Bid Strong, Bid Smart – Try Our Concrete Cost Estimating Service!
- Accurancy
- Efficiency
- Transparency
- Customization
- Time Saving
- Professionalism
- Cost Control
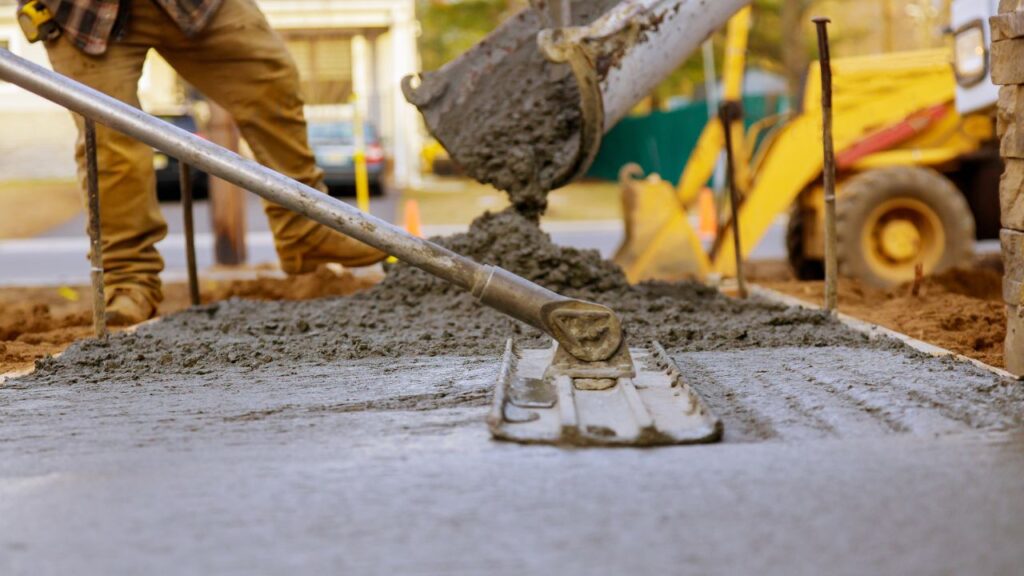
Constructing a townhouse involves a multitude of considerations, and one of the foundational elements, quite literally, is the cost of concrete. Concrete serves as the backbone of any construction project, providing strength, durability, and stability to the structure. Accurately estimating concrete costs is essential for budgeting and ensuring the success of a townhouse construction project. In this guide, we will delve into the key factors influencing townhouse concrete costs and provide insights into developing an effective cost estimate.
The choice of foundation type profoundly impacts both the structural integrity of a townhouse and the associated concrete costs. Slab-on-grade foundations, being a simpler and more economical option, use less concrete but may necessitate additional investment in insulation. Crawl space foundations strike a balance, providing accessibility beneath the structure while maintaining cost efficiency. On the other end, full basements, though requiring more concrete, offer valuable additional usable space. The decision on foundation type involves a careful consideration of project requirements, budget constraints, and the desired functionality of the townhouse.
Fully Insured License
Concrete Construction Contractor
Make Informed Design Decisions Showcase Your Design Ideas
Get RenderingThe intricacies of concrete mix design wield a significant influence on both cost and performance in construction projects. Tailoring the concrete mix to the specific needs of the townhouse involves a nuanced understanding of factors such as required strength, durability, and environmental conditions. High-strength or specialty mixes may come at a higher price point, but their performance attributes are essential for meeting structural demands. A thoughtful analysis of the project’s requirements ensures that the selected mix achieves a harmonious balance between cost and performance.
Ensuring structural integrity often requires the incorporation of reinforcement materials like rebar or mesh into the concrete. The type and quantity of reinforcement significantly impact concrete costs. Structural engineers play a crucial role in determining the specific reinforcement needs based on the townhouse design and adherence to local building codes. The careful selection of reinforcement materials is an investment in the long-term durability and resilience of the structure, contributing to its overall stability.
The condition and accessibility of the construction site are pivotal factors influencing concrete costs. Site preparation involves clearing, grading, and ensuring a suitable foundation for concrete placement. Difficult-to-reach or restricted sites may incur additional expenses due to the need for specialized equipment, impacting both the timeline and budget. A thorough assessment of the site conditions and logistics is essential to anticipate and mitigate potential challenges, ensuring a smooth and cost-effective construction process.
The human and mechanical elements involved in concrete placement contribute significantly to the overall project expense. Skilled labor is indispensable for tasks such as concrete placement, finishing, and curing. Additionally, considerations for equipment costs, including concrete delivery, pumping equipment, and other machinery, further add to the financial considerations. A comprehensive understanding of labor and equipment requirements allows for accurate budgeting and planning, ensuring that the construction proceeds efficiently and within the predetermined financial parameters.
Embarking on a townhouse construction project requires meticulous planning, and developing an accurate cost estimate is a pivotal step in this process. This involves a series of strategic considerations to ensure that the budget aligns with the project’s scope and requirements.
The foundation of a precise cost estimate lies in the accurate measurement of the townhouse’s dimensions. Beyond the foundation, additional concrete elements such as driveways, sidewalks, or patios must also be considered. Thorough measurements provide the foundation for determining the quantity of concrete needed for each specific aspect of the project. This meticulous approach not only ensures that the right amount of materials is budgeted for but also contributes to the overall efficiency of the construction process.
Collaborating with construction professionals is invaluable when developing a concrete cost estimate. Architects, engineers, and contractors bring their expertise to the table, offering insights into project-specific requirements and potential challenges. Their input helps refine the estimate, taking into account structural nuances, local building codes, and other factors that might influence concrete costs. This collaborative approach ensures that the estimate is well-informed and aligns with the standards and expectations of the construction industry.
The choice of concrete supplier can significantly impact the overall cost of the project. Obtaining quotes from multiple suppliers facilitates a comparative analysis of prices. Beyond the raw cost of concrete, factors such as delivery costs, mix quality, and additional services offered by suppliers should be considered. This thorough evaluation enables informed decision-making, allowing for the selection of a supplier that not only meets budgetary constraints but also provides quality materials and services essential for the success of the project.
In the dynamic landscape of construction, unforeseen challenges are inevitable. Therefore, incorporating a contingency factor into the cost estimate is a prudent strategy. This buffer accounts for unexpected expenses, variations in material prices, or unforeseen circumstances that may arise during the construction process. A well-calculated contingency ensures that the budget remains flexible and resilient, offering a financial safety net to address changes or surprises without jeopardizing the overall success of the townhouse construction project.
Constructing a townhouse involves significant concrete expenses, and finding ways to save on costs without compromising quality is crucial. Here are six important cost-saving strategies for your townhouse concrete project:
Opt for an efficient foundation design that meets structural requirements while minimizing the use of concrete. Work closely with architects and engineers to explore foundation options that provide stability and functionality without unnecessary excess. Efficient design not only reduces concrete costs but also enhances the overall sustainability of the project.
Consider bulk purchasing of concrete materials from suppliers. Buying in larger quantities often allows you to negotiate better prices and receive volume discounts. This strategy is particularly effective when you have a clear understanding of the project’s concrete requirements, enabling you to order materials in a cost-effective manner.
Work with concrete experts to optimize the mix design for your project. Different projects have specific concrete mix requirements, and finding the right balance between cost and performance is crucial. Avoid over-specifying concrete strength if it exceeds project needs, as this can contribute to unnecessary expenses. An optimized mix design ensures you get the required performance without unnecessary costs.
Explore local sources for concrete materials to reduce transportation costs. Local suppliers often offer competitive prices, and the proximity can result in lower delivery expenses. Additionally, supporting local businesses contributes to the regional economy. Conduct thorough research to identify reputable local suppliers who can meet your project’s requirements.
Efficient project planning and execution can lead to significant cost savings. Ensure that all aspects of the concrete work are well-coordinated to minimize delays and prevent rework.
Timely completion of each phase of the project reduces labor costs and potential financial implications associated with project extensions. A well-executed plan ensures that resources are used optimally, contributing to overall cost efficiency.
Embrace technological advancements and innovative construction methods that can enhance efficiency and reduce concrete usage. Modern formwork systems, advanced curing techniques, and other innovations in the construction industry can lead to resource savings. While there might be an initial investment in adopting new technologies, the long-term cost benefits often outweigh the upfront expenses.
The national average cost for concrete stands at $150 per cubic yard, falling within the range of $132 to $198 per cubic yard charged by most concrete companies. For smaller projects, homeowners typically invest a minimum of $660, while larger concrete endeavors may incur a total expenditure of up to $20,400.
Fully Insured License
Concrete Construction Contractor
Make Informed Design Decisions Showcase Your Design Ideas
Get RenderingIn conclusion, estimating and managing concrete costs for a townhouse construction project require a strategic and multifaceted approach. Key factors such as foundation type, concrete mix design, reinforcement materials, site preparation, labor, and equipment costs significantly influence the overall budget. Accurate measurements, consultation with construction professionals, a comparative analysis of concrete suppliers, and contingency planning are essential steps in developing a precise cost estimate. To enhance cost-effectiveness, implementing six key strategies, including efficient foundation design, bulk material purchase, optimized mix design, local material sourcing, precise project planning, and embracing technology, can result in substantial savings. The national average cost for concrete provides a benchmark for understanding the financial landscape of such projects. Careful planning, collaboration, and strategic decision-making are crucial for ensuring the success of the townhouse construction, balancing budget constraints with quality outcomes.
The national average cost for concrete stands at $150 per cubic yard, falling within the range of $132 to $198 per cubic yard charged by most concrete companies.
The foundation type significantly influences concrete costs. For instance, slab-on-grade foundations use less concrete but may require additional investment in insulation, while full basements, though requiring more concrete, offer valuable additional usable space.
Reinforcement materials, such as rebar or mesh, contribute to the structural integrity of the townhouse. The type and quantity of reinforcement significantly impact concrete costs, with structural engineers determining specific needs based on the townhouse design and local building codes.
Opting for an efficient foundation design that meets structural requirements while minimizing the use of concrete can contribute to cost savings. Working closely with architects and engineers to explore options that provide stability without unnecessary excess helps enhance overall project sustainability.
Yes, bulk purchasing of concrete materials from suppliers is a practical strategy. Buying in larger quantities often allows negotiation for better prices and volume discounts, especially when there is a clear understanding of the project’s concrete requirements.
Embracing technological advancements and innovative construction methods, such as modern formwork systems and advanced curing techniques, can enhance efficiency and reduce concrete usage. While there might be an initial investment, the long-term cost benefits often outweigh upfront expenses.
Here I am going to share some steps to get your Townhouse Concrete Cost estimate report.
You can send us your plan on info@estimatorflorida.com
Before starting your project, we send you a quote for your service. That quote will have detailed information about your project. Here you will get information about the size, difficulty, complexity and bid date when determining pricing.
Our team will takeoff and estimate your project. When we deliver you’ll receive a PDF and an Excel file of your estimate. We can also offer construction lead generation services for the jobs you’d like to pursue further.
561-530-2845
info@estimatorflorida.com
Address
5245 Wiles Rd Apt 3-102 St. Pete Beach, FL 33073 United States
561-530-2845
info@estimatorflorida.com
Address
5245 Wiles Rd Apt 3-102 St. Pete Beach, FL 33073 United States
All copyright © Reserved | Designed By V Marketing Media | Disclaimer