Commercial Wood Framing Cost Per Square Foot
Commercial buildings are an essential part of our urban landscape, serving as hubs for businesses, offices, and various enterprises. When it comes to constructing these commercial structures, the choice of framing materials plays a significant role in determining the overall cost. Unlike residential construction, commercial buildings require heavier-duty materials and wood framing techniques, which can drive up the expenses considerably. In this article, we’ll delve into the complexities of commercial wood framing and explore the factors that impact its cost per square foot.
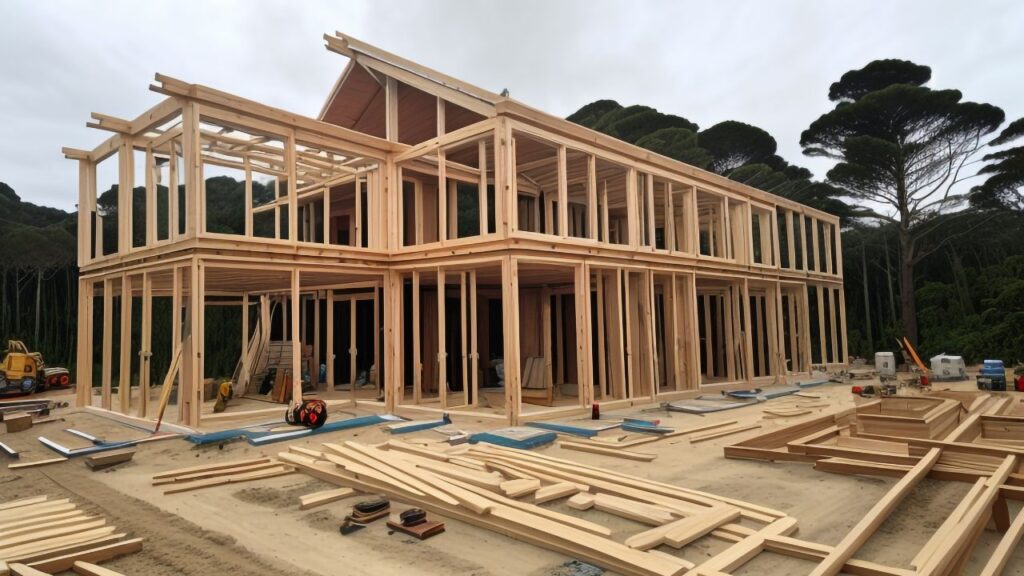
Understanding Commercial Wood Framing
Commercial wood framing involves the use of wooden structural components to create the framework for large-scale structures such as offices, retail outlets, warehouses, and more. This framework provides stability and support for the building, ensuring it can withstand the demands of commercial use. Wood, known for its natural beauty and versatility, is a popular choice for this purpose. However, it’s crucial to note that commercial wood framing requires high-quality, load-bearing wood that can withstand heavy use.
Are You Looking For?

Fully Insured Licensed Hire a Contractor For Commercial wood Framing
Hire Contractor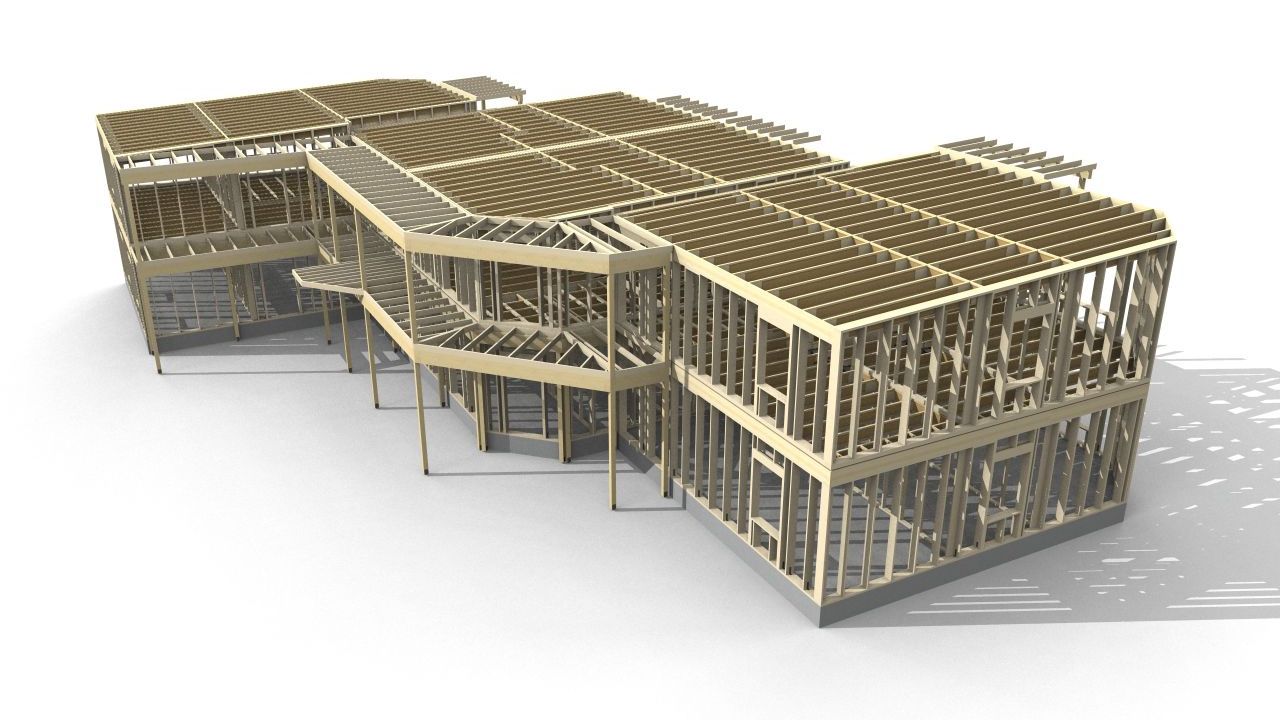
Make Informed Design Decisions Showcase Your Design Ideas
Get RenderingCall Us To Discuss More at 561-530-2845
Factors Affecting Commercial Wood Framing Costs
Several factors contribute to the cost of wood framing for commercial buildings. It’s essential to consider these elements when estimating the expenses for your project.
Type of Wood
The choice of wood has a significant impact on cost. Different wood species come with varying price tags, and some are better suited for structural purposes than others. High-quality hardwoods like oak, maple, or Douglas fir are often pricier than softwoods such as pine or spruce, but they offer superior strength and durability. Choosing the right wood for your project is essential to balance cost and structural integrity.
Complexity of the Design
The architectural design of a commercial building can also affect framing costs. Unconventional designs, intricate details, and unique features may require more labor and materials, thus increasing the overall expense. For instance, if your building design incorporates curved or sloped elements, it will demand more precise cuts and additional time, which can add to the labor cost.
Labor Costs
The cost of labor is a substantial part of any construction project, and commercial wood framing is no exception. Skilled carpenters and laborers are essential for proper wood framing, and their wages contribute significantly to the total cost. The complexity of the design and the size of the project also play a role in determining labor costs.
Location
The geographic location of the construction site can impact costs. Urban areas often have higher labor and material expenses, while rural locations may offer more affordable options. Additionally, the distance from wood suppliers can affect transportation costs, especially if you need specific, high-quality wood species.
Average Cost Ranges
The cost of commercial wood framing can vary widely, and it’s crucial to understand the typical cost ranges. Here are the average cost ranges you can expect:
Low-End Costs
On the lower end of the spectrum, commercial wood framing can cost around $18 per square foot. This typically includes basic materials, straightforward designs, and more cost-effective wood options. Low-end projects often focus on functionality and cost-efficiency.
Mid-Range Costs

For mid-range projects with moderate complexity and higher-quality materials, you might find costs ranging from $25 to $35 per square foot. These projects strike a balance between design complexity and budget considerations. They might involve hardwoods like oak or engineered wood products for added strength.
High-End Costs
Complex commercial projects with high-quality materials, intricate designs, and premium wood choices can reach costs of up to $45 per square foot or more. High-end projects prioritize aesthetics, sustainability, and durability, making use of exotic hardwoods or engineered wood products like laminated veneer lumber.
It’s important to note that these cost ranges are approximate and can vary based on specific project requirements and regional factors. The choice of wood, design complexity, and location are critical determinants of the final cost.
Hire a Commercial Metal Contractor
We provide commercial metal estimating services for small and big construction projects. We analyze the costs of commercial metal projects. A growing trend in commercial metal building construction is the use of prefabricated steel buildings.
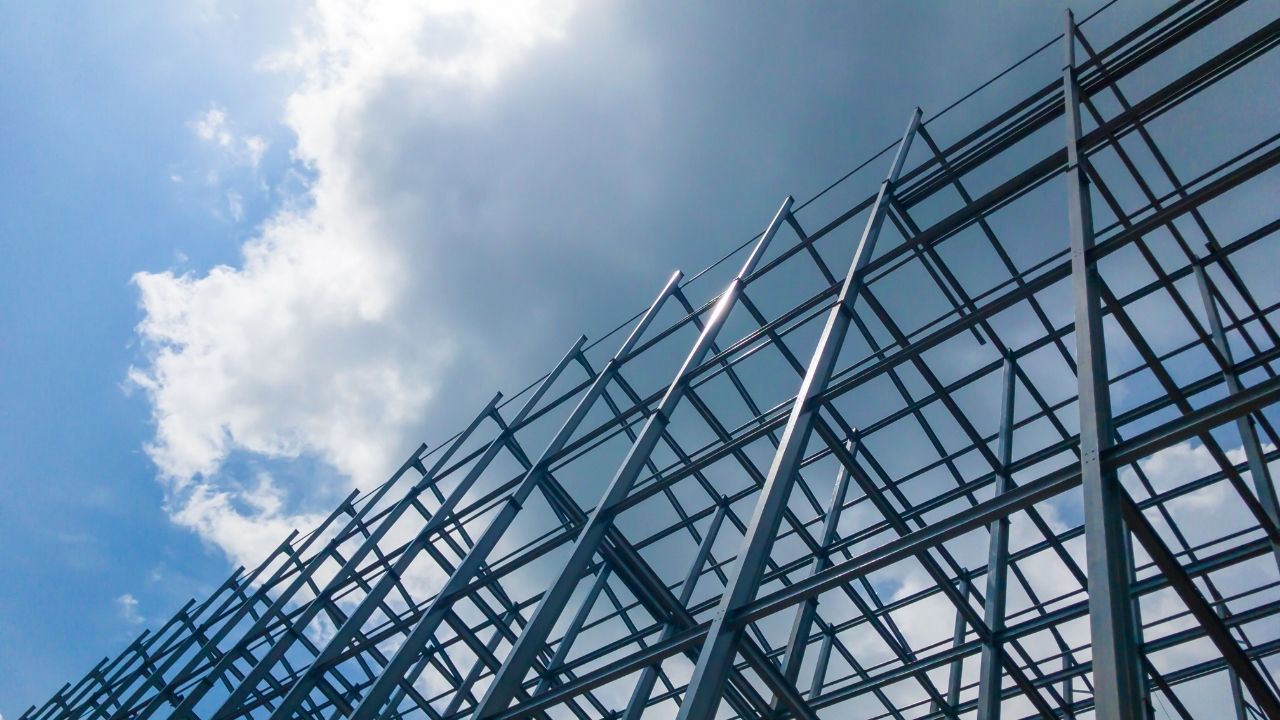
Wood Framing Techniques for Commercial Buildings
Several techniques are used in commercial wood framing, each with its advantages and applications. Understanding these techniques can help you choose the right approach for your project.
Traditional Wood Framing
Traditional wood framing involves the use of standard lumber and framing techniques. It is a cost-effective method suitable for simpler commercial structures. It relies on conventional wood sizes and configurations, making it a practical choice for budget-conscious projects. The cost of traditional wood framing can be on the lower end of the spectrum, especially when combined with cost-effective wood species.
Engineered Wood Products
Engineered wood products, such as laminated veneer lumber (LVL) and glulam beams, offer enhanced strength and stability. These materials are often used in larger, more complex commercial projects, providing superior load-bearing capacity and resistance to warping or bending. While they can be more expensive, they offer long-term value by reducing the need for additional support structures and costly repairs.
Hybrid Wood Framing
Hybrid wood framing combines traditional and engineered wood products, allowing for cost savings while maintaining structural integrity. It’s a versatile choice for various commercial applications, particularly when trying to balance cost and performance. Hybrid framing can use standard lumber for less critical areas and engineered products where additional strength is required.
The choice of framing technique is closely tied to the overall cost of the project, with traditional framing generally being the most cost-effective, while engineered products and hybrid solutions may offer additional benefits at a higher initial cost.
Benefits of Commercial Wood Framing
Despite the costs, commercial wood framing offers several benefits:
- Sustainability: Wood is a renewable resource, making it an eco-friendly choice. When sourced responsibly, it contributes to a more sustainable construction industry.
- Insulation: Wood offers excellent thermal insulation, helping to maintain a comfortable interior environment while reducing heating and cooling costs.
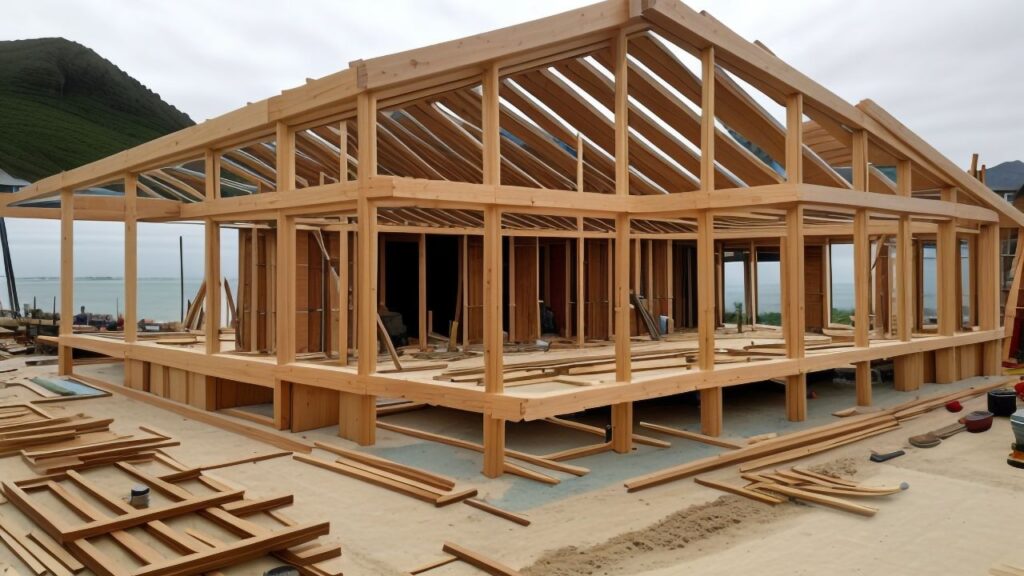
- Ease of Construction: Wood is relatively easy to work with, which can reduce construction time. Skilled carpenters can quickly assemble wood frames, speeding up the overall building process.
- Aesthetic Appeal: Wood’s natural beauty adds an attractive element to commercial structures, making them visually appealing to customers and visitors.
These benefits need to be weighed against the initial cost to determine if wood framing is the right choice for your project.
Challenges in Wood Framing for Commercial Projects
Wood framing in commercial construction also presents challenges:
- Fire Resistance: Wood is flammable, and commercial buildings must meet strict fire safety regulations. This requires additional measures like fire-resistant coatings or the use of fire-rated wood products, which can add to the overall cost.
- Moisture Control: Wood is susceptible to moisture, which can lead to rot, warping, and structural instability. Proper design, materials, and construction practices are essential to prevent moisture-related issues, which can also add to the cost.
Balancing these challenges with the benefits of wood framing is essential for a successful and cost-effective project.
Sustainability and Commercial Wood Framing
Sustainability is a growing focus in construction. Choosing sustainably sourced wood and implementing green building practices can enhance the environmental credentials of a commercial wood framing project. Sustainable options include wood certified by organizations like the Forest Stewardship Council (FSC), which ensures responsible forestry practices. While these certifications may add a small premium to the cost of the wood, they contribute to a more environmentally friendly construction industry.
Cost Savings Strategies
To mitigate costs, various strategies can be employed in commercial wood framing:
Pre-fabrication
Prefabricating wood components off-site can save time and reduce labor costs. It also ensures higher precision in construction, as elements are manufactured under controlled conditions, minimizing errors. Prefabrication can speed up the construction process and reduce on-site labor expenses, ultimately leading to cost savings.
Technology Integration
Utilizing advanced construction technologies and software can streamline the framing process and improve efficiency. Computer-aided design (CAD), Building Information Modeling (BIM), and project management software can enhance project coordination and reduce errors, ultimately saving time and money. While there may be an initial investment in technology, the long-term cost savings can be substantial.
Value Engineering
Value engineering focuses on optimizing project costs without compromising quality. It involves reevaluating design and material choices to find cost-effective alternatives. By working closely with architects, engineers, and contractors, businesses can identify areas where costs can be reduced without compromising structural integrity or safety.
While these cost savings strategies may require some upfront investment, they often lead to long-term savings by reducing construction time, materials wastage, and the need for costly revisions.
Case Studies
Explore real-world examples of successful commercial wood framing projects to gain insights into cost management and the application of different techniques. These case studies provide valuable lessons and illustrate the successful implementation of cost-saving strategies in various commercial construction projects. Analyzing these case studies can offer practical insights for your own projects, helping you make informed decisions that balance cost and performance.
Are You Looking For?

Fully Insured Licensed Hire a Contractor For Commercial wood Framing
Hire Contractor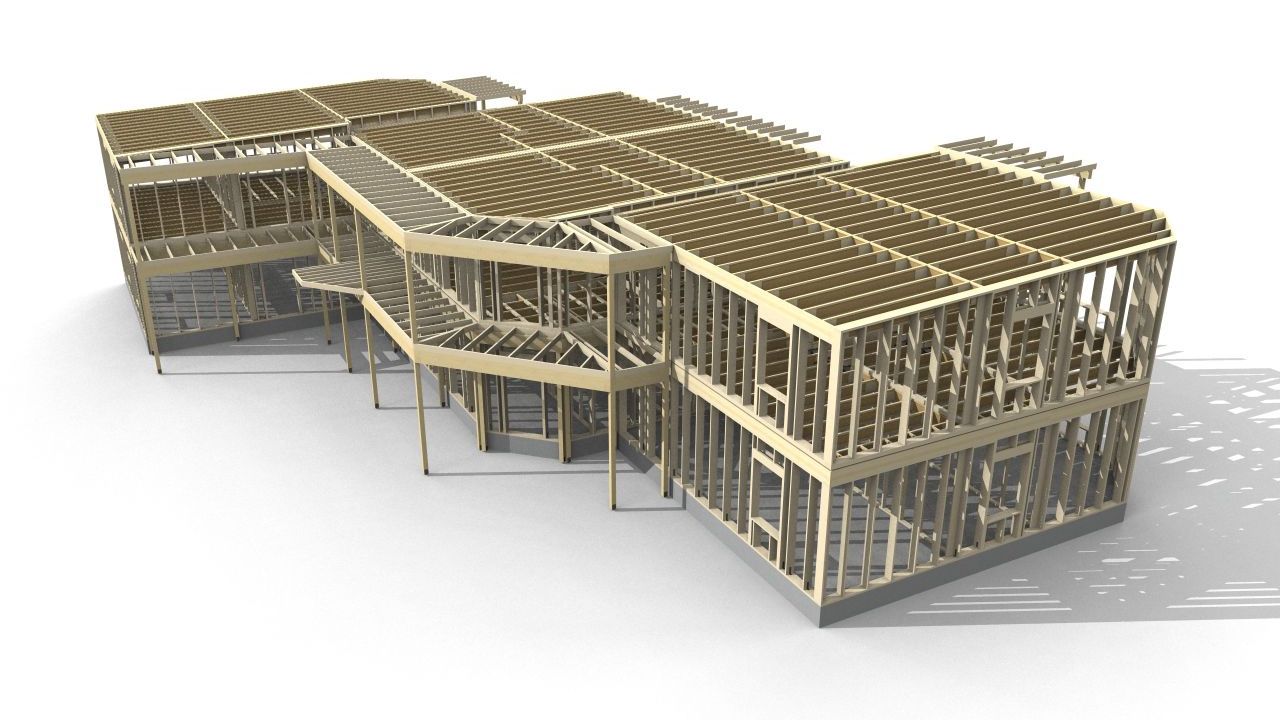
Make Informed Design Decisions Showcase Your Design Ideas
Get RenderingCall Us To Discuss More at 561-530-2845
The Future of Commercial Wood Framing
As the construction industry continues to evolve, commercial wood framing will adapt to meet new demands and standards. Innovations in materials, techniques, and sustainability will shape the future of this essential construction method. The development of new, environmentally friendly treatments and coatings will enhance the durability and longevity of wood framing, while digital technologies will further improve project management and construction efficiency.
Conclusion
Commercial wood framing may come at a cost, but it offers durability, sustainability, and versatility that make it a compelling choice for various projects. By understanding the factors affecting costs and implementing cost-saving strategies, businesses can harness the benefits of wood framing for their commercial buildings. Careful planning, attention to detail, and the use of innovative technologies are key to managing costs effectively while reaping the advantages of wood framing.
FAQs
The average cost of commercial wood framing can vary, but it typically falls within the range of $18 to $45 per square foot. Factors such as the type of wood, complexity of the design, labor costs, and location can influence the final cost.
Yes, wood framing can be a sustainable choice. When responsibly sourced and combined with green building practices, it contributes to a more eco-friendly construction industry. Look for certifications like FSC to ensure sustainable wood sourcing.
Cost reduction strategies include selecting cost-effective wood species, optimizing design complexity, utilizing prefabrication, integrating technology, and engaging in value engineering. These approaches can help you maintain quality while managing expenses.
Yes, alternatives such as steel or concrete framing are common choices for commercial construction. Each material has its advantages and considerations, so the choice depends on the specific project requirements and budget.
When choosing wood for commercial framing, consider factors like the wood’s strength, durability, sustainability, and cost. The type of wood you select should align with the project’s structural requirements and design goals.
Process To Get Commercial Wood Framing Cost Estimate Report
Here I am going to share some steps to get your commercial wood framing cost estimate report.
-
You need to send your plan to us.
You can send us your plan on info@estimatorflorida.com
-
You receive a quote for your project.
Before starting your project, we send you a quote for your service. That quote will have detailed information about your project. Here you will get information about the size, difficulty, complexity and bid date when determining pricing.
-
Get Estimate Report
Our team will takeoff and estimate your project. When we deliver you’ll receive a PDF and an Excel file of your estimate. We can also offer construction lead generation services for the jobs you’d like to pursue further.
Google Reviews
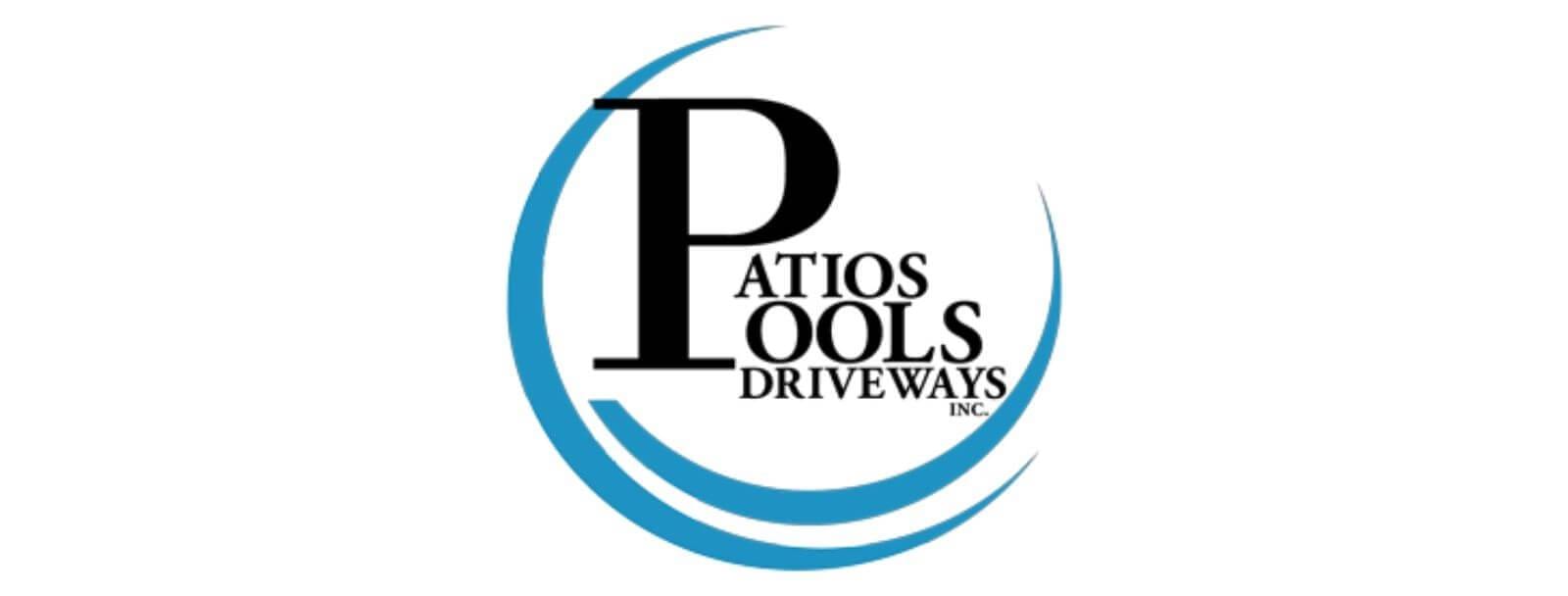
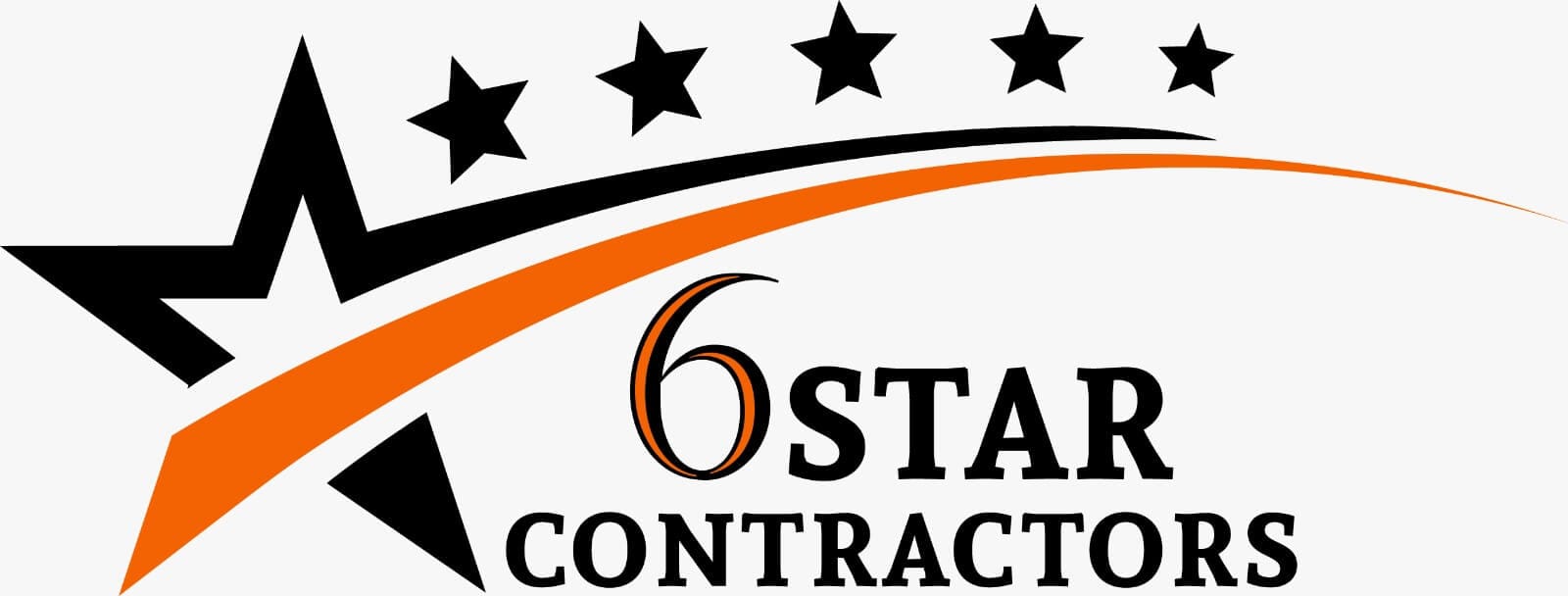
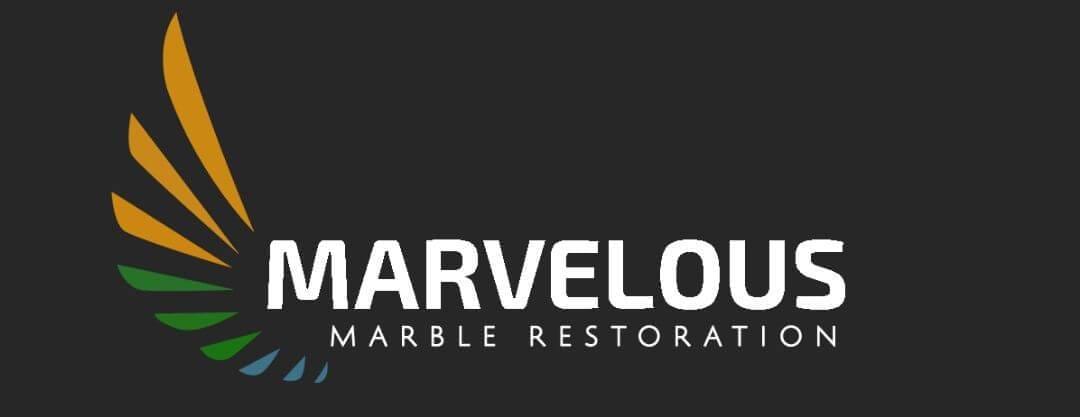