Boost Your Machanical Bids – Request a Precision Estimate!
- Accurancy
- Efficiency
- Transparency
- Customization
- Time Saving
- Professionalism
- Cost Control
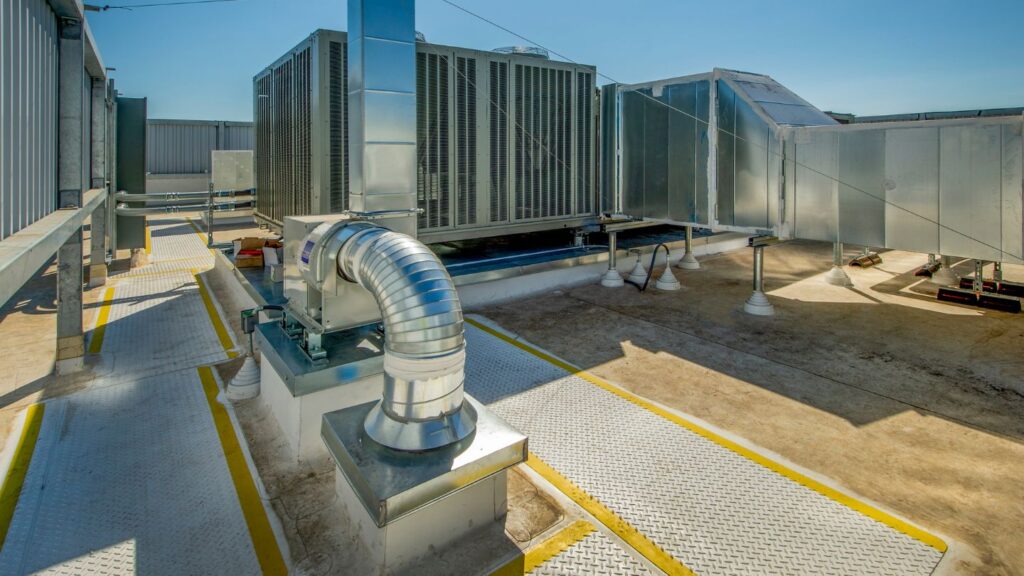
In the intricate landscape of healthcare facilities, where optimal indoor air quality is paramount, the HVAC system plays a vital role. Efficient ductwork is crucial for maintaining a healthy environment for patients, staff, and visitors. This article aims to provide a comprehensive guide to estimating the costs associated with hospital building ductwork, addressing key considerations and factors influencing expenses.
Estimating ductwork costs for hospitals begins with a careful consideration of material expenses. The type and quality of duct material are critical cost factors, with options ranging from galvanized steel and aluminum to stainless steel or fiberglass. In healthcare settings, where hygiene and safety standards are paramount, selecting materials that meet specific requirements is essential. Additionally, estimating costs for insulation materials is crucial, as hospitals often have stringent requirements to maintain temperature control and prevent the spread of contaminants.
Fully Insured License
Hire Contractor For Hospital Construction
Make Informed Design Decisions Showcase Your Design Ideas
Get RenderingLabor is a substantial component of ductwork cost estimation. Skilled labor, including sheet metal workers and HVAC technicians, is necessary for ductwork installation. Local labor rates and any specialized skills required for hospital projects should be considered. Moreover, the complexity of installation, influenced by factors such as hospital layout and ventilation requirements, may impact labor hours and, subsequently, overall costs.
The complexity of the hospital’s ventilation system is a significant cost determinant. Hospital ventilation must adhere to strict standards for air quality and infection control. Factors such as the number of air changes per hour, specialized zones like operating rooms or isolation rooms, and specific filtration requirements contribute to the overall complexity of the design, influencing costs. Ensuring regulatory compliance with local building codes and healthcare facility guidelines is essential and may entail additional costs.
The size and scale of the hospital project directly affect ductwork costs. Consideration of total square footage, including ventilation needs and layout intricacies, is crucial. Larger hospitals with more extensive ventilation requirements will generally incur higher costs. Additionally, if the hospital has multiple floors, vertical duct runs may be necessary, adding complexity and cost to the installation process.
Including a contingency budget is imperative in the estimation process to account for unforeseen circumstances, design changes, or unexpected challenges during construction. Contingency planning helps mitigate potential financial risks. Moreover, factoring in general overhead costs, such as project management, permits, and administrative expenses, ensures a comprehensive estimate that covers all aspects of the project.
Keeping abreast of market conditions is crucial for accurate cost estimation. Fluctuations in material and labor costs based on current market trends can impact the overall estimation. Regularly monitoring and adjusting estimates in response to market changes ensure that the budget remains aligned with real-time conditions.
Innovative ductwork technologies introduce additional considerations for cost estimation. Exploring advanced solutions, such as pre-fabricated components or energy-efficient systems, may have different cost implications. Evaluating the benefits and costs associated with these technological advancements allows for informed decision-making and aligning the project with sustainability goals.
Duct Material | Cost Range (per linear foot) |
Galvanized steel | $10 – $15 |
Aluminum | $15 – $20 |
Stainless steel | $20 – $30 |
Fiberglass | $8 – $12 |
Insulation | Cost Range (per square foot) |
High-quality insulation | $2 – $5 |
Skilled Labor | Cost Range (per hour) |
Sheet metal workers | $40 – $60 |
HVAC technicians | $50 – $70 |
Installation Complexity | Cost Range (labor premium) |
Complex systems | 10% – 20% of total labor costs |
Ventilation System Complexity | Cost Range |
Specialized zones and filtration | $5,000 – $15,000 |
Compliance verification and documentation | $3,000 – $8,000 |
Square Footage | Cost Range (per square foot) |
Ductwork | $6 – $10 |
Number of Floors | Cost Range (vertical duct runs per floor) |
Vertical duct runs | $2,000 – $5,000 |
Contingency | Cost Range (percentage of total estimated costs) |
Contingency | 5% – 10% |
Overhead Costs | Cost Range |
Project management, permits, and administrative expenses | $15,000 – $25,000 |
Material and Labor Market Trends | Adjustment Range |
Monitor and adjust estimates based on market fluctuations | +/- 5% – 10% |
Advanced Ductwork Systems | Cost Range (Varies based on technology) |
Evaluate costs and benefits of innovative solutions | Varies based on technology |
Overall Estimate | Cost Range |
Total Estimated Ductwork Costs | $80,000 – $150,000 |
Note: These estimates are indicative and should be used as a reference. Actual costs may vary based on specific project requirements, location, and market conditions.
The cost of hospital duct installation can vary widely depending on various factors such as the size of the facility, the complexity of the ductwork system, the type of HVAC (heating, ventilation, and air conditioning) system being installed, local labor rates, and regional construction costs. Additionally, any specific requirements or regulations for healthcare facilities may also impact the pricing.
As a general guideline, hospital duct installation costs are typically measured in terms of cost per square foot or cost per linear foot of ductwork. On average, you might expect the cost to range from $5 to $15 per square foot for ductwork installation in a hospital setting.
However, this is a broad estimate and the actual cost could be higher or lower based on the aforementioned factors.
Estimating expenses for HVAC installation in healthcare facilities is contingent on factors such as size, complexity, and facility-specific HVAC needs. Specialized considerations, particularly regarding the critical role HVAC systems play in maintaining air quality and infection prevention, contribute to the overall cost. Larger facilities may incur higher costs due to extensive ventilation requirements, while the complexity of system design, including specialized zones and stringent filtration, adds intricacy. Compliance with healthcare regulations further impacts installation costs. Collaborating with experienced HVAC professionals is essential to ensure precision and expertise in providing a tailored, reliable system for healthcare environments.
Factor | Considerations | Estimated Cost Range |
Facility Size | Larger facilities may require extensive ductwork and larger HVAC systems | $50,000 – $200,000 |
Complexity of HVAC Systems | Specialized systems for critical areas may increase installation costs | $20,000 – $100,000 |
Customizations and Special Requirements | Unique requirements such as specialized filtration, isolation room setups, and compliance features | $10,000 – $50,000 |
Compliance and Regulations | Meeting strict air quality and infection control regulations may involve additional expenses | $15,000 – $70,000 |
Energy Efficiency Considerations | Investing in energy-efficient HVAC systems for long-term savings | $30,000 – $80,000 |
Labor and Material Costs | Local labor rates and material costs can vary significantly | $40,000 – $120,000 |
Emergency Preparedness Features | HVAC systems with redundancy and backup features | $20,000 – $60,000 |
Total Estimated Installation Costs Range | $185,000 – $680,000 or can be exceeded |
Note: These estimates are provided for informational purposes, and actual costs may differ based on project specifics and regional variations.
Estimating the cost of ductwork replacement in medical buildings involves a careful consideration of the material and type of ductwork chosen for the upgrade. The selection of materials such as galvanized steel, aluminum, or fiberglass, each with varying price points, is a crucial determinant. Additionally, the design of the ductwork, whether it follows a rectangular, round, or spiral configuration, contributes to the overall cost. The choice of material and type is influenced by factors such as durability, hygiene standards, and energy efficiency, all of which are particularly significant in medical settings.
The size and complexity of the existing ductwork system play a pivotal role in determining the costs associated with replacement. Larger systems or those with intricate designs, especially those serving specialized areas such as surgical suites or isolation rooms, may entail higher expenses. The need for precision in design and installation to meet the specific requirements of medical facilities contributes to the complexity factor in estimating replacement costs.
Ensuring compliance with evolving air quality standards and regulations is a paramount consideration in estimating ductwork replacement costs for medical buildings. If regulatory changes necessitate modifications to the existing ductwork system, the associated costs must be factored into the estimation. Maintaining compliance with health and safety regulations is not only essential for the well-being of occupants but also for avoiding potential legal and regulatory issues.
The ease of access to the current ductwork and any potential installation challenges are factors that impact replacement costs. If the replacement process requires modifications to existing structures or intricate installations, additional labor and material expenses may be incurred. Assessing the accessibility and addressing potential challenges beforehand ensures a more accurate estimate and smoother execution of the replacement project.
Medical buildings often have specific requirements for insulation and sealing within the ductwork system to prevent contamination and ensure energy efficiency. Upgrading or replacing insulation and sealing materials contributes significantly to the overall replacement costs. These enhancements not only align with healthcare standards but also contribute to the long-term efficiency and performance of the HVAC system.
Ductwork replacement may be part of a broader HVAC system upgrade within a medical building. The integration with the HVAC system, including any necessary modifications or adjustments, is a factor influencing costs. This integration ensures seamless functionality and compatibility between the new ductwork and the upgraded HVAC components.
Labor costs, influenced by local market rates and the availability of skilled technicians, are critical considerations in estimating ductwork replacement expenses. Engaging experienced professionals familiar with the specific requirements of healthcare facilities is essential for a successful replacement project. Skilled labor is necessary not only for the physical replacement but also for ensuring that the new ductwork system aligns with the stringent standards of medical environments.
If the replacement project includes the addition of emergency preparedness features to the ductwork system, such as redundancy or backup systems, these features contribute to higher costs. Emergency preparedness features are crucial in medical settings to ensure continuous and reliable operation, particularly during critical situations. The integration of such features reflects a commitment to maintaining a resilient and responsive HVAC system within the medical facility.
Factor | Considerations | Estimated Cost Range |
Ductwork Material and Type | Material choices (e.g., galvanized steel, aluminum, fiberglass) and type (rectangular, round, spiral) | $10,000 – $50,000 |
Size and Complexity of the System | Larger systems or those serving specialized areas may incur higher expenses | $20,000 – $100,000 |
Regulatory Compliance and Standards | Modifications to comply with air quality standards and regulatory changes | $15,000 – $40,000 |
Accessibility and Installation Challenges | Ease of access and any installation complexities impacting labor and material costs | $5,000 – $30,000 |
Insulation and Sealing Requirements | Upgrading or replacing insulation and sealing materials for contamination prevention | $8,000 – $20,000 |
HVAC System Integration | Integration with the larger HVAC system, including modifications or adjustments | $10,000 – $40,000 |
Labor Costs and Local Market Rates | Local labor rates and skilled technicians’ availability impacting labor costs | $15,000 – $50,000 |
Emergency Preparedness Features | Adding emergency preparedness features like redundancy or backup systems | $10,000 – $30,000 |
Total Estimated Ductwork Replacement Costs Range | $88,000 – $310,000 or can be higher or lower |
Note: These estimates are provided for informational purposes, and actual costs may vary based on specific project requirements, location, and market conditions.
Estimating costs for hospital building ductwork involves a thorough analysis of material choices, labor, system intricacies, project size, and market conditions. Accurate estimation is crucial for maintaining optimal indoor air quality in healthcare settings. The provided cost ranges serve as valuable guidelines, emphasizing the need for meticulous planning and consideration of regulatory compliance, technological advancements, and emergency preparedness features. These estimates empower decision-makers to ensure efficient and reliable HVAC systems, ultimately contributing to a healthy and safe environment for patients, staff, and visitors in medical facilities.
The cost of ductwork in hospital buildings is influenced by various factors, including the material chosen (e.g., galvanized steel, aluminum), labor costs, system design complexity, project size and scale, contingency planning, and market conditions.
Labor costs, including skilled workers such as sheet metal workers and HVAC technicians, play a significant role in ductwork installation expenses. The complexity of the installation, impacted by factors like hospital layout and ventilation requirements, can affect labor hours and overall costs.
Innovative ductwork technologies, such as pre-fabricated components or energy-efficient systems, introduce additional considerations for cost estimation. Evaluating the costs and benefits of these advancements allows decision-makers to make informed choices aligned with sustainability goals.
Regularly monitoring market conditions is crucial for accurate cost estimation. Fluctuations in material and labor costs based on current market trends can impact the overall estimate. Adjustments are made to estimates in response to market changes, ensuring that the budget remains aligned with real-time conditions.
Estimating costs for ductwork replacement involves considerations such as the material and type of ductwork, size and complexity of the existing system, regulatory compliance and standards, accessibility and installation challenges, insulation and sealing requirements, HVAC system integration, labor costs, and the addition of emergency preparedness features. These factors contribute to the overall replacement costs in medical buildings.
Here I am going to share some steps to get your hospital building ductwork cost estimate report.
You can send us your plan on info@estimatorflorida.com
Before starting your project, we send you a quote for your service. That quote will have detailed information about your project. Here you will get information about the size, difficulty, complexity and bid date when determining pricing.
Our team will takeoff and estimate your project. When we deliver you’ll receive a PDF and an Excel file of your estimate. We can also offer construction lead generation services for the jobs you’d like to pursue further.
561-530-2845
info@estimatorflorida.com
Address
5245 Wiles Rd Apt 3-102 St. Pete Beach, FL 33073 United States
561-530-2845
info@estimatorflorida.com
Address
5245 Wiles Rd Apt 3-102 St. Pete Beach, FL 33073 United States
All copyright © Reserved | Designed By V Marketing Media | Disclaimer