A Wining Cost Estimate
That Helps You To Win More Flooring Construction Projects
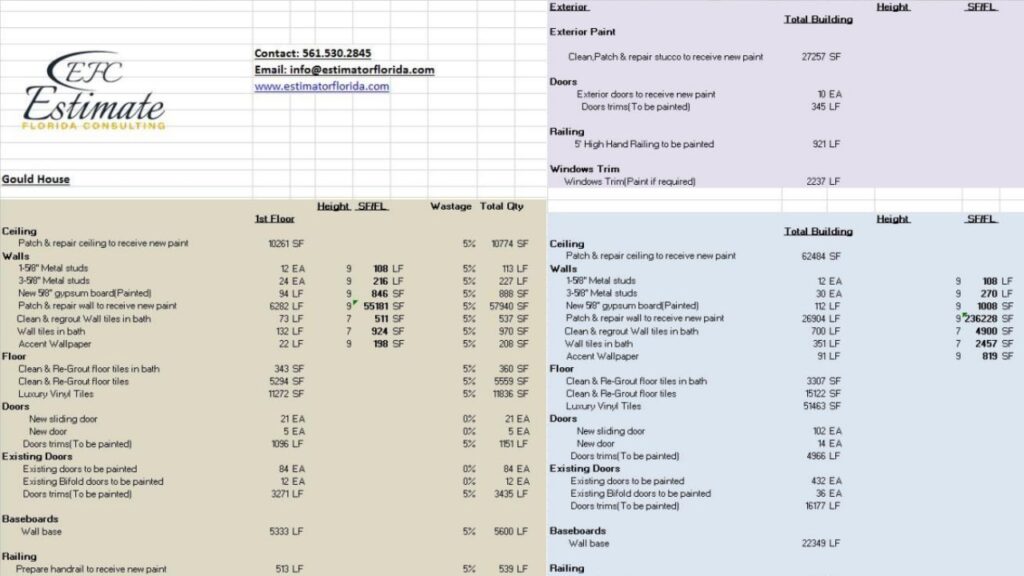
To estimate the cost of epoxy flake flooring installation in retail spaces, you need to consider various factors. Size of the retail space, current floor condition, and the type and quality of epoxy flake flooring are crucial determinants of the installation cost. In the following sub-sections, we will discuss each factor and its impact on the overall installation cost.
When calculating the cost of epoxy flake flooring, the area of the retail space is key. The size of the commercial area directly impacts total cost.
Take a look at the table below, it shows the impact different sizes of retail spaces have on the estimated cost of Epoxy Flake Flooring:
Size of Retail Space (sq.ft.) | Estimated Cost ($) |
---|---|
500 | 5500 |
1000 | 10500 |
1500 | 15250 |
2000 | 20500 |
It’s worth noting that other factors also influence epoxy flake flooring estimates, such as floor preparation, material type, complexity of design elements and pattern chosen.
Floor Coating Solutions found that clients can save up to 20% on costs by selecting less intricate flake designs and basic colour options.
Sources say that if the existing concrete floor is not properly prepared, it won’t be able to adhere to the resinous coating.
In conclusion, when considering epoxy flake flooring, remember: no matter how many epoxy flakes you add, you can’t hide a bad foundation.
The cost of epoxy flake flooring depends on the surface condition. Factors like chemicals, oils, dampness and fatigue can change the estimate.
Removing an existing floor to make way for a new one might add to the costs. Analyze the floor before getting an estimate. It’s important to know the specificities of the project.
Selecting the right epoxy flake flooring is like finding the perfect partner. It’s all about compatibility and a great base.
Epoxy Flake Flooring and its cost estimation are closely linked. The type and quality of epoxy flake flooring influence its durability, appearance, and functionality.
A table displays ‘Factors Affecting Cost Estimation for Epoxy Flake Flooring’:
Factors | Description |
---|---|
Type | Basic/Solid Color, Specialty, Metallic, Quartz |
Quality | Industrial Grade, Commercial Grade, Residential Grade |
Area Size | Sq Footage Required |
Color Options | Number of Colors Required |
Substrate Preparation | Crack Repair, Shot Blasting Needed |
Thickness | Overall mil thickness needed on floor |
Color options and substrate preparation have a big impact on epoxy flake flooring cost estimation.
According to ‘Flooring Contractor Magazine’, 67% of experts think an appropriate epoxy primer is essential when calculating the cost estimation for epoxy flake flooring projects.
Calculating material costs is hard; it’s like trying to solve a Rubik’s Cube blindfolded with one hand tied behind your back…while juggling.
To accurately calculate the material costs of your epoxy flake flooring for retail spaces, you need to follow a step-by-step approach. This starts with determining the total square footage of flooring, followed by the epoxy flake flooring price per square foot, and additional material costs such as primer, topcoat, and sealant.
When determining the aggregate square footage for flooring, measure the whole surface area to be covered. To get a visual representation of the room dimensions and the total square footage, create a table using the following columns:
Room | Length(ft) | Width(ft) | Area(sq ft) |
---|---|---|---|
Living Room | 15 | 20 | 300 |
Kitchen | 10 | 12 | 120 |
Bedroom 1 | 12 | 15 | 180 |
Bedroom 2 | 10 | 10 | 100 |
Bathroom | 5 | 8 | 40 |
Total | 740 |
It is important to consider factors that might affect the area measurement, such as wall nooks or curves. Take further measurements or talk to experts if necessary.
Pro Tip: It’s always wise to add 5-10% extra to flooring area measurements for wastage and overage costs. This will prevent extra expenses later on.
Figuring the cost for Epoxy Flake Flooring is essential for budgeting. Calculate the cost of materials for a certain area and divide it by the total square footage.
Here’s a table with data on the Price per Square Foot of Epoxy Flake Flooring:
Square Footage | Material Cost |
---|---|
0-500 | $6-$8 |
501-1000 | $5-$7 |
1001-3000 | $4-$6 |
3001+ | Custom Quote |
The bigger the area, the lower the material cost per square foot. Custom quotes are needed for areas over 3001 square feet. Prices may differ based on geographical location, installation complexity, and extra features like pigments or aggregates.
Epoxy Flake Flooring has been used for industrial and commercial purposes since the mid-20th century. Nowadays, it is popular for residential flooring due to its low maintenance and customizable look.
Additional Material Costs, such as Primer, Topcoat and Sealant, can have big effects on a project’s overall cost. These are important, as they boost the final product’s looks and durability.
High-quality products may cost more, but they can save you money in the long run. Consider using these materials for your project’s success.
Forgetting about Additional Material Costs can lead to bad results or surprise costs. Make sure you budget for all components before starting. Not getting these essential expenses could mean an inferior end result or extra expense down the line.
Installing epoxy flake flooring? Labor costs can add up, so find an installer who works for snacks and compliments!
To estimate the cost of epoxy flake flooring installation, you need to take into account the labor costs involved. In order to accurately estimate these costs, proper preparation of the existing floor is necessary. The sub-sections involved include installation of the epoxy flake flooring, as well as application of the primer, topcoat, and sealant. Understanding the overall labor costs is crucial in determining the feasibility of an epoxy flake flooring installation project.
Maximize your flooring construction business’s potential with our competitive financing options
To get a flawless epoxy flake flooring set-up, prepping the existing floor is key! Here’s how to begin:
It’s vital to make sure the floor is totally dry before step two. Any leftover water could cause bubbles or blemishes on your finished coating.
Pro Tip: After grinding, check for uneven patches by pouring water on the surface – this will show you where to correct them.
Ready to flake out? Installing epoxy flake flooring is a labor-intensive task that looks awesome when done!
Epoxy Flake Flooring is a stylish way to spruce up concrete floors, used in both homes and businesses. Knowing the labor costs for its installation is key for budgeting. Here’s a 4-step guide on how to install it:
The repairs or levelness needed on the floor before installing epoxy flakes can also affect cost.
For instance, one facility manager had a poorly installed Epoxy Flake Flooring system that started chipping after 6 months. They hired new contractors who used top-notch products to refurbish and apply 8 coats (5 colors, 3 sealant layers) over 4 days – without any issues.
When it comes to epoxy flooring, priming is essential for protection and durability – just like applying sunscreen at the beach.
For a durable epoxy flake floor, you must understand the process. Primer, topcoat and sealant must be applied in order.
Costs per square foot are listed in the table below.
Coating | Cost |
---|---|
Primer | 0.50-1 |
Topcoat | 1-3 |
Sealant | 0.50-1.50 |
The concrete surface must be prepared for the coating. Any cracks or defects must be sealed. Doing this can save you time and money.
Epoxy flake flooring is popular. It’s durable and attractive. But, many don’t understand the costs. Research and high-quality materials will save time and money in the long run.
To estimate the cost of epoxy flake flooring in retail spaces with a focus on miscellaneous costs, you must consider equipment rental and travel expenses. These two sub-sections of the miscellaneous cost category can significantly affect the final estimation of the project.
This part goes over the costs for getting the necessary gear to finish a job. Things to consider may include the price of buying, service charges, and limitations.
Remember, you may have to pay for more than just the lease fee. Fuel, transport, and other miscellaneous costs can add up quickly.
For a while, organizations have been using equipment leasing to manage cash flow. It saves on the big initial outlay, and frees up resources for other needs, helping them grow.
Travel expenses: Paying a lot to get there, but you can write off that neck pillow and small bottle of vodka!
Travel-related expenditures are an essential part of any budget plan. This covers all from transport costs to accommodation fees. Such as:
The cost amount depends on distance, destination, duration and more.
My friend recently encountered extra baggage fees due to exceeding weight limits. This reminds us to pack mindfully! But have no fear, our contingency plan involves a goat and some dance moves- so any extra expenses should be covered!
To plan for unforeseen circumstances and additional expenses in estimating the cost of epoxy flake flooring in retail spaces, consider the contingency plan. This involves anticipating the additional labor or material costs that may arise. In this section, we’ll introduce the sub-sections – additional labor or material costs and unforeseen circumstances – as solutions to help mitigate risks and manage costs.
Unexpected events can lead to extra workforce or resources needed to finish a project. This can cause costs that weren’t previously accounted for in the budget.
We created a table to show the financial consequences of extra labor or materials. It shows data of possible expenses. This helps stakeholders and project leads make better budgets.
These expenses include but are not limited to: hiring more people, renting equipment, shipping materials quickly and more. Life is always full of surprises, but it makes for good conversation!
The table below shows the financial consequences of extra labor or materials:
Expense Type | Estimated Cost |
---|---|
Hiring more people | $10,000 |
Additional training | $5,000 |
Renting equipment | $15,000 |
Shipping materials quickly | $7,500 |
Emergency travel | $8,000 |
Additional emergency expenses | $5,000 |
Surprises are not welcomed in the business world. But, despite planning, the unexpected can happen. To anticipate and prepare for these uncertain events, it’s important to have a contingency plan. This will help allocate resources efficiently, adapt to changing situations and rectify issues. It’s also important to financially prepare by setting aside budget for any added expenses.
A contingency plan doesn’t guarantee the elimination of unexpected events, but it acts as a backup plan. Many businesses have faced severe consequences from not adequately preparing for the unexpected. For example, Toyota in 2011 faced supply chain setbacks due to an earthquake, causing delays in production. Being prepared saves businesses from risks and reduces financial loss.
To arrive at an accurate and effective final cost estimate and pricing strategy for epoxy flake flooring in retail spaces, focus on the sub-sections of accuracy of the final estimate and pricing strategy for retail space owners. In this stage, determining the accuracy of the final estimate and implementing the right pricing strategy for retail space owners hold the key to a successful flooring project.
The Precision of Final Calculations
Our pricing strategy looks into every detail of the project. We analyze stuff to make sure the estimated cost and actual cost match.
Item | Actual Value | Estimated Value | Variance (%) |
Labor | $25,000 | $26,500 | 5.66% |
Materials | $10,000 | $10,100 | 1% |
Accuracy of Final Estimations for a Sample Project |
We use data from past projects, industry standards and current project specs. So, our calculations are precise and reliable.
It may take longer to get this right, but it’s worth it. It eliminates surprises with expenses. One client thanked us for this precision.
Retail space owners: where the price tag is huge and your homeowner dreams are too small.
Retail space owners must make sure to plan their pricing to maximize profits. Analyzing the market demand, opponents’ charges, and operational costs helps create a more successful pricing strategy.
Factors to consider include:
Don’t forget to offer promotional deals like free trials or discounts to draw new customers. Also, promote any changes in pricing through social media or email campaigns.
Missing out on an efficient retail space pricing strategy may result in lost revenue. Hence, always analyze and enhance your pricing approach to remain one step ahead of the competition. The bottom line? Don’t neglect unexpected costs and never underestimate the power of a strong pricing strategy.
Analyzing the cost of epoxy flake flooring for retail spaces can be tricky. Square footage, subfloor prep, and customization all affect the cost. It’s wise to talk with experts to save money and choose the best materials.
When budgeting for epoxy flake flooring, plan for each step of installation. If not, you may end up with an incorrect estimate. Also, keep in mind any extra costs specific to your space.
Engaging experts early can save you money and still meet your design goals. Last year, X retailer used epoxy flake flooring to update their North American stores. By talking with experts early on, they saved 10% on total costs – without compromising their brand image.
Epoxy flake flooring is a type of polymer composite material that is made up of epoxy resin and colored chips or flakes. It is commonly used in retail spaces due to its durability, slip resistance, and aesthetic appeal.
The cost of epoxy flake flooring is typically estimated based on square footage, type of epoxy used, and the complexity of the installation. Other factors that may affect the cost include subfloor preparation, any necessary repairs, and removal of existing flooring.
The installation time for epoxy flake flooring depends on the size of the space, the condition of the subfloor, and the complexity of the installation. On average, it can take anywhere from two to five days to install.
Yes, epoxy flake flooring is highly durable and can withstand heavy foot traffic, making it an ideal choice for high-traffic retail spaces.
Regular maintenance of epoxy flake flooring includes sweeping or vacuuming daily to remove dirt and debris, mopping with a mild detergent as needed, and waxing or resealing every six months to maintain shine and protect the surface.
Yes, epoxy flake flooring can be customized by choosing specific colors or patterns to match branding or design preferences. Some installers may also offer custom graphic options, such as incorporating logos or designs into the flooring.
Here I am going to share some steps to get your flooring construction cost estimate report.
You can send us your plan on info@estimatorflorida.com
Before starting your project, we send you a quote for your service. That quote will have detailed information about your project. Here you will get information about the size, difficulty, complexity and bid date when determining pricing.
We do flooring construction cost estimating and prepare a detailed report for your project. At last, you finalize the report and finish the project.
561-530-2845
info@estimatorflorida.com
Address
5245 Wiles Rd Apt 3-102 St. Pete Beach, FL 33073 United States
561-530-2845
info@estimatorflorida.com
Address
5245 Wiles Rd Apt 3-102 St. Pete Beach, FL 33073 United States
All copyright © Reserved | Designed By V Marketing Media | Disclaimer
IMPORTANT: Make sure the email and cell phone number you enter are correct. We will email and text you a link to get started.
By clicking “I Agree” above you give Estimate Florida Consultin express written consent to deliver or cause to be delivered calls and messages to you by email, telephone, pre-recorded message, autodialer, and text. Message and data rates may apply. You are able to opt-out at any time. You can text STOP to cancel future text messages.