Boost Your Concrete Loading Dock Bids – Request a Precision Estimate!
- Accurancy
- Efficiency
- Transparency
- Customization
- Time Saving
- Professionalism
- Cost Control
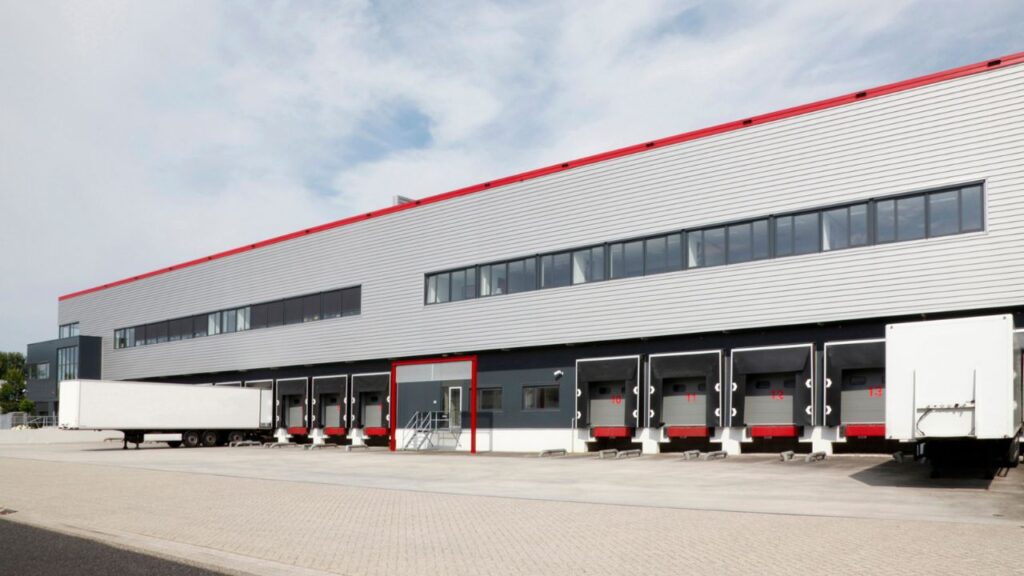
In the dynamic realm of logistics, where the efficient movement of goods is paramount, the loading dock stands as the unsung hero, ensuring the uninterrupted flow that keeps businesses thriving. This critical junction between transportation and facility operations is a concrete fortress, a sturdy linchpin in the intricate machinery of supply chains. However, the construction of such a robust and functional dock demands more than concrete and steel—it requires meticulous planning and a profound understanding of the associated costs.
This comprehensive guide delves into the financial depths of concrete loading dock construction, unraveling the intricate factors that influence the price tags attached to these essential structures.
Estimating the cost of your concrete fortress isn’t a one-size-fits-all equation. Several factors play a crucial role in determining the final figure, making each dock as unique as the needs it serves.
When embarking on the construction journey of a concrete loading dock, the size and complexity of the project emerge as pivotal determinants influencing the overall cost. The number of bays, serving as the operational heart of the dock, intricately interlaces with the amount of concrete needed, excavation requirements, and labor resources. An increase in the number of bays amplifies the scale of the project, inevitably driving the cost upwards. Furthermore, the dimensions of the dock, encompassing both depth and width, play a significant role. Larger dimensions not only result in a more extensive footprint but also escalate the need for additional materials and labor.
It’s a delicate dance between space requirements and financial considerations, with the size of the loading dock intricately woven into the fabric of its construction cost.
Make Informed Design Decisions Showcase Your Design Ideas
Get RenderingThe depth and width of a concrete loading dock unfurl as critical variables, each thread weaving into the intricate tapestry of construction costs. As the dimensions expand, so does the demand for resources. Larger dock sizes necessitate more concrete, a fundamental building block, and contribute to an escalated material cost. Simultaneously, the labor required to handle the increased workload intensifies. The footprint of the dock, extending both horizontally and vertically, becomes a canvas where the financial threads of the project intertwine. It is in these dimensions that the true scope of the construction endeavor becomes apparent, with each incremental increase in size resonating in the final cost estimate.
In the realm of concrete loading dock construction, functionality is paramount. Dock levelers and bumpers, although valuable additions enhancing the operational efficiency of the dock, introduce an additional layer of cost. These components, designed to facilitate the seamless transfer of goods between the dock and the transport vehicle, contribute to the project’s overall complexity and financial requirements. While the upfront investment in dock levelers and bumpers may be seen as an added cost, their long-term benefits in terms of operational ease and safety often justify the expense. Thus, as one navigates the intricate decisions in loading dock design, the consideration of these functional elements becomes a balancing act between enhanced capabilities and the associated costs.
The decision to provide a roof or enclosures to a concrete loading dock introduces a layer of complexity and an increase in construction costs. While offering protection against the elements, covered docks become a strategic choice for businesses requiring weather-resistant loading and unloading operations. However, the benefits of shelter come with an associated price tag. The installation of roofing systems and enclosures elevates the project’s intricacy, demanding additional materials, labor, and design considerations. As businesses weigh the advantages of covered docks, they must also navigate the financial implications, recognizing that the choice to shelter the loading area extends beyond mere protection—it is a calculated investment in operational resilience with its own set of associated costs.
As the literal and metaphorical bedrock of concrete loading dock construction, the foundation and base set the stage for the entire project. Soil conditions play a pivotal role, acting as silent influencers that can significantly impact the construction costs. Soft or uneven ground introduces complexities that demand additional efforts, such as soil stabilization, to ensure a stable foundation. The burden of stabilizing the ground adds both time and cost to the project, emphasizing the critical role that the existing soil plays in shaping the financial landscape of loading dock construction. Understanding and addressing these ground realities become imperative for accurate cost estimations and the overall success of the construction endeavor.
Effective drainage and waterproofing systems are not just elements of convenience; they are vital components that influence material choices and installation costs in concrete loading dock construction. The ability to navigate the flow of water efficiently ensures the longevity and structural integrity of the dock. Robust drainage systems, designed to handle the demands of loading dock operations, become essential considerations, impacting both material costs and the complexity of installation. Waterproofing, a protective layer against the elements, adds another dimension to the project’s intricacies and associated expenses.
As businesses invest in loading docks, the careful management of water becomes a dual commitment—to the structural resilience of the dock and the financial realities of construction.
The durability and load-bearing capacity of a concrete loading dock are closely tied to the reinforcement and type of concrete used in construction. High-traffic docks, subjected to the constant movement of heavy loads, demand a fortification that goes beyond standard requirements. This heightened need for resilience translates into the requirement for heavy-duty reinforcement and specific concrete mixes, which, in turn, can contribute to higher costs. The choice of concrete type becomes a nuanced decision, balancing the demands of durability with the financial considerations of the project. As businesses aim to fortify their loading docks for the rigors of continuous use, they must navigate the landscape of reinforcement options and concrete varieties, recognizing that the upfront investment is a strategic safeguard against long-term wear and tear.
Navigating the construction of a concrete loading dock isn’t just about the physical elements but also involves skillfully navigating local regulations and securing essential permits. The process of obtaining permits and undergoing inspections is not just a bureaucratic formality; it is a crucial aspect of responsible construction that incurs specific fees. The intricacies of adhering to local regulations and ensuring compliance with permitting requirements add a layer of complexity to the overall project, both in terms of time and cost. Businesses investing in concrete loading docks must recognize the significance of this navigational challenge, acknowledging that a thorough understanding of regulatory seas is fundamental to a successful and legally compliant construction venture.
The cost of labor in the construction industry is not a static figure; it is subject to regional variations influenced by factors such as demand, skill availability, and local economic conditions. The rates charged by skilled workers can significantly impact the overall budget for concrete loading dock construction. Regional disparities in labor costs mean that businesses must be attuned to the dynamics of the local labor market when planning their construction projects. The availability of skilled workers, a key resource in the construction process, further contributes to the regional nuances in the cost equation. As businesses set sail in the concrete loading dock construction landscape, understanding and adapting to these regional dynamics become essential components of effective project management and budgeting.
The location of the construction site and the existing infrastructure play a crucial role in shaping the cost considerations of building a concrete loading dock. Difficult access to the site or the need for additional infrastructure elements, such as ramps or specialized transportation, can inflate the overall project price. The accessibility of the construction site influences the ease with which materials and equipment can be transported, impacting logistics and, consequently, costs. Additionally, the availability of existing infrastructure, or the lack thereof, becomes a determinant in the project’s financial landscape. As businesses embark on concrete loading dock construction projects, evaluating the accessibility of the chosen location and considering any required supplementary infrastructure becomes integral to accurate cost estimation and efficient project execution.
Before the foundation of a concrete loading dock can be laid, the ground must often be cleared through demolition and site preparation. Existing structures on the site may need removal, and this process can introduce unforeseen expenses. The challenges of demolishing structures safely, disposing of debris, and ensuring the site is adequately prepared for construction can impact both time and budget. Factors such as the type of structures to be removed, environmental considerations, and the need for specialized equipment can contribute to the complexity and cost of this initial phase.
As stakeholders embark on the journey of concrete loading dock construction, accounting for potential surprises in demolition and site preparation becomes a crucial aspect of financial planning and risk management.
The subterranean aspects of construction, particularly those related to utilities, can often hide beneath the surface but carry significant cost implications. Rerouting or extending utilities to accommodate the new concrete loading dock can be a hidden cost factor. Whether it involves adjustments to electrical lines, water pipes, or other essential services, careful consideration must be given to the impact on both the construction timeline and budget. The challenges of coordinating with utility providers, ensuring compliance with regulations, and addressing any unforeseen issues that may arise during utility work add layers of complexity to the project. Businesses setting sail on the construction of a concrete loading dock must be adept at navigating the subterranean seas of utilities and relocation, recognizing that these hidden costs can surface if not meticulously accounted for in the overall budget.
Construction projects, including the creation of concrete loading docks, are not immune to unexpected challenges that can arise throughout the process. Weather delays, unforeseen ground conditions, or design changes can lead to cost overruns and impact the overall project timeline. Inclement weather, such as heavy rainfall or extreme temperatures, can disrupt construction activities, leading to delays and potential additional costs. Unforeseen ground conditions, such as unexpectedly soft soil or the discovery of buried obstacles, may require adjustments to the construction plan. Design changes, whether due to regulatory requirements or evolving project needs, can introduce complexities that influence costs. As businesses embark on the construction journey, being prepared to weather these storms of unexpected challenges becomes a critical aspect of project management, ensuring that the ship stays on course despite the uncertainties that may arise.
The construction cost of a loading dock is contingent on various factors, such as the dock’s size, complexity, materials utilized, location, and labor expenses. A straightforward loading dock project might have a construction cost as low as $5,000, while a more intricate one could incur expenses exceeding $50,000. Specifically for a concrete loading dock, costs typically range from $5,000 to $10,000, with variations based on the dock’s size and location. The average cost per square foot for a loading dock falls within the range of $20 to $50, with an average of $35 per square foot.
When embarking on the construction of a loading dock, one of the key strategies to manage costs is to optimize the design by aligning it closely with your actual operational needs. Carefully evaluate the size requirements of the loading dock based on your business’s current and future demands. Avoid overdesigning, as an excessively large or complex loading dock can significantly inflate construction costs without providing tangible benefits. Engage with professionals to conduct a thorough analysis of your workflow, ensuring that the design maximizes efficiency and functionality. By tailoring the size and features to meet specific operational requirements, you not only optimize construction costs but also enhance the overall effectiveness of your loading dock.
Obtaining competitive pricing is a fundamental aspect of managing construction costs. Instead of settling for the first contractor you come across, shop around and solicit quotes from multiple reputable contractors. This process allows you to compare not only the overall cost estimates but also the breakdown of expenses, ensuring transparency in the pricing structure. Consider factors such as experience, reputation, and project timelines when selecting a contractor. By fostering healthy competition among contractors, you increase the likelihood of securing a cost-effective construction deal that aligns with your budgetary constraints.
To alleviate the financial burden associated with loading dock construction, consider implementing a phased construction approach. Rather than undertaking the entire project at once, divide it into manageable phases. This approach allows you to spread the costs over time, making the investment more manageable for your budget. Prioritize the construction phases based on critical operational needs, ensuring that each completed stage contributes to the overall functionality of the loading dock. This phased strategy not only provides financial flexibility but also enables you to adapt the construction process based on evolving business requirements.
Exploring alternative materials can be a game-changer in optimizing construction costs. Traditional construction methods may involve time-consuming processes that contribute to higher labor expenses. Consider incorporating precast concrete sections into your loading dock design. Precast concrete offers the advantages of faster installation and potentially reduced labor costs. These sections are manufactured off-site, ensuring precision and quality, and can be assembled more efficiently during on-site construction. By embracing alternative materials with cost and time-saving benefits, you not only optimize the construction process but also contribute to long-term cost efficiency and durability in your loading dock infrastructure.
Receive highly accurate estimates tailored to your zip code, giving you the edge to secure more projects. Upload your plans and start winning!
Remember, the construction cost is just one piece of the puzzle. Factor in long-term maintenance, potential upgrades, and the impact on operational efficiency when making your decision. A well-built dock can translate into significant cost savings down the line by minimizing downtime and repairs.
Building a concrete loading dock is an investment in your business’s future. By understanding the cost variables, strategically planning your design, and choosing the right contractor, you can construct a concrete fortress that facilitates smooth operations, enhances safety, and stands strong for years to come.
So, delve into the details, arm yourself with knowledge, and build a concrete loading dock that serves your business with unwavering strength and efficiency.
The cost of constructing a concrete loading dock is influenced by factors such as size, complexity, materials used, location, labor expenses, and additional features like dock levelers, roofing, and enclosures. Each of these elements plays a crucial role in determining the overall project cost.
The size and complexity of a concrete loading dock directly impact construction costs. Larger docks with more bays and extensive dimensions require additional materials, labor, and resources, leading to higher overall expenses. The intricacies of design and functionality also contribute to the complexity and cost of the project.
The choice of materials, including concrete type and reinforcement, influences the durability and load-bearing capacity of the loading dock. High-traffic docks may require heavy-duty reinforcement and specific concrete mixes, contributing to higher construction costs.
The location of the construction site and adherence to local regulations significantly impact costs. Navigating regulatory requirements, obtaining permits, and complying with local building codes may incur additional fees. The accessibility of the site and regional labor rates also contribute to cost variations.
Yes, several strategies can help optimize construction costs. Prioritizing design based on actual operational needs, obtaining competitive quotes from multiple contractors, phasing the construction to spread costs, and exploring alternative materials like precast concrete sections are effective cost-saving approaches.
Hidden costs may include demolition and site preparation, utility adjustments or relocations, and unexpected challenges like weather delays or unforeseen ground conditions. Proper planning and risk management are essential to account for these potential additional expenses.
Businesses can manage the financial burden by optimizing design based on needs, comparing quotes from multiple contractors, phasing construction to spread costs over time, and considering alternative materials for efficiency. Thorough planning, budgeting, and understanding long-term maintenance implications are crucial aspects of effective financial management.
The cost of concrete loading dock construction can vary widely. On average, a straightforward project may cost as low as $5,000, while a more intricate one could exceed $50,000. Specifically for a concrete loading dock, costs typically range from $5,000 to $10,000, with an average cost per square foot falling within the range of $20 to $50.
Businesses can prepare for unexpected challenges by building contingency funds into their budget, staying informed about regional construction dynamics, and working closely with experienced contractors who can navigate unforeseen circumstances. Flexibility in project timelines and proactive communication are key to managing unexpected challenges effectively.
Beyond construction costs, businesses should consider long-term maintenance, potential upgrades, and the impact on operational efficiency. A well-built loading dock can lead to significant cost savings over time by minimizing downtime and repairs, making it essential to view the investment holistically.
Here I am going to share some steps to get your Concrete Loading Dock Construction Cost Estimating report.
You can send us your plan on info@estimatorflorida.com
Before starting your project, we send you a quote for your service. That quote will have detailed information about your project. Here you will get information about the size, difficulty, complexity and bid date when determining pricing.
Our team will takeoff and estimate your project. When we deliver you’ll receive a PDF and an Excel file of your estimate. We can also offer construction lead generation services for the jobs you’d like to pursue further.
561-530-2845
info@estimatorflorida.com
Address
5245 Wiles Rd Apt 3-102 St. Pete Beach, FL 33073 United States
561-530-2845
info@estimatorflorida.com
Address
5245 Wiles Rd Apt 3-102 St. Pete Beach, FL 33073 United States
All copyright © Reserved | Designed By V Marketing Media | Disclaimer