Boost Your Warehouse Construction Bids – Request a Precision Estimate!
- Accurancy
- Efficiency
- Transparency
- Customization
- Time Saving
- Professionalism
- Cost Control
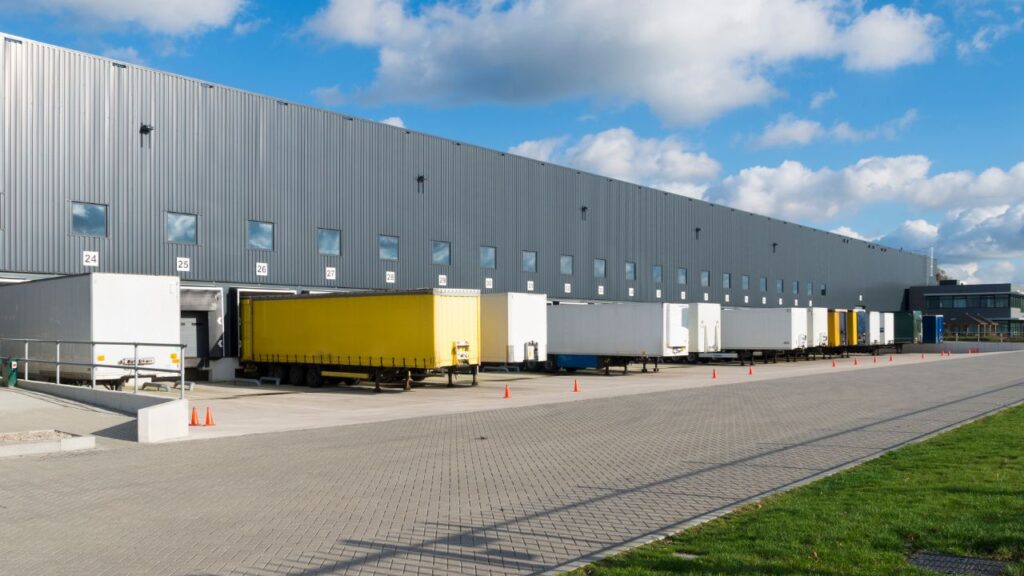
Designing a metal warehouse in Florida involves careful consideration of both functionality and cost. The price of metal buildings in the state varies significantly, with smaller structures like a 20×30 metal shed costing around $6,500, providing an affordable option for basic storage needs. On the other end of the spectrum, large-scale construction projects, such as 40×60 buildings, can exceed $40,000 due to their expansive size and additional requirements. Balancing design elements to meet specific storage or workspace needs while staying within budget is crucial in the metal warehouse construction process in Florida.
At Estimate Florida Consulting, we understand the importance of financial planning in such projects.
Fully Insured Licensed
Hire Contractor For Warehouse Construction
Make Informed Design Decisions Showcase Your Design Ideas
Get RenderingAdditionally, the layout and design of the metal warehouse can impact its functionality and operational efficiency. Factors such as ceiling height, door placements, and the inclusion of mezzanine floors all contribute to the overall cost considerations. A well-designed warehouse maximizes storage capacity and facilitates smooth workflow, potentially offsetting initial construction expenses in the long run. Moreover, the choice of materials, insulation, and energy-efficient features can influence ongoing operational costs. Therefore, a comprehensive evaluation of size, design, and additional features is essential when planning a metal warehouse to ensure cost-effectiveness and operational effectiveness over time.
Furthermore, the selection of materials for a construction project involves a careful consideration of factors beyond just durability and cost-effectiveness. Environmental impact, sustainability, and adherence to local building codes are crucial aspects that shouldn’t be overlooked. For instance, opting for eco-friendly materials not only aligns with global sustainability goals but may also lead to potential cost savings through tax incentives or reduced energy consumption. Additionally, understanding the lifecycle of chosen materials aids in predicting maintenance needs, further influencing the overall cost-effectiveness and success of the project in the long term.
Considering Florida’s diverse landscape is crucial for effective site preparation in construction projects. Factors such as soil composition, drainage patterns, and the risk of extreme weather events must be taken into account. Coastal areas, for instance, may necessitate additional measures to protect against hurricanes and flooding. Moreover, compliance with local regulations and environmental considerations, especially in ecologically sensitive regions, is paramount.
A comprehensive site analysis, including geotechnical assessments and climate considerations, aids in creating a construction plan that mitigates risks, enhances durability, and ultimately contributes to the project’s success within Florida’s unique environment.
Moreover, beyond the initial construction expenses, it’s imperative to consider ongoing costs associated with operating a metal building in Florida’s climate. High temperatures, humidity, and the potential for tropical storms demand robust insulation and structural resilience, which may incur additional costs but prove essential for long-term functionality. Additionally, maintenance costs, insurance premiums, and energy efficiency measures should be factored into the budgetary planning. A comprehensive financial strategy that accounts for both upfront and recurrent expenses ensures a realistic and sustainable approach to successfully implementing and maintaining a metal warehouse project in the dynamic environment of Florida.
Moreover, the strategic allocation of space in metal warehouse design extends beyond mere layout considerations. Thoughtful planning takes into account the specific needs of the stored items, facilitating easy access and retrieval. Utilizing vertical storage solutions, such as mezzanine floors or high-reaching shelving, further enhances storage capacity without compromising accessibility. Additionally, incorporating flexible storage systems accommodates evolving inventory requirements, promoting adaptability in warehouse operations. A comprehensive approach to efficient space utilization not only streamlines day-to-day activities but also positions the warehouse for scalability and responsiveness to future business demands.
Furthermore, energy-efficient design in a metal warehouse involves a meticulous evaluation of various components. Optimal insulation not only regulates internal temperatures but also minimizes the reliance on heating and cooling systems, reducing energy consumption. Implementing LED lighting, equipped with motion sensors and automated controls, not only enhances visibility but also curtails electricity usage. Additionally, exploring renewable energy sources, such as solar panels, aligns the warehouse with eco-friendly initiatives while potentially offering long-term cost savings. A holistic approach to energy efficiency not only lowers operational expenses but also underscores the commitment to environmentally sustainable practices.
Customizing the exterior enhances the warehouse’s aesthetic appeal while serving functional purposes. Exploring finish options provides an opportunity to align the building with the brand image.
Tailoring the interior layout to specific operational needs enhances functionality. From shelving systems to office spaces, customization options play a pivotal role in the overall design.
Comparing the costs of metal construction with traditional methods provides valuable insights. Understanding the long-term benefits and potential savings helps in making informed decisions.
Material Type | Cost per Square Foot |
Steel | $8.00 |
Aluminum | $10.00 |
Insulation | $2.50 |
Roofing | $5.00 |
Concrete | $6.00 |
Glass | $12.00 |
Doors | $4.50 |
Lighting | $3.00 |
HVAC Systems | $7.50 |
Electrical | $4.00 |
Flooring | $5.50 |
Plumbing | $6.50 |
Examining the durability and longevity of metal warehouses extends beyond initial construction considerations. While these structures are recognized for robustness, a comprehensive assessment includes an analysis of ongoing maintenance costs. The choice of high-quality, corrosion-resistant materials can significantly impact long-term maintenance expenses, contributing to the overall value proposition. Regular inspections, preventive maintenance, and corrosion control measures further enhance the structure’s resilience. Understanding the life cycle of a metal warehouse, from construction through maintenance, ensures that the investment continues to deliver value over time, making it a prudent choice for sustained operational success.
Beyond structural advantages, the eco-friendly characteristics of metal construction make it an environmentally conscious choice. Metal is highly recyclable, reducing the demand for new raw materials and minimizing waste. Additionally, the reflective properties of metal roofing contribute to energy efficiency by reducing heat absorption and lowering cooling needs. Choosing metal aligns with green building standards, potentially qualifying for certifications like LEED.
Embracing these environmental benefits not only supports sustainability goals but enhances the overall value proposition, appealing to environmentally conscious stakeholders and contributing to a responsible and forward-thinking construction approach.
Implementing cost-saving strategies, such as bulk purchasing and efficient project management, contributes to budget optimization. Additionally, exploring alternative financing options and government incentives can further alleviate project costs, making metal warehouse construction more financially viable.
Incorporating a contingency plan guards against unforeseen challenges, providing financial reassurance throughout the project. Unexpected delays, material shortages, or regulatory changes can impact costs, and having a contingency plan ensures that the project stays on track without compromising quality.
Hearing about the experiences of others who have undertaken metal warehouse projects offers valuable insights into the process and outcomes. These testimonials provide real-world perspectives on the challenges faced, the benefits reaped, and the overall satisfaction of businesses that have invested in metal warehouse construction.
Metal warehouse design and cost considerations in Florida require a thoughtful and strategic approach. Balancing factors such as size, materials, and customization options can lead to a cost-effective and efficient solution for businesses. Embracing innovations, anticipating future trends, and partnering with the right professionals contribute to the success of metal warehouse projects in the dynamic landscape of Florida’s industrial architecture.
The costs vary based on factors such as size and design. Smaller structures like a 20×30 metal shed can cost around $6,500, while larger projects like 40×60 buildings may exceed $40,000.
The size and layout of the warehouse, including factors like ceiling height and door placements, can influence costs. A well-designed warehouse can maximize storage capacity and operational efficiency, potentially offsetting initial construction expenses.
Material selection involves considering factors beyond durability, including environmental impact and sustainability. Opting for eco-friendly materials may lead to cost savings through tax incentives or reduced energy consumption.
Considering Florida’s diverse landscape is essential for effective site preparation. Factors such as soil composition, drainage patterns, and the risk of extreme weather events must be taken into account to enhance durability and mitigate risks.
Beyond construction, ongoing costs include maintenance, insurance, and energy efficiency measures. Florida’s climate demands robust insulation and structural resilience, which may incur additional costs but are essential for long-term functionality.
Here I am going to share some steps to get your metsl warehouse design and cost estimate report.
You can send us your plan on info@estimatorflorida.com
Before starting your project, we send you a quote for your service. That quote will have detailed information about your project. Here you will get information about the size, difficulty, complexity and bid date when determining pricing.
Our team will takeoff and estimate your project. When we deliver you’ll receive a PDF and an Excel file of your estimate. We can also offer construction lead generation services for the jobs you’d like to pursue further.
561-530-2845
info@estimatorflorida.com
Address
5245 Wiles Rd Apt 3-102 St. Pete Beach, FL 33073 United States
561-530-2845
info@estimatorflorida.com
Address
5245 Wiles Rd Apt 3-102 St. Pete Beach, FL 33073 United States
All copyright © Reserved | Designed By V Marketing Media | Disclaimer