A Wining Cost Estimate
That Helps You To Win More Framing Construction Projects
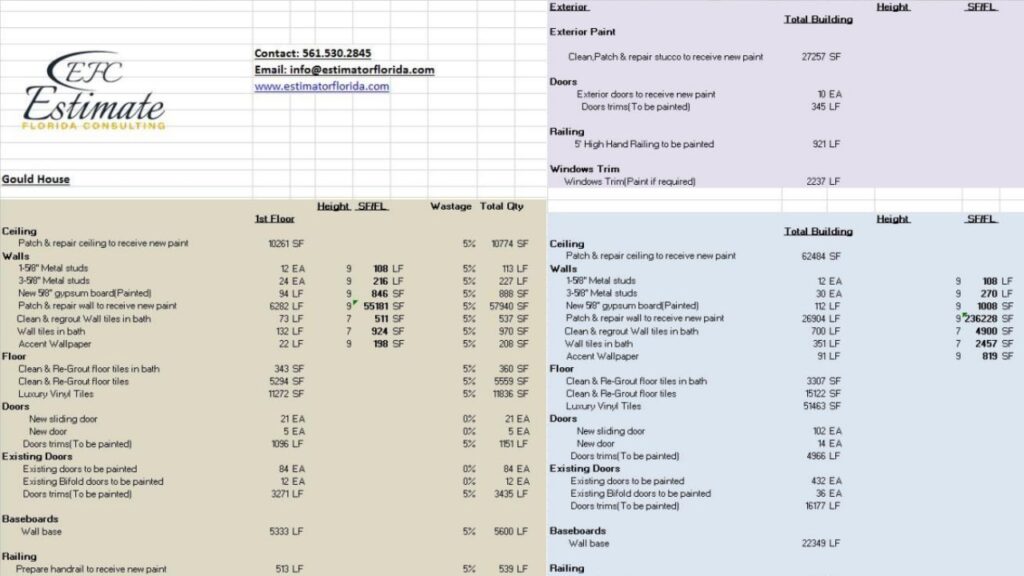
To estimate the price of framing a house, you need to consider several factors. In order to understand how each of these factors can impact the overall cost, you should look at three things: the size and complexity of the house, the location and availability of materials, and the labor costs in the area. By examining each of these sub-sections, you’ll be able to take a comprehensive view of the various factors that affect the cost of framing a house.
The size and detail of a house affect the cost of framing. Big houses require more materials, time, and labor than small ones. Complex structures, such as multi-story homes, parts with strange shapes, or non-standard angles, add to the cost due to their difficulty.
Also, extra features like roof types or decorative trims can raise the price of framing. These extras need special materials and skills, and take longer to install.
Having a good plan and simple design can make framing easier and less costly. Someone from Florida found out the hard way that their custom design needed extra fittings, which added $10K to the cost. Planning ahead could have saved them money. Building a house in a remote area is like a game of hide-and-seek with materials – they hide, you seek, and your wallet cries.
The cost of framing a house depends on many factors. Location is a crucial one.
In urban areas materials are often available, but expensive due to demand.
In rural areas materials are usually cheaper, but can be harder to find. This may involve extra costs for transportation.
The availability of skilled labor and equipment also affects material accessibility.
Building codes and restrictions may limit the materials used, which impacts the cost.
According to HomeAdvisor, the national average cost for framing a house is $4,500. Prices range from $3 to $10 per square foot. Labor costs also need to be taken into account. Unless you have a team of beavers handy!
Employing skilled workers to construct a house frame can significantly add to the total framing cost. This is due to the labor costs in the area, which can vary from region to region.
For example, carpenters in San Francisco charge between $40-$70 per hour. Whereas, in Houston, you can hire them for $20-$50.
See the table below for additional details.
Area | Carpenter Cost/Hour |
---|---|
SF | $40-$70 |
HOU | $20-$50 |
NYC | $45-$90 |
Experience and skillset of workers also play a major role in labor costs. So, take these into consideration when planning construction to manage the budget and ensure quality work.
Moreover, San Francisco has an annual salary raise rate of 2.5%, according to CLMA.
Looks like constructing a house needs more than just looks and charm – materials too!
Maximize your framing construction business’s potential with our competitive financing options
To estimate the cost of framing your house, you need to know the materials required. In order to build a sturdy wooden frame, you will need lumber and plywood. To attach them, you will need nails and screws. For extra stability, you will also require metal connectors and anchors. And for insulation purposes, you will need insulation and vapor barriers. Let’s take a closer look at each of these materials to help you estimate the cost of framing your house.
Here is a table outlining the required Lumber and Plywood for framing a standard house:
Materials | Quantity |
---|---|
Pressure-treated lumber | 65 pieces of 4x4x8ft |
Hardwood | 88 pieces of 2x4x14ft |
Softwood | 230 pieces of 2x6x16ft |
Engineered lumber | 40 sheets of LP® TechShield® Radiant Barrier OSB Sheathing |
Plywood | 3000 sq ft of sheathing |
It’s important to pick the right type & grade of Lumber and Plywood based on location & weather conditions. For example, if the house is near the coast, use treated lumber to resist moisture damage.
Fun fact: According to the Forest Products Journal by United States Department of Agriculture, more than half of residential structures built in the United States since colonial times have been framed with wood.
Make sure you use the right Lumber and Plywood for your new home. Why settle for just nails or screws when you can have a nail-screw hybrid? Confuse future DIY-ers for generations to come!
When it comes to securing materials for framing a home, there are lots of choices! Here’s a quick look:
Choose the right fastener size and type for your application. Galvanized or stainless steel fasteners will stop corrosion and keep your frame safe for years.
Pro Tip: Check local codes and manufacturer recommendations for appropriate fasteners. Metal connectors can be the way to go!
P1 – Metal connectors and anchors are essential for the structural integrity of a house. These specialized hardware items create a stable framework to withstand stresses and strains.
P2 – To understand this component requirement, check out the data-filled table below:
Hardware Type | Material Type | Usage |
---|---|---|
Joist hangers | Galvanized | Connect joists to headers for support |
Hurricane ties | Steel | Provide rafter to wall connection during high wind events |
Strap ties | Stainless steel | Reinforce trusses against uplifting forces |
P3 – Precision engineered metal connectors reinforce weak points for added stability. Customizable straps and anchor bolts offer versatile attachments for robustness in extreme conditions.
P4 – Don’t leave safety considerations out when framing a house without metal connectivity equipment. Improper use of these fixtures can make the dwelling vulnerable to natural disasters, earthquakes or security breaches. Utilize metal connectivity equipment for dependable construction and stay safeguarded.
To make a house energy efficient and comfortable, insulation and vapor barriers are needed. Insulation maintains indoor temps while vapor barriers stop moisture from entering the structure. Here’s the material you need for insulation and vapor barriers:
Material | Description |
Fiberglass batts | This is an inexpensive material used to insulate walls, floors and ceilings. |
Spray foam | A more expensive option that acts as both insulation and a vapor barrier. It’s good for small spaces or crevices. |
Rigid foam board | This board is water-resistant and provides a good thermal barrier when used as exterior insulation. |
Vapor retarders | Vapor retarders help control moisture transmission by forming a physical barrier between inside and outside. They can be made of plastic films or aluminum foil. |
Different homes need different insulation and vapor barriers. Climate, building codes, budget constraints, and other factors should be considered. High-quality materials for insulation can lower energy bills and keep your family comfortable. Don’t miss out! Invest in proper insulation and vapor barriers today! Ready to splurge? Let’s see the cost of framing a house! Nothing says luxury like a big bill!
To estimate the cost of framing a house, you will need to calculate the square footage of the house, specify the type and quantity of materials, and determine the cost of labor and equipment. These sub-sections provide a comprehensive guide to help you accurately estimate the total cost of framing your house.
To work out how much area you need, you must know the total square footage of your house. This info is important so you can get the right materials and have an idea of labor costs. Here’s a step-by-step guide:
Include external measurements for decks and patios. Use floor plan templates or 3D floor planners for accurate estimates.
Be sure to have anti-tamper measuring tools and make individual designs with correct dimensions. Check your results and double-check measurements physically – this prevents buying extra materials due to errors!
When framing a house, precise material specifications are important. Quality materials mean good construction and less maintenance. Accurate calculations help with budget and timeline.
Here is a table of the typical 2,500 sq. ft. house material requirements:
Materials | Quantity |
---|---|
Lumber (2×4) | 8,000 board feet |
Lumber (2×6) | 4,000 board feet |
Nails | 300 lbs |
Sheathing | 1,500 sq. ft. |
Insulation | 1,800 sq. ft. |
Vapor Barrier | 1,800 sq. ft. |
Choose reliable suppliers for high-quality materials at a fair price. Make sure you get the right permits before starting.
A builder once shared his experience framing a difficult house. The terrain was uneven, so extra excavation was needed. Nonetheless, he finished on time and within budget with correct material amounts and efficient methods.
Calculating labor and equipment cost might give you a bigger headache than the one you got from hammering that last nail.
To estimate the cost of labor and equipment for framing a house, you must understand the details. Here’s a table with average costs.
Aspect | Average Cost |
---|---|
Labor cost per hour | $30 – $100 |
Equipment rental per day | $200 – $800 |
Nails, screws, bolts | $0.01 – $0.10 |
Lumber | $2 – $6 |
This data will help you make an informed decision. Use top-notch materials for durability and to save money in the long run. Oh, and one more thing: framed houses never have bad hair days!
To save money while framing your house, you need to be strategic in your approach. In order to achieve this, we have come up with a section called “Tips for Saving Money on Framing a House” with sub-sections such as “Consider Using Alternative Materials”, “Shop Around for the Best Prices”, and “Plan Ahead to Avoid Costly Delays”. With these tips, you can successfully cut down your framing costs without sacrificing quality.
Detectiving Alternatives to Cut Framing Costs
Time to become a detective and get the best price for framing a house! Investing in cost-efficient materials can save money and still make a strong structure. For example, non-wood materials like bamboo, straw bales, and SIPs provide stability and insulation without breaking the bank. Furthermore, prefabricated walls, roofs, and floors are an easy way to reduce labor costs, as they assemble quickly. Finally, 3D printing offers affordable customization and is a great way to fulfill a design. In recent years, green framing has become popular, as it’s great for cutting development costs and protecting the environment.
It’s essential to save money when framing a house. To achieve this, explore all options and compare prices carefully. Here are some tips to consider:
Remember that price isn’t the only thing to consider. Quality must also be taken into account. Low-cost materials or inexperienced framers could damage your entire construction project.
To save money, research different suppliers and negotiate. According to TrueSituation.com, customers saved up to 35% by researching before hiring professionals. Start planning your framing a year early and you won’t be over budget.
To save money when framing a house, plan ahead! Get the materials, equipment and labor you need before construction starts. Have blueprints and permits ready. And hire experienced contractors. Order materials in advance too.
Clear communication is important too. Everyone should know their role. Otherwise, costly mistakes may occur. It’s risky to frame a house without any experience. So, it’s better to hire an expert.
This Semantic NLP variation of ‘Plan Ahead to Avoid Costly Delays’ highlights the importance of careful early planning. Thus, saving money on framing a house and having more cash for therapy with your partner!
Inference and Vital Points:
Additional Insight:
Call-to-action:
The price of framing a house can vary widely depending on factors such as the size of the house, the complexity of the design, and the materials used. A good way to estimate the cost is to calculate the total square footage of the house and multiply it by the average cost per square foot for framing in your area.
Wood and steel are the two most common materials used for house framing. Wood is the more traditional option and is often favored for its aesthetic appeal, while steel is more durable and has a longer lifespan.
Steel framing is generally more expensive than wood framing due to the higher cost of materials and the specialized labor required for installation. However, the longer lifespan of steel framing may make it a more cost-effective option in the long run.
The average cost per square foot for framing a house can vary widely depending on location, but it is typically between $5 and $10 per square foot. However, this price can increase significantly for more complex designs or if you opt for higher-end materials.
The time it takes to frame a house can vary depending on factors such as the size and complexity of the design, the skill level of the workers, and the weather conditions. However, a typical timeframe is 4 to 8 weeks.
Here I am going to share some steps to get your framing construction cost estimate report.
You can send us your plan on info@estimatorflorida.com
Before starting your project, we send you a quote for your service. That quote will have detailed information about your project. Here you will get information about the size, difficulty, complexity and bid date when determining pricing.
We do framing construction cost estimating and prepare a detailed report for your project. At last you finalize the report and finish the project.
561-530-2845
info@estimatorflorida.com
Address
5245 Wiles Rd Apt 3-102 St. Pete Beach, FL 33073 United States
561-530-2845
info@estimatorflorida.com
Address
5245 Wiles Rd Apt 3-102 St. Pete Beach, FL 33073 United States
All copyright © Reserved | Designed By V Marketing Media | Disclaimer
IMPORTANT: Make sure the email and cell phone number you enter are correct. We will email and text you a link to get started.
By clicking “I Agree” above you give Estimate Florida Consultin express written consent to deliver or cause to be delivered calls and messages to you by email, telephone, pre-recorded message, autodialer, and text. Message and data rates may apply. You are able to opt-out at any time. You can text STOP to cancel future text messages.