environmental impact. Failing to secure the necessary permits can result in fines, project delays, or even the need to modify or remove parts of the road. Ensuring that you comply with local regulations not only avoids legal issues but also ensures that your road meets safety and environmental standards.
Ideal Width and Depth for a Gravel Road
When deciding on the appropriate width and depth for your gravel road, it’s important to consider the types of vehicles that will use the road and the traffic volume it will handle. The width of a gravel road typically ranges from 9 to 15 feet, with 12 feet being a common choice for residential driveways and private roads. This width provides enough space for most vehicles to pass without taking up too much material or increasing costs unnecessarily. However, if the road will be used by larger vehicles or heavy machinery, such as farm equipment or delivery trucks, a wider road may be necessary to accommodate their size.
The depth of the gravel layers is another crucial consideration for the road’s durability. A standard depth of 12 inches is recommended for most gravel roads, as it provides a stable foundation that can withstand regular use. This depth includes multiple layers, with larger stones at the base and finer gravel on the surface. In areas with stable soil, such as clay or stone, the gravel depth can be reduced to 3 or 4 inches, which can significantly lower material costs. However, reducing the depth may result in more frequent maintenance and repairs, so it’s important to strike a balance between cost savings and the road’s long-term durability.
Long-Term Considerations for Gravel Road Maintenance
Once your gravel road is constructed, it’s essential to maintain it properly to ensure its longevity and functionality. Regular maintenance tasks, such as grading, adding fresh gravel, and repairing potholes or washouts, are necessary to keep the road in good condition. Without proper maintenance, a gravel road can deteriorate quickly, leading to costly repairs and reduced usability.
Annual maintenance costs for a gravel road typically range from $500 to $3,000, depending on the road’s length and condition. Regular grading is particularly important, as it helps to smooth out any bumps or ruts that may develop over time. Adding fresh gravel as needed also helps to maintain the road’s surface and prevent erosion. Neglecting regular maintenance can lead to more significant issues, such as water pooling, erosion, and damage to the roadbed, which can be more expensive to fix in the long run.
In areas with harsh winters, snow removal is another important consideration for gravel road maintenance. Snow can accumulate on gravel roads, making them impassable without proper snow removal equipment. Depending on the region and the amount of snowfall, snow removal costs can range from $100 to $500 per event. Budgeting for snow removal is crucial for ensuring that the road remains accessible during the winter months.
How Estimate Florida Consulting Helps with Gravel Road Cost Estimates?
At Estimate Florida Consulting, we provide comprehensive cost estimation services for gravel road construction projects. Whether you’re planning to build a new gravel road or upgrade an existing one, we deliver precise and detailed cost estimates that take into account all aspects of the project. With our experience in handling infrastructure and road construction estimates, we help contractors and developers manage their budgets, reduce unforeseen expenses, and streamline their planning process. Our cost estimation service ensures that you have a complete understanding of the costs involved, from materials to labor.
1. Accurate Material Estimates
Gravel roads require a significant amount of materials, such as gravel, base layers, and geotextiles, to ensure durability and longevity. At Estimate Florida Consulting, we calculate the exact quantities of gravel and other necessary materials, ensuring that you don’t over- or under-order.
This level of precision helps you avoid unnecessary costs and ensures the project progresses without material shortages. We provide detailed breakdowns of the types and amounts of gravel needed for different road sections, factoring in traffic loads, drainage needs, and environmental conditions.
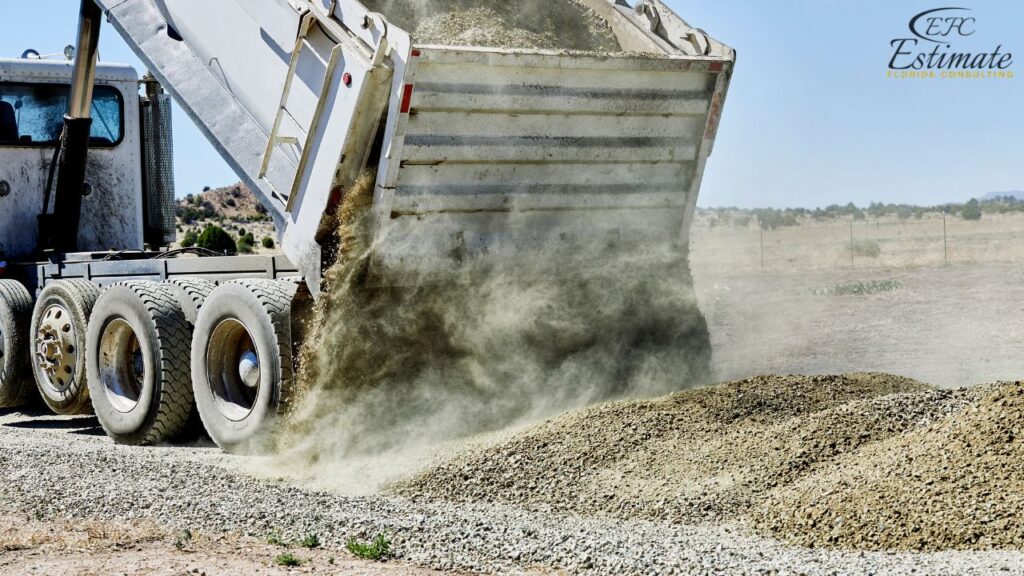
2. Labor Cost Estimation
Labor is a major factor in gravel road construction, and accurate labor estimates are crucial for staying on budget. Our team analyzes the scope of work, including excavation, grading, compacting, and spreading gravel, to provide you with a comprehensive labor cost estimate. We ensure that the estimate reflects local labor rates, equipment needs, and project complexity. By offering precise labor cost predictions, we help you allocate resources efficiently and avoid cost overruns due to underestimating workforce needs.
3. Equipment and Machinery Costs
Gravel road construction often involves heavy machinery, including graders, compactors, and loaders, which can drive up project costs. We include a detailed breakdown of the equipment and machinery costs in our estimates, ensuring you know exactly what equipment is needed and how much it will cost to rent or operate. Our estimates account for the time each piece of machinery will be in use, helping you plan your budget more accurately and avoid unexpected rental or operational costs.
4. Site Preparation and Drainage Considerations
Site preparation is a critical component of any gravel road project, as proper grading and drainage installation are essential for road longevity. At Estimate Florida Consulting, we factor in the costs associated with site clearing, grading, and the installation of drainage systems to ensure your road is durable and functional. Our estimates include everything from excavation costs to the installation of culverts and ditches, providing a complete picture of the site preparation costs involved in your gravel road project.
5. Maintenance and Long-Term Costs
While initial construction costs are important, ongoing maintenance costs for gravel roads must also be considered. We help you estimate the long-term maintenance costs, including periodic regrading, gravel replenishment, and drainage system upkeep. Understanding these long-term expenses allows you to plan ahead and ensure the gravel road remains in good condition over time, ultimately saving you money by preventing costly repairs down the road.
6. Tailored Estimates for Project Size and Scope
Gravel road construction projects vary in size and scope, and our estimation services are tailored to meet the specific requirements of your project. Whether you’re constructing a short driveway or a long rural access road, we customize our estimates to reflect the unique challenges and needs of your project. Our team ensures that every aspect of the project is thoroughly assessed, so you receive an estimate that is accurate and comprehensive, giving you the confidence to move forward with your project.
Download Template For Gravel Road Project Breakdown
- Materials list updated to the zip code
- Fast delivery
- Data base of general contractors and sub-contractors
- Local estimators
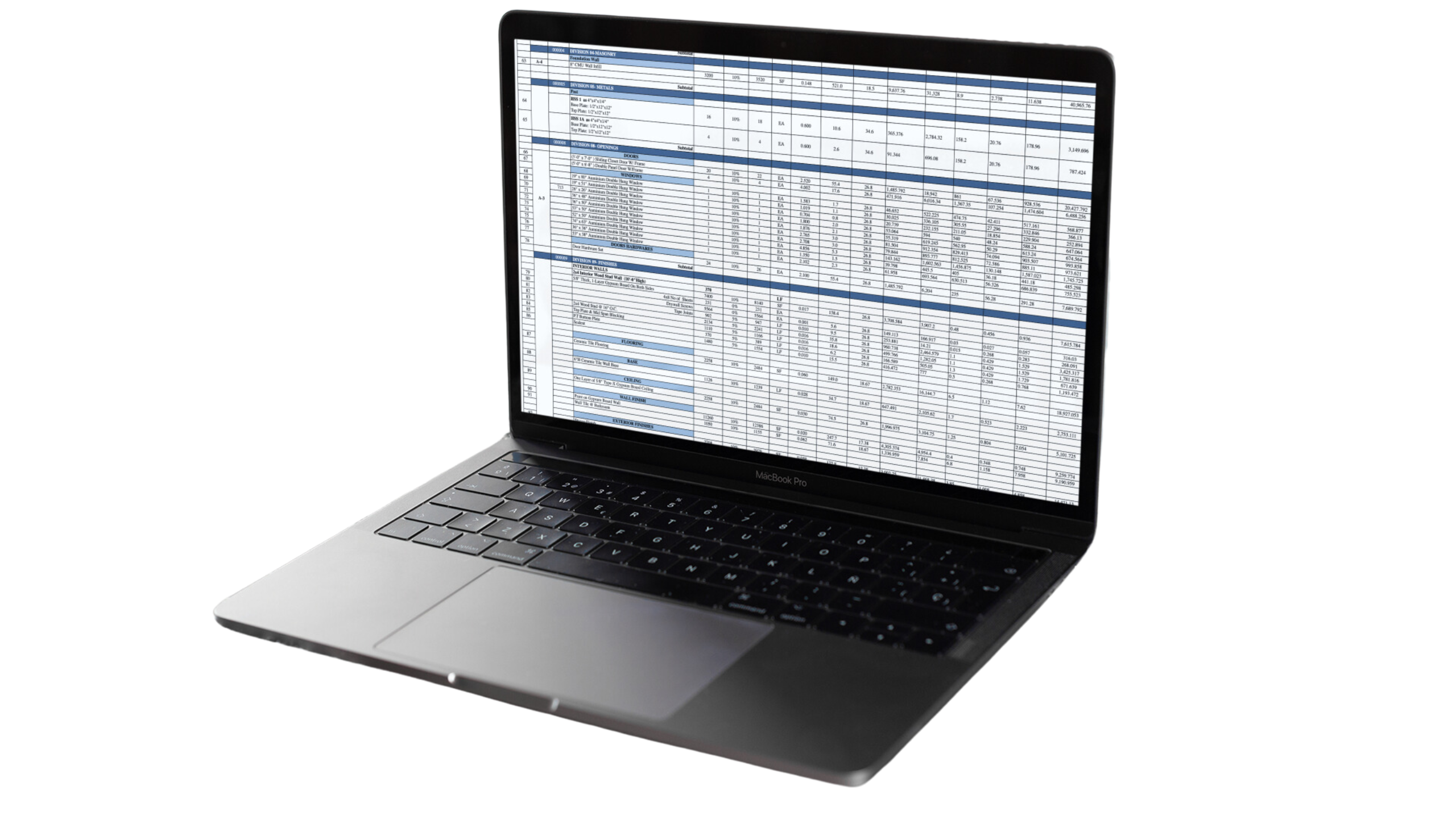
Conclusion
Building a gravel road is a practical and cost-effective solution for providing access to private properties, rural areas, or construction sites. However, the total cost of constructing a gravel road can vary widely, depending on factors such as the width, depth, materials used, and the complexity of the terrain. On average, you can expect to pay between $4.80 and $14.40 per linear foot, with a mile-long road costing between $25,200 and $78,000. In addition to the primary construction costs, you’ll also need to budget for ongoing maintenance, drainage systems, permits, and potential snow removal.
FAQs
To calculate road gravel, measure the road’s length, width, and desired depth in feet. Multiply these dimensions to get the cubic feet, then divide by 27 to convert to cubic yards, the standard unit for gravel.
Gravel driveways have several disadvantages, including frequent maintenance due to shifting or spreading gravel, susceptibility to ruts and potholes, difficulty in snow removal, potential for weed growth, and reduced durability compared to paved surfaces.
A well-maintained gravel driveway can last between 10 to 20 years, depending on factors such as traffic, weather conditions, and regular upkeep, including replenishing gravel, grading, and addressing any ruts or potholes that may develop.
A gravel driveway should typically be 4 to 6 inches deep for standard use. For heavier vehicles or high-traffic areas, a depth of 8 to 12 inches may be recommended to ensure stability and durability.
Mansions often have gravel driveways for their aesthetic appeal, offering a classic, elegant look. Gravel is also cost-effective, provides good drainage, and creates a distinctive sound when driven on, adding to the sense of grandeur and exclusivity.
Google Reviews
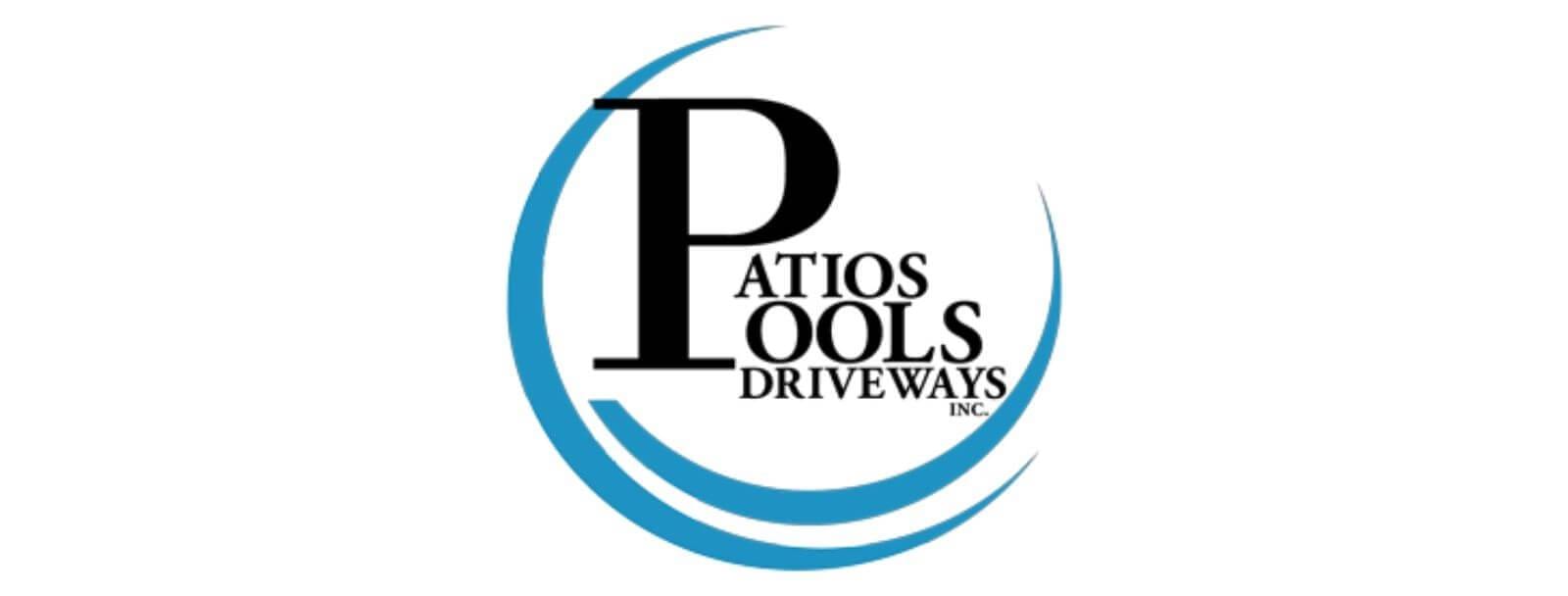
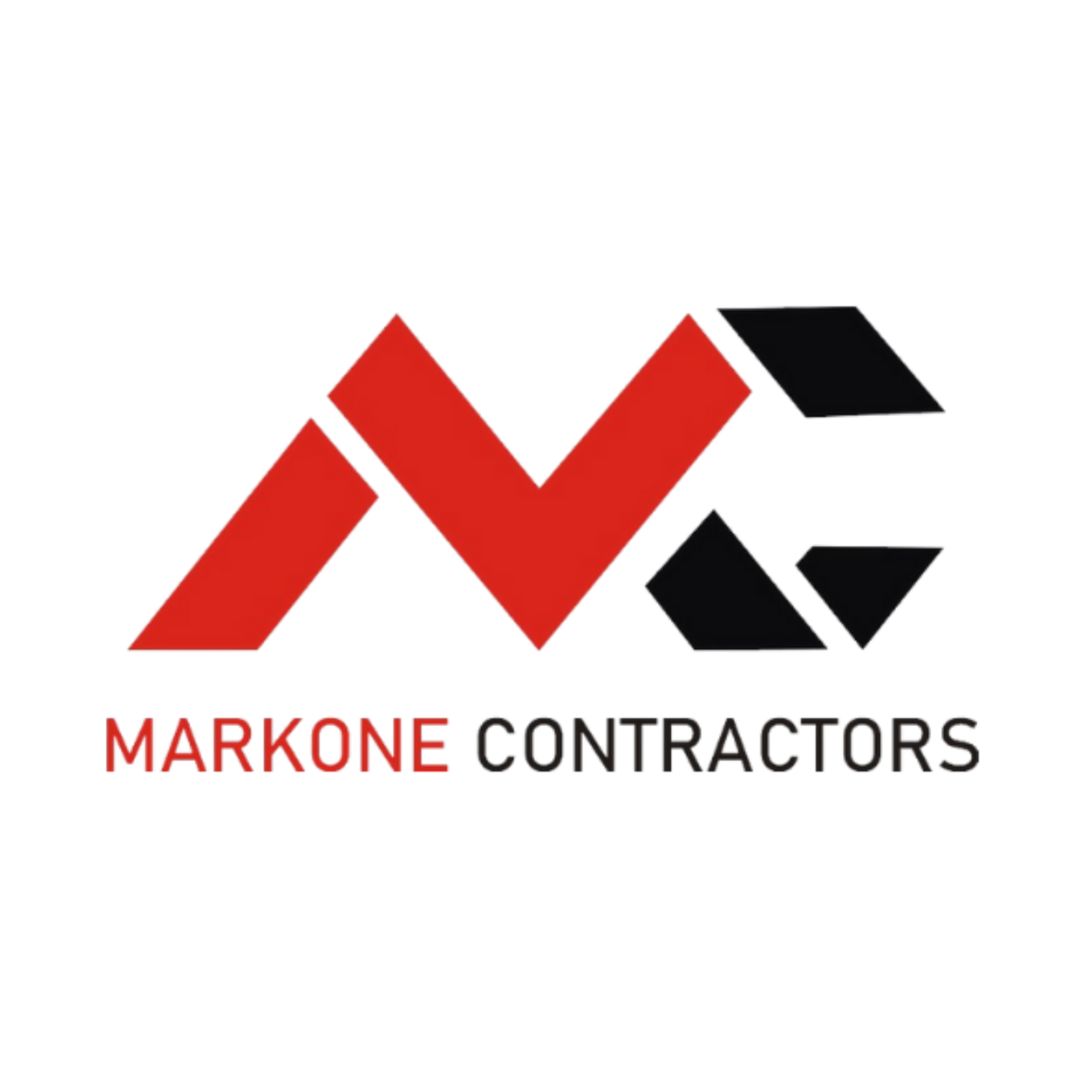

Process To Get Gravel Road Estimate Report
Here I am going to share some steps to get gravel road estimate report.
-
You need to send your plan to us.
You can send us your plan on info@estimatorflorida.com
-
You receive a quote for your project.
Before starting your project, we send you a quote for your service. That quote will have detailed information about your project. Here you will get information about the size, difficulty, complexity and bid date when determining pricing.
-
Get Estimate Report
Our team will takeoff and estimate your project. When we deliver you’ll receive a PDF and an Excel file of your estimate. We can also offer construction lead generation services for the jobs you’d like to pursue further.