Commercial Building Cost Breakdown by Construction Type
When planning a commercial building project, understanding the cost breakdown by construction type is essential for effective budgeting and financial forecasting. Each construction method comes with its own unique set of costs and considerations, which can significantly impact the overall project budget. Factors such as the type of construction, materials used, location, design features, and even market conditions can lead to variations in cost. A thorough analysis of these aspects can help stakeholders make informed decisions and set realistic financial expectations.
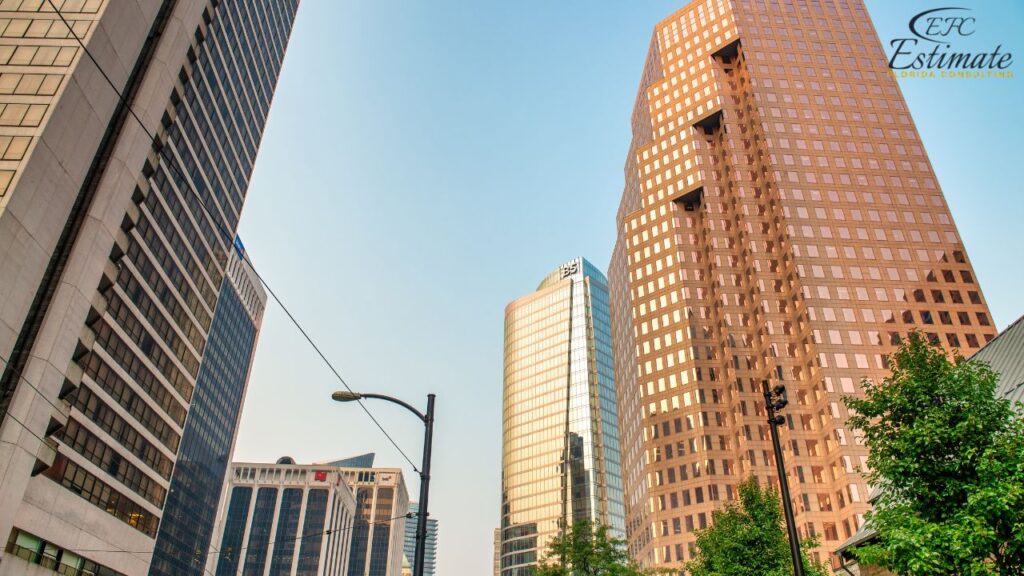
Traditional Construction
Overview
Traditional construction methods typically involve concrete, steel, and wood framing. This approach is widely used for various commercial buildings, including offices, retail spaces, and warehouses. Traditional construction is often favored for its proven reliability and familiarity among contractors and builders. However, it may take longer to complete due to the extensive labor involved and the time required for curing concrete and other materials. In addition, this method can result in higher costs if not managed properly, especially in urban areas where labor and land prices are elevated.
Cost Breakdown
Cost Component | Estimated Cost per Sq Ft | Total Cost for 10,000 Sq Ft |
Site Preparation | $5 – $15 | $50,000 – $150,000 |
$10 – $20 | $100,000 – $200,000 | |
Framing (Wood/Steel) | $15 – $30 | $150,000 – $300,000 |
$5 – $15 | $50,000 – $150,000 | |
$10 – $30 | $100,000 – $300,000 | |
Interior Finishes | $20 – $40 | $200,000 – $400,000 |
Total Estimated Cost | $95 – $150 | $950,000 – $1.5 million |
Advantages and Disadvantages
Traditional construction remains a popular choice due to its versatility and ability to accommodate a wide range of architectural styles. However, it is important for project managers to work closely with architects and engineers to optimize the design and minimize waste during the construction process, which can help keep costs in check. The time-consuming nature of this method can also lead to project delays, affecting the overall timeline and budget.
Pre-Engineered Metal Buildings
Overview
Pre-engineered metal buildings consist of factory-built components that are shipped and assembled on-site. This method is common for warehouses, manufacturing facilities, and storage units, as it allows for quick assembly and reduced labor costs. The use of steel frames provides structural integrity and flexibility in design, making it an ideal choice for buildings that require large open spaces. Additionally, pre-engineered buildings often come with reduced lead times, allowing for quicker project completion.
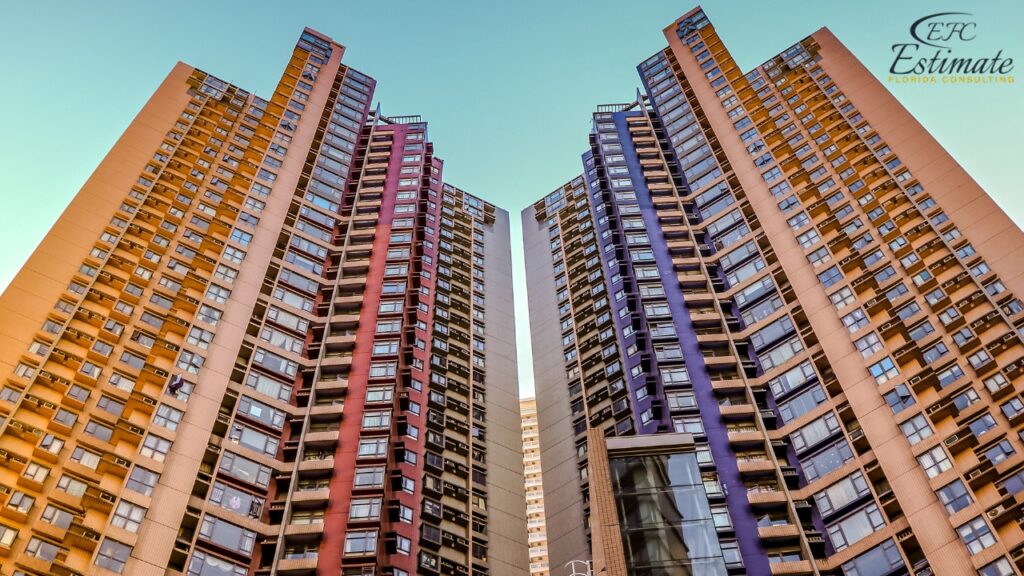
Cost Breakdown
Cost Component | Estimated Cost per Sq Ft | Total Cost for 10,000 Sq Ft |
Site Preparation | $3 – $10 | $30,000 – $100,000 |
Foundation | $5 – $15 | $50,000 – $150,000 |
$10 – $20 | $100,000 – $200,000 | |
Roofing | $3 – $8 | $30,000 – $80,000 |
Exterior Finishes | $5 – $15 | $50,000 – $150,000 |
Interior Finishes | $10 – $30 | $100,000 – $300,000 |
Total Estimated Cost | $36 – $98 | $360,000 – $980,000 |
Benefits of Pre-Engineered Metal Buildings
Pre-engineered metal buildings can also offer cost savings in maintenance over time, as the materials used are often more durable and resistant to the elements compared to traditional materials. However, it is essential to ensure proper insulation and energy efficiency measures are incorporated to avoid higher operational costs in the long run. Furthermore, these buildings can be designed to meet specific needs, allowing for customization while still benefiting from the efficiencies of factory production.
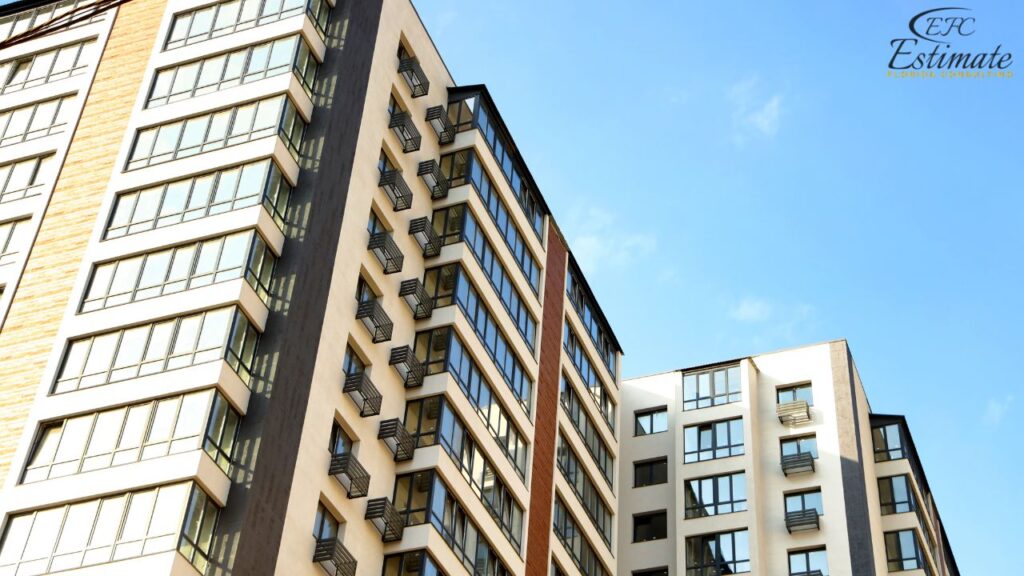
Commercial Construction Videos
Commercial Construction
Factory Construction
Work Shop Construction
Modular Construction
Overview
Modular construction involves pre-fabricating sections of the building in a factory setting and then assembling them on-site. This method is often used for office buildings, hotels, and schools, as it allows for faster construction times and less on-site disruption. By building in a controlled environment, modular construction can enhance quality control and reduce the risks associated with weather delays. Additionally, the modular approach allows for greater flexibility in design and the potential for future expansion.
Cost Breakdown
Cost Component | Estimated Cost per Sq Ft | Total Cost for 10,000 Sq Ft |
Site Preparation | $5 – $15 | $50,000 – $150,000 |
Foundation | $8 – $15 | $80,000 – $150,000 |
Modular Units | $100 – $200 | $1 million – $2 million |
Roofing | $5 – $10 | $50,000 – $100,000 |
Exterior Finishes | $10 – $20 | $100,000 – $200,000 |
Interior Finishes | $20 – $40 | $200,000 – $400,000 |
Total Estimated Cost | $148 – $290 | $1.48 million – $2.9 million |
Key Considerations for Modular Construction
While modular construction can result in higher upfront costs due to the price of pre-fabricated units, the overall time and cost savings during the construction phase can make it an attractive option. Stakeholders should consider the potential for reducing project timelines and labor costs when evaluating this method. Additionally, modular buildings are often easier to relocate or repurpose, which can provide added value over time.
Tilt-Up Construction
Overview
Tilt-up construction involves pouring concrete walls on-site and then lifting them into place. This method is commonly used for large commercial buildings, including warehouses and distribution centers, due to its ability to create sturdy structures quickly and efficiently. The process can significantly reduce labor costs and construction time, as multiple walls can be poured simultaneously. Additionally, tilt-up construction allows for greater design flexibility, enabling architects to create unique and functional building shapes.
Download Template For Commercial Building Project Breakdown
- Materials list updated to the zip code
- Fast delivery
- Data base of general contractors and sub-contractors
- Local estimators
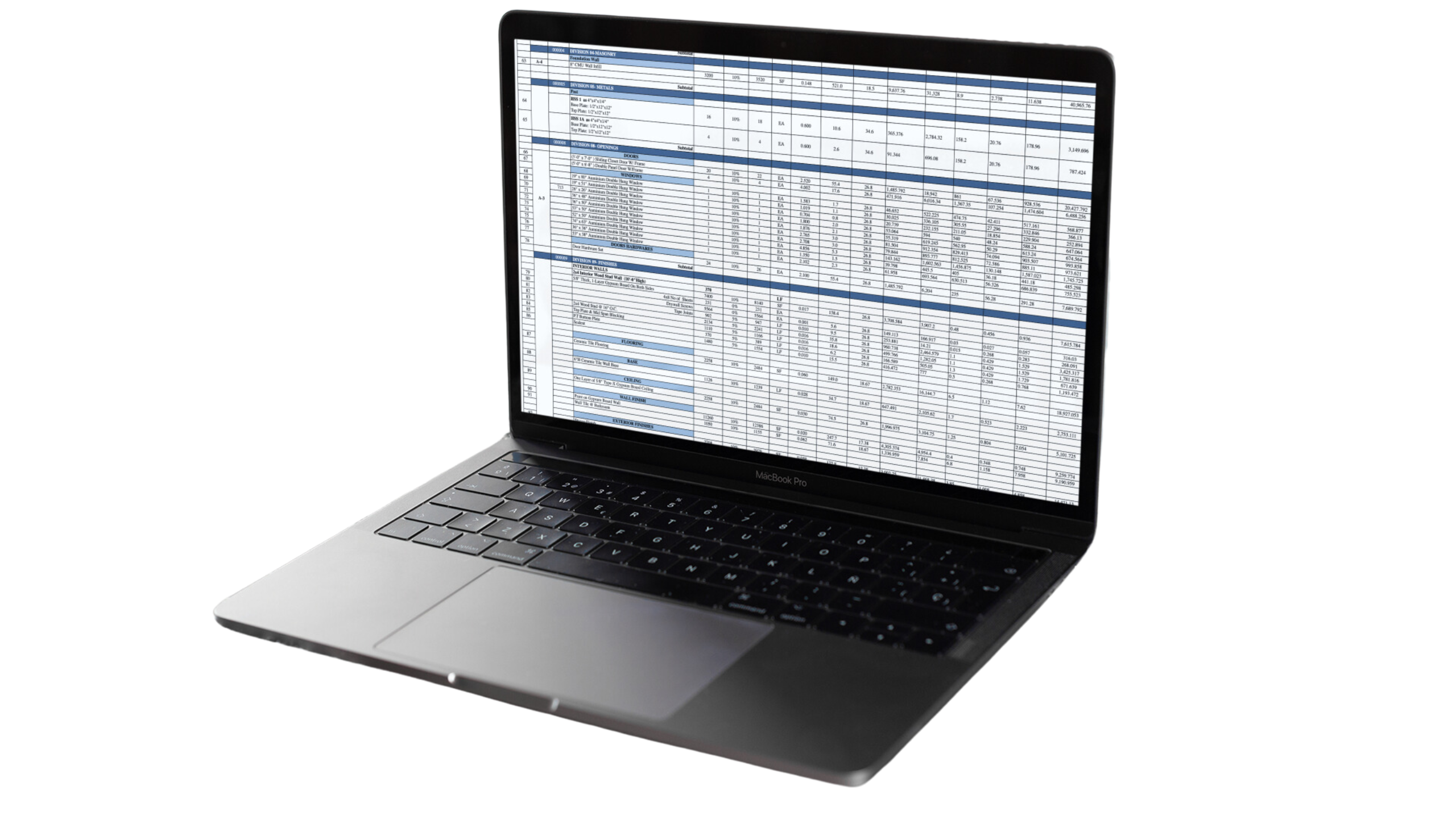
Cost Breakdown
Cost Component | Estimated Cost per Sq Ft | Total Cost for 10,000 Sq Ft |
Site Preparation | $5 – $15 | $50,000 – $150,000 |
Foundation | $10 – $20 | $100,000 – $200,000 |
Concrete Walls | $10 – $20 | $100,000 – $200,000 |
Roofing | $5 – $15 | $50,000 – $150,000 |
Exterior Finishes | $10 – $20 | $100,000 – $200,000 |
Interior Finishes | $20 – $40 | $200,000 – $400,000 |
Total Estimated Cost | $70 – $130 | $700,000 – $1.3 million |
Advantages of Tilt-Up Construction
While tilt-up construction can offer substantial savings in both time and cost, it is important to factor in the experience of the construction crew and the availability of specialized equipment for lifting the walls. Proper planning and execution are critical to the success of this construction method. Moreover, tilt-up buildings are often highly durable and require less maintenance over time, which can be advantageous for long-term ownership.
Green Building
Overview
Green building incorporates sustainable practices, energy-efficient systems, and environmentally friendly materials. This approach is becoming increasingly popular for new commercial constructions, as businesses and consumers alike seek to minimize their environmental impact. By using sustainable materials and energy-efficient technologies, green buildings can significantly reduce operational costs over time, making them a worthwhile investment. Furthermore, many municipalities offer incentives for green building practices, which can offset initial construction costs.
Cost Breakdown
Cost Component | Estimated Cost per Sq Ft | Total Cost for 10,000 Sq Ft |
Site Preparation | $5 – $15 | $50,000 – $150,000 |
Foundation | $10 – $20 | $100,000 – $200,000 |
Sustainable Materials | $10 – $30 | $100,000 – $300,000 |
Energy-Efficient Systems | $10 – $20 | $100,000 – $200,000 |
Roofing | $5 – $15 | $50,000 – $150,000 |
Interior Finishes | $20 – $40 | $200,000 – $400,000 |
Total Estimated Cost | $70 – $130 | $700,000 – $1.3 million |
Benefits of Green Building
In addition to cost savings, green buildings often provide improved indoor air quality and overall occupant comfort, making them more appealing to tenants and employees. Developers should consider the long-term benefits of investing in green technologies and materials, as these can enhance the building’s value and attract a more environmentally conscious clientele. Furthermore, buildings designed with sustainability in mind can often qualify for certification through programs like LEED (Leadership in Energy and Environmental Design), which can further enhance marketability and potential financial incentives.
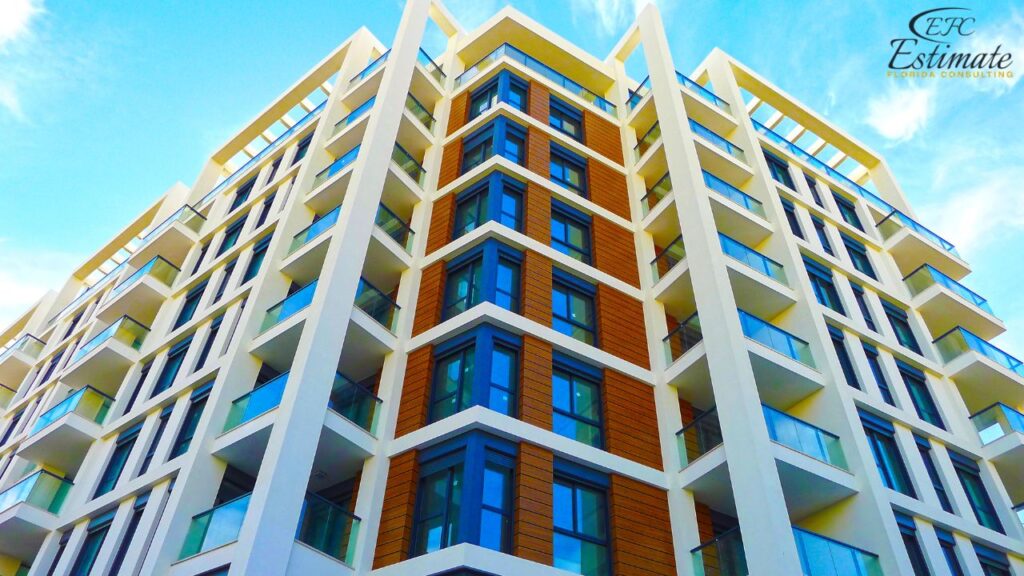
Commercial Construction Costs per Square Foot
When you’re planning the cost of building a commercial property, the type of construction you choose can make a big difference in your budget. Steel-frame buildings, for example, are durable and offer a lot of design flexibility, but they tend to be more expensive due to the cost of materials and labor. If you’re looking to save money, pre-engineered metal buildings might be a better choice. They’re generally cheaper and quicker to put up, making them a good option for more straightforward projects. Concrete buildings, while more costly initially, offer great fire resistance and low maintenance costs over time. Keep in mind that things like your location, the complexity of your design, and local labor rates will also affect your total costs. Understanding these factors can help you make smart choices and keep your project on budget.
Commercial Office Buildings
The cost of constructing office buildings in the US varies widely based on their size and type. For single-story office buildings, the adjusted average cost is approximately $407 per square foot. Mid-rise office buildings now average $730 per square foot, while high-rise buildings are the most expensive, with an average of around $858 per square foot.
Hospitality and Lodging
Construction costs for hotels and lodging facilities depend heavily on their star rating and location. Three-star hotels now cost about $621 per square foot to build. In contrast, five-star hotels are more costly, with an adjusted average construction price of around $899 per square foot.
Warehouses and Manufacturing Facilities
The cost of constructing warehouses and manufacturing facilities varies based on their specific functions. Regional distribution warehouses are relatively affordable at an average of $277 per square foot. Light industrial warehouses are somewhat more expensive, averaging around $309 per square foot. Technology laboratories are the priciest, with costs averaging about $825 per square foot.
Healthcare Facilities
Healthcare facilities are crucial in every community, and their construction costs reflect their complexity and purpose. Acute care facilities are the most expensive, averaging $1,326 per square foot. Medical office buildings are less costly at approximately $647 per square foot. Specialty clinics fall in between, with an average construction cost of $805 per square foot.
Schools and Universities
Educational institutions vary in cost based on their type and size. Constructing primary and secondary schools averages around $425 per square foot, with costs varying from $384 for elementary schools to $466 for high schools. Higher education facilities are more expensive; for example, regular classroom buildings average $754 per square foot, while laboratory buildings cost about $983 per square foot. University buildings are priced at approximately $775 per square foot, and dormitories are relatively more affordable at around $418 per square foot.
Retail
Retail shopping centers, including neighborhood strip centers and regional malls, can be quite costly. The adjusted average construction cost for a neighborhood strip center is $482 per square foot, whereas regional malls are more expensive, averaging $698 per square foot.
Parking Structures
Parking structures are among the least expensive commercial buildings to construct. An underground multi-level parking structure now costs about $186 per square foot, while an above-ground parking lot is significantly cheaper at approximately $93 per square foot.
Public and Community Facilities
Public and community facilities tend to be expensive due to their scale and the number of people they serve. Gymnasiums and recreational centers have an average construction cost of $524 per square foot. Government administration buildings are priced around $768 per square foot, while police stations cost about $754 per square foot. The most expensive public buildings include performing arts centers and museums, with an average cost of $1,159 per square foot.
Additional Considerations
Location
The geographical location of a commercial construction project plays a critical role in determining overall costs. Local labor rates can vary significantly from one region to another, influenced by the availability of skilled workers and demand for construction services. In urban areas with booming construction markets, labor costs may be substantially higher compared to rural locations.
Moreover, material availability can impact pricing. Regions with limited access to certain building materials may face increased transportation costs, leading to higher prices for those materials. For instance, if a project requires specialized steel or eco-friendly materials that aren’t readily available locally, the additional shipping fees and delays can escalate the overall budget. Additionally, land prices vary widely; purchasing land in a prime commercial district typically incurs higher costs than in less desirable locations, which can influence site preparation and foundation costs.
Market Conditions
The construction industry is subject to various market conditions that can affect costs unpredictably. Economic fluctuations can lead to changes in supply and demand for construction materials and labor. For example, during a construction boom, demand for materials like lumber, steel, and concrete may outstrip supply, driving prices up. Conversely, in a downturn, labor costs might decrease as companies compete for fewer projects, but this could also lead to potential delays as subcontractors may be less reliable.
Seasonal factors can also play a significant role. For instance, demand for construction services often peaks in the spring and summer months, resulting in higher costs and potential project delays due to overcrowded schedules. Conversely, winter months may see reduced activity, allowing for potentially lower costs but presenting challenges due to weather-related delays. Stakeholders should closely monitor market trends and economic indicators to anticipate potential impacts on their project budgets.
Regulatory Compliance
Compliance with local building codes and regulations is a crucial aspect of any commercial construction project. Each municipality has specific requirements governing construction practices, safety standards, zoning, and environmental impact. Failing to adhere to these regulations can lead to costly fines, delays, or even the halting of the project until compliance is achieved.
Investing time and resources in understanding and integrating regulatory requirements early in the planning phase is essential. This includes obtaining the necessary permits and inspections at various stages of construction. Additionally, projects that aim for sustainability certifications, such as LEED (Leadership in Energy and Environmental Design), may have additional requirements that can influence material choices and construction methods, potentially increasing costs. Engaging with local regulatory bodies and consulting with professionals experienced in navigating these complexities can help mitigate risks and ensure that the project proceeds smoothly.
Get 5 New Leads Next 7 Days With Our System
- Multi-Family House
- Single-Faimly House
- Modern House
- Duplex
- Ranch House
- Bungalow
Conclusion
Understanding the cost breakdown by construction type is crucial for successfully navigating the complexities of commercial building projects. Each method has its own unique advantages and considerations, which can significantly impact overall project costs and timelines. By carefully evaluating the various construction options and their associated costs, stakeholders can make informed decisions that align with their goals and budgetary constraints. Moreover, investing in the right construction method can lead to long-term benefits in terms of operational efficiency, tenant satisfaction, and overall building performance.
FAQs
Understanding construction costs is essential for effective budgeting and financial forecasting. Each construction method has unique costs and considerations that can significantly impact the overall project budget. A thorough analysis helps stakeholders make informed decisions and set realistic financial expectations.
The main construction types for commercial buildings include:
- Traditional Construction
- Pre-Engineered Metal Buildings
- Modular Construction
- Tilt-Up Construction
- Green Building
- Site Preparation: $5 – $15 per sq ft
- Foundation: $10 – $20 per sq ft
- Framing (Wood/Steel): $15 – $30 per sq ft
- Roofing: $5 – $15 per sq ft
- Exterior Finishes: $10 – $30 per sq ft
- Interior Finishes: $20 – $40 per sq ft
Total Estimated Cost: $95 – $150 per sq ft ($950,000 – $1.5 million for 10,000 sq ft)
Pre-engineered metal buildings allow for quick assembly, reduced labor costs, and structural integrity. They are ideal for large open spaces, often resulting in lower overall costs, faster project completion, and reduced maintenance expenses over time.
Modular construction may have higher upfront costs due to pre-fabrication but often results in time and labor savings during the construction phase. It offers greater flexibility in design and is easier to relocate or repurpose in the future.
- Site Preparation: $5 – $15 per sq ft
- Foundation: $8 – $15 per sq ft
- Modular Units: $100 – $200 per sq ft
- Roofing: $5 – $10 per sq ft
- Exterior Finishes: $10 – $20 per sq ft
- Interior Finishes: $20 – $40 per sq ft
Total Estimated Cost: $148 – $290 per sq ft ($1.48 million – $2.9 million for 10,000 sq ft)
Tilt-up construction is cost-effective and time-efficient, allowing for multiple walls to be poured simultaneously. It is highly durable and can offer significant savings on labor costs, but it requires careful planning and execution.
- Site Preparation: $5 – $15 per sq ft
- Foundation: $10 – $20 per sq ft
- Concrete Walls: $10 – $20 per sq ft
- Roofing: $5 – $15 per sq ft
- Exterior Finishes: $10 – $20 per sq ft
- Interior Finishes: $20 – $40 per sq ft
Total Estimated Cost: $70 – $130 per sq ft ($700,000 – $1.3 million for 10,000 sq ft)
Green buildings incorporate sustainable materials and energy-efficient systems, which can reduce operational costs over time. While initial construction costs may be higher, long-term savings and potential incentives make green buildings a worthwhile investment.
- Site Preparation: $5 – $15 per sq ft
- Foundation: $10 – $20 per sq ft
- Sustainable Materials: $10 – $30 per sq ft
- Energy-Efficient Systems: $10 – $20 per sq ft
- Roofing: $5 – $15 per sq ft
- Interior Finishes: $20 – $40 per sq ft
Total Estimated Cost: $70 – $130 per sq ft ($700,000 – $1.3 million for 10,000 sq ft)
Local labor rates, material availability, and land prices can significantly impact construction costs. Economic fluctuations and seasonal demand can also influence prices and project timelines. It is important to consider these factors when budgeting for a commercial construction project.
Compliance with local building codes and regulations is crucial to avoid fines and project delays. Understanding these requirements early in the planning phase can mitigate risks and help ensure that the project proceeds smoothly.
Google Reviews
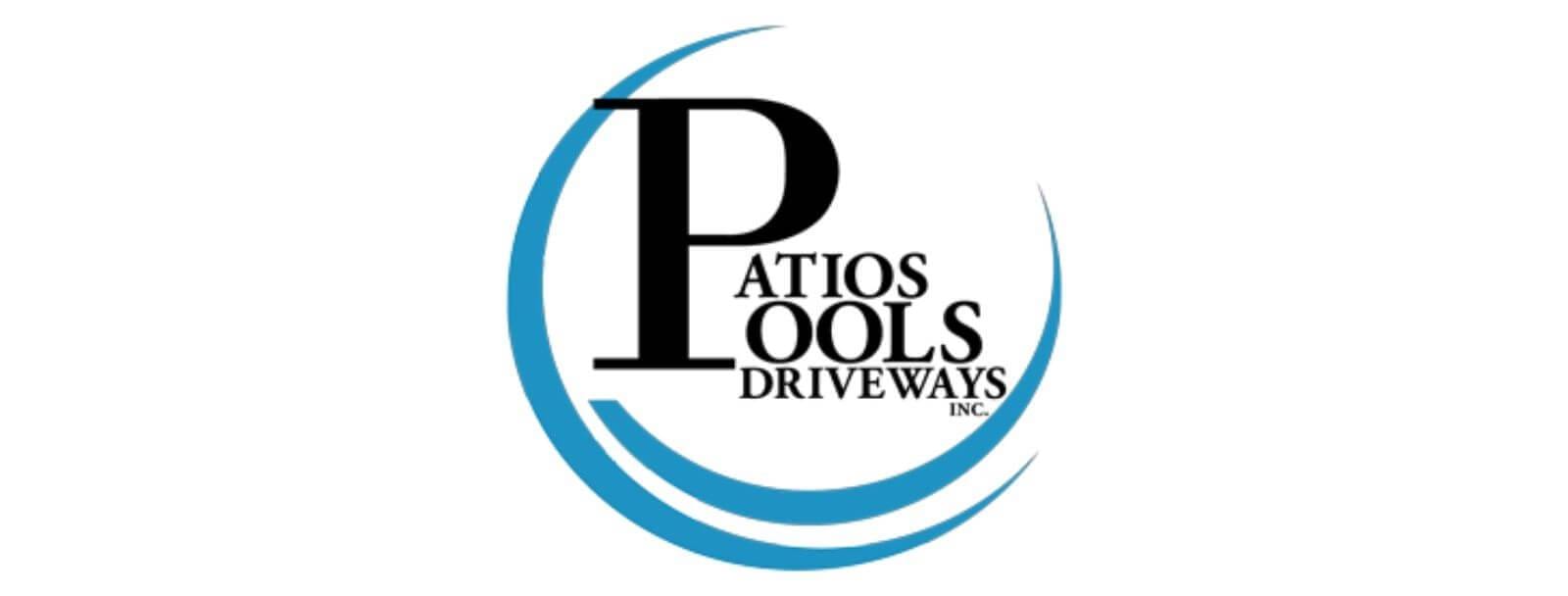
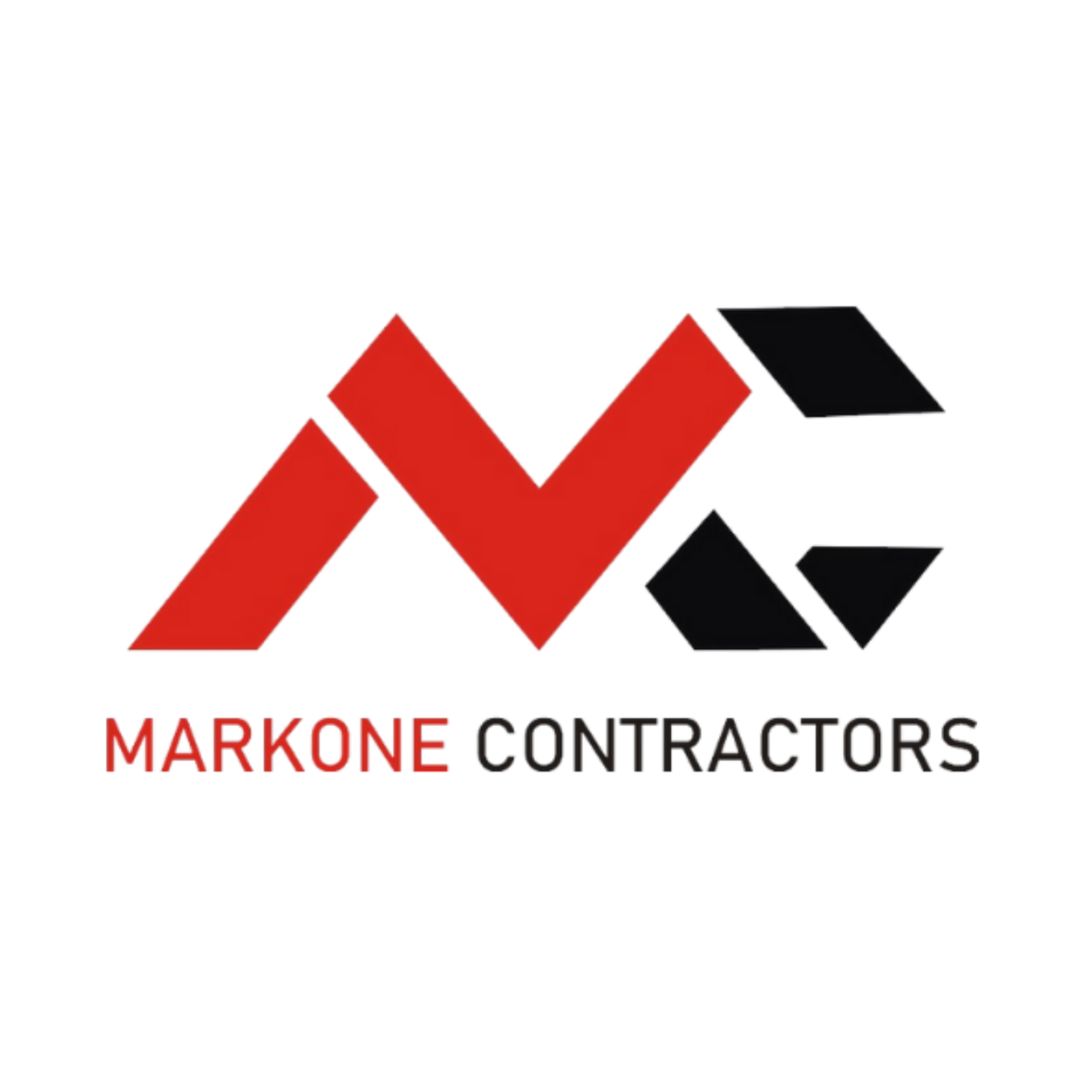

Process To Get Commercial Building Cost Estimate Report
Here I am going to share some steps to get commercial building cost estimate report.
-
You need to send your plan to us.
You can send us your plan on info@estimatorflorida.com
-
You receive a quote for your project.
Before starting your project, we send you a quote for your service. That quote will have detailed information about your project. Here you will get information about the size, difficulty, complexity and bid date when determining pricing.
-
Get Estimate Report
Our team will takeoff and estimate your project. When we deliver you’ll receive a PDF and an Excel file of your estimate. We can also offer construction lead generation services for the jobs you’d like to pursue further.