How Much Does It Cost To Build a 3000 sq ft Warehouse?
Building a warehouse is a significant investment that requires careful planning and budgeting. The costs associated with constructing a 3,000 square foot warehouse can vary widely depending on several factors. This article provides a detailed breakdown of the costs involved, including materials, labor, site preparation, and additional expenses. Understanding these factors will help you make informed decisions and ensure a successful construction project. Properly planning for these costs can also prevent budget overruns and ensure that the warehouse meets your operational needs and standards.
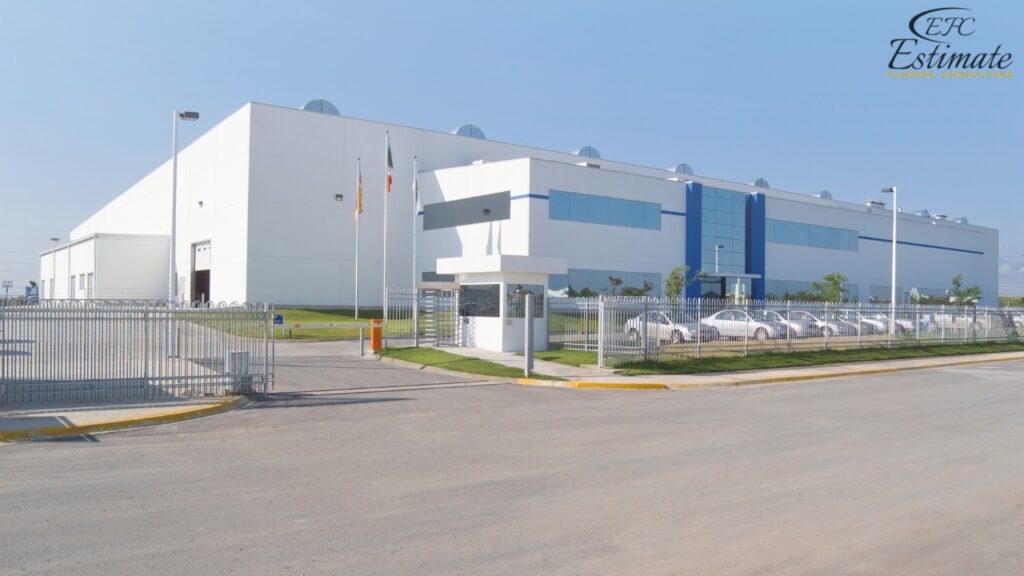
Factors Influencing the Cost of Building a Warehouse
Location
The location of the warehouse plays a crucial role in determining the overall cost. Urban areas typically have higher land costs and stricter building codes, which can increase expenses. Conversely, rural areas may offer more affordable land but could incur additional costs for transportation and infrastructure. Additionally, proximity to major transportation routes and accessibility for suppliers and clients can influence the location’s desirability and, therefore, its cost. Urban locations, while more expensive, can offer logistical advantages, such as closer proximity to key markets and better access to utilities and services. The location can also affect insurance costs and the availability of skilled labor, which can further impact the overall budget.
- Urban Areas: $13 – $39 per square foot. Urban locations might have higher costs due to the demand for land and stricter regulations. Building in urban areas can also involve higher costs for permits, zoning, and compliance with local ordinances. These areas often have more stringent environmental and safety standards, which can require additional investment in sustainable building practices and advanced safety systems.
- Suburban Areas: $10 – $26 per square foot. Suburban areas offer a balance between cost and convenience. These areas typically have more relaxed building codes compared to urban centers but still provide good access to infrastructure and markets. Suburban areas might also offer tax incentives or subsidies to attract businesses, which can offset some construction costs.
- Rural Areas: $7 – $20 per square foot. Rural locations can be more affordable but may require additional infrastructure investments. While land is cheaper, costs can be incurred for road construction, utility extensions, and increased transportation costs due to distance from suppliers and markets. Rural areas might also face challenges such as limited access to high-speed internet and fewer local contractors, which can impact project timelines and logistics.
Location Type | Estimated Cost (per square foot) |
Urban Areas | $13 – $39 |
Suburban Areas | $10 – $26 |
Rural Areas | $7 – $20 |
Construction Type
The type of construction chosen will significantly impact the cost. Common construction types include steel, concrete, and prefabricated buildings. Each has its own advantages and cost implications. The choice of construction type can affect not only the initial costs but also the long-term maintenance and durability of the warehouse. Different construction methods can also influence the flexibility and scalability of the warehouse to adapt to future business needs.
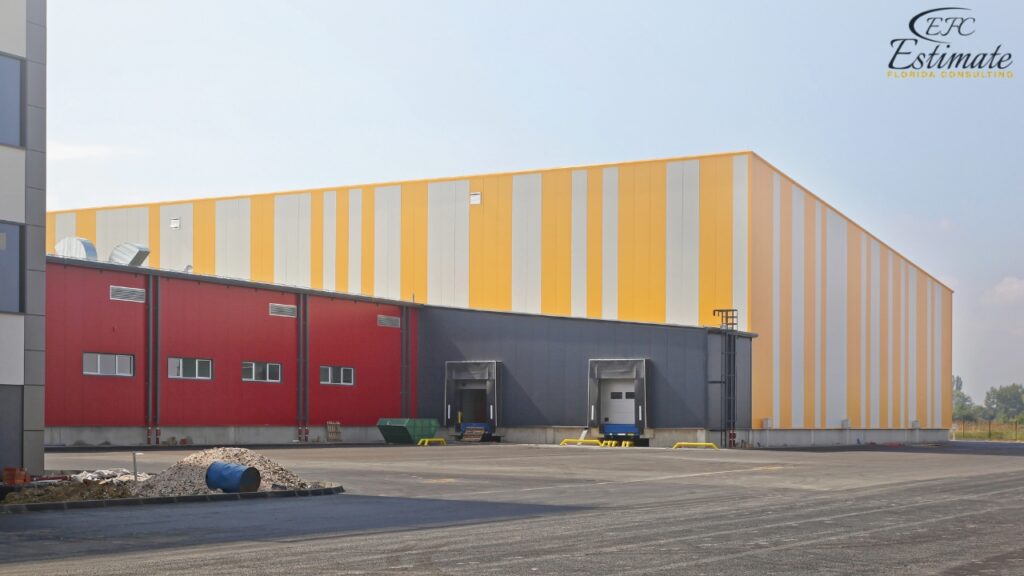
- Steel Construction: $20 – $52 per square foot. Steel is durable and flexible, making it a popular choice for warehouses. It offers quick construction times and can be easily customized for future expansions. Steel structures are also highly resistant to pests and weather conditions, reducing maintenance costs. Steel’s strength allows for large, open spaces without the need for many internal support columns, maximizing usable floor space.
- Concrete Construction: $26 – $65 per square foot. Concrete provides excellent durability and fire resistance. It is ideal for warehouses storing goods that require a controlled environment. Concrete buildings can offer better insulation and climate control, which is beneficial for temperature-sensitive products. Concrete is also highly resistant to wear and tear, making it suitable for heavy industrial use.
- Prefabricated Buildings: $13 – $39 per square foot. Prefabricated options can be more cost-effective and quicker to assemble. These buildings are manufactured off-site and then assembled on location, reducing labor costs and construction time. Prefabricated buildings also offer flexibility in design and can be easily relocated if necessary. This method can minimize construction waste and environmental impact, contributing to sustainable building practices.
Construction Type | Estimated Cost (per square foot) |
Steel Construction | $20 – $52 |
Concrete Construction | $26 – $65 |
Prefabricated Buildings | $13 – $39 |
Materials
The cost of materials can vary based on the type and quality chosen. High-quality materials can increase the overall cost but provide better durability and longevity. The choice of materials can also influence the warehouse’s functionality, energy efficiency, and maintenance requirements. Additionally, material costs can fluctuate based on market conditions, availability, and geopolitical factors.
- Basic Materials: $7 – $20 per square foot. Basic materials include standard steel and concrete. These materials offer fundamental functionality and are sufficient for general storage purposes. Basic materials might not offer the same level of durability or aesthetic appeal as higher-end options, but they can be a cost-effective solution for businesses on a tight budget.
- Mid-Range Materials: $20 – $39 per square foot. These materials offer better quality and durability. Mid-range options might include treated steel, higher-grade concrete, and improved insulation materials. These materials can enhance the warehouse’s energy efficiency and reduce long-term operating costs.
- High-End Materials: $39 – $65 per square foot. High-end materials provide superior quality and aesthetics. These might include reinforced steel, premium concrete with additives for extra durability, and advanced insulation and energy-efficient materials. High-end materials can improve the overall appearance of the warehouse and provide additional benefits such as enhanced security and better resistance to environmental factors.
Material Type | Estimated Cost (per square foot) |
Basic Materials | $7 – $20 |
Mid-Range Materials | $20 – $39 |
High-End Materials | $39 – $65 |
Get 5 New Leads Next 7Days With Our System
- Warehouse Roofing
- Warehouse Flooring
- Electrical
- Warehouse Plumbing
- Warehouse Construction
- Warehouse Insulation
Labor Costs
Labor costs can vary significantly based on the region and the complexity of the project. Skilled labor is essential for ensuring quality construction and adherence to building codes. The availability of skilled labor and local wage rates can also influence overall labor costs. Additionally, the project’s timeline and the need for specialized skills can impact labor expenses.
- Basic Labor: $7 – $13 per square foot. Basic labor includes general construction workers. These workers handle tasks such as framing, roofing, and general construction activities. While basic labor is less expensive, it may require more oversight to ensure quality and compliance with building standards.
- Skilled Labor: $13 – $26 per square foot. Skilled labor includes electricians, plumbers, and specialized trades. These professionals are necessary for installing electrical systems, plumbing, HVAC, and other specialized installations. Skilled labor ensures that the warehouse meets all safety and operational standards, which is crucial for avoiding costly repairs or compliance issues in the future.
- Project Management: $7 – $20 per square foot. Project management includes overseeing the construction process and ensuring timelines and budgets are met. Effective project management is crucial for coordinating the various aspects of the build, ensuring quality control, and managing subcontractors. Good project management can prevent delays and cost overruns, ensuring the project is completed on time and within budget.
Labor Type | Estimated Cost (per square foot) |
Basic Labor | $7 – $13 |
Skilled Labor | $13 – $26 |
Project Management | $7 – $20 |
Site Preparation
Site preparation is a crucial step in the construction process and can include grading, excavation, and utility installation. The cost of site preparation can vary based on the condition of the land and the extent of work required. Proper site preparation ensures a stable foundation and can prevent future structural issues. Site preparation can also involve environmental assessments and remediation, especially if the land was previously used for industrial purposes.
- Basic Site Preparation: $1 – $7 per square foot. This includes minor grading and clearing. Basic site preparation is sufficient for relatively flat and clear land with minimal obstacles. This step ensures that the ground is level and ready for construction.
- Moderate Site Preparation: $7 – $13 per square foot. This includes excavation, drainage, and basic utility installation. Moderate site preparation is necessary for land with slight slopes or some vegetation that needs to be cleared. Proper drainage installation is crucial for preventing water damage and ensuring the longevity of the warehouse.
- Extensive Site Preparation: $13 – $26 per square foot. This includes major grading, complex drainage systems, and comprehensive utility installation. Extensive site preparation is required for land with significant slopes, rock removal, or extensive vegetation clearing. This level of preparation ensures that the site can support the warehouse structure and handle any environmental challenges.
Site Preparation Type | Estimated Cost (per square foot) |
Basic Site Preparation | $1 – $7 |
Moderate Site Preparation | $7 – $13 |
Extensive Site Preparation | $13 – $26 |
Detailed Cost Breakdown for Building a 3,000 Square Foot Warehouse
Here’s a detailed cost breakdown for building a 3,000 square foot warehouse, considering various factors:
Cost Component | Estimated Cost |
Location (Urban) | $39,000 – $117,000 |
Construction Type (Steel) | $60,000 – $156,000 |
Materials (Mid-Range) | $60,000 – $117,000 |
Labor (Skilled) | $39,000 – $78,000 |
Site Preparation (Moderate) | $21,000 – $39,000 |
Total | $219,000 – $507,000 |
Examples of Total Costs for Different Scenarios
To provide a clearer picture, here are some examples of total costs for different scenarios:
Basic Warehouse in a Rural Area
- Low-end: $117,000
- High-end: $210,600. This includes basic materials, minimal site preparation, and basic labor. This type of warehouse is suitable for general storage and less critical operations.
Mid-Range Warehouse in a Suburban Area
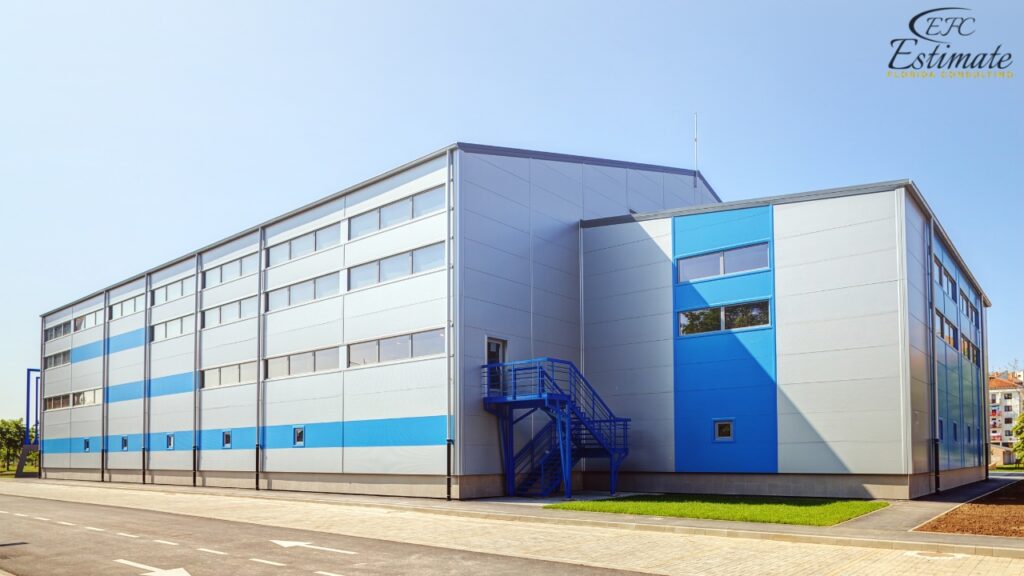
- Low-end: $219,000
- High-end: $421,200. This includes mid-range materials, moderate site preparation, and skilled labor. This option balances cost and functionality, providing a durable and efficient warehouse space.
High-End Warehouse in an Urban Area
- Low-end: $351,000
- High-end: $780,000. This includes high-end materials, extensive site preparation, and comprehensive project management. A high-end warehouse offers advanced features, such as climate control and high-quality finishes, ideal for storing sensitive or high-value goods.
Cost Considerations by Region for Building a Warehouse
The cost of building a warehouse can vary significantly depending on the region due to differences in labor costs, material availability, and local economic conditions. Here’s a brief overview of regional cost variations:
- Northeast: Generally higher costs due to labor and material expenses. Expect to pay 10-20% more than the national average. The higher cost of living and demand for skilled labor in this region contribute to increased expenses. Additionally, the colder climate can impact the availability of certain materials and the timing of installation projects.
- Midwest: More affordable, with costs typically 5-15% lower than the national average. The availability of local materials and lower labor costs help keep prices reasonable in this region. The Midwest’s moderate climate also allows for more flexible scheduling of installation projects throughout the year.
- South: Moderate costs, often close to the national average. Lower labor costs in some Southern states can also help reduce overall expenses. The mild climate in many parts of the South can also extend the installation season, providing more flexibility for scheduling projects. The region’s booming housing market can also impact the demand and pricing for skilled labor and materials.
- West: Higher costs, similar to the Northeast, with variations depending on the urban or rural setting. Coastal areas and major cities tend to have higher labor and material costs, while rural areas may be more affordable. The need for specialized materials and construction techniques in earthquake-prone areas can also increase costs. The region’s diverse climate and geography can also affect the availability and pricing of certain types of granite.
Understanding regional cost differences can help you budget more accurately and make informed decisions about hiring local contractors. It’s also helpful to ask for local references and view previous work to ensure you’re getting the best quality for your investment.
Advantages of Building a Warehouse
Storage and Inventory Management
Building a warehouse provides ample space for storage and inventory management. This is crucial for businesses that deal with large volumes of goods. A well-designed warehouse can improve efficiency and organization, leading to better inventory control and reduced costs associated with lost or damaged goods. With a dedicated warehouse, businesses can implement sophisticated inventory management systems that optimize space utilization and streamline operations. This can result in faster order fulfillment, reduced labor costs, and improved customer satisfaction.
Business Expansion
A warehouse can support business expansion by providing additional space for operations. This is particularly important for growing businesses that need to scale up their storage and distribution capabilities. Having a dedicated warehouse allows businesses to handle increased demand and expand their product lines without facing space constraints. Moreover, owning a warehouse provides flexibility for future growth, enabling businesses to adapt to changing market conditions and consumer demands. It also offers the potential for diversification of services, such as third-party logistics or order fulfillment for other businesses.
Increased Property Value
Investing in a warehouse can increase the property value. Warehouses are valuable assets that can be leased out to other businesses, providing a steady income stream. Additionally, owning a warehouse can enhance the overall value of your business by adding to its physical assets and improving its operational capabilities. Warehouses can be customized to suit various industries, making them attractive to a wide range of potential tenants. This versatility enhances their marketability and can lead to higher rental income and better occupancy rates. Furthermore, a well-maintained warehouse can appreciate over time, providing a significant return on investment.
Download Template For Warehouse Project Breakdown
- Materials list updated to the zip code
- Fast delivery
- Data base of general contractors and sub-contractors
- Local estimators
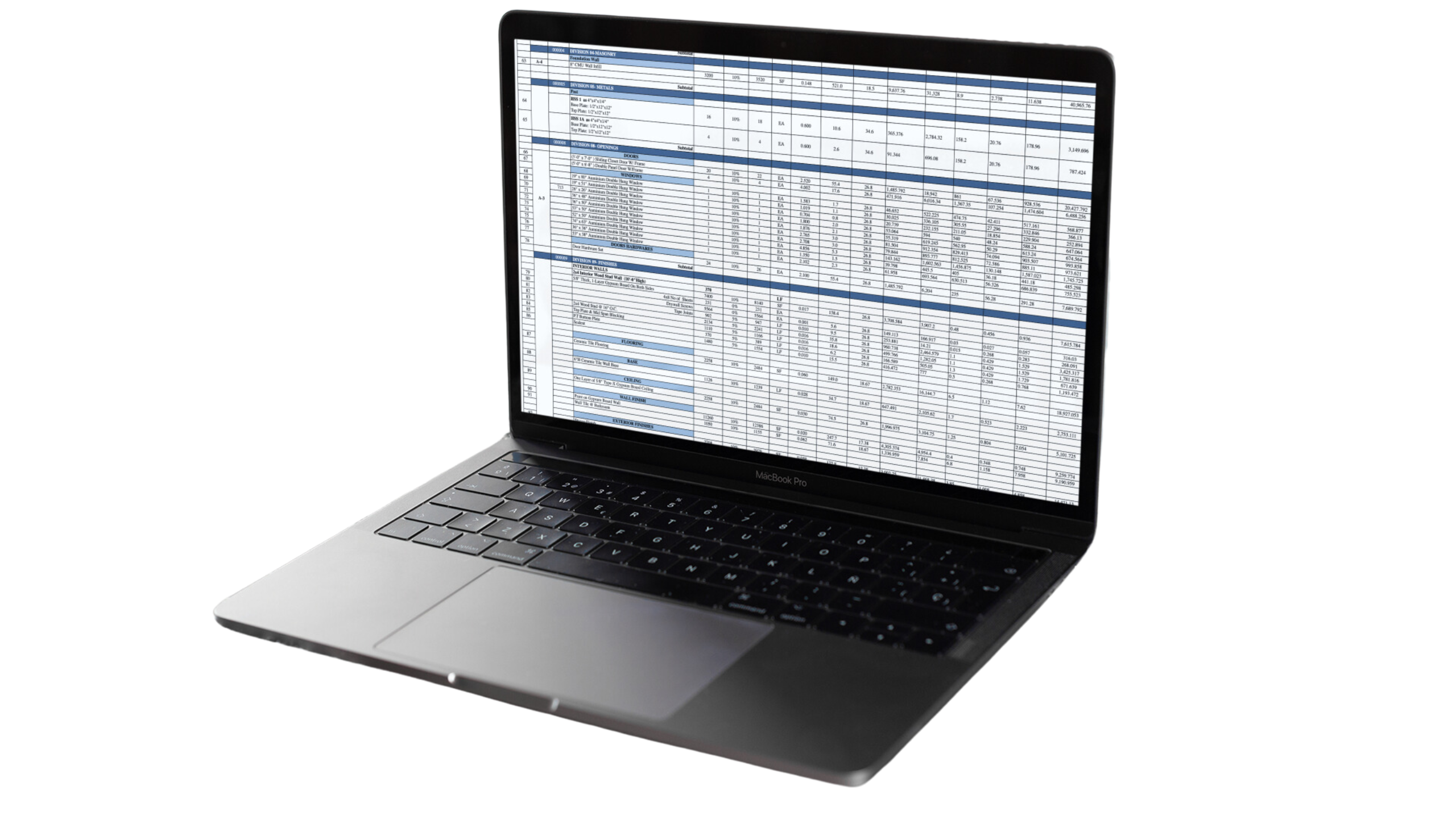
Conclusion
Building a 3,000 square foot warehouse is a significant undertaking that involves various costs, from location and construction type to materials, labor, and site preparation. By understanding these costs and planning accordingly, you can ensure a successful construction project that meets your business needs. Whether you are building a basic warehouse in a rural area or a high-end facility in an urban location, careful budgeting and selecting the right professionals are key to achieving the desired results. Proper planning and execution can help you create a functional, efficient, and valuable asset for your business. Investing in a warehouse not only supports your current operational needs but also positions your business for future growth and success. By considering all factors and making informed decisions, you can build a warehouse that enhances your business’s efficiency, scalability, and profitability.
FAQs
Building a warehouse involves costs influenced by location, construction type, materials, labor, and site preparation. Urban areas generally cost $13 – $39 per sq ft due to higher land prices and regulations, while suburban areas range $10 – $26 per sq ft, and rural areas are $7 – $20 per sq ft.
Urban areas are costly ($13 – $39 per sq ft) due to high demand and regulations. Suburban areas ($10 – $26 per sq ft) offer a balance of cost and convenience, and rural areas ($7 – $20 per sq ft) are affordable but may need more infrastructure investment.
Steel costs $20 – $52 per sq ft for durability and quick construction, concrete costs $26 – $65 per sq ft for durability and climate control, and prefabricated buildings cost $13 – $39 per sq ft for cost-effectiveness and quick assembly.
Basic materials cost $7 – $20 per sq ft, mid-range materials cost $20 – $39 per sq ft for better quality, and high-end materials cost $39 – $65 per sq ft for superior durability and aesthetics.
Basic labor costs $7 – $13 per sq ft, skilled labor costs $13 – $26 per sq ft, and project management costs $7 – $20 per sq ft ensure quality and compliance.
Basic site preparation costs $1 – $7 per sq ft, moderate preparation costs $7 – $13 per sq ft, and extensive preparation costs $13 – $26 per sq ft for stable foundations and compliance.
Estimated costs: Location (Urban): $39,000 – $117,000; Construction Type (Steel): $60,000 – $156,000; Materials (Mid-Range): $60,000 – $117,000; Labor (Skilled): $39,000 – $78,000; Site Preparation (Moderate): $21,000 – $39,000; Total: $219,000 – $507,000.
Basic Warehouse in Rural Area: $117,000 – $210,600; Mid-Range Warehouse in Suburban Area: $219,000 – $421,200; High-End Warehouse in Urban Area: $351,000 – $780,000.
Northeast: 10-20% higher costs; Midwest: 5-15% lower costs; South: moderate costs; West: higher costs in urban areas due to demand and specialized construction needs.
Storage and Inventory Management, Business Expansion, Increased Property Value: Enhancing operational efficiency, scalability, and profitability.
Google Reviews
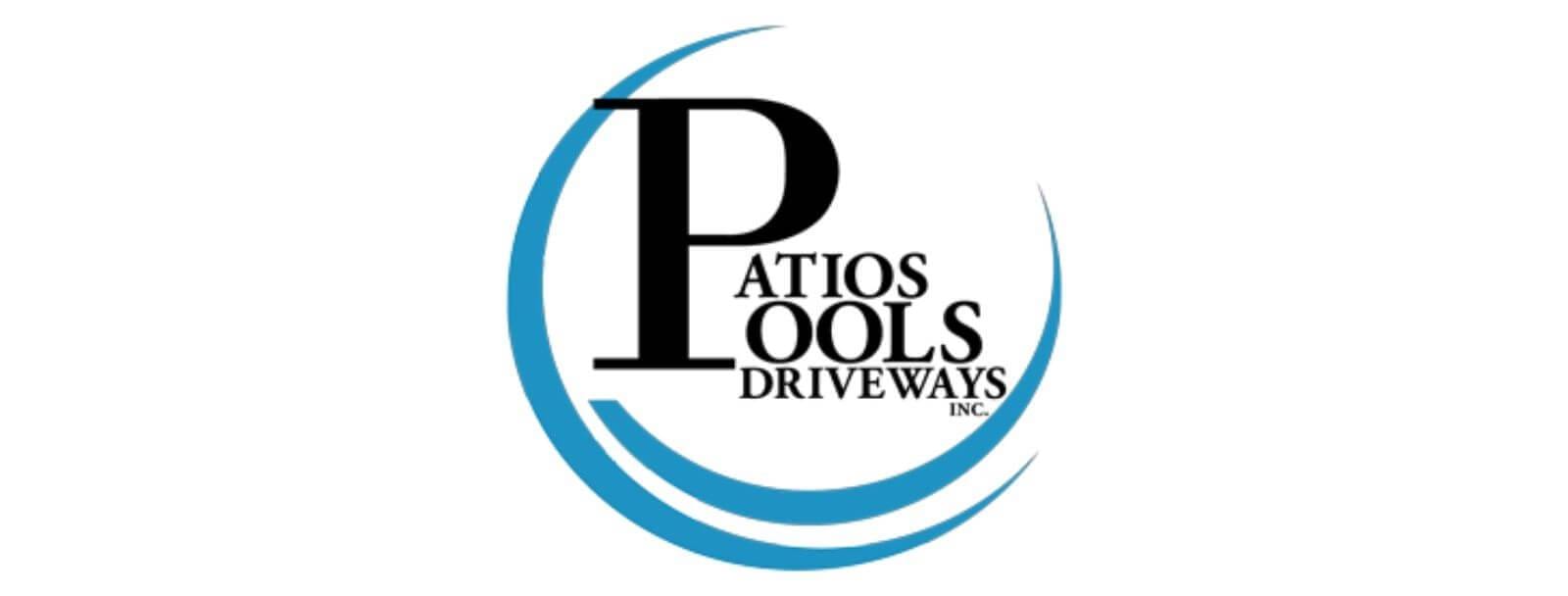
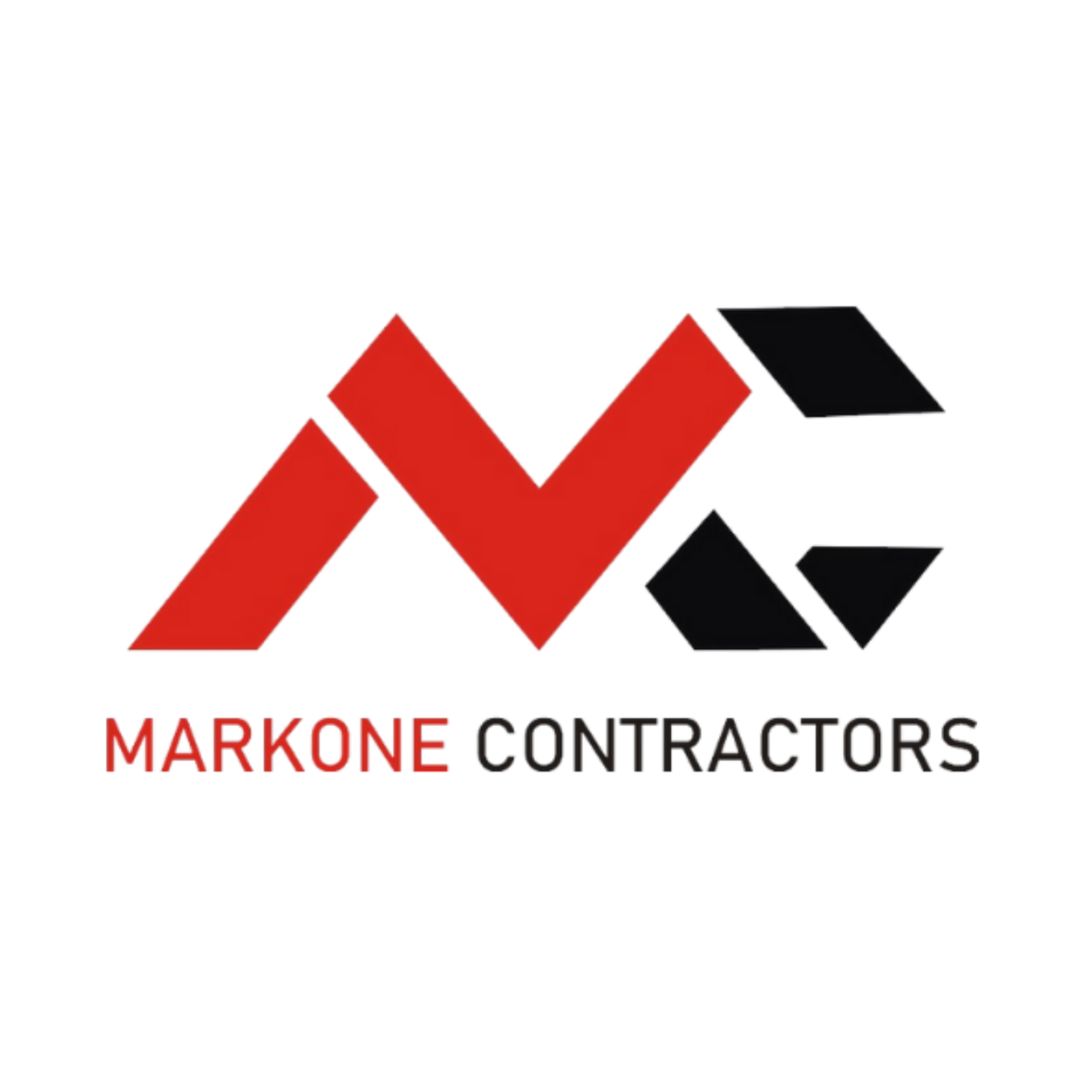

Process To Get It Cost To Build a 3000 sq ft Warehouse Estimate Report
Here I am going to share some steps to get it cost to build a 3000 sq ft warehouse estimate report.
-
You need to send your plan to us.
You can send us your plan on info@estimatorflorida.com
-
You receive a quote for your project.
Before starting your project, we send you a quote for your service. That quote will have detailed information about your project. Here you will get information about the size, difficulty, complexity and bid date when determining pricing.
-
Get Estimate Report
Our team will takeoff and estimate your project. When we deliver you’ll receive a PDF and an Excel file of your estimate. We can also offer construction lead generation services for the jobs you’d like to pursue further.