Boost Your Apartment Building Bids – Request a Precision Estimate!
- Accurancy
- Efficiency
- Transparency
- Customization
- Time Saving
- Professionalism
- Cost Control
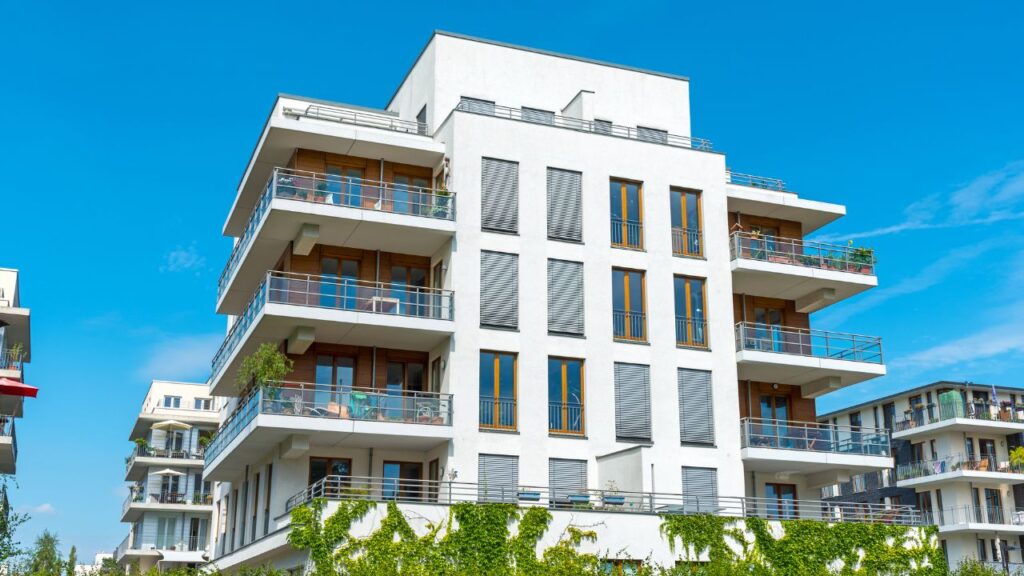
The cost of constructing an apartment building with a concrete structure is highly variable, contingent on numerous factors. In less expensive or rural areas, the construction cost may range from $100 to $150 or more per square foot for a basic structure. Moving into average-cost regions or buildings with additional features, costs could fall within the range of $150 to $250 or more per square foot. In high-cost urban areas or luxury developments, the cost per square foot may exceed $250. It’s essential to note that these estimates often exclude ancillary costs such as land acquisition, permits, professional fees, landscaping, and interior finishes.
The intricacy of architectural and engineering designs, coupled with load-bearing specifications, plays a pivotal role in determining the quantity and type of structural concrete required for an apartment building. More complex designs or higher load-bearing demands may necessitate the use of specialized concrete mixes tailored to meet specific structural requirements. This complexity not only influences material selection but also impacts overall construction costs, as it requires a meticulous approach to ensure that the concrete can withstand the unique stresses and forces imposed by the building’s design.
Fully Insured Licensed
Hire Builder For Apartment Building
Make Informed Design Decisions Showcase Your Design Ideas
Get RenderingCritical to the construction process is the careful consideration of concrete mix design and strength. The choice of the concrete mix is a key factor in determining the overall cost of the project. Depending on the structural demands, higher-strength concrete or specialty mixes may be required. These mixes often involve a precise combination of cement, aggregates, and potentially additives to achieve the desired characteristics. Local availability of materials also factors into the cost, as obtaining specific components may involve additional expenses. Consequently, the decision on concrete mix design directly influences the durability, longevity, and financial aspects of the construction project.
Labor costs for concrete slab construction in apartment buildings can vary depending on location, project complexity, local labor rates, and the required skill level. Typically encompassing site preparation, formwork installation, concrete placement, finishing, and curing, these costs are estimated based on the labor hours needed for each stage. In less expensive or rural areas, labor costs may range from $4 to $8 or more per square foot of concrete slab, while in average-cost regions, the range could be $8 to $12 or more per square foot. High-cost urban areas or projects with specialized finishes may see labor costs exceeding $12 per square foot. These estimates are general and subject to variations based on local market conditions, labor experience, and project specifics.
The cost associated with reinforcement materials, including steel rebar and post-tension cables, constitutes a substantial portion of the construction budget. On average, the price of steel rebar ranges from $0.50 to $0.80 or more per pound, and post-tension cables can cost between $0.70 to $1.50 or more per linear foot. The quantity and type of reinforcement required are contingent on the structural design and local building codes, with material expenses alone accounting for approximately 5% to 15% of the total construction cost.
In addition to material costs, skilled labor for the installation process contributes to the overall expense, with labor expenses typically ranging from $8 to $15 or more per square foot of reinforced area. Despite the upfront investment, the inclusion of reinforcement materials is imperative for ensuring the structural integrity and long-term durability of the building, potentially minimizing future maintenance costs.
The choice of foundation type, whether it be a slab-on-grade, basement, or crawl space, significantly influences costs. Each foundation type has distinct requirements concerning concrete volume, excavation, and labor. For instance, a basement foundation typically involves more extensive excavation and concrete usage than a slab-on-grade foundation. The decision on the foundation type must align with both structural and budgetary considerations, as it directly affects the overall cost and feasibility of the construction project.
Foundation Type | Cost Range (per sq. ft.) |
Slab-on-Grade | $4 – $7 or more |
Basement | $10 – $25 or more |
Crawl Space | $8 – $16 or more |
The construction process involves several stages, each crucial for the overall success of the project:
The initiation of the construction process commences with meticulous site preparation. This multifaceted phase involves clearing the designated land, a task that includes removing any existing structures, vegetation, or debris. Following clearance, grading is undertaken to ensure a level foundation, crucial for the stability of the upcoming structure. Environmental concerns are addressed, incorporating measures to safeguard the surrounding ecosystem. Excavation might be necessary to create the necessary space for the building’s foundation, involving the removal of soil and rock to accommodate the forthcoming structural elements. This initial groundwork sets the stage for subsequent construction phases, laying the foundation—both figuratively and literally—for the entire project.
From small to large projects, residential to commercial, we’re here to help you win. Fast results guaranteed.
Central to the success of any construction project is the meticulous design of the foundation. Engineers, drawing upon expertise in geotechnical and structural engineering, undertake a comprehensive assessment of the soil conditions. This analysis informs the choice of foundation type—whether it be a slab-on-grade, basement, or crawl space. Load-bearing requirements and adherence to local building codes guide the engineers in formulating a foundation design that provides the necessary support and stability for the structure. The foundation design phase is integral, serving as the blueprint for subsequent construction activities.
A critical determinant of the structural integrity of the building is the concrete mix design. During this phase, engineers collaborate to specify the appropriate mix characteristics based on the structural requirements of the project. Factors such as strength, durability, and workability are carefully considered to ensure the resulting concrete meets the demands of the construction. The selection of materials, proportions, and potential additives is fine-tuned, reflecting a bespoke mix designed to withstand the anticipated forces and conditions the structure will encounter.
Enhancing the tensile strength of the concrete is a pivotal step in the construction process, achieved through the strategic installation of steel reinforcement. Commonly in the form of rebar or post-tension cables, these materials are meticulously placed within the concrete forms. The placement follows the predetermined design, with the aim of fortifying the concrete against various forces and potential stresses. The precision and accuracy in the installation of reinforcement materials are paramount, directly impacting the overall structural integrity of the building.
Formwork construction is the next crucial step, involving the creation of molds that will shape the concrete into the desired structure. These molds can be constructed using diverse materials such as wood, metal, or plastic, chosen for their ability to withstand the immense pressure exerted by the wet concrete. The design of the formwork aligns with the architectural and engineering specifications, ensuring that the concrete will take on the intended shape and configuration.
With the foundation prepared, the meticulously designed concrete mix is prepared and transported to the construction site. This mixture is poured into the intricately crafted formwork. The pouring process requires precision and attention to detail to guarantee uniform distribution and to eliminate potential imperfections, such as air pockets or voids, within the concrete. This phase is a critical juncture, marking the transformation of architectural plans into tangible construction reality.
Post-pouring, the concrete undergoes a crucial curing process aimed at optimizing its strength and durability. Various curing methods may be employed, including wet curing or the application of curing compounds. During this period, the concrete sets, gains strength, and matures to meet the specified design requirements. The curing phase is essential for ensuring the long-term resilience and performance of the concrete.
After the concrete has undergone sufficient curing and attained the requisite strength, the formwork is methodically removed. This unveils the finished structure of the foundation or other structural elements, providing a tangible representation of the architectural vision. The removed formwork, often constructed from reusable materials, can be recycled or repurposed for subsequent construction phases, aligning with sustainable construction practices.
Rigorous quality control measures are implemented throughout the construction process to uphold the highest standards of construction. The concrete undergoes comprehensive testing, evaluating properties such as compressive strength and workability. These tests are instrumental in verifying the structural integrity of the concrete, ensuring it aligns with the engineering and architectural specifications. Adherence to stringent quality control protocols is paramount to the success of the construction project.
With the foundation firmly in place, construction seamlessly progresses to the superstructure—the part of the building above the foundation. This phase encompasses the framing and construction of the apartment building, extending the structural concrete work to supporting elements such as columns, beams, and slabs throughout the entire structure. The foundation serves as the robust base upon which the superstructure flourishes, with the entire construction team collaborating to bring the architectural vision to fruition. Coordination, adherence to safety protocols, and ongoing quality control remain pivotal as construction continues toward the completion of the apartment building.
Achieving cost efficiency in apartment building structural concrete construction involves strategic planning and implementation of various strategies:
Achieving cost savings in apartment building structural concrete begins with a meticulous focus on optimizing the concrete mix design. Engineers and concrete specialists must meticulously tailor the mix to align with the specific structural requirements of the project. This involves a careful balance between utilizing locally available aggregates and considering alternative cementitious materials. The aim is to attain the desired strength and durability without incurring unnecessary material costs. By leveraging the availability of local resources and exploring innovative mix compositions, project teams can enhance cost-efficiency while ensuring that the concrete meets or exceeds performance expectations.
The implementation of a value engineering approach stands as a cornerstone for achieving cost-effective alternatives without compromising the structural integrity of the building. This collaborative process involves close coordination among architects, engineers, and contractors to explore innovative design solutions, alternative materials, and construction methods. By scrutinizing each element of the project, from the choice of materials to construction processes, value engineering seeks to identify opportunities for cost savings. The goal is to streamline project costs without sacrificing quality, resulting in a more efficient and budget-conscious construction endeavor.
Investing in efficient and reusable formwork systems represents a strategic move to optimize material costs over multiple construction cycles. High-quality, reusable formwork not only reduces the need for frequent replacements but also minimizes material waste. Moreover, an additional avenue for cost savings lies in the optimization of formwork design. By strategically minimizing the complexity of molds and support structures, construction teams can further economize on both material and labor costs. This dual-pronged approach to formwork underscores the importance of sustainable and cost-conscious construction practices.
A pivotal strategy for cost savings involves the judicious sourcing of construction materials from local suppliers. This practice mitigates transportation costs associated with hauling materials over long distances. By leveraging locally available aggregates, cement, and reinforcement materials, construction projects can significantly reduce expenses and enhance overall cost-effectiveness. Establishing strong partnerships with local suppliers not only ensures a steady and reliable supply chain but also facilitates negotiations for favorable pricing, contributing to streamlined logistics and optimized project budgets.
Embracing advanced construction technologies, such as Building Information Modeling (BIM) and computer-aided design, brings a new dimension to cost-saving strategies. These technologies play a pivotal role in enhancing efficiency in project planning and execution. By utilizing BIM, project teams can identify potential cost-saving opportunities, optimize construction schedules, and improve overall project coordination. The integration of such technologies is not just a technological upgrade but a strategic investment in the precision and efficiency of construction processes, resulting in tangible savings throughout the project lifecycle.
The exploration of prefabrication and modular construction methods introduces a paradigm shift in cost-saving strategies. Prefabricated concrete components, produced under controlled conditions offsite, offer numerous advantages. This approach minimizes material waste, reduces labor costs, and accelerates construction timelines. By capitalizing on the benefits of offsite manufacturing, construction projects can achieve economies of scale, achieving both efficiency and cost-effectiveness. The shift toward prefabrication aligns with modern construction trends, emphasizing sustainability and financial prudence.
Efficient project management practices are pivotal in streamlining the construction timeline and realizing significant cost savings. By minimizing unnecessary delays and optimizing construction schedules, project teams can reduce labor costs associated with prolonged projects. Strategies such as parallel construction activities, where different phases of construction occur simultaneously, can expedite timelines and contribute to overall cost-effectiveness. The optimization of the construction timeline is not merely a logistical consideration but a strategic move to enhance efficiency, reduce overheads, and deliver projects within budget constraints.
The cost of constructing an apartment building with a concrete structure is a multifaceted consideration influenced by various factors such as location, design complexity, and material choices. Cost-saving strategies, including optimized concrete mix design, value engineering, efficient formwork systems, local material sourcing, advanced construction technologies, prefabrication, and construction timeline optimization, play pivotal roles in achieving budgetary efficiency. Balancing innovation, sustainability, and meticulous planning is key to delivering a structurally sound and cost-effective apartment building.
In less expensive or rural areas, costs range from $100 to $150 or more per square foot for basic structures. In average-cost regions, it could be $150 to $250 or more, and in high-cost urban areas or luxury developments, it may exceed $250.
More intricate designs or higher load-bearing demands may require specialized concrete mixes, influencing both material selection and overall construction costs.
Labor costs vary based on location, project complexity, and skill level. In less expensive areas, it may range from $4 to $8 or more per square foot, while high-cost urban areas may see costs exceeding $12 per square foot.
Steel rebar ranges from $0.50 to $0.80 or more per pound, and post-tension cables can cost between $0.70 to $1.50 or more per linear foot. Material expenses, along with skilled labor for installation, typically account for 5% to 15% of total construction costs.
The choice of foundation type, such as slab-on-grade, basement, or crawl space, significantly influences costs. Slabs range from $4 to $7 or more per square foot, basements from $10 to $25 or more, and crawl spaces from $8 to $16 or more.
Here I am going to share some steps to get your apartment building structural concrete cost estimate report.
You can send us your plan on info@estimatorflorida.com
Before starting your project, we send you a quote for your service. That quote will have detailed information about your project. Here you will get information about the size, difficulty, complexity and bid date when determining pricing.
Our team will takeoff and estimate your project. When we deliver you’ll receive a PDF and an Excel file of your estimate. We can also offer construction lead generation services for the jobs you’d like to pursue further.
561-530-2845
info@estimatorflorida.com
Address
5245 Wiles Rd Apt 3-102 St. Pete Beach, FL 33073 United States
561-530-2845
info@estimatorflorida.com
Address
5245 Wiles Rd Apt 3-102 St. Pete Beach, FL 33073 United States
All copyright © Reserved | Designed By V Marketing Media | Disclaimer