Bid Strong, Bid Smart – Try Our Hospital Construction Cost Estimating Service!
- Accurancy
- Efficiency
- Transparency
- Customization
- Time Saving
- Professionalism
- Cost Control
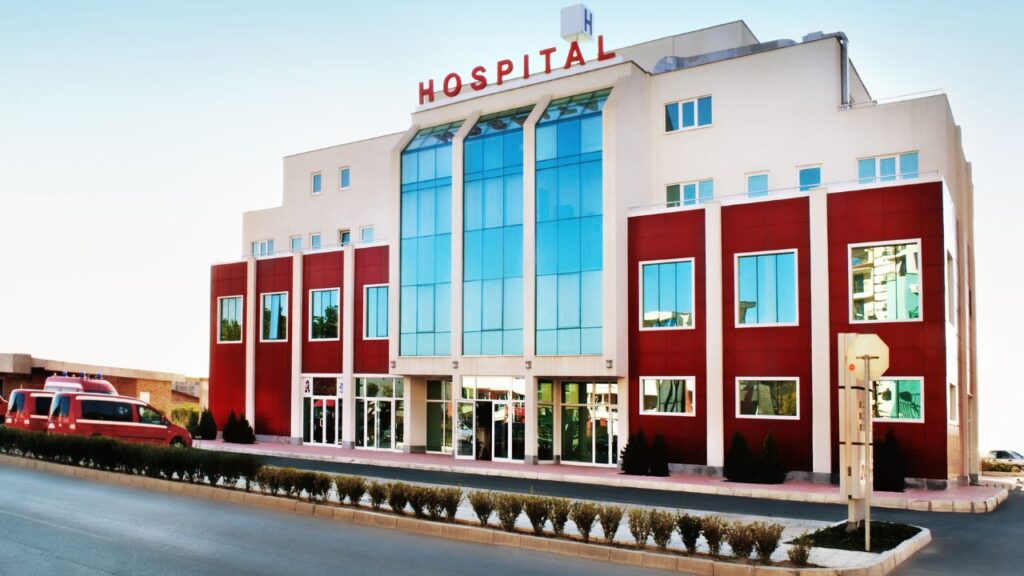
Constructing a hospital requires a meticulous approach to various aspects of the building, with the foundation playing a critical role in ensuring stability, safety, and longevity. Among the foundation options, concrete slabs are a common choice due to their versatility and cost-effectiveness. In this article, we will delve into the factors and considerations that influence the cost of concrete slabs in hospital construction, providing insights for project managers, architects, and stakeholders.
Concrete slabs serve as a foundational element in hospital buildings, providing a flat, stable surface upon which the entire structure rests. Hospitals, with their diverse and specialized spaces, demand a foundation that can accommodate heavy loads, support intricate infrastructure, and meet stringent safety standards. Concrete slabs, known for their strength and durability, are well-suited to fulfill these requirements, making them a popular choice in hospital construction.
Fully Insured License
Hire Contractor For Hospital Construction
Make Informed Design Decisions Showcase Your Design Ideas
Get RenderingThe thickness of the concrete slab is a critical factor influencing the overall costs of hospital construction projects. In healthcare facilities, where heavy medical equipment is prevalent, the slab must be designed to withstand substantial loads. Thicker slabs are often necessary to provide the necessary structural support, which, in turn, impacts both material and labor costs. Additionally, the level of reinforcement, such as the use of rebar or mesh, adds another layer of complexity. The intricacy involved in reinforcing the slab to meet the specific demands of a hospital setting contributes not only to the material expenses but also increases labor costs. Achieving the delicate balance between structural integrity and cost efficiency requires a meticulous approach in the design and construction phases.
The site where a hospital is constructed plays a pivotal role in determining the expenses associated with the concrete slab foundation. Site-specific factors, such as soil conditions and terrain, exert a significant influence on overall costs. Extensive site preparation, involving tasks like excavation and grading, may be indispensable to ensure the stability and suitability of the foundation. The nature of the site, whether it requires substantial earthmoving or intricate adjustments, directly impacts construction costs. Unforeseen challenges related to site conditions can lead to unexpected expenses, emphasizing the importance of a thorough site analysis during the initial phases of hospital construction projects.
Hospital designs present unique challenges and requirements, particularly in critical areas like operating rooms and laboratories. The structural design of concrete slabs must adhere to stringent specifications to accommodate specialized equipment and ensure optimal functionality. Meeting these specific structural requirements often involves additional engineering considerations, such as precision in load distribution and environmental control. The customization necessary for hospital settings introduces complexities that contribute to increased costs. Striking the right balance between meeting design specifications and managing costs requires collaboration between architects, engineers, and construction teams throughout the planning and execution phases.
The location and accessibility of the construction site are pivotal factors influencing the logistics and transportation costs associated with concrete delivery. In hospital construction, where precision and timely execution are paramount, the concrete must reach the site efficiently. Remote construction sites or those with logistical challenges may experience higher expenses related to the transportation of concrete. Factors such as the distance from concrete plants, traffic conditions, and the need for specialized equipment for challenging terrains can contribute to increased costs. Efficiently managing accessibility and logistics is crucial in minimizing additional expenses related to concrete delivery.
Hospitals demand the highest quality concrete to ensure the longevity and resilience of their structures. The choice of concrete mix, encompassing the quality of cement, aggregates, and additives, directly influences material costs. Opting for premium-quality materials may incur higher initial expenses, but it is a strategic investment in the durability of the hospital structure. High-quality concrete contributes to the long-term resilience of the facility, minimizing the need for future repairs and replacements. The emphasis on quality in the concrete mix aligns with the healthcare sector’s commitment to providing a safe and sustainable environment.
Compliance with building codes and safety regulations is non-negotiable in hospital construction. Meeting these stringent standards often involves additional measures, inspections, and documentation. Ensuring that the concrete slab adheres to safety and regulatory requirements is a fundamental aspect of responsible construction practices. While the commitment to compliance enhances the overall safety of the healthcare facility, it also contributes to increased construction costs. The integration of safety protocols and regulatory adherence is a foundational element in the ethical construction of hospital buildings, prioritizing the well-being of occupants and aligning with legal requirements.
In the quest for cost-effective and structurally sound concrete slabs in hospital construction, a pivotal strategy involves close collaboration with structural engineers. By fostering a symbiotic relationship, architects and engineers can optimize the design using advanced modeling tools. This approach ensures not only the structural integrity required for hospital load-bearing demands but also maximizes efficiency in material usage and construction processes. The emphasis is on creating a design that not only meets the unique specifications of healthcare facilities but also streamlines construction, contributing to potential cost savings without compromising quality.
A comprehensive site analysis is a cornerstone in the pursuit of cost-effective concrete slabs. Delving into soil conditions and potential challenges during the planning phase allows for proactive solutions, minimizing unexpected costs during construction. Understanding the intricacies of the site, such as soil stability and composition, enables the development of targeted strategies to address specific issues. Thorough site analysis not only contributes to cost efficiency but also lays the groundwork for a smoother construction process, emphasizing the importance of foresight and informed decision-making.
Implementing a value engineering approach is integral to scrutinizing every aspect of the hospital construction project, with a specific focus on concrete slabs. This collaborative and dynamic process involves architects, engineers, and contractors working together to identify cost-saving opportunities. Through meticulous examination, stakeholders can optimize material choices, construction techniques, and design elements without compromising the structural integrity of the concrete slabs. The goal is to strike a balance between efficiency, safety, and cost-effectiveness, making value engineering a strategic pillar in achieving optimal project outcomes.
A sustainable and cost-effective approach to material procurement involves sourcing construction materials locally. This strategy is particularly relevant for concrete slabs, where aggregates and other components can be obtained from nearby suppliers. Beyond minimizing transportation costs, sourcing materials locally aligns with sustainability goals by reducing the carbon footprint associated with transportation. Establishing partnerships with nearby suppliers not only contributes to economic efficiency but also underscores the importance of environmental responsibility in the construction process, presenting a holistic strategy for achieving sustainable cost savings.
Adopting efficient construction practices is fundamental to realizing cost savings in hospital construction, especially concerning concrete slabs. This involves the integration of modern equipment, adherence to lean construction principles, and effective project scheduling. Optimizing both labor and equipment usage contributes significantly to overall project cost savings. By minimizing downtime and streamlining construction processes, efficient practices not only reduce direct costs but also ensure timely project completion. The dynamic and adaptive nature of these practices underscores the importance of ongoing evaluation and adjustment to align with project goals.
The integration of construction technologies, such as Building Information Modeling (BIM) and construction management software, plays a transformative role in enhancing project efficiency, particularly in the context of concrete slabs. These tools facilitate improved communication, reduce errors, and enable real-time collaboration among project stakeholders. The seamless flow of information afforded by technology integration allows for agile decision-making, contributing to better overall project management. Embracing these technological advancements is integral to achieving long-term cost savings and ensuring success in a rapidly evolving construction landscape.
Considering the long-term costs associated with concrete slabs involves conducting a comprehensive lifecycle cost analysis. This strategic perspective evaluates not only the initial construction expenses but also ongoing maintenance costs and potential modifications. The holistic view provided by lifecycle cost analysis guides decisions that offer sustained cost savings over the lifespan of the hospital. Emphasizing the importance of investing in a cost-effective and enduring structural foundation, this approach encourages informed decision-making, ensuring that long-term considerations are seamlessly integrated into the construction process.
The typical expense for a concrete slab is approximately $8 or more per square foot, covering both material and labor costs. Most individuals pay between $6 per square foot at the lower end and $14 or more per square foot at the higher end.
Costs tend to escalate based on specific preferences such as desired finish, thickness, inclusion of wire-mesh, and necessary site preparation work. The size of the project is a significant influencing factor, as contractors commonly apply a minimum delivery fee for smaller slabs.
Constructing hospitals demands meticulous planning, with concrete slabs playing a crucial role. Key factors influencing costs include slab thickness, site conditions, unique design requirements, logistics, concrete quality, and regulatory compliance. Collaborative strategies and innovative practices help optimize costs. Concrete slab costs for hospitals average around $8 per square foot. In conclusion, a strategic approach ensures both immediate success and long-term resilience in hospital construction.
Concrete slabs serve as a foundational element in hospital buildings, providing a stable surface for the entire structure. They must accommodate heavy loads, support intricate infrastructure, and meet stringent safety standards.
The thickness of a concrete slab is a critical factor, especially in healthcare facilities with heavy medical equipment. Thicker slabs, designed for structural support, influence both material and labor costs.
Site conditions, including soil type and terrain, significantly influence overall costs. Extensive site preparation, such as excavation and grading, may be required, impacting the stability and suitability of the foundation.
Hospital designs, particularly in critical areas like operating rooms and laboratories, demand specific structural considerations. Meeting these requirements involves additional engineering complexities, contributing to higher costs.
The location and accessibility of the construction site influence transportation costs. Remote sites or those with logistical challenges may experience higher expenses related to the efficient delivery of concrete.
Strategies include optimized design and engineering, thorough site analysis, value engineering, local material sourcing, efficient construction practices, technology integration, and lifecycle cost analysis. These approaches aim to balance efficiency, safety, and cost-effectiveness.
Here I am going to share some steps to get your hospital construction concrete cost estimate report.
You can send us your plan on info@estimatorflorida.com
Before starting your project, we send you a quote for your service. That quote will have detailed information about your project. Here you will get information about the size, difficulty, complexity and bid date when determining pricing.
Our team will takeoff and estimate your project. When we deliver you’ll receive a PDF and an Excel file of your estimate. We can also offer construction lead generation services for the jobs you’d like to pursue further.
561-530-2845
info@estimatorflorida.com
Address
5245 Wiles Rd Apt 3-102 St. Pete Beach, FL 33073 United States
561-530-2845
info@estimatorflorida.com
Address
5245 Wiles Rd Apt 3-102 St. Pete Beach, FL 33073 United States
All copyright © Reserved | Designed By V Marketing Media | Disclaimer