Boost Your Demolition Bids – Request a Precision Estimate!
- Accurancy
- Efficiency
- Transparency
- Customization
- Time Saving
- Professionalism
- Cost Control
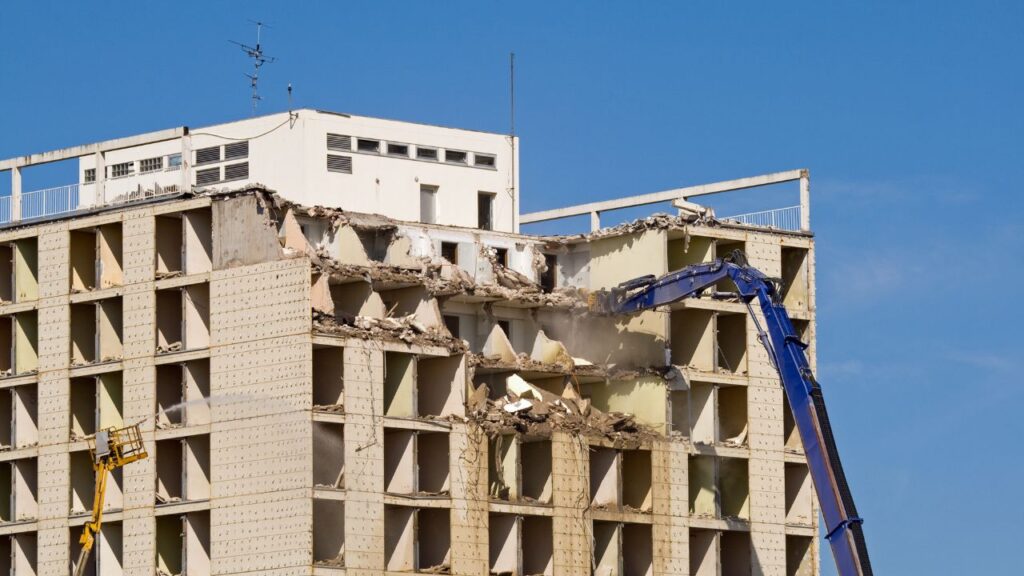
Demolishing a warehouse is a complex undertaking that involves intricate planning, precise budgeting, and a thorough understanding of various factors that influence costs. One essential tool in this process is the Warehouse Demolition Cost Estimator. In this article, we delve into the key considerations, factors, and strategies related to warehouse demolition costs, emphasizing the significance of accurate estimation and how a dedicated cost estimator can streamline this challenging process.
Warehouse demolition involves a range of complexities, including structural considerations, materials handling, waste disposal, and adherence to safety standards. Accurate cost estimation is pivotal during the initial planning stages, enabling project stakeholders to allocate resources efficiently, avoid budget overruns, and ensure the timely completion of the demolition project.
Fully Insured Licensed Hire Contractor For Demolition
Hire ContractorMake Informed Design Decisions Showcase Your Design Ideas
Get RenderingThe size and structural intricacies of a warehouse are fundamental factors influencing demolition costs. Larger warehouses with complex designs may require more extensive and careful demolition efforts, leading to higher expenses. Additionally, factors such as the height of the warehouse, the presence of mezzanines, and the type of construction materials used contribute to the overall cost considerations.
The type of materials present in the warehouse and the subsequent removal of debris significantly impact costs. Warehouses often store diverse materials, and their proper handling and disposal play a crucial role. Hazardous materials may necessitate special removal procedures, and disposal fees can vary based on local regulations. Efficient sorting and management of debris removal are essential considerations during the estimation process.
The ease of access to the demolition site and the necessary preparations influence costs. Warehouses are often situated in industrial areas, and factors such as limited access or the need for additional site clearing can contribute to higher expenses. A comprehensive assessment of site accessibility and preparation requirements is vital for accurate cost estimation.
Compliance with environmental regulations and safety standards is paramount in warehouse demolition. Identification and proper handling of hazardous materials within the warehouse contribute to additional costs. Adherence to disposal guidelines to minimize environmental impact is essential. Prioritizing environmentally conscious demolition practices may incur initial costs but aligns with ethical and legal responsibilities.
The chosen demolition methodology is a key determinant of costs. Different methods, including mechanical demolition, deconstruction, or implosion, come with unique requirements and considerations. Mechanical demolition involves systematic dismantling, while deconstruction focuses on salvaging materials for reuse. Implosion, although dramatic, requires meticulous planning. Each method has its own set of challenges and costs, impacting the overall expense of the warehouse demolition project.
Obtaining necessary permits and ensuring regulatory compliance are critical components of the demolition process. Permitting requirements vary by location and may involve fees. Delays or fines due to non-compliance can impact both the budget and timeline of the project. A thorough understanding of local regulations and proactive measures to secure necessary permits is essential for effective cost estimation.
Accurate budgeting is fundamental to the success of any demolition project, and cost estimators play a pivotal role in achieving this precision. By providing a detailed breakdown of anticipated expenses, cost estimators empower project managers to create budgets that align closely with the actual costs involved in the warehouse demolition process. This meticulous budgeting minimizes the risk of budget overruns and ensures the efficient allocation of resources.
Understanding the specific needs of a warehouse demolition project allows stakeholders to optimize the allocation of resources effectively. This includes determining the right equipment for the demolition tasks at hand, managing labor requirements efficiently, and planning for waste disposal in a sustainable manner. Cost estimators contribute to this optimization process by providing insights into the most effective use of resources.
Efficient cost estimation is crucial for ensuring timely project completion in warehouse demolition endeavors. Project managers, armed with a clear understanding of the intricacies of the demolition process, can create realistic timelines that account for potential challenges. The proactive approach to estimating costs mitigates the risk of delays, ensuring that the project stays on schedule.
Cost estimators function as proactive risk management tools during the planning phase of warehouse demolition projects. Their expertise allows for the identification of potential risks and challenges related to the demolition process. Armed with this insight, project teams can develop comprehensive mitigation strategies, reducing the likelihood of disruptions during demolition.
The utilization of cost estimators empowers project stakeholders to engage in informed comparative analysis, a critical aspect of decision-making in warehouse demolition projects. Comparative analysis involves evaluating different scenarios and considering the cost implications of specific demolition methods, materials, or environmental considerations. Cost estimators provide a comprehensive breakdown of potential costs for each scenario, facilitating data-driven decision-making.
To provide a general overview, let’s consider some average cost ranges for warehouse demolition:
It’s crucial to note that these adjustments provide a broad estimate, and actual costs may still vary based on specific project requirements, site conditions, and regional differences.
Consulting with demolition professionals and obtaining detailed quotes based on the unique characteristics of the warehouse is recommended for more accurate budgeting.
Before initiating the demolition of a warehouse, a meticulous project assessment is crucial. This involves a comprehensive examination of the warehouse’s structure, materials used, and potential salvageable components. Identifying items that can be salvaged or repurposed contributes to cost savings and aligns with sustainability goals.
Opting for a selective or partial demolition approach can be a key strategy for cost savings. Instead of demolishing the entire warehouse, selectively dismantling specific components can significantly reduce disposal costs. Salvaging materials like steel beams, concrete, or other valuable components not only lowers project expenses but also opens avenues for potential revenue through material recycling.
Early identification and removal of hazardous materials are critical cost-saving strategies in warehouse demolition. Conducting thorough inspections to detect materials such as asbestos or lead allow for proper planning and budgeting. Addressing hazardous materials early in the process helps prevent unexpected delays and additional costs during demolition.
Efficient debris management is a fundamental aspect of warehouse demolition cost savings. Implementing on-site sorting practices enables the identification of recyclable materials, reducing the volume of waste sent to landfills. Collaboration with recycling facilities can sometimes result in cost savings or even revenue for salvaged materials.
Choosing the right demolition techniques is crucial for cost-effective and efficient project execution. Depending on the warehouse’s structure and location, methods such as mechanical demolition, deconstruction, or implosion may offer savings in terms of time and resources. Tailoring the demolition approach to the specific characteristics of the warehouse ensures optimal efficiency and cost-effectiveness.
The integration of advanced technologies and modern demolition equipment can enhance precision and efficiency in the warehouse demolition process. Utilizing cutting-edge equipment may streamline tasks, reducing labor costs and overall project timelines. Embracing technology not only contributes to cost savings but also improves safety and accuracy during the demolition.
Strategic timing is a valuable consideration for achieving cost savings in warehouse demolition. Planning the project during periods of favorable economic conditions for construction and demolition services may result in more competitive pricing from contractors. Understanding market dynamics and scheduling the demolition when demand for services is lower can lead to cost efficiencies. Strategic timing aligns with budget considerations, ensuring that the project benefits from competitive pricing and optimized resource utilization.
The Warehouse Demolition Cost Estimator is an indispensable tool for the intricate process of demolishing warehouses. Accurate cost estimation is vital, considering factors like warehouse size, materials, environmental considerations, and chosen demolition methodology. The estimator facilitates accurate budgeting, resource optimization, timely project completion, risk mitigation, and informed comparative analysis. By providing a breakdown of demolition costs, it empowers stakeholders to make informed decisions, fostering transparency and trust. Additionally, cost-saving strategies, such as detailed project assessment, selective demolition, and technology integration, further enhance the efficiency and economic viability of warehouse demolition. Strategic timing and adherence to regulatory compliance contribute to overall project success and cost savings. In essence, leveraging specialized tools and strategic approaches ensures the successful and cost-effective execution of warehouse demolition projects.
Accurate cost estimation is vital for warehouse demolition as it enables project stakeholders to allocate resources efficiently, avoid budget overruns, and ensure timely project completion. It provides a detailed breakdown of anticipated expenses, empowering project managers to make informed decisions and fostering transparency among stakeholders.
Several factors impact warehouse demolition costs, including the size and structure of the warehouse, materials and debris removal, site accessibility and preparation, environmental considerations, chosen demolition methodology, and permitting and regulatory compliance.
The Warehouse Demolition Cost Estimator provides a comprehensive breakdown of anticipated expenses, allowing project managers to create accurate budgets aligned with the actual costs of the demolition process. This tool minimizes the risk of budget overruns and ensures efficient resource allocation.
Cost estimators contribute to resource optimization, timely project completion, risk mitigation, and informed comparative analysis. They offer insights into the most effective use of resources, help create realistic timelines, identify potential risks, and facilitate data-driven decision-making for optimal project outcomes.
The cost ranges provided are general estimates and may vary based on specific project requirements, site conditions, and regional differences. It is advisable to consult with demolition professionals and obtain detailed quotes based on the unique characteristics of the warehouse for more accurate budgeting.
Opting for selective or partial demolition reduces disposal costs by dismantling specific components rather than demolishing the entire warehouse. Salvaging valuable materials lowers project expenses and opens opportunities for potential revenue through material recycling.
Technology integration enhances precision and efficiency in warehouse demolition. Advanced equipment can streamline tasks, reducing labor costs and overall project timelines. Embracing technology not only contributes to cost savings but also improves safety and accuracy during the demolition process.
Planning warehouse demolition projects during periods of favorable economic conditions for construction and demolition services may result in more competitive pricing. Understanding market dynamics and scheduling demolition during lower demand periods can lead to cost efficiencies, aligning with budget considerations.
Stakeholders can ensure environmental compliance by identifying hazardous materials, adhering to disposal guidelines, and prioritizing environmentally conscious demolition practices. Compliance with safety standards and regulations minimizes risks and associated costs during the demolition process.
Yes, obtaining detailed quotes from multiple demolition professionals based on the unique characteristics of the warehouse project is advisable. This ensures more accurate budgeting and allows stakeholders to make informed decisions about the most suitable and cost-effective demolition solutions.
Here I am going to share some steps to get your warehouse demolition cost estimate report.
You can send us your plan on info@estimatorflorida.com
Before starting your project, we send you a quote for your service. That quote will have detailed information about your project. Here you will get information about the size, difficulty, complexity and bid date when determining pricing.
Our team will takeoff and estimate your project. When we deliver you’ll receive a PDF and an Excel file of your estimate. We can also offer construction lead generation services for the jobs you’d like to pursue further.
561-530-2845
info@estimatorflorida.com
Address
5245 Wiles Rd Apt 3-102 St. Pete Beach, FL 33073 United States
561-530-2845
info@estimatorflorida.com
Address
5245 Wiles Rd Apt 3-102 St. Pete Beach, FL 33073 United States
All copyright © Reserved | Designed By V Marketing Media | Disclaimer