Boost Your Warehouse Construction Bids – Request a Precision Estimate!
- Accurancy
- Efficiency
- Transparency
- Customization
- Time Saving
- Professionalism
- Cost Control
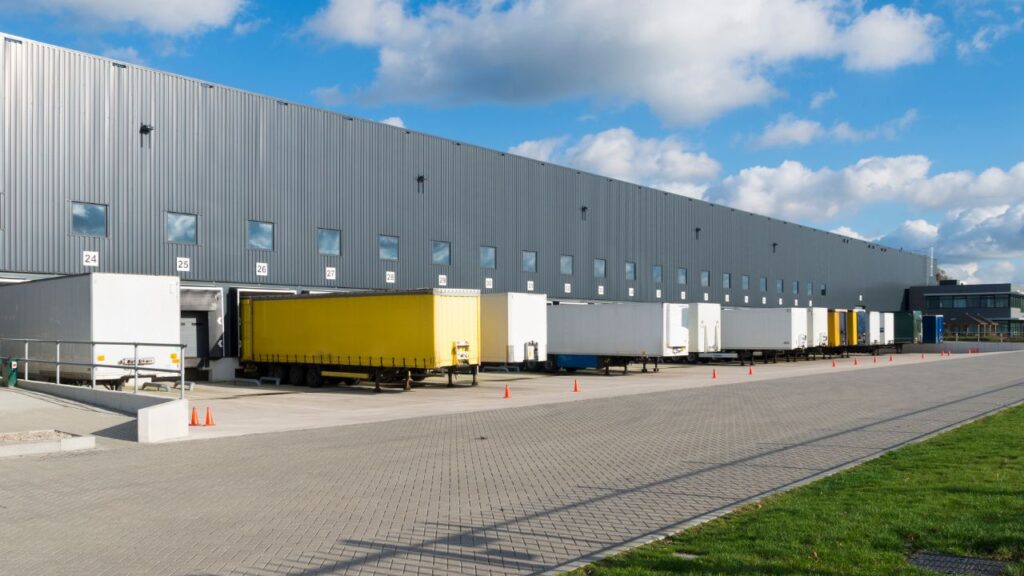
The cost of insulating a metal warehouse with spray foam can vary widely, ranging from $0.50 to $4.50 per square foot. This cost is influenced by factors such as the size of the building, prevailing climate conditions, and whether the insulation is intended for new or existing construction. Alternatively, closed-cell spray foam may cost between $1.5 and $3.5 per square foot, open-cell spray foam between $0.5 and $1.5 per square foot, and batt and roll insulation between $0.90 and $2.80 per square foot. Labor costs for installing insulation in a metal building range from $0.50 to $1.25 per square foot for new construction.
When making decisions about insulation, considerations should include the desired R-value and budget constraints. Various options, including spray foam, foam board, blown-in cellulose, and fiberglass batts, are popular choices for insulating metal buildings. At Estimate Florida Consulting, we provide detailed estimates for your projects, helping you make informed decisions about metal warehouse insulation.
Fully Insured Licensed
Hire Contractor For Warehouse Construction
Make Informed Design Decisions Showcase Your Design Ideas
Get RenderingUpon completion, factoring in all material and construction costs, you can expect to invest between $1,440 and $3,960 or more for insulating a steel building. Opting for a blown-in wall insulation system comes at an approximate cost of $480, while foam-spraying an entire wall may amount to around $1,200. It’s essential to consider material costs, ranging from $0.60 per square foot for blown-in insulation to $3.60 per square foot for vapor-tight insulation. The application of spray foam involves additional expenses. Labor costs, potentially up to $360 per hour depending on your contractor’s expertise, should also be accounted for. In making decisions regarding drywall, blown-in insulation, and spray foam, prioritize the most cost-effective option based on your project’s specific requirements. For instance, spray foam applications may total around $1,200, while blown-in insulation can be a more economical choice, starting at $480 for a 500-square-foot area.
While there are various insulation types available, fiberglass stands out as the most widely used and popular choice. Its lightweight and cost-effective nature makes fiberglass insulation a budget-friendly option. Whether rolled, blasted, or loose-filled, fiberglass insulation creates a protective barrier. The average cost per square foot ranges from $0.36 to $1.80 or more. If you opt for a DIY approach, you might incur expenses ranging from $180 to $840 or more for a 500-square-foot project. For a professional six-hour job, including labor costs of $240 to $600, the total could range from $420 to $1,200 or can be exceeded. While fiberglass is a money-saving insulation choice, caution is advised. It may not be suitable for drafty spaces as it doesn’t effectively trap air. Additionally, if you have pets or children, note that fiberglass insulation can be harmful if ingested.
The cost of spray foaming a 30×40 metal warehouse may vary depending on the chosen company and the desired insulation thickness. Generally, you can expect the cost to be around $1,800 or more for the job.
Various insulation types are available in the market, and the insulation cost can significantly fluctuate based on the type, quality, and quantity needed. Fiberglass insulation is commonly the most economical choice, while other options like spray foam insulation tend to be pricier. Insulation costs are typically calculated per square foot, ranging from $0.60 to $2.40 or more on average.
Achieving optimal energy efficiency in a metal warehouse involves meticulous consideration of insulation materials and their thermal resistance properties. The selection of materials with high R-values is essential to create an effective barrier against heat transfer, ensuring that the interior temperature remains stable. Conducting a comprehensive energy audit is a crucial step to identify specific areas within the warehouse where heat gain or loss occurs, allowing for targeted insulation strategies. Moreover, integrating reflective insulation into the overall insulation plan can further minimize radiant heat transfer, contributing significantly to the overall energy efficiency of the warehouse.
The selection of insulation materials for a metal warehouse is a pivotal decision that involves striking a delicate balance between cost-effectiveness and long-term performance. Different insulation types, such as fiberglass, foam board, reflective foil, or sprayed foam insulation, offer varying benefits and costs. Considering the local climate and the unique requirements of the warehouse environment is crucial in making informed choices. The insulation material selected should not only meet the immediate needs of the warehouse but also provide durable and sustainable performance over the long term, ensuring that the initial investment translates into lasting cost savings.
Evaluating installation costs is a critical aspect of the overall insulation strategy. While choosing effective insulation materials is paramount, it is equally important to consider the ease of installation and associated labor costs. Opting for materials that are not only efficient but also easy to install can lead to significant immediate and long-term cost reductions. Streamlining the installation process not only ensures that the insulation system is put in place effectively but also minimizes the financial burden associated with labor-intensive installation methods.
Beyond the initial investment, considering the life cycle costs of insulation materials provides a comprehensive perspective on the economic viability of the chosen solution. Some insulation materials may have higher upfront costs but offer substantial long-term energy savings, resulting in lower overall costs over the life of the insulation. This holistic approach to cost analysis allows for a more informed decision-making process, aligning the insulation strategy with both economic and sustainability goals.
The efficiency of the heating, ventilation, and air conditioning (HVAC) system is intricately linked to the insulation of a metal warehouse. Well-insulated warehouses often necessitate smaller HVAC systems, reducing both the initial capital investment and ongoing operational costs. Proper sizing and efficient operation of the HVAC system contribute to a synergistic relationship with the insulation, ensuring that the entire climate control system operates optimally to maintain a comfortable and energy-efficient interior environment.
Addressing air leakage is a fundamental component of an effective warehouse insulation strategy. Sealing gaps, seams, and joints in the building envelope not only enhances the insulation’s overall effectiveness but also plays a pivotal role in maintaining a consistent indoor temperature. By reducing air leakage, the workload on HVAC systems is minimized, leading to energy savings and contributing significantly to long-term cost reductions. This meticulous attention to a well-sealed structure enhances the overall efficiency of the insulation system.
Exploring available government incentives and rebates for energy-efficient upgrades is a strategic approach to mitigating the upfront costs associated with warehouse insulation. Many regions offer financial support to businesses adopting sustainable and energy-saving practices. Thorough research and leveraging these opportunities can substantially offset the initial investment, making the insulation project more economically viable. Considering and capitalizing on available incentives is a prudent step in aligning the insulation strategy with broader economic and environmental goals.
Energy efficiency stands at the forefront of the importance of metal warehouse insulation. Metal structures, with their high thermal conductivity, are particularly susceptible to rapid heat transfer, making effective insulation a critical factor in mitigating this issue. By creating a thermal barrier, insulation helps regulate the internal temperature of the warehouse, preventing excessive heat gain in warmer seasons and heat loss during colder periods. This, in turn, significantly reduces the workload on the heating, ventilation, and air conditioning (HVAC) systems, translating into improved energy efficiency and notable reductions in utility costs over the long term.
The significance of metal warehouse insulation is underscored by its role in temperature regulation within the facility. Metal structures are prone to temperature extremes that can have adverse effects on stored goods, equipment, and the comfort of workers. Insulation plays a pivotal role in maintaining stable internal temperatures, preventing temperature fluctuations and the formation of condensation. This is particularly crucial in industries where temperature-sensitive products are stored, ensuring the quality, integrity, and longevity of the stored materials.
The financial implications of metal warehouse insulation are substantial, contributing significantly to overall cost savings. The reduction in energy consumption achieved through effective insulation directly translates into lower operational expenses. Additionally, well-insulated warehouses often require smaller HVAC systems, leading to reduced upfront capital investments and ongoing maintenance costs. The long-term economic benefits make insulation a strategic investment that not only pays for itself but continues to deliver cost savings over the operational life of the facility.
Beyond financial considerations, the importance of insulation in a metal warehouse extends to the well-being and productivity of the workforce. Adequate insulation creates a more comfortable working environment by mitigating the impact of extreme temperatures. This, in turn, enhances employee morale, job satisfaction, and overall productivity. A workforce operating in a climate-controlled and comfortable environment is likely to exhibit higher efficiency and engagement, contributing positively to the overall operational success of the warehouse.
An often-overlooked aspect of insulation’s importance lies in its role in protecting stored goods and materials. Warehouses frequently house products that are sensitive to temperature fluctuations, humidity, and condensation. Proper insulation serves as a protective shield, preventing damage to these goods and ensuring their quality and market viability. Industries such as pharmaceuticals, food storage, and electronics, where precise environmental conditions are crucial, benefit significantly from insulation as a safeguard against potential losses.
Insulation plays a pivotal role in preventing condensation within metal warehouses. Metal structures are inherently prone to condensation, which can lead to corrosion and degradation of building materials. By acting as a barrier that prevents warm, moist air from coming into contact with cold surfaces, insulation minimizes the risk of condensation. This not only safeguards the structural integrity of the warehouse but also reduces the need for extensive maintenance and repair, resulting in additional cost savings.
The importance of metal warehouse insulation is underscored by the necessity to comply with building codes and regulations. Many regions have specific mandates regarding the inclusion of insulation in commercial and industrial structures. Compliance not only ensures legal adherence but also guarantees that the warehouse operates in alignment with industry standards, safety guidelines, and environmental regulations. Meeting these requirements is fundamental to the seamless and lawful operation of the facility.
Beyond immediate operational considerations, the importance of metal warehouse insulation extends to the broader realm of environmental impact and sustainability. Insulating a metal warehouse aligns with sustainable practices by reducing overall energy consumption and greenhouse gas emissions. As a result, the facility becomes a more environmentally responsible entity, contributing to corporate social responsibility efforts and aligning with global initiatives to mitigate the environmental impact of industrial operations. The positive environmental footprint is an additional facet that enhances the overall importance and relevance of insulation in metal warehouses.
Insulation is vital for metal warehouses due to their susceptibility to rapid heat transfer. It helps regulate internal temperatures, preventing excessive heat gain or loss, contributing to improved energy efficiency, and reducing utility costs.
The cost of insulating a metal warehouse can range from $0.60 to $1.50 or more per square foot during construction. For a 40’x60′ metal warehouse, the expenses may vary from $1,440 to $3,600 or potentially higher, depending on specific project requirements and regional variations.
Various factors, such as insulation material, quality, quantity, and labor costs, influence the overall cost. Fiberglass insulation is often the most cost-effective option, with costs ranging from $0.60 to $2.40 or more per square foot on average.
Proper insulation contributes to a more comfortable working environment by mitigating extreme temperatures. This enhances employee morale, job satisfaction, and overall productivity, creating a positive impact on the workforce.
Insulation in metal warehouses aligns with sustainable practices by reducing energy consumption and greenhouse gas emissions. It contributes to environmental responsibility, supporting corporate social responsibility efforts and global initiatives to mitigate the environmental impact of industrial operations.
Here I am going to share some steps to get your metal warehouse insulation cost estimate report.
You can send us your plan on info@estimatorflorida.com
Before starting your project, we send you a quote for your service. That quote will have detailed information about your project. Here you will get information about the size, difficulty, complexity and bid date when determining pricing.
Our team will takeoff and estimate your project. When we deliver you’ll receive a PDF and an Excel file of your estimate. We can also offer construction lead generation services for the jobs you’d like to pursue further.
561-530-2845
info@estimatorflorida.com
Address
5245 Wiles Rd Apt 3-102 St. Pete Beach, FL 33073 United States
561-530-2845
info@estimatorflorida.com
Address
5245 Wiles Rd Apt 3-102 St. Pete Beach, FL 33073 United States
All copyright © Reserved | Designed By V Marketing Media | Disclaimer