A Wining Cost Estimate
That Helps You To Win More Concrete Construction Projects
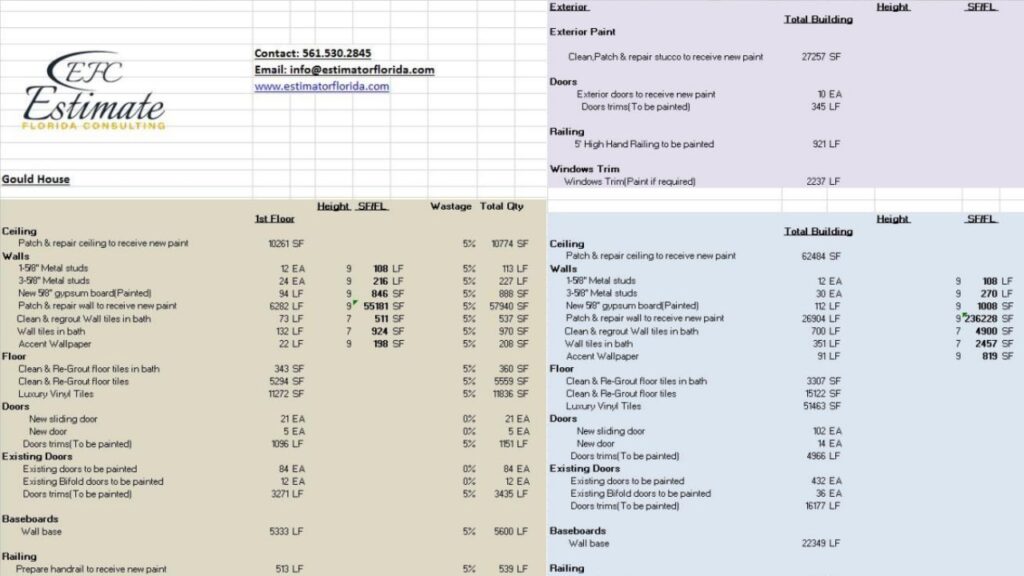
For a complete knowledge of the parts and costs for a commercial concrete job, it is important to look into the details of the concrete cost breakdown. This breakdown involves many factors that add up to the final cost, such as materials, labor, equipment and extra costs that may come up.
A table below shows the different components of a commercial concrete job and their related costs:
Component | Cost |
---|---|
Materials | $X |
Labor | $Y |
Equipment | $Z |
Additional Expenses | $W |
These costs can vary depending on such things as location, the type of project and market rates.
Moreover, more costs may be incurred during construction. These include hauling fees, rental for equipment or machinery, subcontractor fees, permits, insurance, taxes and much more.
Pro Tip: To make sure the cost estimation for a commercial concrete job is accurate, get detailed quotes from multiple contractors before making the final choice.
Warning: Checking out the cost breakdown for materials may cause shock and a sudden wish to become a minimalist.
To break down the cost of materials in your commercial project efficiently, we’re discussing the ‘Cost of Materials’ section in ‘Concrete Cost Breakdown.’ Cement cost, Aggregate cost, Water cost, and Additives cost will be explored in the following sub-sections as a solution to grasp the essential components accurately.
Cost of Cement – the expenses related to procuring cement. Here’s a table showing the precise cost in USD per metric tonne for different types of cement:
Type of Cement | Cost Per Metric Tonne (USD) |
---|---|
Portland | 78 |
Masonry | 65 |
White | 125 |
Besides these costs, there could be additional charges like transportation and handling fees.
It’s important to get high-quality cement for a durable construction. An experienced contractor can help you pick the right one as per your choice.
I once saw a project where the contractor picked cheap, low-quality cement. It caused frequent repairs and maintenance in the future, turning out to be expensive. Planning and quality control at every stage of construction is essential to finish it within budget and meet quality standards.
Aggregate cost? More like aggravate cost – because that’s exactly what it does to your wallet!
To determine the total cost of materials, we calculate the Aggregate Expenditure. This includes purchase price, transportation fees, storage charges, insurance costs and more.
See the table below for the Aggregate Costs:
S.No. | Expense Type |
---|---|
1 | Purchase Price |
2 | Transportation |
3 | Storage |
4 | Insurance |
Note: Unique expenses may differ based on project size and location. A thorough analysis is needed for the correct calculation.
For an accurate estimation, identify and document every step in the process. You can avoid mistakes and miscalculations.
One way to minimize cost is to take advantage of bulk discounts available from suppliers or manufacturers. Bulk purchases can reduce unit prices significantly, resulting in a lower Total Aggregate Cost.
Bottling tears is a suggestion to save money on water costs.
We help contractors find new customers with high-converting websites and locally targeted niche-specific lead-generation programs. You’ll never need to worry about running out of work again! We focus on quality over quantity with our leads for contractors.
Handling the Expense of Water Consumption
When examining the cost of a project, water consumption must be addressed. It can greatly impact the overall cost, even in projects that don’t seem to need much water.
Water prices are not the same throughout the year. They vary based on region, season, and other factors.
When managing a project with lots of water usage, it’s essential to keep an eye on the timeline. Monitor your water bill each month, as changes can be costly. An alternative is to capture rainwater, which is a money-saver in areas with seasonal rainfall.
Lowering water consumption isn’t only about saving money, but also being eco-friendly. Projects that show a commitment to resource management are often more successful than those that don’t in today’s economy.
Additives may make your product sparkle, but they’ll also make your wallet bark.
The cost of materials can include the cost of additives or adding extras expense. This includes the price of any additional substances added to the primary material. The cost of these additives varies based on the type and quantity of additives.
It is important to note that the initial costs for certain intricate materials can be lowered. This is done by reducing upkeep expenses and creating longer-lasting end products.
Our manufacturer once used a low-cost additive for a batch. This resulted in poor quality goods. They realized their mistake and returned to their trusted high-quality additive provider. This resulted in a major improvement in product standards that impressed our clients.
Watching the labor cost go up and down can give you a workout – no need for a gym membership!
To understand the cost of labor in commercial projects, the two main sub-sections you need to focus on are skilled labor cost and unskilled labor cost. Each type of labor functions differently and incurs different expenses. This section will offer insights into these two types of labor costs, helping you understand better how labor cost breakdown plays an important role in the total cost of your commercial project.
Skilled Artisan Expense – Wow!
The skilled artisan expense is the cost of hiring and keeping specialized staff for tasks requiring special expertise. Here’s a table with actual data from different countries in various sectors:
Country | Sector | Hourly Rate (USD) |
USA | Construction | 50 |
Japan | Automotive Manufacturing | 30 |
Australia | Creative Designing | 70 |
Apart from the hourly rates, companies must consider health insurance, pension plans and vacation time when calculating the total cost of skilled labor. The demand for specialized skills increases these expenses.
To manage skilled artisan costs, companies can use initiatives like offshoring, automation, employee training programs, and strategic outsourcing. For instance, investing in tech automation or hiring interns and apprentices can reduce expenses.
Why pay for a personal trainer when you can get the same burn in muscles and wallet after a day of unskilled labor?
Unskilled labor is usually cheaper than skilled labor, due to its abundance in the job market. Wages vary depending on factors such as location, industry, job type, and experience level. These workers are essential to many industries like construction, agriculture, and manufacturing.
Plus, costs can include worker’s compensation insurance and payroll taxes paid by employers. Minimum wage in the US ranges from $7.25-$15 per hour. Low-skilled jobs may pay less than skilled ones, but they still offer valuable opportunities.
Moreover, Pew Research Center (2016) says that over 80% of American adults are concerned with increasing income inequality. Statista (2021) reports the median hourly wage for General Laborers in the US was $14.53 in May 2020. So why break your back when you can break your bank? It may be wise to just hire a team of strongmen instead of buying equipment.
To understand the cost of equipment involved in a commercial project, we present the section on ‘Cost of Equipment’ in ‘Concrete Cost Breakdown’. This section will highlight the two sub-sections on ‘Heavy Equipment Cost’ and ‘Small Equipment Cost’ as solutions for a clearer picture of the budget involved in a commercial project.
Getting and keeping heavy equipment is a major investment for companies that need machinery for building or industrial work. To see Heavy Equipment Cost better, let’s analyze the data.
Each machine has its own cost. Maintenance costs can differ by year, depending on the use time and the total life of the machine. Investing in Heavy Equipment requires extensive financial planning and awareness of the different costs linked to buying and using special machines.
Forbes says “The average expense of having and operating heavy equipment ranges from $96 an hour for light-duty snowplows to $399 an hour or more for specialized machines.” It’s vital to consider all the elements that bring up these costs before settling on a new heavy machine.
Don’t ignore the cost of smaller equipment – those little expenses can add up quicker than a kid with a new credit card.
Small Equipment Investment – Learn the Costs and Benefits!
When considering small equipment investment, there are several things to keep in mind:
Maximize your concrete construction business’s potential with our competitive financing options
To understand the cost of transportation in your commercial project, it is essential to comprehend the expenses you will encounter along the way. In order to keep an accurate concrete cost breakdown, you need to factor in transportation-related expenses such as shipping cost and delivery cost.
The expenditure on moving goods from one place to another is called the “Cost of Transportation“. Let’s see the details.
Mode of Trans. | Avg. Cost/Mile($) |
Road | 3.00 |
Railroad | 1.50 |
Airplane | 10.00 |
Ocean Liner | 0.025 |
If time is an important factor, air travel may be the best option even though it has a higher cost per mile than other options. If you are crossing a sea, an ocean liner would be the ideal choice because it has the lowest cost per mile.
Here are some ideas to reduce shipping expenses:
Delivery cost is like a puzzle, you try to fit everything in one truck and hope it all makes it there safe and sound.
The expenses of sending goods from one place to another are known as Shipping Cost. This cost can vary depending on factors like the origin and destination, mode of travel, weight, speed of shipping, and handling charges. Estimating Shipping Costs is critical for any business that moves items, as it affects their income.
Figuring out Shipping Costs precisely can be tricky for companies that manage a lot of shipments. Manual estimates can take up time and cause errors. There are online tools and programs to automate this process, yet they require exact data to provide precise results.
In recent years, Logistics Cost including transportation costs has gone up due to multiple reasons such as changes in fuel prices, increased demand for delivery services, and driver shortage. Planning and optimizing supply chain operations can help reduce these costs while making sure deliveries come on time.
Once, a small business owner was overwhelmed by his rising orders and deliveries. Calculating transportation expenses accurately was hard, and he ended up charging some clients more and others less. To solve this problem, he bought a dependable shipping calculator tool. It calculated the shipping cost with accurate parameters, leading to higher customer satisfaction and better profits.
What do you call the cost of overhead? The price you pay for not having a magical genie!
To better understand the cost of overhead in commercial projects, dive deeper into the details of insurance, permits, inspections, project manager, and administrative staff costs. Each of these sub-sections provides a unique perspective on the various expenses required to complete a commercial project, and how each component impacts the total cost of the project.
Risk Management Expense is the cost of mitigating risk through insurance. It includes premiums for general liability, property and casualty, and professional liability. Premiums vary depending on an organization’s industry. Neglecting to insure carries greater long-term costs. To manage expenses, organizations should review coverage needs, compare quotes, and use risk control services.
Reducing insurance costs is possible by increasing deductibles. However, weigh potential savings against any negative impacts. A yearly review of insurance coverage will guarantee sufficient protection at a fair cost. Plus, permits and inspections might be annoying, but you can use the wait time to catch up on reading!
Discover the transformative power of hiring professional contractors for your project. Unlock a wealth of expertise and experience to ensure success. Get started today and see the difference!
Legal regulations, quality control – they all come with a hefty cost, known as the ‘Cost of Permits and Inspections.’ To help you understand better, we have made a table with a list of all such payments. It covers building permits, electrical inspections, fire department permits, health department licenses and more.
And, it doesn’t stop there. Companies must also bear the burden of acquiring and maintaining bureaucratic formalities. Like annual inspections, and fees for staying compliant with state and federal laws.
One business owner shared their experience with us about having to pay multiple visits to city offices, due to miscommunication from authorities. It took longer than expected and increased their overhead cost greatly. Why pay for just a project manager and admin staff, when you can get a whole circus of overhead costs?
Managing projects requires thought on costs for project management and admin staff. This includes salaries, benefits and other costs. For better grasp of this, we made a table with data on project size. It shows number of project managers, admin staff, salaries (including benefits) and total cost. It helps with budgeting resources efficiently.
Project size and complexity affects the number of staff needed. Smaller projects with less budget may need one manager and no admin staff. But larger, more complex projects need a team of managers and support staff.
Software to streamline work processes and reduce admin tasks’ load is recommended. Automating time-tracking and reporting can save time for more important project aspects. Investing in tech can help teams focus on critical aspects rather than manual work.
The following table shows the data on project size:
Project Size | Project Managers | Admin Staff | Salaries (Including Benefits) | Total Cost |
---|---|---|---|---|
Small | 1 | 0 | $50,000 | $50,000 |
Medium | 2 | 1 | $200,000 | $300,000 |
Large | 5 | 3 | $500,000 | $1,000,000 |
Profit Margin and Contingency Fees are two key cost components. Profit Margin is the amount added to the project cost by the contractor for earning a profit. It varies based on industry standards, market competition, and contractor experience. Contingency Fees are for unforeseen circumstances during a project.
Initially, Profit Margin wasn’t a factor in contracts. But, over time, it has become an integral part of pricing models. Similarly, Contingency Fees weren’t a factor but now it’s a common practice to account for unknowns.
Understanding the cost breakdown of a project is more than just cementing your knowledge!
We’ve listed a breakdown of the cost components that make up a commercial concrete project.
This table offers an overview of the materials, labor, equipment rental, and project management fees that determine the total cost.
By studying each section, clients can figure out ways to cut costs without compromising quality. For example, they can go for cheaper materials or only rent out non-essential equipment.
It’s important to remember that these are average costs for commercial projects. Prices may change depending on different job factors.
Pro Tip: Before starting a concrete project, make sure everyone agrees on the final cost. Get all expenses and potential change orders in writing to prevent any confusion in the future.
The components of a commercial project’s concrete cost breakdown include materials, labor, equipment, formwork, reinforcing steel, concrete additives, concrete placement, and finishing.
The cost of materials includes the cost of concrete, as well as any additives, reinforcing steel, and formwork. This cost is usually calculated by the square footage of the project and the thickness of the slab.
The cost of labor is generally a significant factor in the concrete cost breakdown, as it involves the actual construction and finishing of the slab. Labor costs can vary depending on location, project complexity, and the experience of the workers.
The cost of equipment in a concrete project includes any machinery used in the construction process, such as mixers, bulldozers, and backhoes. This cost can be substantial, especially if specialized equipment is required.
Reinforcing steel is used to strengthen the concrete and prevent it from cracking. Its cost is generally calculated based on the weight of the steel and the complexity of the project, and it is typically a significant portion of the overall concrete cost breakdown.
The cost of finishing the concrete includes any final touches to the surface, such as polishing, staining, or stamping. This cost can vary significantly depending on the chosen finish and the area to be covered.
Here I am going to share some steps to get your concrete construction cost estimate report.
You can send us your plan on info@estimatorflorida.com
Before starting your project, we send you a quote for your service. That quote will have detailed information about your project. Here you will get information about the size, difficulty, complexity and bid date when determining pricing.
We do concrete construction cost estimating and prepare a detailed report for your project. At last, you finalize the report and finish the project.
561-530-2845
info@estimatorflorida.com
Address
5245 Wiles Rd Apt 3-102 St. Pete Beach, FL 33073 United States
561-530-2845
info@estimatorflorida.com
Address
5245 Wiles Rd Apt 3-102 St. Pete Beach, FL 33073 United States
All copyright © Reserved | Designed By V Marketing Media | Disclaimer
IMPORTANT: Make sure the email and cell phone number you enter are correct. We will email and text you a link to get started.
By clicking “I Agree” above you give Estimate Florida Consultin express written consent to deliver or cause to be delivered calls and messages to you by email, telephone, pre-recorded message, autodialer, and text. Message and data rates may apply. You are able to opt-out at any time. You can text STOP to cancel future text messages.