Commercial Mechanical Cost Estimator Services
Commercial mechanical systems, including HVAC (Heating, Ventilation, and Air Conditioning), plumbing, and electrical systems, are critical components of any commercial building. Understanding the costs associated with installing these systems is essential for budgeting and planning your project. Below, we dive into the various aspects of commercial mechanical installation costs, breaking down expenses by building type, materials, and factors that influence overall costs.
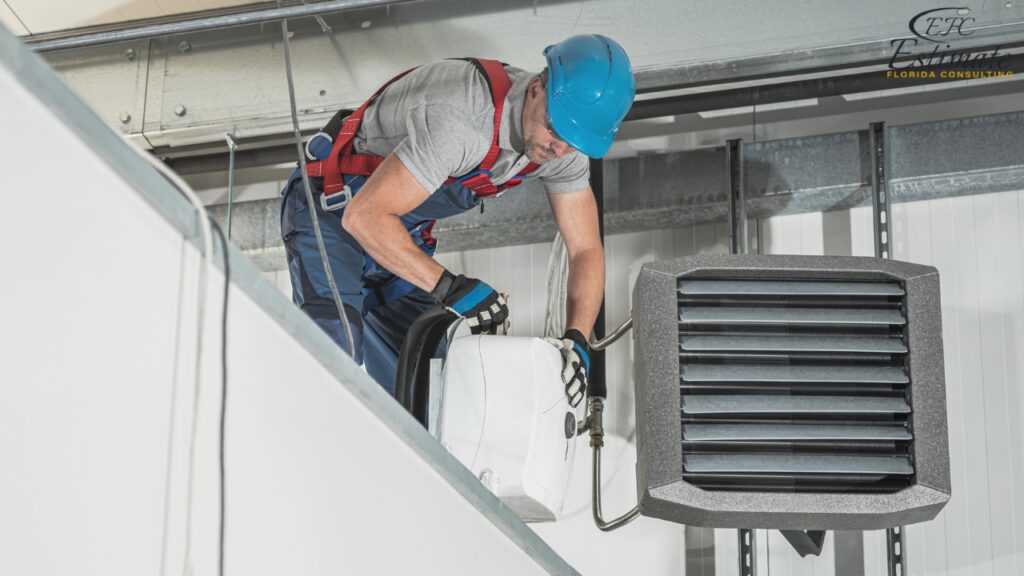
How Much Does Commercial Mechanical Installation Cost per Square Foot?
The cost of commercial mechanical installation typically ranges from $40 to $80 per square foot. This cost includes the installation of HVAC systems, plumbing, and other mechanical systems essential to the operation of a commercial building. The exact price can vary based on the complexity of the system, the type of building, and the specific requirements of the project. For example, a straightforward office building may be on the lower end of the scale, while a complex industrial facility with specialized systems may be on the higher end.
Commercial Building Types and Mechanical System Installation Costs
Different types of commercial buildings have varying mechanical needs, which can significantly impact installation costs. For example, an office building typically requires a standard HVAC system, basic plumbing, and electrical systems, resulting in lower overall costs. In contrast, an industrial facility might need heavy-duty HVAC units, complex plumbing systems to handle industrial processes, and robust electrical infrastructure to support machinery, leading to higher installation costs. Here’s a breakdown of the average costs for mechanical system installation by building type:
Commercial Building Type | Cost per Square Foot | Total Installation Cost Range |
Office Building | $40 – $60 | $200,000 – $300,000 (for 5,000 sq ft) |
Retail Store | $45 – $65 | $225,000 – $325,000 (for 5,000 sq ft) |
Industrial Facility | $50 – $80 | $500,000 – $800,000 (for 10,000 sq ft) |
Hotel | $55 – $85 | $1,100,000 – $1,700,000 (for 20,000 sq ft) |
Healthcare Facility | $60 – $90 | $600,000 – $900,000 (for 10,000 sq ft) |
Office Building
Office buildings are often designed with a focus on functionality and efficiency, which can influence the overall cost. The price range of $40 to $60 per square foot includes the basic construction elements such as the building shell, HVAC systems, electrical wiring, and basic interior finishes. Depending on the level of customization, such as high-end finishes or advanced technology integrations, costs can vary. For a standard 5,000 square foot office building, the total cost would range from $200,000 to $300,000, making it a relatively affordable option for businesses needing office space.
Retail Store
Retail stores require a balance between functionality and aesthetics to attract customers while also providing a practical space for operations. The cost per square foot for a retail store ranges from $45 to $65, which includes the basic construction, electrical and plumbing systems, and interior finishes suitable for retail environments. The total cost for a 5,000 square foot retail space would typically fall between $225,000 and $325,000. This cost variation allows for flexibility in the design and layout, enabling businesses to create inviting spaces that align with their brand identity and customer experience goals.
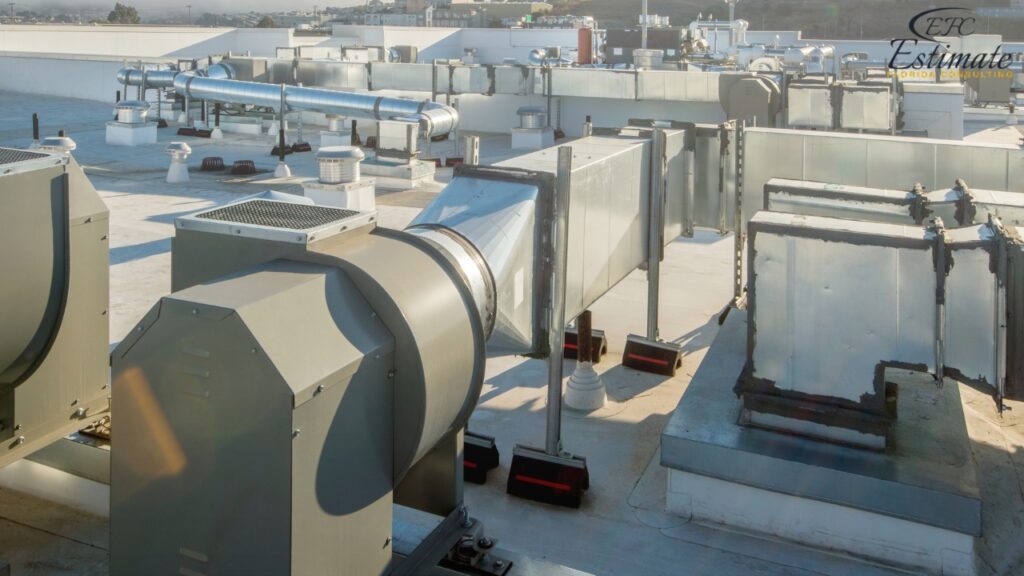
Industrial Facility
Industrial facilities are generally more complex to construct due to their need for robust structural components and specialized equipment. The cost per square foot for industrial buildings ranges from $50 to $80, reflecting the requirements for heavy-duty materials, reinforced foundations, and specialized systems like ventilation and large-scale electrical setups. For a 10,000 square foot industrial facility, the total cost would range from $500,000 to $800,000. These facilities are designed to accommodate manufacturing processes, storage, and other industrial activities, and the cost reflects the need for durability and functionality in a demanding environment.
Hotel
Hotels require a higher level of investment due to the need for high-quality finishes, extensive plumbing and electrical systems, and compliance with safety and accessibility regulations. The cost per square foot for a hotel ranges from $55 to $85, depending on the level of luxury and the specific amenities included, such as restaurants, conference rooms, and recreational facilities. For a 20,000 square foot hotel, the total installation cost would be between $1,100,000 and $1,700,000. This cost reflects the comprehensive nature of hotel construction, which must cater to guest comfort, safety, and operational efficiency.
Healthcare Facility
Healthcare facilities are among the most expensive types of commercial buildings to construct due to the stringent requirements for safety, sanitation, and specialized medical equipment. The cost per square foot ranges from $60 to $90, covering the construction of treatment rooms, laboratories, patient areas, and administrative spaces. For a 10,000 square foot healthcare facility, the total installation cost would typically range from $600,000 to $900,000. These facilities must meet high standards for cleanliness, accessibility, and patient care, which contributes to the higher overall construction costs.
Mechanical System Material Options for Commercial Buildings
The choice of materials for mechanical systems can significantly impact both the cost and the performance of the systems. Materials must be selected based on the building’s intended use, environmental conditions, and desired durability. For instance, ductwork made from galvanized steel is durable and widely used in commercial settings due to its resistance to corrosion and structural integrity. However, aluminum ductwork, while more lightweight, might be preferred in specific applications where weight is a concern.
Here are some common material options and their associated costs:
Material Type | Cost per Unit |
Ductwork (Galvanized Steel) | $8 – $15 per sq ft |
HVAC Unit (Packaged System) | $1,500 – $2,500 per ton |
Plumbing Piping (Copper) | $10 – $15 per linear foot |
Electrical Wiring (Copper) | $3 – $5 per linear foot |
Insulation (Fiberglass) | $1.50 – $3.00 per sq ft |
Ductwork (Galvanized Steel)
Galvanized steel ductwork is a vital component of HVAC systems, providing the necessary channels for air distribution throughout the building. The cost for galvanized steel ductwork typically ranges from $8 to $15 per square foot. This cost includes the material itself, as well as any necessary fittings and connections. Galvanized steel is favored for its durability and resistance to corrosion, making it a reliable choice for long-term use in both commercial and residential buildings. The price range allows for flexibility based on the specific design and layout of the HVAC system, ensuring that it meets the building’s heating, cooling, and ventilation needs efficiently.
HVAC Unit (Packaged System)
The HVAC unit is one of the most critical components in a building’s mechanical system, responsible for heating, ventilation, and air conditioning. The cost of a packaged HVAC system ranges from $1,500 to $2,500 per ton, with the total cost dependent on the size and capacity required to effectively service the building. Packaged systems are typically more cost-effective and easier to install than split systems, as they combine heating and cooling components into a single unit. The price variation reflects differences in brand, energy efficiency ratings, and additional features such as smart controls and enhanced filtration systems, which can contribute to improved indoor air quality and energy savings over time.
Plumbing Piping (Copper)
Copper piping is widely used in plumbing systems due to its durability, corrosion resistance, and ability to handle both hot and cold water. The cost for copper plumbing piping ranges from $10 to $15 per linear foot, making it one of the more expensive piping options available. This price includes the copper material as well as the fittings and labor required for installation. Despite its higher cost, copper piping is preferred for its long lifespan and reliability, particularly in applications where water quality and longevity are critical considerations. The use of copper can also add value to the building, as it is often seen as a premium material in construction.
Electrical Wiring (Copper)
Copper wiring is the standard choice for electrical systems in buildings due to its excellent conductivity, flexibility, and durability. The cost for copper electrical wiring typically ranges from $3 to $5 per linear foot, depending on the gauge and insulation type required for the specific application. This cost includes the copper wire itself, as well as any necessary connectors and labor for installation. Copper wiring is essential for ensuring the safe and efficient operation of electrical systems, supporting everything from lighting and outlets to HVAC systems and large appliances. The investment in high-quality copper wiring can reduce the risk of electrical issues and improve the overall safety and performance of the building.
Insulation (Fiberglass)
Fiberglass insulation is a common and cost-effective solution for improving a building’s thermal efficiency. The cost for fiberglass insulation ranges from $1.50 to $3.00 per square foot, depending on the R-value (a measure of thermal resistance) and the specific installation method. This price covers the material itself, as well as the labor required for installation. Fiberglass insulation is widely used in both commercial and residential buildings to reduce energy consumption, maintain indoor comfort, and comply with building codes related to energy efficiency. The variation in cost allows builders to choose the level of insulation that best meets their energy-saving goals while staying within budget.
Factors Influencing the Cost of Commercial Mechanical Systems Installation
Several factors can influence the cost of installing commercial mechanical systems, each playing a crucial role in determining the overall budget. Understanding these factors can help in making informed decisions during the planning and execution phases of the project:
Building Size and Layout
Larger buildings and those with complex layouts will typically incur higher installation costs due to the increased amount of materials and labor required. For example, a sprawling industrial facility with multiple zones and floors will require more extensive ductwork, piping, and wiring compared to a smaller, single-story office building. Additionally, buildings with irregular shapes or those requiring specialized climate zones may necessitate custom solutions, further driving up costs.
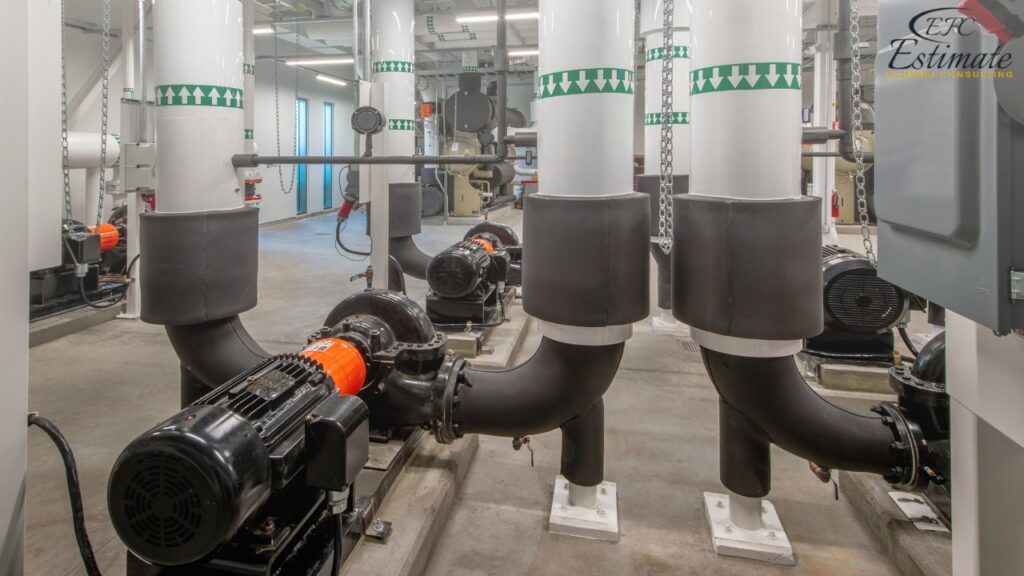
System Complexity
Buildings with specialized climate control needs, such as laboratories, data centers, or healthcare facilities, may require more advanced mechanical systems. These systems often involve additional components such as specialized filtration units, redundancy systems, and precise temperature and humidity controls, which can increase costs significantly. The complexity of these systems not only affects the installation cost but also the ongoing maintenance and operational costs.
Energy Efficiency Requirements
High-efficiency systems and those that meet green building standards may have higher upfront costs but can result in long-term energy savings. Investing in energy-efficient HVAC units, insulation, and smart controls can reduce operational costs over the building’s lifecycle, making the initial investment worthwhile. Additionally, energy-efficient systems can help buildings achieve certifications like LEED (Leadership in Energy and Environmental Design), which can increase the property’s value and appeal.
Local Labor and Material Costs
The availability and cost of skilled labor and materials in the project’s location can significantly impact overall expenses. In areas where skilled labor is in short supply or where materials must be imported, costs can rise. Additionally, local regulations and building codes may require specific materials or installation practices, adding to the complexity and cost of the project.
Customization Needs
Custom mechanical systems tailored to the specific needs of the building or business may also raise costs. Customization might include unique HVAC zoning, specialized filtration systems, or custom ductwork designs to fit irregular spaces. While these custom solutions can enhance the functionality and comfort of the building, they often require additional design, engineering, and installation work, increasing the overall cost.
Mechanical Videos
Mechanical
Mechanical Rooftop
Thermaduct Installation
Cost Breakdown by Type of Commercial Building
Different commercial buildings have unique mechanical system requirements, which can affect the overall cost. For instance, an office building might prioritize comfort and air quality, leading to a focus on HVAC systems, while an industrial facility might require robust plumbing and electrical systems to support heavy machinery. Here’s a detailed breakdown:
Building Type | HVAC Cost | Plumbing Cost | Electrical Cost | Total Cost |
Office Building | $40,000 – $60,000 | $30,000 – $50,000 | $20,000 – $30,000 | $90,000 – $140,000 |
Retail Store | $45,000 – $65,000 | $35,000 – $55,000 | $25,000 – $35,000 | $105,000 – $155,000 |
Industrial Facility | $100,000 – $160,000 | $80,000 – $130,000 | $50,000 – $80,000 | $230,000 – $370,000 |
Hotel | $220,000 – $340,000 | $180,000 – $270,000 | $150,000 – $230,000 | $550,000 – $840,000 |
Healthcare Facility | $120,000 – $180,000 | $100,000 – $150,000 | $80,000 – $120,000 | $300,000 – $450,000 |
Office Building
The HVAC system must efficiently regulate the temperature to maintain a comfortable working environment. The cost for HVAC in an office building ranges from $40,000 to $60,000, depending on the size and complexity of the system. Plumbing costs, typically between $30,000 and $50,000, include installations for restrooms, breakrooms, and any additional water features. Electrical systems, costing $20,000 to $30,000, cover lighting, outlets, and power for office equipment. The total cost for these systems in an office building ranges from $90,000 to $140,000, reflecting the need for reliable, high-performing infrastructure to support daily operations.
Download Template For Mechanical Work Project Breakdown
- Materials list updated to the zip code
- Fast delivery
- Data base of general contractors and sub-contractors
- Local estimators
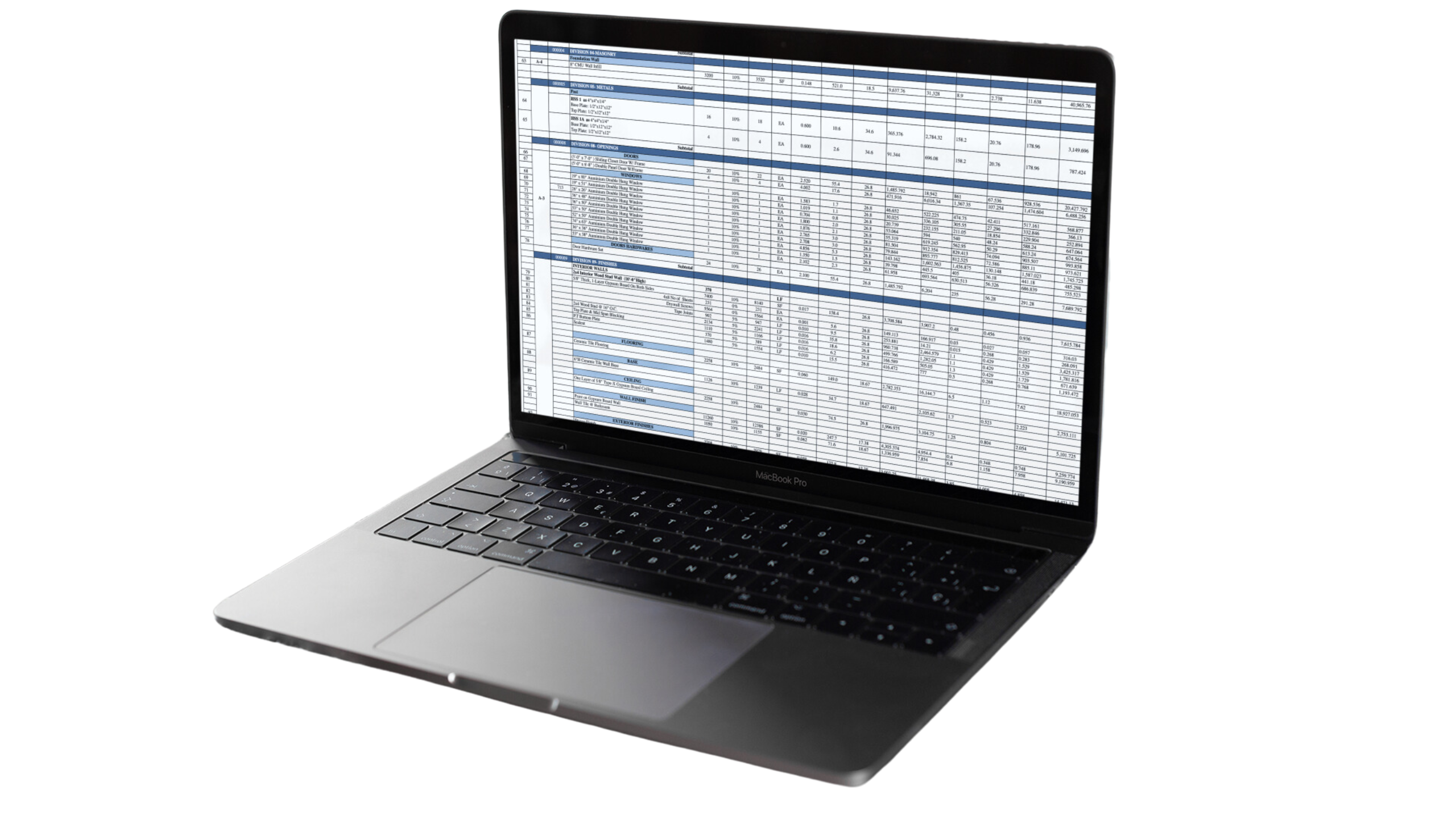
Retail Store
Retail stores require robust systems to ensure a pleasant shopping environment for customers. The HVAC costs for a retail store typically range from $45,000 to $65,000, depending on the size of the space and the level of climate control required. Plumbing costs, ranging from $35,000 to $55,000, often include restrooms and, in some cases, small kitchen areas or specialty fixtures. Electrical systems, which cost between $25,000 and $35,000, need to support extensive lighting, signage, and electronic payment systems. The total cost for these systems in a retail store falls between $105,000 and $155,000, ensuring that the store operates efficiently and provides a comfortable environment for customers.
Industrial Facility
Industrial facilities, such as manufacturing plants or warehouses, have more demanding requirements due to the nature of their operations. The HVAC system in an industrial facility, which may need to handle large spaces or specialized climate control, can cost between $100,000 and $160,000. Plumbing systems, costing $80,000 to $130,000, often include extensive piping, industrial-grade fixtures, and specialized drainage systems. Electrical costs range from $50,000 to $80,000, reflecting the need to power heavy machinery, lighting, and other industrial equipment. The total cost for these systems in an industrial facility ranges from $230,000 to $370,000, ensuring that the facility can operate efficiently and safely under industrial conditions.
Hotel
Hotels require extensive and high-quality systems to meet the comfort and service expectations of guests. The HVAC system, which must provide individualized climate control for each room as well as common areas, can cost between $220,000 and $340,000. Plumbing costs are substantial, ranging from $180,000 to $270,000, due to the need for numerous bathrooms, laundry facilities, kitchens, and possibly pools or spas. Electrical systems, costing between $150,000 and $230,000, support everything from room lighting and outlets to elevators and emergency systems. The total cost for these systems in a hotel ranges from $550,000 to $840,000, reflecting the high standards required for guest comfort and operational efficiency.
Healthcare Facility
Healthcare facilities have some of the most stringent requirements for HVAC, plumbing, and electrical systems due to the need for a sterile environment, precise temperature control, and reliable power. The HVAC system, costing between $120,000 and $180,000, must maintain consistent temperatures and air quality in patient rooms, operating theaters, and laboratories. Plumbing costs, ranging from $100,000 to $150,000, include specialized systems for sterilization, patient care, and waste management. Electrical systems, costing between $80,000 and $120,000, must be highly reliable, supporting critical medical equipment, lighting, and emergency systems. The total cost for these systems in a healthcare facility ranges from $300,000 to $450,000, ensuring that the facility can meet the rigorous demands of healthcare services.
Detailed Cost Breakdown for Commercial Mechanical Systems Installation
A detailed cost breakdown helps in understanding where your investment goes in a commercial mechanical system installation:
Cost Component | Low-End Cost | High-End Cost |
HVAC Installation | $20 – $40 per sq ft | $30 – $60 per sq ft |
Plumbing Installation | $15 – $25 per sq ft | $20 – $35 per sq ft |
Electrical Wiring and Panels | $10 – $20 per sq ft | $15 – $30 per sq ft |
System Insulation | $2 – $5 per sq ft | $3 – $7 per sq ft |
Controls and Automation | $5 – $10 per sq ft | $8 – $15 per sq ft |
Additional Considerations for Commercial Mechanical System Installation Projects
When planning a commercial mechanical system installation, consider these additional factors:
- Building Codes and Permits: Compliance with local building codes and securing the necessary permits can add to the overall cost and time required for the project. It’s essential to factor these into your budget and timeline to avoid any delays or legal issues that could arise during construction.
- Maintenance Requirements: High-quality mechanical systems often require less frequent maintenance, but planning for regular upkeep is essential for long-term performance. Regular maintenance not only ensures that the systems operate efficiently but also extends their lifespan, ultimately providing better value for your investment.
- System Integration: If your project involves integrating new systems with existing ones, additional costs for retrofitting and compatibility checks may apply. Properly integrating new systems with existing infrastructure ensures seamless operation and prevents potential issues down the line.
- Energy Efficiency Incentives: Investigate potential incentives or rebates for installing energy-efficient systems, which can offset some of the initial costs. These incentives can make it more financially viable to invest in high-efficiency systems that reduce long-term operational costs.
- Timeline and Scheduling: Consider the impact of your project’s timeline on costs, particularly if work must be completed outside of regular hours to avoid disrupting business operations. Proper scheduling can help manage labor costs and minimize the impact on ongoing business activities.
What is the Cost of Installing a Commercial Mechanical System?
The cost of installing a commercial mechanical system varies depending on the building’s size, complexity, and the specific systems being installed. On average, you can expect to pay between $40 to $80 per square foot, which includes the installation of HVAC systems, plumbing, and electrical systems. For a 10,000 square foot building, this translates to a total cost ranging from $400,000 to $800,000. These figures can fluctuate based on factors such as material choices, system complexity, and labor rates. Understanding these costs in advance allows for better financial planning and helps in making informed decisions during the construction process.
How to Choose the Right Contractor for Commercial Mechanical Systems?
Selecting the right contractor is crucial to the success of your commercial mechanical system installation. Here’s how to make the best choice:
- Verify Credentials and Experience: Ensure the contractor is licensed, insured, and has extensive experience with commercial mechanical installations. A contractor with a proven track record will likely deliver higher-quality work, ensuring that the project is completed on time and within budget.
- Check References and Reviews: Ask for references from previous clients and check online reviews to get an idea of the contractor’s reputation. Positive feedback from past clients is a good indicator of the contractor’s reliability and quality of work. Additionally, consider visiting completed projects if possible to see the quality of the contractor’s work firsthand.
- Get Multiple Quotes: Obtain quotes from several contractors to compare pricing and services. This will help you make an informed decision and ensure that you’re getting a fair price for the work. When reviewing quotes, be sure to compare not only the total cost but also the scope of work, materials, and warranties offered.
- Understand the Contract: Make sure the contract outlines all aspects of the project, including materials, labor, timelines, and payment schedules. Clear terms help prevent misunderstandings and ensure that both parties are on the same page. A well-drafted contract should also include provisions for handling any unexpected issues or changes that may arise during the project.
- Choose a Contractor Who Understands Local Conditions: In Miami, it’s essential to work with a contractor who understands the local climate and building codes. A local contractor will be familiar with the challenges posed by the area’s weather conditions and can recommend the best materials and techniques for your project.
Get 5 New Leads Next 7Days With Our System
- Multi-Family Building
- Hotel Building
- Hospital Building
- Warehouse Building
- High-Rise Building
- Shopping Complex
Conclusion
Understanding and accurately estimating the costs associated with commercial mechanical systems is essential for the successful planning and execution of any construction project. These systems, including HVAC, plumbing, and electrical, are critical to the functionality and efficiency of commercial buildings. By utilizing professional cost estimator services, you can ensure that your project stays within budget and meets the highest standards of quality. With costs typically ranging from $40 to $80 per square foot, careful consideration of material choices, system complexity, and contractor selection is key to achieving a successful and cost-effective installation.
FAQs
Commercial Mechanical Cost Estimator Services are specialized tools and consulting services designed to calculate the costs of installing mechanical systems in commercial buildings. These systems include HVAC, plumbing, and electrical components, all of which are essential for the building’s operation. Estimating these costs accurately is crucial for budgeting and planning construction projects.
The cost of commercial mechanical installation typically ranges from $40 to $80 per square foot. This range includes the installation of HVAC systems, plumbing, and electrical infrastructure. The exact cost depends on factors such as the complexity of the systems, the building type, and specific project requirements.
Several factors can affect the cost, including:
- Building Size and Layout: Larger and more complex buildings require more materials and labor.
- System Complexity: Advanced systems for specialized buildings like healthcare facilities or data centers cost more.
- Energy Efficiency Requirements: High-efficiency systems may have higher upfront costs but lower long-term operating costs.
- Local Labor and Material Costs: Availability and cost of skilled labor and materials can vary by location.
- Customization Needs: Custom mechanical systems tailored to specific building requirements may increase costs.
Costs vary depending on the type of building:
- Office Building: $40 to $60 per square foot, totaling $200,000 to $300,000 for 5,000 sq ft.
- Retail Store: $45 to $65 per square foot, totaling $225,000 to $325,000 for 5,000 sq ft.
- Industrial Facility: $50 to $80 per square foot, totaling $500,000 to $800,000 for 10,000 sq ft.
- Hotel: $55 to $85 per square foot, totaling $1,100,000 to $1,700,000 for 20,000 sq ft.
- Healthcare Facility: $60 to $90 per square foot, totaling $600,000 to $900,000 for 10,000 sq ft.
Common materials include:
- Ductwork (Galvanized Steel): $8 – $15 per sq ft.
- HVAC Unit (Packaged System): $1,500 – $2,500 per ton.
- Plumbing Piping (Copper): $10 – $15 per linear foot.
- Electrical Wiring (Copper): $3 – $5 per linear foot.
- Insulation (Fiberglass): $1.50 – $3.00 per sq ft.
- Building Codes and Permits: Compliance can add costs and time.
- Maintenance Requirements: High-quality systems may require less frequent maintenance.
- System Integration: Additional costs for retrofitting and compatibility checks may apply.
- Energy Efficiency Incentives: Potential rebates for energy-efficient systems can offset some initial costs.
- Timeline and Scheduling: Completing work outside of regular hours to avoid business disruption may increase costs.
The cost varies depending on the size and complexity of the building. On average, expect to pay between $40 to $80 per square foot. For a 10,000 sq ft building, this translates to a total cost of $400,000 to $800,000.
- Verify Credentials and Experience: Ensure the contractor is licensed, insured, and experienced.
- Check References and Reviews: Positive feedback from past clients indicates reliability.
- Get Multiple Quotes: Compare pricing and services to make an informed decision.
- Understand the Contract: Ensure all project aspects, including materials, labor, and timelines, are clearly outlined.
- Choose a Contractor Familiar with Local Conditions: Local contractors are more likely to understand regional challenges and building codes.
Florida’s Cities
- Alachua
- Altamonte Springs
- Anna Maria
- Apalachicola
- Apopka
- Atlantic Beach
- Auburndale
- Aventura
- Avon Park
- Bal Harbour
- Bartow
- Bay Harbor Islands
- Boca Raton
- Bonita Springs
- Boynton Beach
- Bradenton
- Brooksville
- Cape Canaveral
- Cape Coral
- Casselberry
- Celebration
- Chipley
- Cinco Bayou
- Clearwater
- Clermont
- Clewiston
- Cocoa
- Cocoa Beach
- Coconut Creek
- Coral Gables
- Coral Springs
- Crystal River
- Dania Beach
- Davie
- Daytona Beach
- Deerfield Beach
- DeFuniak Springs
- DeLand
- Delray Beach
- Deltona
- Destin
- Dunedin
- Eagle Lake
- Edgewater
- Edgewood
- Eustis
- Fort Lauderdale
- Fort Meade
- Fort Myers
- Fort Myers Beach
- Fort Pierce
- Fort Walton Beach
- Fruitland Park
- Gainesville
- Greenacres
- Green Cove Springs
- Gulf Breeze
- Gulfport
- Haines City
- Hallandale Beach
- Hawthorne
- Hialeah
- Hialeah Gardens
- Highland Beach
- Hollywood
- Holly Hill
- Holmes Beach
- Homestead
- Hypoluxo
- Indialantic
- Jacksonville
- Juno Beach
- Jupiter
- Key Biscayne
- Key West
- Kissimmee
- LaBelle
- Lady Lake
- Lake Alfred
- Lakeland
- Lake Mary
- Lake Park
- Lake Wales
- Lake Worth
- Lantana
- Largo
- Lauderdale By The Sea
- Lauderhill
- Leesburg
- Lighthouse Point
- Longboat Key
- Longwood
- Maitland
- Marco Island
- Margate
- Melbourne
- Melbourne Beach
- Miami
- Miami Beach
- Milton
- Minneola
- Miramar
- Mount Dora
- Naples
- Neptune Beach
- New Port Richey
- New Smyrna Beach
- Niceville
- North Miami
- North Miami Beach
- North Port
- Oakland Park
- Ocala
- Ocean Ridge
- Ocoee
- Okeechobee
- Oldsmar
- Orange Park
- Orlando
- Ormond Beach
- Oviedo
- Palatka
- Palm Bay
- Palm Beach
- Palm Beach Gardens
- Palm Coast
- Palmetto
- Panama City
- Panama City Beach
- Pembroke Pines
- Pensacola
- Pinecrest
- Pinellas Park
- Plant City
- Plantation
- Pompano Beach
- Ponce Inlet
- Port Orange
- Port St. Lucie
- Punta Gorda
- Rockledge
- Royal Palm Beach
- St. Augustine
- St. Augustine Beach
- St. Cloud
- St. Pete Beach
- St. Petersburg
- Safety Harbor
- Sanford
- Sanibel
- Sarasota
- Satellite Beach
- Seaside
- Sebastian
- Sewall's Point
- Shalimar
- Stuart
- Surfside
- Tallahassee
- Tamarac
- Tampa
- Tarpon Springs
- Tavares
- Temple Terrace
- Titusville
- Treasure Island
- Valparaiso
- Venice
- Vero Beach
- Wellington
- West Melbourne
- West Palm Beach
- Weston
- Wilton Manors
- Winter Garden
- Winter Haven
- Winter Park
- Winter Springs
Google Reviews

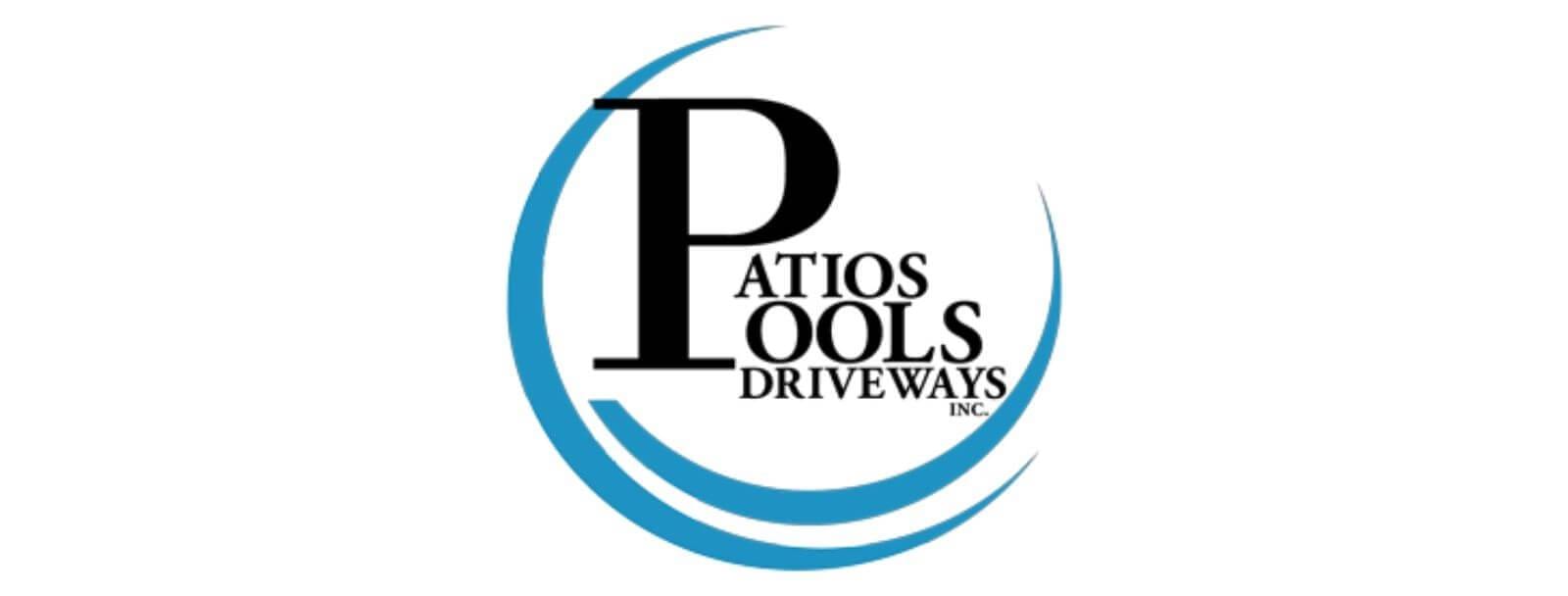
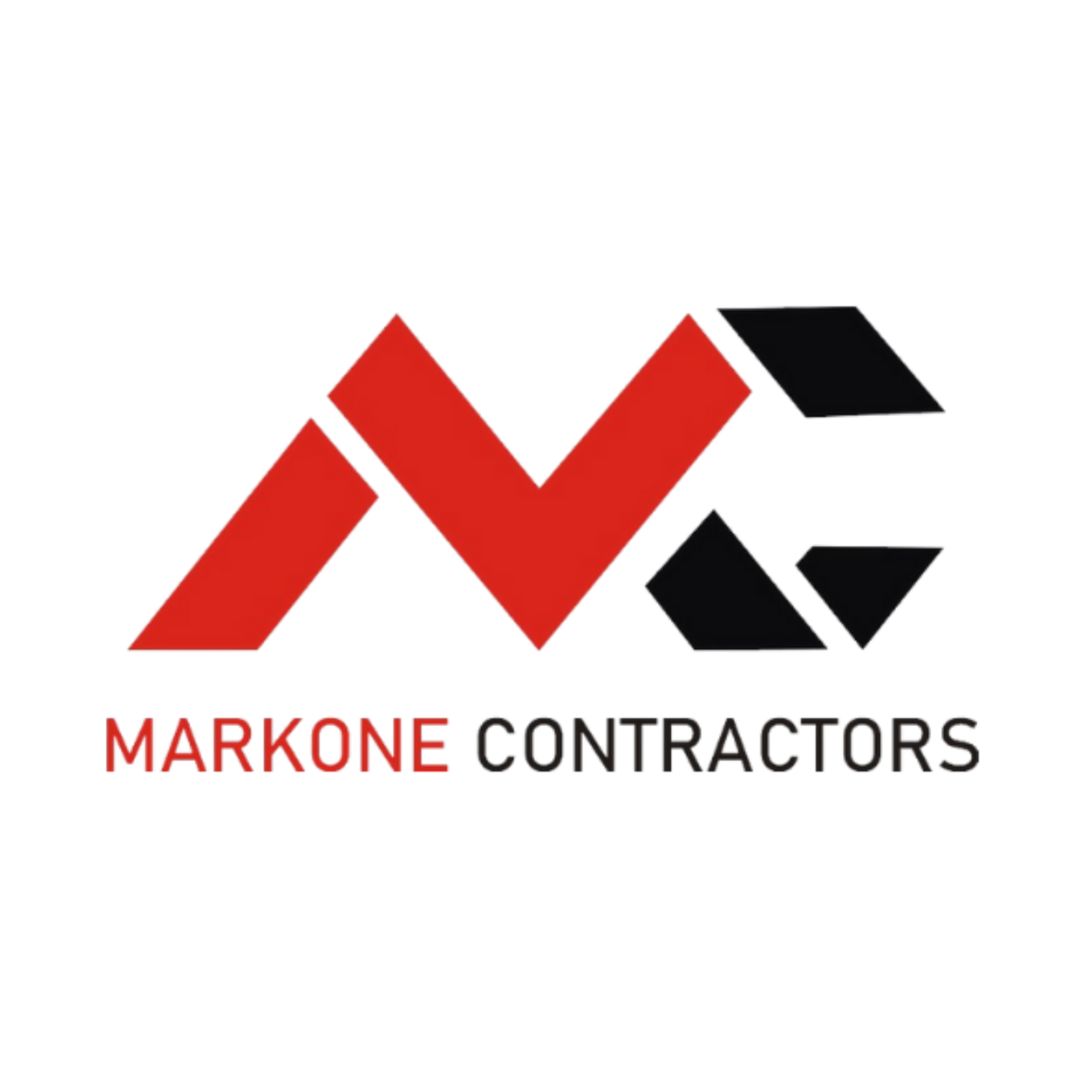

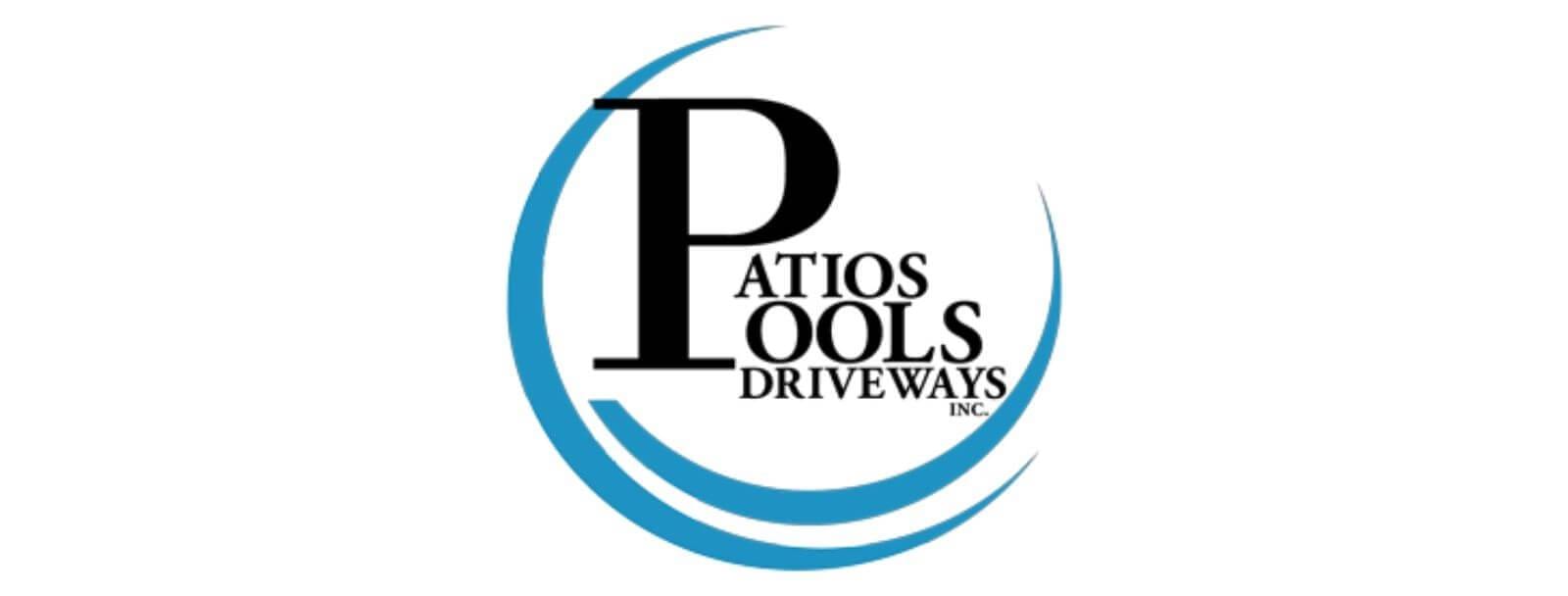
Process To Get The Commercial Mechanical Cost Estimate Report
Here I am going to share some steps to get the commercial mechanical cost estimate report.
-
You need to send your plan to us.
You can send us your plan on info@estimatorflorida.com
-
You receive a quote for your project.
Before starting your project, we send you a quote for your service. That quote will have detailed information about your project. Here you will get information about the size, difficulty, complexity and bid date when determining pricing.
-
Get Estimate Report
Our team will takeoff and estimate your project. When we deliver you’ll receive a PDF and an Excel file of your estimate. We can also offer construction lead generation services for the jobs you’d like to pursue further.