Bid Strong, Bid Smart – Try Our Hospital Construction Cost Estimating Service!
- Accurancy
- Efficiency
- Transparency
- Customization
- Time Saving
- Professionalism
- Cost Control
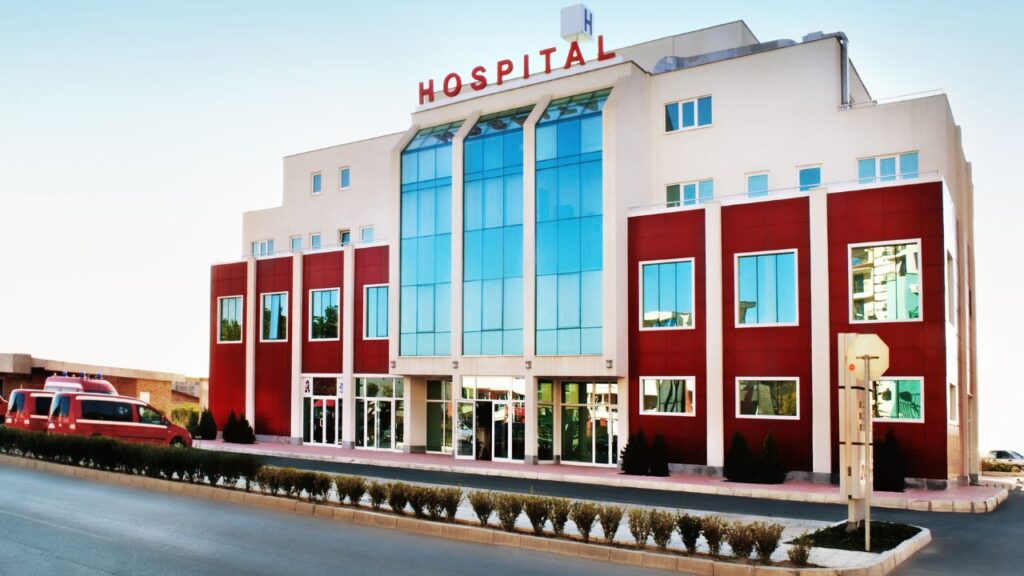
The construction of a hospital involves numerous intricate steps, and among them, the process of concrete pouring stands out as a critical element. The pouring of concrete serves as the backbone for the hospital’s structure, providing the necessary strength, durability, and stability. In this article, we will delve into the various factors influencing the cost of concrete pouring in hospital construction, highlighting essential considerations and strategies for optimizing costs while maintaining structural integrity.
Concrete pouring is a foundational stage in hospital construction, forming the basis for walls, floors, and other structural components. The quality of concrete pouring directly impacts the safety, longevity, and functionality of the hospital building. Given the stringent standards and specialized requirements of healthcare facilities, precise and well-executed concrete pouring is paramount for ensuring a secure environment for patients, staff, and medical equipment.
Fully Insured License
Hire Contractor For Hospital Construction
Make Informed Design Decisions Showcase Your Design Ideas
Get RenderingThe formulation of the concrete mix plays a pivotal role in determining construction costs, especially in the context of specialized healthcare infrastructure. Healthcare facilities often demand specific concrete formulations tailored to meet stringent structural requirements. Achieving a balance between factors like strength, durability, and workability is paramount in selecting an optimal concrete mix. The cost implications arise from the need for specialized additives or unique blends that align with the unique demands of hospital structures. Careful consideration of these factors during the mix design phase is essential for ensuring both structural integrity and cost-effectiveness in healthcare construction projects.
The intricacy of architectural designs and structural elements significantly influences the costs associated with formwork and reinforcement. Complex layouts, characteristic of modern healthcare facilities, may necessitate custom formwork solutions to mold concrete into specific shapes. Simultaneously, the use of reinforcement materials, such as steel, adds to the overall expenses. However, efficient design planning becomes the linchpin for cost-effective formwork and reinforcement. Collaborative efforts between architects and construction teams are indispensable in creating designs that balance aesthetic aspirations with the pragmatic need for cost efficiency, ensuring optimal use of materials without compromising structural integrity.
The location and accessibility of the construction site emerge as pivotal factors influencing concrete pouring costs. Challenges such as limited access, difficult terrain, or the need for specialized equipment can significantly increase labor costs and logistical complexities. Proactive planning becomes imperative to address site-specific conditions and optimize costs. Site assessments, strategic placement of equipment, and logistical planning contribute to mitigating challenges, ultimately ensuring that the concrete pouring process is executed with efficiency and cost-effectiveness.
The method of concrete delivery and pouring techniques introduces substantial cost considerations. Factors such as the distance of the construction site from the concrete plant, the utilization of ready-mix concrete, and the employment of concrete pumps all contribute to overall expenses. Making strategic decisions regarding efficient and cost-effective delivery methods is key to managing concrete pouring costs. The logistics of concrete transportation, whether through traditional mixers or advanced pumping systems, directly impact the project’s financial dynamics. Careful planning in this domain ensures a streamlined process that minimizes unnecessary costs while optimizing the efficiency of concrete pouring.
Weather conditions represent a dynamic and often unpredictable factor that significantly affects concrete pouring costs. Adverse weather, such as extreme temperatures or precipitation, can necessitate additional measures to ensure proper curing of the concrete. This might involve the implementation of temperature control mechanisms or protective enclosures, contributing to increased costs. Strategic scheduling of concrete pouring during favorable weather windows becomes crucial for minimizing potential delays and the associated costs. Weather-sensitive planning allows for the efficient utilization of labor and resources, preventing unnecessary expenditures caused by weather-induced complications.
Concrete pouring costs for hospital buildings vary based on project-specific factors. On average, the cost can range from $75 to $150 or more per cubic yard of concrete. This estimate includes expenses related to material procurement, labor, formwork, reinforcement, equipment, and site-specific considerations.
Thorough project planning, coupled with a meticulously detailed schedule for concrete pouring activities, stands as the cornerstone of cost-effective construction. Advanced planning involves aligning concrete pouring activities with favorable weather conditions and coordinating seamlessly with other phases of construction. This strategic alignment minimizes delays, enhances overall efficiency, and prevents additional costs associated with weather-induced disruptions. The proactive orchestration of pouring activities within a well-structured schedule ensures that resources are optimally utilized, contributing to both time and cost savings throughout the construction process.
Collaboration between architects and construction teams is pivotal in designing efficient formwork and reinforcement systems, contributing to substantial cost savings. Optimal designs not only fulfill structural requirements but also ensure the judicious use of materials during concrete pouring. Customized formwork solutions, tailored to the intricacies of the project, minimize material waste and streamline the pouring process. This collaborative approach to design strikes a delicate balance between aesthetic aspirations and cost-effective construction, fostering an environment where efficiency and structural integrity coexist harmoniously.
The integration of construction technologies, such as Building Information Modeling (BIM), plays a transformative role in precise planning and coordination during concrete pouring activities. BIM facilitates a comprehensive digital representation of the project, allowing for detailed visualization and analysis. This enhances overall efficiency by streamlining communication and minimizing errors in the planning phase. Additionally, the use of advanced concrete mix additives, guided by technological insights, can improve workability and reduce curing time. This dual integration of technology not only contributes to the efficiency of concrete pouring but also enhances cost-effectiveness through optimized resource utilization.
Choosing sustainable materials and adopting efficient concrete mix designs is a dual strategy that aligns with both environmental goals and cost-effectiveness. Sustainable materials, often derived from recycled sources, not only contribute to environmental stewardship but also aid in controlling costs. Furthermore, efficient concrete mix designs, guided by technological advancements, ensure that the right balance of ingredients is used, minimizing waste. The incorporation of recycling practices on-site further enhances material efficiency, creating a symbiotic relationship between sustainable practices and cost control in the realm of concrete pouring.
Implementing robust quality control measures during concrete pouring is a proactive strategy to safeguard against additional costs arising from structural deficiencies. Stringent adherence to specified standards, coupled with thorough inspection and testing, minimizes the likelihood of rework or corrective measures. Investing in quality control measures during the pouring process is an upfront commitment that pays dividends by preventing costly rectifications in the later stages of construction. This commitment to quality not only ensures structural integrity but also aligns with the overarching goal of cost-effective and efficient construction practices.
In the realm of hospital construction, concrete pouring is foundational, shaping structures with precision. This article highlighted key cost influencers, from concrete mix design to site logistics and technology integration. To balance structural integrity and budget constraints, strategic planning, collaboration, and advanced technologies prove vital.
Efficient formwork design, material sustainability, and quality control measures contribute to cost-effectiveness without compromising excellence. This dual commitment ensures hospitals meet stringent standards economically. The intersection of quality and efficiency sets the stage for healthcare facilities that embody both structural resilience and financial prudence.
The cost of concrete pouring is influenced by various factors, including concrete mix design, formwork and reinforcement intricacies, site accessibility, concrete delivery and pumping methods, and the impact of weather conditions.
Healthcare facilities often require specific concrete formulations to meet stringent structural standards. The balance between strength, durability, and workability influences the cost, as specialized additives or blends may be needed.
The intricacy of hospital designs may require custom formwork solutions. Efficient design planning, balancing architectural aspirations with cost efficiency, minimizes material waste and contributes to overall cost-effectiveness.
Site-specific conditions, limited access, difficult terrain, or the need for specialized equipment can increase labor costs. Proactive planning, site assessments, and strategic logistics are crucial to optimizing costs.
Strategies include advanced planning and scheduling to align with favorable weather, efficient formwork and reinforcement design through collaboration, technology integration with tools like BIM, a dual approach to material efficiency and sustainability, and robust quality control measures to prevent additional costs from structural deficiencies.
Here I am going to share some steps to get your hospital building concrete pouring cost estimate report.
You can send us your plan on info@estimatorflorida.com
Before starting your project, we send you a quote for your service. That quote will have detailed information about your project. Here you will get information about the size, difficulty, complexity and bid date when determining pricing.
Our team will takeoff and estimate your project. When we deliver you’ll receive a PDF and an Excel file of your estimate. We can also offer construction lead generation services for the jobs you’d like to pursue further.
561-530-2845
info@estimatorflorida.com
Address
5245 Wiles Rd Apt 3-102 St. Pete Beach, FL 33073 United States
561-530-2845
info@estimatorflorida.com
Address
5245 Wiles Rd Apt 3-102 St. Pete Beach, FL 33073 United States
All copyright © Reserved | Designed By V Marketing Media | Disclaimer