Building Material Estimator
In the world of construction, precision and accuracy are paramount, especially when it comes to estimating materials. The success of any building project relies heavily on the correct estimation of materials required. This article delves into the fascinating realm of building material estimation, guiding you through its importance, benefits, types, usage, and challenges, all while keeping it engaging and informative. Whether you’re a seasoned contractor or a DIY enthusiast, mastering the art of being a Building Material Estimator is essential for project success.
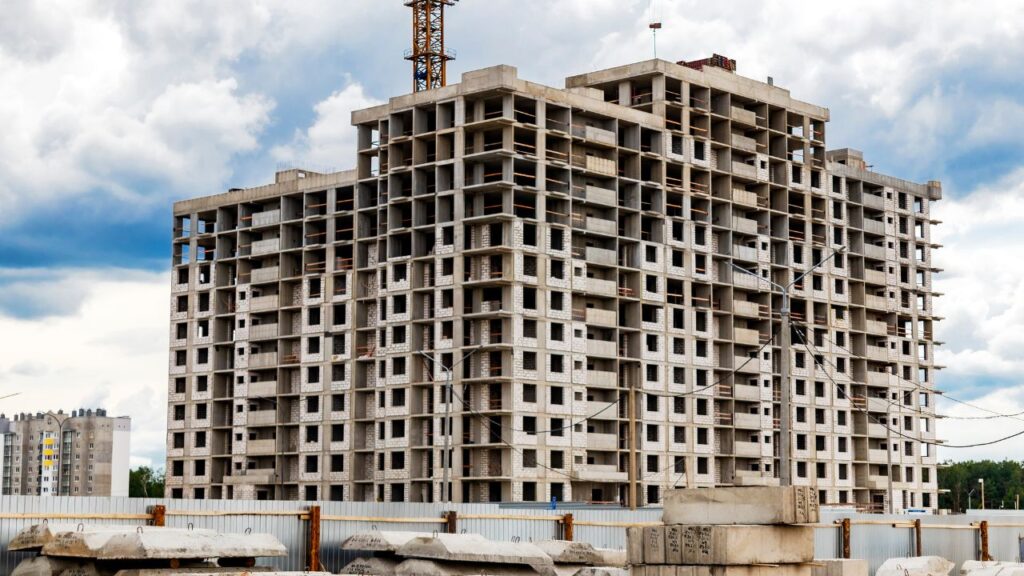
This skill can save you time and money while ensuring your construction project runs smoothly from start to finish. If you’re in Florida and looking for expert consulting in material estimation, be sure to reach out to Estimate Florida Consulting for top-notch guidance and assistance.
What does a materials estimate?
A materials estimate, also referred to as a quantity takeoff, a construction takeoff, or a material takeoff, involves extracting essential details from the blueprints regarding the necessary materials and their quantities for the construction project. In a material takeoff, the focus is solely on tallying the materials, while labor costs, equipment expenses, and other indirect costs are itemized separately in the overall construction estimate.
How to Estimate Construction Materials for a Project
Before commencing the material estimation process, you’ve already determined the project’s feasibility and decided to move forward. Now, let’s delve into the detailed estimation procedure.
Identify Required Materials:
The initial step involves identifying the materials necessary to complete the project. For most construction projects, this often begins with a site visit to address site-specific conditions and potential additional material requirements. Keep in mind that even two projects based on the same blueprint may differ due to the unique worksite. It’s crucial to account for all required materials when estimating project costs.
Select the Right Products:
Part of the cost estimation process is selecting the appropriate raw materials and products for your house or building project. Consider factors like client preferences for eco-friendly products, the need for specific products to enhance site drainage, regional regulations, and product availability. Product delivery timelines and urgency should also influence your product choices. Utilizing estimating software can assist in pricing products using your dealer’s price lists.
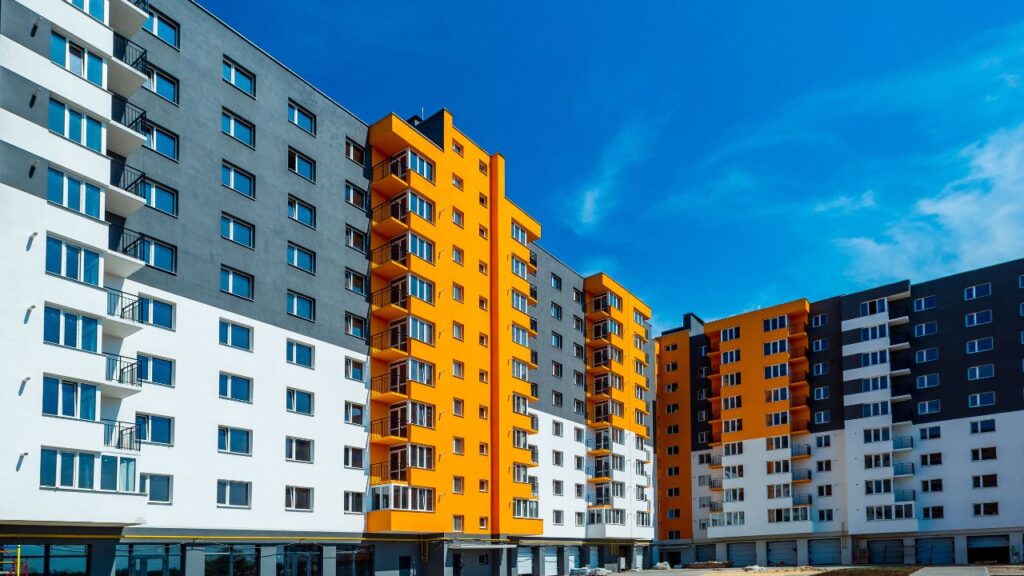
Calculate Material Quantities:
Once you’ve determined the best-suited materials for the project, it’s time to quantify and calculate their costs. Begin with your project’s blueprints and initiate a quantity takeoff.
Count: Every product, such as air conditioners, ovens, or windows, is counted individually, while items like nails, lightbulbs, or hinges are counted by unit or box.
Length: Materials like lumber, pipes, or cornices are measured by length. Ensure you cover your project’s needs without excessive waste.
Area: Products like carpet, paint, or tiles that require coverage are calculated using length x width.
Volume: Materials like concrete or landfill are measured by volume, specifically length x width x depth, which provides the cubic foot, cubic yards, or cubic meter measurements.
Calculate Material Costs:
After determining the required material quantities, square footage, and other measurements, it’s essential to ascertain the material prices. If you’re conducting your takeoff manually, you’ll need to research or have prior knowledge of material prices. Alternatively, software can provide access to cost lists and databases. Remember to account for potential price fluctuations due to inflation, especially if the estimate pertains to a future project.
By following these steps, you can effectively estimate construction materials for your project, ensuring accurate and comprehensive cost projections.
The Basic Estimations
Listed below are the most effective methods for calculating quantities of common building materials. For most of these materials, it is crucial to ascertain three key pieces of information:
The method of sale (e.g., by the cubic yard, per piece, in bundles, by sheets, etc.).
The dimensions or coverage provided by each unit of the product (e.g., 4’x8′ sheets, packs covering 10 sq. ft., etc.).
The price per unit of the product.
Once you have gathered this data, you can proceed with your price estimations.
PRO TIP! – As you will observe, many of these materials necessitate the calculation of the total square footage of a given area. While you can perform this manually, it can be time-consuming. The most efficient method is to employ a home design program. Which automates square footage calculations for you.
Concrete
Delivered premixed concrete is typically sold by the cubic yard. To determine the required cubic yardage, you can utilize the following formula:
Length x Width x Thickness / 27 = Cubic yards for a rectangular pad, beam, or column.
For example, if you intend to pour a concrete pad measuring 24′ x 12′ x 6″ in thickness:
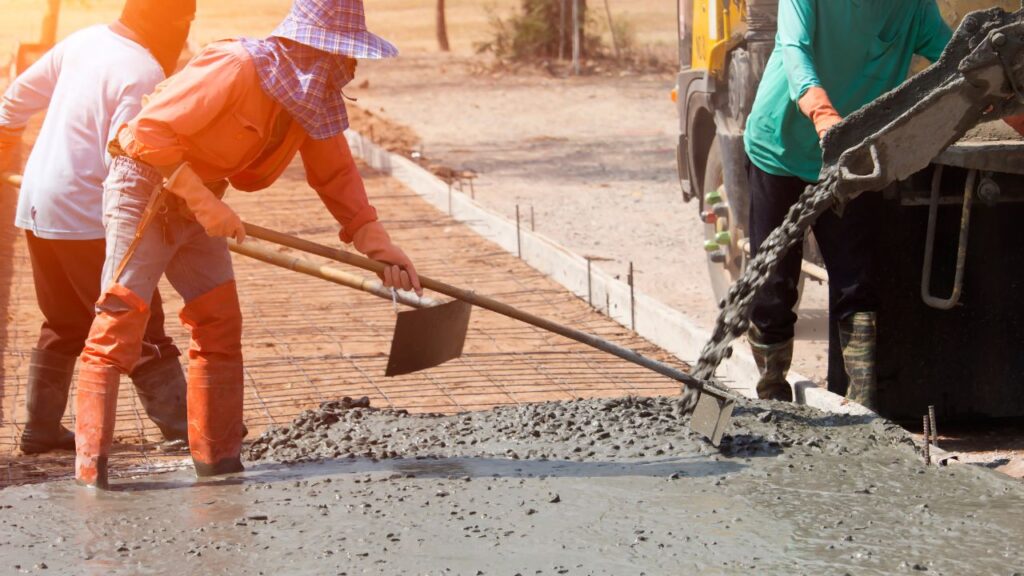
24′ x 12′ x 0.5′ = 144 cubic feet.
144 / 27 = 5.33 cubic yards of concrete.
Like most materials, it’s advisable to add approximately 10% extra to account for potential waste. A simple way to do this is by multiplying the total by 1.10:
5.33 x 1.10 = 5.86 cubic yards.
Depending on the supplier, you might have the option to order by the ¼ yard. Therefore, you could choose either 5.75 or 6 cubic yards, depending on the desired margin of extra material.
Finally, take your last calculation and multiply it by the prevailing price per cubic yard.
PRO TIP! – For smaller projects where you plan to purchase and mix your own concrete by the bag, Quickrete and Sakrete offer an online building materials calculator that helps you determine the number of bags of concrete needed. You only need to know the square footage or the size of the column you intend to pour.
Lumber
While standard-size lumber pieces are typically sold individually, many lumberyards sell hardwood lumber and pieces of random dimensions by the board foot. To calculate board feet for a piece of lumber, use the following formula:
Thickness (in) x Width (in) x Length (ft) / 12 = Board Feet (bf).
For instance, if you need to purchase a piece of lumber measuring 4″ x 10″ x 8′:
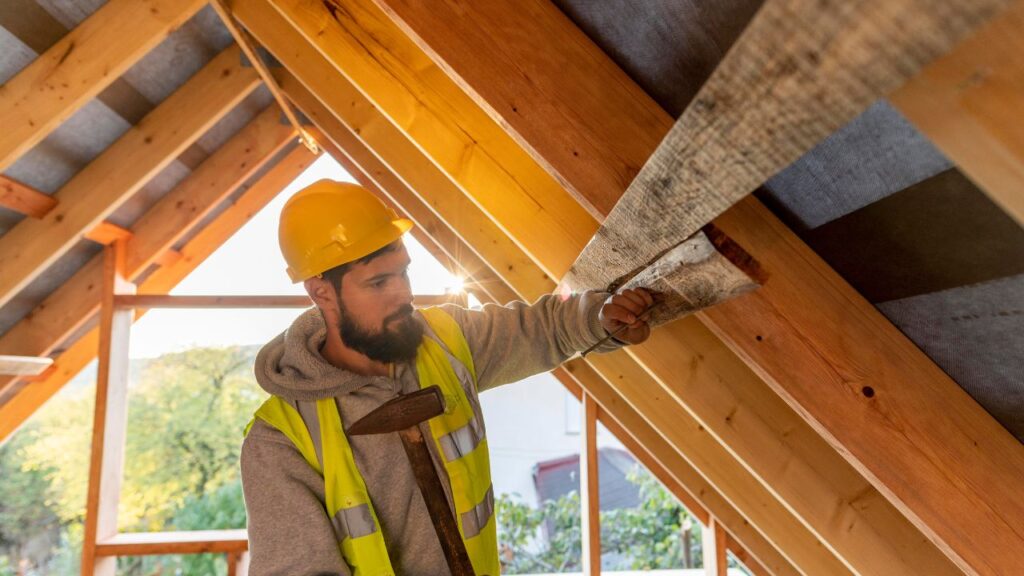
4 x 10 x 8 = 320
320 / 12 = 26.67 board feet.
Next, simply multiply this quantity by the current price per board foot for that particular type of lumber to obtain an estimate of the total cost.
Wall Sheathing
When estimating the requirements for drywall or other wall sheathing, the process begins with determining the total square footage of the surface to be covered.
Then, simply divide that overall figure by 32 (for 4’x8′ sheets) or by 48 (for 4’x12′ sheets).
For instance, if the total square footage amounts to 1,000 square feet, you will need:
1,000 / 32 = 31.3 (4’x8′ sheets)
1,000 / 48 = 20.8 (4’x12′ sheets)
To factor in additional material and potential waste, multiply this number by 1.10. Afterward, multiply the result by the price per sheet.
Framing
Determining the quantity of 2x4s or 2x6s required for framed walls involves the following steps:
Calculate the combined total length of all the walls.
Multiply the total length in feet by 0.75 (for 16-inch on-center spacing).
Add extra studs for each corner, wall intersection, and wall opening.
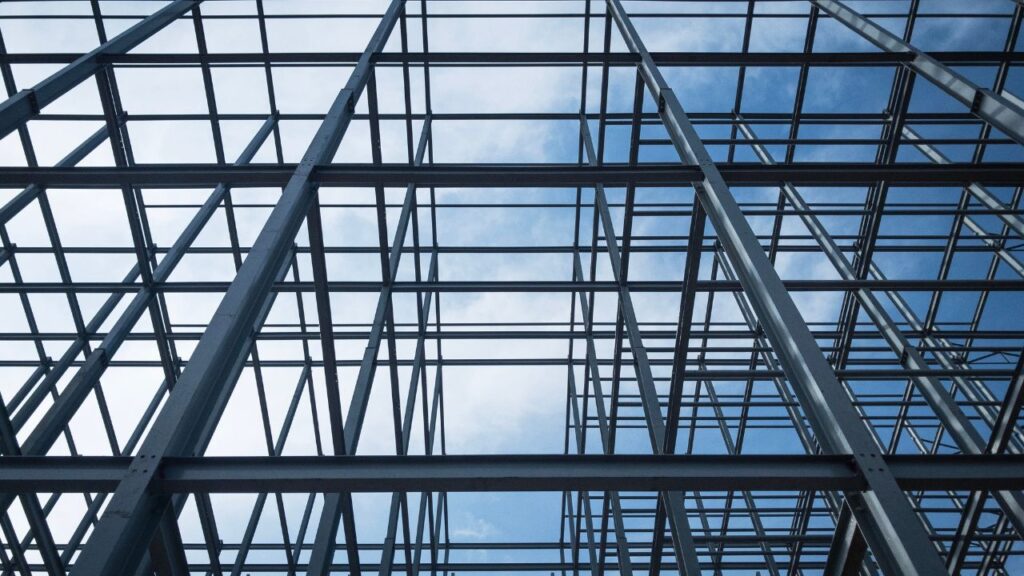
Calculate the top and sill plates by multiplying the total length by 3 and dividing by the length of the boards.
Multiply the total by 1.15 to account for waste and any additional material needed for blocking, sills, or other elements.
Roofing
Roof sizes are typically measured in “squares.” To determine the number of squares your roof requires, divide the total square footage of the roof by 100.
For example, if your roof covers 2,000 square feet, it is equivalent to 20 squares.
For shingled roofs, it usually takes 3 bundles of shingles to cover one square, and one roll of tar paper typically covers 4 squares. Always verify the specifications for each product.
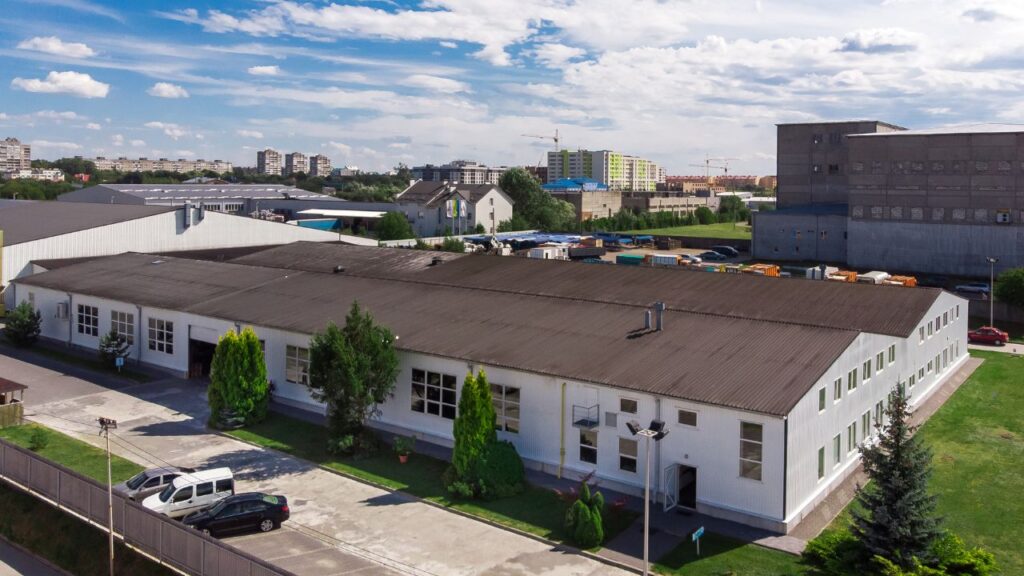
20 x 3 = 60 bundles of shingles
20 / 4 = 5 rolls of tar paper
To determine the total amount of drip edge required, measure the eaves and the rakes. Then, take your final calculations and multiply them by the price per product.
Case Study: Successful Building Material Estimation
In this illustrative case study, we delve into the real-life intricacies of a construction project that exemplifies the paramount importance of precise building material estimation. This project serves as a beacon of insight, showcasing how meticulous planning, coupled with advanced estimation techniques, can yield remarkable outcomes in the construction industry.
The chosen construction endeavor encompasses various facets, including architectural design, structural engineering, and project management. We’ll explore the challenges faced by the project team and how their adept material estimation played a pivotal role in surmounting these challenges. Detailed accounts of material selection, procurement, and utilization will underscore the project’s efficiency and resource optimization.
Furthermore, we will dissect the strategies and technologies employed in achieving unparalleled accuracy in material estimation. This case study offers a unique opportunity to gain practical insights into the world of construction, underlining the significance of meticulous material estimation in enhancing project timelines, budgets, and overall success.
FAQs for Building Material Estimator Blog:
A materials estimate, also known as a quantity takeoff, is the process of determining the necessary materials and their quantities for a construction project. It involves extracting essential details from blueprints and itemizing the materials required, excluding labor costs and other indirect expenses.
Accurate material estimation is crucial in construction because it ensures that you have the right amount of materials for your project. It helps prevent shortages or excess waste, saving both time and money. Additionally, it contributes to the overall success of the construction project.
To estimate construction materials for your project, follow these steps:
- Identify required materials.
- Select the right products, considering factors like regulations and client preferences.
- Calculate material quantities based on blueprints.
- Calculate material costs, considering factors like inflation.
By following these steps, you can create accurate and comprehensive cost projections for your project.
- Concrete: Calculate the required cubic yardage based on length, width, and thickness.
- Lumber: Determine board feet by using the formula: Thickness x Width x Length / 12.
- Wall Sheathing: Divide the total square footage by sheet dimensions (e.g., 4’x8′ or 4’x12′) to calculate the number of sheets needed.
- Framing: Calculate the total length of walls, add extra studs for corners and openings, and account for plates and waste.
- Roofing: Measure roof area in “squares” and determine the number of shingle bundles and tar paper rolls needed.
Factoring in additional materials and potential waste is important to account for unforeseen circumstances, errors in measurement, or any material that may be damaged or unusable. It helps ensure that you have enough materials to complete the project.
- Utilize estimating software for efficient calculations.
- Consider potential price fluctuations due to inflation.
- Collaborate with suppliers and manufacturers for the most accurate pricing information.
- Always add a margin for extra material to account for waste and unexpected changes.
Estimating construction materials is a valuable skill for both contractors and DIY enthusiasts. Whether you’re building a small project at home or overseeing a large construction site, accurate material estimation can help you save time and money while ensuring a successful outcome.
Precise material estimation helps streamline project timelines by ensuring that materials are readily available when needed, reducing delays. It also plays a significant role in managing project budgets by preventing over-purchasing or material shortages, ultimately contributing to the project’s overall success.
If you’re in Florida and looking for expert consulting in material estimation, you can reach out to Estimate Florida Consulting for top-notch guidance and assistance. They can provide you with the expertise and support needed to ensure your project’s success through accurate material estimation.
In conclusion
Accurate building material estimation is the cornerstone of successful construction projects. Whether you’re a seasoned contractor or a DIY enthusiast, mastering the art of material estimation is essential. It ensures you have the right amount of materials, prevents costly delays, and helps manage project budgets effectively. This blog has guided you through the importance, benefits, types, and challenges of material estimation, providing practical insights and tips. By following the steps outlined here and considering factors like potential waste and price fluctuations, you can create precise and comprehensive cost projections for your construction projects. Remember, whether you’re in Florida or anywhere else, expert consulting, like that offered by Estimate Florida Consulting, can be invaluable for ensuring your project’s success through accurate material estimation. So, embrace the world of material estimation, and build with confidence.
Process To Get Building Replacement Cost Estimate Report
Here I am going to share some steps to get your building replacement cost estimate report.
-
You need to send your plan to us.
You can send us your plan on info@estimatorflorida.com
-
You receive a quote for your project.
Before starting your project, we send you a quote for your service. That quote will have detailed information about your project. Here you will get information about the size, difficulty, complexity and bid date when determining pricing.
-
Get Estimate Report
Our team will takeoff and estimate your project. When we deliver you’ll receive a PDF and an Excel file of your estimate. We can also offer construction lead generation services for the jobs you’d like to pursue further.
Google Reviews
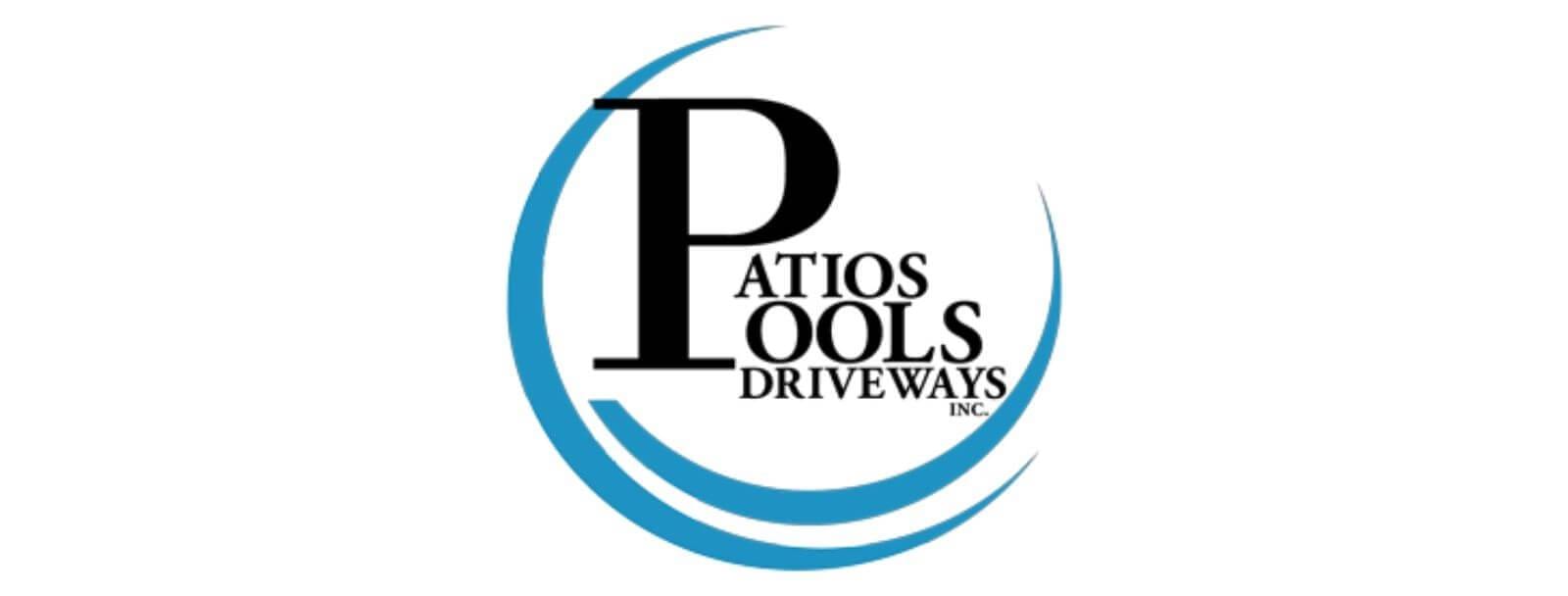
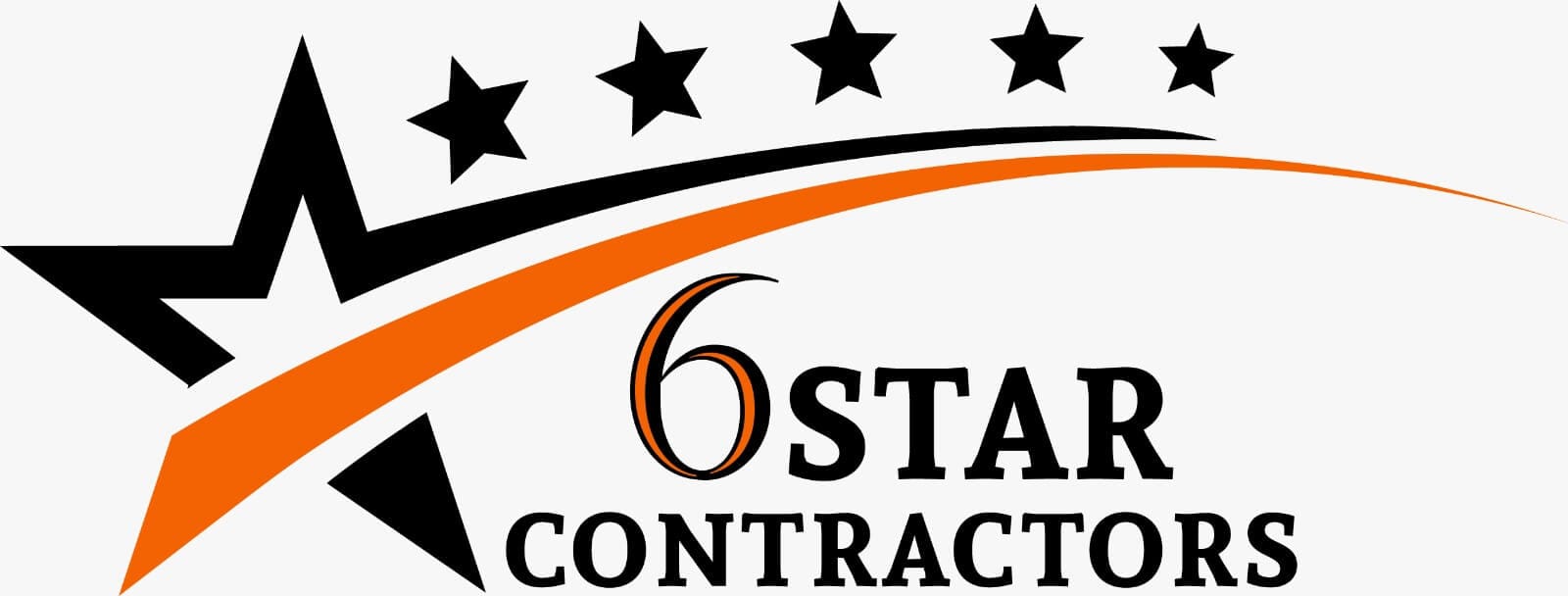
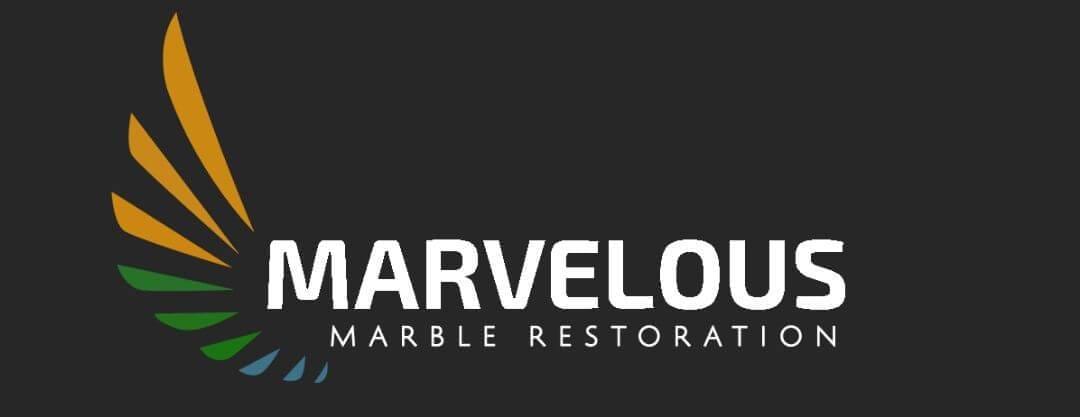