Boost Your Warehouse Construction Bids – Request a Precision Estimate!
- Accurancy
- Efficiency
- Transparency
- Customization
- Time Saving
- Professionalism
- Cost Control
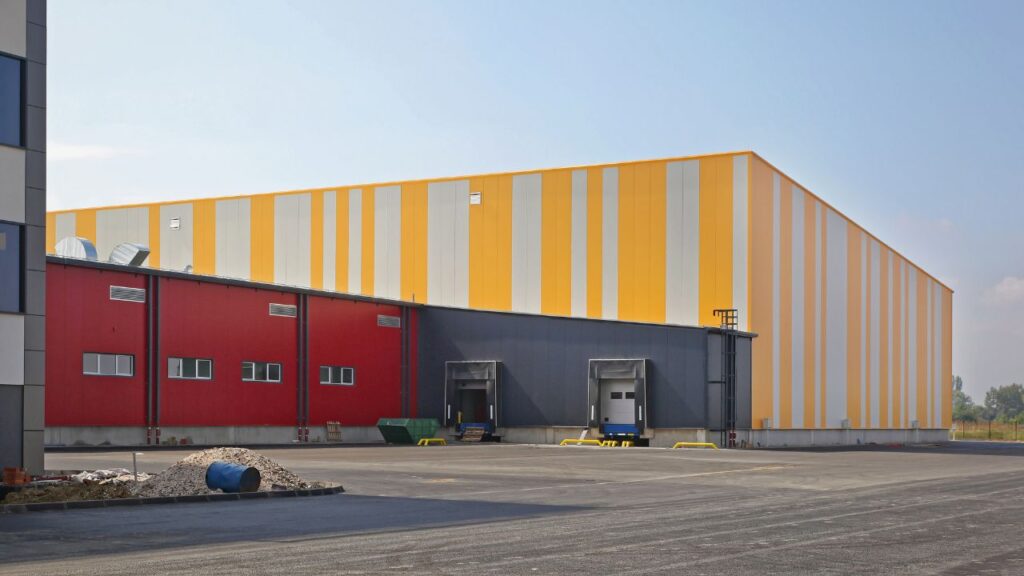
The cost to build a 15,000 sq ft warehouse can vary significantly based on factors like location, materials used, and labor costs. On average, such a project can cost anywhere from $750,000 to $1.5 million. As part of our estimation services, Estimate Florida Consulting provides detailed cost breakdowns for warehouse construction projects. With our expertise, we ensure that clients receive accurate estimates tailored to their specific needs and budgetary considerations. Whether it’s optimizing material choices or streamlining construction processes, our goal is to help clients achieve their warehouse construction goals efficiently and cost-effectively.
Estimate Florida Consulting stands ready to assist clients at every stage of the construction process, offering reliable guidance and support to ensure successful project outcomes.
A warehouse is a large commercial building designed for storage of goods, inventory, and materials. It serves as a centralized location for distribution, logistics, and supply chain operations.
The primary purpose of a warehouse is to facilitate the efficient storage and movement of goods. By providing a secure and organized space, warehouses ensure that products can be stored safely until they are needed for distribution. They play a crucial role in inventory management, enabling businesses to keep track of stock levels, monitor incoming and outgoing shipments, and optimize their storage space. Warehouses are vital in the overall supply chain process, as they act as key nodes for consolidating, sorting, and distributing goods to customers in a timely manner.
Make Informed Design Decisions Showcase Your Design Ideas
Get RenderingThe cost of building a warehouse is influenced by various factors including construction materials, labor expenses, project scope, and market pricing.
The selection of construction materials plays a significant role in determining the overall budget. High-quality materials come at a premium, potentially increasing the cost of the project.
Labor expenses can vary depending on the skill level of workers and the complexity of the construction process. The scale of the warehouse project also impacts the final price, as larger warehouses typically require more materials and labor, leading to higher costs.
Market conditions, such as demand for construction services and fluctuating material prices, can also affect the overall expense of warehouse construction.
The size and layout of a warehouse, such as a 15000 sq ft facility, play a significant role in determining the construction costs and operational efficiency.
A larger warehouse typically requires higher construction expenses, both in terms of initial building costs and ongoing maintenance. By contrast, smaller warehouses may have lower upfront expenses but could face challenges in accommodating growing inventory.
Therefore, it is crucial to strike a balance between space utilization and cost efficiency when designing the layout. Optimizing the warehouse layout to minimize wasted space and streamline workflows can lead to improved operational efficiency and reduced expenses over time.
By carefully planning the layout, businesses can make better use of available square footage and enhance productivity.
The location of a warehouse affects construction costs, land acquisition expenses, regulatory compliance, and zoning requirements, all of which impact the overall project budget.
For instance, selecting a site in a prime industrial area might result in higher land prices but could offer proximity to suppliers and markets, reducing transportation costs.
Different locations come with varying permitting procedures and regulatory frameworks, influencing the timeline and costs associated with obtaining necessary approvals.
Zoning considerations play a crucial role as well, as they determine the types of activities allowed in a particular area, impacting operational flexibility and potential future expansion plans.
Selecting the right building materials for a warehouse construction project is crucial for balancing costs, ensuring structural integrity, and maintaining quality standards throughout the build.
Quality control measures, such as regular inspections and testing, play a vital role in ensuring that the chosen materials meet the project’s specifications. Adherence to industry standards not only guarantees safety and functionality but also enhances the overall longevity and performance of the warehouse structure.
Labor costs in warehouse construction encompass expenses related to project management, contractor fees, skilled labor, and workforce efficiency, all of which contribute to the total project expenses.
Warehouses come in various types, including distribution centers, fulfillment centers, and cold storage facilities, each serving specific functions in the supply chain.
A distribution center is a warehouse designed for efficient logistics operations, inventory management, and order fulfillment to meet the demands of a widespread customer base.
These centers play a crucial role in the supply chain by serving as hubs for receiving, storing, and shipping goods. They help in streamlining the movement of products, consolidating shipments, and reducing transportation costs.
Distribution centers facilitate quick order processing, ensuring timely delivery to customers. By strategically locating these centers, companies can optimize their inventory levels and respond swiftly to fluctuations in demand. This centralized approach enhances overall operational efficiency, improves customer satisfaction, and enables better inventory control.
A fulfillment center is a warehouse dedicated to processing online orders, managing inventory for e-commerce businesses, and ensuring timely delivery to customers.
These centers play a crucial role in the e-commerce supply chain by handling tasks such as receiving, storing, and shipping goods efficiently. Order fulfillment processes in fulfillment centers involve picking, packing, and shipping products accurately and swiftly. Advanced inventory tracking systems help in managing stock levels, reducing errors, and optimizing storage space.
Technology plays a significant role in streamlining operations, with automation, robotics, and AI enhancing the efficiency of logistics processes, ultimately leading to improved customer service and satisfaction.
A cold storage warehouse provides refrigerated or frozen storage facilities for perishable goods, maintaining controlled temperature conditions to preserve product quality and safety.
By utilizing advanced refrigeration technology, these warehouses play a crucial role in managing temperature-sensitive inventory such as dairy products, pharmaceuticals, and fresh produce. In the cold chain logistics industry, these facilities ensure compliance with strict storage regulations to prevent spoilage and contamination. Cold storage warehouses are equipped with specialized monitoring systems to track temperature variations and ensure optimal conditions for storing delicate items. These facilities serve as vital links in the supply chain, extending the shelf life of perishable items and enabling efficient distribution to consumers.
Constructing a 15,000 sq ft warehouse isn’t just about the square footage; it’s about where you build, what you build with, and who does the building. On average, prices range from $750,000 to $1.5 million. But don’t just guess your budget – let Estimate Florida Consulting give you the details. We specialize in tailored cost breakdowns for warehouse projects, ensuring your estimates align with your unique requirements and financial plan. From material selection to construction efficiency, our aim is to help you build smart, not just big. Count on Estimate Florida Consulting for thorough support at every construction phase, guiding you towards a successful, budget-friendly warehouse project.”
The average cost for constructing a basic warehouse typically includes expenses for foundation work, framing, roofing, and essential utilities, providing a baseline estimate for budget planning.
Foundation work is one of the critical aspects of warehouse construction, involving excavation, site preparation, and concrete pouring. The expenses for foundation materials like footings and slabs vary based on the soil condition and local building codes.
When it comes to structural framing, factors such as steel or wood framing, size, and complexity of the warehouse influence costs. Roofing materials such as metal panels or asphalt shingles are significant cost components. Basic utilities encompass electrical wiring, plumbing, and HVAC systems, contributing to the overall construction budget.
Several factors can escalate the cost of warehouse construction, including expanded project scope, quality control measures, and thorough risk assessment to mitigate potential financial risks.
Efficient cost management practices, value engineering techniques, and effective contract negotiations can help reduce the overall expenses of building a warehouse while optimizing project efficiency.
Beyond construction expenses, building a warehouse incurs additional costs for site preparation, permit acquisition, utility installations, and procurement of necessary equipment and furniture.
Site development charges are a crucial component of these supplementary expenses, involving land grading, drainage systems, and road access creation. Regulatory permits cover fees for zoning, environmental assessments, and building code compliance.
Utility connections encompass expenses for water, electricity, gas, and telecommunications hook-ups. The purchase of equipment such as storage racks, forklifts, and conveyors adds to the overall financial outlay required for setting up a functional warehouse facility.
Site preparation activities for a warehouse project encompass land clearing, earthwork, environmental assessments, and compliance with zoning regulations to ensure a suitable foundation for construction.
These crucial tasks play a pivotal role in the initial stages of warehouse development. Land acquisition processes involve negotiations, property assessments, and securing necessary permits. Environmental impact studies help identify and mitigate potential risks to ecosystems and water sources, ensuring sustainable development practices are followed. Regulatory compliance checks ensure that the project meets local and national standards, safeguarding against legal issues. This comprehensive approach sets the stage for a well-planned and environmentally conscious warehouse project.
Obtaining necessary permits, conducting inspections, and adhering to building codes and regulations are essential steps in the warehouse construction process to ensure legal compliance and project approval.
Without the proper permits, a warehouse project may encounter delays, fines, or even complete shutdowns, causing significant financial setbacks and legal issues. Understanding the permit application procedures and regulatory compliance requirements is crucial for navigating the complex landscape of building regulations.
Inspections play a key role in verifying that construction meets safety standards, ensuring the structural integrity and fire safety of the warehouse. By following these procedures diligently, warehouse developers can mitigate risks and avoid costly legal complications down the line.
Installing essential utilities such as electrical systems, plumbing fixtures, and HVAC units is crucial for operational functionality and occupant comfort within a warehouse structure.
Effective utility installations play a pivotal role in the overall functionality and efficiency of a warehouse. Proper electrical wiring ensures a reliable power supply for machinery and lighting, improving productivity and safety. Plumbing infrastructure facilitates water supply and sanitation needs, ensuring smooth operations and a hygienic environment. HVAC considerations are essential for maintaining optimal indoor air quality and temperature control, creating a comfortable working environment for employees. Incorporating energy-efficient measures such as LED lighting and high-efficiency HVAC systems can lead to cost savings and sustainability benefits in the long run.
Equipping a warehouse with necessary tools, storage systems, pallet racking, shelving units, and office furniture is essential to support efficient storage, inventory management, and operational workflow.
For seamless operations, procurement of specific equipment like forklifts, pallet jacks, conveyors, and mezzanine systems is vital. These material handling tools contribute significantly to the smooth movement and organization of goods within the warehouse.
When selecting office furnishings, ergonomic chairs, desks, and lighting fixtures should be prioritized to create a comfortable and productive workspace for warehouse staff. Considering the space layout, implementing mezzanine flooring can efficiently maximize vertical space. Integrating these elements ensures a well-equipped warehouse setup.
Building a 15,000 square foot warehouse involves various costs, from construction materials and labor expenses to additional factors such as site preparation and equipment. On average, these projects can range from $750,000 to $1.5 million, but the final cost will depend on specific requirements and location. At Estimate Florida Consulting, we offer comprehensive cost breakdowns and guidance, ensuring each project is handled efficiently and within budget. Our expertise in navigating the complexities of warehouse construction, from material selection to project management, ensures clients receive accurate estimates and quality service. Trust in our ability to assist you through every stage of your warehouse construction project, delivering results that meet your specific needs and financial parameters.
The cost to build a 15000 sq ft warehouse can vary depending on factors such as location, materials used, and labor costs. However, on average, it can cost anywhere from $750,000 to $1.5 million.
The main factors that can affect the cost of building a 15000 sq ft warehouse include the location and size of the warehouse, the type of materials used, labor costs, and any additional features or customizations.
When it comes to materials, it is important to choose ones that are durable and cost-effective. Some commonly used materials for warehouse construction include steel, concrete, and metal panels.
The location of a warehouse can greatly impact the cost of construction. Factors such as land prices, building regulations, and access to utilities can all affect the overall cost of building a 15000 sq ft warehouse in a specific location.
Aside from the construction costs, there may be additional expenses to consider such as permits, architectural and engineering fees, and equipment costs. It is important to factor in all of these costs when budgeting for a warehouse build.
Yes, there are ways to reduce the cost of building a 15000 sq ft warehouse. These include choosing cost-effective materials, utilizing energy-efficient features, and working with experienced contractors who can help find cost-saving solutions.
Here I am going to share some steps to get it cost to build a 15000 square foot warehouse estimate report.
You can send us your plan on info@estimatorflorida.com
Before starting your project, we send you a quote for your service. That quote will have detailed information about your project. Here you will get information about the size, difficulty, complexity and bid date when determining pricing.
Our team will takeoff and estimate your project. When we deliver you’ll receive a PDF and an Excel file of your estimate. We can also offer construction lead generation services for the jobs you’d like to pursue further.
561-530-2845
info@estimatorflorida.com
Address
5245 Wiles Rd Apt 3-102 St. Pete Beach, FL 33073 United States
561-530-2845
info@estimatorflorida.com
Address
5245 Wiles Rd Apt 3-102 St. Pete Beach, FL 33073 United States
All copyright © Reserved | Designed By V Marketing Media | Disclaimer