Bid Strong, Bid Smart – Try Our Concrete Column Cost Estimating Service!
- Accurancy
- Efficiency
- Transparency
- Customization
- Time Saving
- Professionalism
- Cost Control
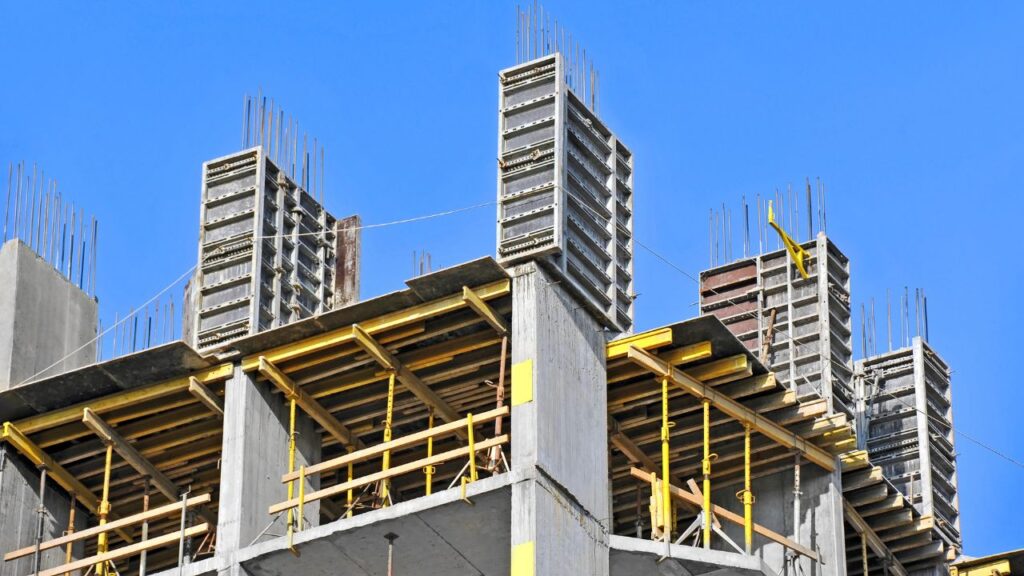
Constructing a hotel structure involves numerous considerations, and among the critical aspects is the cost associated with concrete columns and beams. These structural elements not only provide the essential framework for the building but also contribute significantly to its overall strength, stability, and durability. This article delves into the various factors influencing the costs of concrete columns and beams in hotel construction, offering insights into the key considerations for hotel developers, architects, and project managers.
Concrete columns and beams form the backbone of a hotel structure, supporting the load of floors, walls, and roofs. Their primary function is to distribute the building’s weight efficiently, ensuring stability and preventing structural failure. In hotel construction, where large open spaces, multiple floors, and varied architectural designs are common, the role of these elements becomes even more crucial.
Make Informed Design Decisions Showcase Your Design Ideas
Get RenderingThe intricate dance between architectural and structural design complexity in hotel construction significantly influences the cost dynamics of concrete columns and beams. When architects weave unique designs, intricate patterns, or introduce non-standard shapes into the structural blueprint, a cascade of considerations unfolds. Specialized formwork tailored to these distinctive designs becomes imperative, requiring skilled labor with a nuanced understanding of the complexities involved. These specialized requirements contribute to heightened costs, emphasizing the delicate balance between design aspirations and budget constraints. The quest for architectural uniqueness may necessitate a financial commitment commensurate with the intricacies embedded in the design, guiding developers and project managers in making informed decisions that harmonize aesthetics and cost-effectiveness.
Within the foundational stages of hotel construction lies the fundamental consideration of load-bearing requirements, acting as the cornerstone in the design phase. The load-bearing capacity of a hotel structure serves as a pivotal determinant in the selection of concrete mixes for columns and beams. As load-bearing demands escalate, a consequential shift towards stronger and potentially more expensive concrete mixes becomes inevitable. This strategic decision-making is not merely about meeting structural codes but involves a delicate balance between the required load-bearing prowess and the associated financial investments. Developers navigate this terrain carefully, ensuring that the chosen concrete compositions align with both the structural integrity and budgetary constraints of the hotel project.
The composition of concrete and reinforcing materials emerges as a paramount factor shaping the cost landscape of hotel construction. The type and quality of these materials wield substantial influence, transcending mere construction necessities to become integral components defining structural robustness. Opting for high-strength concrete or specialized mixes may entail a higher price per cubic yard, but the trade-off lies in the enhanced structural performance they deliver.
This nuanced dance between material quality, cost considerations, and structural requirements underscores the importance of meticulous material selection, where every choice becomes a strategic investment in the longevity and resilience of the hotel structure.
The method by which the concrete components come to life in a hotel structure—whether through traditional on-site casting or the utilization of prefabricated or precast elements—plays a pivotal role in shaping cost considerations. The adoption of prefabricated or precast concrete components introduces a different set of cost dynamics compared to the traditional on-site casting approach. While prefabrication may streamline the construction process and potentially reduce labor costs, it brings its own set of considerations, including transportation and assembly logistics. This strategic decision-making in construction methodology becomes a delicate balance between efficiency, cost-effectiveness, and adherence to project timelines, guiding developers in choosing the most suitable path for their specific hotel construction project.
In the realm of hotel construction, the size and scale of the structure stand as defining factors in the cost equation associated with concrete columns and beams. Larger structures, characterized by more floors and expansive footprints, invariably incur higher costs. The correlation between project scale and costs extends beyond material requirements to encompass increased labor demands, extended timelines, and a comprehensive scope that transcends the boundaries of smaller-scale projects. Developers navigating the expansive landscape of large-scale hotel structures recognize the inherent cost implications, prompting meticulous planning and resource allocation to ensure a harmonious alignment between the grandeur of the project and its financial underpinnings.
In the realm of small to medium-sized hotel structures, the financial landscape of concrete columns unveils itself within the range of $180 to $360 per linear foot. This adjusted cost encapsulates the intricacies of material selection, labor, and design considerations, offering a nuanced perspective for developers and project managers. When venturing into the domain of larger hotels with heightened load-bearing demands, the adjusted cost per linear foot may witness an escalation to $360 to $600, embodying the structural demands of these expansive projects. These figures, while providing a foundational understanding, underscore the necessity of considering project-specific nuances, regional market conditions, and other influencing factors for a precise cost estimation.
As we delve into the realm of concrete beams, the cost landscape undergoes a transformative shift, reflecting the intricacies of design and load-bearing capabilities. Basic reinforced concrete beams, fundamental for standard hotel structures, may now fall within the range of $108 to $180 per linear foot. For designs of a more complex nature or those necessitating higher load-bearing capacities, the adjusted cost spectrum expands to $180 to $360 per linear foot, encapsulating the heightened demands.
It is imperative to emphasize that these cost estimates provide a starting point, and the actual costs will be molded by the unique requirements of each project, regional market dynamics, and other contextual factors that shape the cost narrative.
Embarking on a journey of structural optimization requires seamless collaboration with architects and engineers. This involves a comprehensive review and refinement of the design to achieve structural efficiency, strategically minimizing the necessity for excessive columns and beams. By fostering a collaborative environment, the project team can identify opportunities for design enhancements that not only meet performance requirements but also contribute to a more cost-effective structural framework.
This meticulous optimization process, intertwined with the expertise of architects and engineers, lays the foundation for a structurally sound yet economically efficient hotel project.
The selection of construction materials is a pivotal aspect of cost-conscious hotel construction. Striking a delicate balance between performance requirements and cost considerations is essential. Through a meticulous cost-benefit analysis, project stakeholders can discern the most economical options that meet the structural needs of the hotel. This strategic approach to material selection involves considering factors such as durability, load-bearing capacity, and long-term maintenance costs. The result is a judicious choice of construction materials that align with the project’s budget while ensuring optimal structural performance and longevity.
Exploring efficient construction methods stands as a key strategy for minimizing costs associated with columns and beams. Prefabrication, in particular, offers a streamlined installation process that can potentially reduce labor costs. By manufacturing components off-site and assembling them on-site, construction timelines may be expedited, leading to additional cost savings. This approach not only enhances efficiency but also aligns with the broader goal of optimizing the construction process for enhanced economic viability. Efficient construction methods, when thoughtfully integrated into the project plan, contribute to a harmonious balance between structural integrity and cost-effectiveness.
A savvy approach to cost reduction involves the consideration of bulk purchases for construction materials. By leveraging economies of scale, hotel developers can capitalize on discounts and reduce the overall material costs for columns and beams. This entails strategic planning and coordination with suppliers to procure materials in larger quantities. Bulk purchasing not only presents a cost advantage but also ensures a more efficient logistics chain, minimizing delays and disruptions. This approach aligns with a broader cost optimization strategy, where meticulous planning and execution lead to substantial savings in the overall construction budget.
In the realm of hotel construction, managing costs for concrete columns and beams is a nuanced challenge. With costs ranging from $180 to $360 per linear foot for columns and $108 to $180 per linear foot for beams, navigating expenses requires strategic approaches.
Collaborative design optimization, judicious material selection, streamlined construction methods, and bulk purchases emerge as key strategies. These not only enhance structural efficiency but also contribute to a cost-effective construction process. In the dynamic landscape of hotel development, integrating innovation with fiscal responsibility ensures that projects achieve both architectural excellence and financial prudence.
Concrete columns and beams form the structural backbone of a hotel, providing essential support for floors, walls, and roofs. Their primary function is to distribute the building’s weight efficiently, ensuring stability and preventing structural failure.
Unique designs, intricate patterns, or non-standard shapes in architectural and structural design increase costs. Specialized formwork and skilled labor are often required, striking a balance between design aspirations and budget constraints.
The type and quality of concrete and reinforcing materials significantly impact costs. Opting for high-strength or specialized mixes may have a higher price per cubic yard but enhances structural performance.
The method of construction, whether traditional on-site casting or prefabrication, plays a crucial role. Prefabrication may reduce labor costs but introduces different considerations such as transportation and assembly logistics.
Larger hotel structures with more floors and expansive footprints generally incur higher costs due to increased material and labor requirements. Project scale influences the overall scope, demanding meticulous planning and resource allocation.
Strategies include collaborative design optimization, judicious material selection, exploring efficient construction methods like prefabrication, and capitalizing on economies of scale through bulk purchases. These approaches aim to enhance structural efficiency while minimizing costs.
Here I am going to share some steps to get your hotel structures concrete column and beam cost estimate report.
You can send us your plan on info@estimatorflorida.com
Before starting your project, we send you a quote for your service. That quote will have detailed information about your project. Here you will get information about the size, difficulty, complexity and bid date when determining pricing.
Our team will takeoff and estimate your project. When we deliver you’ll receive a PDF and an Excel file of your estimate. We can also offer construction lead generation services for the jobs you’d like to pursue further.
561-530-2845
info@estimatorflorida.com
Address
5245 Wiles Rd Apt 3-102 St. Pete Beach, FL 33073 United States
561-530-2845
info@estimatorflorida.com
Address
5245 Wiles Rd Apt 3-102 St. Pete Beach, FL 33073 United States
All copyright © Reserved | Designed By V Marketing Media | Disclaimer