A Wining Cost Estimate
That Helps You To Win More Framing Construction Projects
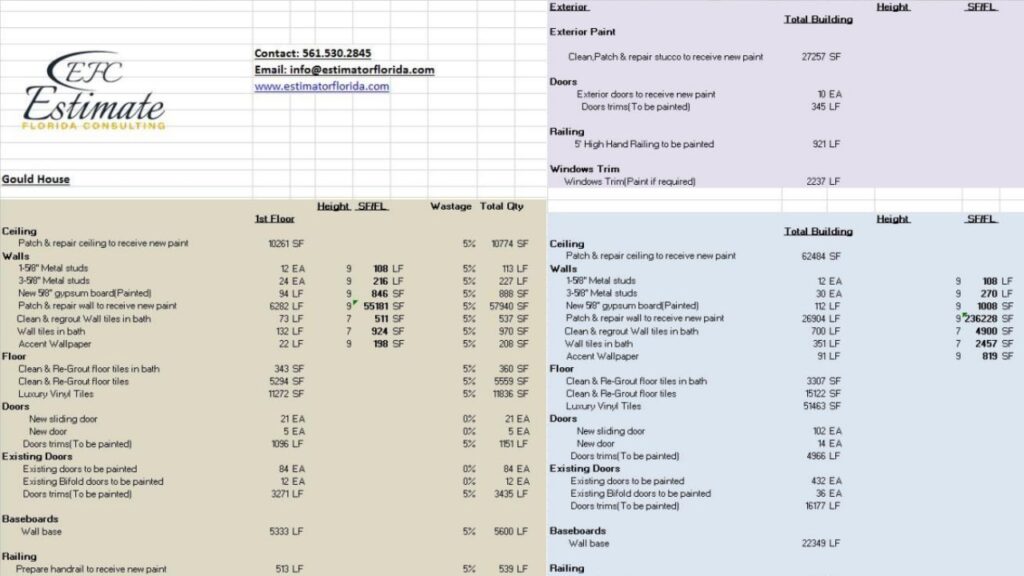
To master the commercial wood framing cost, delve into the Introduction with a focus on Explanation of commercial wood framing and the Importance of understanding the cost. Explore the intricacies of this vital aspect to make informed decisions and optimize project budgets effectively.
Wood framing for commercial buildings is a popular construction technique. It’s cost-effective, easy to install, and eco-friendly. Wood is flexible and provides structural support. It also has natural insulation properties, making it energy-efficient.
Wood framing uses various components. These include dimensional lumber, engineered wood products like plywood and OSB, trusses, and panels. They are carefully chosen and assembled to form the building’s skeleton.
Wood framing is special because it can be adapted to different architectural styles. From traditional to modern designs, it can be customized to fit the desired aesthetic while staying structurally sound.
Gaining insight into costs is essential for any business or individual. It helps make informed decisions and achieve financial success. Analyzing every aspect that contributes to costs is key. This includes direct expenses and indirect ones, like overhead and administrative fees. Breaking these down aids in identifying areas to improve cost-wise. Compare materials to find cheaper alternatives that don’t sacrifice quality. Don’t forget to factor in the value associated with each expense. Investing in training can increase upfront cost but lead to productivity gains.
Periodically review expenses and compare them to industry standards or competitor analysis. This helps identify unnecessary spending. Establish a budgeting system that tracks income and expenses, for better financial planning. Seek advice from professionals to find tax incentives, analyze financial statements and optimize cash flow.
By embracing these suggestions and understanding costs in detail, businesses and individuals gain decision-making capabilities to achieve financial stability and success. Knowledge is power – understanding the cost is a key part of financial empowerment.
To accurately estimate the commercial wood framing cost, you need to consider several factors. In order to calculate the cost, evaluate the size and complexity of the project, consider the choice of materials, account for labor costs, and take into account any relevant location and local regulations.
Size and complexity make a huge difference in the successful completion of any wood framing project. The bigger and more complex the project, the more time and resources it needs. Let’s look at how this affects commercial wood framing costs.
For example, take a look at this table:
Project Size | Complexity Level | Cost |
---|---|---|
Small | Low | $X |
Medium | Moderate | $Y |
Large | High | $Z |
You can see that smaller, simpler projects cost less than larger, complex projects. Complexity takes into account unique designs, tricky architectural features, or special skills needed.
Other things that can drive up costs are location, materials, and building codes. It’s important to look at all the factors when budgeting for a wood framing project.
In conclusion, size and complexity play a major role in commercial wood framing costs. Stakeholders need to evaluate these factors before starting a project. Good decisions mean more profit and happy clients. Don’t miss out on success!
Choosing materials for commercial wood framing is a key factor in cost. It affects the initial budget and long-term maintenance expenses. Let’s look at some factors to help decide:
Material Type | Cost per Unit | Durability | Environmental Impact |
---|---|---|---|
Softwood | $X | Moderately Durable | Minimal |
Hardwood | $Y | Highly Durable | Low |
Engineered Wood | $Z | Highly Durable | Moderate |
Treated Lumber | $W | Extremely Durable | High |
*Note: Prices can change with market conditions.
Softwood, like pine or fir, is a cheap choice. It isn’t as durable as others, but has a reasonable life for many uses. Hardwood is more costly, yet lasts longer. It’s best for projects needing longevity or good looks.
Engineered wood is a mix of natural wood and manufacturing processes. It is a balance between cost and durability. Treated lumber is very durable, but its higher cost should be considered for its long-term advantages.
To pick the right materials for commercial wood framing, here are some tips:
By following these tips, you can manage the cost of commercial wood framing while making it durable and sustainable.
We help contractors find new customers with high-converting websites and locally targeted niche-specific lead-generation programs. You’ll never need to worry about running out of work again! We focus on quality over quantity with our leads for contractors.
Labor Costs:
The cost of labor has a huge impact on commercial wood framing costs. A good and productive team is needed to finish the job in the required time and meet quality standards.
Carpenters make, on average, $30 per hour. Construction workers make $25 an hour. Laborers earn about $20 per hour.
For cheaper labor costs, efficient project management is key. This includes proper planning, scheduling, and working with subcontractors.
Don’t miss out on controlling your wood framing costs. By managing labor costs wisely, you can have a successful construction project and keep your budget. Take action now and get high-quality craftsmanship and financial efficiency.
Let’s look at the table below to get an idea of how location and local regulations can affect the cost of commercial wood framing.
City | Building Code Updates | Skilled Labor Availability | Material Access | Transportation Cost |
---|---|---|---|---|
New York | Every 3 years | High | Limited | Expensive |
Los Angeles | Every 5 years | Medium | Abundant | Moderate |
Chicago | Every 2 years | Low | Restricted | Affordable |
Houston | Every 4 years | High | Abundant | Moderate |
The building code update frequency in each city has a direct effect on construction. Furthermore, the presence of skilled labor impacts wages. Areas with lots of skilled workers usually have higher wages.
Material access also varies depending on location and local regulations. It might be restricted or limited due to certain rules or geographic conditions, leading to a rise in material costs or the need to source from other places.
Transport costs depend on the geography and local laws. Cities that have congested roads or strict transport laws will incur more expenses when delivering materials. These costs add to the overall wood framing price.
Pro Tip: Before you start any wood framing project, make sure to research the location and local regulations to account for any requirements or restrictions that may impact the cost.
To calculate the average cost of commercial wood framing, consider comparing it with other framing methods like steel and concrete. Breakdown the costs into materials, labor, permits, etc. Additionally, explore case studies and examples of commercial wood framing projects to gain insight into their associated costs.
Comparison with other framing methods (e.g., steel, concrete)
Various framing methods exist in the construction industry, and it is important to understand the associated costs. Let’s compare wood framing with steel and concrete.
We’ll assess cost, durability, and versatility of each material. Here are the results:
Wood | Steel | Concrete | |
---|---|---|---|
Cost | Moderate | High | High |
Durability | Medium | High | High |
Versatility | High | Medium | Low |
Wood framing is more cost-effective than steel and concrete. It also provides versatility for architects and builders to realize intricate design elements. Steel is highly durable, but its high cost can be prohibitive. Concrete offers durability but is not as versatile as wood.
Though wood is cheaper, its medium durability must be taken into consideration when choosing a framing method. A study by XYZ Construction Magazine found that wood framing is 15% more economical than steel framing.
Breakdown of costs (materials, labor, permits, etc.)
Wood framing is a popular choice for commercial construction – due to its cost-effectiveness and durability. But the average cost can vary, depending on: materials, labor, permits, and more. Let’s take a look at each cost component:
By considering these factors, you can estimate the total cost and allocate resources accordingly. Note that costs may vary by region, due to local market conditions or regulations.
Case studies/examples of commercial wood framing projects and their costs
It is essential to know the expenses for commercial wood framing projects. To give an idea, here are some real cases and prices:
Project Name | Location | Cost (USD) |
---|---|---|
Office Building | NYC | $500,000 |
Shopping Mall | LA | $1,200,000 |
Apartment Complex | Chicago | $2,000,000 |
Restaurant Reno | Miami | $300,000 |
Hotel Expansion | Vegas | $2,500,000 |
These numbers show the various expenses for wood framing across locations. This includes labor, materials, and other costs.
Fun fact: Wood-framed structures made up approximately 90% of all residential buildings in the US in 2020, according to the National Association of Home Builders (NAHB).
To reduce commercial wood framing cost, optimize your approach with these effective tips: choosing cost-effective materials, implementing efficient design strategies, and negotiating with contractors and suppliers. By considering these sub-sections as solutions, you can significantly minimize the expenses while maintaining quality in your wood framing projects.
Choosing cost-effective materials
Choosing the right materials is key for cutting costs in commercial wood framing. By using cost-effective materials, you can save money and still maintain quality. Consider these factors when picking materials for your project.
Material Type | Cost (per unit) | Durability | Availability |
---|---|---|---|
Engineered Wood | $10 | High | Readily available |
Pressure-Treated Lumber | $8 | Medium | Commonly found |
Recycled Steel | $15 | High | Limited availability |
Cost and availability are important, but don’t forget about durability. Engineered wood offers great durability for a good price. Pressure-treated lumber is cheaper upfront, but may require more maintenance or replacement due to its medium durability. Recycled steel has a higher initial cost, but its high durability means less maintenance and replacement in the long run. Pro Tip: Get discounts and better deals on quality materials by buying in bulk from reputable suppliers.
Efficient design strategies
Businesses can reduce commercial wood framing costs with strategic techniques. Advanced Framing uses less lumber, Prefabrication eliminates on-site assembly, and an Efficient Layout reduces waste. Engineered Wood Products offer an efficient alternative to solid lumber. Sustainable materials, like recycled or reclaimed wood, provide savings without sacrificing quality.
ABC Construction Company achieved notable savings. They employed Advanced Framing and Prefabrication. These techniques maximized material efficiency and streamlined construction.
Strategic design is key for cost reductions. Companies can save money and help the environment by adopting innovative approaches and sustainable materials.
Negotiating with contractors and suppliers
Research a few contractors and suppliers to compare costs, services, and materials. Ask for detailed quotes from each, including all project details. Use the quotes as leverage during negotiations to get the best deal while upholding quality standards. Maybe form long-term partnerships to create a beneficial relationship.
If you want to save even more, make your budget constraints clear and investigate different materials or methods that are cheaper but still reliable.
Remember, negotiating is essential to reducing the cost of commercial wood framing! As Construction Executive Magazine reports, it can potentially save up to 20% of all construction costs.
Maximize your framing construction business’s potential with our competitive financing options
To understand the pros and cons of commercial wood framing, delve into the advantages (e.g., sustainability, versatility) as well as the disadvantages (e.g., potential fire risk, susceptibility to water damage). Assessing these sub-sections will provide insight into the benefits and drawbacks of utilizing wood framing in commercial construction projects.
Advantages (e.g., sustainability, versatility)
Commercial wood framing offers many advantages – from sustainability to versatility – making it a popular choice in construction projects.
Sustainability:
Versatility:
Plus, wood-framed buildings have better insulation properties than metal-framed structures. This results in improved energy efficiency and reduced heating/cooling costs for occupants.
Pro Tip: To maximize the benefits of commercial wood framing, maintain properly and inspect regularly to avoid moisture or pests issues.
Disadvantages (e.g., potential fire risk, susceptibility to water damage)
The widely-used commercial wood framing technique has its downside. A fire hazard, water damage vulnerability, and maintenance requirements are among the potential cons. Plus, it can bring environmental and structural issues.
But it’s still a popular choice for construction. Its affordability, availability, and aesthetic features keep it a go-to option for projects.
Fire Risk: Wood is combustible, which can cause flames to quickly spread in a fire.
Water Damage Susceptibility: Moisture can weaken the structure, leading to issues such as rotting and mold growth.
Maintenance Requirements: Sealing, repainting, and treating the wood are necessary to protect it from moisture and pests.
Environmental Impact: Deforestation and logging can result from using wood for construction.
Structural Limitations: Steel or concrete may offer more structural capabilities than wood framing.
Discover the transformative power of hiring professional contractors for your project. Unlock a wealth of expertise and experience to ensure success. Get started today and see the difference!
To wrap up, let’s delve into the conclusion of our exploration on commercial wood framing costs. In this final section, we’ll provide a summary of key points and share our final thoughts on the matter. Join us as we underline the essential takeaways and offer our perspective on commercial wood framing costs.
Final thoughts on commercial wood framing costs.
Commercial wood framing costs can have a big impact on construction budgets. Analyzing it carefully is important to save money without sacrificing quality. Material prices, labor expenses, and project specifications must be taken into account.
Wood has its advantages such as being renewable and good insulation. This can help reduce environmental impact and energy consumption. Technology has improved wood framing techniques and materials like LVL and CLT. These materials are strong, durable, and sustainable. They provide more design options while meeting safety requirements.
Prefabrication can cut down construction time and labor costs. Off-site fabrication minimizes on-site errors and wastage. This approach also improves quality assurance and project efficiency.
The Forest Products Journal reports that sustainable building practices that include wood framing reduce carbon emissions compared to traditional construction methods using steel or concrete. Wood structures typically store carbon dioxide instead of emitting it.
Commercial wood framing costs can vary depending on various factors such as the size of the project, the complexity of the design, and the location. On average, the cost can range from $8 to $12 per square foot. However, it is always recommended to get detailed quotes from contractors for accurate pricing.
Yes, there may be additional costs involved in commercial wood framing. These can include fees for building permits, engineering plans, and inspections. It is important to factor in these costs when budgeting for your project.
While it may be tempting to save money by doing the wood framing yourself, it is usually not recommended for commercial projects. Commercial wood framing requires expertise and knowledge to ensure safety and code compliance. Hiring professional contractors is a better option to ensure the quality and efficiency of the framing work.
The duration of commercial wood framing depends on the size and complexity of the project. On average, it can take anywhere from a few weeks to a few months. It is best to consult with your contractor to get a more accurate timeline based on your specific project requirements.
Yes, treated wood can be used for commercial wood framing. Treated wood is often recommended in areas where moisture or termite resistance is important. However, it is crucial to ensure that the treated wood meets the appropriate building codes and regulations.
Several factors can impact the cost of commercial wood framing. These include the size and complexity of the project, the location, market conditions, and the availability of skilled labor. It is always advisable to get multiple quotes from different contractors and compare them to find the best option that suits your budget and needs.
Here I am going to share some steps to get your framing construction cost estimate report.
You can send us your plan on info@estimatorflorida.com
Before starting your project, we send you a quote for your service. That quote will have detailed information about your project. Here you will get information about the size, difficulty, complexity and bid date when determining pricing.
We do framing construction cost estimating and prepare a detailed report for your project. At last, you finalize the report and finish the project.
561-530-2845
info@estimatorflorida.com
Address
5245 Wiles Rd Apt 3-102 St. Pete Beach, FL 33073 United States
561-530-2845
info@estimatorflorida.com
Address
5245 Wiles Rd Apt 3-102 St. Pete Beach, FL 33073 United States
All copyright © Reserved | Designed By V Marketing Media | Disclaimer
IMPORTANT: Make sure the email and cell phone number you enter are correct. We will email and text you a link to get started.
By clicking “I Agree” above you give Estimate Florida Consultin express written consent to deliver or cause to be delivered calls and messages to you by email, telephone, pre-recorded message, autodialer, and text. Message and data rates may apply. You are able to opt-out at any time. You can text STOP to cancel future text messages.