Boost Your Roof Bids – Request a Precision Estimate!
- Accurancy
- Efficiency
- Transparency
- Customization
- Time Saving
- Professionalism
- Cost Control
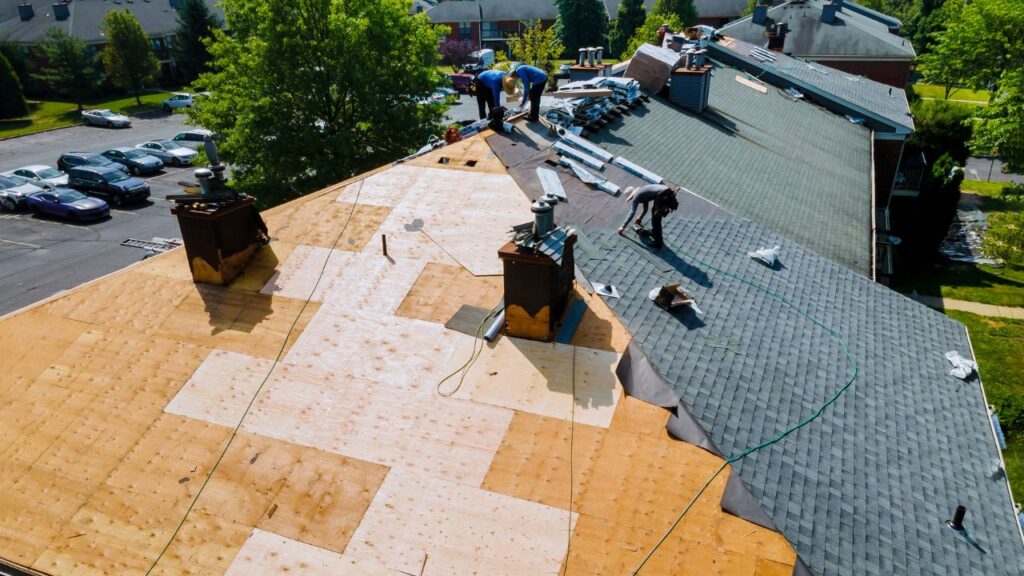
Warehouse owners and managers understand the importance of a reliable and durable roof to safeguard their valuable assets. When the time comes for a warehouse roof replacement, it’s crucial to have a comprehensive understanding of the factors influencing costs, effective cost management strategies, and a breakdown of the expenses involved. In this guide, we’ll explore key considerations for warehouse roof replacement costs and offer insights to help property owners make informed decisions.
The roof is a critical component of any warehouse, providing protection for both the structure and its contents. Over time, wear and tear or damage can compromise the integrity of the roof, necessitating timely replacement. Here are key signs indicating that it might be time for a warehouse roof replacement:
Regular roof inspections by professionals can help identify these signs early, allowing for timely repairs or replacement to avoid more extensive damage and costs.
The size and complexity of a warehouse roof are pivotal factors influencing replacement costs. Larger roofs or those with intricate designs, multiple penetrations, and equipment installations impose heightened demands for labor, time, and resources. Managing complex structures requires specialized skills, impacting the overall project expenses. The intricacies associated with warehouse roofs underscore the importance of meticulous planning and the need for skilled professionals to ensure a successful and cost-effective replacement.
The selection of roofing material is a critical determinant in overall replacement costs. Warehouse owners can choose from various materials such as TPO, EPDM, metal, and asphalt, each presenting its own costs, benefits, and considerations. Property owners must carefully assess factors like durability, energy efficiency, and budget constraints when making decisions about the right material for their warehouse roof. The choice of roofing material significantly shapes the long-term performance and maintenance costs of the roofing system.
The condition of a warehouse roof’s underlayment and the choice of insulation materials play a crucial role in both cost and performance. Opting for high-quality underlayment and insulation contributes substantially to energy efficiency and weather resistance. While upgrading these components may introduce additional upfront costs, the long-term benefits, including significant savings and enhanced comfort within the warehouse, make such investments prudent. Quality underlayment and insulation are integral to ensuring the longevity and efficiency of the entire roofing system.
Labor costs constitute a substantial portion of warehouse roof replacement expenses. The location of the warehouse, accessibility challenges, and the complexity of the roof structure are key factors influencing labor costs. Certain roofing materials may demand specialized skills, impacting overall labor expenses. Skilled professionals are essential for the successful installation of warehouse roofing, contributing significantly to the overall costs of the replacement project.
The cost associated with the meticulous removal of existing roofing material is a necessary consideration in warehouse roof replacement. Proper disposal, in compliance with environmental regulations, adds to the overall project cost. The detailed removal process is crucial for setting the stage for a seamless roof replacement, minimizing the risk of underlying issues and ensuring the new roofing system’s long-term effectiveness.
Incorporating accessories such as skylights, ventilation systems, or other features can impact overall costs. While these additions contribute to a well-equipped roofing system, property owners must carefully weigh the benefits against the added expenses. Accessories enhance the functionality and aesthetics of the warehouse roof, but a strategic balance between features and costs is essential for a cost-effective and efficient roofing solution.
Investing in high-quality roofing materials with extended warranties is a strategic decision for warehouse owners. While premium materials may entail higher upfront costs, they ensure superior resistance to environmental factors, significantly reducing the likelihood of premature deterioration. Carefully considering the lifespan and warranty coverage of selected materials is paramount for achieving long-term cost-effectiveness. This strategic investment transforms the initial cost into a wise decision, providing durability and resilience for the warehouse roof over the years.
For a warehouse roof replacement, the costs vary depending on the type of roofing material chosen:
The choice of roofing material significantly influences the overall cost of a warehouse roof replacement. It’s important to consider your specific needs, preferred style, and budget when making a decision.
Ready to raise the roof on your bids? Take your construction projects to new heights by inquiring about our top-notch estimating services.
Warehouse roof replacement is a significant investment, and effective cost management strategies are crucial for ensuring a successful and financially sound project. Here are key strategies to manage costs during warehouse roof replacement:
Engaging in comparative bidding is a strategic approach that empowers warehouse owners to make well-informed decisions while managing costs effectively. By obtaining detailed bids from multiple reputable contractors, property owners gain insight into the range of pricing and services offered in the market. This transparency fosters competition among contractors, potentially leading to more competitive pricing. Comparative bidding not only helps identify cost-saving opportunities but also ensures that the selected contractor aligns with the specific needs of the warehouse. It establishes a foundation for transparency and collaboration throughout the roof replacement project.
Exploring energy-efficient roofing options is a forward-thinking strategy that goes beyond immediate costs to consider long-term operational savings. Warehouse owners can opt for materials and technologies that enhance energy efficiency, such as reflective coatings or cool roofing solutions. While the upfront costs for energy-efficient options may be slightly higher, the potential for reduced heating and cooling expenses over time makes them a prudent investment. This strategy not only contributes to cost management but also aligns with sustainability goals, positioning the warehouse as an environmentally responsible facility.
Seeking professional consultation from experienced roofing professionals is an indispensable step in effective cost management. Experienced roofers bring a wealth of knowledge regarding material selection, design considerations, and cost-effective solutions. Their expertise ensures accurate cost estimation, effective project planning, and optimal decision-making tailored to the warehouse’s specific needs. Professional consultation minimizes the risk of unforeseen challenges, contributing to a smoother and more cost-effective roof replacement process.
Implementing regular maintenance plans is a proactive strategy that pays dividends in long-term cost savings. A well-maintained roof not only extends its lifespan but also helps identify and address potential issues early on, preventing costly repairs or replacements in the future. Routine inspections, gutter cleaning, and timely repairs contribute to the overall health of the roofing system, reducing the likelihood of major issues that could escalate costs over time.
Strategic timing of the roof replacement project is a cost management strategy that takes into account seasonal variations and weather conditions. Performing the replacement during favorable weather conditions can streamline the process, reduce potential delays, and minimize associated costs. Additionally, scheduling the project during periods of lower demand for roofing services may provide an opportunity to negotiate better pricing with contractors, optimizing overall project costs.
Striking a balance between material quality and cost is a crucial consideration for warehouse owners. While investing in high-quality roofing materials is essential for long-term durability, it’s equally important to avoid unnecessary over-specification that may inflate costs. Careful assessment of the specific needs of the warehouse allows property owners to select materials that meet quality standards without exceeding budget constraints, ensuring a cost-effective yet resilient roofing solution.
Incorporating a contingency budget into the overall project plan is a prudent measure to account for unforeseen challenges or additional requirements. Unanticipated issues may arise during the roof replacement process, and having a contingency budget provides the flexibility to address these challenges without compromising the overall project quality or timeline. This strategy adds a layer of financial preparedness, enhancing the project’s resilience to unexpected circumstances.
Warehouse owners can explore potential government incentives or rebates for energy-efficient roofing solutions. Many regions offer financial incentives to encourage the use of sustainable and energy-efficient roofing materials. Taking advantage of such programs can offset initial costs and improve the overall cost-effectiveness of the project. Researching and leveraging available incentives aligns with cost management objectives while contributing to the warehouse’s environmental sustainability goals.
Warehouse roof replacement is a significant undertaking that requires careful consideration of various factors to ensure a successful and cost-effective project. Recognizing signs indicating the need for replacement, understanding the factors influencing costs, and implementing effective cost management strategies are crucial for warehouse owners and managers. Regular inspections, material selection, and strategic planning contribute to the longevity and efficiency of the new roofing system. Additionally, exploring energy-efficient solutions, seeking professional consultation, and taking advantage of government incentives further enhance the overall cost-effectiveness of the project. By integrating these considerations and strategies, warehouse owners can make informed decisions that not only protect their valuable assets but also contribute to the sustainability and resilience of their facilities over the years.
Look for signs such as visible water stains, deteriorating roofing materials, sagging roof surfaces, increased energy costs, mold or mildew growth, interior temperature fluctuations, and if the roof has surpassed its expected lifespan.
Key factors include the size and complexity of the roof, choice of roofing material, condition of underlayment and insulation, labor costs, removal of existing roofing material, incorporation of accessories, and the quality of materials and warranties.
Costs vary based on the chosen material. For instance, single-ply roofing ranges from $9.00 to $16.20 per square foot, while metal roofing averages between $15.00 and $22.50 per square foot.
Employ strategies such as comparative bidding, exploring energy-efficient solutions, seeking professional consultation, implementing regular maintenance plans, strategic timing of the project, balancing material quality with cost, and incorporating a contingency budget.
Experienced roofers provide valuable insights into material selection, design considerations, and cost-effective solutions. Their expertise ensures accurate cost estimation, effective project planning, and optimal decision-making tailored to your warehouse’s specific needs.
Energy-efficient options, such as reflective coatings or cool roofing solutions, may have slightly higher upfront costs but offer long-term operational savings by reducing heating and cooling expenses over time.
Explore potential incentives or rebates for energy-efficient roofing solutions offered by regional governments. Researching and leveraging these programs can offset initial costs and improve the overall cost-effectiveness of the project.
Strategic timing, considering seasonal variations and weather conditions, can streamline the replacement process, reduce potential delays, and minimize associated costs. Scheduling the project during periods of lower demand for roofing services may also lead to better pricing with contractors.
Here I am going to share some steps to get your warehouse roof replacement cost estimate report.
You can send us your plan on info@estimatorflorida.com
Before starting your project, we send you a quote for your service. That quote will have detailed information about your project. Here you will get information about the size, difficulty, complexity and bid date when determining pricing.
Our team will takeoff and estimate your project. When we deliver you’ll receive a PDF and an Excel file of your estimate. We can also offer construction lead generation services for the jobs you’d like to pursue further.
561-530-2845
info@estimatorflorida.com
Address
5245 Wiles Rd Apt 3-102 St. Pete Beach, FL 33073 United States
561-530-2845
info@estimatorflorida.com
Address
5245 Wiles Rd Apt 3-102 St. Pete Beach, FL 33073 United States
All copyright © Reserved | Designed By V Marketing Media | Disclaimer