A Wining Cost Estimate
That Helps You To Win More Millwork Construction Projects
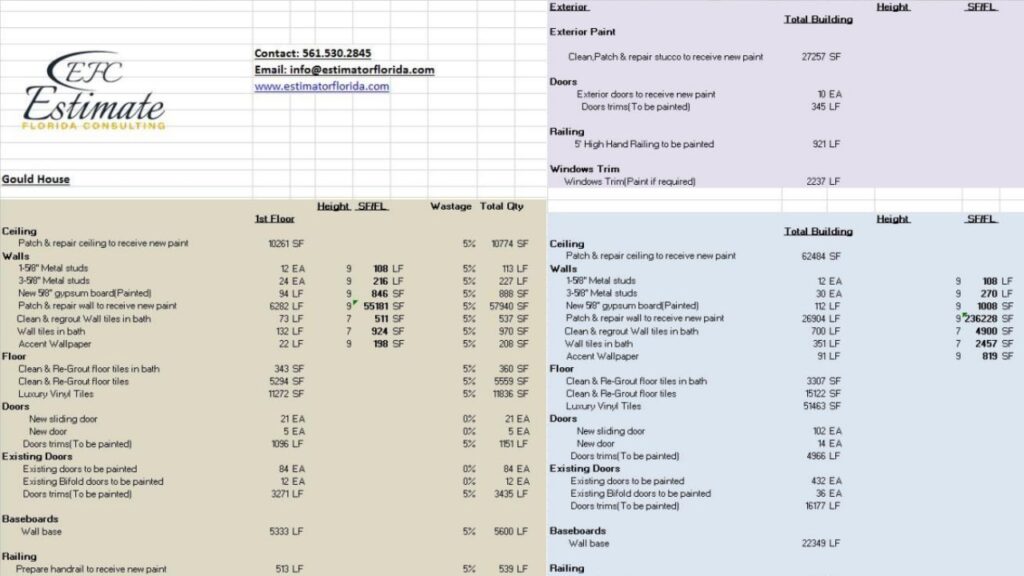
Custom Architectural Millwork: Design, manufacture and install decorative woodwork in commercial spaces. A specialized field that requires woodworking experience and attention to detail. Elevates aesthetic appeal and serves practical functions.
Many unique details for commercial spaces. Designers can create one-of-a-kind designs and incorporate functional elements.
Recently worked on project with customized wooden wall panels. We collaborated with manufacturer to create bespoke pieces that looked amazing and were functional. The finished product exceeded expectations – highlighting the benefits of custom millwork in adding uniqueness to commercial spaces.
To prepare for estimating the cost of custom architectural millwork for commercial spaces, you need to examine the project site, assess client needs, decide on materials, and review architectural drawings. This will help you ensure that you provide an accurate estimate that aligns with the client’s vision and budget.
Conducting a Site Analysis
It’s key to conduct a thorough analysis of the project site before preparing an estimate. Check out the following table for a comprehensive overview of the essential factors to consider during site analysis.
Factors to consider | Details to note |
---|---|
Location & Accessibility | Analyze accessibility. See if any transportation or storage constraints could increase the cost. |
Topography | Check the area’s topography – it can affect construction equipment and methods used. |
Soil Conditions | Inspect soil conditions. Weak or unstable soils may require extra foundation support for the building. |
Environmental Factors | Assess environmental factors like weather, ecology, and noise levels. This could cause delays or need extra safety precautions. |
Remember that each project site is unique – tailor your attention during analysis.
For centuries, site analysis has been an important part of project planning. In ancient civilizations like Egypt and Greece, architects would carefully examine locations before beginning construction projects to ensure successful outcomes.
Assessing client needs is like trying to read minds – but with less psychic ability and more spreadsheets!
The first step is to understand what the client wants. This includes the goals and any deadlines or restrictions. It’s important to know the project before beginning the estimate.
After understanding the client’s needs, all the information that affects the budget and timeline must be collected. For example, the cost of any needed materials or equipment must be included. If there is a time limit, more people can be hired to reduce the timeline, but at an extra cost.
Small details can make a big difference. Neglecting a single requirement could disqualify the estimate. It’s essential to take note of all details.
Sending the estimate on time shows professionalism and increases trust in your services. It also helps you get more jobs. Ensure you have enough time to review costs and make estimates. Delays in sending estimates can hurt revenue.
Choosing suitable materials for a project is essential when creating an estimate. It affects the cost, strength, and durability of the outcome. Thus, careful thought must be taken before selecting materials.
Besides cost, suitability, and durability, quality, availability, and environmental impact should also be considered. Through informed decisions on material selection, contractors can make better estimates and obtain better results.
Past projects show that inadequate material estimation may cause under-budgeting or over-budgeting. These lead to financial losses or client dissatisfaction. That’s why it’s essential to conduct research and analysis before deciding on materials. Put on your detective hat – reviewing architectural drawings is like playing ‘Spot the Difference’ on expert mode!
Evaluating Design Parts
Knowing and understanding design elements in architectural drawings is essential for precise estimation. A comprehensive look at drawings guarantees no significant details are missed.
Table: Architectural Drawing Review Checklist
Design Element | Consideration |
---|---|
Dimensions | Make sure dimensions are clear and correct |
Materials | Note materials used for each component of the design |
Structural Integrity | Check if the design’s structural strength is sound |
Functionality | Guarantee design mirrors functional needs |
Building Code Compliance | Confirm design follows local building codes |
Apart from the normal drawing review process, make sure to look into all project specifications given by clients. These specs may contain info on particular materials or finishes required by customers, which must be taken into estimations.
Once, a reliable construction firm encountered a project where they failed to recognize a basic problem in a client’s original sketches. The mistake led to unexpected costs, disrupting the entire estimation process. Therefore, it highlights the importance of a thorough review before estimation.
It’s time to get cracking – let’s examine the cost of custom architectural millwork!
To calculate the cost of custom architectural millwork for commercial spaces, you need to consider various factors. Labor costs, materials costs, equipment costs, and transportation costs are the sub-sections that you need to focus on. Each sub-section has a different impact on the overall cost of the project. By breaking down the expenses into these categories, you can get a comprehensive understanding of the cost structure.
Costs for personnel for custom architectural millwork can be pricey. This is due to specialized skills, exactness, and the time-consuming nature of the job. Experts are needed for each step, from design to fabrication to installation.
Calculating the labor costs for custom millwork projects is important. People experienced with complex designs and designs needing high detail often charge higher hourly rates. The complexity of the project decides how many workers are needed and the time frame for each step.
Sometimes, project managers select prefabricated or pre-designed components instead of custom pieces to save on labor costs. But, this could decrease quality and the final product could be less impressive.
It’s worth noting that going for cheap labor may seem appealing, but it could end up costing more due to mistakes made during fabrication or installation. High quality workmanship is essential to achieving the best results for architectural millwork projects.
Professionally calculating the expenses of customized architectural millwork requires analyzing different factors. A key one is materials cost. The type and quality of material used affects the overall cost.
Let’s make a table to analyze costs:
Material Name | Material Type | Quantity Required | Price per Unit | Total Cost |
---|---|---|---|---|
Wood | Mahogany | 20 Board Feet | $10 per board foot | $200 |
Paint/Finish | Semi-Gloss Enamel Paint | 2 Gallons | $50 per gallon | $100 |
Hardware | Knobs and Pulls | 5 Pairs | $20 per pair | $100 |
Total Cost | $ | $400 |
Note: Costs may vary depending on materials and other project variables.
Custom millwork manufacturers may have relationships with suppliers or mills that allow them to buy materials at discounted rates. This could reduce costs.
Pro Tip: Communicate clearly about material preferences and budget guidelines from the start of the project. Your wallet may be unhappy, but your home will be happy in the end. Equipment costs for custom architectural millwork can be expensive.
Maximize your millwork construction business’s potential with our competitive financing options
For our custom architectural millwork project, we must consider the cost of different equipment. This includes buying or renting the machines and tools for milling and cutting wood.
Have a look at the Equipment Costs table:
Equipment | Cost |
---|---|
CNC Router | $50,000 |
Planer/Jointer | $4,000 |
Band Saw | $2,500 |
The table shows the essential machines required for custom architectural millwork. Plus, there are other tools which might be needed occasionally, like cutting disks, drill bits and sanding tools.
It is important to think about what you need and which machines can provide them. Buying new machines is pricey, but it is better if you plan to use them often. Renting could be more affordable.
Remember to service the machines regularly. Include additional costs when planning the project. Maintenance boosts productivity, reduces breakages and increases operational life span.
Save money on a gym membership; just lift and haul your custom millwork!
Transportation costs for custom architectural millwork must be taken into account. Factors like distance, transport mode, and delivery time all influence the cost.
The further the millwork needs to go, the more expensive it is. Difficult terrain or traffic can also add to the costs.
Trucking is usually the most common transport method, but air or sea freight may be necessary at extra cost. Rush orders require expedited shipping services or a dedicated truck driver, which can hike up the price.
For cheaper shipping rates, use a local manufacturer near your job site. Ignorance isn’t bliss when it comes to home renovations – be prepared for extra expenses.
To better estimate the cost of custom architectural millwork for commercial spaces when planning your budget, you need to consider the additional costs that come with it. In order to provide you with a comprehensive understanding of these costs, we will walk you through a few essential sub-sections that you should look out for, including installation and setup, taxes and fees, and contingency budget.
When it comes to new systems or software, there’s more to consider than just the purchase price. Setup and installation has its own costs. Here’s a 4-Step Guide to helping you set it up:
Remember, each setup may be different. Plus, don’t forget security settings and backups! Doing all of this properly can save you from extra costs and ensure a good Return on Investment. Like taxes, it might not taste great, but it’s necessary for a healthy budget.
When shopping, consider all tariffs and surcharges that could be added to the price. These extra expenses may take the form of taxes or fees. Taxes are paid to the government compulsorily, while fees are charged for services.
Taxes depend on where the goods or services are bought. There are state and local taxes to pay. Luxury items, such as cars or jewelry, may have specific taxes. It’s a must to factor these costs into your budget.
Fees could include shipping and handling, activation fees for new accounts or visas, or application expenses. Processing fees for using credit cards instead of cash may also be charged by some retailers.
Pro Tip: Before purchasing, find out applicable taxes and fees to prevent budget surprises! Don’t forget about having an emergency budget – you’ll be glad you did!
Planning a budget? Make sure to allocate a chunk as a ‘just-in-case’ fund. A few key points to keep in mind:
It’s tempting to use every penny, but having an emergency cushion can make success or failure. Unexpected expenses can happen at any time- be prepared! When planning, remember the ‘just-in-case’ fund and feel more secure. Don’t regret not putting aside enough! It’s better to overestimate than to underestimate.
To make sure your custom architectural millwork project comes in on budget, you need to accurately estimate the costs involved. In order to do that, you can follow some helpful tips for accurate cost estimation. Regular communication with clients, doing your research, building relationships with suppliers, and keeping records of previous projects all contribute to a successful, cost-effective project.
Stay connected with clients to build trust and clarify project scope, timelines, and budget. Also, it helps ensure smooth collaboration.
To engage clients, offer progress updates and have open communication channels. Provide a portal for clients to monitor milestones and give feedback throughout the project cycle. For optimal client-engagement, stay abreast of industry trends to better advise on cost implications.
Maximizing Quality Communications leads to Better Results!
Regular client-engagement helps with cost forecasting. To maximize communication quality:
Comprehensive market analysis is key to accurate cost estimating. Trends, supplier prices, and competition should be researched to determine project costs. This helps when negotiating with vendors, reducing costs.
Past projects should be looked at for similar scope. This gives insight into potential roadblocks or setbacks. Online databases and industry publications provide info on pricing trends, supply chain issues, and regulations.
Gut instincts and assumptions should be avoided when estimating costs. Sources should be consulted and findings kept transparent.
Harvard Business Review states that businesses investing in research before projects tend to do better financially than those who don’t.
Building relationships with suppliers is like dating, except payments and communication take the place of flowers and chocolates.
Making strong links with suppliers is a clever way to gain precise cost calculations. Conversation and negotiations are key in this process, ensuring both sides understand each other’s requirements and expectations.
By talking openly, suppliers could supply precious insights about pricing strategies that are not well-known. This info could be used to make more exact estimates, leading to wiser choices. Spending less also opens up chances for bargaining better prices, making it more likely to get good rates on future buys.
Furthermore, having dependable suppliers can raise customer service levels and guarantee faster delivery times. Connecting with suppliers lets businesses handle problems proactively instead of reacting in the long run.
Analyze past tenders and point out areas where suppliers could save money by suggesting other options or approaches. Inspect supplier performance consistently and use a supplier scorecard for fairer evaluation based on metrics such as quality of products or raw materials, consistency of service delivery, and payment terms. Pushing collaboration between stakeholders guarantees sustainable performance advancement in the long run.
By putting into practice these strategies, businesses can find reliable sources of info while reducing costs linked to inaccurate estimations. Genuine communication policies help build long-term relationships with suppliers to get the best deals at reasonable prices.
Retaining details of past tasks and costs is necessary for exact cost estimation. Here’s why:
Moreover, detailed records can be a useful asset in case of disagreements or legal matters.
Pro Tip: Make sure to keep records structured and easily available so you can rapidly refer to them during the estimation process. Remember, a wrong estimate is like a bad haircut – you’ll be dealing with it for a while.
Accurate and precise estimation is key for custom architectural millwork in commercial spaces. To get an accurate estimate, multiple factors must be considered. These include materials, size, design, labor hours, and deadlines.
Being precise is essential, as it affects the success of a project. If estimates are above budget or late, customer satisfaction may suffer. This can also lead to legal issues. Therefore, developers must understand the entire estimation process to avoid these risks.
To get accurate estimations, project managers must be knowledgeable about millwork’s principles. They should continually learn about industry standards through professional organizations like AWI (Architectural Woodwork Institute). Additionally, computer-assisted programs like Excel spreadsheets with pre-made formulas are recommended.
Did you know that custom millwork dates back to ancient Egypt? They created stunning architecture from hardwoods and adorned it with ivory and rare stones such as lapis lazuli (Forbes).
Architectural millwork involves the precise design, manufacture, and installation of custom architectural elements made from wood, such as cabinetry, moldings, and paneling.
The cost of architectural millwork is estimated by calculating the amount of wood required for the project, the type of wood used, and the complexity of the design. The cost also includes labor, equipment costs, and the finishing materials used.
Factors that can affect the cost of architectural millwork include the size and complexity of the project, the type of wood used, the design details, and the finishing materials used.
To ensure the accuracy of your estimates, it’s important to work with experienced and reputable architectural millwork companies and to provide as much detail as possible about your project’s specifications.
The production time for custom architectural millwork can vary depending on the complexity of the design, the number of pieces required, and the availability of materials. It’s important to discuss timelines with your millwork provider.
It’s possible to make changes to the design after the project has started, but it may result in additional costs and delays in production. It’s important to communicate any changes as early as possible to your millwork provider.
Here I am going to share some steps to get your millwork construction cost estimate report.
You can send us your plan on info@estimatorflorida.com
Before starting your project, we send you a quote for your service. That quote will have detailed information about your project. Here you will get information about the size, difficulty, complexity and bid date when determining pricing.
We do millwork construction cost estimating and prepare a detailed report for your project. At last, you finalize the report and finish the project.
561-530-2845
info@estimatorflorida.com
Address
5245 Wiles Rd Apt 3-102 St. Pete Beach, FL 33073 United States
561-530-2845
info@estimatorflorida.com
Address
5245 Wiles Rd Apt 3-102 St. Pete Beach, FL 33073 United States
All copyright © Reserved | Designed By V Marketing Media | Disclaimer
IMPORTANT: Make sure the email and cell phone number you enter are correct. We will email and text you a link to get started.
By clicking “I Agree” above you give Estimate Florida Consultin express written consent to deliver or cause to be delivered calls and messages to you by email, telephone, pre-recorded message, autodialer, and text. Message and data rates may apply. You are able to opt-out at any time. You can text STOP to cancel future text messages.