Boost Your Roof Bids – Request a Precision Estimate!
- Accurancy
- Efficiency
- Transparency
- Customization
- Time Saving
- Professionalism
- Cost Control
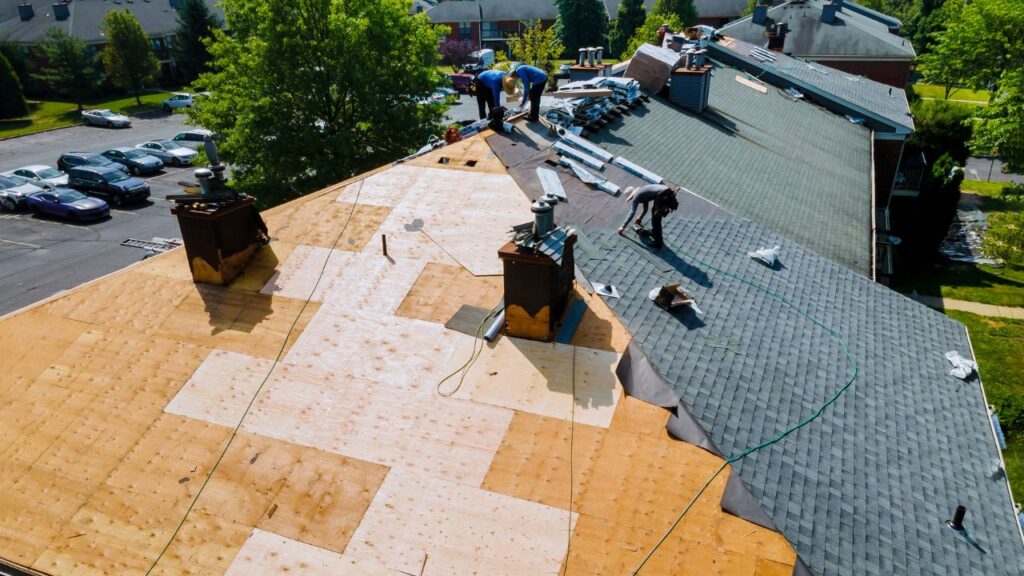
Replacing or installing a new aluminum roof for a warehouse is a significant undertaking that involves various factors influencing the overall cost. Whether you are considering upgrading your existing roof or constructing a new warehouse, understanding the key elements affecting aluminum roofing costs is crucial. In this comprehensive guide, we will explore the factors influencing warehouse aluminum roof costs and provide insights to help you estimate expenses accurately.
The dimensions and intricacy of your warehouse roof are pivotal factors in determining the overall project cost. Larger roofs, especially those with complex designs, necessitate increased material quantities, extended labor hours, and a longer installation period, all contributing to higher expenses. Additionally, factors like roof pitch and shape can introduce complexities during installation, impacting the overall project cost. Careful consideration of these design aspects is essential for an accurate estimation that aligns with both your budget and project requirements.
The quality and grade of the chosen aluminum material are influential cost determinants in your roofing project. Opting for a higher-grade aluminum, which often boasts enhanced durability and corrosion resistance, comes with a higher price tag. It’s crucial to strike a balance between the specific requirements of your warehouse and the desired material quality. This ensures a cost-effective decision-making process that aligns with both your immediate and long-term roofing needs.
The need for insulation within your warehouse adds another layer of consideration to the overall cost estimation. Proper insulation is crucial for energy efficiency and climate control within the facility. Factors such as the choice of insulation materials, thickness, and installation complexity should be carefully weighed in the estimation process. Factoring in insulation requirements ensures that your aluminum roof not only meets structural needs but also provides optimal thermal performance.
The inclusion of additional features such as skylights, ventilation systems, or solar panels contributes to the overall roofing cost. While these accessories offer enhanced functionality and long-term benefits, they also introduce complexities during installation, impacting both material and labor expenses. A meticulous assessment of necessary accessories is vital for an accurate cost estimation, allowing you to make informed decisions about which features align with your warehouse’s specific needs.
The cost of labor for the installation of your aluminum roof is a significant component of the overall budget. Labor costs can vary based on factors such as the availability of skilled workers, their experience levels, and the complexity of the installation process. Seeking quotes from reputable roofing contractors aids in assessing the labor component accurately, ensuring that your budget accounts for the skilled work required to bring your roofing project to fruition.
Compliance with local building codes and securing necessary permits are foundational steps in the roofing process. Permit fees and expenses related to meeting regulatory requirements should be factored into the cost estimation. Understanding and adhering to local regulations not only prevent potential legal complications but also ensure a smooth and transparent project, avoiding unexpected costs that may arise due to non-compliance.
The type and quality of the underlayment beneath the aluminum roofing sheets significantly impact the roof’s overall longevity and performance. Investing in high-quality underlayment adds an extra layer of protection against moisture and guarantees a more durable roofing system. While this contributes to material costs, the choice of underlayment is a critical consideration that influences the overall quality and resilience of your warehouse roof over time.
The geographical location of your warehouse and the logistics involved in transporting roofing materials to the site can influence overall project costs. Warehouses situated in remote or challenging-to-access locations may incur higher transportation expenses. Evaluating the intricacies of transportation and logistics is crucial for achieving an accurate cost estimate, allowing you to plan for potential challenges associated with material delivery to your warehouse site.
Initiate the estimation process with a comprehensive roof inspection, meticulously examining the existing roof or, in the case of new construction, the warehouse structure. Evaluate the size, design, and overall condition of the roof to identify potential challenges and determine if there are any specific requirements for additional features. This initial step sets the groundwork for an accurate estimation, allowing you to address specific nuances and intricacies associated with the roof that may impact the overall project cost.
Choosing the right aluminum material is a critical decision in the roofing process. Tailor the selection based on the unique needs of your warehouse, taking into account factors such as climate considerations, required durability, and budget constraints. Collaborate with roofing professionals to determine the most suitable grade of aluminum for your project. The material selected not only influences the immediate project cost but also plays a crucial role in the long-term performance and resilience of your warehouse roof.
Evaluate the insulation requirements based on the purpose and location of the warehouse. Understanding the specific needs for optimal energy efficiency enables you to determine the type and thickness of insulation required. Factor in insulation costs and the potential complexities involved in installation during the estimation process. Proper insulation planning not only contributes to the immediate project cost but also influences ongoing energy savings and environmental sustainability.
The decision to incorporate additional features and accessories, such as skylights, ventilation systems, or solar panels, should be made with careful consideration. While these elements can enhance the functionality and sustainability of your warehouse, it’s crucial to be mindful of their impact on costs. Collaborate with roofing experts to seamlessly integrate these accessories into the overall roofing plan, ensuring that their inclusion aligns with your budget and contributes positively to the long-term goals of your warehouse.
Ensure a well-informed decision-making process by reaching out to several reputable roofing contractors to obtain detailed quotes. Request comprehensive quotes that encompass material costs, labor costs, permit fees, and any additional expenses. Comparing multiple quotes allows you to understand market rates, evaluate the scope of services offered by different contractors, and select a roofing professional that not only fits your budget but also aligns with your specific project requirements.
While upfront costs are undeniably significant, it’s essential to take a holistic approach by factoring in the long-term costs associated with various roofing choices. High-quality materials and insulation may incur higher initial costs, but they often result in substantial savings on energy bills and maintenance over the lifespan of the roof. Considering the long-term costs ensures that your roofing decisions align with both immediate budget constraints and the broader financial sustainability of your warehouse.
Warehouse aluminum roof costs vary widely based on the factors mentioned above. On average, the cost per square foot for an aluminum roof installation ranges from $7 to $17. Larger warehouses or those with complex designs can fall on the higher end of the cost spectrum. It’s important to note that these are general estimates, and obtaining customized quotes based on your warehouse’s specific needs is essential for accurate budgeting.
Prioritize energy-efficient design principles when planning your aluminum roof installation. Investing in proper insulation, reflective coatings, and strategically placing skylights can significantly reduce long-term operational costs. Effective insulation contributes to thermal efficiency, while reflective coatings minimize heat absorption. Strategically positioned skylights not only enhance natural lighting, reducing the reliance on artificial sources but also contribute to a more sustainable and energy-efficient warehouse environment. While the initial investment may be higher, the long-term cost savings in energy bills make energy-efficient design a financially prudent decision.
Establishing a proactive maintenance plan is crucial for preserving the longevity of your aluminum roof and avoiding potential costly repairs. Regular inspections and prompt addressing of minor issues can prevent them from escalating into more significant problems. By investing in regular maintenance, you ensure that your roof remains in optimal condition, reducing the likelihood of unexpected expenses. This preventative approach not only safeguards your investment but also minimizes the overall costs associated with roof repairs and replacements over time.
Carefully assess the necessity of additional accessories when planning your aluminum roof. While accessories like skylights, ventilation systems, or solar panels can enhance functionality, consider opting for essential additions and minimizing complex features. This approach allows you to achieve your desired outcomes while contributing to cost savings. A streamlined selection of accessories not only reduces upfront costs but also simplifies the installation process, potentially lowering labor expenses.
Collaborate with roofing contractors who can leverage bulk purchasing discounts on materials. Grouping multiple projects or coordinating with other nearby construction endeavors provides the opportunity to benefit from reduced material costs. Bulk material purchases enable you to take advantage of economies of scale, translating into substantial savings on the overall project budget. This collaborative approach ensures cost-effectiveness without compromising the quality of the roofing materials used.
Take advantage of potential government incentives available for energy-efficient roofing installations. Research local and federal programs that offer tax incentives, rebates, or grants for incorporating sustainable features such as reflective roofing materials or solar panels. These incentives not only contribute to offsetting initial costs but also align your project with broader environmental goals. Exploring government incentives enhances the economic viability of your roofing project and positions it within a framework of sustainability.
From small to large projects, residential to commercial, we’re here to help you win. Fast results guaranteed.
Engage in competitive bidding by seeking quotes from multiple roofing contractors. This approach ensures that you receive competitive pricing for your aluminum roof installation. By obtaining detailed quotes that encompass material costs, labor costs, and additional expenses, you gain a comprehensive understanding of the market rates. Competitive bidding empowers you to make an informed decision, selecting a roofing contractor that not only aligns with your budgetary constraints but also meets your specific project requirements. This strategic approach contributes to overall cost-effectiveness while ensuring the quality and efficiency of the roofing process.
Estimating the cost of an aluminum roof for a warehouse involves a thorough assessment of various factors, ranging from roof size and material quality to labor costs and accessories. The estimation process should be meticulous, considering the specific needs of the warehouse and complying with local regulations.
While the initial costs are a crucial consideration, it’s equally important to factor in long-term savings and the overall performance of the roofing system. Implementing cost-saving strategies, such as energy-efficient design and regular maintenance, contributes to the economic viability of the project.
Navigating the complexities of warehouse aluminum roofing requires collaboration with experienced roofing professionals who can provide tailored solutions. By incorporating these insights and strategies, you can achieve a cost-effective and durable aluminum roofing solution for your warehouse.
The cost of installing an aluminum roof depends on various factors, including the size and design of the roof, the quality of the aluminum material chosen, insulation requirements, the inclusion of accessories, labor costs, permits, regulations, the type of underlayment used, and logistical considerations.
The estimation process involves a thorough roof inspection, careful material selection, planning for insulation and accessories, obtaining multiple quotes from reputable roofing contractors, and considering long-term costs. Each of these steps contributes to a comprehensive understanding of the project’s financial aspects.
On average, the cost per square foot for an aluminum roof installation on a warehouse ranges from $7 to $17. However, the actual cost can vary based on specific factors such as roof size, design complexity, and location.
Cost-saving strategies include prioritizing energy-efficient design principles, implementing regular maintenance plans, optimizing roofing accessories, collaborating with contractors for bulk material purchases, exploring government incentives, and engaging in competitive bidding to obtain favorable pricing from roofing contractors.
The grade and quality of the chosen aluminum material directly impact the overall cost. Higher-grade aluminum, with enhanced durability and corrosion resistance, tends to be more expensive. Balancing the specific needs of the warehouse with the desired material quality is crucial for making cost-effective decisions.
Government incentives, such as tax incentives, rebates, or grants, can offset initial costs associated with energy-efficient roofing installations. Researching and leveraging these incentives align your project with sustainability goals and enhance the economic viability of the roofing project.
Here I am going to share some steps to get a storage building roofing cost estimate report.
You can send us your plan on info@estimatorflorida.com
Before starting your project, we send you a quote for your service. That quote will have detailed information about your project. Here you will get information about the size, difficulty, complexity and bid date when determining pricing.
Our team will takeoff and estimate your project. When we deliver you’ll receive a PDF and an Excel file of your estimate. We can also offer construction lead generation services for the jobs you’d like to pursue further.
561-530-2845
info@estimatorflorida.com
Address
5245 Wiles Rd Apt 3-102 St. Pete Beach, FL 33073 United States
561-530-2845
info@estimatorflorida.com
Address
5245 Wiles Rd Apt 3-102 St. Pete Beach, FL 33073 United States
All copyright © Reserved | Designed By V Marketing Media | Disclaimer