90% More Chances to Win Projects With Our Estimate!
- Multi-Family Building
- Hotel Building
- Hospital Building
- Warehouse Building
- School & University Building
- High-Rise Building
- Shopping Complex
- Data Center Building
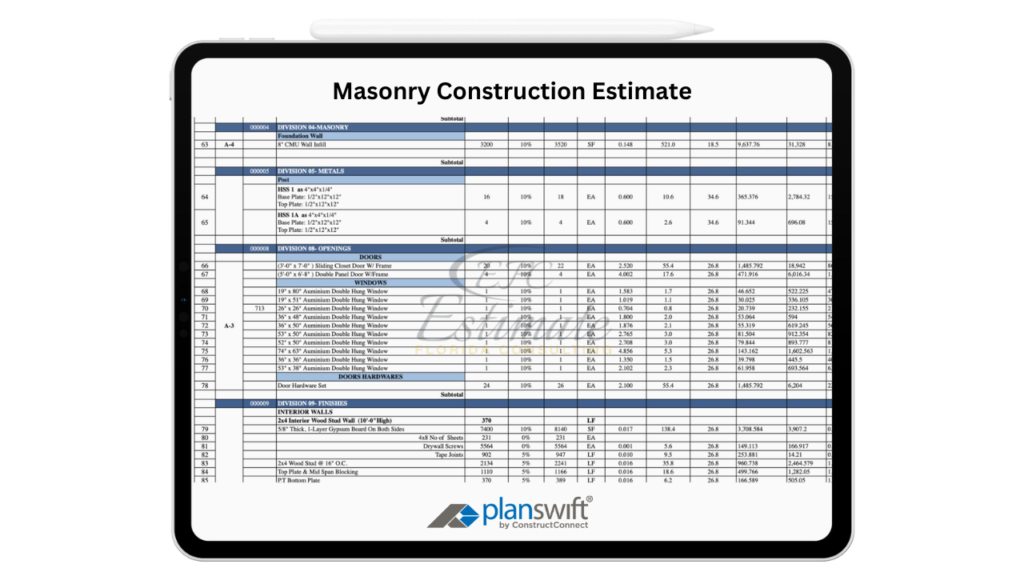
Concrete block masonry is a widely used construction method known for its strength, versatility, and affordability. Comprising concrete blocks, also known as concrete masonry units (CMUs), this method is popular for various applications, including residential, commercial, and industrial buildings. As a sustainable and durable building solution, concrete block masonry allows for efficient construction and design flexibility, making it an appealing choice for many builders and developers.
A detailed breakdown of concrete block masonry costs helps clarify budgeting and financial planning.
The materials cost is a significant component of any concrete block masonry project. Here’s an estimated breakdown of common materials:
Material Type | Estimated Cost per Unit | Estimated Quantity | Total Estimated Cost |
Concrete Blocks | $1.10 – $3.30 | 2,000 units | $2,200 – $6,600 |
Mortar | $10.00 – $15.00 per sack | 50 sacks | $500 – $750 |
Reinforcement (Rebar) | $0.60 – $1.00 per foot | 500 feet | $300 – $500 |
Insulation (if required) | $0.50 – $1.00 per sq ft | 1,000 sq ft | $500 – $1,000 |
Other Materials | Varies (e.g., sealants, finishes) | N/A | $300 – $600 |
Total Estimated Cost | $4,600 – $9,950 |
Estimating materials costs accurately requires careful consideration of design specifications, local pricing, and project needs. Collaborating with suppliers to understand the pricing structure and seeking bulk discounts can significantly impact the overall materials cost. Furthermore, factor in potential waste during construction to ensure that material estimates are sufficient for project completion.
Labor costs, as previously discussed, represent a considerable part of the overall masonry budget. Here’s a summary of estimated labor costs for a typical concrete block masonry project:
Labor Type | Estimated Cost per Hour | Estimated Hours | Total Estimated Cost |
Mason (Skilled Labor) | $27.50 – $55.00 | 120 hours | $3,300 – $6,600 |
Helper (Unskilled Labor) | $16.50 – $33.00 | 80 hours | $1,320 – $2,640 |
Total Estimated Cost | $4,620 – $9,240 |
Accurate labor cost estimates require careful consideration of project timelines, labor availability, and local wage rates. Effective project management, including scheduling and oversight, can optimize labor efficiency and help control costs. Additionally, it’s advisable to maintain open communication with labor teams to ensure that project expectations and requirements are clearly understood, reducing the likelihood of misunderstandings and delays.
Other associated costs can include permits, inspections, site preparation, and equipment rentals. Below is an estimate for these additional costs:
Cost Type | Estimated Total Cost |
Permits and Inspections | $500 – $1,500 |
Site Preparation | $1,000 – $2,000 |
Equipment Rentals | $500 – $1,000 |
Total Estimated Cost | $2,000 – $4,500 |
Budgeting for these additional expenses is crucial for avoiding surprises during the construction process. Engaging with local authorities to understand permit requirements and associated fees can help streamline the project and ensure compliance with local regulations. Furthermore, site preparation costs can vary significantly based on land conditions, so it’s advisable to conduct thorough site assessments before construction begins. Considering all potential costs helps ensure that the project remains on track financially.
Understanding the estimated costs associated with various concrete block masonry projects is vital for effective planning and budgeting.
For residential projects, the cost of concrete block masonry varies based on size, design, and material selection. On average, the estimated cost for a single-family home can range from $16.50 to $38.50 per square foot, including materials and labor. This translates to a total cost of approximately $33,000 to $77,000 for a typical 2,000-square-foot home.
When planning a residential project, it’s crucial to collaborate closely with architects and contractors to refine your design and budget. Custom features, such as decorative blockwork or integrated insulation, may enhance aesthetic appeal but can also impact overall costs. Engaging with experienced professionals can help streamline the process and lead to a successful outcome. Moreover, considering future maintenance and energy costs associated with different design choices can help homeowners make more informed decisions that align with their long-term goals.
Commercial projects often involve larger operations and more intricate designs. The cost per square foot for commercial concrete block masonry can range from $22.00 to $49.50, depending on the project’s complexity and specifications. For instance, a 10,000-square-foot commercial building could incur costs between $220,000 and $495,000.
These projects frequently have specific building codes and requirements that can add to the complexity and cost. It’s essential to collaborate closely with professional builders who understand the nuances of commercial construction and can navigate the regulatory landscape effectively.
Investing in thorough planning and communication can yield significant long-term benefits. Additionally, considering the specific operational needs of the business being housed can help tailor the design and features, ensuring that the structure meets all functional requirements while remaining within budget.
Several factors contribute to the overall costs of concrete block masonry projects. Understanding these elements is crucial for accurate budgeting and planning.
The type of concrete block selected for a project can significantly impact costs. Standard hollow concrete blocks are typically the most affordable option due to their widespread availability and manufacturing efficiency. However, specialty blocks—such as insulated blocks designed for energy efficiency or decorative blocks with unique textures—can substantially increase material costs. Here’s a breakdown of estimated costs for different types of concrete blocks:
Concrete Block Type | Estimated Cost per Block |
Standard Hollow | $1.10 – $3.30 |
Solid Concrete Block | $3.30 – $6.60 |
Insulated Concrete Block | $3.85 – $7.70 |
Decorative Block | $5.50 – $11.00 |
When selecting blocks, it’s essential to consider both the upfront costs and the long-term benefits associated with durability, energy efficiency, and aesthetic appeal. While standard blocks are generally more economical, investing in higher-quality or specialty blocks can yield better performance, contribute to energy savings, and enhance property value over time. Additionally, local availability of specific block types can affect pricing, so it’s advisable to research suppliers in your area for the best deals.
Labor costs represent a substantial portion of the overall budget for concrete block masonry projects. Rates can vary based on geographic location, the complexity of the project, and the skill level of the workers involved. Below is an average estimate of labor costs for various types of labor involved in masonry projects:
Labor Type | Estimated Cost per Hour |
Mason (Skilled Labor) | $27.50 – $55.00 |
Helper (Unskilled Labor) | $16.50 – $33.00 |
It’s essential to budget for both skilled and unskilled labor, as experienced masons can work more efficiently, potentially reducing overall project time and costs. Engaging qualified professionals ensures that the work adheres to industry standards and local building codes. Moreover, skilled masons often have a deeper understanding of material properties and construction techniques, which can help prevent costly errors and delays during construction. Additionally, factors such as union labor agreements or prevailing wage laws may further influence labor costs, so it’s important to be aware of local regulations when estimating expenses.
The size and complexity of a masonry project play a crucial role in determining costs. Larger projects may benefit from economies of scale, leading to lower per-square-foot costs due to the efficiencies gained through bulk purchasing of materials and labor specialization. Conversely, intricate designs, custom features, or challenging site conditions can lead to increased labor and material expenses. Below is an average estimate for masonry projects based on size and complexity:
Project Size | Estimated Total Cost |
Small (Up to 500 sq ft) | $11,000 – $22,000 |
Medium (500 – 1,500 sq ft) | $22,000 – $44,000 |
Large (1,500+ sq ft) | $44,000 – $110,000 |
Understanding the relationship between size and complexity helps in accurately estimating costs and making informed decisions about design and materials. For instance, a small, straightforward wall may require fewer materials and less labor compared to a large structure with multiple corners, arches, and embedded utilities. Additionally, projects that involve significant excavation or site preparation may incur higher initial costs, so careful planning is essential to ensure that all aspects of the project are accounted for in the budget.
The geographic location of a construction project can significantly influence costs. Urban areas typically experience higher material and labor costs due to increased demand and higher living expenses. Additionally, projects situated in hard-to-access locations may incur extra charges for specialized equipment or extended labor hours. Here’s an overview of how location affects costs:
Location Type | Estimated Cost Increase |
Urban Areas | 10% – 30% higher |
Suburban Areas | 5% – 15% higher |
Rural Areas | Standard or lower |
Being aware of local market conditions and accessibility challenges is essential for accurate budgeting and effective project planning. For example, projects in urban centers may also face additional costs related to zoning regulations and permit fees, whereas rural projects may benefit from lower land costs but incur higher transportation expenses for materials. Additionally, local labor availability can vary, impacting labor rates and project timelines. Therefore, it is crucial to conduct thorough research on local conditions before initiating a project.
Choosing concrete block masonry comes with numerous advantages, making it an attractive option for various construction projects. Below are some of the key benefits.
While concrete block masonry offers numerous benefits, costs can add up quickly. Here are some practical tips to help you manage and reduce expenses:
Estimating the cost of concrete block masonry is a critical step in planning and executing any construction project. By understanding the factors that influence costs—such as materials, labor, project size, and complexity—you can make informed decisions that align with your budget and project goals.
Concrete block masonry involves constructing walls and other structures using concrete blocks, also known as concrete masonry units (CMUs). This method is valued for its strength, durability, and versatility in various applications, including residential, commercial, and industrial buildings.
The total cost for concrete block masonry varies based on several factors, including the type of blocks used, labor rates, project size, and complexity. On average, costs for residential projects range from $16.50 to $38.50 per square foot, while commercial projects can vary from $22.00 to $49.50 per square foot.
To estimate materials cost, multiply the estimated cost per unit of each material by the quantity needed. Common materials include concrete blocks, mortar, rebar, and insulation. For example, if you need 2,000 concrete blocks at $1.10 to $3.30 each, the total cost for blocks would range from $2,200 to $6,600.
Several factors can affect costs, including the type of concrete block selected, labor rates in your area, the size and complexity of the project, and location accessibility. Custom designs and special features can also add to the overall expenses.
Labor costs typically represent a significant portion of the budget. For skilled masons, the hourly rate can range from $27.50 to $55.00, while unskilled helpers may earn between $16.50 and $33.00 per hour. Total labor costs will depend on the estimated hours needed for the project.
Yes, additional costs may include permits, inspections, site preparation, and equipment rentals. Budgeting for these expenses is crucial to avoid surprises during construction. For example, permits can range from $500 to $1,500, and site preparation costs can be between $1,000 and $2,000.
To manage and reduce costs, consider bulk purchasing materials, opting for standard concrete blocks instead of specialty ones, hiring experienced contractors, and carefully planning your project to avoid unnecessary changes.
At Estimate Florida Consulting, we offer detailed cost estimates across all major trades, ensuring no part of your project is overlooked. From the foundation to the finishing touches, our trade-specific estimates provide you with a complete and accurate breakdown of costs for any type of construction project.
We take pride in delivering accurate, timely, and reliable estimates that help contractors and builders win more projects. Our clients consistently praise our attention to detail, fast turnaround times, and the positive impact our estimates have on their businesses.
Estimate Florida Consulting has helped us win more bids with their fast and accurate estimates. We trust them for every project!
Submit your project plans, blueprints, or relevant documents through our online form or via email.
We’ll review your project details and send you a quote based on your scope and requirements.
Confirm the details and finalize any adjustments to ensure the estimate meets your project needs.
Receive your detailed, trade-specific estimate within 1-2 business days, ready for your project execution.
561-530-2845
info@estimatorflorida.com
Address
5245 Wiles Rd Apt 3-102 St. Pete Beach, FL 33073 United States
561-530-2845
info@estimatorflorida.com
Address
5245 Wiles Rd Apt 3-102 St. Pete Beach, FL 33073 United States
All copyright © Reserved | Designed By V Marketing Media | Disclaimer