Boost Your Apartment Building Bids – Request a Precision Estimate!
- Accurancy
- Efficiency
- Transparency
- Customization
- Time Saving
- Professionalism
- Cost Control
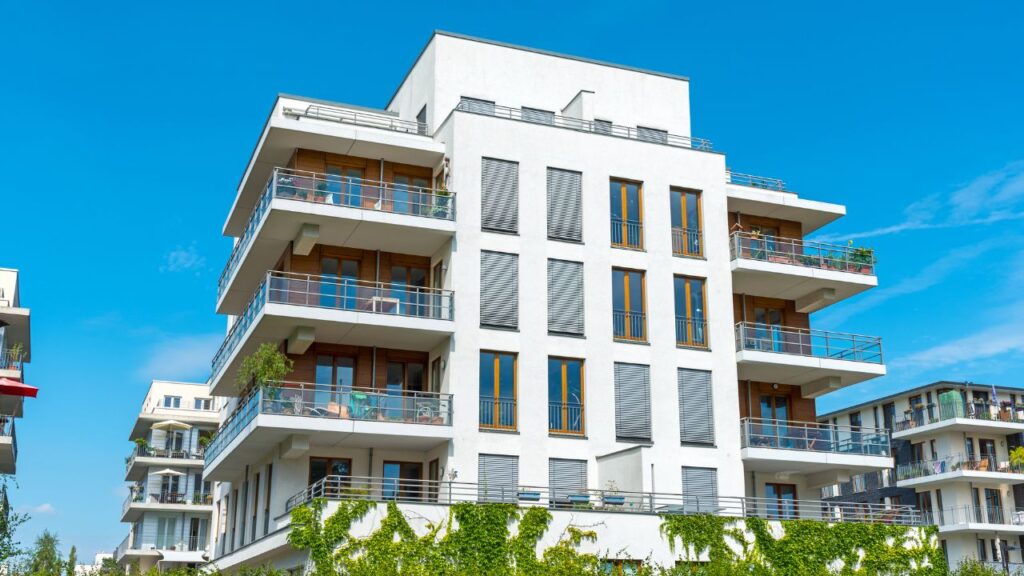
Embarking on the construction journey of apartment buildings involves navigating a complex landscape, and one of the critical considerations is the cost of concrete, a cornerstone that significantly impacts the overall budget. As an indispensable element in contemporary construction, concrete stands as a symbol of durability, strength, and versatility. For developers, contractors, and investors immersed in apartment building projects, a comprehensive understanding of the myriad factors influencing concrete costs is imperative for precise financial planning.
This article delves into these influential factors, shedding light on the intricacies of budgeting, and provides a general cost range. Typically, the cost of concrete in apartment building construction falls within the range of $90 to $120 per cubic yard, offering pragmatic insights for stakeholders navigating the realms of successful and cost-effective construction.
Fully Insured Licensed
Hire Builder For Apartment Building
Make Informed Design Decisions Showcase Your Design Ideas
Get RenderingApartment building construction involves considering various factors, and the concrete cost is a significant component. Please note that the costs provided are estimates and can vary based on location, project specifications, and market conditions. Below is a simplified cost table for concrete in apartment building construction:
Concrete Component | Estimated Cost per Cubic Yard | Notes |
Foundation (Slab or Footings) | $90 – $150 or more | Includes excavation, formwork, rebar, concrete, and finishing. |
Vertical Elements (Walls) | $100 – $180 or more | Cost per cubic yard for exterior and load-bearing walls. |
Columns and Beams | $120 – $200 or more | Cost per cubic yard for structural columns and beams. |
Floor Slabs (Each Level) | $90 – $150 or more | Includes formwork, rebar, concrete, and finishing. |
Stairs and Landings | $120 – $200 or more | Cost per cubic yard for the construction of stairs and landings. |
Exterior Pavements | $90 – $150 or more | Sidewalks, driveways, or other external concrete surfaces. |
Miscellaneous Concrete Work | Varies | Additional costs for special features, decorative concrete, etc. |
The cost of concrete is intricately tied to the prices of its essential raw materials, which encompass cement, aggregates, and water. The global market dynamics play a pivotal role, with fluctuations, supply chain disruptions, and demand fluctuations directly influencing the overall cost of concrete. Any variations in the prices of these raw materials can have a cascading effect on the construction budget, making it essential for stakeholders to closely monitor and adapt to the dynamic nature of the raw material market.
A critical determinant of concrete costs lies in its mix design, where the precise ratio of cement, aggregates, water, and additives significantly impacts overall expenses. Achieving the delicate balance between optimal structural performance and cost efficiency is paramount. The selection of a concrete mix design tailored to meet specific project requirements directly influences the final cost, emphasizing the need for a strategic approach in crafting a mix that aligns with both performance expectations and budget constraints.
The logistical aspect of transporting concrete from the batching plant to the construction site constitutes a substantial component of overall costs. The distance traveled plays a pivotal role in transportation expenses, with longer hauls and potential logistical challenges contributing to increased costs. Efficient planning and strategic batching plant placement are essential to minimize transportation costs, highlighting the importance of considering geographical factors in the overall construction budget.
The proper mixing, pouring, and finishing of concrete necessitate skilled labor, and labor costs significantly impact the overall expense of concrete in construction projects. Wages, benefits, and training expenses for the skilled workforce directly contribute to the financial considerations. Recognizing the importance of skilled labor in ensuring the quality and integrity of concrete installations, stakeholders must factor in labor costs as a substantial component of the overall construction budget.
The scale and intricacy of the apartment building project are pivotal determinants of concrete costs. Larger projects may benefit from economies of scale, potentially reducing the cost per unit of concrete. Conversely, projects with intricate designs or specific architectural features may require specialized concrete mixes, impacting costs. Tailoring the concrete strategy to the unique size and scope of the project is essential for accurate budgeting and cost-effective construction.
The conditions of the construction site introduce nuanced considerations that can influence concrete costs. Factors such as site accessibility, terrain challenges, and environmental considerations can impact the overall expenses. Challenging site conditions may require additional measures, adjustments, or specialized equipment, directly affecting the concrete budget. A thorough site analysis is crucial for anticipating and mitigating potential challenges to control costs effectively.
Ensuring the quality of concrete through rigorous testing and quality assurance measures introduces additional costs to the construction budget. Adhering to industry standards requires regular testing for factors such as compressive strength, durability, and consistency. While these measures contribute to the longevity and performance of the structure, they are integral components that need to be accounted for in the overall cost considerations.
Concrete costs are subject to seasonal variations influenced by construction activity, weather conditions, industry cycles, and regional demand patterns. Seasonal fluctuations in demand can impact prices, and construction stakeholders need to be cognizant of these variations in their budgeting processes. Adapting to the seasonal dynamics ensures that the budget accurately reflects the prevailing market conditions, contributing to effective financial planning and resource allocation.
Efficient raw material procurement is a cornerstone of cost-saving strategies in apartment building construction. The cost of concrete is directly tied to the prices of its raw materials, such as cement and aggregates. Developers and project managers can achieve significant cost savings by establishing strategic partnerships with reliable suppliers, negotiating favorable pricing agreements, and staying informed about market trends. Implementing robust inventory management practices allows for the timely acquisition of materials, mitigating the impact of price fluctuations and ensuring a steady supply at optimal costs.
The optimization of concrete mix design plays a pivotal role in achieving a balance between performance requirements and cost efficiency. Developers must conduct in-depth research to identify mix compositions that are both cost-effective and meet high-performance standards. This involves considering locally available materials, exploring alternative additives, and collaborating with concrete experts to fine-tune mix designs. The goal is to deliver structural integrity and durability at a lower overall cost, making the most of available resources without compromising quality.
Strategic logistics planning is a key consideration in minimizing concrete costs associated with transportation and delivery. The distance between concrete batching plants and construction sites directly influences transportation expenses. Developers can optimize logistics by minimizing travel distances, strategically locating batching plants in proximity to construction sites, and coordinating deliveries efficiently. The integration of technology, such as real-time tracking and logistics optimization software, enhances the overall efficiency of concrete transportation, resulting in substantial cost savings.
The optimization of labor costs in apartment building construction involves strategic management of skilled workers engaged in concrete-related tasks. This includes implementing training programs to enhance skill sets, optimizing work schedules to maximize productivity, and ensuring safety measures are in place to minimize potential delays or accidents. Investing in a skilled and efficient workforce not only contributes to the quality of construction but also serves as a proactive measure to control labor-related costs.
Capitalizing on economies of scale is a strategic approach for reducing concrete costs in larger apartment building projects. The concept involves leveraging the advantages that come with larger quantities, such as bulk purchasing of materials, streamlined logistics, and optimized batching processes. Project planners should explore opportunities to consolidate resources efficiently, recognizing the potential for long-term cost savings that arise from economies of scale in the construction process.
Thorough site-specific planning is crucial for minimizing concrete costs by addressing challenges related to accessibility, terrain, and environmental considerations. Developers and project managers need to conduct a comprehensive analysis of the construction site, allowing for proactive measures to minimize disruptions and additional expenses. Adapting construction schedules to optimize weather conditions further prevents unnecessary delays and associated costs, ensuring that site-specific challenges are effectively managed.
Quality management strategies are integral to avoiding rework and additional costs in concrete construction. Ensuring that concrete meets specified standards through regular testing and quality assurance measures reduces the risk of defects or structural issues. Prioritizing quality at every stage of the construction process contributes to long-term cost savings by minimizing the likelihood of repairs or renovations, ultimately enhancing the efficiency of the construction process.
Embracing technology in apartment building construction can lead to efficiencies and cost savings. This includes utilizing advanced concrete mixing technologies, automated batching systems, and real-time project management tools. Technology integration enhances precision, reduces manual errors, and streamlines processes, contributing to overall project cost-effectiveness. Stakeholders should explore innovative technologies that align with the specific needs of the project to maximize efficiency gains.
Exploring energy-efficient practices in concrete production and construction is a dual strategy for cost savings and sustainability. This involves optimizing energy consumption in concrete batching, exploring alternative energy sources, and adopting environmentally friendly concrete mixtures. Energy-efficient practices not only reduce operational costs but also align with broader environmental goals, reflecting a commitment to sustainable and cost-effective construction practices.
Conducting a comprehensive lifecycle cost analysis is a strategic consideration for evaluating the long-term economic viability of different concrete strategies. While upfront costs are essential, considering maintenance, durability, and energy efficiency over the building’s lifecycle provides a holistic view. Selecting concrete solutions that offer long-term cost savings, even if with slightly higher initial costs, can be economically advantageous. This approach ensures that the overall project aligns with both short-term financial objectives and long-term sustainability goals.
The cost of concrete is a pivotal factor in apartment building construction, impacting the overall budget. With a general cost range of $90 to $120 per cubic yard, stakeholders must consider various factors. Raw material prices, mix design, transportation, labor, project size, site conditions, quality assurance, seasonal variations, and cost-saving strategies all play crucial roles. Implementing efficient procurement, optimized mix designs, strategic logistics, skilled labor management, economies of scale, site-specific planning, quality control, technology integration, energy efficiency, and lifecycle cost analysis are essential for minimizing expenses while ensuring long-term success. This holistic approach allows for precise budgeting, enabling developers, contractors, and investors to navigate construction complexities with financial precision and sustainability in mind.
The cost of concrete in apartment building construction typically falls within the range of $90 to $120 per cubic yard. However, it’s essential to note that these costs are estimates and can vary based on factors such as location, project specifications, and market conditions.
Various factors influence concrete costs, including raw material prices (cement, aggregates, and water), concrete mix design, transportation and delivery, labor costs, project size and scope, site conditions, quality assurance and testing, and seasonal variations. Understanding these factors is crucial for accurate financial planning.
Developers can employ several cost-saving strategies, such as efficient raw material procurement through strategic partnerships, optimized concrete mix design for performance and cost efficiency, strategic logistics planning to minimize transportation costs, skilled labor management, capitalizing on economies of scale, site-specific planning, quality management strategies, technology integration, energy-efficient practices, and conducting lifecycle cost analysis.
The cost table for concrete includes estimated costs per cubic yard for various components, such as foundation (slab or footings), vertical elements (walls), columns and beams, floor slabs (each level), stairs and landings, exterior pavements, and miscellaneous concrete work. These costs cover excavation, formwork, rebar, concrete, finishing, and additional features.
A lifecycle cost analysis is crucial for evaluating the long-term economic viability of different concrete strategies. While upfront costs are essential, considering maintenance, durability, and energy efficiency over the building’s lifecycle provides a holistic view. Selecting concrete solutions that offer long-term cost savings ensures alignment with both short-term financial objectives and long-term sustainability goals.
Here I am going to share some steps to get your apartment building construction concrete cost estimate report.
You can send us your plan on info@estimatorflorida.com
Before starting your project, we send you a quote for your service. That quote will have detailed information about your project. Here you will get information about the size, difficulty, complexity and bid date when determining pricing.
Our team will takeoff and estimate your project. When we deliver you’ll receive a PDF and an Excel file of your estimate. We can also offer construction lead generation services for the jobs you’d like to pursue further.
561-530-2845
info@estimatorflorida.com
Address
5245 Wiles Rd Apt 3-102 St. Pete Beach, FL 33073 United States
561-530-2845
info@estimatorflorida.com
Address
5245 Wiles Rd Apt 3-102 St. Pete Beach, FL 33073 United States
All copyright © Reserved | Designed By V Marketing Media | Disclaimer